This article introduces the paper 'Current Trends in Metallic Materials for Body Panels and Structural Members Used in the Automotive Industry' published by 'MDPI'.
1. Overview:
- Title: Current Trends in Metallic Materials for Body Panels and Structural Members Used in the Automotive Industry
- Author: Tomasz Trzepieciński, Sherwan Mohammed Najm
- Publication Year: 2024
- Publishing Journal/Academic Society: Materials, MDPI
- Keywords: aluminium alloy; automotive industry; body panel; steel; titanium alloy
![Figure 1. Classification of steels used in the automotive industry(reproduced with permission from Reference [4]; copyright © 2024 Acta Materialia Inc. Published by Elsevier B.V. All rights reserved).](https://castman.co.kr/wp-content/uploads/image-804-1024x426.webp)
![Table 1. Selected properties of cold-rolled flat products from low-carbon steel, prepared on the basis of PN-EN 10130 [62] standard.](https://castman.co.kr/wp-content/uploads/image-805-1024x263.webp)
2. Abstracts or Introduction
Abstract: The development of lightweight and durable materials for car body panels and load-bearing elements in the automotive industry results from the constant desire to reduce fuel consumption without reducing vehicle performance. The investigations mainly concern the use of these alloys in the automotive industry, which is characterised by mass production series. Increasing the share of lightweight metals in the entire structure is part of the effort to reduce fuel consumption and carbon dioxide emissions into the atmosphere. Taking into account environmental sustainability aspects, metal sheets are easier to recycle than composite materials. At the same time, the last decade has seen an increase in work related to the plastic forming of sheets made of non-ferrous metal alloys. This article provides an up-to-date systematic overview of the basic applications of metallic materials in the automotive industry. The article focuses on the four largest groups of metallic materials: steels, aluminium alloys, titanium alloys, and magnesium alloys. The work draws attention to the limitations in the development of individual material groups and potential development trends of materials used for car body panels and other structural components.
3. Research Background:
Background of the Research Topic:
The automotive industry is driven by the need to reduce fuel consumption and emissions while maintaining vehicle performance. This necessitates the development and application of lightweight and durable materials for car body panels and load-bearing elements. The industry is characterized by mass production, making material selection crucial based on technological, material, and economic criteria. Historically, steel was the primary material, but the evolution towards lightweight equivalents like aluminium alloys, titanium alloys, and magnesium alloys is ongoing due to environmental concerns and the need for fuel efficiency.
Status of Existing Research:
Existing research and development efforts are significantly focused on Advanced High-Strength Steel (AHSS) grades, driven by projects like the Ultra-Light Steel Auto Body (ULSAB). Work related to the plastic forming of sheets made of non-ferrous metal alloys, particularly aluminium alloys, has also increased in the last decade. There is continuous optimization of steel compositions and microstructures, alongside growing interest in metal-based laminates and hybrid structures combining different materials to achieve desired stiffness and weight reduction.
Necessity of the Research:
The research is necessary to provide an up-to-date systematic overview of metallic materials applications in the automotive industry, specifically focusing on steels, aluminium alloys, titanium alloys, and magnesium alloys. Understanding the current trends, limitations, and potential development trends for these material groups is crucial for guiding future material selection and development efforts in the automotive sector, especially considering the increasing demands for lightweighting and sustainability.
4. Research Purpose and Research Questions:
Research Purpose:
This article aims to present an up-to-date overview of the applications of metallic materials in car body panels and bearing components within the automotive industry. It focuses on the four largest groups of metallic materials: steels, aluminium alloys, titanium alloys, and magnesium alloys. The study also aims to highlight the limitations in the development of individual material groups and potential development trends for materials used in car body panels and other structural components.
Key Research:
The key research areas explored in this paper are:
- Current applications of steels, aluminium alloys, titanium alloys, and magnesium alloys in automotive body panels and structural members.
- Classification and properties of different grades within each material group (e.g., Low-Strength Steels, High-Strength Steels, Advanced High-Strength Steels for steels).
- Processing methods and factors influencing the formability and application of these metallic materials.
- Limitations and potential development trends for each material group in the automotive industry.
