This article introduces the paper 'Design of Lightweight Electric Vehicles' submitted to the University of Waikato
1. Overview:
- Title: Design of Lightweight Electric Vehicles
- Author: Travis de Fluiter
- Publication Year: March 2008
- Publishing Journal/Academic Society: University of Waikato (Thesis)
- Keywords: lightweight electric vehicles, Ultracommuter, titanium aluminide, automotive industry, electric vehicle design
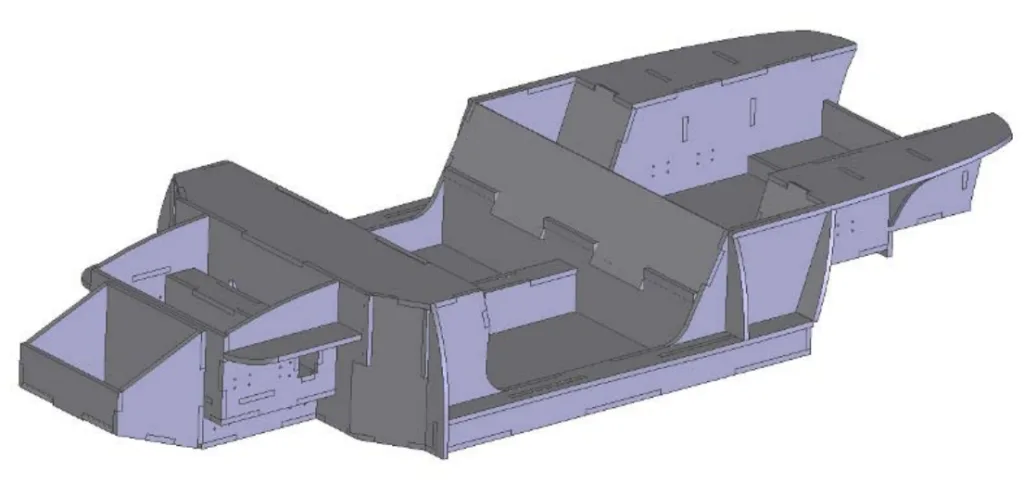
2. Research Background:
Background of the Research Topic:
The research addresses the increasing importance of lightweight electric vehicles due to the rising cost of petrol and the environmental impact of emissions from petrol-powered vehicles. The design and manufacture of lightweight electric vehicles are presented as a solution to ongoing transportation issues.
Status of Existing Research:
Existing research and literature on electric vehicles are reviewed, focusing on the history of electric vehicles, their design, and development. The literature review covers various vehicle options including hybrid vehicles, hydrogen fuel cell vehicles, bio-fuels, and battery electric vehicles, with a detailed historical overview of electric vehicle development phases from the 1880s to the 21st century. The review also touches upon lightweight vehicle design, light weight alloys in the automotive industry, and fundamental vehicle mechanics.
Necessity of the Research:
The research is necessitated by the finite nature of crude oil resources and the urgency to reduce CO2 emissions from transportation. New Zealand's reliance on personal transportation and the global trend towards stricter emission regulations and fuel efficiency standards highlight the need for alternative vehicle technologies, particularly electric vehicles. The research aims to explore the potential of lightweight design and advanced materials to enhance the viability of electric vehicles.
3. Research Purpose and Research Questions:
Research Purpose:
The primary purpose of this research is to design and build a working prototype of a lightweight electric vehicle, named the Ultracommuter, as a solution to transportation challenges. A secondary purpose is to investigate the potential use of gamma titanium aluminide components in battery electric vehicles.
Key Research:
The key research encompasses:
- Designing and manufacturing a lightweight electric vehicle prototype.
- Integrating various vehicle components and systems in a cohesive design.
- Utilizing advanced materials and manufacturing techniques for weight reduction and efficiency.
- Testing the performance and driving characteristics of the Ultracommuter.
- Exploring the potential application of gamma titanium aluminide in automotive components, specifically for electric vehicles.
Research Hypotheses:
While not explicitly stated as hypotheses, the research operates under the premise that:
- An integrated design approach is crucial for successful electric vehicle development.
- Lightweight design is essential for improving the efficiency and reducing emissions of electric vehicles.
