OksanaOzhoga-MaslovskajaElisabettaGariboldiJannis NicolasLemkeShow moreAdd to MendeleyShareCite
https://doi.org/10.1016/j.matdes.2015.12.003Get rights and content
Highlights
•
Critical conditions for blister formation of Al–9Si–3Cu–Fe alloy are identified via a FE model.•
Blister formation is modeled for wide range of temperatures, pore pressure, shape, location, and size.•
Strain field shows blister formation related to strain localization, depending of pore geometry.•
Lamina-shaped discontinuities of cast part are most critical for blister formation.
Abstract
The mechanism of blister formation during thermal cycle in a High Pressure Die Cast Al–9Si–3Cu–Fe alloy (EN 46000) was investigated by means of FEM simulation of a pressurized subsurface defect, considering the high-temperature elastoplastic behavior experimentally derived. The effect of parameters related to initial defect geometry, location and maximum temperature was analyzed. Blister formation was considered to occur as the maximum surface displacement after a thermal cycle exceeded 0.005 mm. It was shown that, for a given reference gas pressure, pore volume and depth, as well as temperature, blisters were developed from pores below a critical aspect ratio, as a result of high plastic strain accumulation in localized regions laying between the pore and the outer surface (ligament). Similarly, critical ligament thickness was identified and correlated to temperature and reference gas pressure. The development of blisters at temperatures lower than 400 °C from pores with reference pressure 90 MPa was predicted for a wide range of aspect ratios and ligament thickness. The possible occurrence of blisters in conventional HPDC components during heat treatment cycles at 350 °C was modeled for different pore pressures in the case of surface-near defects, mainly from lamina-shaped pores and was experimentally confirmed.
고압 다이 캐스트 Al-9Si-3Cu-Fe 합금(EN 46000)에서 열 사이클 중 블리스터 형성 메커니즘은 실험적으로 도출된 고온 탄소성 거동을 고려하여 가압된 표면 결함의 FEM 시뮬레이션을 통해 조사되었습니다. 초기 결함 형상, 위치 및 최대 온도와 관련된 매개변수의 영향을 분석했습니다.
블리스터 형성은 열 사이클 후 최대 표면 변위가 0.005mm를 초과할 때 발생하는 것으로 간주되었습니다. 주어진 기준 가스 압력, 기공 부피 및 깊이, 온도에 대해 기공과 기공 사이에 있는 국부적 영역에서 높은 소성 변형 축적의 결과로 임계 종횡비 미만의 기공에서 기포가 발생하는 것으로 나타났습니다.
외부 표면 (인대). 유사하게 임계 인대 두께가 식별되었고 온도 및 기준 가스 압력과 상관관계가 있었습니다. 기준 압력이 90MPa인 기공에서 400°C 미만의 온도에서 기포가 발생하는 것은 광범위한 종횡비 및 인대 두께에 대해 예측되었습니다.
350°C에서 열처리 주기 동안 기존 HPDC 구성 요소에서 기포가 발생할 가능성은 주로 박판 모양의 기공에서 발생하는 표면 근처 결함의 경우 다양한 기공 압력에 대해 모델링되었으며 실험적으로 확인되었습니다.