Research Hypotheses:
The paper is a review article and does not explicitly state research hypotheses. It systematically reviews and summarizes existing knowledge and trends in the application of metallic materials in the automotive industry.
5. Research Methodology
Research Design:
This research employs a systematic review design. It is a literature review that compiles and analyzes existing research and publications related to metallic materials in the automotive industry.
Data Collection Method:
The data collection method involves gathering information from existing literature, including research articles, industry reports, standards, and publications from academic societies and journals related to materials science, automotive engineering, and manufacturing. The references listed at the end of the paper indicate the sources used for data collection.
Analysis Method:
The analysis method is qualitative and descriptive. The authors systematically reviewed and synthesized information from various sources to provide an overview of current trends, applications, limitations, and future directions for metallic materials in the automotive industry. The paper classifies materials into groups and subgroups, describes their properties, and discusses their applications based on the reviewed literature.
Research Subjects and Scope:
The research subjects are metallic materials used in the automotive industry, specifically for car body panels and structural members. The scope is limited to the four largest groups of metallic materials: steels, aluminium alloys, titanium alloys, and magnesium alloys. The review focuses on the applications, properties, limitations, and development trends of these materials within the automotive context.
6. Main Research Results:
Key Research Results:
- Steels: The paper details the evolution of steel usage from low-carbon steels to advanced high-strength steels (AHSS), including different generations of AHSS (first, second, and third generation). It outlines various steel grades like IF steels, DP steels, TRIP steels, TWIP steels, and Press-Hardened steels, discussing their properties, strengthening mechanisms, and applications in body structures, frames, and reinforcements. Corrosion protection methods for steel are also discussed.
- Aluminium Alloys: The review covers the increasing importance of aluminium alloys due to their low density and corrosion resistance. It classifies aluminium alloys into series (1xxx to 9xxx), detailing their alloying elements, properties, and applications. The paper highlights 5xxx and 6xxx series as most relevant for automotive body components and discusses specific alloys and their applications in body panels, structural parts, and closures.
- Titanium Alloys: Titanium and its alloys are presented as materials with high specific strength and corrosion resistance, suitable for high-performance applications. The paper discusses different grades and classifications of titanium alloys (alpha, alpha-beta, beta), their properties, and applications in exhaust systems, suspension springs, body parts, and frames, particularly in high-end and niche vehicles.
- Magnesium Alloys: Magnesium alloys are highlighted for their extremely low density and high damping capacity. The review discusses the challenges in forming magnesium alloys due to their low plasticity but notes their growing use in drive systems, vehicle rims, brackets, profiles, and interior door components. Specific magnesium alloys and their applications in automotive structures are listed.
Analysis of presented data:
The paper presents data primarily in a descriptive format, supported by tables and figures directly referenced from other publications. Tables list specific grades of steels, aluminium, titanium, and magnesium alloys along with their applications in various car components and references to the source material. Figures illustrate material classifications (steels, titanium alloys), processing methods (QP steel thermal cycle, TWIP steel fabrication), and examples of material applications (Audi AL2 body structure, Bugatti titanium components). Tensile strength and elongation data for different steel grades are presented graphically (Figure 1), and tensile curves for different stainless steel families are compared (Figure 6).