- Virtual engineering techniques can significantly aid in the design and optimization of electric vehicles.
- Titanium aluminide components can offer performance benefits in specific electric vehicle applications due to their lightweight and material properties.
4. Research Methodology
Research Design:
The research employs a design and development approach, centered around the creation of a functional electric vehicle prototype. This involves conceptual design, detailed engineering design using Computer Aided Engineering (CAE) tools, material selection, manufacturing, and testing.
Data Collection Method:
Data collection methods are implied through the research process, including:
- Literature Review: Gathering existing knowledge on electric vehicles, lightweight design, and materials.
- Engineering Design and Simulation: Utilizing SolidWorks and FloWorks for CAD modeling, FEA, and CFD analysis.
- Prototype Testing: Performance testing of the Ultracommuter chassis and vehicle, including driving performance evaluation during the World Solar Challenge.
- Material Property Analysis: Reviewing existing data on titanium aluminide and other materials.
Analysis Method:
Analysis methods include:
- Engineering Analysis: Applying fundamental vehicle mechanics and physics principles to design and performance calculations.
- Finite Element Analysis (FEA): Using SolidWorks for structural analysis of components like suspension mounts and brake callipers.
- Computational Fluid Dynamics (CFD): Employing FloWorks for aerodynamic analysis and optimization.
- Performance Evaluation: Assessing the Ultracommuter's performance against design specifications and through real-world testing.
- Cost Analysis: Estimating manufacturing costs for different production volumes.
Research Subjects and Scope:
The primary research subject is the Ultracommuter, a prototype lightweight electric vehicle designed and built as part of this research. The scope encompasses the design, manufacturing, and testing of this vehicle, along with an investigation into the potential application of titanium aluminide in electric vehicles. The research is focused on personal transportation and the automotive industry context, particularly concerning electric vehicle technology and lightweighting strategies.
5. Main Research Results:
Key Research Results:
- Ultracommuter Prototype Development: Successful design and construction of a functional lightweight electric vehicle prototype, the Ultracommuter, capable of participating in the World Solar Challenge.
- Lightweight Design and Material Selection: Effective use of aluminium honeycomb for the chassis and fibreglass for the body shell, achieving significant weight reduction.
- Aerodynamic Optimization: Implementation of aerodynamic features like rounded front end, windscreen design, fastback rear end, full underbody, and wheel spats, resulting in a low drag coefficient (Cd of 0.24-0.25 estimated).
- Electric Drive System Integration: Successful integration of in-wheel motors and Tritium Wavesculptor controllers, demonstrating high efficiency.
- Battery System Performance: Utilization of Thundersky Li-ion batteries, showing good energy storage and thermal performance during testing.
- Titanium Aluminide Potential: Identification of potential applications for titanium aluminide components in electric vehicles, particularly in brake systems and motor components, due to their lightweight and high strength properties.
Data Interpretation:
- Testing of the Ultracommuter demonstrated driving capabilities comparable to internal combustion engine vehicles in terms of handling and acceleration, although ride comfort and high-speed stability required further refinement.
- Aerodynamic analysis and efficiency figures suggested that the Ultracommuter achieved a low drag profile, contributing to energy efficiency.
- Battery testing indicated satisfactory performance of the Thundersky Li-ion batteries, although battery management and reliability were identified as areas for improvement.
- FEA analysis of a brake calliper design indicated the potential weight saving and increased safety factor achievable with titanium aluminide compared to aluminium.
Figure Name List:
- Figure 4.1 Ultracommuter Chassis design
- Figure 4.2 Chassis pieces laid out in SolidWorks model, and water jet cut aluminium honeycomb
- Figure 4.3 Aluminium honeycomb chassis under construction
- Figure 4.4 Roll cage design
- Figure 4.5 Chassis testing by Dr Mike Duke and Jing Zhao
- Figure 4.6 Interior models of the Ultracommuter
- Figure 4.7 Ultracommuter Interior
- Figure 4.8 Ultracommuter front profile
- Figure 4.9 Windscreen bubble
- Figure 4.10 Large curved A-pillar and windscreen transitions
- Figure 4.11 The rear end of the Ultracommuter, a classic fastback design
- Figure 4.12 FloWorks analysis
- Figure 4.13 Ultracommuter surface area
- Figure 4.14 Prototype hemp composite body shell
- Figure 4.15 a) AlphaCam creating a cutting program b) An engineer simulates a virtual mill of the Ultracommuter body shell.
