This introductory paper is the research content of the paper ["Design and Computational Analysis of Compound Castings and other Multi-Material Structures"] published by ['Technische Universität Wien'].
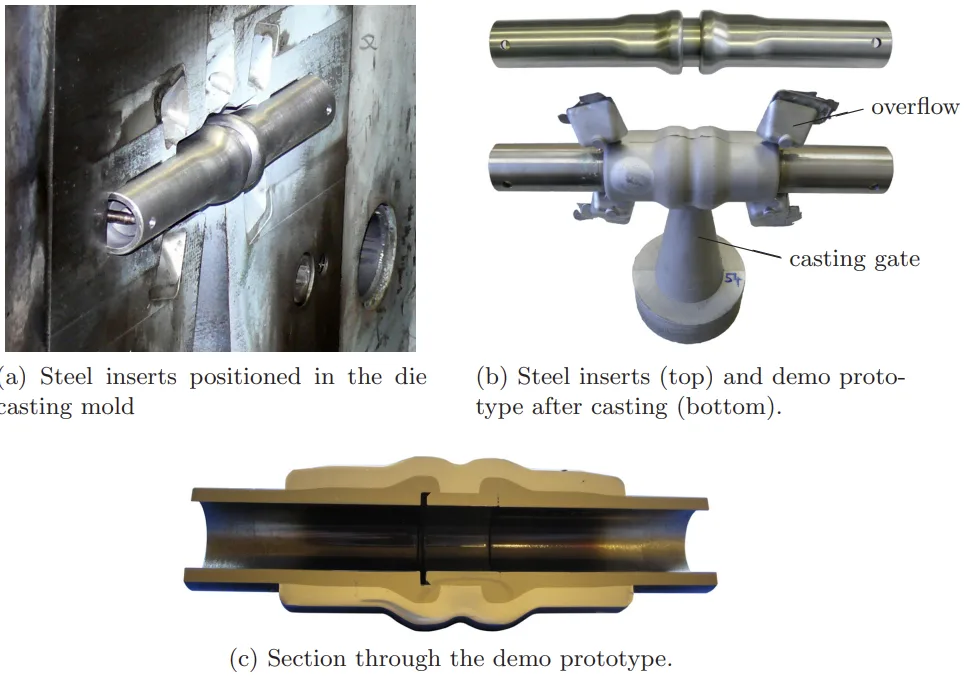
1. Overview:
- Title: Design and Computational Analysis of Compound Castings and other Multi-Material Structures
- Author: Dipl.-Ing. Robert D. Bitsche
- Publication Year: April 2009
- Publishing Journal/Academic Society: Technische Universität Wien
- Keywords: compound casting, multi-material structures, quenching simulation, thermal contact conductance, finite element analysis, stress singularities.
2. Abstracts / Introduction
The multi-material lightweight design concept strives to use the “best” material and manufacturing process for each part of a structure in order to combine the advantages of different materials. Obviously, joining techniques play a major role in the manufac turing of these structures.
The compound casting process allows for the joining of a casting to other parts during the casting process. That is, the casting process serves both as a production and a joining process. The aim of this thesis is to develop computational methods for the analysis and design of compound castings and other multi-material structures. Both finite element methods and asymptotic analysis techniques are used.
During the quenching (or cooling) of a compound casting residual stresses develop due to the inhomogeneous transient temperature field and the dissimilar coefficients of thermal expansion of the materials involved. As these stresses determine the frictional connection and other important characteristics (e.g. the fatigue life) of the structure, the simulation of the quenching process is of central importance. In the case of purely contacting interfaces, i.e., if no metallurgical bonding exists, the heat transfer at the interface is either by contact or through the gap, and the thermal contact conductance at the bimaterial interface of the compound casting depends on contact pressure and gap opening.
A major finding of this thesis is that, in general, the consideration of this dependence is crucial to the simulation of the quenching process of compound castings. During the quenching process gaps can open up at the bimaterial interface even if the structure is geometrically simple. The opening of the gap severely reduces the thermal contact conductance and forces heat to flow mainly parallel to the open gap.
Practical examples of steel-aluminum compound castings with form-locking and/or frictional connection are presented. In general, the strength of these connections could be well predicted by the finite element simulations. Local stress concentrations can occur due to the abrupt change in material properties at the interface of a multi-material structure. Under the assumptions of linear elasticity theory, these stress concentrations can manifest themselves as stress singularities.
The dependence of the order of these singularities on geometrical and material parameters is examined in a systematic way and “design charts” are developed by which the order of the stress singularity can be directly registered. Using these charts, geometry modifications can be determined that either minimize the order of the stress singularity or lead to a regular stress field.
Often, great improvements can be achieved through comparatively small and local modifications of the geometry. Keywords: compound casting, multi-material structures, quenching simulation, ther mal contact conductance, finite element analysis, stress singularities.
