This article introduces the paper 'DESIGNING AN INNOVATIVE MODULAR PLATFORM FOR SPORTS CARS USING THE GENERATIVE DESIGN METHOD' published by 'Università di Bologna'.
1. Overview:
- Title: DESIGNING AN INNOVATIVE MODULAR PLATFORM FOR SPORTS CARS USING THE GENERATIVE DESIGN METHOD
- Author: Merve Sali
- Publication Year: 2024
- Publishing Journal/Academic Society: DOTTORATO DI RICERCA IN MECCANICA E SCIENZE AVANZATE DELL'INGEGNERIA, Università di Bologna
- Keywords: Not explicitly listed in the provided document. Keywords can be inferred from the title and abstract as: Modular Platform, Sports Cars, Generative Design Method, Automotive Chassis, Lightweight Design, Agile Method, Scrum.
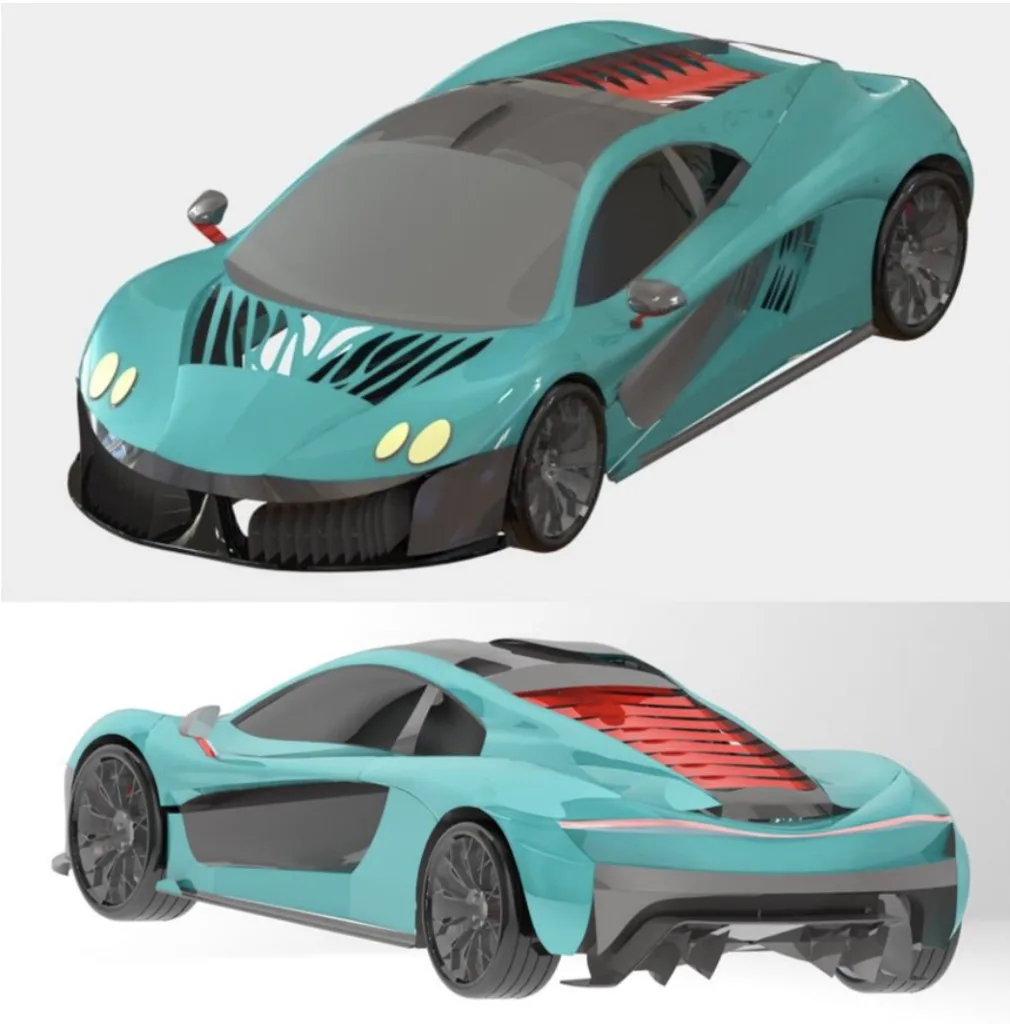
2. Abstracts
Traditional methods, where chassis components are tailored for each vehicle type, lack flexibility and efficiency. The concept of current modular platforms, allows the reuse of components across different models, reducing production costs and enhancing adaptability. But, in current situation these solutions are not common in sports cars segment. The research delves into the challenges and opportunities posed by modular platforms in the context of sports cars, highlighting their potential impact on driving dynamics, design aesthetics, and future innovations. The project focuses on a modular platform approach, providing diversity while maintaining a standardized design sections, emphasizing interchangeability of components besides flexibility, using cutting-edge design methods. This study addresses to create a modular platform suitable for different drivetrain and powertrain configurations, with iterative sprints targeting lightweight and high-stiffness designs by using generative design method. In addition to improving design outcomes, efforts have been made to enhance creativity by employing the steps of the generative design method within the existing workflow (IDeS), and collaboration with the Agile method variant, Scrum, has been established to filter the results, which is crucial for project development. Moreover, it has been applied to an alternative modular platform created with new parts obtained through the generative design application. The results obtained have been evaluated in terms of the model's mechanical properties. These new parts are not only geometrically more efficient but also capable of yielding the same mechanical results even when different materials are used. Numerical results of simulations are compared for the final assemblies created with generated components (Part 1, Part 3, and Part 4) and with initial components. In particular, it has been demonstrated that, by employing the generative design method, equivalent strength values can be achieved by using aluminium alloy instead of steel alloy for the component of Part 3 (Outcome 7). Torsion and bending stiffness tests on each model have been performed before and after generative design process. The parts defined to generate decided with crash tests on rear-mid and front modular platform layouts separately. The results have been compared and it has found that stress distributions are similar which means the parts that we have generated are sufficient in new design such as shapes, weight, and mechanical properties.
3. Research Background:
Background of the Research Topic:
Traditional chassis design methods for vehicles lack flexibility and efficiency because components are tailored for each vehicle type. Current modular platforms offer component reuse across models, reducing production costs and improving adaptability. However, these solutions are uncommon in the sports car segment. This research addresses the challenges and opportunities of modular platforms in sports cars, considering their impact on driving dynamics, design aesthetics, and innovation. The project aims to create a modular platform for sports cars, emphasizing diversity, standardized design, component interchangeability, and flexibility using cutting-edge design methods.
Status of Existing Research:
Existing research acknowledges the benefits of modular platforms in the automotive industry, including cost reduction and increased flexibility (Florea et al., 2016; Lampón et al., 2015). Literature review highlights the evolution of platform strategies, from shared platforms pioneered by Mitsubishi (Cusumano & Nobeoka, 1998) to the standardization efforts by PSA Group (Holweg, 2008; Patchong et al., 2003). Research also explores the application of generative design and additive manufacturing for lightweight automotive components (Junk & Rothe, 2022; Fenoon et al., 2021; Dalpadulo et al., 2020), indicating a trend towards innovative design and material utilization in chassis development.
Necessity of the Research:
The research is necessary due to the limited application of modular platforms in the sports car segment despite their potential benefits. The increasing demand for flexibility, efficiency, and adaptability in automotive manufacturing, coupled with the need for lightweight designs and sustainable practices, necessitates exploring innovative approaches like generative design for modular sports car platforms. Furthermore, the need to address climate change and reduce CO2 emissions (European Parliament and the Council of the European Union, 2019) drives the automotive industry towards modular and sustainable solutions.
4. Research Purpose and Research Questions:
Research Purpose:
This study addresses to create a modular platform suitable for different drivetrain and powertrain configurations, with iterative sprints targeting lightweight and high-stiffness designs by using generative design method. In addition to improving design outcomes, efforts have been made to enhance creativity by employing the steps of the generative design method within the existing workflow (IDeS), and collaboration with the Agile method variant, Scrum, has been established to filter the results, which is crucial for project development.
Key Research:
- Creation of a modular platform for sports cars adaptable to different drivetrain and powertrain configurations.
- Application of generative design method to achieve lightweight and high-stiffness designs.
- Integration of generative design within the Industrial Design Structure (IDeS) workflow.
- Implementation of Scrum methodology to manage and filter generative design outputs.
- Evaluation of the modular platform's mechanical properties and performance.
Research Hypotheses:
The paper does not explicitly state research hypotheses. However, based on the research purpose and key research questions, the implicit hypotheses are:
- Generative design method can create geometrically efficient and lightweight components for a modular sports car platform.
- A modular platform designed with generative design can achieve equivalent or improved mechanical properties compared to platforms designed with traditional methods.
- Integrating Scrum methodology with IDeS workflow and generative design can enhance the efficiency and creativity of the design process for modular platforms.
- Using aluminium alloy in generatively designed components can achieve equivalent strength to steel alloy components while reducing weight.
5. Research Methodology
Research Design:
The research employs a design-based research approach, focusing on the development of an innovative modular platform using generative design. It integrates the Industrial Design Structure (IDeS) workflow with Scrum methodology and generative design techniques. The design process is iterative, involving sprints and adaptations based on analysis and testing.
Data Collection Method:
Data collection methods are not explicitly detailed in this summary, but can be inferred as:
- Literature review: To understand existing research on modular platforms, generative design, and automotive chassis design.
- Market analysis data: To understand market trends, customer requirements, and competitor analysis.
- Simulation data: Numerical results from simulations (torsion, bending, crash tests) to evaluate mechanical properties.
- Expert interviews: Break-up of the profiles of industry experts are shown in Figure 3.1.
