This article introduces the paper "Development and application of magnesium alloy parts for automotive OEMs: A review".
1. Overview:
- Title: Development and application of magnesium alloy parts for automotive OEMs: A review
- Authors: Bo Liu, Jian Yang, Xiaoyu Zhang, Qin Yang, Jinsheng Zhang, Xiaoqing Li
- Publication Year: 2023
- Publishing Journal/Academic Society: Journal of Magnesium and Alloys
- Keywords: Magnesium alloy; Original equipment manufacturer; Automotive application; Development process.
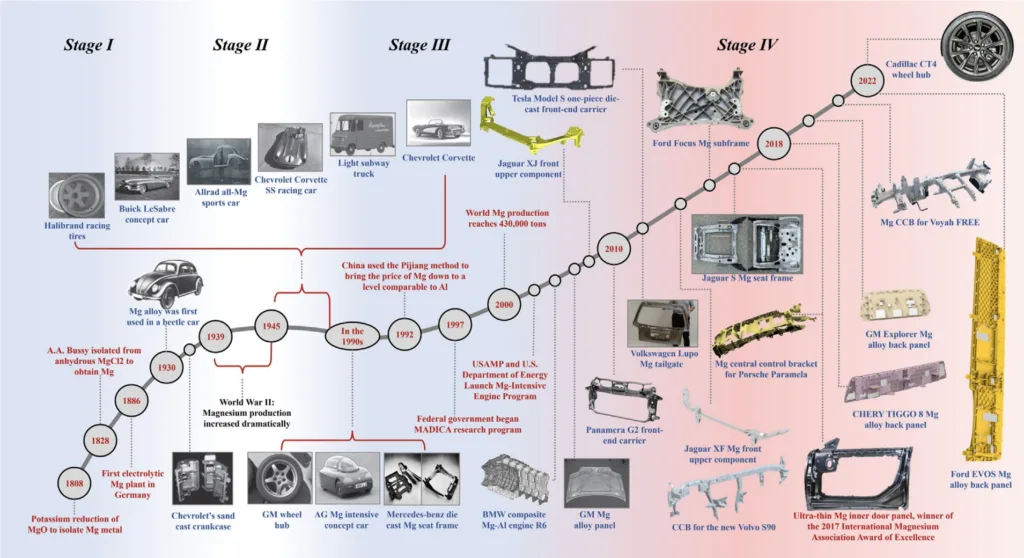
2. Research Background:
- Social/Academic Context of the Research Topic:
China is actively pursuing "energy conservation and emission reduction" and "dual carbon" strategies. Magnesium (Mg) alloy, being China's most resource-advantaged light metal, is increasingly used in automotive, rail, aerospace, medical, and electronics sectors. Extensive research on Mg alloy preparation, properties, and processes has been conducted by institutions like Chongqing University, Shanghai Jiaotong University, and Australian National University. Over the past two decades, Mg alloy usage in the automotive industry has grown. - Limitations of Existing Research:
Despite the increasing use, there's a scarcity of reports detailing the design and development of Mg alloy parts specifically for automobiles. Information on the complete development process and performance requirements for these parts is limited. - Necessity of the Research:
This review addresses the need to summarize application models and typical part examples of Mg alloy in vehicles, focusing on the four main systems: body, chassis, powertrain, and interior/exterior. It aims to introduce the development logic for reliable die-cast Mg alloy parts for Original Equipment Manufacturers (OEMs). The goal is to share methods, processes, and key considerations for automotive OEMs in developing Mg alloy parts, thereby boosting confidence and motivation for wider adoption in the automotive field. Finally, the paper aims to identify and discuss the challenges facing Mg alloy materials and potential solutions.
3. Research Purpose and Research Questions:
- Research Purpose:
The primary purpose of this review is to summarize the historical progression and recent advancements in the development of various Mg alloy series for automotive components. A critical analysis of existing literature is provided. Crucially, the paper aims to elucidate the entire process development technology route for die casting Mg alloy through real-world production cases. This is intended to enhance OEM confidence in developing new Mg parts and is deemed valuable for companies and manufacturers engaged in automotive lightweighting research. Furthermore, the review discusses the challenges facing Mg alloy materials in the context of national policies, environmental protection, energy saving, and consumer demands, and offers a future outlook. - Key Research Questions:
The research implicitly addresses questions such as:- What are the typical applications and models of Mg alloy parts within the four major automotive systems?
- What is the step-by-step development process for creating reliable die-cast Mg alloy components for automotive OEMs?
- What are the primary obstacles hindering the broader application of Mg alloys in the automotive sector?
- Research Hypotheses:
The underlying hypothesis is that by providing a comprehensive review of Mg alloy applications, coupled with detailed OEM case studies illustrating successful development processes, the review can significantly increase OEM confidence and drive greater adoption of Mg alloys in automotive manufacturing.
4. Research Methodology:
- Research Design:
This study employs a review-based research design, synthesizing information from existing literature and real-world case studies from automotive OEMs. - Data Collection Method:
The research relies on a comprehensive literature review of academic publications and industry reports related to magnesium alloys in automotive applications. It also incorporates case studies of actual OEM applications to illustrate the development process. - Analysis Method:
The analysis involves summarizing and critically analyzing existing literature. Case study analysis is used to understand the practical application and development process of Mg alloy parts in automotive manufacturing. - Research Subjects and Scope:
The scope of the review encompasses the application of different Mg alloy series in automotive components. It is structured around the four major vehicle systems: body, chassis, powertrain, and interior/exterior trim. The research specifically focuses on die casting as the primary manufacturing process and examines OEM case studies to detail the development technology route.
5. Main Research Results:
- Key Research Results:
The review successfully summarized application models and typical part examples of Mg alloy across the four major vehicle systems. Two OEM case studies were presented to illustrate the development logic for reliable die-cast Mg alloy components. The paper also identified and categorized the multiple challenges currently hindering the wider adoption of Mg alloys in the automotive industry and discussed potential solutions. - Statistical/Qualitative Analysis Results:
The paper presents quantitative data in the form of tables and figures, including:- Table 1: "Comparison of mechanical properties of Mg alloys." This table provides density, specific heat, thermal conductivity, melting temperature, tensile strength, yield limit, elongation rate, elastic modulus, and Brinell hardness for Mg, AZ91, AM50, AS41, AE42, and AISI8Cu3 alloys.
- Table 2: "Application areas of Mg alloy series in car body." This table lists Mg alloy series (AZ, AM, AS, AE, AXE and AJ), their performance advantages, specific classifications (e.g., AZ91D, AM60B), applications (e.g., central control bracket, seat frame), and die casting processes.
- Table 3: "Examples of Mg front-end carriers and front upper components of some models." This table details vehicle type, period, weight/kg, and provides images of parts and vehicle types for Jaguar XJ, Jaguar XF, Benz AMG GT, Lincoln MKT, Tesla Model S, NIO ES8, Range Rover, Porsche Panamera G2, and Changan ENDO EV460.
- Table 4: "Some cases of typical Mg CCB in automotive applications." This table lists vehicle type, weight/kg, CCB pictures, and vehicle type pictures for Rongwei 550, Ford Explorer, Dodge Caliber, LandRover LWB 5.0, LandRover LR3, ARCFOX-1(C11CB), Mercedes-Benz M-Class, Mini Cooper, Mercedes-Benz E-Class, and Voyah FREE.