Figure Name List:
![Figure 2. The influence of bake hardening on stress (reproduced with permission from Reference [78]; copyright © 2024 Elsevier Ltd. All rights reserved).](https://castman.co.kr/wp-content/uploads/image-806-png.webp)
![Figure 3. Typical microstructure of (a) HSLA and (b) DP steel (reproduced with permission from Reference [31]; copyright © 2024 Woodhead Publishing Limited. All rights reserved).](https://castman.co.kr/wp-content/uploads/image-807-1024x435.webp)
![Figure 4. Fabrication procedure of the cold-rolled LC/TWIP/LC and IF/TWIP/IF sheets (reproduced with permission from Reference [102]; copyright © 2024 Elsevier B.V. All rights reserved).](https://castman.co.kr/wp-content/uploads/image-808-1024x428.webp)
![Figure 5. Thermal cycle for the quenching and partitioning process (Ac3—transformation temperature, RT—room temperature), prepared with permission from Reference [132] (copyright © 2024 Acta Materialia Inc. Published by Elsevier Ltd. All rights reserved).](https://castman.co.kr/wp-content/uploads/image-809-png.webp)
![Figure 6. Comparison of tensile curves of selected corrosion-resistant steel families (reproduced with permission from Reference [139] (copyright © 2024 Elsevier Ltd. All rights reserved).](https://castman.co.kr/wp-content/uploads/image-810-png.webp)
![Figure 7. Aluminium alloy-specific Chinese automotive demand estimates. Top to bottom, the three rows show No-LT (a–c), Middle-LT (d–f), and High-LT (g–i). Three columns show Low-PN, Middle-PN, and High-PN situations from left to right. Where LT = light-weighting-trend and PN = penetration scenario (reproduced with permission from Reference [218]; copyright © 2024 The Author(s). Published by Elsevier B.V.).](https://castman.co.kr/wp-content/uploads/image-811-1024x846.webp)
![Figure 8. Audi AL2 aluminium body structure (reproduced with permission from Reference [251]; copyright © 2024 Elsevier Science S.A. All rights reserved).](https://castman.co.kr/wp-content/uploads/image-812-png.webp)
![Figure 9. Baseline part and demonstration part geometry (reproduced with permission from Reference [279]; copyright © 2024, The Minerals, Metals & Materials Society).](https://castman.co.kr/wp-content/uploads/image-803-png.webp)
![Figure 10. Forming trial results on 7xxx alloy at various forming temperatures (reproduced with permission from Reference [279]; copyright © 2024, The Minerals, Metals & Materials Society).](https://castman.co.kr/wp-content/uploads/image-813-1024x206.webp)
![Figure 11. The strength of Al–Si alloys, prepared on the basis of data from [209,287–290].](https://castman.co.kr/wp-content/uploads/image-814-1024x608.webp)
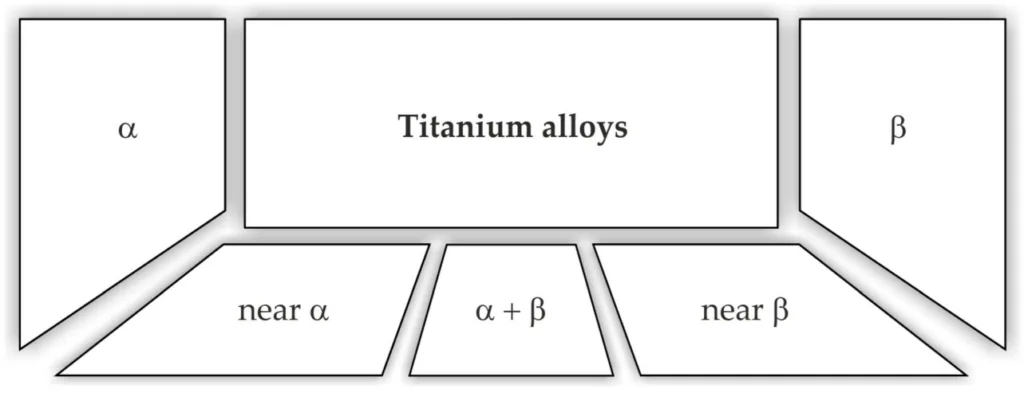
![Figure 13. The main applications of titanium and titanium alloys (reproduced with permission from Reference [314]; copyright © 2024, Springer Nature Switzerland AG).](https://castman.co.kr/wp-content/uploads/image-816-1024x670.webp)
![Figure 14. Bugatti titanium components: (a) eight-piston monobloc brake calliper, (b) active
spoiler bracket, and (c) tailpipe trim covers (reproduced with permission from Reference [319];
copyright © 2024 The Authors. Published by Elsevier B.V.).](https://castman.co.kr/wp-content/uploads/image-817-png.webp)
![Figure 15. Large titanium engine component by Precision Castparts Corporation (reproduced with
permission from Reference [320]; copyright © 2024 Published by Elsevier B.V.).](https://castman.co.kr/wp-content/uploads/image-818-png.webp)
![Figure 16. Development chronologically of titanium parts (reproduced with permission from Reference [331]; copyright © 2024 Elsevier Inc. All rights reserved).](https://castman.co.kr/wp-content/uploads/image-819-1024x633.webp)
- Figure 1. Classification of steels used in the automotive industry(reproduced with permission from Reference [4]; copyright © 2024 Acta Materialia Inc. Published by Elsevier B.V. All rights reserved).
