Yung-Kuang Yang and Chorng-Jyh Tzeng
Keywords: ANOVA, AZ91D, Die-casting, Taguchi method, Stress–strain.
Introduction
Magnesium and its alloys are becoming increasingly important as structural materials for applications in which weight reduction is critical, because of their low density and high stiffness-to-weight ratio. Popular applications include automotive, industrial, materials-handling, and aerospace equipment such as automotive pulleys, cog-tooth sprockets, oil pump covers, cylinder liners, and aircraft engine castings [1, 2].
Recently, a variety of portable products, which are convenient for users, have been developed. These products are typically light and small in size. Magnesium alloys have been extensively adopted in the shells of devices such as notebook computers, cellular phones, and PDAs [3].
Since the external shell of a notebook computer is a thin wall, notebooks have a small thickness-aspect ratio. When using the magnesium alloy AZ91D as an external shell material, possible formation techniques include die-casting and semisolid molding.
Advantages of die-casting include higher production rate, stable quality, and reasonable cost [4]. As stated previously, die-casting is a key forming method, but produces workpieces that cannot be further machined. Because the workpieces have thin walls, the profile dimensions need to be accurate and the surface must be lustrous.
Three factors—the solid solution rate, pressure differential, and temperature differential—affect product quality in the molding cavity. Numerous Japanese manufacturers have successfully implemented the Taguchi method to improve product and process quality.
Taguchi is a novel approach for improving quality, which applies several statistical concepts to quality engineering. The factorial experimental design developed by Taguchi concentrates on reducing variation in the Received April 26, 2005; Accepted August 1, 2005 Address correspondence to Yung-Kuang Yang, Department of Mechanical Engineering, Ming Hsin University of Science and Technology, 1, Hsin Hsing Road, Hsin Feng, 304 Hsinchu, Taiwan; Fax: +886-3-5782822; E-mail: yky@must.edu.tw presence of noise.
These experiments are established using orthogonal arrays. The Taguchi method [5–7] combines the effects of each noise factor and calculates a signal-tonoise ratio (S/N ratio) for each experiment. Inner and outer orthogonal arrays are used to calculate the signal-to-noise ratio for determining the optimal setting of each parameter.
Several studies have proven that the Taguchi method can be applied to various engineering designs [8–13]. The Taguchi method has been used successfully in several industrial applications, such as manufacturing processes, mechanical component design, and process optimization.
The experimental results were satisfactory. For instance, Tarng and Yang [10] have studied the application of the Taguchi method to the optimization of the submerged arc welding process. Connor [11] presented parameter-sizing methods for fluid power circuits using the Taguchi method. Tseng et al. [12] employed the Taguchi method to find the optimal conditions for the dry-etching process.
Hsiang and Kuo [13] have also studied the hot extrusion process of magnesium alloy sheet etching. This study used the Taguchi method to investigate the die-casting process parameter optimization for AZ91D in notebook computer base shells. The Flow-3D software package was employed for the simulation, while fusion slurry pressure, fusion slurry velocity, fusion slurry temperature, and initial die temperature were selected as the die-casting process parameters. Furthermore, mechanical properties such as stress, elongation, and hardness were examined.
The abruption surfaces after tensile testing were observed by SEM to understand the abruption mechanisms.
Experimental procedures
2.1. Material
Table 1 lists the basic physical properties of the magnesium alloy AZ91D employed in this study.
2.2. Schematic Mechanisms
Figure 1 illustrates the base shell configuration of a notebook computer. The products were molded in
a computerized reciprocating die-casting machine with a maximum die-casting pressure of 182 MPa and a locking
force of 660 tons.
2.3. Experimental Design
Die-casting product quality is influenced by process parameters such as cooling time, filling pressure, filling
speed, melt temperature, mold temperature, mold geometry shape, melt material properties, and heat transfer action
of flow field. According to the FLOW-3D manual [14], the filling pressure, filling speed, melt temperature,
and mold temperatures are the most significant factors in the die-casting process for product quality control.
Accordingly, this study performed the experiment using four controllable three-level factors and three response variables. Additionally, the recommendation of the technology report of Oskar Frech GmbH company [15] for the
application parameter range was employed: filling pressure of 15–21MPa, filling speed of 50–100 m/s, melt temperature of 600–700C, and mold temperature of 200–250C.
Table 2 presents the fusion slurry pressure [i.e., A (MPa)], fusion slurry velocity [i.e., B (m · s−1)], fusion slurry temperature [i.e., C (C)], and initial die temperature [i.e., D (C)] with three levels under the applied Taguchi method in this investigation.