- Table 5: "Strength and modal analysis results." This table presents results for various front cover lock stiffness, load limit, ultimate pull strength, strength, radiator system module mounting point stiffness, headlight bracket stiffness, modal analysis, and acceleration shock tests, indicating whether results are qualified or not.
- Table 6: "Mold flow analysis parameter setting." This table shows material temperature, mold temperature, pressure chamber length, material cake thickness, filling rate, critical speed, and high speed for three rounds of mold flow analysis.
- Weight reduction percentages are mentioned for specific parts, such as "43% less" for Aston Martin DB9 side door parts and "50%" weight reduction for Chrysler Pacifica tailgate.
- Data Interpretation:
The data presented and analyzed throughout the review consistently indicates that Mg alloys offer significant lightweighting potential in automotive applications. OEM case studies demonstrate the feasibility and benefits of using die-cast Mg alloy parts. However, the challenges related to cost, corrosion, and technological maturity remain significant hurdles to overcome for broader adoption. - Figure Name List:
- Fig. 1. Mg alloy in the development of automotive parts of the historical process.
- Fig. 2. Development and application of Mg alloys in car doors.
- Fig. 3. Development and application of Mg alloys in front-end carrier and front upper component.
- Fig. 4. Development and application of Mg alloy on roof, hood, and trunk lid.
- Fig. 5. The development and application of Mg alloy in the wheel.
- Fig. 6. The development and application of Mg alloy in the steering wheel.