3. Research Background:
Background of the Research Topic:
- The multi-material lightweight design concept aims to utilize the "best" material and manufacturing process for each structural component to maximize the benefits of diverse materials. Joining technologies are crucial in manufacturing these structures. Compound casting is a process that joins castings to other parts during the casting process itself, serving as both a production and joining method.
Status of Existing Research:
- Achieving a perfect, continuous metallurgical bond in industrial compound casting is challenging. Material-locking connections are often used alongside form-locking or frictional connections. However, cracks in brittle intermetallic layers can propagate along interfaces and deflect into adjacent materials, potentially reducing load-bearing capacity compared to purely form-locking or frictional connections.
Necessity of the Research:
- Residual stresses develop during the quenching of compound castings due to inhomogeneous temperature fields and differing thermal expansion coefficients. These stresses are critical as they influence the frictional connection and structural characteristics like fatigue life. Simulating the quenching process is therefore essential. Understanding and managing thermal contact conductance at bimaterial interfaces is also crucial for accurate quenching simulations, especially in the absence of metallurgical bonding.
4. Research Purpose and Research Questions:
Research Purpose:
- The primary aim of this thesis is to develop computational methods for analyzing and designing compound castings and multi-material structures. This involves employing both Finite Element Methods and asymptotic analysis techniques to address the complexities of these structures.
Key Research:
- Development of computational methods for analysis and design of compound castings.
- Investigation of residual stress development during quenching of compound castings.
- Analysis of thermal contact conductance at bimaterial interfaces during quenching.
- Examination of stress singularities at multi-material interfaces and development of "design charts".
- Application of finite element models for simulating quenching, machining, and mechanical testing of steel-aluminum compound castings.
5. Research Methodology
Research Design:
- This research employs computational methods, combining finite element analysis and asymptotic analysis techniques to investigate compound castings and multi-material structures.
Data Collection Method:
- The research relies on computational simulations using material properties and established theoretical models. Experimental data from mechanical testing of steel-aluminum compound castings are used for validation of the simulations.
Analysis Method:
- Finite Element Analysis (FEA): Used for simulating quenching, machining, and mechanical testing processes. Non-linear FEA is employed, considering thermo-elastic-plastic material behavior and thermal contact conductance.
- Asymptotic Analysis: Applied to investigate stress singularities at multi-material interfaces, developing analytical expressions and "design charts".
Research Subjects and Scope:
- Materials: Steel (S355, C45E) and Aluminum alloy (A356.0) compound castings.
- Processes: Quenching and heat treatment processes, machining operations, mechanical testing (tensile and push-out tests).
- Phenomena: Residual stress, thermal contact conductance, stress singularities, ductile failure.
- Geometries: Simple step-bars with axisymmetric inserts and a demo prototype of a compound casting.
6. Main Research Results:
Key Research Results:
- Thermal Contact Conductance: Consideration of variable thermal contact conductance, dependent on contact pressure and gap opening, is crucial for accurate quenching simulations of steel-aluminum compound castings without material-locking connections. Gaps at bimaterial interfaces significantly reduce thermal contact conductance, forcing heat to flow parallel to the gap.
- Stress Singularities: "Design charts" were developed to directly determine the order of stress singularities at multi-material interfaces based on geometrical and material parameters. These charts aid in geometry modifications to minimize stress singularities or achieve regular stress fields.
- Validation: Finite element simulations, incorporating variable thermal contact conductance and material models, effectively predicted the strength and failure modes of steel-aluminum compound castings in practical examples.
Analysis of presented data:
- Figure 2.2 illustrates the schematic dependence of heat transfer coefficient during quenching.
- Figure 2.6 shows the 0.2% proof stress of A356.0 in different tempers.
- Figure 3.2 shows the ratio of real to apparent contact area as a function of contact pressure.
- Figure 3.3 shows contact conductance due to conduction through actual contact spots.
- Figure 3.9 shows total thermal contact conductance at a steel-aluminum interface.
- Figure 6.6 illustrates temperature, radial stress and contact pressure during quenching simulation.
- Figure 6.8 compares measured and simulated force-displacement curves for push-out tests.
- Figure 7.9 shows circumferential residual stresses in the cast node after quenching and after removal of casting gate.
- Figure 7.10 shows Von Mises equivalent stress after removal of the casting gate.
- Figure 7.13 compares measured and simulated force-displacement curves for tensile tests.