Graphical abstract

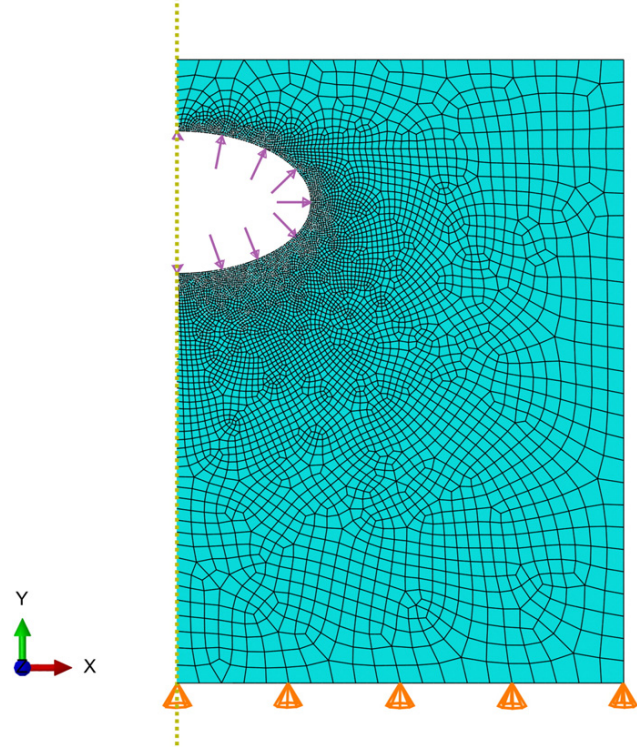
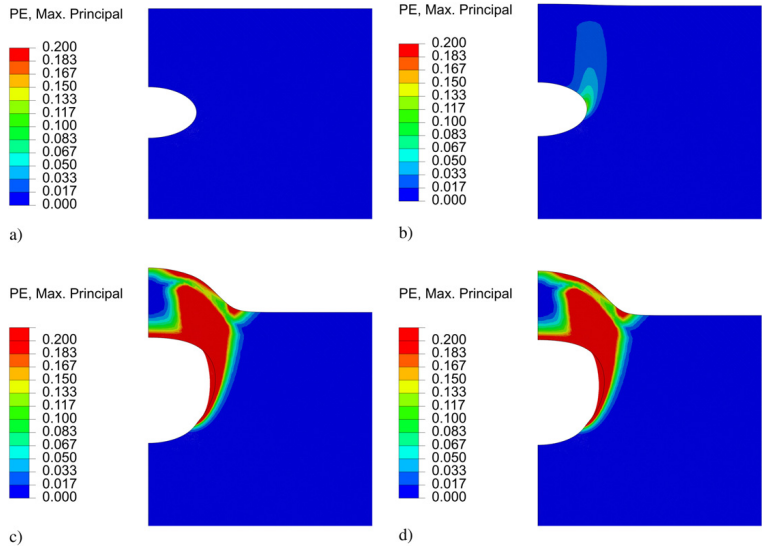
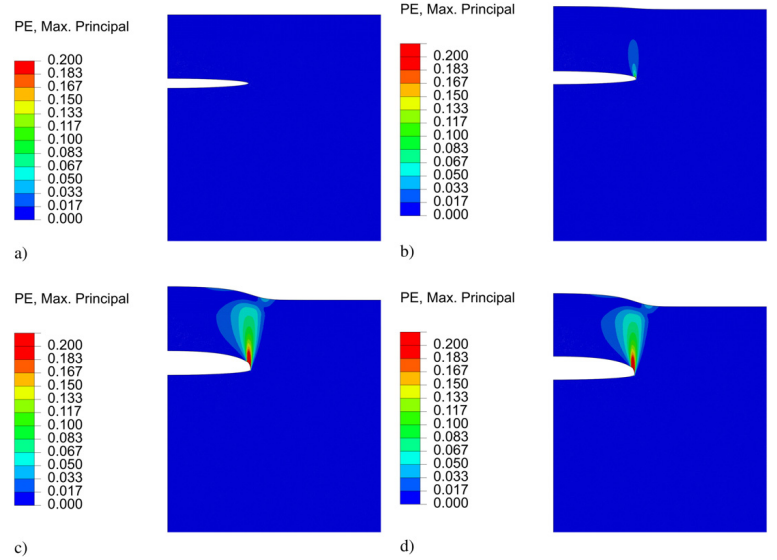
Keywords
Blister
High pressure die casting
Thermal cycle
Al–9Si–3Cu–Fe alloy (EN 46000)
High temperature behavior
References
[1] E. Sjölander, Heat Treatment of Al–Si–Cu–Mg Casting AlloysPhD thesis Jönköping
University, 2011.
[2] Lumley R, Odonnell R, Gunasegaram D, Givord, M. Heat treatment of high-pressure
die castings. Metall. Mater. Trans. A2007;38A; 2564–74.
[3] E. Gariboldi, F. Bonollo, P. Parona, Handbook of Defects in High Pressure Diecastings,
Associazione Italiana di Metallurgia, Milano, 2011.
[4] X. Niu, B. Hu, I. Pinwill, H. Li, Vacuum assisted high pressure die casting of aluminium alloys, J. Mater. Process. Technol. 105 (2000) 119–127.
[5] P. Homayonifar, R. Babaei, E. Attar, S. Shahinfar, P. Davami, Numerical modeling
splashing and air entrapment in high-pressure die casting, Int. J. Adv. Manuf.
Technol. 39 (2008) 219–228.
[6] M. Thirugnanam, Modern high pressure die-casting processes for aluminium castings, Trans. of 61st Indian Foundry Congress 2013, pp. 1–7.
