This article introduces the paper ['Determination of interfacial heat transfer coefficient and its application in high pressure die casting process'] published by ['CHINA FOUNDRY'].
1. Overview:
- Title: Determination of interfacial heat transfer coefficient and its application in high pressure die casting process
- Author: Cao Yongyou, Guo Zhipeng, and Xiong Shoumei
- Publication Year: 2014
- Publishing Journal/Academic Society: CHINA FOUNDRY
- Keywords: high pressure die casting; interfacial heat transfer coefficient; inverse method
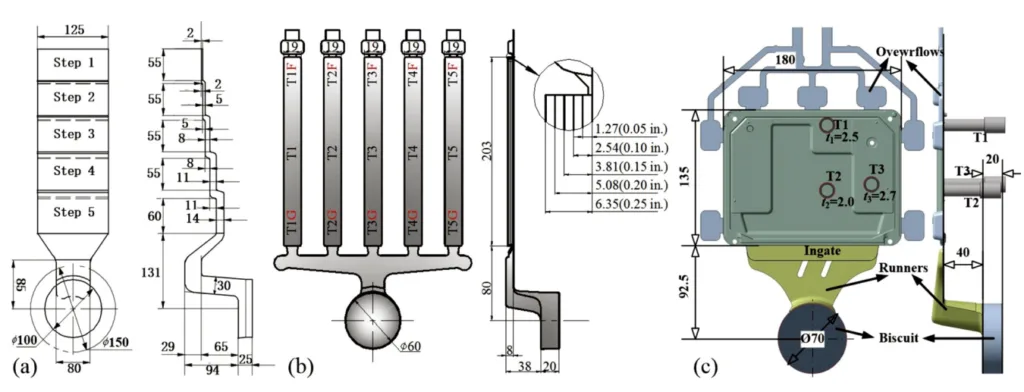
2. Abstracts or Introduction
In this paper, the research progress of the interfacial heat transfer in high pressure die casting (HPDC) is reviewed. Results including determination of the interfacial heat transfer coefficient (IHTC), influence of casting thickness, process parameters and casting alloys on the IHTC are summarized and discussed. A thermal boundary condition model was developed based on the two correlations: (a) IHTC and casting solid fraction and (b) IHTC peak value and initial die surface temperature. The boundary model was then applied during the determination of the temperature field in HPDC and excellent agreement was found.
3. Research Background:
Background of the Research Topic:
High pressure die casting (HPDC) is a net shape process for producing thin wall components. Numerical simulation is important to predict mold filling, solidification, and temperature distribution in the die. The interfacial heat transfer coefficient (IHTC) is a critical parameter characterizing heat transfer behavior at the metal-mold interface during solidification in computer simulations. Determination and application of IHTC are key issues for researchers.
Status of Existing Research:
Existing methods to determine IHTC are categorized into: (1) Purely analytical approaches, (2) Semi-analytical approaches based on empirical correlations, and (3) Numerical approaches. Purely analytical and semi-analytical approaches assume a constant IHTC, which is a significant limitation. Numerical approaches, especially inverse heat conduction problems (IHCP), offer a more complete exploration of heat flux history across the interface. Previous studies have investigated IHTC in HPDC since the 1970s, but temperature measurement remains a difficult task, and improper thermocouple installation can lead to uncertainties.
Necessity of the Research:
Accurate determination of IHTC in HPDC is crucial for improving the accuracy of numerical simulations, which are essential for optimizing casting processes and product development. The transient nature of heat transfer in HPDC and the difficulties in direct measurement necessitate further research into robust methods for IHTC determination and application in process modeling.
4. Research Purpose and Research Questions:
Research Purpose:
This paper aims to review the research progress in determining the interfacial heat transfer coefficient (IHTC) in high pressure die casting (HPDC) and to present a thermal boundary condition model based on experimental findings from the Tsinghua Group.
Key Research:
- Review of existing methods for IHTC determination in HPDC (analytical, semi-analytical, numerical).
- Summarization of factors influencing IHTC, including casting thickness, process parameters, and casting alloys.
- Development of a thermal boundary condition model based on correlations between IHTC and casting solid fraction, and IHTC peak value and initial die surface temperature.