Analysis Method:
- Quality Function Deployment (QFD): To analyze customer requirements and translate them into design parameters.
- Dependence / Independence Matrix and Relative importance matrix: To prioritize customer requirements.
- Benchmarking: To compare existing sports car models and identify design parameters.
- Finite Element Analysis (FEA): Using SolidWorks Simulation to perform mechanical stress analyses (torsional stiffness, bending stiffness, frontal impact analysis) and evaluate the performance of the modular platform and generatively designed components.
- Comparative analysis: Comparing simulation results of initial and generatively designed components, and platforms with different configurations and materials.
Research Subjects and Scope:
- Research Subjects: Design and analysis of a modular platform for sports cars. Generatively designed components for engine compartment (Part 1), cockpit underbody (Part 3), and electric motor compartment (Part 4).
- Research Scope: Focuses on the structural design and mechanical performance of the modular platform, particularly its chassis components. The styling and broader vehicle development aspects are also considered but are secondary to the structural and modular design aspects. The material scope is primarily steel and aluminium alloys.
6. Main Research Results:
Key Research Results:
- Generative design method was successfully applied to create lightweight components for the modular platform (Part 1, Part 3, Part 4).
- Generatively designed components using aluminium alloy achieved equivalent strength values to initial steel alloy components, with significant weight reduction, particularly for Part 3 (Outcome 7).
- Torsion and bending stiffness tests were performed and compared for initial and generatively designed modular platforms, demonstrating the viability of the new designs.
- A new Scrum workflow model integrated with generative design method and IDeS workflow was developed and applied.
- The modular platform design allows for adaptability to different engine layouts (rear-mid and front engine) and powertrain configurations.
Analysis of presented data:
- Torsional Stiffness: Torsional stiffness values for both initial and generatively designed platforms are within a comparable range, although slightly lower for the generatively designed rear-mid engine platform (9179.317 Nm/deg) compared to the initial rear-mid engine platform (9705.0857 Nm/deg).
- Bending Stiffness: Bending stiffness values are also comparable between initial and generatively designed platforms, with the generatively designed rear-mid platform showing a slightly lower value (21773.6 Nm/deg) than the initial rear-mid platform (25786.02 Nm/deg).
- Mass Reduction: Generative design and aluminium alloy usage resulted in significant mass reduction in components (Table 3.14), especially for Part 3, where aluminium alloy Outcome 7 achieved a mass of 3.932 kg compared to the initial steel alloy part.
- Stress Distribution: Stress distribution analysis indicated that maximum stress locations are similar in both initial and generatively designed platforms, primarily at connection points and areas of load concentration.
Figure Name List:
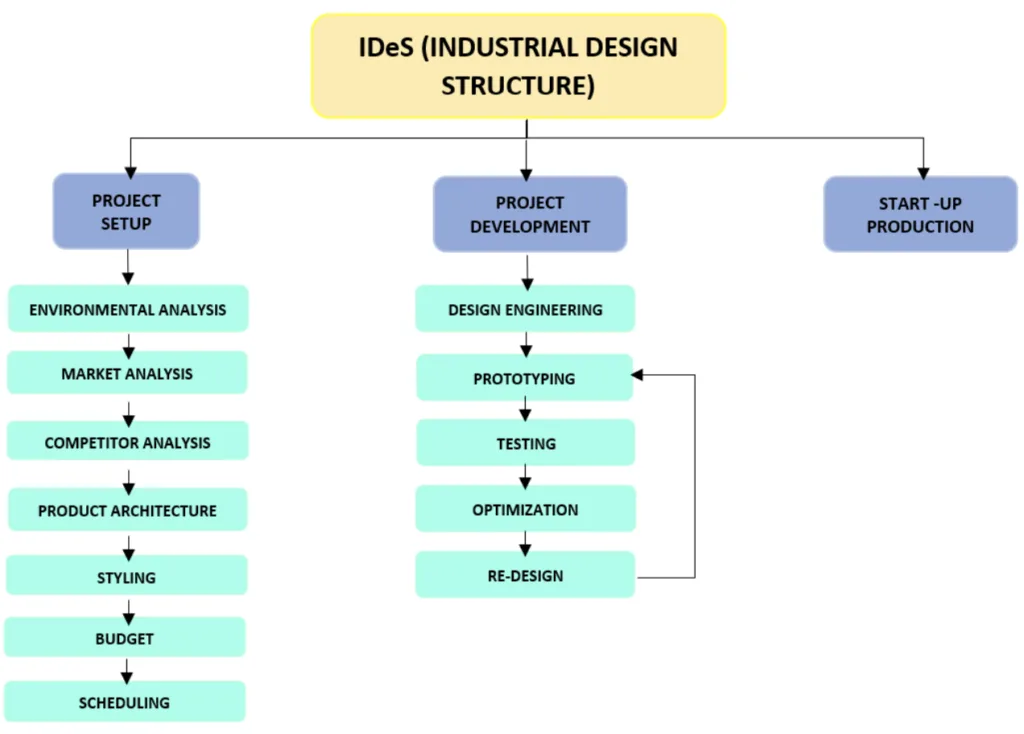
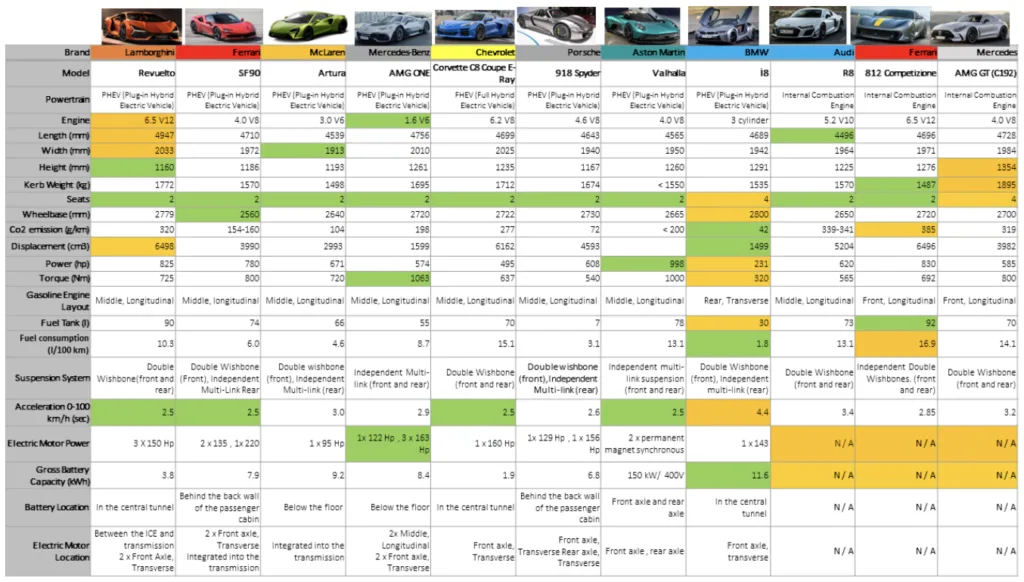
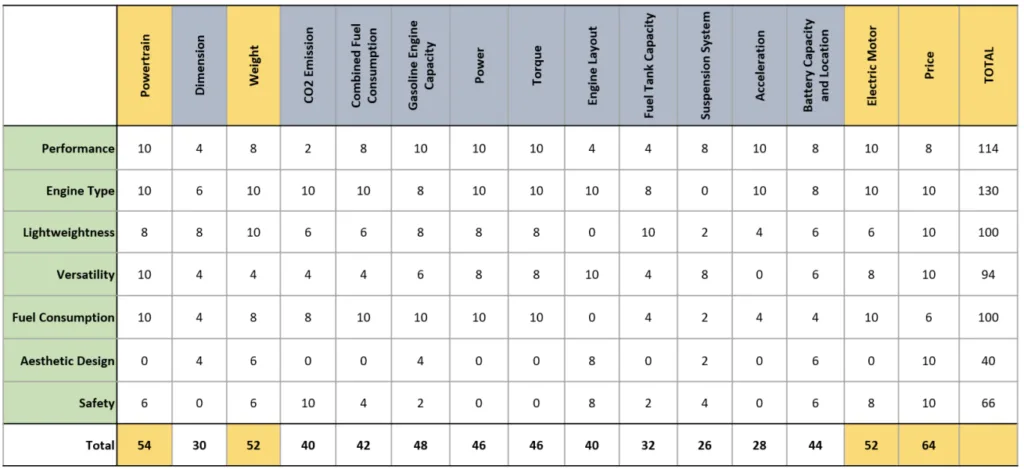
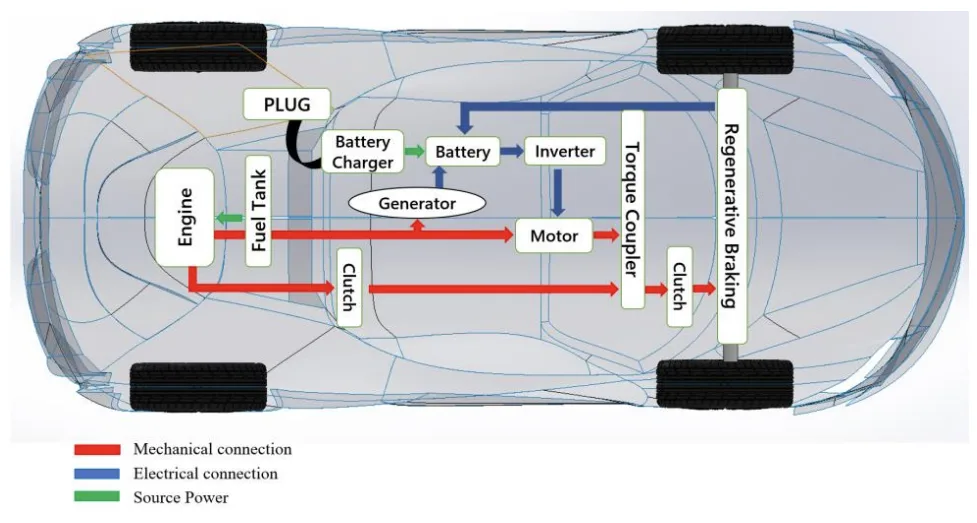