[7] M. Uchida, Development of vacuum die-casting process, China foundry 6 (2009)
137–144.
[8] C. Garcia-Cordovilla, E. Louis, A. Pamies, The surface tension of liquid pure aluminium and aluminium–magnesium alloy, J. Mater. Sci. 21 (1986) 2787–2792.
[9] M. Dargusch, G. Dour, N. Schauer, C. Dinnis, G. Savage, The influence of pressure during solidification of high pressure die cast aluminium telecommunications components, J. Mater. Process. Technol. 180 (2006) 37–43.
[10] H. Toda, P.C. Qu, S. Ito, K. Shimizu, K. Uesugi, A. Takeuchi, Y. Suzuki, M. Kobayashi,
Formation behaviour of blister in cast aluminium alloy, Int. J. Cast Met. Res. 27
(2014) 369–377.
[11] J.E. Hatch, Aluminium: Properties and Physical Metallurgy, ASM International, Materials
Park Ohio, 2004.
[12] G. Timelli, F. Bonollo, Quality mapping of aluminum alloy die castings, Metall. Sci.
Technol. 26 (2008) 2–8.
[13] G. Timelli, S. Ferraro, F. Grosselle, F. Bonollo, F. Voltazza, L. Capra, Mechanical and microstructural characterization of diecast aluminium alloys, Metall. Ital. 103 (2011) 5–17.
[14] H. Hollomon, Trans. AIME 162 (1945) 268.
[15] R. Kuester, K.-H. Bode, W. Fritz, Beitrag zur Messung der Wärmeletfähigkeit von
Metallen im Bereich von 0 bis 500 °C, Waerme- Stoffuebertrag. 1 (1968) 129–139 (in
German).
[16] R.M. Jones, Deformation Theory of Plasticity, Bull Ridge Publishing, Blacksburg Virginia,
2009.
[17] R.N. Lumley, Progress on the heat treatment of high pressure diecastings, Fundamentals
of Aluminium Metallurgy, Woodhead Publishing 2010, pp. 262–302.
[18] Z.W. Chen, Skin solidification during high pressure die casting of Al–11Si–2Cu–1Fe
alloy, Mater. Sci. Eng. A348 (2003) 145–153.
Cited by (20)
- Effects of solution treatment temperature and time on the porosities and mechanical properties of vacuum die-casted and T6 heat-treated Al–Si–Mg alloy2021, VacuumShow abstract
- Evaluation of the gas porosity and mechanical properties of vacuum assisted pore-free die-cast Al-Si-Cu alloy2021, VacuumShow abstract
- Influence of porosity characteristics on the variability in mechanical properties of high pressure die casting (HPDC) AlSi7MgMn alloys2020, Journal of Manufacturing ProcessesShow abstract
- Effect of pressure cycles and thermal conditions on the reliability of a high-pressure diecast Al alloy heating radiator2019, Engineering Failure AnalysisCitation Excerpt :This is due to thin and uniform wall thickness of the component as well as the combined effect of rapid cooling rate and constitutional undercooling at the last stage of solidification. Furthermore, the contribution to gas pores' formation is mainly due to the decomposition of coolant and die lubrication [29], which are normally sprayed to increase the die life and reduce the adhesion of the solidified component during HPDC [30]. If there is no route for the vapor to escape through the overflows, it may be entrapped into the liquid metal as bubbles, which are dragged inside the die cavity.Show abstract
- Skin layer of A380 aluminium alloy die castings and its blistering during solution treatment2019, Journal of Materials Science and TechnologyCitation Excerpt :The high pressure gas pores, especially those close to the surface of die castings, tend to expand when exposed at high temperature [22,23]. Ozhoga-Maslovskaja et al. [24] simulated the development of blisters using FEM with consideration of aspect ratio, ligament thickness and pore pressure. Lumley et al. [25] thought that a thin laminar defect (see Fig. 1) of sub-surface was responsible for a significant proportion of blisters in an A380 alloy during solution treatment.Show abstract
- The effect of internal pressure in gas pores containing materials on their mechanical stability under shear2019, Mechanics Research CommunicationsCitation Excerpt :A common issue in both AM and HPDC is the appearance of structural defects resulting from the manufacturing process, which limits the ductility. Among the various defects accounted for in PBF and HPDC is the appearance of gas containing pores, which are produced by the entrapment of gas bubbles in the solidification process [1–7]. Consequently, the tensile ductility and fatigue life of HPDC and PBF materials are strongly influenced by the defect population [8–10].Show abstract