- Application of the developed boundary model to determine temperature field in HPDC and validation against experimental results.
Research Hypotheses:
While not explicitly stated as hypotheses, the research is based on the premise that:
- IHTC in HPDC is not constant and varies during solidification.
- Numerical methods, particularly IHCP, are necessary for accurate IHTC determination.
- IHTC is influenced by casting thickness, process parameters (shot velocity, die temperature, pressure), and casting alloy.
- A thermal boundary condition model based on IHTC correlations can accurately predict temperature fields in HPDC simulations.
5. Research Methodology
Research Design:
This paper is primarily a review paper, summarizing existing literature and the authors' own research. It incorporates experimental findings from die casting experiments conducted by the Tsinghua Group to support the development and validation of a thermal boundary condition model.
Data Collection Method:
The paper reviews experimental data from previous studies by the authors and other researchers. The Tsinghua Group's experiments utilized specially designed "step-shape", "finger-shape", and "cover-plate" castings (Fig. 1). Temperature measurements were taken using special temperature sensor units (TSU) at 1, 3, and 6 mm from the die-casting interface.
Analysis Method:
The paper discusses various analytical, semi-analytical, and numerical methods for IHTC determination. The Tsinghua Group employed inverse methods to evaluate heat transfer coefficients. Correlation analysis and regression methods were used to establish relationships between IHTC, process parameters, casting solid fraction, and die surface temperature.
Research Subjects and Scope:
The research focuses on interfacial heat transfer in high pressure die casting (HPDC). The scope includes:
- Review of literature on IHTC determination methods in HPDC.
- Experimental studies using aluminum alloys (ADC12, AM50, AM60B, B390) in HPDC.
- Investigation of the influence of casting thickness, process parameters (shot velocity, die temperature, pressure), and casting alloys on IHTC.
- Development and application of a thermal boundary condition model for HPDC simulations.
6. Main Research Results:
Key Research Results:
- IHTC Determination Methods: Review of purely analytical, semi-analytical, and numerical (inverse method) approaches for determining IHTC. Numerical methods, especially IHCP, are highlighted as more effective for capturing transient heat transfer.
- Factors Influencing IHTC: Summarized the influence of casting thickness, process parameters (shot velocity, initial die temperature, pressure), and casting alloys (ADC12, AM50, AM60B, B390) on IHTC. Fast shot velocity and initial die temperature were found to have prominent influence. The influence of pressure is contested and depends on casting thickness.
- IHTC Evolution Stages: Identified four stages in IHTC evolution during HPDC: initial increasing stage, high value maintained stage, fast decreasing stage, and low value maintained stage.
- Thermal Boundary Condition Model: Developed a thermal boundary condition model based on two correlations: (a) IHTC and casting solid fraction, and (b) IHTC peak value and initial die surface temperature. The model is described by equations for each of the four IHTC evolution stages (Fig. 6).
- (i) h = hmax, before and during the initial increasing stage;
- (ii) h = hmax - fs / fsF ×(hmax - ho), high value maintaining stage;
- (iii) h = ho+khf ×(1-fs)ε, fast decreasing stage;
- (iv) h = ho, low value stage.
- Model Validation: The developed boundary condition model was applied to simulate the temperature field and thermal equilibrium of a cover-plate casting, showing excellent agreement with experimental results (Figs. 7 and 8).
Analysis of presented data:
- IHTC Profiles (Fig. 2): IHTC increases rapidly after shot, reaches a maximum, maintains a high level, and then decreases sharply. ADC12 alloy exhibits higher IHTC than AM50. Thinner steps show slimmer IHTC profiles.
- Influence of Initial Die Temperature (Fig. 3, 4, 5): IHTC peak value (hmax) generally decreases with increasing initial die surface temperature (ODI). Correlation analysis revealed relationships between ln(hmax/ODI²) and ln(ODI) (Equations 4 and 5).
- Model Application (Figs. 7, 8): Simulations using the developed thermal boundary condition model accurately predicted casting and die surface temperature changes during a casting cycle, demonstrating the model's ability to capture the transient heat transfer behavior in HPDC.