- Fig. 7. The development and application of Mg alloy in subframe.
- Fig. 8. Mg alloy in powertrain applications.
- Fig. 9. Development and application of Mg alloy in oil pan.
- Fig. 10. Application of Mg alloy on seat frame.
- Fig. 11. Several applications of Mg alloy CCB.
- Fig. 12. Several applications of Mg alloy center bracket.
- Fig. 13. Some other Mg alloy parts for automobiles.
- Fig. 14. MASF full process analysis process and results.
- Fig. 15. MAFC full process analysis process and results.
- Fig. 16. MASF detailed development process.
- Fig. 17. MAFC detailed development process.
- Fig. 18. Mg alloy corrosion protection solutions.
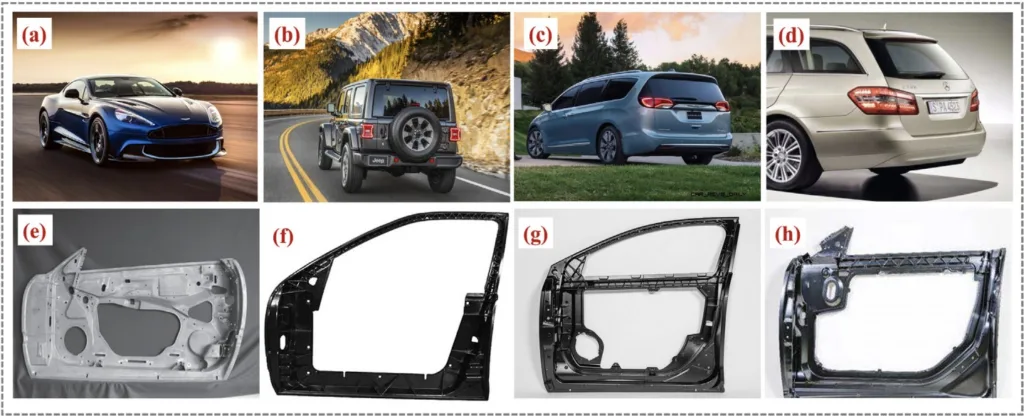
Mercedes-Benz E-Class T-Model featuring the hybrid Mg-Al hatch back; (e) Inner door frame of the Daimler-Chrysler SL Roadster; (f) Ford’s concept die-cast Mg door inner with an open architecture; (g) Integrated Mg die-cast door inner designed as part of a DOE sponsored project led by GMC; (h) Ultra-thin and ultra-light Mg alloy door inner.
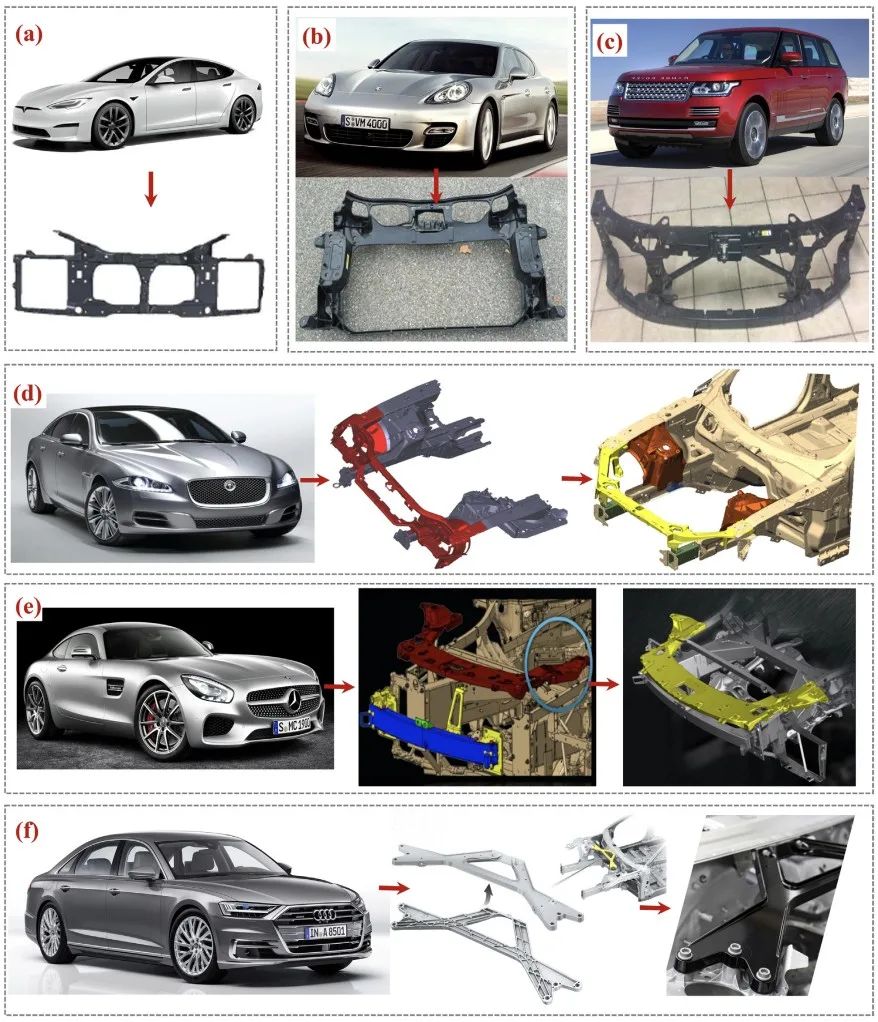
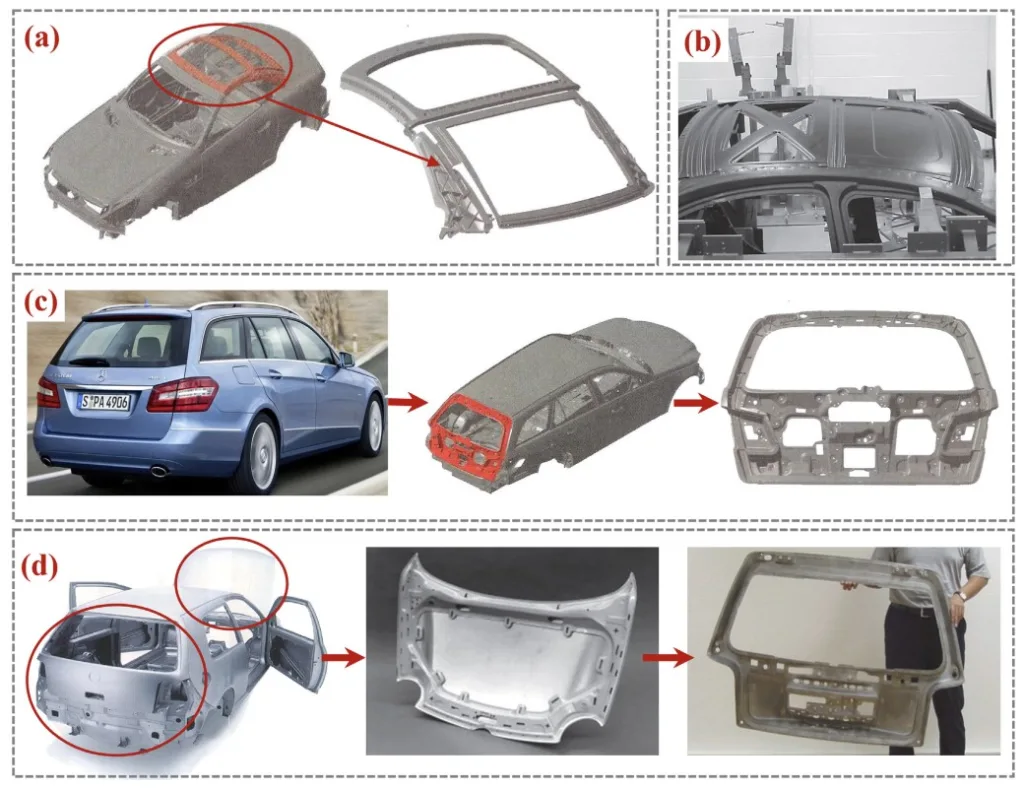
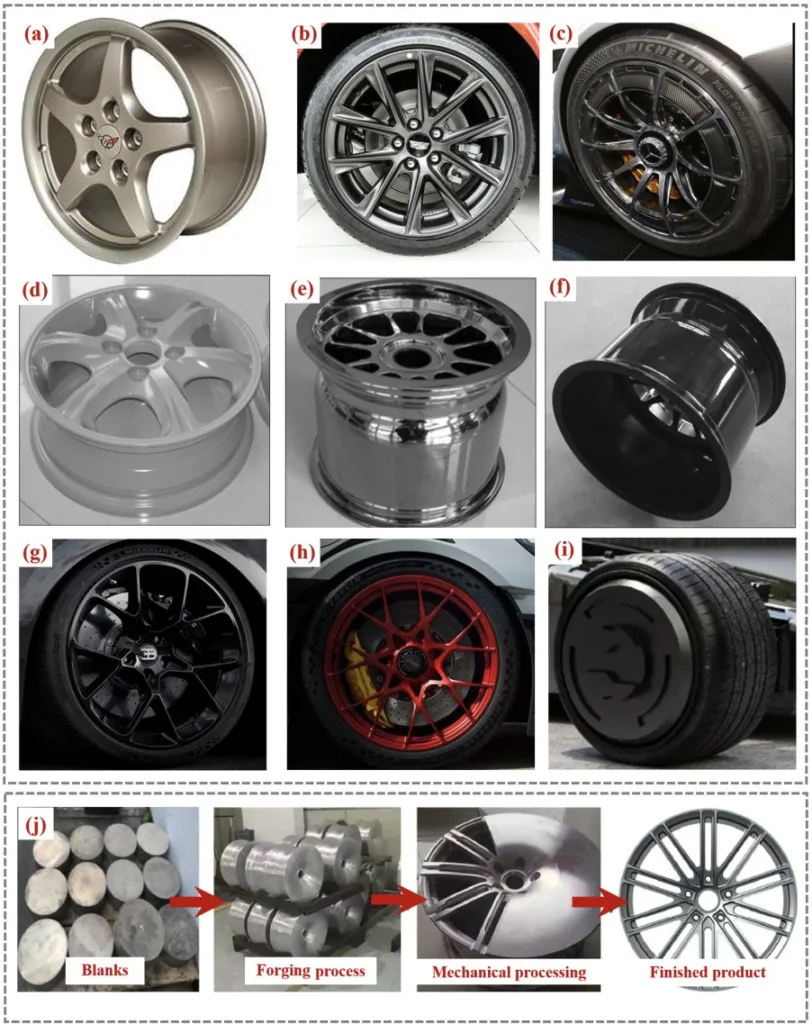
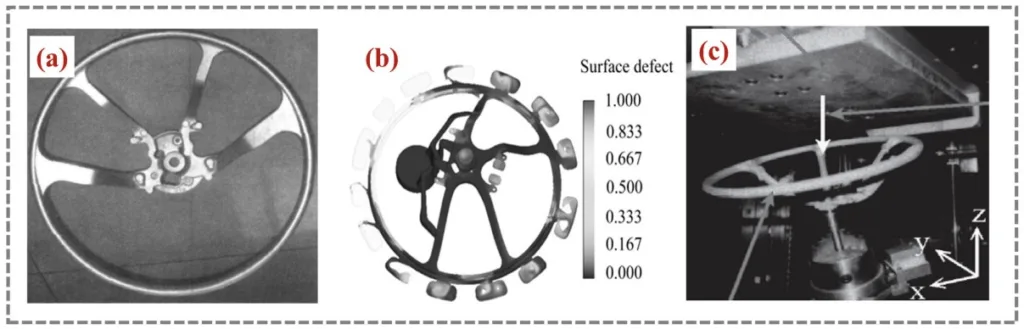
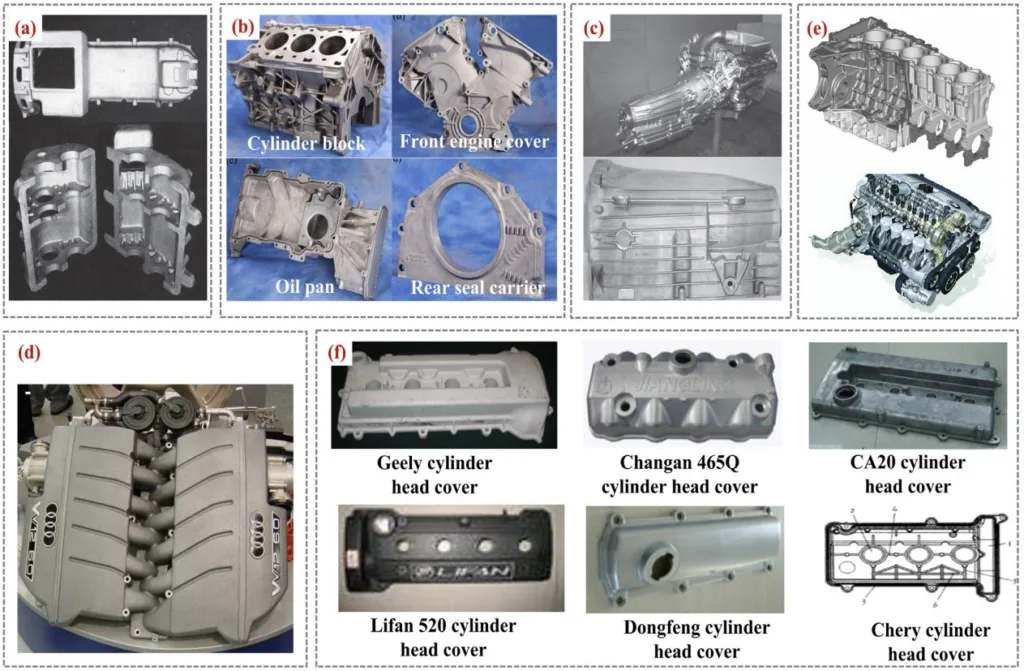
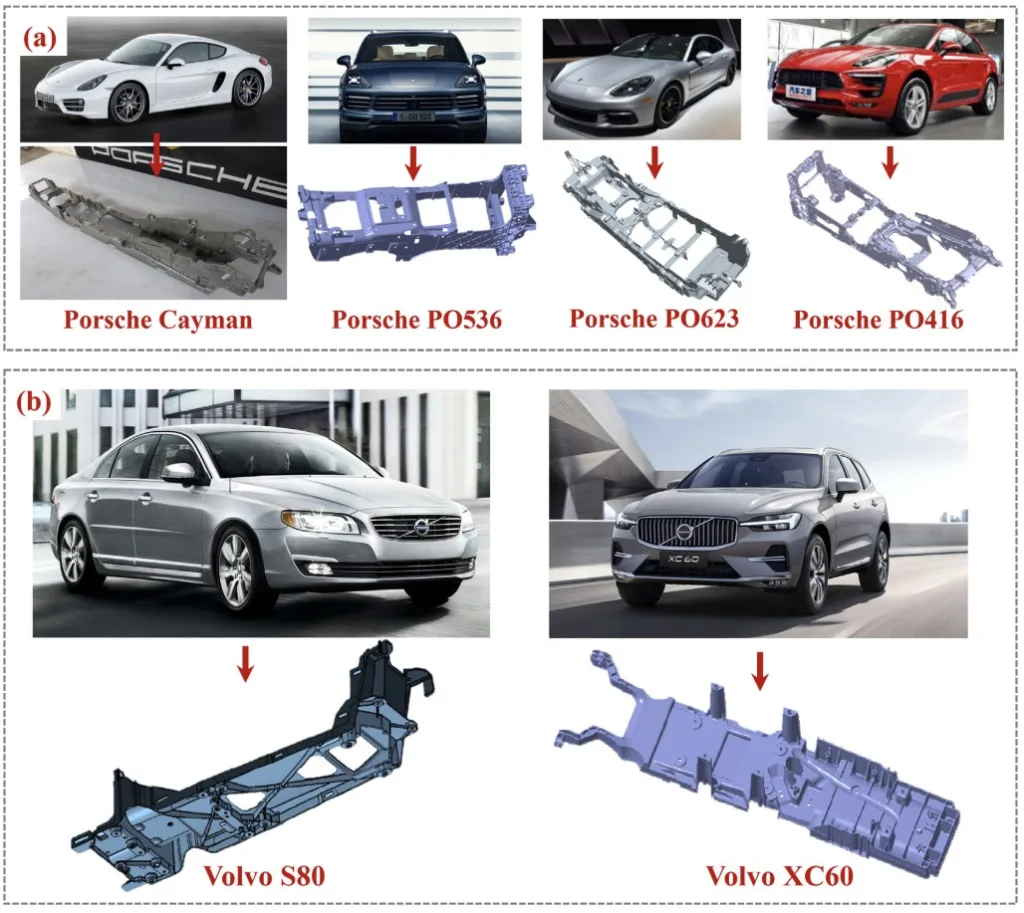
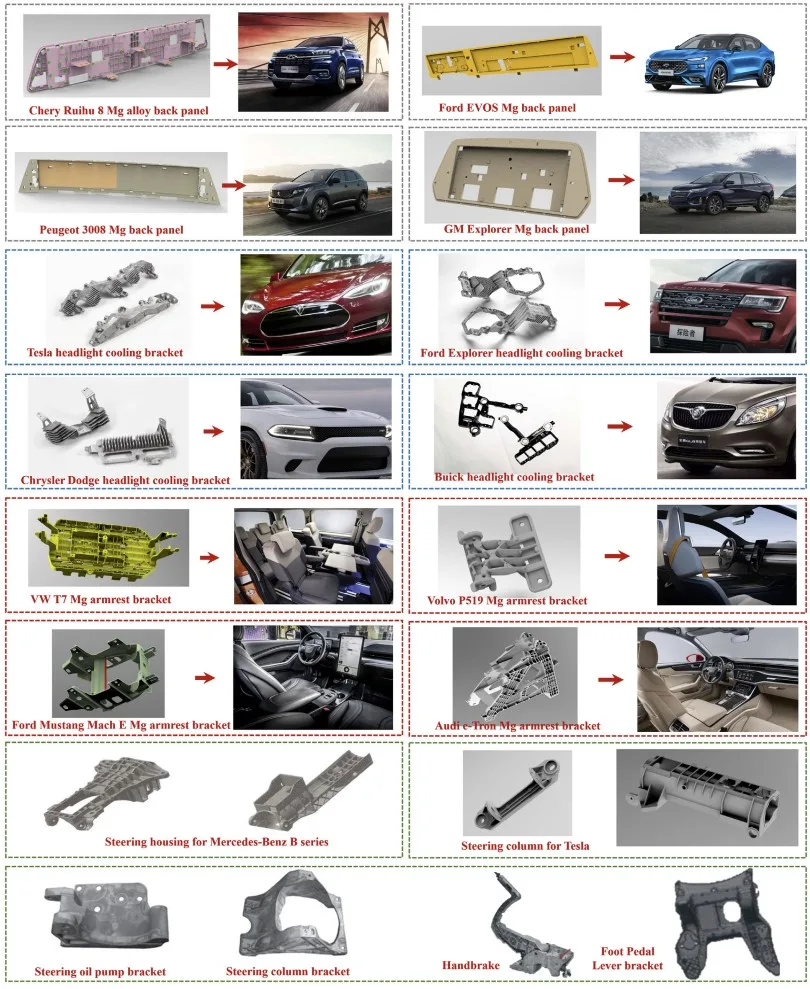
6. Conclusion and Discussion:
- Summary of Main Results:
The review concludes that Magnesium alloy has established itself as a valuable engineering material in the automotive industry due to its advantageous properties. The paper highlighted the development technology route for die casting Mg alloy through OEM production cases. It demonstrated the extensive range of Mg alloy applications in vehicles, aiming to boost OEM confidence in utilizing these materials for new component designs. The application of Mg alloy adheres to the principle of "right material in the right place," leveraging its light density and good fluidity while mitigating drawbacks like lower strength and corrosion susceptibility. The review identifies AM50/60 and AZ91D series Mg alloys as mainstream materials, with die casting being the most common molding process. Mg alloys are typically used in skeleton or bracket forms, rather than high load-bearing beam structures, and are applied in environments less prone to galvanic corrosion. Structural design and optimization are crucial for cost reduction. - Academic Significance of the Research:
This review provides a comprehensive and up-to-date overview of Mg alloy applications in the automotive sector. It offers valuable academic insights into the current state of research and development, serving as a reference point for future studies and a consolidated resource for researchers in the field. - Practical Implications:
The review has significant practical implications for automotive OEMs. By showcasing successful OEM case studies and detailing the development process, it aims to enhance OEM confidence in adopting Mg alloys for new part development. It provides a practical reference for developing Mg alloy components and highlights key challenges and opportunities for future innovation in automotive lightweighting. - Limitations of the Research:
The review's scope is primarily focused on die casting processes and OEM case studies. It may not comprehensively cover all possible Mg alloy applications in automobiles or explore other manufacturing techniques in detail.