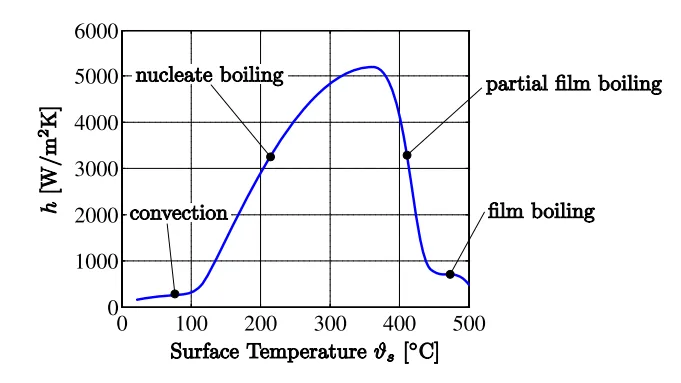
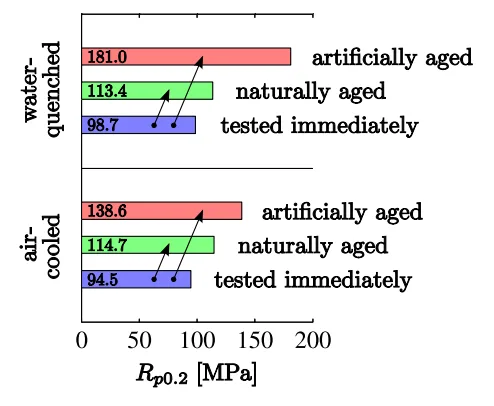
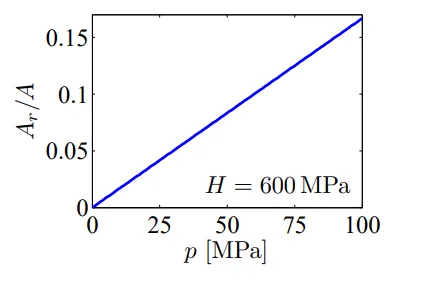
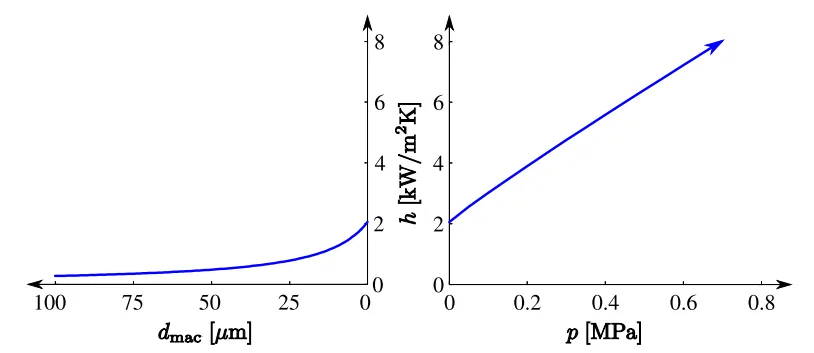
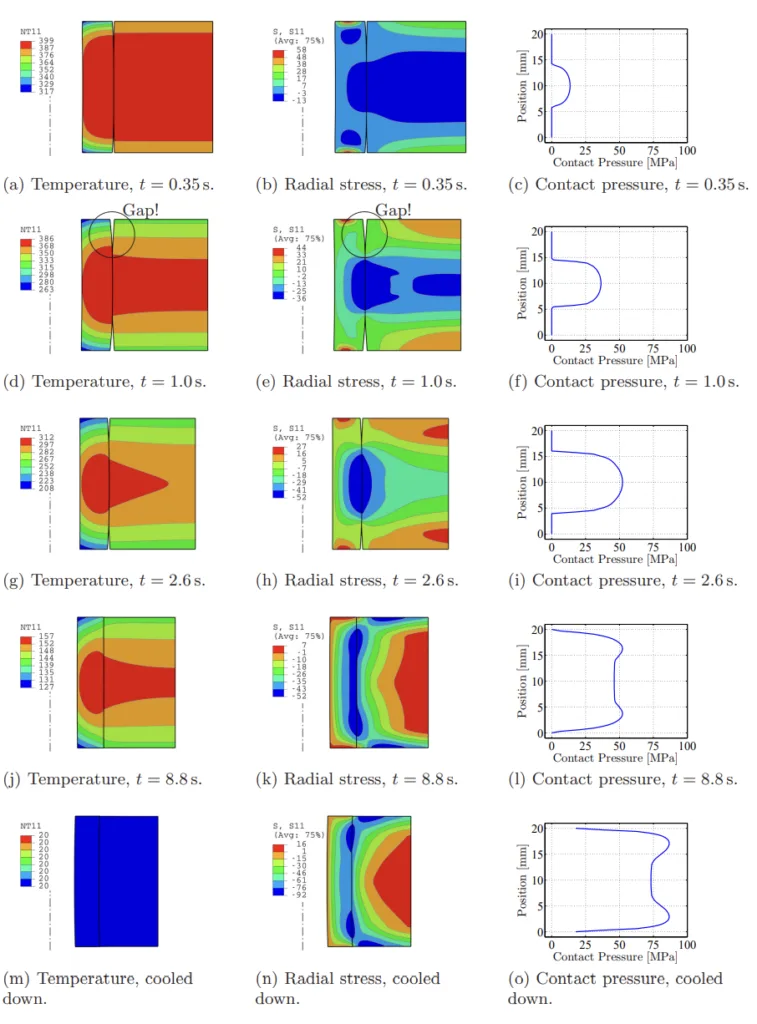
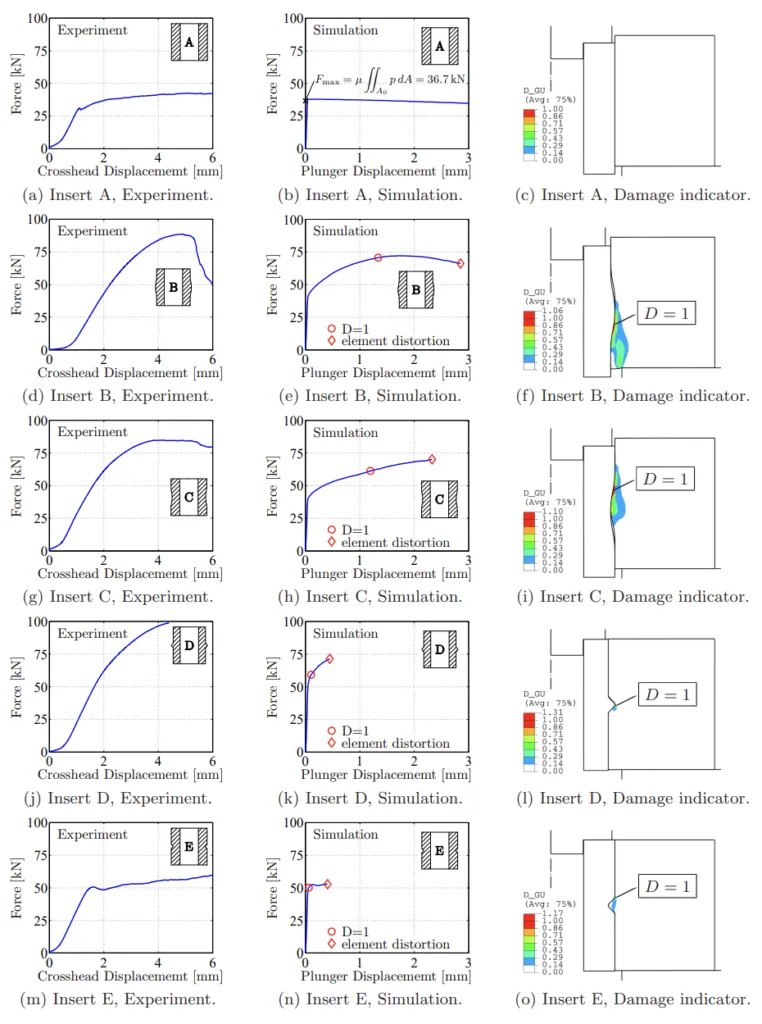
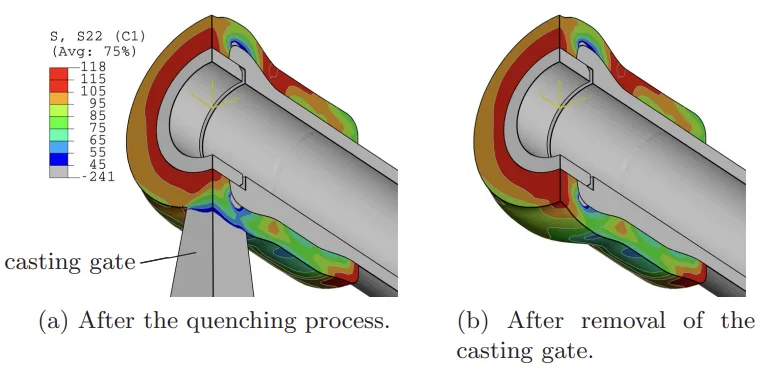
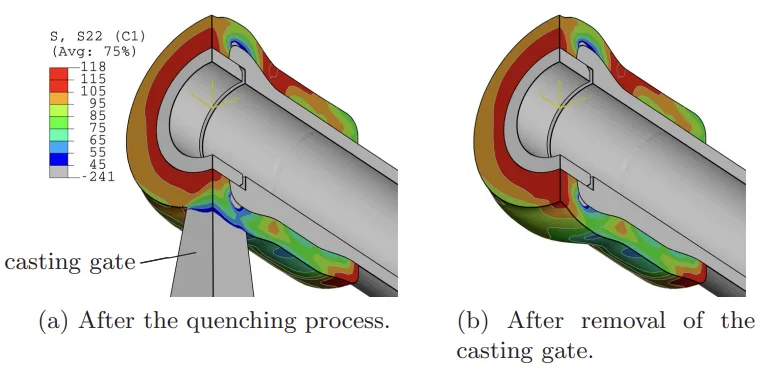
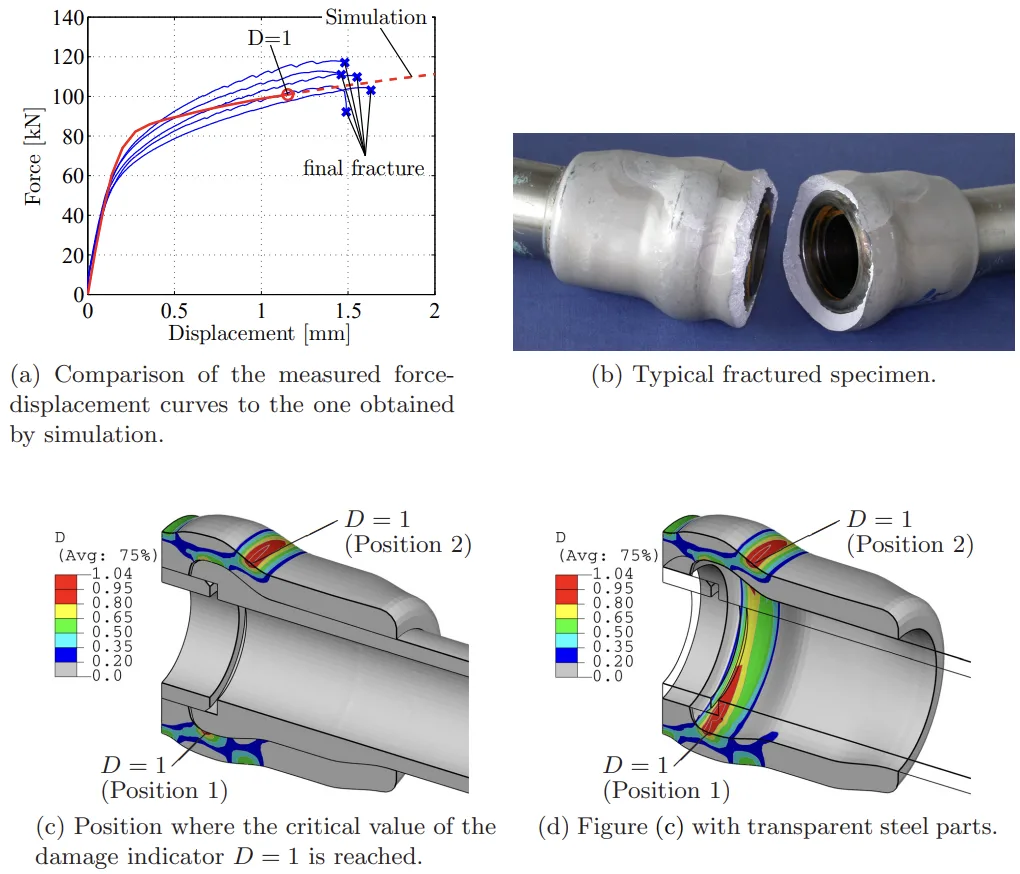
Figure Name List:
- Figure 2.2: Schematic dependence of the heat transfer coefficient h on surface temperature ϑ during quenching
- Figure 2.6: 0.2% proof stress of A356.0 in different tempers.
- Figure 3.2: Ratio of the real to the apparent area of contact as a function of contact pressure for H = 600MPa.
- Figure 3.3: Contact conductance due to conduction through the actual contact spots hs as described by Equation (3.5) and the material properties and surface parameters in Table 3.1.
- Figure 3.9: Total thermal contact conductance at a steel-aluminum interface.