Figure Name List:
- Fig. 1: Configuration of (a) step-shape casting, (b) finger-shape casting, and (c) cover-plate casting
- Fig. 2: Calculated heat transfer coefficient profiles at steps 1-5 for AM50 and ADC12 alloys
- Fig. 3: Calculated IHTC peaks as a function of initial die temperature of steps 1 to 5 for AM50 and ADC12 alloys [24]
- Fig. 4: Calculated IHTC peaks as a function of initial die temperature of finger-shape casting for B390 alloy [8]
- Fig. 5: Calculated IHTC peaks as a function of initial die temperature of cover-plate casting for AM60B alloy [7]
- Fig. 6: Four stages of heat transfer coefficient for thermal boundary condition model
- Fig. 7: Casting surface temperature changes during one cycle of cover-plate casting
- Fig. 8: Die surface temperature changes during one cycle of cover-plate casting
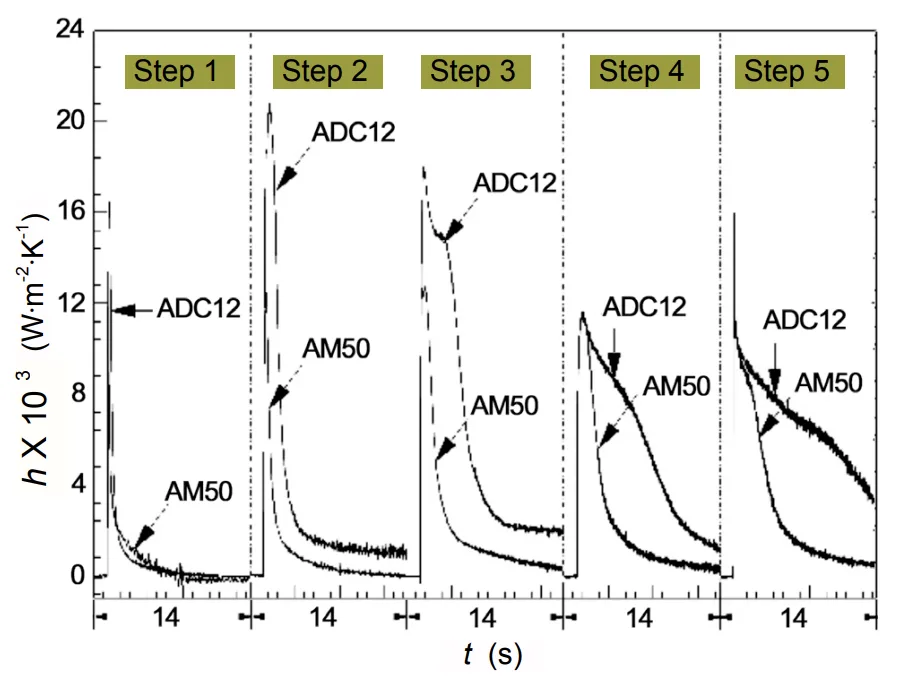
![Fig. 3: Calculated IHTC peaks as a function of initial die temperature of steps 1 to 5 for AM50 and ADC12 alloys [24]](https://castman.co.kr/wp-content/uploads/image-973-png.webp)