- Figure 2. The influence of bake hardening on stress (reproduced with permission from Reference [78]; copyright © 2024 Elsevier Ltd. All rights reserved).
- Figure 3. Typical microstructure of (a) HSLA and (b) DP steel (reproduced with permission from Reference [31]; copyright © 2024 Woodhead Publishing Limited. All rights reserved).
- Figure 4. Fabrication procedure of the cold-rolled LC/TWIP/LC and IF/TWIP/IF sheets (reproduced with permission from Reference [102]; copyright © 2024 Elsevier B.V. All rights reserved).
- Figure 5. Thermal cycle for the quenching and partitioning process (Ac3-transformation temperature, RT-room temperature), prepared with permission from Reference [132] (copyright © 2024 Acta Materialia Inc. Published by Elsevier Ltd. All rights reserved).
- Figure 6. Comparison of tensile curves of selected corrosion-resistant steel families (reproduced with permission from Reference [139] (copyright © 2024 Elsevier Ltd. All rights reserved).
- Figure 7. Aluminium alloy-specific Chinese automotive demand estimates. Top to bottom, the three rows show No-LT (a−c), Middle-LT (d-f), and High-LT (g-i). Three columns show Low-PN, Middle-PN, and High-PN situations from left to right. Where LT = light-weighting-trend and PN = penetration scenario (reproduced with permission from Reference [218]; copyright © 2024 The Author(s). Published by Elsevier B.V.).
- Figure 8. Audi AL2 aluminium body structure (reproduced with permission from Reference [251]; copyright © 2024 Elsevier Science S.A. All rights reserved).
- Figure 9. Baseline part and demonstration part geometry (reproduced with permission from Reference [279]; copyright © 2024, The Minerals, Metals & Materials Society).
- Figure 10. Forming trial results on 7xxx alloy at various forming temperatures (reproduced with permission from Reference [279]; copyright © 2024, The Minerals, Metals & Materials Society).
- Figure 11. The strength of Al–Si alloys, prepared on the basis of data from [209,287-290].
- Figure 12. Classification of the titanium alloys.
- Figure 13. The main applications of titanium and titanium alloys (reproduced with permission from Reference [314]; copyright © 2024, Springer Nature Switzerland AG).
- Figure 14. Bugatti titanium components: (a) eight-piston monobloc brake calliper, (b) active spoiler bracket, and (c) tailpipe trim covers (reproduced with permission from Reference [319]; copyright © 2024 The Authors. Published by Elsevier B.V.).
- Figure 15. Large titanium engine component by Precision Castparts Corporation (reproduced with permission from Reference [320]; copyright © 2024 Published by Elsevier B.V.).
- Figure 16. Development chronologically of titanium parts (reproduced with permission from Reference [331]; copyright © 2024 Elsevier Inc. All rights reserved).
7. Conclusion:
Summary of Key Findings:
The review concludes that steel remains a widely used and cost-effective material, especially AHSS, in automotive manufacturing due to its balance of properties and recyclability. Aluminium alloys are increasingly important for lightweighting, with 5xxx and 6xxx series being dominant. Titanium alloys, while offering superior specific strength and corrosion resistance, are limited to niche applications due to cost and forming challenges. Magnesium alloys offer the greatest potential for weight reduction but face limitations in formability and high-volume production.
Academic Significance of the Study:
This study provides a comprehensive and up-to-date systematic overview of metallic materials used in the automotive industry. It serves as a valuable resource for researchers and experts by consolidating current knowledge on material trends, classifications, properties, and applications. The review highlights research gaps and potential future directions in automotive material science.
