R Palanivel, Shaqra University, Riyadh, Saudi Arabia
I Dinaharan, Tsinghua University, Beijing, China
RF Laubscher, University of Johannesburg, Johannesburg, South Africa
금속 기반 복합 부품 생산을 위한 주조 경로
Introduction
A composite material is a material system consisting of a mixture or combination of two or more nano-micro- or macro-based elements with a separating interface where the constituents differ in shape and in the chemical make-up and is essentially insoluble (Smith and Hashemi, 2008; Kala et al., 2014). The dispersed phase of the mixture (combination) is typically referred to as the reinforcement whereas the continuous phase is known as the matrix (Kala et al., 2014). Composites are categorized as metal matrix (MMC), polymer matrix (PMC), or ceramic matrix (CMC) composites depending on the chemical nature of the matrix phase. A metal matrix composite (MMCs) therefore consists of at least two components of which the matrix is a metal and the dispersed or reinforcement phase being either another metal, a ceramic or an organic compound. MMCs are of significant interest due the fact that various material properties may be modified and or designed for a specific purpose. These include physical characteristics such as density, thermal expansion and thermal diffusivity and mechanical characteristics such as tensile and compressive strength, tribological behavior, etc. The increasing demand for advanced materials especially in the aerospace and automotive industries is driving the growth in use of MMCs. Ideally metal matrix composites aim to provide both improved static and dynamic material properties by the introduction of a tough yet rigid material that is resistant to crack formation and propagation. MMCs containing various types of ceramic particles have been produced by either solid state or liquid state methods (David Raja Selvam et al., 2013). These include solid state methods such as mechanical alloying (Srinivasarao et al., 2009) and powder metallurgy (Rahimian et al., 2009), whereas the liquid state methods include stir casting (Kalaiselvan et al., 2011), compocasting (Amirkhanlou et al., 2011), squeeze casting (Xiu et al., 2012), and spray deposition (Srivastava and Ojha, 2005). The solid state methods may be subject to certain disadvantages that include reduced strength, high tooling cost, high material cost, limitations on size and shape, dimensional changes while sintering, changes in density and safety and health risks. The liquid state techniques typically involve mixing of ceramic particles into melts with certain significant benefits when compared to the solid state techniques. These include improved matrix to particle binding, easier matrix-structure control, ease of processing, and a closer to final geometry result (Hanumanth and Irons, 1993; Seo and Kang, 1995; Sahin et al., 2002; Taha and El-Mahallawy, 1998). The casting routes are preferred mainly because they may have a significant effect on the MMCs mechanical and tribological behavior. Improved MMC properties require that the ceramic particles are efficiently incorporated and successfully bonded into the metal matrix (David Raja Selvam et al., 2013). MMC components are mainly used in the transport industries. These include aerospace and automotive components such as pistons, automotive disc brakes, connecting rods, cylinder heads, blades, cylinder liners, vane shafts, aircraft landing gear, bolts, valves, and structural shapes such as rods, beams, and tubes. Electrical contacts and brushes are also manufactured. The current chapter introduces the different casting methods with special emphasis on aluminum matrix composites (Rosso, 2006).
Stir Casting