![Fig. 4: Calculated IHTC peaks as a function of initial die temperature of finger-shape casting for B390 alloy[8]](https://castman.co.kr/wp-content/uploads/image-974-1024x705.webp)
![Fig. 5: Calculated IHTC peaks as a function of initial die temperature of cover-plate casting for AM60B alloy [7]](https://castman.co.kr/wp-content/uploads/image-975-1024x729.webp)
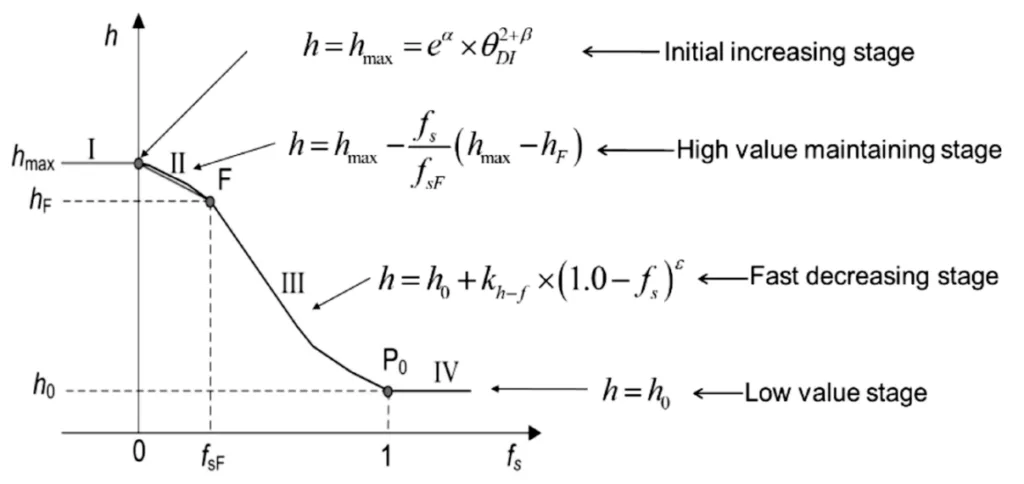
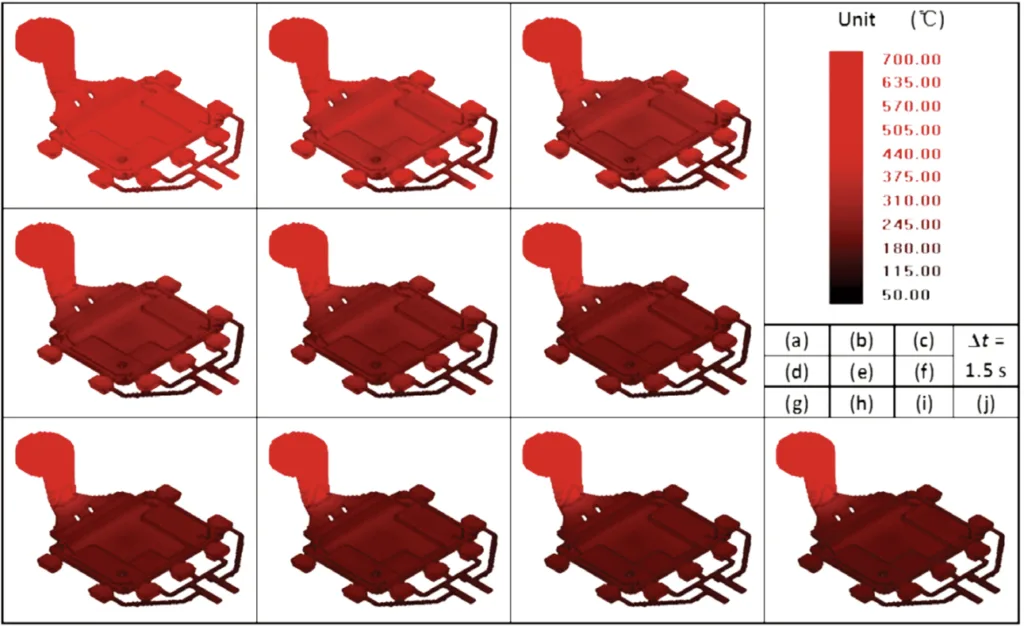
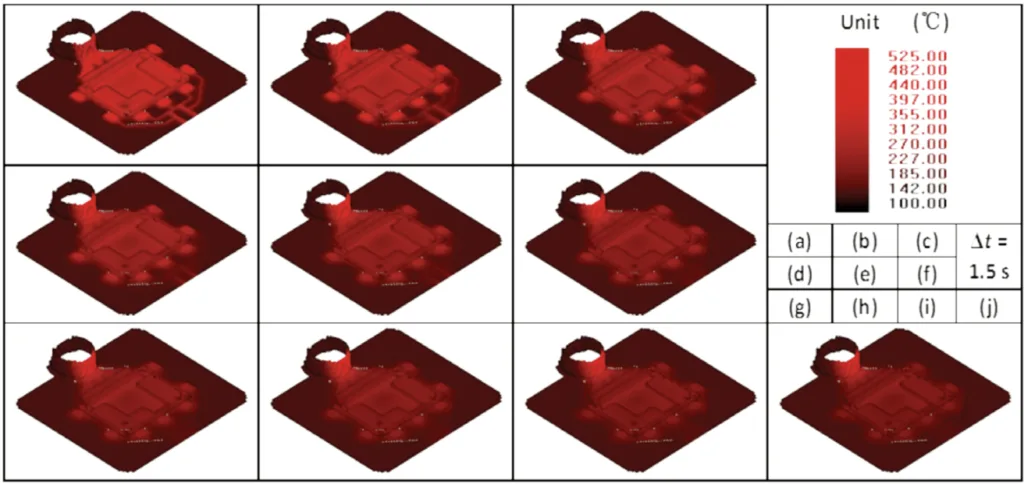
7. Conclusion:
Summary of Key Findings:
This paper reviewed the research progress on interfacial heat transfer coefficient (IHTC) determination in high pressure die casting (HPDC). It summarized three main approaches for IHTC determination and highlighted the challenges in accurate temperature measurement in HPDC. The Tsinghua Group's research progress was presented, leading to the development of a thermal boundary condition model based on correlations between IHTC, casting solid fraction, and initial die surface temperature. The model was validated through simulations, showing excellent agreement with experimental data.