- Figure 4.16 a) The 5-axis CNC creates a rough cut b) the finishing cut
- Figure 4.17 Plug after molds have been lifted with mocked shut lines on it
- Figure 4.18 Ultracommuter mold, blue gelcoat coated by fibreglass layers
- Figure 4.19 a) Ultracommuter body fresh from the mold b) Aluminium strengthening bars laminated in
- Figure 4.20 Ultracommuter Split lines
- Figure 4.21 Ultracommuter bodyshell fitted to vehicle
- Figure 4.22 The Ultracommuter body shell completed in red
- Figure 4.23 Ultracommuter front suspension.
- Figure 4.24 Rear suspension design.
- Figure 4.25 Torque application of wheel motor vs conventional driveshaft
- Figure 4.26 Ackerman steering geometry of the Ultracommuter
- Figure 4.27 Pivot points of Ultracommuter steering
- Figure 4.28 Ultracommuter wheel and tyre
- Figure 4.29 High power system schematic
- Figure 4.30 Electronics layout
- Figure 4.31 Ultracommuter motor
- Figure 4.32 Tritium Wavesculptor efficiency plot (www.tritium.com.au)
- Figure 4.33 Zinc Air Issue source: www.electric-fuel.com
- Figure 4.34 Battery testing rig
- Figure 4.35 Cell discharge curves for Thundersky cells.
- Figure 4.36 Ultracommuter battery pack
- Figure 4.37 Ultracommuter Charging on WSC
- Figure 4.38 Ultracommuter battery monitoring – Labview and DAQ card