During stir casting the particle reinforcement is typically distributed into the melted metal by rotational mechanical stirring. The key feature of this process is the mechanical stirring. A typical stir casting setup is presented in Fig. 1 . A graphite crucible is contained in the center of the furnace within an induction heating coil arrangement. Melting occurs within the graphite crucible. The mixing method is performed by a graphite mixer mounted on a steel mandrel powered by a variable speed AC motor. The mechanical stirrer is orientated along the main crucible axis. Its vertical position is continuously adjustable. A feeding hopper arrangement is used to add the ceramic powder and alloy components in the appropriate amount and time. To prevent contact with the molten metal, the steel mandrel is enclosed in a graphite sleeve. Glass fiber roving is used as heat insulation on the inside of the production unit. Argon gas is used both to insulate the molten metal from interacting with the atmosphere and to facilitate and regulate controlled addition of the reinforcement particles. Temperature control of the melt is facilitated by thermostat via internally and externally (crucible) mounted thermocouples (Kok, 2005; Mahadevana et al., 2008; Deshmanya and Purohit, 2012). Stir casting is typically a cost-effective method of producing MMCs and suitable for mass production. It is also relatively simple and may produce components close to net shape. Stir casting is useful for the manufacture of products with numerous features and irregular contours (Chadwich and Heath, 1990). The process parameters that may affect the mechanical and metallurgical characteristics of stir casts include the following; mold material, mold design, reinforcing particle feed rate, preheat temperature, temperature of the furnace, pouring method, properties of the matrix alloy, composition of matrix alloys, freezing range of matrix material, stirring speed, material of the stirrer, stirring time, impellor blade angle, and number of blades in the stirrer (Jebeen Moses et al., 2016; Nai and Gupta, 2002; Naher et al., 2003; Akhlaghi et al., 2004; Prabu et al., 2006; Ravi et al., 2007; Amirkhanlou and Niroumand, 2010; Zhang et al., 2010; Guan et al., 2011; Sajjadi et al ., 2012a; Du et al., 2012; Akbari et al., 2013; Khosravi et al., 2014). Typical problems that my manifest during stir casting include; non uniform distribution of reinforcing particles in the matrix, poor wettability between the matrix alloy and reinforcing particles, porosity and chemical reactions between the reinforcement and the matrix alloy. Stir casting is the most common technique for the manufacture of specifically aluminum matrix composites (AMCs). The aluminum matrix is typically fully melted and ceramic particles are added and mixed into the matrix by mechanical stirrer. Diverse techniques of improving wettability, including the addition of weighting agents and pre-heating and/or coating of the ceramic particles were attempted with varying success by researchers (Hashim et al., 2001; Kerti and Toptan, 2008; Sahin, 2003; Ramesha et al., 2009). Sahin (2003) used stir casting to prepare AA2024/SiC AMCs. As reinforcement material, SiC particles with an average size of 110, 45 or 29 µm were used. In total, 10 and 20 wt% SiC particles were added. Before the melting process was initiated, SiC particles were oxidized at a temperature of 1100°C for 2 h. Between 5 and 8 g of SiC particulates, wrapped in aluminum foil packets, were selectively added into the molten metal upon formation of the molten pool vortex every 15–25 s. Upon insertion of the mixture packet it commences to melt thereby introducing the particulates into the melt. Stirring occurs after which the melt is poured into a pre-heated mold. This technique facilitates complete and homogeneous distribution of the particulates into the matrix. Optical micrographs of 10 wt% SiC strengthened AA2024 aluminum alloy are presented in Fig. 2(a)–(c). The SiC distribution in these composites is uniform. The microstructure