Academic Significance of the Study:
This review provides a comprehensive overview of IHTC research in HPDC, consolidating knowledge on determination methods and influencing factors. The developed thermal boundary condition model contributes to a more accurate representation of heat transfer at the metal-mold interface in HPDC simulations, advancing the field of casting process modeling.
Practical Implications:
The validated thermal boundary condition model can be practically applied in HPDC process simulations to improve the prediction of temperature fields and solidification behavior. This can aid in optimizing die design, process parameters, and ultimately, casting quality and efficiency in industrial HPDC applications.
Limitations of the Study and Areas for Future Research:
The paper primarily focuses on aluminum alloys and specific casting geometries. Further research is needed to:
- Validate the thermal boundary condition model for a wider range of casting alloys and complex geometries.
- Investigate the influence of other process parameters and die coating conditions on IHTC.
- Refine the model to account for more complex phenomena at the metal-mold interface, such as gap formation and surface roughness effects.
- Explore advanced temperature measurement techniques to improve the accuracy of experimental IHTC determination in HPDC.
8. References:
- [1] Nelson C W. Nature of heat transfer at the die face. In: Proceedings of 6th SDCE International Die Casting Congrass; Cleveland, OH, 1970: 1-8.
- [2] Garcia A and Prates M. Mathematical model for the unidirectional solidification of metals: I. Cooled molds. Metallurgical Transaction B, 1978, 9(3): 449-457.
- [3] Garcia A, Clyne T, and Prates M. Mathematical model for the unidirectional solidification of metals: II. Massive molds. Metallurgical Transactions B, 1979, 10(1): 85-92.
- [4] Prates M and Biloni H. Variables affecting the nature of the chill zone. Metallurgical Transactions, 1972, 3(6): 1501-1510.
- [5] Beck J V. Nonlinear estimation applied to the nonlinear inverse heat conduction problem. International Journal of Heat and Mass Transfer, 1970, 13(4): 703-716.
- [6] Beck J V, Blackwell B, and Clair C R. Inverse Heat Conduction: III-posed problems, 1985.
- [7] Cao Y, Guo Z, and Xiong S. A Study on Heat Transfer at Metal/ Die Interface during High Pressure Die Casting of AM60B Alloy. In: Proceedings of the 8th Pacific Rim International Congress on Advanced Materials and Processing (Pricm 8). Waikoloa, Hawaii, US, TMS (The Minerals, Metals & Materials Society), 2013: 3041-3049.
- [8] Cao Y, Guo Z, and Xiong S. Determination of the metal/die interfacial heat transfer coefficient of high pressure die cast B390 alloy. IOP Conference Series, Materials Science and Engineering, 2012, 33(1): 012010.
- [9] Guo Z P, Xiong S M, Liu B C, et al. Effect of Process Parameters, Casting Thickness, and Alloys on the Interfacial Heat Transfer coefficient in the High-Pressure Die-Casting Process. Metallurgical and Materials Transactions A: Physical Metallurgy and Materials Science, 2008, 39A(12): 2896-2905.