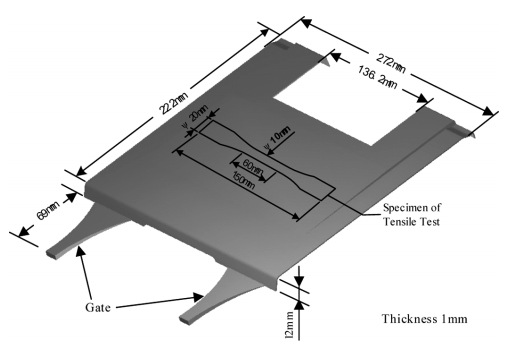
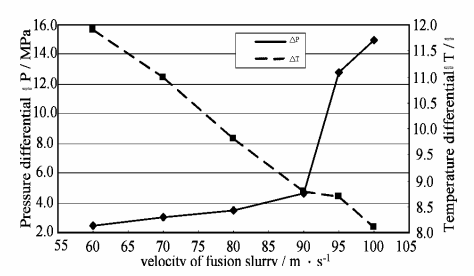
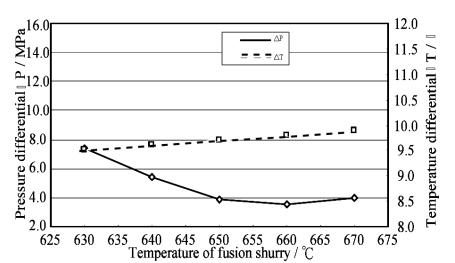
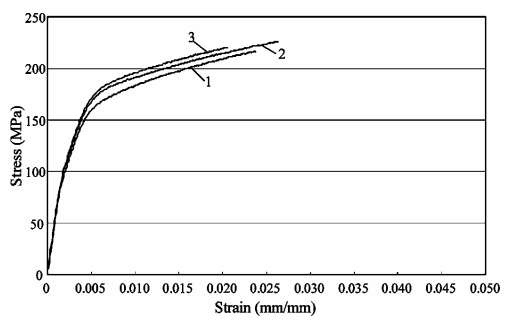
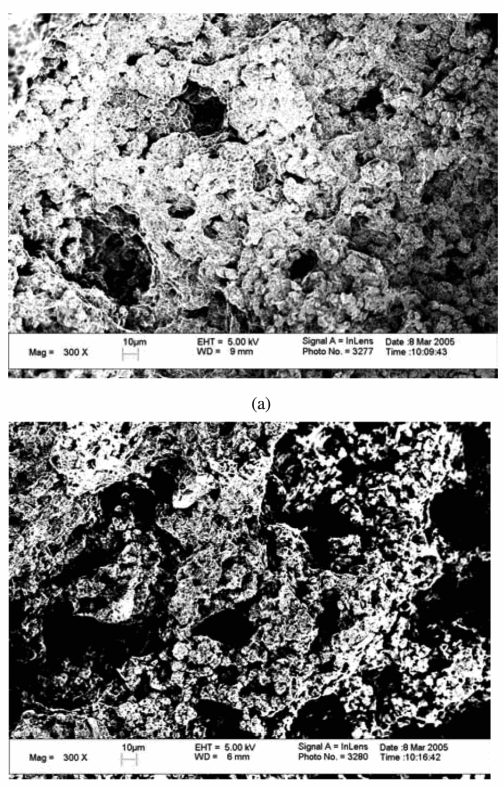
Conclusions
This study investigated the optimization of die-casting process factor and levels using the Taguchi method.
Also, ANOVA was applied to examine which parameters most influence the die-casting process. The pressure and
temperature differentials in the molding cavity were selected as the production quality targets. The analytical results are summarized as follows:
- The optimal parameter combination of the die-casting process corresponded to a fusion slurry pressure of
21MPa, a fusion slurry velocity of 80 m/s, a fusion slurry temperature of 660C, and an initial die temperature of
230C. Therefore, A3B2C3D2 is recommended for the die-casting process parameters. - Fusion slurry velocity was the most influential of the die-casting process parameters.
- Increasing the fusion slurry velocity increases the pressure differential and decreases the temperature
differential. - A low fusion slurry velocity reduces both hardness and stress, and increases the number of pinholes on the cross surface.
References
- Luo, A. Processing, microstructure, and mechanical behavior of cast magnesium metal matrix composites. Metallurgical and Materials Transactions A, 1995, 26A, 2445–2455.
- Friedrich, H.; Schumann, S. Research for a new age of magnesium in the automotive industry. J. Mater. Process. Technol. 2001, 117, 276–281.
- EI-Mahallawy, N.A.; Taha, M.A.; Pokora, E.; Klein, F. On the influence of process variables on the thermal conditions and properties of high pressure die-cast magnesium alloys. J. Mater. Process. Technol. 1998, 73, 125–138.
- Song, G.; Atrens, A.; Dargusch, M. Influence of microstructure on the corrosion of diecast AZ91D. Corrosion Science 1999, 41, 249–273.
- Taguchi, G. Introduction to Quality Engineering; Asian Productivity Organization, 1990.
- Su, C.D. Quality Engineering, R.O.C., Quality Association, 2002; 123–128.
- Ross, P.J. Taguchi Techniques for Quality Engineering, 2nd Ed.; McGraw-Hill: New York, 1996.
- Ku, K.J.; Rao, S.S.; Chen, L. Taguchi-aided search method for design optimization of engineering system. Engineering Optimization 1998, 30, 1–23.
- Lin, C.L. Use of the Taguchi method and grey relational analysis to optimize turning operations with multiple performance characteristics. Materials and Manufacturing Processes 2004, 19 (2), 209–220.
- Tarng, Y.S.; Yang, W.H. Application of Taguchi method to the optimization of the submerged arc welding process. Materials and Manufacturing Processes 1998, 13 (3), 455–467.
- Connor, A.M. Parameter sizing for fluid power circuits using Taguchi method. Engineering Design 1999, 10 (4), 377–390.
- Tseng, T.C.; Cheng, Y.H.; Chuang, B.C.; Hsiao, M.N. Optimal conditions for the dry-etching process under Taguchi method, 38th Annual Conference of CSQ & 8th NQMS, R.O.C., 2002; 581–587.
- Hsiang, S.H.; Kuo, J.L. An investigation on the hot extrusion process of magnesium alloy sheet. J. Mater. Process. Technol. 2003, 140, 6–12.
- FLOW-3D User’s Manual. Vols. 1 and 2, Version 8.0, Flow Science Inc.: 2002.
- Oskar Frech GmbH + Co. KG, Schorndorfer Straße 32, D-73614, Schorndorf-Weiler, Deutschland.
- Kalpakjian, S.; Schmid, S.R. Manufacturing Engineering and Technology International, 4th Ed.; Prentice Hall Co.: 2001; 241–260.