in Fig. 1(a) does not display the presence of any pores. This is due to the adequate wettability of the SiC and AA 2014 alloy combination. Fig. 2(b) displays a composite with a particle size of 45 µm. It once again displays no porosity or other cavities indicating effective bonding between the matrix and ceramic particulates. The same is true for the 110 µm particulate size (Fig. 2(c)). The particles do however display an angular shape and the presence of finer particles (also SiC) of less than 25 µm size. Fig. 2(d)–(f) display composites manufactured with a 20 wt% of SiC particles with sizes of 29 µm, 45 µm, and 110 µm, respectively. These micrographs indicate once again that these composites are free from porosity. A homogeneous distribution of the particles was achieved only for the 110 µm particle size. Limited agglomeration was visible for the other two sizes (29 µm, 45 µm).
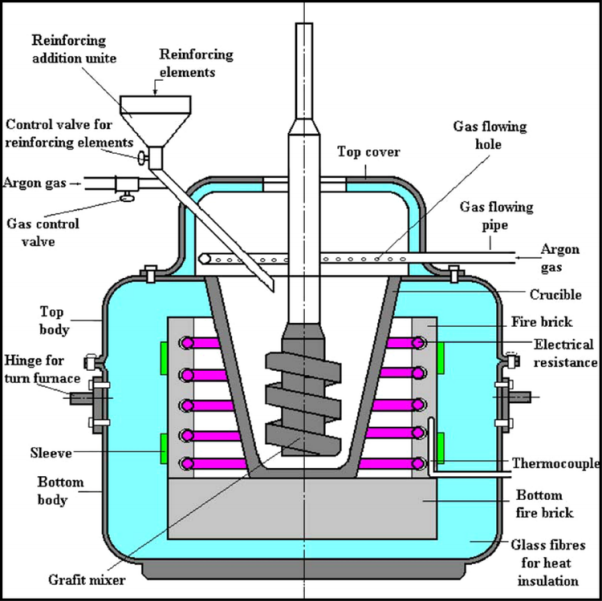
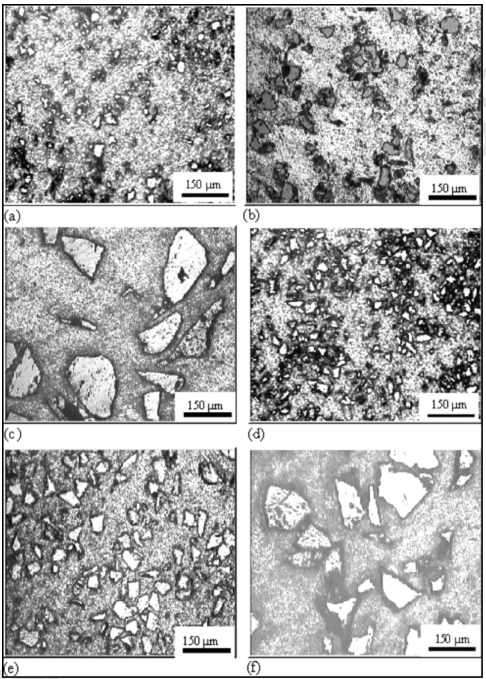
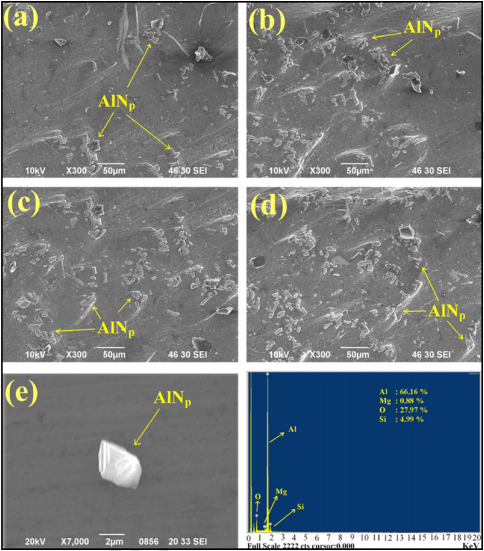
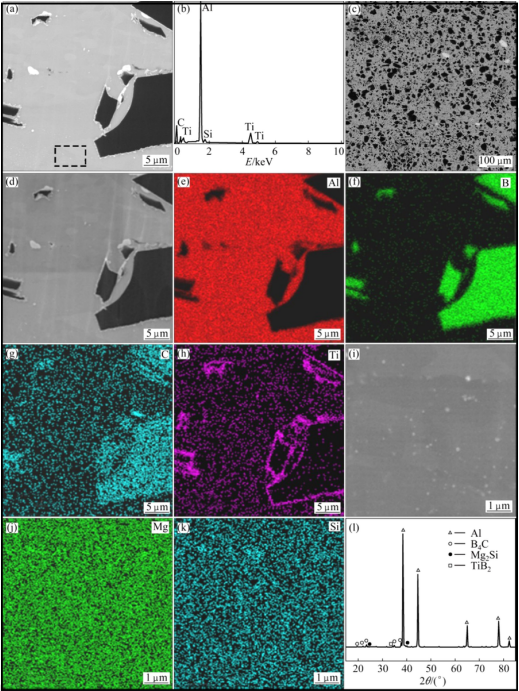
Continue....
Reference
Akbari, M.K., Mirzaee, O., Baharvandi, H.R., 2013. Fabrication and study on mechanical properties and fracture behavior of nanometric Al2O3
particle-reinforced A356 composites focusing on the parameters of vortex method. Materials & Design 46, 199–205.
Akhlaghi, F., Lajevardi, A., Maghanaki, H.M., 2004. Effects of casting temperature on the microstructure and wear resistance of compocast A356/SiCp
composites: A comparison between SS and SL routes. Journal of Materials Processing Technology 155−156, 1874–1880.
Allwyn Kingsly Gladston, J., Mohamed Sheriff, N., Dinaharan, I., David Raja Selvam, J., 2015. Production and characterization of rich husk ash particulate
reinforced AA6061 aluminum alloy composites by compocasting. Transactions of Nonferrous Metals Society of China 25, 683–691.
Amirkhanlou, S., Niroumand, B., 2010. Synthesis and characterization of 356−SiCp composites by stir casting and compocasting methods. Transactions of
Nonferrous Metals Society of China 20, 788–793.
Amirkhanlou, S., Niroumand, B., 2012. Fabrication and characterization of Al356/SiCp semisolid composites by injecting SiCp containing composite
powders. Journal of Materials Processing Technology 212, 841–847.
Amirkhanlou, S., Rezaei, M.R., Niroumand, B., Toroghinejad, M.R., 2011. High-strength and highly-uniform composites produced by compocasting and cold
rolling processes. Material & Design 32, 2085–2090.
Arsha, A.G., Jayakumar, E., Rajan, T.P.D., Antony, V., Pai, B.C., 2015. Design and fabrication of functionally graded in-situ aluminium composites for
automotive pistons. Materials and Design 88, 1201–1209.
Ashok Kumar, B., Murugan, N., 2012. Metallurgical and mechanical characterization of stir cast AA6061-T6–AlNp composite. Materials and Design 40,
52–58.
Balasivanandha Prabu, S., Karunamoorthy, L., Kathiresan, S., Mohan, B., 2006. Influence of stirring speed and stirring time on distribution of particles in cast
metal matrix composite. Journal of Materials Processing Technology 171, 268–273.
Balasubramanian, I., Maheswaran, R., 2015. Effect of inclusion of SiC particulates on the mechanical resistance behaviour of stir-cast AA6063/SiC
composites. Materials and Design 65, 511–520.
Baumli, P., Sychev, J., Budai, I., Szabo, J.T., Kaptay, G., 2013. Fabrication of carbon fiber reinforced aluminum matrix composites via titanium-ion containing
flux. Composites Part A 44, 47–50.
Celaya, F.O., Canul, M.I.P., Cuevas, J.L., Angeles, J.C.R., Canul, M.A.P., 2007. Microstructure and impact behavior of Al/SiCp composites fabricated by
pressureless infiltration with different types of SiCp. Journal of Materials Processing Technology 183, 368–373.
Ceschini, L., Minak, G., Morri, A., 2006. Tensile and fatigue properties of the AA6061/20 vol% Al2O3p and AA7005/10 vol% Al2O3p composites.