- Figure 6.6: Insert A: Temperature (Celsius), radial stress (MPa) and contact pressure t seconds after immersion into the quenching water
- Figure 6.8: Push-out test: Comparison of measured force-displacement curves (left column) to the ones obtained by simulation (middle column)
- Figure 7.9: Circumferential residual stresses in the cast node.
- Figure 7.10: Von Mises equivalent stress after removal of the casting gate depicted on an exploded view of the model.
- Figure 7.13: Tensile test.
7. Conclusion:
Summary of Key Findings:
- The research successfully developed computational methods for analyzing and designing compound castings, emphasizing the importance of considering variable thermal contact conductance in quenching simulations. Design charts for stress singularities were created, offering practical guidance for geometry optimization in multi-material structures. Finite element simulations were validated against experimental data, demonstrating their predictive capability for compound casting behavior.
Academic Significance of the Study:
- This study contributes to the fundamental understanding of heat transfer and stress development in compound castings. The developed "design charts" for stress singularities and methodologies for simulating thermal contact conductance offer valuable tools for academic research in multi-material design and analysis.
Practical Implications:
- The "design charts" provide practical guidelines for engineers to design compound castings with reduced stress concentrations, enhancing durability. The validated simulation methods enable optimization of casting processes and prediction of component performance, reducing prototyping costs and improving product reliability in industries utilizing compound casting technologies.