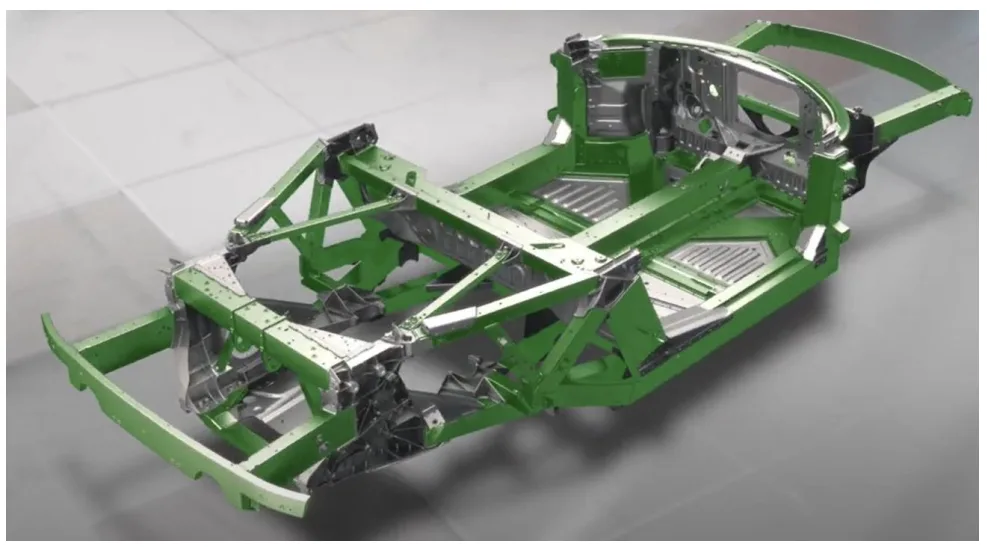
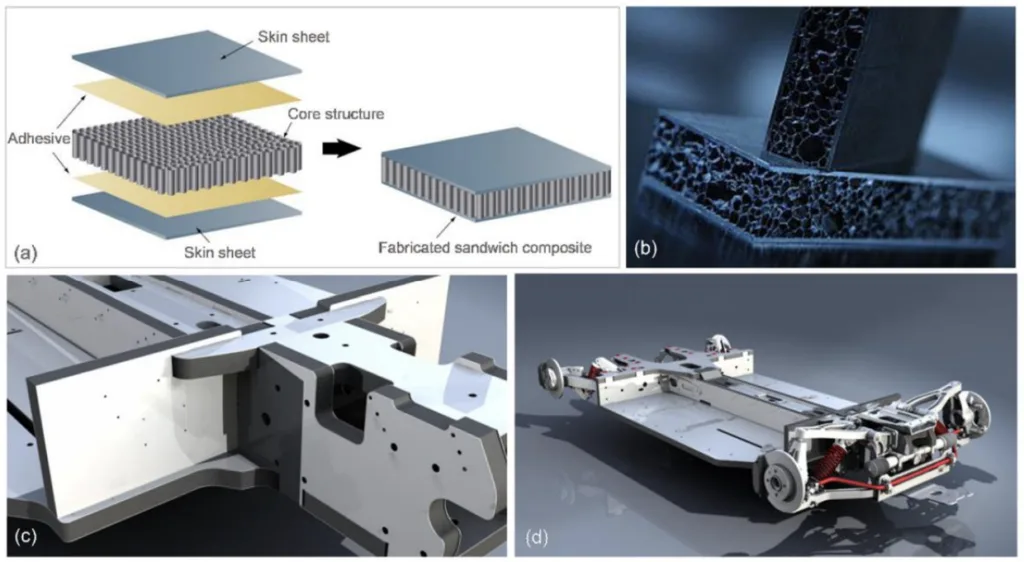
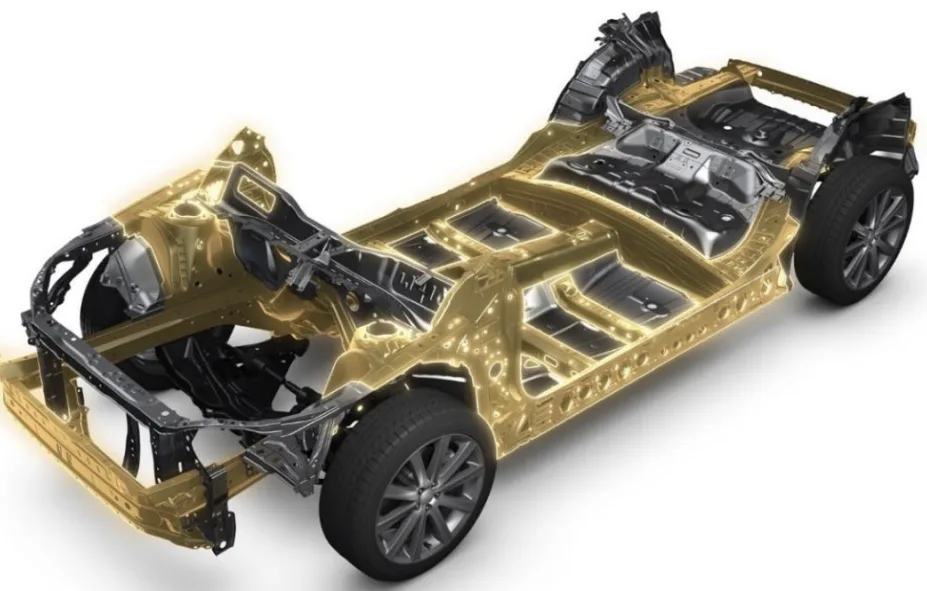
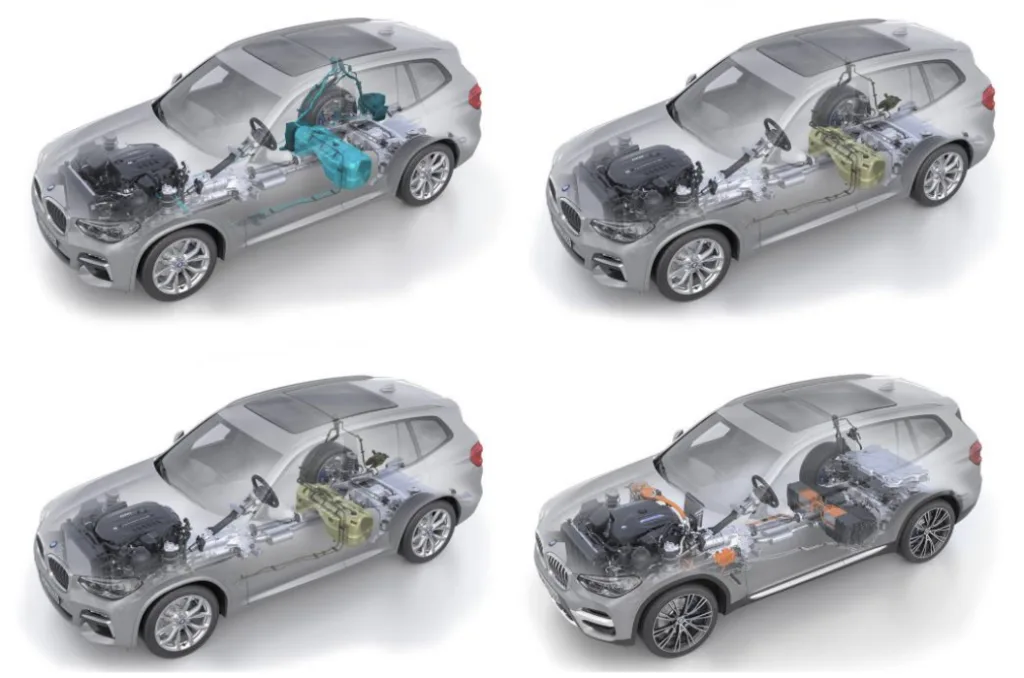
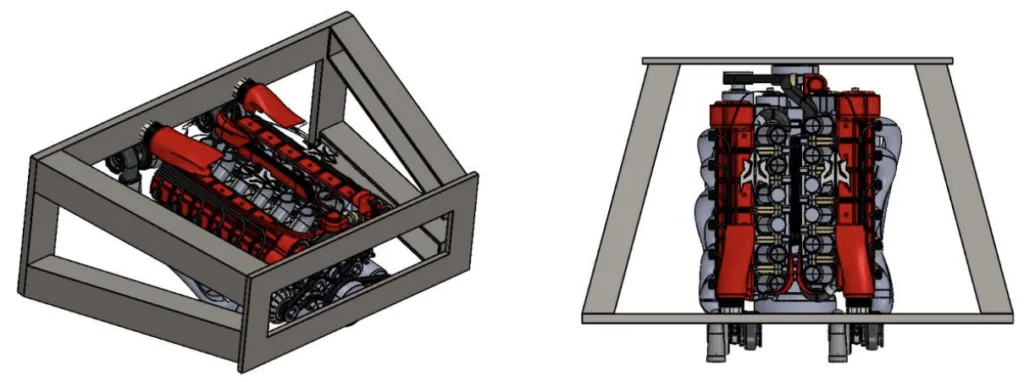
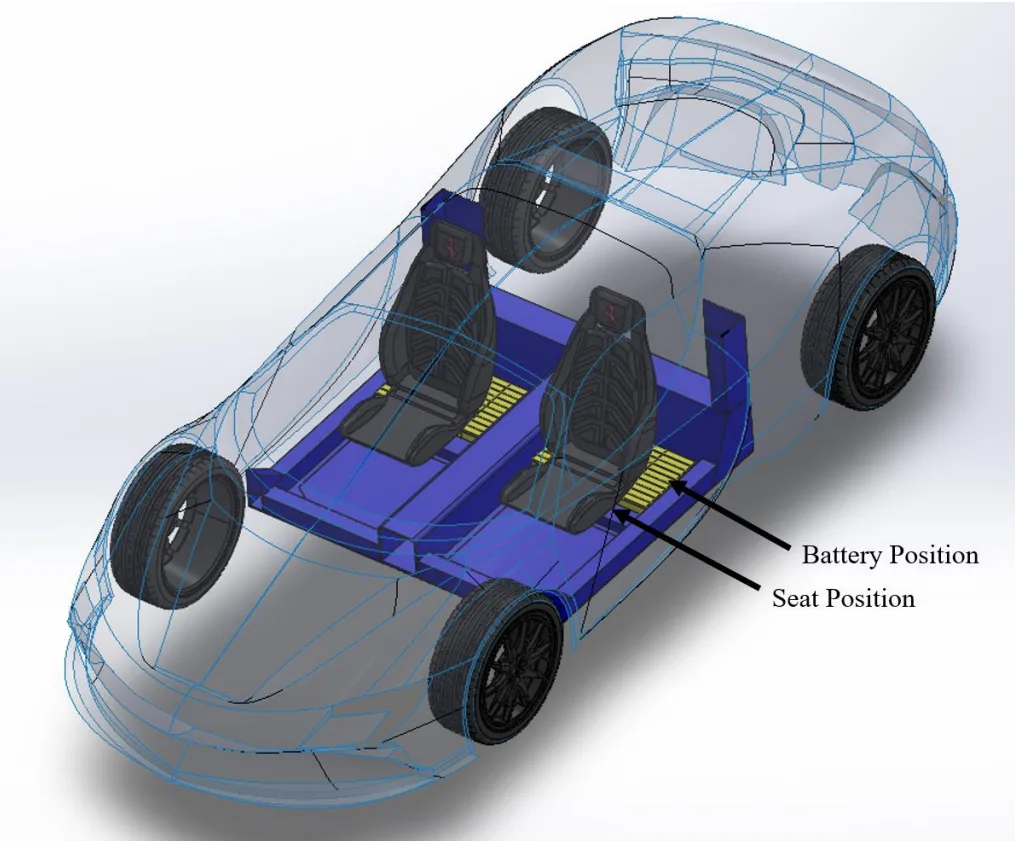
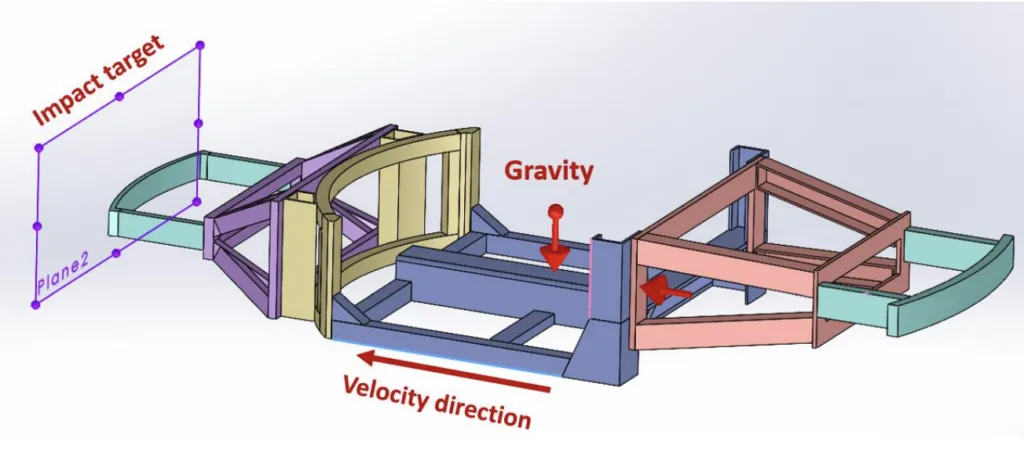
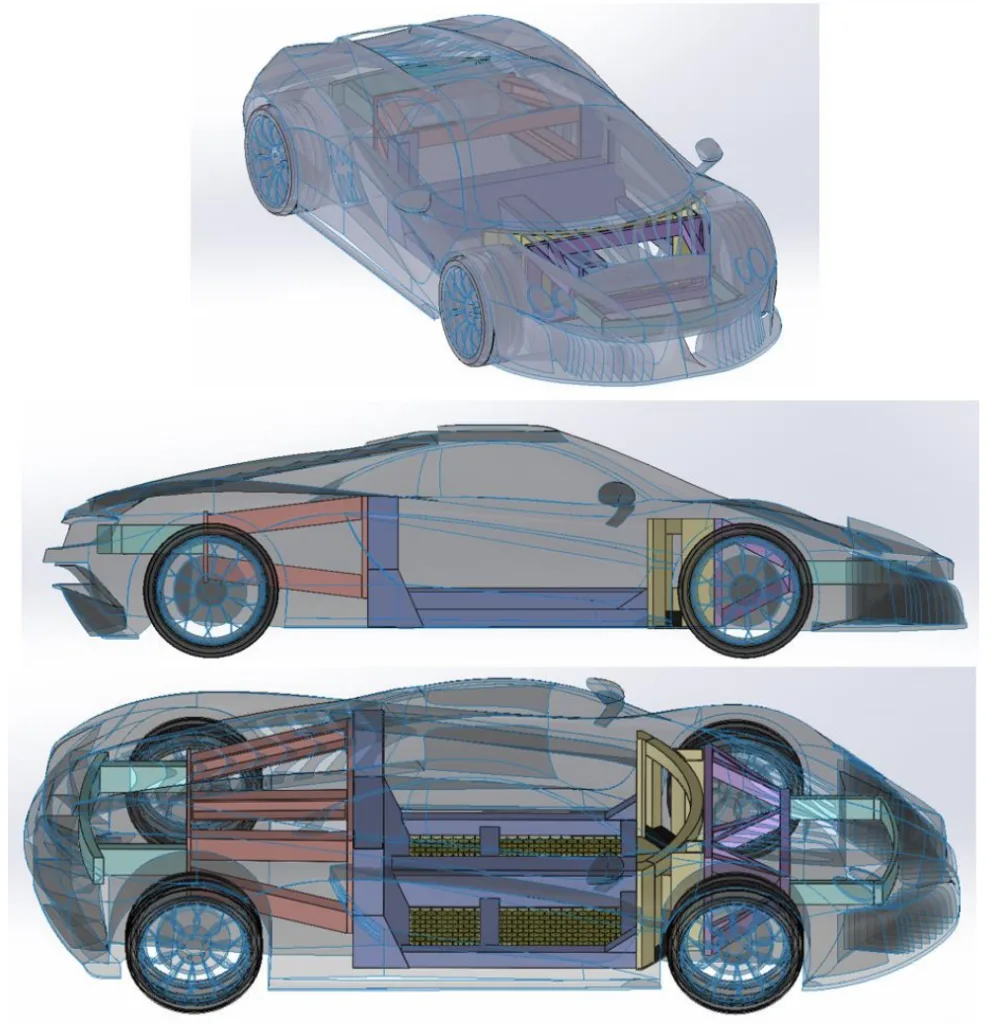
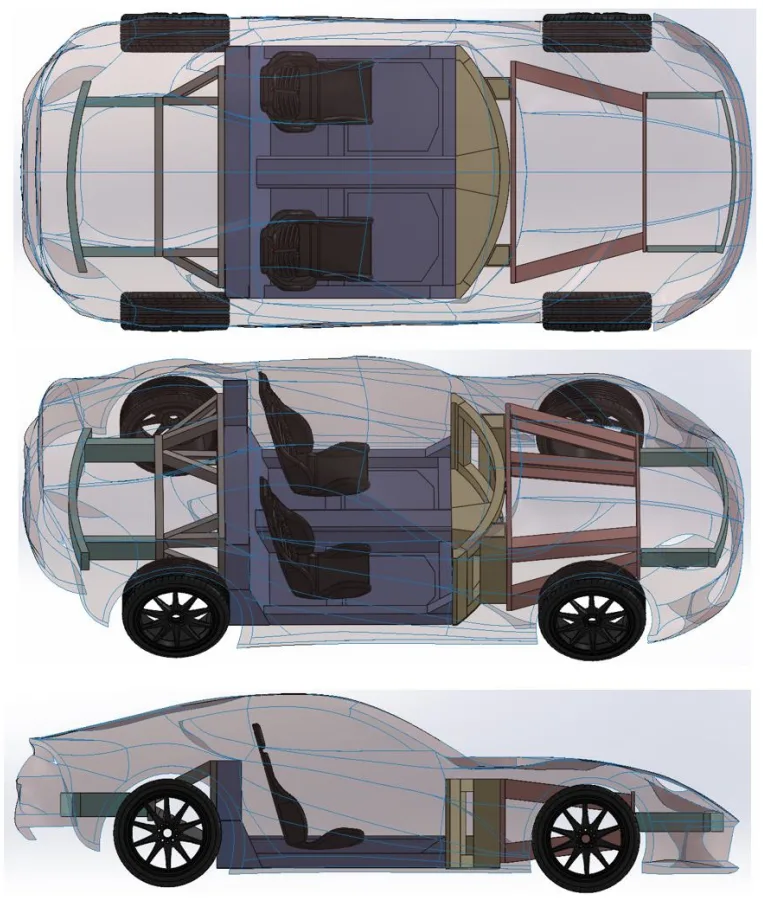
- Figure 1.1: Industrial Design Structure
- Figure 3.1: Break-up of the profiles of industry experts
- Figure 3.2: The market size of the Automotive Chassis in the Asia Pacific, 2019-2030(USD Billion)
- Figure 3.3: Global automotive chassis market share by chassis type, 2022
- Figure 3.4: House of quality template
- Figure 3.5: QFD- Six Questions
- Figure 3.6: Dependence / Independence matrix
- Figure 3.7: Relative importance matrix
- Figure 3.8: What-How matrix
- Figure 3.9: Front Engine layouts with different drivetrain configurations
- Figure 3.10: Front Engine layout with all wheel drive configuration
- Figure 3.11: Rear Engine layouts with different drivetrain configurations
- Figure 3.12: Series HEV configuration
- Figure 3.13: Parallel hybrid powertrain configuration
- Figure 3.14. Series-Parallel split hybrid powertrain configuration
- Figure 3.15: Plug-in series hybrid electric vehicle configuration
- Figure 3.16: Plug-in parallel hybrid electric vehicle configuration
- Figure 3.17: Plug-in series / Parallel hybrid electric vehicle configuration
- Figure 3.18: Generative design iterative process example
- Figure 3.19: Example of CAD and generated module used model
- Figure 3.20: Parts produced through extrusion
- Figure 3.21: The relationship between ultimate tensile strength and total elongation in traditional high-strength steels
- Figure 3.22: Sandwich structured composite application in automotive sub-frame
- Figure 3.23: PSA Common modular platform
- Figure 3.24: Volkswagen MQB modular platform
- Figure 3.25: Toyota (TNGA) modular platform
- Figure 3.26: Subaru (SGP) modular platform
- Figure 3.27: Renault-Nissan CMF modular platform
- Figure 3.28: BMW (CLAR) modular platform
- Figure 3.29: Modular vehicle platform
- Figure 3.30: Part 1: Engine compartment dimensions
- Figure 3.31: V6 Chevrolet engine for longitudinal position
- Figure 3.32: V6 Jaguar engine for longitudinal position
- Figure 3.33: V8 Engine for longitudinal position
- Figure 3.34: V8 Engine for transverse position
- Figure 3.35: V12 Engine for longitudinal positioning with transmission
- Figure 3.36: V12 Engine for longitudinal position
- Figure 3.37: Dimensional parameters of seat arrangement illustrated on a car
- Figure 3.38: Sports car seat dimensions of fit parameters
- Figure 3.39: Battery positioning on modular platform
- Figure 3.40: Part 2: Passenger zone dimensions
- Figure 3.41: Part 3: Assembly with a) Rear-Mid engine configuration b) Front engine configuration
- Figure 3.42: Part 3: Cockpit underbody dimensions
- Figure 3.43: Part 4: Assembly with double electric motor
- Figure 3.44: Part 4: Electric motor compartment dimensions
- Figure 3.45: Modular platform design final model and dimensions
- Figure 3.46: Forces during the car motion
- Figure 3.47: Longitudinal torsion
- Figure 3.48: Torsional stiffness load case
- Figure 3.49: Vertical bending
- Figure 3.50: Bending stiffness load case
- Figure 3.51: Lateral bending
- Figure 3.52: Horizontal lozenging