Composites Science and Technology 66, 333–342.
Chadwich, G.A., Heath, P.J., 1990. Machining of metal matrix composites. Metals and Materials 2–6 (1990), 73–76.
Chawla, N., Shen, Y.L., 2001. Mechanical behavior of particle reinforced metal matrix composites. Advanced Engineering Materials 3, 357–370.
Chelladurai, S.J.S., Arthanari, R., Krishnamoorthy, K., Selvaraj, K.S., Govindan, P., 2018. Effect of copper coating and reinforcement orientation on
mechanical properties of LM6 aluminium alloy composites reinforced with steel mesh by squeeze casting. Transactions of the Indian Institute of Metals
71, 1041–1048.
Chi, H., Jiang, L., Chen, G., et al., 2015. Dry sliding friction and wear behavior of (TiB2+h-BN)/2024Al composites. Materials and Design 87, 960–968.
David Raja Selvam, J., Robinson Smart, D.S., Dinaharan, I., 2013. Microstructure and some mechanical properties of fly ash particulate reinforced AA6061
aluminum alloy composites prepared by compocasting. Materials and Design 49, 28–34.
Davidson, A.M., Regener, D., 2000. A comparison of aluminium-based metal-matrix composites reinforced with coated and uncoated particulate silicon
carbide. Composites Science and Technology 60, 865–869.
Deshmanya, I.B., Purohit, G.K., 2012. Development of models for predicting impact strength of Al7075/Al2O3
composites produced by stir-casting. Journal
of Composite Materials 46, 3247–3253.
Du, Y., Zhang, P., Zhang, J., Yao, S., 2012. Radial distribution of SiC particles in mechanical stirring of A356−SiCp liquid. Journal of Materials Science and
Technology 28, 951–955.
Ebhota, W.S., Karun, A.S., Inambao, F.L., 2016. Centrifugal casting technique baseline knowledge, applications, and processing parameters. International
Journal of Materials Research 107, 960–969.
El-Galy, I.M., Ahmed, M.H., Bassiouny, B.I., 2017. Characterization of functionally graded Al-SiCp metal matrix composites manufactured by centrifugal
casting. Alexandria Engineering Journal 56, 371–381.
Feng, Y.C., Geng, L., Zheng, P.Q., Zheng, Z.Z., Wang, G.S., 2008. Fabrication and characteristic of Al-based hybrid composite reinforced with tungsten
oxide particle and aluminum borate whisker by squeeze casting. Materials and Design 29, 2023–2026.
Filipovic, M., Kamberovic, Z., Korac, M., Gavrilovski, M., 2013. Microstructure and mechanical properties of Fe–Cr–C–Nb white cast irons. Material and
Design 47, 41–48.
Flemings, M.C., 1991. Behavior of metal alloys in the semisolid state. Metallurgical Transactions A 22, 957–981.
Forster, M.F., Hamilton, R.W., Dashwood, R.J., Lee, P.D., 2003. Centrifugal casting of aluminium containing in situ formed TiB2
. Materials Science and
Technology 19, 1215–1219.
Fukui, Y., Takashima, K., Ponton, C.B., 1994. Measurement of Young’s modulus and internal friction of an in situ Al–Al3Ni functionally gradient material.
Journal of Materia. Science 29, 2281–2288.
Fukui, Y., Watanabe, Y., 1996. Analysis of thermal residual stress in a thick-walled ring of dural can-base Al-Sic functionally graded material. Metallurgical
and Materials Transactions A 27, 4145–4415.
Fukui, Y., Yamanaka, N., Enokida, Y., 1997. Bending strength of an Al–Al3Ni functionally graded material. Composites Part B:Engineering 28, 37–43.
Ghandvar, H., Farahany, S., Idris, J., 2015. Wettability enhancement of SiCp in cast A356/SiCp composite using semisolid process. Materials and
Manufacturing Processes 30, 1442–1449.
Ghomashchi, M.R., Vikhrov, A., 2000. Squeeze casting: An overview. Journal of Materials Processing Technology 101, 1–9.
Girot, F.A., Fédou, R., Quenisset, J.M., Naslain, R., 1990. On the squeeze casting conditions of aluminum matrix composite materials. Journal of Reinforced
Plastics and Composites 9, 456–469.
Guan, L.N., Geng, L., Zhang, H.W., Huang, L.J., 2011. Effects of stirring parameters on microstructure and tensile properties of (ABOw+SiCp)/6061Al
composites fabricated by semi-solid stirring technique. Transactions of Nonferrous Metals Society of China 21, 274–279.
Hadad, S.E., Sato, H., Watanabe, Y., 2010. Wear of Al/Al3Zr functionally graded materials fabricated by centrifugal solid-particle method. Journal of
Materials Processing Technology 210, 2245–2251.
Haddad, F., Amara, S.E., Kesri, R., 2008. Liquidus surface projection of the Fe-Nb-C system in the iron-rich corner. Metallurgical and Materials Transactions
A 39, 1026–1033.