Limitations of the Study and Areas for Future Research:
- The study acknowledges limitations in material model complexity and the assumed constancy of certain parameters in thermal contact conductance models. Future research should focus on:
- Experimentally verifying the thermal contact conductance model.
- Determining static and kinetic coefficients of friction at steel-aluminum interfaces.
- Developing more sophisticated material models, including elastic-visco-plastic constitutive models and models capturing the evolution of yield stress during natural ageing.
- Experimentally determining fracture mechanics parameters for intermetallic phases in metallurgically bonded compound castings.
8. References:
- [ASM, 1991] ASM Handbook, vol. 4, Heat Treating. ASM International.
- [Bathe, 2002] Bathe, K.-J., 2002. Finite-Elemente-Methoden. Berlin: Springer, second edn.
- [Blanke, 1989] Blanke, W., ed., 1989. Thermophysikalische Stoffgr¨oßen. Springer.
- [Blumm et al., 1998] Blumm, J., Henderson, J. B., and Hagemann, L., 1998. Measurement of the thermophysical properties of an aluminium-silicon casting alloy in the solid and molten regions. High Temperatures - High Pressures, 30:153–157.
- [Bogy, 1971] Bogy, D. B., 1971. Two edge-bonded elastic wedges of different materials and wedge angles under surface tractions. Journal of Applied Mechanics, 38(2):377–386.
- [Borrisutthekul et al., 2007] Borrisutthekul, R., Yachi, T., Miyashita, Y., and Mutoh, Y., Oct. 2007. Suppression of intermetallic reaction layer formation by controlling heat flow in dissimilar joining of steel and aluminum alloy. Materials Science and Engineering: A, 467:108–113.
- [Chen and Nisitani, 1993] Chen, D.-h. and Nisitani, H., 1993. Singular stress field near the corner of jointed dissimilar materials. Journal of Applied Mechanics, 60(3):607–613.
- [Churchman et al., 2003] Churchman, C., Mugadu, A., and Hills, D. A., 2003. Asymptotic results for slipping complete frictional contacts. European Journal of Mechanics - A/Solids, 22(6):793–800.
- [Comninou, 1976] Comninou, M., 1976. Stress singularity at a sharp edge in contact problems with friction. Journal of Applied Mathematics and Physics (ZAMP), 27:493–499.
- [Dassault Syst
emes, 2008a] Dassault Syst
emes, Apr. 2008a. Abaqus Analysis User’s Manual. Version 6.8, http://www.simulia.com. - [Dassault Syst
emes, 2008b] Dassault Syst
emes, Apr. 2008b. Abaqus Scripting User’s Manual. Version 6.8, http://www.simulia.com. - [DIN 32711-1] DIN 32711-1, Jan. 2007. Welle-Nabe-Verbindung - Polygonprofile P3G. Proposed Technical Standard.
- [Dittmann, 1995] Dittmann, A., 1995. Repetitorium der technischen Thermodynamik. Vieweg+Teubner.
- [Dundurs, 1969] Dundurs, J., 1969. Discussion of [Bogy, 1968]. Journal of Applied Mechanics, 36(3):650–652.
- [Durelli and Parks, 1972] Durelli, A. J. and Parks, V. J., 1972. Discussion of [Bogy, 1971]. Journal of Applied Mechanics, 39(1):317.
- [El Sebaie et al., 2008] El Sebaie, O., Samuel, A. M., Samuel, F. H., and Doty, H. W., Jul. 2008. The effects of mischmetal, cooling rate and heat treatment on the hardness of A319.1, A356.2 and A413.1 Al-Si casting alloys. Materials Science and Engineering: A, 486(1-2):241–252.
- [Estey et al., 2004] Estey, C. M., Cockcroft, S. L., Maijer, D. M., and Hermesmann, C., Oct. 2004. Constitutive behaviour of A356 during the quenching operation. Materials Science and Engineering: A, 383(2):245–251.
- [Fragner et al., 2006] Fragner, W., Zberg, B., Sonnleitner, R., Uggowitzer, P. J., and L¨offler, J. F., 2006. Interface reactions of Al and binary Al-alloys on mild steel substrates in controlled atmosphere. Materials Science Forum, 519–521:1157–1162.
- [Frank and Pflanzl, 1998] Frank, A. and Pflanzl, M., 1998. VDI Berichte 1384, Welle-Nabe-Verbindungen, chap. Die Norm-Polygonverbindungen P3G und P4C - Geometrische Grundlagen, Funktionsverhalten und Fertigung, pages 105–120. VDI.
- [G¨anser et al., 2001] G¨anser, H.-P., Atkins, A. G., Kolednik, O., Fischer, F. D., and Richard, O., 2001. Upsetting of cylinders: A comparison of two different damage indicators. Journal of Engineering Materials and Technology, 123:94–99.
- [Giannakopoulos et al., 1998] Giannakopoulos, A. E., Lindley, T. C., and Suresh, S., May 1998. Aspects of equivalence between contact mechanics and fracture mechanics: theoretical connections and a life-prediction methodology for fretting-fatigue. Acta Materialia, 46:2955–2968.