- [10] Guo Z P, Xiong S M, Liu B C, et al. Determination of the heat transfer coefficient at metal-die interface in high pressure die casting process of AM50 alloy. International Journal of Heat and Mass Transfer. 2008, 51(25-26): 6032-6038.
- [11] Guo Z P, Xiong S M, Murakami M, et al. Study on interfacial heat transfer coefficient as metal/die interface during high pressure die casting process of AZ91D alloy. China Foundry, 2007, 4(1): 5-9.
- [12] Hamasaiid A, Dour G, Dargusch M et al. Heat transfer at the casting /die interface in high pressure casting - Experimental results and contribution to modeling. In: Proceedings of MCWASP XI: Modeling of Casting, Welding and Advanced Solidification Processes, Opio, France: Minerals, Metals and Materials Society (TMS), 2006, 2: 1205-1212.
- [13] Dour G, Daugusch M, Davidson C, et al. Development of a non-intrusive heat transfer coefficient gauge and its application to high pressure die casting; Effect of the process parameters. Journal of Materials Processing Technology, 2005, 169(2): 223-233.
- [14] Hallam C P and Griffiths W D. A model of the interfacial heat-transfer coefficient for the aluminum gravity die-casting process. Metallurgical and Materials Transactions B: Process Metallurgy and Materials Processing Science, 2004, 35(4): 721-733.
- [15] El-Mahallawy N A, Taha M A, Pokora E, et al. On the influence of process variables on the thermal conditions and properties of high pressure die-cast magnesium alloys. Journal of Materials Processing Technology, 1998, 73(1-3): 125-138.
- [16] Papai J and Mobley C. Die thermal fields and heat fluxes during die casting of 380 aluminum alloy in H-13 steel dies. NADCA Transactions, 1991: 377-384.
- [17] Ho K and Pehlke R D. Metal-mold interfacial heat transfer. Metallurgical Transactions B (Process Metallurgy), 1985, 16B(3): 585-594.
- [18] Sekhar J A, Abbaschian G J, and Mehrabian R. Effect of pressure on metal-die heat transfer coefficient during solidification. Materials Science and Engineering, 1979, 40(1): 105-110.
- [19] Hong S, Backman D, and Mehrabian R. Heat transfer coefficient in aluminum alloy die casting. Metallurgical Transactions B, 1979, 10(2): 299-301.
- [20] Backman D, Mehrabian R, and Flemings M. Die thermal behavior in machine casting of partially solid high temperature alloys. Metallurgical Transactions B, 1977, 8(2): 471-477.
- [21] Ho K and Pehlke R D. Transient methods for determination of metal-mold interfacial heat transfer. In: Proceedings of Transactions of the American Foundrymen's Society, Proceedings of the Eighty-seventh Annual Meeting, Rosemont, II, USA, AFS, 1983, 91: 689-698.
- [22] Dour G, Dargusch M, and Davidson C. Recommendations and guidelines for the performance of accurate heat transfer measurements in rapid forming processes. International Journal of Heat and Mass Transfer, 2006, 49(11-12): 1773-1789.
- [23] Hamasaiid A, Dour G, Dargusch M S, et al. Heat-transfer coefficient and in-cavity pressure at the casting-die interface during high-pressure die casting of the magnesium alloy AZ91D. Metallurgical and Materials Transactions A - Physical Metallurgy and Materials Science, 2008, 39A(4): 853-864.
- [24] Guo Z P, Xiong S M, Liu B C, et al. Development of thermal boundary condition model at metal/die interface of high pressure die casting process. International Journal of Cast Metals Research, 2011, 24(3-4): 151-157.
9. Copyright:
- This material is "Cao Yongyou, Guo Zhipeng, and Xiong Shoumei"'s paper: Based on "Determination of interfacial heat transfer coefficient and its application in high pressure die casting process".
- Paper Source: [https://doi.org/](DOI URL is not available in the paper, please add if you have it)
This material was summarized based on the above paper, and unauthorized use for commercial purposes is prohibited.
Copyright © 2025 CASTMAN. All rights reserved.