- Figure 3.53: Boundary conditions on rear-mid modular platform
- Figure 3.54. Displacement results of torsional test for rear-mid modular platform
- Figure 3.55. Torsional stress distribution of rear-mid modular platform
- Figure 3.56: Boundary conditions on front modular platform
- Figure 3.57: Displacement results of torsional test for front modular platform
- Figure 3.58: Torsional stress distribution of front modular platform
- Figure 3.59: Boundary conditions on rear-mid modular platform for bending test
- Figure 3.60: Displacement results of bending test for rear-mid modular platform
- Figure 3.61: Bending stress distribution results of rear-mid modular platform
- Figure 3.62: Boundary conditions on front modular platform for bending test
- Figure 3.63: Displacement results of bending test for front modular platform
- Figure 3.64: Bending stress distribution results of front modular platform
- Figure 3.65: Impact test settings for rear-mid modular platform
- Figure 3.66: Impact test results (a) Displacement results, (b) Deformation distribution results
- Figure 3.67: Defined sections for part development on Part 3 and Part 4
- Figure 3.68: Impact test settings for front modular platform
- Figure 3.69: Impact test results (a) Displacement results, (b) Deformation distribution results
- Figure 3.70: Defined section for the part development on Part 1
- Figure 3.71: Retro design
- Figure 3.72: Stone design
- Figure 3.73: Natural design inspired from the dorsal lines of the sailfish
- Figure 3.74: Natural design
- Figure 3.75: Advanced design
- Figure 3.76: Representation of the details selected for the final design
- Figure 3.77: Final design sketching
- Figure 3.78: Blueprint of final sketch
- Figure 3.79: Raw design of final sketch
- Figure 3.80: Final 3D design
- Figure 3.81: Rendered final design
- Figure 3.82: Modular platform and final design assembly
- Figure 3.83: Scrum process
- Figure 3.84: Generative design workflow
- Figure 3.85: Comparison of methods a) Sprint steps (Srivastava et al., 2017) b) Generative design process steps
- Figure 3.86: New scrum workflow model with generative design method
- Figure 3.87: Modified IDeS workflow using Scrum and Generative Design method
- Figure 3.88: Volkswagen MQB platform with material details
- Figure 3.89: Boundaries of platform sections
- Figure 3.90: Exploded view of the modular platform assembly
- Figure 3.91: Modular platform for rear-mid engine
- Figure 3.92: Modular platform for front engine
- Figure 3.93: Bolted joints of the modular platform
- Figure 3.94: Areas defined for generative design
- Figure 3.95: Boundary conditions of engine compartment (Part1)
- Figure 3.96: Boundary conditions of cockpit underbody (Part3)
- Figure 3.97: Boundary conditions for electric motor compartment (Part 4)
- Figure 3.98: Structural constraints and loads on Part 1
- Figure 3.99: Structural constraints and loads on Part 3
- Figure 3.100: Structural constraints and loads on Part 4
- Figure 3.101: Generative design results steel alloys applied Part 1
- Figure 3.102: Generative design results steel alloys applied Part 3
- Figure 3.103: Generative design results steel alloys applied Part 4
- Figure 3.104: Generative design results aluminium alloys applied Part 1
- Figure 3.105: Generative design results aluminium alloys applied Part 3
- Figure 3.106: Generative design results aluminium alloys applied Part 4