- [Goede et al., 2008] Goede, M., Stehlin, M., Rafflenbeul, L., Kopp, G., and Beeh, E., Dec. 2008. Super light car – lightweight construction thanks to a multi-material design and function integration. European Transport Research Review.
- [Gross and Seelig, 2007] Gross, D. and Seelig, T., 2007. Bruchmechanik. Springer, fourth edn.
- [Hancock and Mackenzie, 1976] Hancock, J. W. and Mackenzie, A. C., 1976. On the mechanisms of ductile failure in high-strength steels subjected to multi-axial stress-states. Journal of the Mechanics and Physics of Solids, 24:147–169.
- [Kammer, 2002] Kammer, C., 2002. Aluminium Taschenbuch. Aluminium-Verlag, 16th edn.
- [Kaufman and Rooy, 2005] Kaufman, J. G. and Rooy, E. L., 2005. Aluminum Alloy Castings, Properties, Processes and Applications. ASM International.
- [Kliauga et al., 2008] Kliauga, A. M., Vieira, E. A., and Ferrante, M., 2008. The influence of impurity level and tin addition on the ageing heat treatment of the 356 class alloy. Materials Science and Engineering: A, 480(1-2):5–16.
- [Kluting and Landerl, 2004] Kluting, M. and Landerl, C., 2004. Der neue Sechszylinder Ottomotor von BMW, Teil I: Konzept und konstruktiver Aufbau. MTZ, 11:868–880.
- [Lee and Barber, 2006] Lee, D. and Barber, J. R., 2006. An automated procedure for determining asymptotic elastic stress fields at singular points. The Journal of Strain Analysis for Engineering Design, 41(4):287–295.
- [Lemaitre and Desmorat, 2005] Lemaitre, J. and Desmorat, R., 2005. Engineering Damage Mechanics. Springer.
- [Loulou et al., 1999a] Loulou, T., Artyukhin, E. A., and Bardon, J. P., Jun. 1999a. Estimation of thermal contact resistance during the first stages of metal solidification process: I–experiment principle and modelisation. International Journal of Heat and Mass Transfer, 42(12):2119–2127.
- [Loulou et al., 1999b] Loulou, T., Artyukhin, E. A., and Bardon, J. P., Jun. 1999b. Estimation of thermal contract resistance during the first stages of metal solidification process: II–experimental setup and results. International Journal of Heat and Mass Transfer, 42(12):2129–2142.
- [Lumley et al., 2007] Lumley, R. N., O’Donnell, R. G., Gunasegaram, D. R., and Givord, M., Oct. 2007. Heat treatment of high-pressure die castings. Metallurgical and Materials Transactions A, 38(10):2564–2574.
- [Madhusudana, 1996] Madhusudana, C. V., 1996. Thermal Contact Conductance. Springer.
- [Maniruzzaman and Sisson, 2004] Maniruzzaman, M. and Sisson, R. D., Jr., Dec. 2004. Heat transfer coefficients for quenching process simulation. Journal de Physique IV (Proceedings), 120:521–528.
- [Mikic, 1974] Mikic, B. B., 1974. Thermal contact conductance - theoretical considerations. International Journal Of Heat And Mass Transfer, 17(2):205–214.
- [Mohr and Henn, 2007] Mohr, D. and Henn, S., Dec. 2007. Calibration of stress-triaxiality dependent crack formation criteria: A new hybrid experimental-numerical method. Experimental Mechanics, 47(6):805–820.
- [Mondolfo, 1979] Mondolfo, L. F., 1979. Aluminum Alloys, Structure and Properties. Butterworths.
- [Nikanorov et al., 2005] Nikanorov, S., Volkov, M., Gurin, V., Burenkov, Y., Derkachenko, L., Kardashev, B., Regel, L., and Wilcox, W., Jan. 2005. Structural and mechanical properties of Al-Si alloys obtained by fast cooling of a levitated melt. Materials Science and Engineering: A, 390(1-2):63–69.
- [Nowell et al., 2006] Nowell, D., Dini, D., and Hills, D. A., 2006. Recent developments in the understanding of fretting fatigue. Engineering Fracture Mechanics, 73(2):207–222.
- [O’Dowd, 2008] O’Dowd, N. P., 2008. Concise Encyclopedia of the Properties of Materials Surfaces and Interfaces, chap. Fracture at Interfaces, pages 154–160. Elsevier, first edn.
- [Papis et al., 2008] Papis, K. J. M., Hallstedt, B., L¨offler, J. F., and Uggowitzer, P. J., 2008. Interface formation in aluminium-aluminium compound casting. Acta Materialia, 56(13):3036–3043.
- [Polmear, 2006] Polmear, I., 2006. Light Alloys. Elsevier, fourth edn.