- Figure 4.39 Ultracommuter range verse velocity graph
- Figure 4.40 Ultracommuter LPE lighting
- Figure 5.1 Ultracommuter driving on WSC 2007
- Figure 6.1 γ-TiAl structure (Leyens & Peters, 2006)
- Figure 6.2 Comparions of lightweight materials (Leyens & Peters, 2006)
- Figure 6.3 The 1956 Titanium Firebird II with a body made completely from titanium source:http://www.diseno-art.com/images/firebird_II_rear.jpg
- Figure 6.4 Ultracommuter Brake calliper FEA comparison
- Figure 7.1 Ultracommuter on a lotus chassis (courtesy of HybridAuto)
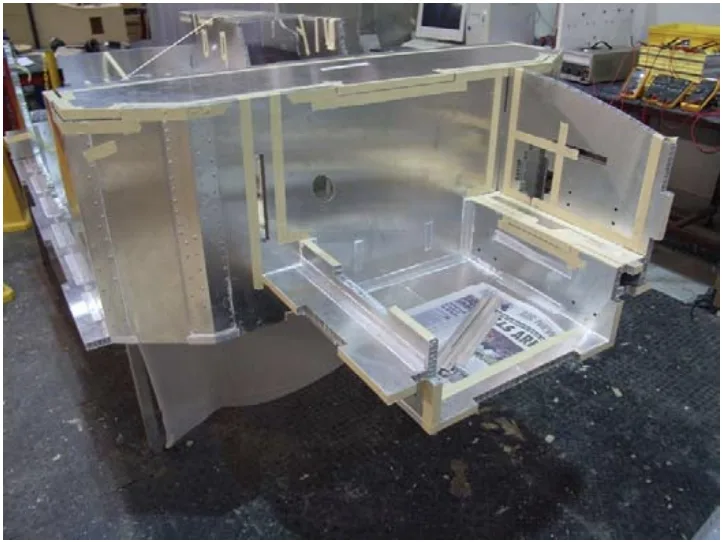
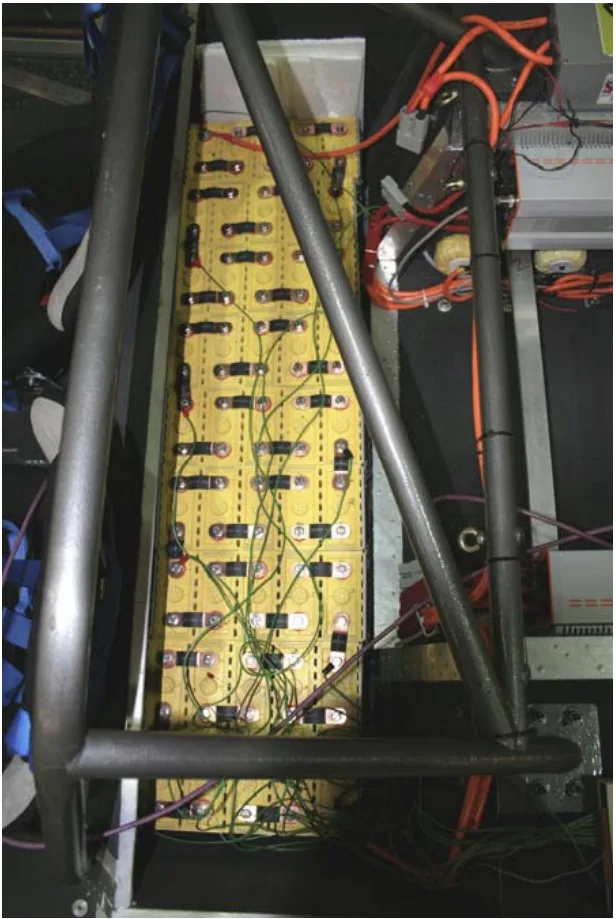
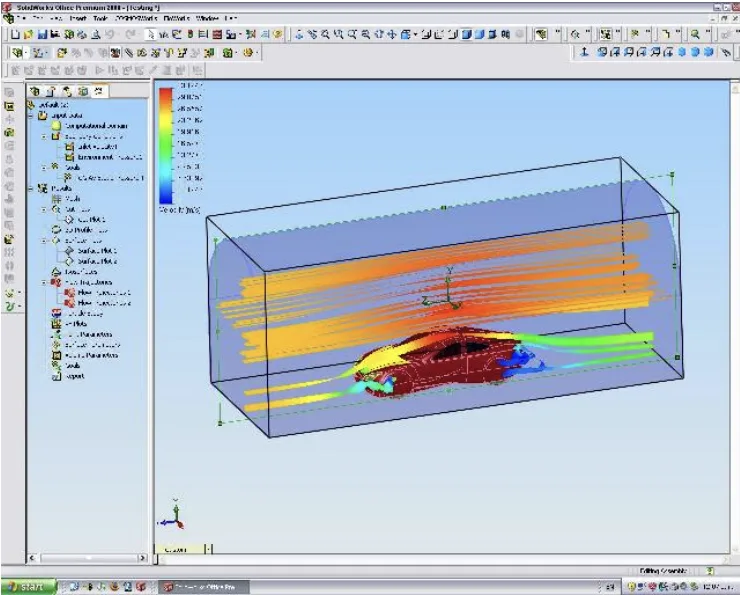
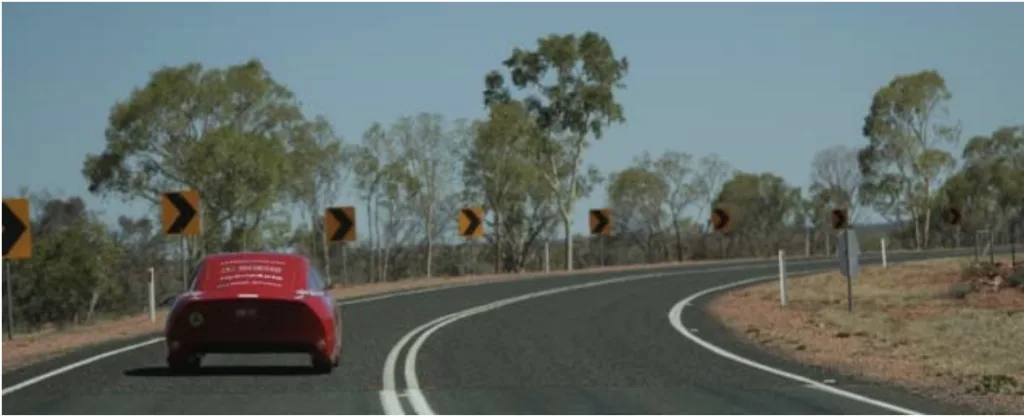
6. Conclusion:
Summary of Main Results:
The research successfully demonstrated the design and construction of a lightweight electric vehicle prototype, the Ultracommuter, showcasing the potential of integrated design, advanced materials, and virtual engineering in achieving energy efficiency. The vehicle participated in the World Solar Challenge, validating its functionality and performance in challenging conditions. The study also highlighted the potential of titanium aluminide for specific automotive applications, particularly in reducing un-sprung mass in electric vehicles.