Hanumanth, G.S., Irons, G.A., 1993. Particle incorporation by melt stirring for the production of metal-matrix composites. Journal of Materials Science 28,
2459–2465.
Hashim, J., Looney, L., Hashmi, M.S.J., 2001. The enhancement of wettability of SiC particles in cast aluminum matrix composites. Journal of Materials
Processing Technology 119, 329–335.
Hashim, J., Looney, L., Hashmi, M.S.J., 2002. Particle distribution in cast metal matrix composites − Part I. Journal of Materials Processing Technology 123,
251–257.
Hu, Q., Zhao, H., Li, F., 2016. Effects of manufacturing processes on microstructure and properties of Al/A356–B4C composites. Materials and Manufacturing
Processes 31, 1292–1300.
Jayakumar, E., Jacob, J.C., Rajan, T.P.D., Joseph, M.A., Pai, B.C., 2016. Processing and characterization of functionally graded aluminum (A319)–SiCp
metallic composites by centrifugal casting technique. The Minerals, Metals & Materials Society and ASM International 47, 4306–4315.
Jebeen Moses, J., Dinaharan, I., Joseph Sekhar, S., 2016. Prediction of influence of process parameters on tensile strength of AA6061/TiC aluminum matrix
composites produced using stir casting. Transactions of Nonferrous Metals Society of China 26, 1498–1511.
Jebeen Moses, J., Joseph Sekhar, S., 2016. Investigation on the tensile strength and microhardness of AA6061/TiC composites by stir casting. Transactions
of the Indian Institute of Metals 70, 1035–1046.
Jojith, R., Radhika, N., 2018. Fabrication of LM 25/WC functionally graded composite for automotive applications and investigation of its mechanical and
wear properties. Journal of the Brazilian Society of Mechanical Sciences and Engineering 40, 1–13.
Kalaiselvan, K., Murugan, N., Parameswaran, S., 2011. Production and characterization of AA6061–B4C stir cast composite. Material & Design 32,
4004–4009.
Kala, K., Mer, K.K.S., Kumar, S., 2014. A review on mechanical and tribological behaviors of stir cast aluminum matrix composites. Procedia Materials
Science 6, 1951–1960.
Kalkanli, A., Yilmaz, S., 2008. Synthesis and characterization of aluminum alloy 7075 reinforced with silicon carbide particulates. Materials and Design 29,
775–780.
Kana, W.H., Albino, C., Costa, D.D., et al., 2018. Microstructure characterisation and mechanical properties of a functionally graded NbC/high chromium
white cast iron composite. Materials Characterization 136, 196–205.
Karbalaei Akbari, M., Baharvandi, H.R., Shirvanimoghaddam, K., 2015. Tensile and fracture behavior of nano/micro TiB2 particle reinforced casting A356
aluminum alloy composites. Materials and Design 66, 150–161.
Kennedy, A.R., 2001. The reactive wetting and incorporation of B4C particles into molten aluminium. Scripta Materialia 44, 1077–1082.
Kennedy, A.R., 2002. The microstructure and mechanical properties of Al−Si−B4C metal matrix composites. Journal of Materials Science 37, 317–323.
Kerti, I., Toptan, F., 2008. Microstructural variations in cast B4C-reinforced aluminum matrix composites (AMCs). Material Letters 62, 1215–1218.
Kesri, R., Durand-Charre, M., 1997. Phase equilibria, solidification and solid-state transformations of white cast irons containing niobium. Journal of Material
Science 22, 2959–2964.
Kevorkijan, V., 2004. Mg AZ80/SiC composite bars fabricated by infiltration of porous ceramic preforms. Metallurgical and Materials Transactions A 35,
707–715.
Khosravi, H., Bakhshi, H., Salahinejad, E., 2014. Effects of compocasting process parameters on microstructural characteristics and tensile properties of
A356−SiCp composites. Transactions of Nonferrous Metals Society of China 24, 2482–2488.
Kok, M., 2005. Production and mechanical properties of Al2O3 particle-reinforced 2024 aluminium alloy composites. Journal of Materials Processing
Technology 161, 381–387.
Kumar, A., Lal, S., Kumar, S., 2013. Fabrication and characterization of A359/Al2O3 metal matrix composite using electromagnetic stir casting method.
Journal of Materials Research and Technology 2, 250–254.
Lekatou, A., Karantzalis, A.E., Evangelou, A., et al., 2015. Aluminium reinforced by WC and TiC nanoparticles (ex-situ) and aluminide particles (in-situ):
Microstructure, wear and corrosion behaviour. Materials and Design 65, 1121–1135.
Lin, G., Wei, Z.H., Ze, L.H., Na, G.L., Jun, H.L., 2010. Effects of Mg content on microstructure and mechanical properties of SiCp/Al-Mg composites
fabricated by semi-solid stirring technique. Transactions of Non ferrous Metals Society of China 20, 1851–1855.
Lloyd, D.J., 1994. Particle reinforced aluminium and magnesium metal matrix composites. International Materials Reviews 39 (1), 1–23.
