This article introduces the paper "Development of Low-Pressure Die-Cast Al-Zn-Mg-Cu Alloy Propellers Part II: Simulations for Process Optimization".
1. Overview:
Title: Development of Low-Pressure Die-Cast Al-Zn-Mg-Cu Alloy Propellers Part II: Simulations for Process Optimization
Author: Min-Seok Kim and Soonho Won
Publication Year: 2024
Publishing Journal: Materials (MDPI)
Keywords: Al-Zn-Mg-Cu alloy; low-pressure die-casting; simulation; propeller; hot tearing
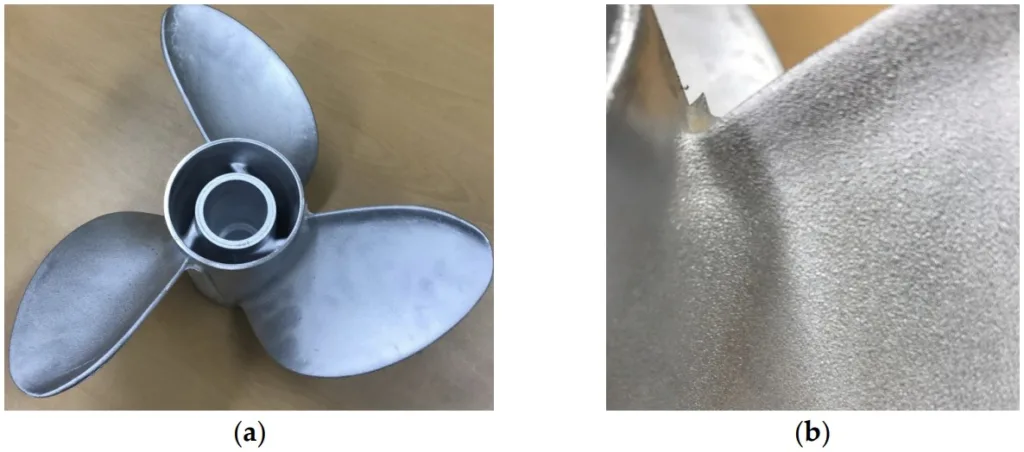
2. Research Background:
The demand for high-performance leisure boat propellers is steadily increasing. While stainless steel propellers offer superior properties, their high manufacturing costs and processing difficulties present challenges. Cast aluminum alloys, though easier to manufacture, are limited to low-power applications due to their material properties. High-strength aluminum alloys offer a promising alternative by balancing mechanical properties and cost-effectiveness.
In Part I of this study, the authors developed an Al-6Zn-2Mg-1.5Cu alloy suitable for propeller production and identified hot tearing at the hub-blade junction as a significant challenge in low-pressure die-casting (LPDC). Conventional gravity casting methods struggle to control casting defects in high-strength aluminum alloys, hindering the production of high-quality components. Therefore, optimizing the LPDC process is crucial to overcome hot tearing and ensure stable mass production of these propellers. Simulation technology is essential for efficient process optimization, as trial-and-error adjustments on mass-production lines are limited.
3. Research Purpose and Research Questions:
Research Purpose:
This study aims to develop a coupled thermal fluid stress analysis model using ProCAST software to optimize the LPDC process for manufacturing high-strength Al-Zn-Mg-Cu alloy propellers. The primary goal is to minimize hot tearing defects observed at the junction of the hub and blades.
Key Research Questions:
The research focuses on understanding how adjusting LPDC process parameters, specifically:
- Melt supply temperature
- Initial mold temperature
- Curvature radius between the hub and blades
influences the occurrence of hot tearing in Al-Zn-Mg-Cu alloy propellers.
Research Hypotheses:
The study hypothesizes that by strategically adjusting these casting parameters and the geometric design (curvature radius), it is possible to minimize hot tearing and improve the overall quality and structural integrity of LPDC Al-Zn-Mg-Cu alloy propellers.
4. Research Methodology
Research Design:
The research employs a simulation-based process optimization approach using commercial ProCAST software. The simulation results are validated through both further simulations and practical application in a mass-production setting. Non-destructive testing is used to confirm the simulation findings.
Data Collection Method:
- Simulation Data: ProCAST software is used to perform coupled thermal fluid stress analysis, generating data on Effective Plastic Strain (EPS) distribution under varying process conditions.