Academic Significance of the Research:
This research contributes to the body of knowledge on lightweight electric vehicle design by providing a practical example of integrated design methodologies and the application of advanced materials. It underscores the importance of considering vehicle mechanics, aerodynamics, and material science in the development of efficient electric vehicles. The detailed documentation of the Ultracommuter project serves as a valuable case study for future research and development in this field.
Practical Implications:
The research demonstrates the feasibility of building a functional and relatively high-performance lightweight electric vehicle using available technologies and manufacturing techniques. The findings have practical implications for the automotive industry, suggesting pathways for developing more efficient and sustainable electric vehicles. The exploration of titanium aluminide applications offers insights into potential material solutions for enhancing vehicle performance and reducing weight.
Limitations of the Research
The research acknowledges limitations primarily related to cost and experience constraints during the Ultracommuter project. Specifically, the reliability of the electronics system was identified as an area needing improvement. Handling and ride comfort also require further refinement. The study also notes that the high cost of titanium aluminide currently limits its widespread application, and further research is needed to optimize manufacturing and reduce costs.
7. Future Follow-up Research:
- Directions for Follow-up Research
Future research directions include:- Battery Technology Advancement: Continued research into battery technology to achieve higher energy densities, improved battery management systems, and enhanced reliability.
- Integrated Design Optimization: Further optimization of integrated vehicle design, focusing on body shell integration with the chassis and improved component integration for weight reduction and structural efficiency.
- Aerodynamic Refinement: Detailed aerodynamic optimization, particularly in areas like wheel spats, split lines, wheel arches, and cabin airflow, to further minimize energy consumption.
- Titanium Aluminide Material Research: Focused research on manufacturing and production methods for cast and PM titanium aluminide parts, as well as comprehensive testing of material wear and thermal properties for automotive applications.
- Suspension and Handling Improvement: Further development and refinement of the suspension system to enhance ride comfort and high-speed stability.
- Areas Requiring Further Exploration
- Long-term reliability and durability testing of electric vehicle components and systems.
- Cost-effective manufacturing methods for lightweight electric vehicles and advanced materials.
- Comprehensive life cycle assessment of electric vehicles, considering material production, vehicle operation, and end-of-life disposal.
- Exploration of regenerative braking systems to potentially replace mechanical braking systems and further reduce un-sprung mass.
8. References:
- Allan, R. (2005). Setting the standard for hybrid cars. Electronic design, 53(25), 41.
- Anderson, J., & Anderson, C. (2005). Electric and Hybrid cars a history. North Carolina: McFarland and company.
- Ashley, S. (1996). Composite car stuctures pass the crash test. Mechanical Engineering, 118(12), 59.
- Ashley, S. (1997). Lightweight car prototypes. Mechanical Engineering, 119(5), 8.
- Aucock, R. (2007). Electric Potential. Automotive Engineer, 32(7), 20.
- Audi R8: the design [Electronic (2007). Version]. Retrieved 22/1/07 from http://www.carbodydesign.com.
- Australia's Electricity Supply. (2007).
- AYRLITE 2022 Data Sheet. (2007).).
- Bernard, S. (2008). Toyota Prius sales pass Ford Explorer in US. Retrieved 10/1/08, from www.ft.com.
- Bickerstaffe, S. (2006). Mixed Messages. Automotive Engineer.