7. Future Follow-up Research:
- Directions for Follow-up Research:
The paper suggests future research should explore:- Mg alloy additive manufacturing technologies.
- Hydrogen storage applications of Mg alloys.
- Development of a comprehensive Mg alloy material database and performance evaluation system.
- Addressing process and cost optimization for Mg alloy manufacturing.
- Overcoming technological innovation gaps and industrial structure contradictions.
- Areas Requiring Further Exploration:
Future research should focus on:- Developing novel Mg alloy structures and technologies to achieve further weight reduction in vehicles.
- Promoting green power electrolytic Mg technology for sustainable and recyclable Mg production.
- Strengthening collaboration between universities, governments, and research institutions to address global challenges in Mg alloy development and application.
8. References:
- [1] C. Moosbrugger, L. Marquard, Engineering Properties of Magnesium Alloys, ASM International, 2017.
- [2] F. Tong, X. Chen, S. Wei, et al., J. Magn. Alloys 9 (6) (2021) 1967-1976.
- [3] R. Li, Q. Liu, R. Zhang, et al., Energy Storage Mater. (2022).
- [4] S.H. Kang, D.W. Han, H.K. Kim, J. Magn. Alloys 8 (1) (2020) 241-251.
- [5] G. Ma, H. Xiao, J. Ye, et al., Mater. Sci. Technol. 36 (6) (2020) 645-653.
- [6] M.K. Kulekci, Int. J. Adv. Manuf. Technol. 39 (2008) 851-865.
- [7] G.L. Song, A. Atrens, Adv. Eng. Mater. 1 (1999) 11-33.
- [8] M. Grassel, M. Koch, South Dakota Med. 75 (5) (2022).
- [9] O. Myagmarjav, M. Zamengo, J. Ryu, et al., Appl. Therm. Eng. 91 (2015) 377-386.
- [10] Y. Yang, J. Zhang, B. Li, Ekoloji, 28 (107) (2019) 4827-4833.
- [11] J.S. Hoksbergen, M. Ramulu, P. Reinhall, et al., Appl. Compos. Mater. 16 (5) (2009) 263-283.
- [12] J.S. Binoj, N. Manikandan, P. Thejasree, et al., in: Investigations on Wire Electrical Discharge Machining of Magnesium Alloy AZ31B by Taguchi's Approach. Recent Advances in Materials and Modern Manufacturing, Springer, Singapore, 2022, pp. 923-931.
- [13] G. Sasaki, in: Material Mechanical Properties and Microstructure of Magnesium Alloy Matrix Composites Fabricated by Casting Process, 426, Materials Science Forum. Trans Tech Publications Ltd., Zurich-Uetikon, Switzerland, 2003, pp. 2015-2019.
- [14] Z.Q. Huang, H.Y. Lai, H.B. Zhou, et al., J. Min. Metall. B: Metall. 58 (1) (2022) 1-10.
- [15] N.P. Papenberg, S. Gneiger, I. Weissensteiner, et al., Materials (Basel) 13 (4) (2020) 985.
- [16] Z Zeng, M Salehi, A Kopp, et al., J. Magn. Alloys 10 (6) (2022) 1511-1541.
- [17] A.A Luo, J. Magn. Alloys 1 (1) (2013) 2-22.
- [18] T. Xu, Y. Yang, X. Peng, et al., J. Magn. Alloys 7 (3) (2019) 536-544.
- [19] J.A. Santamaría, J. Sertucha, A. Redondo, et al., Metals (Basel) 12 (4) (2022) 656.
- [20] F. D'Errico, D. Casari, La Metall. Ital. 36 (2022).
- [21] S.R. Golroudbary, I. Makarava, E. Repo, et al., Proc. CIRP 105 (2022) 589-594.
- [22] A.A Luo, Fundam. Magn. Alloy Metall. 266 (2013) 316.
- [23] S Prithivirajan, G M Naik, S Narendranath, et al., Int. J. Lightw. Mater. Manuf. 6 (1) (2023) 82-107.
- [24] A. Dziubińska, A. Gontarz, M. Dziubiński, et al., Adv. Sci. Technol. Res. J. 10 (31) (2016).
- [25] G.G. Wang, J.P Weiler, J. Magn. Alloys (2022).
- [26] Y. Yang, X. Xiong, J. Chen, et al., J. Magn. Alloys 9 (3) (2021) 705-747.
- [27] A.G Morachevskii, Russ. J. Appl. Chem. 92 (10) (2019) 1325-1335.
- [28] M.O. Pekguleryuz, A.A Kaya, Adv. Eng. Mater. 5 (12) (2003) 866-878.
- [29] J. Tan, S. Ramakrishna, Appl. Sci. 11 (15) (2021) 6861.
- [30] Alias J., Bakar N.F.A., Romzi M.A.F., et al. Development of Mg-Graphene composites and effect on microstructure and mechanical properties-a review. Enabling industry 4.0 through advances in manufacturing and materials, 2022: 139-149.
- [31] G.R Chapman, Min. Process. Extract. Metall. 111 (2) (2002) 49-52.
- [32] J. Li, B. Li, H. Shao, et al., Catalysts 8 (2) (2018) 89.
- [33] X. Tang, L. Guo, Q. Liu, et al., Cryst. Res. Technol. 50 (3) (2015) 203-209.
- [34] I. Kabdaşlı, A. Demirbilek, T. Ölmez, Fresenius Environ. Bull. 13 (10) (2004) 951-955.
- [35] MLQLH Guo, XQ B G F Ye, Z. Wu, Progr. Chem. 21 (11) (2009) 2358.
- [36] G. Long, P. Ma, M. Chu, in: Ammoniation Technology For Dehydration of Hydrated Magnesium Chloride in China, 488, Materials Science Forum. Trans Tech Publications Ltd, 2005, pp. 95-98.
- [37] F. Wang, J.J. Wang, Q.S. Li, et al., Adv. Mater. Sci. Eng. 2022 (2022).
- [38] D.B Zhao, in: The FEA Comparison of the Front Sub Frame in a Car between JDM2 Magnesium and steel. Applied Mechanics and Materials, 538, Trans Tech Publications Ltd, 2014, pp. 87-90.
- [39] R. Lu, K. Jiao, Y. Zhao, et al., Materials (Basel) 13 (20) (2020) 4654.
- [40] R. Senthilkumar, P. Ponnusamy, M. Prakash, SAE Int. J. Adv. Curr. Pract. Mob. 3 (2020) 831-835 (2020-28-0425).
- [41] Y.Z. Li, D.W. Fan, J.M Chen, Adv. Mat. Res. 211 (2011) 705-709.
- [42] J. Lyu, A. Lider, V. Kudiiarov, Metals (Basel) 9 (7) (2019) 768.