- [Potesser et al., 2006] Potesser, M., Schoeberl, T., Antrekowitsch, H., and Bruckner, J., 2006. The characterization of the intermetallic Fe-Al layer of steel-aluminum weldings. In EPD Congress 2006. The Minerals, Metals & Materials Society.
- [Reddy and Deevi, 2000] Reddy, B. V. and Deevi, S. C., Dec. 2000. Thermophysical properties of FeAl (Fe-40 at.% Al). Intermetallics, 8:1369–1376.
- [Rice, 1988] Rice, J. R., 1988. Elastic fracture mechanics concepts for interfacial cracks. Journal of Applied Mechanics, 55:98–103.
- [Rice and Tracey, 1969] Rice, J. R. and Tracey, T. M., 1969. On the ductile enlargement of voids in triaxial stress fields. Journal of the Mechanics and Physics of Solids, 17:201–217.
- [Richter, 1973] Richter, F., 1973. Stahleisen Sonderbericht: Die wichtigsten physikalischen Eigenschaften von 52 Eisenwerkstoffen. Tech. rep., Verlag Stahleisen.
- [Richter, 1991] Richter, F., 1991. Die physikalischen Eigenschaften von metallischen Werkstoffen. Metall, 45(6):582.
- [Rohloff and Zastera, 1996] Rohloff, H. and Zastera, A., eds., 1996. Physikalische Eigenschaften gebr¨auchlicher St¨ahle. Stahleisen.
- [Rometsch et al., 2003] Rometsch, P. A., Starink, M. J., and Gregson, P. J., Jan. 2003. Improvements in quench factor modelling. Materials Science and Engineering: A, 339(1-2):255–264.
- [Santos et al., 2001] Santos, C. A., Quaresma, J. M. V., and Garcia, A., Apr. 2001. Determination of transient interfacial heat transfer coefficients in chill mold castings. Journal of Alloys and Compounds, 319(1-2):174–186.
- [Schulze, 1967] Schulze, G. E. R., 1967. Metallphysik. Akademie-Verlag.
- [SEW 310, 1992] SEW 310, Aug. 1992. Physikalische Eigenschaften von St¨ahlen. Taschenbuch der Stahl-Eisen-Werkstoffbl¨atter, 10. Auflage, Stahleisen.
- [Sinclair, 2004a] Sinclair, G. B., 2004a. Stress singularities in classical elasticity–I: Removal, interpretation, and analysis. Applied Mechanics Reviews, 57(4):251–298.
- [Sinclair, 2004b] Sinclair, G. B., 2004b. Stress singularities in classical elasticity–II: Asymptotic identification. Applied Mechanics Reviews, 57(5):385–439.
- [Sritharan et al., 2000] Sritharan, T., Murali, S., and Hing, P., Jul. 2000. Synthesis of aluminium-iron-silicon intermetallics by reaction of elemental powders. Materials Science and Engineering: A, 286(2):209–217.
- [THERPRO] THERPRO. Thermo-physical Properties Database provided by the International Atomic Energy Agency. URL http://therpro.hanyang.ac.kr.
- [VDI, 2002] VDI, 2002. VDI-W¨armeatlas. VDI-Gesellschaft Verfahrenstechnik und Chemieingenieurwesen, 9th edn.
- [Wahid and Madhusudana, 2000] Wahid, S. M. S. and Madhusudana, C. V., Dec. 2000. Gap conductance in contact heat transfer. International Journal of Heat and Mass Transfer, 43(24):4483–4487.
- [Whitcomb et al., 1982] Whitcomb, J. D., Raju, I. S., and Goree, J. G., 1982. Reliability of the finite element method for calculating free edge stresses in composite laminates. Computers & Structures, 15(1):23–37.
- [Williams, 1952] Williams, M. L., 1952. Stress singularities resulting from various boundary conditions in angular corners of plates in extension. Journal of Applied Mechanics, 19:526–528.
- [Zhang et al., 2007a] Zhang, B., Maijer, D. M., and Cockcroft, S. L., 2007a. Development of a 3-D thermal model of the low-pressure die-cast (LPDC) process of A356 aluminum alloy wheels. Materials Science and Engineering: A, 464(1-2):295 – 305.
- [Zhang et al., 2007b] Zhang, L., Zhou, B., Zhan, Z., Jia, Y., Shan, S., Zhang, B., and Wang, W., Mar. 2007b. Mechanical properties of cast A356 alloy, solidified at cooling rates enhanced by phase transition of a cooling medium. Materials Science and Engineering: A, 448(1-2):361–365.
9. Copyright:
- This material is "Robert D. Bitsche"'s paper: Based on "Design and Computational Analysis of Compound Castings and other Multi-Material Structures".
- Paper Source: http://www.ub.tuwien.ac.at/
This material was created to introduce the above paper, and unauthorized use for commercial purposes is prohibited.
Copyright © 2025 CASTMAN. All rights reserved.