- Experimental Validation: Prototype propellers are manufactured using optimized LPDC parameters.
- Defect Analysis: Non-destructive X-ray Computed Tomography (CT) is used to analyze internal defects in both optimized and commercially available propellers. Surface microstructure of hot tearing is examined using Scanning Electron Microscopy (SEM).
Analysis Method:
- Finite Element Method (FEM): ProCAST software utilizes FEM for thermal flow stress analysis.
- Effective Plastic Strain (EPS) Model: The EPS model within ProCAST is used to predict hot tearing susceptibility. EPS is defined as the total accumulated plastic strain during solidification. Stress analysis is conducted from a solid fraction of 0.5 or higher, considering the dendrite coherency point.
Research Subjects and Scope:
The study focuses on the LPDC process for manufacturing propellers using an Al-6Zn-2Mg-1.5Cu alloy. The scope includes:
- Simulation of the LPDC process using ProCAST.
- Investigating the influence of melt supply temperature (680~820 °C), initial mold temperature (200~500 °C), and curvature radius (4.0 mm and 4.6 mm) on hot tearing.
- Validation of simulation results through practical manufacturing and defect analysis.
5. Main Research Results:
Key Research Results:
- EPS Prediction Accuracy: Simulations using the EPS model accurately predicted the locations of hot tearing observed in actual propeller castings, validating the model's effectiveness.
- Curvature Radius Optimization: Reducing the curvature radius at the hub-blade junction from 4.6 mm to 4.0 mm significantly decreased the maximum EPS value from "0.085 to 0.058" (Figure 4), indicating a reduction in hot tearing susceptibility. This suggests that a smoother transition structure at the junction disperses deformation concentration.
- Initial Mold Temperature Effect: Increasing the initial mold temperature from 200 °C to 500 °C decreased the maximum EPS value from "0.065 to 0.051" (Figure 6), demonstrating that higher mold temperatures help suppress hot tearing.
- Melt Supply Temperature Effect: Varying the melt supply temperature (680 °C to 820 °C) showed a less significant effect on hot tearing within the tested range. "Considering the difference between the maximum value of 0.059 and the minimum value of 0.052, no significant effect was observed" (Figure 5).
- Non-Uniform Mold Temperature: Simulations considering non-uniform mold temperature distribution, reflecting mold preheating and cycle analysis, showed that it can lead to higher cooling rates and increased EPS values compared to uniform mold temperature conditions (Figure 7). "When the average cooling rates near the hot tearing region were calculated for the results in Figure 7, the uniform temperature condition and the non-uniform temperature condition showed cooling rates of approximately 1.9 °C/s and 4.4 °C/s, respectively."
Statistical/Qualitative Analysis Results:
- EPS Values: Quantitative EPS values were obtained from simulations for different curvature radii and initial mold temperatures, demonstrating the reduction in hot tearing potential with optimized parameters.
- Cooling Rates: Cooling rate analysis showed that initial mold temperature significantly affects the cooling rate, which in turn influences hot tearing susceptibility.
- Visual Inspection & SEM: Visual inspection and SEM analysis (Figure 3) confirmed the presence of hot tearing at the hub-blade junction in initial prototypes and characterized the fracture surface.
- X-ray CT Analysis: X-ray CT analysis (Figure 9) revealed a significant reduction in internal defects (shrinkage cavities and pores) in the optimized propellers compared to commercially available Al-7Si-0.3Mg propellers.
Data Interpretation:
The simulation results, validated by experimental observations and non-destructive testing, demonstrate that optimizing the curvature radius and increasing the initial mold temperature in the LPDC process effectively reduces hot tearing in Al-Zn-Mg-Cu alloy propellers. Maintaining a uniform mold temperature is also crucial for minimizing hot tearing.
Figure Name List:
- Figure 1. Simulation model of the propeller LPDC process
- Figure 2. Curvature radius conditions between the hub and blades of the propeller
- Figure 3. Hot tearing in Al-6Zn-2Mg-1.5Cu propeller
- Figure 4. Simulation results of EPS prediction according to the curvature radius between the blade and hub of the propeller
- Figure 5. Simulation results on the effect of melt supply temperature on EPS and cooling rate in the Max. EPS region.
- Figure 6. Simulation results on the effect of initial mold temperature on EPS and cooling rate in the Max. EPS region.