Practical Implications:
The practical implications of this review are significant for automotive engineers and material scientists. It offers guidance for material selection based on performance requirements, cost considerations, and sustainability goals. The overview of limitations and development trends can inform future research and development efforts aimed at improving material properties, reducing costs, and enhancing the application of lightweight metals in mass-produced vehicles.
Limitations of the Study and Areas for Future Research:
The study is limited to a review of existing literature and does not include original experimental research. Future research areas identified include:
- Development of technologies for deep drawing of coated materials and materials with desired anisotropic features.
- Further development of AHSS with enhanced strength and formability, including new cold stamping technologies.
- Exploration of cost-effective alternatives to traditional materials for lightweighting to enable broader adoption in mass production.
- Development of mass recycling technologies for composite materials to address sustainability concerns.
- Overcoming formability limitations of magnesium alloys for wider structural applications.
8. References:
- [1] Samek, L.; Krizan, D. Steel—Material of choice for automotive lightweight applications. In Proceedings of the International Conference Metal'2012, Brno, Czech Republic, 23–25 May 2012; pp. 1–6.
- [2] Ultra Light Steel Auto Body; Final Report; American Iron and Steel Institute: Washington, DC, USA, 1998; Available online: https://www.yumpu.com/en/document/view/5349987/ultralight-steel-auto-body-final-report-american-iron-steel- (accessed on 17 November 2023).
- [3] Perka, A.K.; John, M.; Kuruveri, U.B.; Menezes, P.L. Advanced high-strength steels for automotive applications: Arc and laser welding process, properties, and challenges. Metals 2022, 12, 1051. [CrossRef]
- [4] Kumar, A.; Singh, A. Mechanical properties of nanostructured bainitic steels. Materialia 2021, 15, 101034. [CrossRef]
- [5] All-New 2021 Jeep®Grand Cherokee Breaks New Ground in the Full-Size SUV Segment. Available online: https://www.media.stellantis.com/uk-en/jeep/press/all-new-2021-jeep-grand-cherokee-breaks-new-ground-in-the-full-size-suv-segment-uk (accessed on 17 November 2023).
- [6] Galán, J.; Samek, L.; Verleysen, P.; Verbeken, K.; Houbaert, Y. Advanced high strength steels for automotive industry. Rev. Metal. 2012, 48, 118-131. [CrossRef]
- [7] Kuziak, R.; Kawalla, R.; Waengler, S. Advanced high strength steels for automotive industry. Arch. Civ. Mech. Eng. 2008, 8, 103-117. [CrossRef]
- [8] Siczek, K.; Siczek, K. Lekkie rozwiązania w przemyśle samochodowym. Autobusy 2017, 14, 1311–1314.
- [9] According to the Automotive and Transportation Market Research Report. Available online: https://mobilityforesights.com/product/automotive-ahss-market/ (accessed on 15 December 2023).
- [10] Schneider, R.; Heine, B.; Grant, R.J. Mechanical Behaviour of Commercial Aluminium Wrought Alloys at Low Temperatures, Light Metal Alloys Applications; Waldemar, A.M., Ed.; InTech: Houston, TX, USA, 2014; Available online: https://www.intechopen.com/chapters/46602 (accessed on 16 November 2023).
- [11] Bielefeldt, K.; Papacz, W.; Walkowiak, J. Environmentally friendly car plastics in automotive engineering. Arch. Motoryz. 2011, 2, 5-19.
- [12] This Aluminum-Bodied 1953 Porsche 356 1500 Pre-A Cabriolet Is Shrouded in Mystery. Available online: https://www.hagerty.com/media/automotive-history/this-aluminum-bodied-1953-porsche-356-1500-pre-a-cabriolet-is-shrouded-in-mystery/ (accessed on 16 November 2023).
- [13] Choi, C.H.; Park, S.S.; Hwang, T.W. Development of composite body panels for a lightweight vehicle. SAE Trans. 2001, 110, 143-149.
- [14] Fantuzzi, N.; Bacciocchi, M.; Benedetti, D.; Agnelli, J. The use of sustainable composites for the manufacturing of electric cars. Compos. Part C Open Access 2021, 4, 100096. [CrossRef]
- [15] Cieniek, Ł. Anizotropia i Tekstura Krystalograficzna. Starzenie po Odkształceniu. Available online: https://docplayer.pl/56885357-Cwiczenie-nr-4-anizotropia-i-tekstura-krystalograficzna-starzenie-po-odksztalceniu.html (accessed on 15 November 2023).