- Bickerstaffe, S. (2007a). Racing Cells. Automotive Engineer, 32(10), 34-35.
- Bickerstaffe, S. (2007b). Weight savings all round. Automotive Engineer, 32(10).
- Biofuels. (2005). Retrieved. from www.eeca.govt.nz.
- Blanco, A. (2004). Putting the :Pedalk to Composites". Plastics Engineering, 60(3), 10.
- Body in White [Electronic (2008). Version]. Retrieved 6/3/08 from www.wikipedia.org.
- BP. (2007). BP Statistical Review of World Energy June 2007.
- BP Statistical Review of World Energy June 2007. (2007).).
- Brown, L. (2006). Plan B 2.0: Rescuing a Planet Under Stress and a Civilization in Trouble: W. W. Norton & Company.
- Bullis, K. (2007). Electric Cars 2.0. Technology review, 110(5), 100.
- Chang-Ran, K. (2008). Nissan CFO won't say co's shares undervalued [Electronic Version]. Reuters News. Retrieved 4/2/08.
- Chitoshi, T., Ishizaka, K., & Nagamachi, M. (1997). Kansei Engineering: A study on perception of vehicle interior image. International Journal of Industrial Ergonomics, 19, 115-128.
- Composites, A. (2007). Welcome [Electronic Version]. Retrieved 6/2/08 from http://www.ayrescom.com/.
- Concept gets a new spin. (1998). The Engineer, 25.
- Crabb, H. (1998). The virtual engineer-21st century product development. Society of manufacturing engeers.
- Dang, H., & Cowie, P. (2006). New Zealand: Energy in Brief. Retrieved. from.
- Degarmo, P., Kosher, J., & Ronald, A. (2003). Materials and Proccesses in Manufacturing: John Wiley and Sons.
- Dhameja, S. (2001). Electric Vehicle Battery Systems. New Delhi: Newnes.
- Donachie, M. (2000). Titanium: A technical guide (2 ed.). USA: ASM International.
- Donovan, J. (2005). Battery Management comes of age. Portable Design, 11(10), 28.
- Dowling, T. (1999). EV1 VIN [Electronic Version] from http://ev1-club.power.net.
- Dr Heitner, K. (2001). AC Powertrain Technology for Electric Drive Vehicles. Retrieved. from.
- Drury, B. (2001). The control techniques drives and controls handbook. Herts, UK: Institution of Electircal Engineers.
- Durbin, D.-A. (2008, 17/7/08). Green, mean, plush plug-in machines. The seattle times, p. C1.
- Eisenstein, P. (2006). Second Chance. Professional Engineering, 19(16), 29.
- Eisenstein, P. (2007). Batteries Included. Professional Engineering, 20(1), 26.
- Energizer. (2007). Energizer e2 Titanium battery [Electronic Version]. Retrieved 19th May 2007 from http://www.everything2.com.
- Fetcenko, M., Ovshinsky, S., Reichman, B., Young, K., Fierro, C., Koch, J., et al. (2007). Recent advances in NiMH battery technology. Journal of Power Sources(165).
- Field, F., & Clark, J. (1997). A practical road to lightweight cars. Technology Review, 100(1), 28.
- FlexForm. (2005). Flexform: Natural Fiber Composites Used in More Than 1.5 Million Vehicles [Electronic Version], 1. Retrieved 12/2/08 from http://plasticker.de/news/shownews.php?nr=1376.
- Fossil Fuels [Electronic (2006). Version]. Retrieved 17/10/06 from http://www.biotour.org/fossilfuels.html.
- Franco, J. (2007). Fuel Cell and Battery Briefs. Octane Week, 22(50).
- Frank, B., Tudron, James, R., Akridge, & Puglisi, V. (2004). Lithium-Sulfur Rechargeable Batteries: Characteristics, State of Development, and Applicability to Powering Portable Electronics [Electronic Version] from www.sionpower.com.
- Froes, F., Friedrich, H., Kiese, J., & Bergoint, D. (2004). Titanium in the family automobile the cost challenge. JOM, 56(2), 40-44.