- Figure 7. Initial mold temperature conditions and the resultant EPS predictions
- Figure 8. Developed Al-6Zn-2Mg-1.5Cu alloy propeller
- Figure 9. Internal defect investigation of aluminum alloy propellers through CT analysis
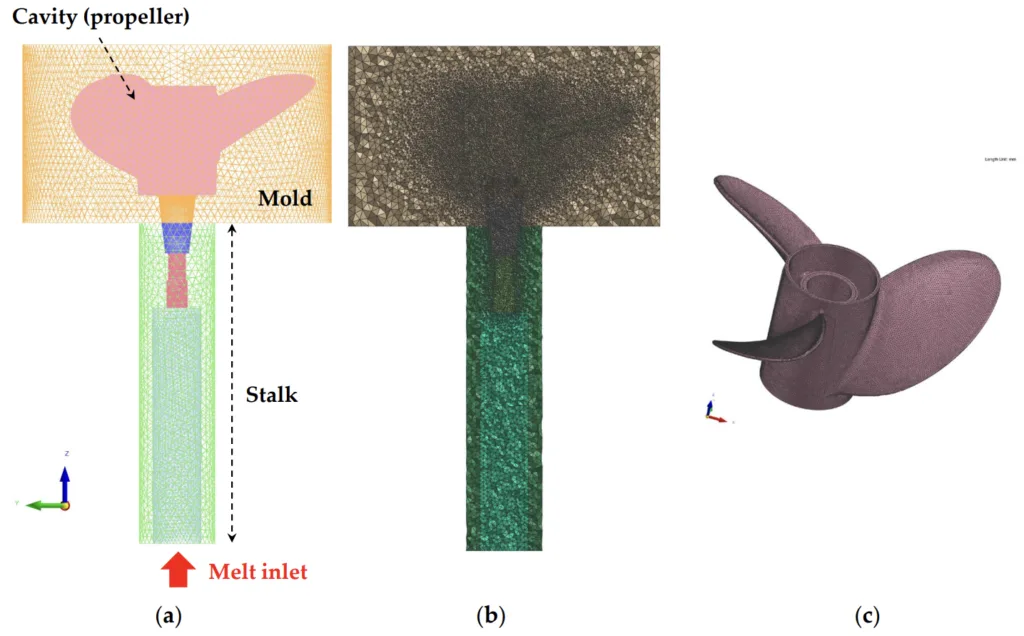
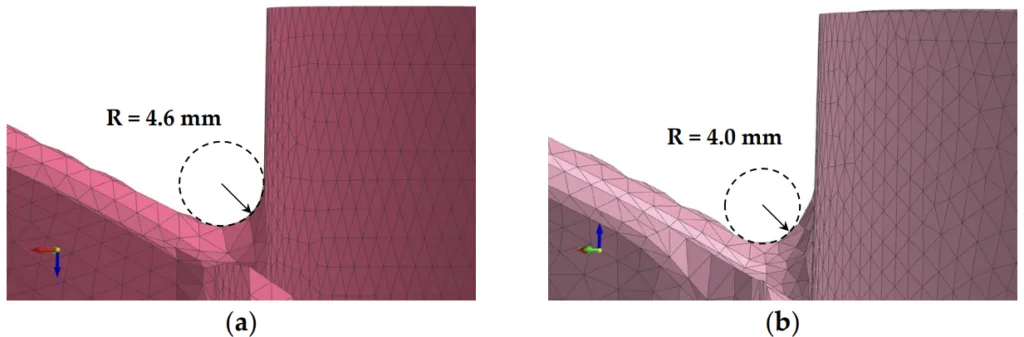
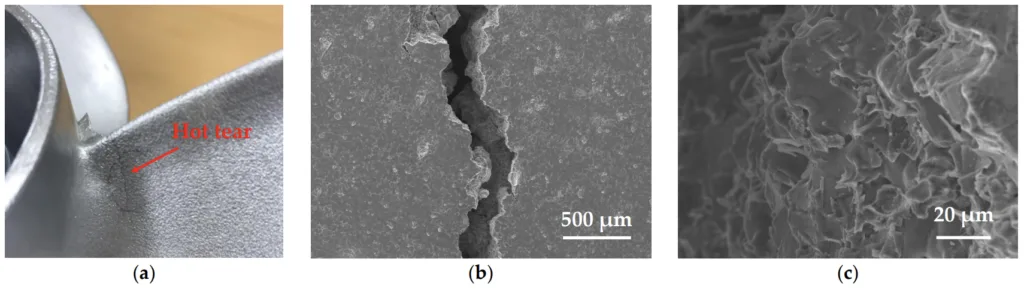
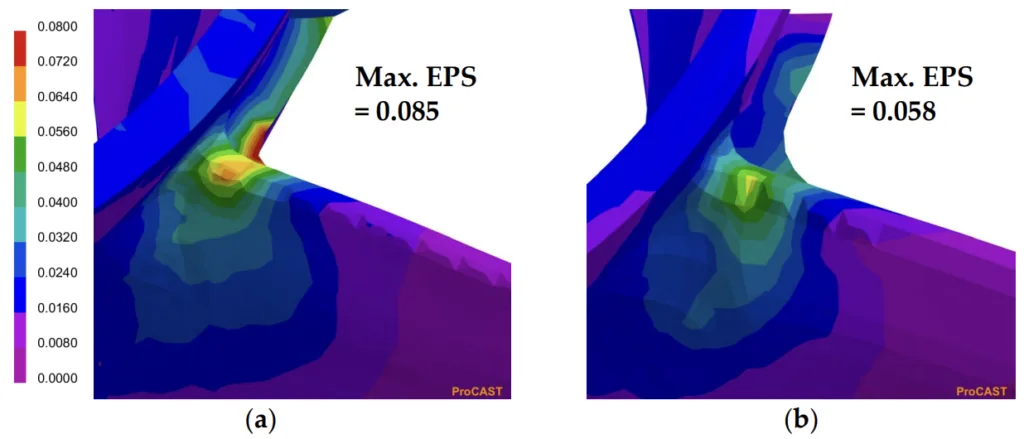
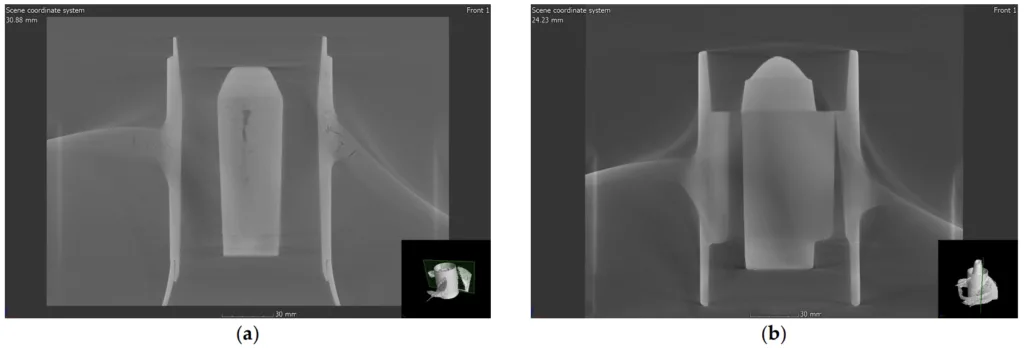
6. Conclusion and Discussion:
Summary of Main Results:
This study successfully optimized the LPDC process for Al-Zn-Mg-Cu alloy propellers using simulation-based process optimization with ProCAST software. The key findings include: optimized curvature radius and increased initial mold temperature effectively reduce hot tearing; melt supply temperature has a less significant impact within the tested range; and maintaining uniform mold temperature is beneficial. Practical application of these optimized conditions resulted in high-quality propellers with minimized hot tearing and internal defects, validated by X-ray CT analysis.
Academic Significance of the Research:
This research demonstrates the effectiveness and practicality of using simulation technology for optimizing die casting processes, specifically for mitigating hot tearing in high-strength aluminum alloys. It highlights that even small and medium-sized enterprises with limited resources can leverage simulation tools for efficient product development and process improvement.
Practical Implications:
The optimized LPDC process parameters identified in this study provide a practical guide for mass-producing high-quality Al-Zn-Mg-Cu alloy propellers with significantly reduced hot tearing and internal defects. The findings emphasize the importance of curvature radius design, initial mold temperature control, and uniform mold temperature management in achieving defect-free LPDC components.