- Figure 3.107: Generative design applied “Ideal Modular Platform”
- Figure 3.108: Beam model of ideal modular platform
- Figure 3.109: Displacement results of ideal modular platform for rear-mid engine layout
- Figure 3.110: Torsional stress distribution of ideal modular platform for rear-mid engine layout
- Figure 3.111: Boundary conditions on front ideal modular platform
- Figure 3.112: Displacement results of ideal modular platform for front engine layout
- Figure 3.113: Torsional stress distribution of ideal modular platform for front engine layout
- Figure 3.114: Boundary conditions on rear-mid ideal modular platform for bending test
- Figure 3.115: Displacement results of bending test for rear-mid ideal modular platform
- Figure 3.116: Bending stress distribution results of rear-mid ideal modular platform
- Figure 3.117: Boundary conditions on front ideal modular platform for bending test
- Figure 3.118: Displacement results of bending test for front ideal modular platform
- Figure 3.119: Bending stress distribution results of front ideal modular platform
7. Conclusion:
Summary of Key Findings:
The study successfully designed a modular platform for sports cars using generative design methods within an adapted IDeS workflow incorporating Scrum. Generative design enabled the creation of lightweight components, particularly when using aluminium alloys, while maintaining or improving mechanical performance. The modular platform is adaptable to different engine layouts and powertrain configurations, demonstrating its versatility. The integration of Scrum methodology facilitated an iterative and efficient design process.
Academic Significance of the Study:
This study contributes to the academic field by demonstrating the effective application of generative design and agile methodologies (Scrum) in automotive chassis design, specifically for modular platforms in sports cars. It provides a detailed methodology for integrating these cutting-edge techniques within a structured design workflow (IDeS). The research also expands the understanding of material selection and optimization in generative design for achieving lightweight and high-performance automotive structures.
Practical Implications:
The practical implications of this study are significant for the automotive industry, particularly for sports car manufacturers. The developed modular platform design offers a viable solution for reducing production costs, enhancing vehicle adaptability, and improving fuel efficiency through lightweighting. The use of generative design and additive manufacturing techniques can lead to more innovative and efficient chassis designs. The integration of Scrum methodology can streamline the product development process, making it more agile and responsive to changing market demands.
Limitations of the Study and Areas for Future Research:
The study is limited by its focus on the lower part of the chassis and beam model simulations, which are simplifications of a full vehicle chassis. The torsional rigidity values obtained are not directly comparable to full chassis values of existing sports cars. Future research should focus on:
- Validating the modular platform design through full vehicle simulations and physical prototyping.
- Exploring a wider range of materials and manufacturing processes in generative design.