Lu, D.H., Li, H.Z., Ren, B., 2018. Effect of Si content on impact-abrasive wear resistance of Al2O3p/steel composites prepared by squeeze casting. Journal of
Iron and Steel Research International 25, 984–994.
Mahadevana, K., Raghukandan, K., Pai, B.C., Pillai, U.T.S., 2008. Influence of precipitation hardening parameters on the fatigue strength of AA 6061-SiCp
composite. Journal of Materials Processing Technology 198, 241–247.
Mahendra, K.V., Radhakrishna, K., 2010. Characterization of stir cast Al-Cu-(fly ash + SiC) hybrid metal matrix composites. Journal of Composite Materials
44, 989–1005.
Manoharan, M., Lewandowski, J.J., 1992. Effect of reinforcement size and matrix microstructure on the fracture properties of an aluminum metal matrix
composite. Materials Science and Engineering A 150, 179–186.
Mehrabian, R., Riek, R.G., Flemings, M.C., 1974. Preparation and casting of metal-particulate non-metal composites. Metallurgical Transactions 5,
1899–1905.
Mitra, R., Chalapathi Rao, V.S., Maiti, R., Chakraborty, M., 2004. Stability and response to rolling of the interfaces in cast Al-SiCp and Al-Mg alloy-SiCp
composites. Materials Science & Engineering A 379, 391–400.
Naher, S., Brabazon, D., Looney, L., 2003. Simulation of the stir casting process. Journal of Materials Processing Technology 143−144, 567–571.
Nai, S.M.L., Gupta, M., 2002. Influence of stirring speed on the synthesis of Al/SiC based functionally gradient materials. Composite Structures 57, 227–233.
Pozdniakov, A.V., Lotfy, A., Qadir, A., et al., 2017. Development of Al-5Cu/B4C composites with low coefficient of thermal expansion for automotive
application. Materials Science & Engineering A 688, 1–8.
Prabhu, T.R., 2017. Processing and properties evaluation of functionally continuous graded 7075 Al alloy/SiC composites. Archives of Civil and Mechanical
Engineering 17, 20–31.
Prabu, S.B., Karunamoorthy, L., Kathiresan, S., Mohan, B., 2006. Influence of stirring speed and stirring time on distribution of particles in cast metal matrix
composite. Journal of Materials Processing Technology 171, 268–273.
Qiu, F., Gao, X., Tang, J., et al., 2017. Microstructures and tensile properties of Al–Cu matrix composites reinforced with nano-sized SiCp fabricated by
semisolid stirring process. Metals 49, 1–8.
Quaak, C.J., Kool, W.H., 1994. Properties of semisolid aluminium matrix composites. Materials Science & Engineering A 188, 277–282.
Radhika, N., 2018. Comparison of the mechanical and wear behaviour of aluminium alloy with homogeneous and functionally graded silicon nitride
composites. Science and Engineering of Composite Materials 25, 261–271.
Radhika, N., Raghu, R., 2016. Development of functionally graded aluminium composites using centrifugal casting and influence of reinforcements on
mechanical and wear properties. Transactions of Nonferrous Metals Society of China 26, 905–916.
Rahimian, M., Ehsani, N., Parvin, N., Baharvandi, H.R., 2009. The effect of particle size, sintering temperature and sintering time on the properties of
Al–Al2O3
composites, made by powder metallurgy. Journal of Materials Processing Technology 209, 5387–5393.
Rahimipour, M.R., Sobhani, M., 2013. Evaluation of centrifugal casting process parameters for in situ fabricated functionally gradient Fe-TiC composite.
Metallurgical and Materials Transactions B 44, 1120–1123.
Rajan, T.P.D., Jayakumar, E., Pai, B.C., 2012. Developments in solidification processing of functionally graded aluminium alloys and composites by
centrifugal casting technique. Transactions of the Indian Institute of Metals 65, 531–537.
Rajan, T.P.D., Pillai, R.M., Pai, B.C., 2008. Centrifugal casting of functionally graded aluminium matrix composite components. International Journal of Cast
Metals Research 21, 214–218.
Rajan, T.P.D., Pillai, R.M., Pai, B.C., 2010. Characterization of centrifugal cast functionally graded aluminum-silicon carbide metal matrix composites.
Materials Characterization 61, 923–928.
Rambo, C.R., Travitzky, N., Zimmermann, K., Greil, P., 2005. Synthesis of TiC/Ti–Cu composites by pressureless reactive infiltration of TiCu alloy into
carbon preforms fabricated by 3D-printing. Materials Letters 59, 1028–1031.
Ramesha, C.S., Keshavamurthy, R., Channabasappa, B.H., Ahmed, A., 2009. Microstructure and mechanical properties of Ni–P coated Si3N4 reinforced
Al6061 composites. Materials Science and Engineering A 502, 99–106.
Ranjith, R., Giridharan, P.K., Devaraj, J., Bharath, V., 2017. Influence of titanium-coated (B4Cp + SiCp) particles on sulphide stress corrosion and wear
behaviour of AA7050 hybrid composites (for MLG link). Journal of the Australian Ceramic Society 53, 1017–1025.