- Furukawa, T. (1992). Titanium crucial for new NSX - Honda NSX sports car [Electronic Version], 1. Retrieved 4/12/2007 from http://findarticles.com/p/articles/mi_m3MKT/is_n121_v100/ai_12275952.
- Gawel, R. (2006). Roadsters charges up the electric car. Electronic design.
- Gawel, R. (2007). Volt: chargers up the crowd in detroit. Electronic design, 23.
- Gebauer, K. (2005). Performance, tolerance and cost of TiAl passenger car valves.
- General Motors EV1 [Electronic (2007). Version]. Retrieved 4/2/08 from http://en.wikipedia.org.
- Goldstein, J., Brown, I., & Koretz, B. (1999, May 1999). New Developments in the Electric Fuel Zinc-Air System. Paper presented at the International Power Sources Symposium.
- Greaves, M., Walker, G., & Walsh, B. (2002). Design optimisation of Ironless Motors based on Magnet selection. Journal of Electrical and Electronics Engineering Australia, 22(1), 43-48.
- Griffiths, J. (2007). Hydrogen cases its state. Automotive Engineer, 32(10), 30-31.
- Happian-Smith, J. (2001). An Introduction to Modern Vehicle Design: Elsevier.
- Heitner, K. (2001). AC Powertrain Technology for Electric Drive Vehicles. Retrieved. from.
- Hoffman, J. (2007). Mazda develops first biofabric for interiors. Machine Design, 122-123.
- Honda fuel cell power: FCX. (2004).).
- Honda gets Thailand's eco-car rolling [Electronic (2007). Version]. Retrieved 27/2/08 from www.hindustantimes.com.
- Honeywill, T. (2007a). Biofuel grows up. Automotive Engineer, 32(10), 32.
- Honeywill, T. (2007b). Go-faster Green. Automotive Engineer, 32(10), 28-29.
- Howden, D. (2007, 14 June 2007). World Oil supplies are set to run out faster than expected. The Independent.
- Hucho, W.-H. (1998). Aerodynamics of Road Vehciles: Aociety of Automotive Engineers.
- Hussain, I. (2003). Electric and Hybrid Vehicles design fundamentals. Florida: CRC Press.
- Johnson, T. (2007). Hobby car technical manual. New Zealand hot rod association.
- Karden, E., Ploumen, E., Fricke, B., Miller, T., & Snyder, T. (2006). Energy storage devices for future hybrid electric vehicles. Power Sources, 168, 2-11.
- Kassner, M., & Perez-Prado, M. (2004). Fundametnals of Creep in Matals and Alloys: Elsevier.
- Kiehne, H. A. (2003). Battery Technology Handbook (2 ed.). New York: Marcel Dekker.
- King, S. (2007). Towards an Electrical Transformation of the New Zealand Light Vehicle Fleet.
- Kirsch, D. A. (2000). The Electric Vehicle and the Burden of History (1 ed. Vol. 1). London: Rutgers University Press.
- Koganti, R. (2005). Re-Engineering a Legend. Manufacturing Engineering, 135(3), 101.
- Larminie, J., & Lowry, J. (2003). Electric Vehicle Technology Explained John Wiley and Sons.
- Leyens, C., & Peters, M. (2006). Titanium and Titanium Alloys: Fundamentals and Applications: : Wiley-VCH.
- Li, J. (1996). Microstructure and properties of materials: World Scientific.
- LTSA. (2006). New Zeland motor vehicle registration statistics 2006. Palmerston North.
- Matthews, C. (1998). Case studies in engineering design. London: Wiley and sons.
- McBeath, S. (2000). Competition Car Composites: a practical handbook. Haynes Publishers.
- McQuay, P. (2001). Cast gamma TiAl alloys
- MEPs vote for tougher CO2 targets. (2007). Automotive Engineer, 32(10), 5.
- Meyera, I., Leimbachb, I., & Jaeger, C. (2007). International passenger transport and climate change: A sector analysis in car demand and associated CO2 emissions from 2000 to 2050. Elsevier.
- Mom, G. (2004). The Electric Vehicle. Baltimore: The John Hopkins University Press.