- Investigating the integration of generative design with multi-objective optimization for enhanced performance and sustainability.
- Further refining the Scrum-IDeS workflow for different automotive design projects and evaluating its broader applicability.
- Conducting experimental validation of the mechanical properties of generatively designed components and the modular platform.
8. References:
- Ary, A. K., Sanjaya, Y., Prabowo, A. R., Imaduddin, F., Nordin, N. A. B., Istanto, I., & Cho, J. H. (2021). Numerical estimation of the torsional stiffness characteristics on urban Shell Eco-Marathon (SEM) vehicle design. Curved and Layered Structures, 8(1), 167–180. https://doi.org/10.1515/cls-2021-0016
- Attar, R., Aish, R., Stam, J., Brinsmead, D., Tessier, A., Glueck, M., & Khan, A. (2009). PHYSICS-BASED GENERATIVE DESIGN.
- Benajes, J., García, A., Monsalve-Serrano, J., & Martínez-Boggio, S. (2019). Optimization of the parallel and mild hybrid vehicle platforms operating under conventional and advanced combustion modes. Energy Conversion and Management, 190, 73–90. https://doi.org/https://doi.org/10.1016/j.enconman.2019.04.010
- Bire, S. R. (2014, March 2). Design Criteria for Automobile Seat. Slideshare. https://www.slideshare.net/sarangbire/sarang-bire-seat-design
- Boeriu, H. (2020, November 4). 2025 CLAR: BMW CEO announces new cluster architecture. https://www.bmwblog.com/2020/11/04/bmw-clar-2025/
- Bonsanto Oliveira, A., A Rodrigues, A. F., Gertz, L. C., Cervieri, A., Poncio, A., Oliveira, A. B., & Pereira, M. S. (2018). Static and Dynamic Analysis of a Chassis of a Prototype Car. SAE Brasil.
- Briard, T., Segonds, F., & Zamariola, N. (2020). G-DfAM: a methodological proposal of generative design for additive manufacturing in the automotive industry. International Journal on Interactive Design and Manufacturing, 14(3), 875–886. https://doi.org/10.1007/s12008-020-00669-6
- Buiga, A. (2012). Investigating the role of MQB platform in volkswagen group’s strategy and automobile industry. International Journal of Academic Research in Business and Social Sciences, 9, 391–399.
- Buonamici, F., Carfagni, M., Furferi, R., Volpe, Y., & Governi, L. (2020). Generative design: An explorative study. Computer-Aided Design and Applications, 18(1), 144–155. https://doi.org/10.14733/cadaps.2021.144-155
- Caldas, L. (2001). An evolution-based generative design system : using adaptation to shape architectural form. https://api.semanticscholar.org/CorpusID:109280128
- Carroll, J., Adolph, T., Chauvel, C., Labrousse, M., Trosseille, X., Pastor, C., Eggers, A., Smith, S., & Hynd, D. (2010). OVERVIEW OF SERIOUS THORAX INJURIES IN EUROPEAN FRONTAL CAR CRASH ACCIDENTS AND IMPLICATIONS FOR CRASH TEST DUMMY DEVELOPMENT. IRCOBI Conference. www.gidas.org
- Cervone, H. F. (2011). Understanding agile project management methods using Scrum. OCLC Systems & Services: International Digital Library Perspectives, 27(1), 18–22. https://doi.org/10.1108/10650751111106528
- Chandak, A., Gandhe, N., Choudhari, K., Gaikwad, N., & Thorat, P. (2021). To enhance crashworthiness of an automobile by introducing energy absorbers and to study its implementation. Materials Today: Proceedings, 47, 3006–3011. https://doi.org/10.1016/j.matpr.2021.05.477
- Cheli, R. : F. (2013). Study on the influence of the car body flexibility on handling performance and forces distribution with CAE methods. Politecnico di Milano.
- Chen, X., Tao, Y., Wang, G., Kang, R., Grossman, T., Coros, S., & Hudson, S. E. (2018). Forte: User-driven generative design. Conference on Human Factors in Computing Systems - Proceedings, 2018-April. https://doi.org/10.1145/3173574.3174070
- Cobb, C. G. (2011). Making sense of agile project management [electronic resource] : balancing control and agility. Hoboken, NJ : Wiley, 2011.
- Cohen, D., Lindvall, M., & Costa, P. (2004). An Introduction to Agile Methods. In Advances in Computers (Vol. 62, pp. 1–66). Elsevier. https://doi.org/https://doi.org/10.1016/S0065-2458(03)62001-2
- Coram, M., & Bohner, S. (2005). The impact of agile methods on software project management. 12th IEEE International Conference and Workshops on the Engineering of Computer-Based Systems (ECBS’05), 363–370. https://doi.org/10.1109/ECBS.2005.68
- Crolla, D., & Mashadi, B. (2011). Vehicle powertrain systems. John Wiley & Sons.
- Cui, J., & MingXi, T. (2011). GENERATIVE DESIGN EXPLORATION FRAMEWORK BASED ON SUBJECTIVE EVALUATION.
- Cusumano, M. A., & Nobeoka, K. (1998). Thinking beyond lean: how multi-project management is transforming product development at Toyota and other companies. Simon and Schuster.
- Czerwinski, F. (2021). Current Trends in Automotive Lightweighting Strategies and Materials. Materials, 14(21). https://doi.org/10.3390/ma14216631
- Dalpadulo, E., Pini, F., & Leali, F. (2020). Integrated CAD platform approach for Design for Additive Manufacturing of high performance automotive components. International Journal on Interactive Design and Manufacturing, 14(3), 899–909. https://doi.org/10.1007/s12008-020-00684-7
- Danielsson, O. (2015). Influence of Body Stiffness on Vehicle Dynamics Characteristics in Passenger Cars [Master’s Thesis]. Chalmers University of Technology.
- Daruis, D. D. I., Deros, B. M., & Nor, M. J. M. (2011). Malaysian sitting anthropometry for seat fit parameters. Human Factors and Ergonomics in Manufacturing & Service Industries, 21(5), 443–455. https://doi.org/https://doi.org/10.1002/hfm.20237
- Diebold, P., Ostberg, J.-P., Wagner, S., & Zendler, U. (2015). What Do Practitioners Vary in Using Scrum? In C. Lassenius, T. Dingsøyr, & M. Paasivaara (Eds.), Agile Processes in Software Engineering and Extreme Programming (pp. 40–51). Springer International Publishing.
- Du, B., Li, Q., Zheng, C., Wang, S., Gao, C., & Chen, L. (2023). Application of Lightweight Structure in Automobile Bumper Beam: A Review. Materials, 16(3). https://doi.org/10.3390/ma16030967
- Elliott, A. (2016, April 19). 2017 BMW X5 to Use New 7-Series CLAR Platform. GTspirit. https://gtspirit.com/2016/04/19/2017-bmw-x5-use-new-7-series-clar-platform/
- Emadi, A., Lee, Y. J., & Rajashekara, K. (2008). Power electronics and motor drives in electric, hybrid electric, and plug-in hybrid electric vehicles. In IEEE Transactions on Industrial Electronics (Vol. 55, Issue 6, pp. 2237–2245). https://doi.org/10.1109/TIE.2008.922768
- Fellini, R., Kokkolaras, M., & Papalambros, P. (2006). Quantitative platform selection in optimal design of product families, with application to automotive engine design. Journal of Engineering Design, 17, 429–446. https://doi.org/10.1080/09544820500287797
- Feloy, M., Dsouza, R., Jones, R., & Bayliss, M. (2013). Technology and Skills in the Aerospace and Automotive Industries i Technology and Skills in the Aerospace and Automotive Industries. www.ukces.org.uk
- Fenoon, M., Alquabeh, O., Nisar, M. M., & Zia, S. (2021). Generative Design of a Mechanical Pedal. International Journal of Engineering and Management Sciences (IJEMS), 6(1). https://doi.org/10.21791/IJEMS.2021.1.5
- Ferrari 488 Spider. (n.d.). Retrieved January 21, 2024, from https://www.ferrari.com/it-IT/auto/488-spider
- Florea, M., Croitorescu, V., & Oprean, M. (2016). Smart Solutions for Vehicle Chassis. In C. Andreescu & A. Clenci (Eds.), Proceedings of the European Automotive Congress EAEC-ESFA 2015 (pp. 233–244). Springer International Publishing.
- Freddi, M., Borri, N., Alessandri, G., Galiè, G., Donnici, G., & Frizziero, L. (2022). IDeS Method Applied to the Concept of a Sports Car. Proceedings of the First Australian International Conference on Industrial Engineering and Operations Management.
- Frizziero, L., Liverani, A., Giuliano, I., Grazia Picciariello, M., Tucci, L., & Donnici, G. (2020). Application of IDeS (Industrial Design Structure) to Sustainable Mobility: case study of an innovative bicycle. Symmetry, 12. www.mdpi.com/journal/symmetry
- Frizziero, L., Liverani, A., & Ricciardelli, G. M. (2019). Design for Six Sigma (DFSS) Applied to a New E-Segment Sedan. Applied Sciences, 12(3). www.mdpi.com/journal/applsci
- Ganesh Sarvankar, S., & Yewale, S. N. (2019). Additive Manufacturing in Automobile Industry. 7(4).
- Garcia, L. A., OliveiraJr, E., & Morandini, M. (2022). Tailoring the Scrum framework for software development: Literature mapping and feature-based support. Information and Software Technology, 146, 106814. https://doi.org/https://doi.org/10.1016/j.infsof.2021.106814
- Gauss, L., Lacerda, D. P., & Cauchick Miguel, P. A. (2021). Module-based product family design: systematic literature review and meta-synthesis. Journal of Intelligent Manufacturing, 32(1), 265–312. https://doi.org/10.1007/s10845-020-01572-3
- Genta, G., & Morello, L. (2009). Chassis Structures. In The Automotive Chassis Volume 1: Components Design (pp. 351–381). Springer Link.