- [16] Sherman, A.M.; Allison, J.E. Potential for Automotive Applications of Titanium Alloys; SAE Technical Paper 860608; SAE International: Warrendale, PA, USA, 1986. [CrossRef]
- [17] Titanium for Automotive Applications. Available online: https://www.azom.com/article.aspx?ArticleID=553 (accessed on 16 November 2023).
- [18] Schauerte, O. Titanium in automotive production. Adv. Eng. Mater. 2003, 5, 411-418. [CrossRef]
- [19] Blicharski, M. Inżynieria Materiałowa, Stal.; WNT: Warszawa, Poland, 2004.
- [20] Evaluation Technologies on High Strength Steel Sheet for Automobiles. Available online: https://www.kobelcokaken.co.jp/en/example/c/index.html (accessed on 16 November 2023).
- [21] Senkara, J. Współczesne stale karoseryjne dla przemysłu motoryzacyjnego i wytyczne technologiczne ich zgrzewania. Prz. Spaw. 2009, 11, 3-7.
- [22] Best Surfaces for Cat Body Panels. Available online: https://www.thyssenkrupp-steel.com/en/industries/automotivetrucks/surfaces-for-car-body-panels/best-surfaces.html (accessed on 16 December 2023).
- [23] Kubińska-Jabcoń, E.; Niekurzak, M. Wykorzystanie nowoczesnych materiałów stosowanych w motoryzacji w celu poprawy jakości i bezpieczeństwa użytkowania pojazdów mechanicznych. Autobusy 2019, 10–11, 47–52.
- [24] Close, D.; Lallement, R.; Feuser, P.; Bold, J. Challenges in Corrosion Protection for Press-Hardened Steels. In Tagungsband Zum 9. Erlanger Workshop Warmblechumformung; Meisenbach Verlag: Erlangen, Germany, 2014; pp. 31–52.
- [25] Abotani, K.; Hirohata, K.; Kiyasu, T. Hot-Dip Galvanized Sheet Steel with Excellent Press Formability and Surface Quality for the Automotive Panels. Kawasaki Steel Tech. Rep. 2003, 48, 17-22.
- [26] EN ISO 1461:2009; Hot Dip Galvanized Coatings On Fabricated Iron And Steel Articles. Specifications and Test Methods. Comite Europeen de Normalisation: Brussels, Belgium, 1994.
- [27] Close, D. Alternative Protective Coatings for Hot Stamped Automotive Body Parts. Ph.D. Thesis, Universite de Lorraine, Lorraine, France, 22 March 2018.
- [28] Ulbrich, D.; Kowalczyk, J.; Stachowiak, A.; Sawczuk, W.; Selech, J. The Influence of Surface Preparation of the Steel during the Renovation of the Car Body on Its Corrosion Resistance. Coatings 2021, 11, 384. [CrossRef]
- [29] Santos, D.; Raminhos, H.; Costa, M.R.; Diamantino, T.; Goodwin, F. Performance of finish coated galvanized steel sheets for automotive bodies. Prog. Org. Coat. 2008, 62, 265-273. [CrossRef]
- [30] Wyrobek, K. Modelowanie procesu tłoczenia części nadwozia samochodu ze stali superwysoko wytrzymałej. Inż. Masz. 2017, 22, 76-84.
- [31] Horvath, C.D. Advanced steels for lightweight automotive structures. In Materials, Design and Manufacturing for Lightweight Vehicles; Mallick, P.K., Ed.; Woodhead Publishing: Sawston, UK, 2010; pp. 35–78.
- [32] Grosman, F.; Piela, A. Zastosowanie nowej metody badań do wstępnej oceny właściwości użytkowych blach dla motoryzacji. Inż. Mater. 1991, 12, 84-87.