- [43] D.T. Nguyen, S.W. Song, J. Power Sources 368 (2017) 11-17.
- [44] J. Chen, L. Tan, X. Yu, et al., J. Mech. Behav. Biomed. Mater. 87 (2018) 68-79.
- [45] SAE J 465-1983, Magnesium Casting Alloys.
- [46] Pantelakis S.G., Alexopoulos N.D., Chamos A.N. Mechanical performance evaluation of cast magnesium alloys for automotive and aeronautical applications. 2007.
- [47] B.R. Powell, A.A. Luo, P.E Krajewski, Woodhead Publishing, 2012, pp. 150-209.
- [48] S. Ando, N. Harada, M. Tsushida, et al., Key Eng. Mater. 345 (2007) 101-104.
- [49] T. Li, J. Rao, J. Zheng, et al., J. Magn. Alloys 10 (6) (2022) 1581-1597.
- [50] D. Wenbo, Q. Yaling, Y. Zhenjie, et al., Rare Met. Mater. Eng. 38 (10) (2009) 1870-1875.
- [51] R.B. Figueiredo, M.T.P. Aguilar, P.R. Cetlin, et al., Processing magnesium alloys by severe plastic deformation. IOP conference series: materials science and engineering, 63, IOP Publishing, 2014.
- [52] S.S. Wu, J.W. Zhao, L. Wan, et al., in: Numerical Simulation of Mould Filling in Rheo-Diecasting Process of Semi-Solid Magnesium alloys. Solid State Phenomena, 116, Trans Tech Publications Ltd, 2006, pp. 554-557.
- [53] H. Yan, T. Wang, M.F Fu, Mater. Sci. Forum 575 (2008) 32-36.
- [54] F. Czerwinski, in: Selected Aspects of Semisolid Forming Magnesium alloys. Materials science Forum, 539, Trans Tech Publications Ltd, 2007, pp. 1644-1649.
- [55] F. Czerwinski, Materials (Basel) 14 (21) (2021) 6631.
- [56] Y. Zhang, Q. Zhu, C. Su, et al., Front. Chem. 10 (2022).
- [57] R. Kong, F. Xue, J. Wang, et al., Res. Policy 52 (2017) 19-28.
- [58] Y. Yu, Auto Manuf. Eng. 3 (11) (2020).
- [59] B.R. Powell, P.E. Krajewski, A.A Luo, Magnesium Alloys for Lightweight Powertrains and Automotive Structures, in: Materials, Design and Manufacturing for Lightweight Vehicles, Elsevier, Amsterdam, The Netherlands, 2021, pp. 125-186.
- [60] M.A Shand, The Chemistry and Technology of Magnesia, John Wiley & Sons, 2006.
- [61] D.A Kramer, Magnesium, its Alloys and Compounds, in: Magnesium, its Alloys and Compounds, 1, US Geological Survey Open-File Report, 2001, p. 341.
- [62] J. Durlach, in: Overview of Magnesium research: History and Current trends. New Perspectives in Magnesium Research, Springer, London, 2007, pp. 3-10.
- [63] B.J.C. Luthringer, F. Feyerabend, R. Willumeit-Römer, Magn. Res. 27 (4) (2014) 142-154.
- [64] B.B Clow, in: History of Primary Magnesium Since World War II. Essential Readings in Magnesium Technology, Springer, Cham, 2016, pp. 85-87.
- [65] USAMP teamMagnesium Vision 2020: A North American Automotive Strategic Vision For Magnesium, USCAR, 2006.
- [66] C. Blawert, N. Hort, K.U Kainer, Trans. Indian Inst. Met 57 (4) (2004) 397-408.
- [67] T.K. Aune, H. Westengen, T. Ruden, SAE Trans. (1994) 553-557.
- [68] Hawke D., Gaw K. Effects of chemical surface treatments on the performance of an automotive paint system on die cast magnesium. SAE Technical Paper, 1992.
- [69] G.D. Tong, H.F. Liu, Y.H Liu, Trans. Nonferrous Met. Soc. China 20 (2010) s336-s340.
- [70] R. Seetharaman, B. Lavanya, N. Niharika, et al., Mater. Today: Proc. 4 (6) (2017) 6743-6749.
- [71] Y.G. Liu, Z.H. Huang, H. Ding, et al., Key Eng. Mater. 353 (2007) 1614-1616.
- [72] Jacques R.P., DasGupta R., Shearouse J.D. Hot chamber diecasting of magnesium alloy AM50A for automotive interior structural components. SAE Technical Paper, 1996.
- [73] Grebetz J.C. A comparison of the impact characteristics of several magnesium die casting alloys. SAE Technical Paper, 1993.
- [74] J. Jekl, J. Auld, C. Sweet, et al., Development of a Thin-Wall Magnesium Side Door Inner Panel for Automobiles, General Motors LLC, Detroit, MI (United States), 2015.
- [75] Murray R.W., Hillis J.E. Magnesium finishing: chemical treatment and coating practices. 1990.
- [76] S. Annamalai, S. Periyakgoundar, K. Paramasivam, et al., Adv. Mater. Sci. Eng. 2020 (2020).
- [77] Durairaj S.R.N., Ganesan T., Rao P.C. Vibration analysis on magnesium alloy housing and analysis of resonant frequency on the housing between magnesium and aluminium alloy. SAE Technical Paper, 2017.
- [78] Luo A.A., Forsmark J., Sun X., et al. Mechanical and thermophysical properties of magnesium alloy extrusions. SAE Technical Paper, 2010.
- [79] Verma R., Carter J.T. Quick plastic forming of a decklid inner panel with commercial AZ31 magnesium sheet. SAE Technical Paper, 2006.
- [80] Kim S.W., Lee Y.S. Warm forming of 3t Mg alloy sheet for an automotive electronic compressor case. SAE Technical Paper, 2014.
- [81] Aune T.K., Westengen H., Ruden T. Mechanical properties of energy absorbing magnesium alloys. SAE Technical Paper, 1993.
- [82] S.V. Galatanu, M. Scano, D. Pietras, et al., Proc. Struct. Integr. 26 (2020) 269-276.
- [83] Effect of Section Thicknesses On Tensile Behavior and Microstructure of High Pressure Die Cast Magnesium Alloy AM50. Pacific Rim International Conference On Advanced Materials and Processing (PRICM 5) pt.1. Dept. of Mechanical, Automotive & Materials Engineering University of Windsor Windsor, Ontario, Canada, 2005 N9B 3P4; Manufacturing System Department, Ford Research Laboratory, Ford Motor Company, Dearborn, MI, USA 48121; Dept. of Mechanical, Automotive & Material.
- [84] H. Alves, U. Koster, E. Aghion, et al., Mater. Technol. 16 (2) (2001) 110-126.
- [85] Sadayappan K., Vassos M. Evaluation of a thixomolded magnesium alloy component for automotive application. SAE Technical Paper, 2010.
- [86] Hubbert T., Chen X., Li N., et al. 2005 Ford GT magnesium I/P structure. SAE Technical Paper, 2004.
- [87] S. Kim, H. Yoo, Y. Kim, Magn. Technol. (2002).
- [88] Y.Q. Ma, R. Chen, E.H Han, Mater. Sci. Forum 488 (2005) 265-268.