- Goncalves, M., & Heda, R. (2010a). A Case for Agile. In M. Goncalves & R. Heda (Eds.), Fundamentals of Agile Project Management: An Overview (p. 0). ASME Press. https://doi.org/10.1115/1.802960.ch1
- Goncalves, M., & Heda, R. (2010b). Fundamentals of Agile Project Management: An Overview. ASME Press. https://doi.org/10.1115/1.802960
- Gruss, M., Nagel, M., & Hofel, P. (2012). HD - High ductility, low-alloy, fine-grain structural steels: A new product series for cold forming. 28–31.
- Gulanova, J., & Vereš, M. (2014). COMPUTER AIDED GENERATIVE DESIGN OF AUTOMOTIVE SHAPED COMPONENTS. https://www.researchgate.net/publication/294892055
- Ha, N., & Lu, G. (2020). A review of recent research on bio-inspired structures and materials for energy absorption applications. Composites Part B, 181.
- Hannan, M. A., Azidin, F. A., & Mohamed, A. (2014). Hybrid electric vehicles and their challenges: A review. Renewable and Sustainable Energy Reviews, 29, 135–150. https://doi.org/https://doi.org/10.1016/j.rser.2013.08.097
- Hazimi, H., Ubaidillah, Setiyawan, A. E. P., Ramdhani, H. C., Saputra, M. Z., & Imaduddin, F. (2018). Vertical bending strength and torsional rigidity analysis of formula student car chassis. AIP Conference Proceedings, 1931(1), 030050. https://doi.org/10.1063/1.5024109
- Hidalgo, E. S. (2019). Adapting the scrum framework for agile project management in science: case study of a distributed research initiative. Heliyon, 5(3), e01447. https://doi.org/https://doi.org/10.1016/j.heliyon.2019.e01447
- Hirsch, J. (2011). Aluminium in innovative light-weight car design. Materials Transactions, 52(5), 818–824. https://doi.org/10.2320/matertrans.L-MZ201132
- Hirsch, J. (2014). Recent development in aluminium for automotive applications. Transactions of Nonferrous Metals Society of China, 24(7), 1995–2002. https://doi.org/https://doi.org/10.1016/S1003-6326(14)63305-7
- Holweg, M. (2008). The evolution of competition in the automotive industry. In Build To Order: The Road to the 5-Day Car (pp. 13–34). Springer London. https://doi.org/10.1007/978-1-84800-225-8_2
- Homes, J. (2016, April 14). Next BMW X5 to Use 7 Series “CLAR” Platform. Automobile Magazine. https://www.motortrend.com/news/report-next-bmw-x5-use-7-series-clar-platform/
- Hossain, E., Babar, M. A., & Paik, H. (2009). Using Scrum in Global Software Development: A Systematic Literature Review. 2009 Fourth IEEE International Conference on Global Software Engineering, 175–184. https://doi.org/10.1109/ICGSE.2009.25
- Hou, W., Shan, C., Yu, Y., Hu, P., & Zhang, H. (2017). Modular platform optimization in conceptual vehicle body design via modified graph-based decomposition algorithm and cost-based priority method. Structural and Multidisciplinary Optimization, 55(6), 2087–2097. https://doi.org/10.1007/s00158-016-1629-5
- Jiang, P., Hu, Y.-C., Yen, G.-F., & Tsao, S.-J. (2018). Green supplier selection for sustainable development of the automotive industry using grey decision-making. Sustainable Development, 26(6), 890–903. https://doi.org/https://doi.org/10.1002/sd.1860
- Junk, S., & Rothe, N. (2022). Lightweight design of automotive components using generative design with fiber-reinforced additive manufacturing. Procedia CIRP, 109, 119–124. https://doi.org/https://doi.org/10.1016/j.procir.2022.05.224
- Kale, H. N., & Dhamejani, C. L. (2015). DESIGN PARAMETERS OF DRIVER SEAT IN AN AUTOMOBILE. In IJRET: International Journal of Research in Engineering and Technology. http://www.ijret.org
- Kallioras, N. Ath., & Lagaros, N. D. (2020). DzAIℕ: Deep learning based generative design. Procedia Manufacturing, 44, 591–598. https://doi.org/https://doi.org/10.1016/j.promfg.2020.02.251
- Kazi, R. H., Grossman, T., Cheong, H., Hashemi, A., & Fitzmaurice, G. (2017). DreamSketch: Early stage 3D design explorations with sketching and generative design. UIST 2017 - Proceedings of the 30th Annual ACM Symposium on User Interface Software and Technology, 401–414. https://doi.org/10.1145/3126594.3126662
- Ketterman, S. (n.d.). Data-driven Design and Generative Design – An Overview. Designers. Retrieved November 14, 2023, from https://www.toptal.com/designers/product-design/data-driven-generative-design-overview
- Khademian, nima, & Peimaei, Y. (2020, February 5). Lightweight materials (LWM) in transportation especially application of aluminum in light weight automobiles (LWA). International Conference on Interdisciplinary Studies in Technology.
- Kokkolaras, M., Fellini, R., Kim, H. M., Michelena, N. F., & Papalambros, P. Y. (2002). Extension of the target cascading formulation to the design of product families. Structural and Multidisciplinary Optimization, 24(4), 293–301. https://doi.org/10.1007/s00158-002-0240-0
- Krish, S. (2011). A practical generative design method. Computer-Aided Design, 43(1), 88–100. https://doi.org/https://doi.org/10.1016/j.cad.2010.09.009
- Kumar Jauhar, S., Jauhar, S., Asthankar, K. M., & Kuthe, A. M. (2012). Cost benefit analysis of Rapid Manufacturing in Automotive Industries 1. In Advances in Mechanical Engineering and its Applications (AMEA) (Vol. 181, Issue 3). www.worldsciencepublisher.org
- Kuziak, R., Kawalla, R., & Waengler, S. (2008). Advanced high strength steels for automotive industry. Archives of Civil and Mechanical Engineering, 8(2), 103–117. https://doi.org/10.1016/S1644-9665(12)60197-6
- Lampón, J. F. (2023). Efficiency in design and production to achieve sustainable development challenges in the automobile industry: Modular electric vehicle platforms. Sustainable Development, 31(1), 26–38. https://doi.org/10.1002/sd.2370
- Lampón, J. F., Cabanelas, P., & González Benito, J. (2015). The impact of implementation of a modular platform strategy in automobile manufacturing networks. http://webs.uvigo.es/infogen
- Lampón, J. F., & Rivo-López, E. (2022). Modular product architecture implementation and decisions on production network structure and strategic plant roles. Production Planning & Control, 33(15), 1449–1464. https://doi.org/10.1080/09537287.2021.1877367
- Leary, M. (2020). Generative design. Design for Additive Manufacturing, Chapter 2, 203–222. https://doi.org/10.1016/b978-0-12-816721-2.00007-5
- Lei, H., Ganjeizadeh, F., Jayachandran, P. K., & Ozcan, P. (2017). A statistical analysis of the effects of Scrum and Kanban on software development projects. Robotics and Computer-Integrated Manufacturing, 43, 59–67. https://doi.org/https://doi.org/10.1016/j.rcim.2015.12.001
- Lightweight heavy impact. (2012). McKinsey&Company.
- Mallick, P. K. (2020). Materials, design and manufacturing for lightweight vehicles. Woodhead publishing.
- Marinov, M., Amagliani, M., Barback, T., Flower, J., Barley, S., Furuta, S., Charrot, P., Henley, I., Santhanam, N., Finnigan, G. T., Meshkat, S., Hallet, J., Sapun, M., & Wolski, P. (2019). Generative Design Conversion to Editable and Watertight Boundary Representation. CAD Computer Aided Design, 115, 194–205. https://doi.org/10.1016/j.cad.2019.05.016
- Market Research Report. (2018). Automotive Chassis Market by Chassis Type, Material, Electric Vehicle, Vehicle Type and Region - Global Forecast to 2025. In Markets and Markets.
- Market Research Report. (2023). Automotive Chassis Market Size, Share & COVID-19 Impact Analysis, by Vehicle Type, by Chassis Type and Regional Forecast, 2023-2030. In Fortune Business Insights.
- Marsh, J. (2013). Efficient Modular Platform 2 The New Vehicle Platform by PSA Peugeot Citroën Platform: definition and purpose. Citroenet. www.citroenet.org.uk/miscellaneous/emp2/emp2.html
- Mehta, P. S., Solis Ocampo, J., Tovar, A., & Chaudhari, P. (2016). Bio-Inspired Design of Lightweight and Protective Structures. SAE Technical Papers. https://doi.org/10.4271/2016-01-0396
- Mendes Costa, P. (2020). Chassis Loading Scenarios.
- Milliken, W., & Milliken, D. (1995). Race Car Vehicle Dynamics. SAE International.
- Modi, S. (2016). Material Qualification in the Automotive Industry. www.cargroup.org
- Modular Transverse Matrix. (n.d.). Volkswagen Newsroom. Retrieved December 5, 2023, from https://www.volkswagen-newsroom.com/en/modular-transverse-matrix-3655
- Morandini, M., Coleti, T. A., Oliveira, E., & Corrêa, P. L. P. (2021). Considerations about the efficiency and sufficiency of the utilization of the Scrum methodology: A survey for analyzing results for development teams. Computer Science Review, 39, 100314. https://doi.org/https://doi.org/10.1016/j.cosrev.2020.100314
- Muehlbauer, M., Song, A., & Burry, J. (2017). Towards Intelligent Control in Generative Design.