- [33] Trzepieciński, T.; Najm, S.M. Application of artificial neural networks to the analysis of friction behaviour in a drawbead profile in sheet metal forming. Materials 2022, 15, 9022. [CrossRef] [PubMed]
- [34] Trzepieciński, T.; Szwajka, K.; Szewczyk, M. Pressure-assisted lubrication of DC01 steel sheets to reduce friction in sheet-metal-forming processes. Lubricants 2023, 11, 169. [CrossRef]
- [35] Kajal, G.; Tyagi, M.R.; Kumar, G. A review on the effect of residual stresses in incremental sheet metal forming used in automotive and medical sectors. Mater. Today Proc. 2023, 78, 524-534. [CrossRef]
- [36] Ma, L.; Wang, Z. The effects of through-thickness shear stress on the formability of sheet metal—A review. J. Manuf. Proc. 2021, 71, 269-289. [CrossRef]
- [37] Trzepieciński, T.; Lemu, H.G. Improving prediction of springback in sheet metal forming using multilayer perceptron-based genetic algorithm. Materials 2020, 13, 3129. [CrossRef] [PubMed]
- [38] Szewczyk, M.; Szwajka, K. Assessment of the tribological performance of bio-based lubricants using analysis of variance. Adv. Mech. Mater. Eng. 2023, 40, 31-38. [CrossRef]
- [39] Trzepieciński, T.; Najm, S.M.; Sbayti, M.; Belhadjsalah, H.; Szpunar, M.; Lemu, H.G. New advances and future possibilities in forming technology of hybrid metal-polymer composites used in aerospace applications. J. Compos. Sci. 2021, 5, 217. [CrossRef]
- [40] Trzepieciński, T.; Najm, S.M.; Oleksik, V.; Vasilca, D.; Paniti, I.; Szpunar, M. Recent developments and future challenges in incremental sheet forming of aluminium and aluminium alloy sheets. Metals 2022, 12, 124. [CrossRef]
- [41] Żaba, K.; Puchlerska, S.; Kuczek, Ł.; Trzepieciński, T.; Maj, P. Effect of step size on the formability of Al/Cu bimetallic sheets in single point incremental sheet forming. Materials 2023, 16, 367. [CrossRef] [PubMed]
- [42] Rajarajan, C.; Sivaraj, P.; Sonar, T.; Raja, S.; Mathiazhagan, N. Resistance spot welding of advanced high strength steel for fabrication of thin-walled automotive structural frames. Forces Mech. 2022, 7, 100084. [CrossRef]
- [43] Ahmed, M.M.Z.; El-Sayed Selaman, M.M.; Fydrych, D.; Cam, G. Review on friction stir welding of dissimilar magnesium and aluminum alloys: Scientometric analysis and strategies for achieving high-quality joints. J. Magnes. Alloys 2023, 11, 4082-4127. [CrossRef]
- [44] Tomków, J.; Fydrych, D.; Rogalski, G. Dissimilar underwater wet welding of HSLA steels. Int. J. Adv. Manuf. Technol. 2020, 109, 717-725. [CrossRef]
- [45] André, V.; Costas, M.; Langseth, M.; Morin, D. Behavior and Large-Scale Modeling of Multi-Sheet Aluminum Connections With Self-Piercing Rivets. J. Manuf. Sci. Eng. 2023, 145, 101010. [CrossRef]
- [46] Çavuşoğlu, O.; Bakırcı, A.; Dinkçi, H.; Yılmazoğlu, A.G. Triple joining of different sheets with self-pierce riveting method. Sci. Technol. Weld. Join. 2022, 27, 579-585. [CrossRef]
- [47] Zhou, Z.-J.; Huang, Z.-C.; Jiang, Y.-Q.; Tang, N.-L. Joining Properties of SPFC440/AA5052 Multi-Material Self-Piercing Riveting Joints. Materials 2022, 15, 2962. [CrossRef]
- [48] Cmorej, D.; Kaščák, L'. Numerical simulation of mechanical joining of three DP600 and DC06 steel sheets. Adv. Mech. Mater. Eng. 2023, 40, 23-29. [CrossRef]
- [49] Huang, Z.C.; Huang, G.H.; Shan, F.W.; Jiang, Y.Q.; Zou, Y.Q.; Nie, X.Y. Forming quality and microstructure evolution of AA6061-T6 aluminum alloy joint during flow drill screwing process. Adv. Eng. Mater. 2023, 25, 2300054. [CrossRef]
- [50] Kinsley, B.L. 7—Tailor welded blanks for the automotive industry. In Tailor Welded Blanks for Advanced Manufacturing; Kinsley, B.L., Wu, X., Eds.; Woodhead Publishing: Sawston, UK, 2011; pp. 164-180.