- [89] Gerken R.T., Ghaffari B., Sachdev A.K., et al. Low-cost magnesium alloy sheet component development and demonstration project. SAE Technical Paper, 2022.
- [90] M.O. Pekguleryuz, E. Baril, in: Development of Creep Resistant Mg-Al-Sr alloys. Essential readings in Magnesium Technology, Springer, Cham, 2016, pp. 283-289.
- [91] H. Westengen, P. Bakke, Mater. Sci. Forum. 419 (2003) 35-42.
- [92] M.A. Easton, S. Zhu, T.B. Abbott, et al., Adv. Eng. Mater. 18 (6) (2016) 953-962.
- [93] S. Gavras, S. Zhu, M.A. Easton, et al., Front. Mater. 6 (2019) 262.
- [94] Y. Xue, M.F. Horstemeyer, D.L. McDowell, et al., Int. J. Fatigue 29 (4) (2007) 666-676.
- [95] D. Argo, M. Lefebvre, Melt protection for the AJ 52 magnesium strontium alloy, in: Magnesium Technology 2003 as held at the 2003 TMS Annual Meeting, 2003, pp. 15-21.
- [96] Burns J., Han L., Hu H., et al. Effects of section thicknesses on tensile properties of permanent mould cast magnesium alloy AJ 62. Minerals, metals and materials society/AIME, 420 Commonwealth Dr., P. O. Box 430 Warrendale PA 15086 USA. [np]. 14-18 Feb, 2010.
- [97] Blanchard P.J., Bretz G.T., Subramanian S., et al. The application of magnesium die casting to vehicle closures. SAE Technical Paper, 2005.
- [98] L. Riopelle, Magnesium Applications, in: International Magnesium Association (IMA) Annual Magnesium in Automotive Seminar, April 20, 2004 Livonia, MI.
- [99] Eng L. An assessment of mass reduction opportunities for a 2017-2020 model year vehicle program. 2010.
- [100] Aston Martin global website, 2018.
- [101] Daimler Global Media, media.daimler.com, 2017.
- [102] FCA North America media, media.fcanorthamerica.com, 2017.
- [103] S. Gibbs, Metal Casting Design and Purchasing (July/August 2010) 29e33.
- [104] IMA, Magn. Showcase 12 (2010) 2.
- [105] J.P Weiler, Next generation magnesium liftgate-utilizing advanced technologies to maximum ass reduction in a high volume vehicle application. International magnesium association's 73rd annual world magnesium conference, 2016.
- [106] Blawert C., Heitmann V., Hche D., et al. Design of hybrid Mg/Al components for the automotive body-Preventing general and galvanic corrosion. ibekor com, 2011.
- [107] J.P Weiler, J. Magn. Alloys 7 (2) (2019) 297-304.
- [108] Balzer J.S., Dellock P.K., Maj M.H., et al. Structural magnesium front end support assembly. SAE Technical Paper, 2003.
- [109] A.A. Luo, R.C. McCune, Magnesium Front End Projects, V.S. Department of Energy, Automotive Lightweighting Materials, FY, 2008 2006 Progress Report, TMS 2008.
- [110] C. Blawert, N. Hort, K.U Kainer, Trans.- Indian Inst. Met. 57 (4) (2004) 397-408.
- [111] S. Logan, A. Kizyma, C. Patterson, et al., SAE Trans. (2006) 469-486.
- [112] F. Moll, M. Mekkaoui, S. Schumann, et al., Application of Mg sheets in car body structures, in: Magnesium: Proceedings of the 6th International Conference Magnesium Alloys and Their Applications, Wiley-VCH Verlag GmbH & Co. KGaA, Weinheim, FRG, 2003, pp. 936-942.
- [113] J.T. Carter, P.E. Krajewski, R. Verma, JOM 60 (11) (2008) 77-81.
- [114] Reuters, G.M. Tests magnesium sheet metal to make cars lighter, Oct. 2012.
- [115] A.A. Luo, A.K. Sachdev, B.R Powell, China Foundry 7 (4) (2010) 463-469.
- [116] A.K. Rodriguez, G. Ayoub, G. Kridli, et al., Phys. Proc. 55 (2014) 46-52.
- [117] W.H. Zhu, Z.X. Zheng, J.Z. Feng, et al., Adv. Mater. Res. 118 (2010) 930-934.
- [118] M. Gobbi, G. MASTINU, F. Ballo, et al., SAE Int. J. Passeng. Cars-Mech. Syst. 8 (1) (2015) 119-127.
- [119] M. Graf, M. Ullmann, R. Kawalla, Proc. Eng. 81 (2014) 546-551.
- [120] Wang J., Chen H. A preparation method for wheel hub production by positive and negative extrusion: CN102581053A. 2012.
- [121] P.H. Fu, L.M. Peng, W.J. Ding, Chin. J. Eng. Sci. 20 (1) (2018) 84-89.
- [122] Y.H. Peng, D.Y. Li, Y.C. Wang, et al., Mater. Sci. Forum. 488 (2005) 393-396.
- [123] R. Shang, W. Altenhof, H. Hu, et al., SAE Int. J. Mater. Manuf. 1 (1) (2009) 9-15.
- [124] G.F. Quan, S.D Liu, Ordnance Mater. Sci. Eng. 35 (04) (2012) 26-31.
- [125] W. Qiang, Z. Zhang, X. Zhang, et al., Trans. Nonferrous Met. Soc. China 20 (2010) s599-s603.
- [126] W. Qiang, Z.M. Zhang, X. Zhang, et al., Trans. Nonferrous Met. Soc. China 18 (2008) s205-s208.
- [127] Nayak S., Garg A.K., Chaturvedi M., et al. Performance evaluation of PU over-molded thermoplastic steering wheel. SAE Technical Paper, 2010.
- [128] Garg A., Surisetty G., Chaturvedi M., et al. High performance thermoplastic steering wheel. SAE Technical Paper, 2009.
- [129] W. Ames, W. Altenhof, SAE Trans. (2000) 390-399.
- [130] P.L. Mao, L.I.U. Zheng, C.Y. Wang, et al., Trans. Nonferrous Met. Soc. China 18 (2008) s218-s222.
- [131] D.Y Kwak, A study on performance evaluation and improvement of steering wheel with Mg die casting core, in: Transactions of Korean Society of Automotive Engineers Annual Autumn Conference, 2003, pp. 1185-1190.
- [132] W.J. Altenhof, W. Ames, P.R. Frise, et al., Int. J. Crashworth. 8 (3) (2003) 237-246.
- [133] J. Liao, Adv. Mat. Res. 328 (2011) 213-219.
- [134] K.J. Kim, H.J. Kim, C.Y Jeong, Mater. Res. Innov. 18 (sup2) (2014) S2-666-S2-672.
- [135] Wickberg A., Ericsson R. Magnesium in the Volvo LCP 2000. SAE Technical Paper, 1985.
- [136] Aragones J., Goundan K., Kolp S., et al. Development of the 2006 Corvette Z06 structural cast magnesium crossmember. SAE Technical Paper, 2005.
- [137] N. Li, R. Osborne, B. Cox, et al., SAE Trans. (2005) 79–88.
- [138] Chen X., Wagner D., Heath G., et al. Cast magnesium subframe development-bolt load retention. SAE Technical Paper, 2021.
- [139] H. Friedrich, S. Schumann, J. Mater. Process. Technol. 117 (3) (2001) 276-281.