Limitations of the Research:
The study primarily focused on understanding the tendencies of hot tearing by controlling specific casting conditions. While the simulations and experimental validations are consistent, further research may be needed to explore the interaction of multiple parameters and to optimize for other potential defects beyond hot tearing under mass production conditions.
7. Future Follow-up Research:
Directions for Follow-up Research:
Future research directions include integrating the demonstrated simulation techniques with machine learning technologies. This integration could further enhance the efficiency and effectiveness of research and development in die casting process optimization, potentially leading to more sophisticated predictive models and automated process control strategies.
Areas Requiring Further Exploration:
Further exploration could focus on a more comprehensive multi-objective optimization considering other casting defects and mechanical properties, and extending the simulation-based optimization approach to other complex die casting components and alloy systems.
8. References:
- Kluczyk, M.; Grządziela, A.; Batur, T. Design and operational diagnostics of marine propellers made of polymer materials. Pol. Marit. Res. 2022, 29, 49–59.
- Cass, A.; Nielson, J.R. Smart energy systems approach to zero emissions long-range sailing vessels. Smart Energy 2022, 7, 100086.
- Oloruntobi, O.; Mokhtar, K.; Gohari, A.; Asif, S. Sustainable transition towards greener and cleaner seaborne shipping industry: Challenges and opportunities. Clean. Eng. Technol. 2023, 13, 100628.
- Baley, C.; Davies, P.; Troalen, W.; Chamley, A.; Dinham-Price, I.; Marchandise, A.; Keryvin, V. Sustainable polymer composite marine structure: Developments and challenges. Prog. Mater. Sci. 2024, 145, 101307.
- Dashtimanesh, A.; Ghaemi, M.H.; Wang, Y. Digitalization of high speed craft design and operation challenges and opportunities. Procedia Comput. Sci. 2022, 200, 566–576.
- Begovic, E.; Bertorello, C.; De Luca, F. KISS (Keep It Sustainable and Smart): A research and development program for a zero-emission small crafts. J. Mar. Sci. Eng. 2022, 10, 16.
- Choudhary, G.; Singh, G. Comparative analysis of corrosion behaviour of stainless steel grades 304 and 316L for different applications. I-Manag. J. Mater. Sci. 2020, 7, 8–22.
- Mendagaliev, R.; Klimova-Korsmik, O.; Promakhov, V.; Schulz, N.; Zhukov, A.; Klimenko, V.; Olisov, A. Heat treatment of corrosion resistant steel for water propellers fabricated by direct laser deposition. Materials 2020, 13, 2738.
- Konieczny, J.; Labisz, K. Materials used in the combat aviation construction. Transp. Probl. 2021, 16, 5–18.
- Kim, M.S.; Kim, J. Development of low-pressure die-cast Al—Zn—Mg—Cu alloy propellers—Part I: Hot tearing simulations for alloy optimization. Materials 2024, 17, 3133.
- Pulisheru, K.S.; Birru, A.K. Effect of pouring temperature on hot tearing susceptibility of Al-Cu cast alloy: Casting simulation. Mater. Today Proc. 2021, 47, 7086–7090.
- Rahangmetan, K.A.; Sariman, F.; Parenden, D. The effect of riser use in the quality of casting Al 7075 for ship propeller. Int. J. Mech. Eng. Technol. 2019, 10, 10–17.
- Dong, G.; Li, S.; Ma, S.; Zhang, D.; Bi, J.; Wang, J.; Starostenkov, M.D.; Xu, Z. Process optimization of A356 aluminum alloy wheel hub fabricated by low-pressure die casting with simulation and experimental coupling methods. J. Mater. Res. Tehnol. 2023, 24, 3118–3132.
- Khan, M.A.A.; Sheikh, A.K. A comparative study of simulation software for modelling metal casting processes. Int. J. Simul. Model. 2018, 17, 197–209.
- Wei, C.; Ou, J.; Mehr, F.F.; Maijer, D.; Cockcroft, S.; Wang, X.; A, L.; Chen, Z.; Zhu, Z. A thermal-stress modelling methodology in ABAQUS for fundamentally describing the die/casting interface bahaviour in a cyclic permanent die casting process. J. Mater. Res. Technol. 2021, 15, 5252–5264.
- Zhnag, B.; Maijer, D.M.; Cockcroft, S.L. Development of a 3-D thermal model of the low-pressure die-cast (LPDC) process of A356 aluminum alloy wheels. Mater. Sci. Eng. A 2007, 464, 295–305.