- [51] Keeler, S.; Kimchi, M. Advanced High-Strength Steels. Application Guidelines Version 5.0, World Auto Steel. 2014. Available online: https://www.worldautosteel.org/projects/advanced-high-strength-steel-application-guidelines/ (accessed on 16 November 2023).
- [52] ULSAB-AVC. Available online: https://www.worldautosteel.org/projects/ulsab-avc-2/ (accessed on 16 November 2022).
- [53] ULSAC. Available online: https://www.worldautosteel.org/projects/ulsac-2/ (accessed on 16 November 2022).
- [54] ULSAS-UltraLight Steel Auto Suspensions Report. Available online: https://www.worldautosteel.org/ulsas-ultralight-steel-auto-suspensions-report/ (accessed on 16 November 2022).
- [55] FutureSteel Vehicle. Available online: https://www.worldautosteel.org/projects/future-steel-vehicle/ (accessed on 16 November 2022).
- [56] Richter, J.; Kuhtz, M.; Hornig, A.; Harhash, M.; Palkowski, H.; Gude, M. A mixed numerical-experimental method to characterize metal-polymer interfaces for crash applications. Metals 2021, 11, 818. [CrossRef]
- [57] Structure-Borne-Damping Composite Material with Customized Properties. Available online: https://www.thyssenkrupp-steel.com/en/products/composite-material/overview-composite-material.html (accessed on 16 November 2023).
- [58] Kustroń, P.; Korzeniowski, M.; Piwowarczyk, T.; Sokołowski, P. Development of resistance spot welding processes of metal-plastic composites. Materials 2021, 14, 3233. [CrossRef] [PubMed]
- [59] HybrixTM = ∑[214Lightweight, Formable, Strong, Eco-Friendly]. Available online: https://www.lamera.se/ (accessed on 16 November 2023).
- [60] Hammarberg, S.; Kajberg, J.; Larsson, S.; Moshfegh, R.; Jonsén, P. Novel methodology for experimental characterization of micro-sandwich materials. Materials 2021, 14, 4396. [CrossRef] [PubMed]
- [61] Sokolova, O.A.; Kühn, M.; Palkowski, H. Deep drawing properties of lightweight steel/polymer/steel sandwich composites. Arch. Civ. Mech. Eng. 2012, 12, 105-112. [CrossRef]
- [62] EN 10130; Cold Rolled Low Carbon Steel Flat Products for Cold Forming—Technical Delivery Conditions. European Committee for Standardization: Brussels, Belgium, 2009.
- [63] Trzepieciński, T.; Szwajka, K.; Szewczyk, M. An investigation into the friction of cold-rolled low-carbon DC06 steel sheets in sheet metal forming using radial basis function neural networks. Appl. Sci. 2023, 13, 9572. [CrossRef]
- [64] Sudo, M.; Hashimoto, S.I.; Kambe, S. Niobium bearing ferrite-bainite high strength hot-rolled sheet steel with improved formability. Trans. Iron Steel Inst. Jpn. 1983, 23, 303-311. [CrossRef]
- [65] Complex Phase Steels. Available online: https://automotive.arcelormittal.com/products/flat/first_gen_AHSS/CP (accessed on 16 November 2023).
9. Copyright:
- This material is "Tomasz Trzepieciński and Sherwan Mohammed Najm"'s paper: Based on "Current Trends in Metallic Materials for Body Panels and Structural Members Used in the Automotive Industry".
- Paper Source: https://doi.org/10.3390/ma17030590
This material was summarized based on the above paper, and unauthorized use for commercial purposes is prohibited.
Copyright © 2025 CASTMAN. All rights reserved.