- Muffatto, M., & Roveda, M. (2000). Developing product platforms: analysis of the development process. Technovation, 20(11), 617–630. https://doi.org/https://doi.org/10.1016/S0166-4972(99)00178-9
- Naik, A. (2016). What Is Volkswagen’s MLB Platform All About? Car and Bike. https://www.carandbike.com/news/what-is-volkswagens-mlb-platform-all-about-1449884
- New CMP Platform. (2018). The New Modular, Multi-energy Platform for Groupe PSA-Groupe PSA CMP: The New Modular, Multi-energy Platform for Groupe PSA. Stellantis. https://www.groupe-psa.com/en/newsroom/corporate-en/cmp-modular-platform/
- Nissan Motor Corporation. (2013). Common Module Family (CMF): A New Approach to Engineering for the Renault-Nissan Alliance. In Nissan Motor Corporation.
- Ntintakis, I., & Stavroulakis, G. E. (2020). Progress and recent trends in generative design. MATEC Web Conf., 318. https://doi.org/10.1051/matecconf/202031801006
- Oh, S., Jung, Y., Kim, S., Lee, I., & Kang, N. (2019). Deep generative design: Integration of topology optimization and generative models. Journal of Mechanical Design, Transactions of the ASME, 141(11). https://doi.org/10.1115/1.4044229
- Oomen, S., De Waal, B., Albertin, A., Ravesteyn, P., & Waal, D. (2017). HOW CAN SCRUM BE SUCCESFUL? COMPETENCES OF THE SCRUM PRODUCT OWNER. http://aisel.aisnet.org/ecis2017_rp/9
- Oymak, Y. A., & Feyzullahoğlu, E. (2021). Formula Student Race Car Chassis Design and Analysis. Journal of Advanced Research in Natural and Applied Sciences, 7(2), 201–218. https://doi.org/10.28979/jarnas.957134
- Patchong, A., Lemoine, T., & Kern, G. (2003). Improving Car Body Production at PSA Peugeot Citroën. Interfaces, 33(1), 36–49. http://www.jstor.org/stable/20141221
- Piran, F. S., Lacerda, D. P., Sellitto, M. A., & Morandi, M. I. W. M. (2021). Influence of modularity on delivery dependability: analysis in a bus manufacturer. Production Planning & Control, 32(8), 688–698. https://doi.org/10.1080/09537287.2020.1776411
- Qureshi, O. M., Bertocchi, E., Qaiser, Z., & Aslam Awan, K. (2014). Frequency embedded box beam crash absorbers under oblique impacts. Thin-Walled Structures, 75, 1–7. https://doi.org/10.1016/j.tws.2013.09.020
- Refiadi, G., Aisyah, I. S., & Siregar, J. P. (2019). Trends in lightweight automotive materials for improving fuel efficiency and reducing carbon emissions. Automotive Experiences, 2(3), 78–90.
- Research and Markets. (2021, June 21). Automotive Modularization Trend Research Report 2021: Creation of Electric Modular Platforms, Reduction of the Number of Platforms, Development of Core Platforms. Cision PR Newswire.
- Ringstad, M. A., Dingsøyr, T., & Brede Moe, N. (2011). Agile Process Improvement: Diagnosis and Planning to Improve Teamwork. In R. V O‘Connor, J. Pries-Heje, & R. Messnarz (Eds.), Systems, Software and Service Process Improvement (pp. 167–178). Springer Berlin Heidelberg.
- Rosberg, J. (2008). A Requirement process for Scrum development.
- Roy, R., Souchoroukov, P., & Shehab, E. (2011). Detailed cost estimating in the automotive industry: Data and information requirements. International Journal of Production Economics, 133(2), 694–707. https://doi.org/https://doi.org/10.1016/j.ijpe.2011.05.018
- Rubin, K. S. (2012). Essential Scrum: A practical guide to the most popular Agile process. Addison-Wesley.
- Saidpour Shsaidpour, H. (2004). Lightweight High Performance Materials for Car Body Structures. NTI Technology Conference, 14.
- Seghal, B., & Gorai, P. (2012). Platform strategy shaping the future of Automotive OEMs Flexibility to drive growth. www.evalueserve.com
- Seyfried, P., Taiss, E. J. M., Calijorne, A. C., Li, F.-P., & Song, Q.-F. (2015). Light weighting opportunities and material choice for commercial vehicle frame structures from a design point of view. Advances in Manufacturing, 3(1), 19–26. https://doi.org/10.1007/s40436-015-0103-8
- Shafiee, S., Wautelet, Y., Poelmans, S., & Heng, S. (2023). An empirical evaluation of scrum training’s suitability for the model-driven development of knowledge-intensive software systems. Data & Knowledge Engineering, 146, 102195. https://doi.org/https://doi.org/10.1016/j.datak.2023.102195
- Shamsuzzoha, A., & Helo, P. (2017). Development of sustainable platform for modular product family: a case study. Production Planning & Control, 28(6–8), 512–523. https://doi.org/10.1080/09537287.2017.1309715
- Shea, K., Aish, R., & Gourtovaia, M. (2005). Towards integrated performance-driven generative design tools. Automation in Construction, 14(2), 253–264. https://doi.org/https://doi.org/10.1016/j.autcon.2004.07.002
- Singh, M., Www, W. :, & Singh, M. K. (2016). Application of Steel in Automotive Industry International Journal of Emerging Technology and Advanced Engineering Application of Steel in Automotive Industry. In Certified Journal (Vol. 9001, Issue 7). www.ijetae.com
- Sköld, M., & Karlsson, C. (2007). Multibranded Platform Development: A Corporate Strategy with Multimanagerial Challenges. Journal of Product Innovation Management, 24(6), 554–566. https://doi.org/https://doi.org/10.1111/j.1540-5885.2007.00271.x
- Society of Automotive Engineers. (2001). SAE J1100: Motor Vehicle Dimensions. CC0 1.0 Universal.
- Srivastava, A., Bhardwaj, S., & Saraswat, S. (2017). SCRUM model for agile methodology. 2017 International Conference on Computing, Communication and Automation (ICCCA), 864–869. https://doi.org/10.1109/CCAA.2017.8229928
- Subaru Global Platform. (n.d.). Subaru Canada.
- Suh, E. S., de Weck, O., Kim, I. Y., & Chang, D. (2007). Flexible platform component design under uncertainty. Journal of Intelligent Manufacturing, 18(1), 115–126. https://doi.org/10.1007/s10845-007-0008-x
- Sun, H., & Ma, L. (2020). Generative design by using exploration approaches of reinforcement learning in density-based structural topology optimization. Designs, 4(2), 1–20. https://doi.org/10.3390/designs4020010
- Tisza, M., & Czinege, I. (2018). Comparative study of the application of steels and aluminium in lightweight production of automotive parts. International Journal of Lightweight Materials and Manufacture, 1(4), 229–238. https://doi.org/https://doi.org/10.1016/j.ijlmm.2018.09.001
- Tran, M.-K., Akinsanya, M., Panchal, S., Fraser, R., & Fowler, M. (2020). Design of a Hybrid Electric Vehicle Powertrain for Performance Optimization Considering Various Powertrain Components and Configurations. Vehicles, 3(1), 20–32. https://doi.org/10.3390/vehicles
- Trzesniowski, M. (2014). Rennwagentechnik. In Springer. Springer. https://doi.org/10.1007/978-3-658-04919-5
- Turker, H., Bacha, S., & Chatroux, D. (2010). Impact of plug-in hybrid electric vehicles (PHEVs) on the French electric grid. IEEE PES Innovative Smart Grid Technologies Conference Europe, ISGT Europe. https://doi.org/10.1109/ISGTEUROPE.2010.5638948
- Tyflopoulos, E., Flem, D., Steinert, M., & Olsen, A. (2018). State of the art of generative design and topology optimization and potential research needs.
- Wesselmecking, S., Kreins, M., Dahmen, M., & Bleck, W. (2022). Material oriented crash-box design – Combining structural and material design todoc_improve specific energy absorption. Materials and Design, 213. https://doi.org/10.1016/j.matdes.2021.110357
- Whiteley, A., Pollack, J., & Matous, P. (2021). The origins of agile and iterative methods. Journal of Modern Project Management, 8(3), 21–29. https://doi.org/10.19255/JMPM02502
- Yao, S., Zhou, Y., Li, Z., Zhang, P., Cao, Y., & Xu, P. (2021). IMP-Energy absorption char lattice structure. Composite Structures.
- Zhen Hui, L. (2012). DESIGN, ANALYSIS AND EXPERIMENTAL VERIFICATION OF TUBULAR SPACEFRAME CHASSIS FOR FSAE APPLICATION [MASTER’S THESIS]. NATIONAL UNIVERSITY OF SINGAPORE.
- Zhuang, W., Li (Eben), S., Zhang, X., Kum, D., Song, Z., Yin, G., & Ju, F. (2020). A survey of powertrain configuration studies on hybrid electric vehicles. In Applied Energy (Vol. 262). Elsevier Ltd. https://doi.org/10.1016/j.apenergy.2020.114553
9. Copyright:
- This material is "Merve Sali"'s paper: Based on "DESIGNING AN INNOVATIVE MODULAR PLATFORM FOR SPORTS CARS USING THE GENERATIVE DESIGN METHOD".
- Paper Source: DOI URL is not available in the document.
This material was summarized based on the above paper, and unauthorized use for commercial purposes is prohibited.
Copyright © 2025 CASTMAN. All rights reserved.