- Ou, J.; Wei, C.; Cockcroft, S.; Maijer, D.; Zhu, L.; A, L.; Li, C.; Zhu, Z. Advanced process simulation of low pressure die cast A356 aluminum automotive wheels—Part II modeling methodology and validation. Metals 2020, 10, 1418.
- Sun, J.; Le, Q.; Fu, L.; Bai, J.; Tretter, J.; Herbold, K.; Huo, H. Gas entrainment behavior of aluminum alloy engine crankcases during the low-pressure-die-casting process. J. Mater. Process. Technol. 2019, 266, 274–282.
- Song, J.; Pan, F.; Jiang, B.; Atrens, A.; Zhang, M.; Lu, Y. A review on hot tearing of magnesium alloys. J. Magnes. Alloy 2016, 4, 151–172.
- Chen, Z.; Li, Y.; Zhao, F.; Li, S.; Zhang, J. Process in numerical simulation of casting process. Meas. Control 2022, 55, 257–264.
- Ren, Y.; Zhang, S.; Liu, T.; Bao, C.; Song, H. Prediction of hot tearing and grain structure in TiAl alloy casting. Int. J. Met. 2024, 18, 799–809.
- Dubey, S.; Swain, R. Numerical investigation on solidification in casting using ProCAST. IOP Conf. Ser. Mater. Sci. Eng. 2019, 561, 012049.
- Li, Y.; Zhang, Z.R.; Zhao, Z.Y.; Li, H.X.; Katgerman, L.; Zhang, J.S.; Zhuang, L.Z. Effect of main elements (Zn, Mg, and Cu) on hot tearing susceptibility during direct-chill casting of 7xxx aluminum alloys. Metall. Mater. Trans. A 2019, 50, 3603–3616.
- Kim, J.H.; Jo, J.S.; Sim, W.J.; Im, H.J. The influence of alloy composition on the hot tear susceptibility of the Al-Zn-Mg-Cu alloy system. Korean J. Met. Mater. 2012, 50, 669–675.
- Guo, J.; Samonds, M.T. Alloy thermal physical property prediction coupled computational thermodynamics with back diffusion consideration. J. Ph. Equilibr. Diffus. 2007, 28, 58–63.
- Wang, H.; Alexandrov, B.T.; Przybylowicz, E. Experimental and numerical modeling study of solidification cracking in alloy 52M filler metal in the cast pin tear test. Weld. World 2019, 63, 913–924.
- Dahle, A.K.; Arnberg, L. Development of strength in solidifying aluminium alloys. Acta Mater. 1997, 45, 547–559.
- Ha, Y.S.; Kwon, J.B.; Yang, W.J.; Seo, J.K. Application of industrial 3D X-ray CT (computed tomography) to improve reliability of additive manufacturing technology. In Proceedings of the 34th International Ocean and Polar Engineering Conference, Rhodes, Greece, 16-21 June 2024.
- Clyne, T.W.; Wolf, M.; Kurz, W. The effect of melt composition on solidification cracking of steel, with particular reference to continuous casting. Metall. Trans. B 1982, 13B, 259–266.
- Li, Y.; Li, H.; Katgerman, L.; Du, Q.; Zhang, J. Recent advances in hot tearing during casting of aluminium alloys. Prog. Mater. Sci. 2021, 117, 100741.
- Dutta, B.; Pompe, O.; Rettenmayr, M. Quantitative image analysis for evaluation of eutectic fractions in as cast microstructures. Mater. Sci. Technol. 2004, 20, 1011–1018.
- Zhang, L.Y.; Jiang, Y.H.; Ma, Z.; Shan, S.F.; Jia, Y.Z.; Fan, C.Z.; Wang, W.K. Effect of cooling rate on solidified microstructure and mechanical properties of aluminium-A356 alloy. J. Mater. Process. Technol. 2008, 207, 107–111.
9. Copyright:
This material is Min-Seok Kim and Soonho Won's paper: Based on Development of Low-Pressure Die-Cast Al-Zn-Mg-Cu Alloy Propellers Part II: Simulations for Process Optimization.
Paper Source: https://doi.org/10.3390/ma17164027
This material was summarized based on the above paper, and unauthorized use for commercial purposes is prohibited.
Copyright © 2025 CASTMAN. All rights reserved.