- Newton, B. (2001). Holden Delivers its cyber-age baby [Electronic Version]. Retrieved 6/2/08 from http://www1.autotrader.com.au/mellor/MELLOR.NSF/story2/2AA87A45919CBEFCCA256AE1008022DA.
- Nissan expects to build electric vehicle by 2015. (2007). Automotive Engineer, 32(9), 8.
- Payne, E. (2007). Corbin Motors [Electronic Version] from http://www.3wheelers.com/corbin.html.
- Population of New Zealand [Electronic (2008). Version]. Retrieved 7/1/08 from http://www.stats.govt.nz/populationclock.htm.
- Ramsden, D. (2006). Spaceframe propels Ford GT. Modern Casting.
- Reed, P. (2007). Miles Automotive's Electric Car Breaks Battery Barrier [Electronic Version]. Retrieved 2-3-08 from http://www.edmunds.com/advice/alternativefuels/articles/122759/article.html.
- Schoenberger, R. (2007). Myers Motors aims to produce a good electric commuter car [Electronic Version]. Retrieved 25/12/07 from http://blog.cleveland.com/business/2007/12/myers_motors_of_tallmadge_aims.html.
- Schreffler, R. (2008). Toyota Prius Turns 10. Wards Auto World, 44(1).
- Simpson, A. (2003). Comparing Future Alternative Fuels and Powetrain Technologies for Vehivles. University of Queensland.
- Small cars take bigger share of the market. (2007). Automotive Engineer, 32(10), 4.
- Smarsly, W., Baur, H., Glitz, G., Clemens, H., Khan, T., & Thomas, M. (2001). Titanium aluminides for automotive and gas turbine applications. Paper presented at the International Symposium on Structural Intermetallics, Jackson Hole, USA.
- Steele, R. (2005). LED automotive hadlamps move closer to market. Laser Focus World, 41(11), 91.
- Taniguchi, A., Fujioka, N., Ikoma, M., & Ohta, A. (2001). Development of nickel/metal-hydride batteries for EVs and HEVs. Journal of Power Sources, 117–124.
- Team 05: Timely solutions. (2005). The Engineer, 48.
- Technology And Manufacturing Process [Electronic (2003). Version] from http://www.indiainfoline.com/sect/atca/ch05.html.
- Thomas, M., Raviart, J., & Popoff, F. (2005). Cast and PM processing development in gamma aluminides. Intermetallics, 13.
- Toyota Prius tests protoype plug-in Prius in US and Japan markets. (2007). Automotive Engineer, 32(8), 10.
- Tritium 220A Inductors specification. (2007).). Brisbane.
- Tuite, D. (2007). No Ultracaps in Electric vehicles yet, but maybe there should be. Electronic Design, 24.
- UK 'green' Vehicles CO2 Emissions Directory. (2007). Hampshire
- Ulrich, K. (2003). Estimating the technology frontier for personal electric vehicles. Transportation Research.
- VanMierlo, J., & Maggetto, G. (2006). Fuel Cell or Battery: Electric Cars are the Future. Fuel Cells(2), 165-173.
- Voelcker, J. (2006). Electric Cars For Enlightened Stars. IEEE Spectrum, 43(11).
- Wan, M. (1998). Differnet types of chassis [Electronic Version]. Retrieved 27/1/08 from http://www.autozine.org/technical_school/chassis/tech_chassis.htm#Ladder.
- We drive the world's best electric car. (1994). Popular Science, 244(1), 52-59.
- Wells, H. (2007). Gone in 4s. Current Science.
- Westbrook, M. (2005). The Electric car. London: IEE.
- Worth the weight. (2004). The Engineer, 34-35.
- Yamaguchi, J. (2007). Denso turns up the heat Automotive Engineering International, 115(8), 58-60.
- Yolton, C., Habel, U., & Clemens, H. (1997). Advanced particulate materials and processes. Metal Powder Report, 52(7), 161.
9. Copyright:
- This material is "Travis de Fluiter"'s paper: Based on "Design of Lightweight Electric Vehicles".
- Paper Source: http://waikato.researchgateway.ac.nz/handle/10289/219
This material was summarized based on the above paper, and unauthorized use for commercial purposes is prohibited.
Copyright © 2025 CASTMAN. All rights reserved.