- [140] F.H. Froes, D. Eliezer, E. Aghion, JOM 50 (9) (1998) 30-34.
- [141] B.R. Powell, Magnesium Powertrain Cast Components, U.S. Department of Energy, Washington, D.C, April 2009 Published in FY2008 Annual Progress Report for Automotive Lightweighting Materials.
- [142] B.R. Powell, L.J. Ouimet, J.E. Allison, et al., SAE Trans. (2004) 250-259.
- [143] J. Greiner, C. Doerr, H. Nauerz, et al., Comfort Fuel Econ. SAE Trans. (2004) 283-293.
- [144] Bavarian Motor Works (2007) Magnesium fosters rebirth of an automotive engine. International magnesium association: the global voice for magnesium (May):1-3.
- [145] Hoeschl M., Wagener W., Wolf J. BMW's magnesium-aluminium composite crankcase, state-of-the-art light metal casting and manufacturing. SAE Technical Paper, 2006.
- [146] H.W. Shin, Y.J Chung, Trans. Korean Soc. Autom. Eng. 17 (2) (2009) 141-149.
- [147] H.W. Shin, Int. J. Precis. Eng. Manuf. 13 (11) (2012) 2011–2016.
- [148] M. Pekguleryuz, P. Labelle, D. Argo, Magnesium die casting alloy AJ62x with superior creep resistance, ductility and die castability, SAE 2003 World Congress & Exhibition, 2001 2003-01-0190.
- [149] Hines J.A., McCune R.C., Allison J.E., et al. The USAMP magnesium powertrain cast components project. SAE Technical Paper, 2006.
- [150] S. Mantovani, G.A. Campo, A. Ferrari, Proc. Inst. Mech. Eng., Part C: J. Mech. Eng. Sci. 235 (10) (2021) 1703-1723.
- [151] Y. Kuwano, Y. Sakamoto, A. Uno, et al., Honda R D Tech. Rev. 20 (1) (2008) 46.
- [152] S.F. Wang, W.W. Hu, Z.H. Gao, et al., The application of magnesium alloy in automotive seat design, in: Applied Mechanics and Materials, 395, Trans Tech Publications Ltd, 2013, pp. 266-270.
- [153] J.M Willekens, Magnesium seat-frames: history and evaluation, in: Proceedings of the Third International Magnesium Conference, 1996, pp. 207-211.
- [154] Sikora S.P., Beeh E., Jäger A., et al. Concepts for manufacturing a seat backrest structure dominated by an extruded magnesium alloy. SAE Technical Paper, 2021.
- [155] Abate M., Willman M. Use of cast magnesium back frames in automotive seating. SAE Technical Paper, 2005.
- [156] Hector B., Heiss W. Magnesium die-castings as structural members in the integral seat of the new mercedes-benz roadster. SAE Technical Paper, 1990.
- [157] P. Koltun, A. Tharumarajah, Mater. Sci. Forum 618 (2009) 17-20.
- [158] B. Liu, Z.C. Qiu, Q. Yang, et al., Mater. Sci. Forum 877 (2017) 668-673.
- [159] W.J. Joost, P.E Krajewski, Scr. Mater. 128 (2017) 107-112.
- [160] I.J Polmear, Mater. Sci. Technol. 10 (1) (1994) 1-16.
- [161] E. Baril, P. Labelle, M. Pekguleryuz, JOM 55 (11) (2003) 34-39.
- [162] E. Aghion, B. Bronfin, F. Von Buch, et al., JOM 55 (11) (2003) 30-33.
- [163] S. Novotny, M. Geiger, J. Mater. Process. Technol. 138 (1-3) (2003) 594-599.
- [164] Liu B., Zhan Z., Zhao X., et al. A research on the body-in-white (BIW) weight reduction at the conceptual design phase. SAE Technical Paper, 2014.
- [165] B. Liu, J. Yang, Z. Zhan, et al., SAE Int. J. Mater. Manuf. 8 (3) (2015) 616-622.
- [166] B. Liu, C. Yan, H. Wang, Proc. Inst. Mech. Eng., Part B: J. Eng. Manuf. 234 (3) (2020) 621-628.
- [167] Y.K. Gao, D.W. Gao, Y.H Gao, Adv. Mat. Res. 156 (2011) 245-251.
- [168] S. Chandra, M. Maeder, J. Bienert, et al., Mech. Syst. Signal. Process. 187 (2023) 109945.
- [169] G. Dao, S. Youhong, L. Guanyu, et al., Mech. Syst. Signal. Process. 185 (2023) 109768.
- [170] G.G. Wang, J. Bos, J. Magn. Alloys 6 (2) (2018) 114-120.
- [171] M.H. Yoo, J.H. Song, J.H. Oh, et al., Robot Comput. Integr. Manuf. 55 (2019) 154-159.
- [172] B. Liu, P. Liu, Z.T Zhu, Adv. Mater. Res. 1063 (2015) 207-210.
- [173] G. Li, W. Jiang, Z. Fan, et al., Int. J. Adv. Manuf. Technol. 91 (1) (2017) 1355-1368.
- [174] B. Dybowski, R. Jarosz, A. Kiełbus, Solid State Phenom. 197 (2013) 125-130.
- [175] Y.K. Shen, J.J. Liu, C.T. Chang, et al., Int. Commun. Heat Mass Transf. 29 (1) (2002) 97-105.
- [176] L. Bichler, C. Ravindran, Mater. Sci. Forum. 638 (2010) 1591-1595.
- [177] F.W. Bach, M. Rodman, A. Rossberg, Adv. Mater. Res. 6 (2005) 665-672.
- [178] K. Strobel, M.A. Easton, V. Tyagi, et al., Int. J. Cast Met. Res. 23 (2) (2010) 81-91.
- [179] S. Das, A. Dubreuil, L. Bushi, et al., A Life Cycle Assessment of a Magnesium Automotive Front End, Oak Ridge National Lab. (ORNL), Oak Ridge, TN (United States), 2009.
- [180] S.V.S. Prasad, S.B. Prasad, K. Verma, et al., J. Magn. Alloys (2021).
- [181] H. Haferkamp, R. Boehm, U. Holzkamp, et al., Mater. Trans. 42 (7) (2001) 1160-1166.
- [182] P.S. Sreejith, B.K.A Ngoi, J. Mater. Process. Technol. 101 (1-3) (2000) 287-291.
- [183] S. Agarwal, J. Curtin, B. Duffy, et al., Mater. Sci. Eng.: C 68 (2016) 948-963.
- [184] K.S. Tseng, G.L. Sheu, S.T Huang, Mater. Sci. Forum. 488 (2005) 49-52.
- [185] J. Song, J. She, D. Chen, et al., J. Magn. Alloys 8 (1) (2020) 1-41.
- [186] R. Shah, V. Mittal, E. Matsil, et al., Adv. Mech. Eng. 13 (3) (2021) 16878140211003398.
9. Copyright:
- This material is Bo Liu, Jian Yang, Xiaoyu Zhang, Qin Yang, Jinsheng Zhang, Xiaoqing Li's paper: Based on Development and application of magnesium alloy parts for automotive OEMs: A review.
- Paper Source: https://doi.org/10.1016/j.jma.2022.12.015
This material was summarized based on the above paper, and unauthorized use for commercial purposes is prohibited.
Copyright © 2025 CASTMAN. All rights reserved.