Ravikumar, K., Kiran, K., Sreebalaji, V.S., 2017. Characterization of mechanical properties of aluminium/tungsten carbide composite. Measurement 102,
142–149.
Ravi, K.R., Sreekumar, V.M., Pillai, R.M., et al., 2007. Optimization of mixing parameters through a water model for metal matrix composites synthesis.
Materials & Design 28, 871–881.
Rosso, M., 2006. Ceramic and metal matrix composites: Routes and properties. Journal of Materials Processing Technology 175, 364–375.
Sahin, Y., Kok, M., Celik, H., 2002. Tool wear and surface roughness of Al2O3 particle-reinforced aluminium alloy composites. Journal of Materials
Processing Technology 128, 280–291.
Sahin, Y., 2003. Preparation and some properties of SiC particle reinforced aluminum alloy composites. Materials & Design 24, 671–679.
Sajjadi, S.A., Ezatpour, H.R., Parizi, M.T., 2012. Comparison of microstructure and mechanical properties of A356 aluminum alloy/Al2O3
composites
fabricated by stir and compo-casting processes. Materials & Design 34, 106–111.
Sajjadi, S.A., Torabi Parizi, M., Ezatpour, H.R., Sedghi, A., 2012. Fabrication of A356 composite reinforced with micro and nano Al2O3 particles by a
developed compocasting method and study of its properties. Journal of Alloys and Compounds 511, 226–231.
Salvo, L., Esperance, G.L., Suery, M., Legoux, J.G., 1994. Interfacial reactionsand age hardening in Al–Mg–Si metal matrix composites reinforced with SiC
particles. Materials Science &Engineering A 177, 173–183.
Samal, P., Newkirk, J., 2015. Powder metallurgy methods and applications. ASM Handbook 7, 1–11.
Seah, K.H.W., Hemanth, J., Sharma, S.,.C., 2003. Mechanical properties of aluminium quartz particulate composites cast using metallic and non-metallic
chills. Materials and Design 24, 87–93.
Senthil, P., Amirthagadeswaran, K.S., 2012. Optimization of squeeze casting parameters for non symmetrical AC2A aluminium alloy castings through
Taguchi method. Journal of Mechanical Science and Technology 26, 1141–1147.
Seo, Y.H., Kang, C.G., 1995. The effect of applied pressure on particle dispersion characteristics and mechanical properties in melt-stirring squeeze-cast SiC/
Al composites. Journal of Materials Processing Technology 55, 370–379.
Sequeira, P.D., Watanabe, Y., Rocha, L.A., 2005. Aluminum matrix texture in Al–Al3Ti FGMs produced by a centrifugal method. Sol. Stat. Phen 105,
415–420.
Sevik, H., Kurnaz, S.C., 2006. Properties of alumina particulate reinforced aluminum alloy produced by pressure die casting. Materials and Design 27,
676–683.
Sharma, P., Sharma, S., Khanduja, D., 2016. Effect of graphite reinforcement on physical and mechanical properties of aluminium metal matrix composites.
Particulate Science and Technology 34, 17–22.
Shirvanimoghaddam, K., Khayyam, H., Abdizadeh, H., et al., 2016. Boron carbide reinforced aluminium matrix composite: physical, mechanical
characterization and mathematical modelling. Materials Science & Engineering A 658, 135–149.
Sivananth, V., Vijayarangan, S., Rajamanickam, N., 2014. Evaluation of fatigue and impact behavior of titanium carbide reinforced metal matrix composites.
Materials Science and Engineering A 597, 304–313.
Smith, W.F., Hashemi, J., 2008. Materials Science and Engineering. Tata McGraw Hill Education Private Limited, New Delhi, (ISBN- 13: 978-0-
07-066717-4).
Sobczak, J.J., Drenchev, Ludmil, 2013. Metallic functionally graded materials: A specific class of advanced composites. Journal of Materials Science &
Technology 29, 297–316.
Sohrabi Baba Heidary, D., Akhlaghi, F., 2011. Theoretical and experimental study on settling of SiC particles in composite slurries of aluminum A356/SiC.
Acta Materialia 59, 4556–4568.
Soundararajan, R., Ramesh, A., Mohanraj, N., Parthasarathi, N., 2016. An investigation of material removal rate and surface roughness of squeeze casted
A413 alloy on WEDM by multi response optimization using RSM. Journal of Alloys and Compounds 685, 533–545.
Srinivasarao, B., Suryanarayana, C., Oh-ishi, K., Hono, K., 2009. Microstructure and mechanical properties of Al–Zr nanocomposite materials. Materials
Science and Engineering A 518, 100–107.
Srivastava, V.C., Ojha, S.N., 2005. Microstructure and electrical conductivity of Al–SiCp composites produced by spray forming process. Bulletin of
Materials Science 28, 125–130.
Subramaniam, B., Natarajan, B., Kaliyaperumal, B., Chelladurai, S.J.S., 2018. Investigation on mechanical properties of aluminium 7075 - boron carbide -
coconut shell fly ash reinforced hybrid metal matrix composites. China foundry 15, 449–456.
Taha, M.A., El-Mahallawy, N.A., 1998. Metal-matrix composites fabricated by pressure-assisted infiltration of loose ceramic powder. Journal of Materials
Processing Technology 73, 139–146.
Tofigh, A.A., Rahimipour, M.R., Shabani, M.O., Davami, P., 2015. Application of the combined neuro-computing, fuzzy logic and swarm intelligence for
optimization of compocast nano composites. Journal of Composite Material 49, 1653–1663.
Toptan, F., Kilicarslan, A., Karaaslan, A., Cigdem, M., Kerti, I., 2010. Processing and microstructural characterization of AA 1070 and AA 6063 matrix B4Cp
reinforced composites. Materials and Design 31, 87–91.
Torralba, J.M., da Costa, C.E., Velasco, F., 2003. P/M aluminum matrix composites: An overview. Journal of Materials Processing Technology 133, 203–206.
Tzamtzis, S., Barekar, N.S., HariBabu, N., et al., 2009. Processing of advanced Al/SiC particulate metal matrix composites under intensive shearing – A novel
Rheo-process. Composites: Part A 40, 144–151.
Vembu, V., Ganesan, G., 2015. Heat treatment optimization for tensile properties of 8011 Al/15% SiCp metal matrix composite using response surface
methodology. Defence Technology 11, 390–395.
Verma, N., Vettivel, S.C., 2018. Characterization and experimental analysis of boron carbide and rice husk ash reinforced AA7075 aluminium alloy hybrid
composite. Journal of Alloys and Compounds 741, 981–998.
Vijian, P., Arunachalam, V.P., 2006. Optimization of squeeze casting process parameters using Taguchi analysis. The International Journal of Advanced
Manufacturing Technology 33, 1122–1127.
Vijian, P., Arunachalam, V.P., 2007. Modelling and multi objective optimization of LM24 aluminium alloy squeeze cast process parameters using genetic
algorithm. Journal of Materials Processing Technology 186, 82–86.
Watanabe, Y., Eryu, H., Matsuura, K., 2001. Evaluation of three-dimensional orientation of Al3Ti platelet in Al-based functionally graded materials fabricated
by a centrifugal casting technique. Acta Materials 49, 775–783.
Watanabe, Y., Oike, S., 2005. Formation mechanism of graded composition in Al–Al2Cu functionally graded materials fabricated by a centrifugal in situ
method. Acta Materials 53, 1631–1641.
Watanabe, Y., Yamanaka, N., Fukui, Y., 1997. Orientation of Al3Ti platelets in Al–Al3Ti functionally graded material manufactured by centrifugal method.
Materials ((Basel)) 88, 717–721.
Xiu, Z., Yang, W., Chen, G., et al., 2012. Microstructure and tensile properties of Si3N4p/2024Al composite fabricated by pressure infiltration method.
Material & Design 33, 350–355.
Xiu, Z., Yang, Wenshu, Dong, Ronghua, et al., 2015. Microstructure and mechanical properties of 45 vol% SiCp/7075Al composite. Journal of Materials
Science & Technology 31, 930–934.
Yana, C., Lifeng, W.G., Jianyue, R., 2008. Multi-functional SiC/Al composites for aerospace applications. Chinese Journal of Aeronautics 21, 578–584.
Yu, L., Qiu-lin, L., Dong, L., Wei, L., Guo-gang, S., 2016. Fabrication and characterization of stir casting AA6061−31%B4C composite. Transactions of
Nonferrous Metals Society of China 26, 2304–2312.
Yu, L., Qiulin, L., Wei, L., Guogang, S., 2016. Effect of Ti content and stirring time on microstructure and mechanical behavior of Al-B4C composites.
Journal of Alloys and Compounds 684, 496–503.
Zhang, Q., Chen, G., Wu, G., Xiu, Z., Luan, B., 2003. Property characteristics of a AlNp/Al composite fabricated by squeeze casting technology. Materials
Letters 57, 1453–1458.
Zhang, H., Geng, L., Guan, L., Huang, L., 2010. Effects of SiC particle pretreatment and stirring parameters on the microstructure and mechanical properties
of SiCp/Al−6.8Mg composites fabricated by semi-solid stirring technique. Materials Science and Engineering A 528, 513–518.
Zhang, J., Guan, R.G., Tie, D., et al., 2014. Effects of technical parameters of semi-solid stirring and Rheo-rolling on microstructure of A356–5wt% B4C
composite strip. Materials and Manufacturing Processes 30, 1–6.
Further Reading
Bakshi, S.R., Lahiri, D., Agarwal, A., 2010. Carbon nanotube reinforced metal matrix composites – A review. International Materials Reviews 55, 41–64.
Loharkar, P.K., Ingle, A., Jhavar, S., 2019. Parametric review of microwave-based materials processing and its applications. Journal of Materials Research
and Technology 8, 3306–3326.
Manrique, P.H., Lei, X., Xu, R., et al., 2019. Copper/graphene composites: A review. Journal of Materials Science 54, 12236–12289