This article introduces the paper "Casting Characteristics of Aluminum Die Casting Alloys" presented at the "US Department of Energy, Office of Industrial Technologies"
1. Overview:
*Title: Casting Characteristics of Aluminum Die Casting Alloys
*Author: Makhlouf M. Makhlouf, Diran Apelian
*Publication Year: February 5, 2002
*Publishing Journal/Academic Society: US Department of Energy, Office of Industrial Technologies
*Keywords: Aluminum alloys, die casting, casting characteristics, die soldering, sludge formation, fluidity

2. Research Background:
*Social/Academic Context of the Research Topic:
The research is a follow-up to a previous program investigating "Alloy - Microstructure - Performance Interactions in Aluminum Die Casting Alloys". The earlier program identified optimum alloy compositions for enhanced mechanical and physical properties. However, the die castability of these projected alloys was uncertain. Die casting is a crucial manufacturing process, and understanding the casting characteristics of aluminum alloys is essential for producing high-quality components.
*Limitations of Existing Research:
Previous research focused on optimizing mechanical and physical properties of aluminum die casting alloys without fully evaluating their casting characteristics, specifically die soldering, sludge formation, fluidity, and machinability. Existing literature on sludge formation and die soldering showed inconsistencies and lacked comprehensive understanding, especially concerning the influence of die casting specific conditions like high cooling rates. Furthermore, a universally accepted, standardized fluidity test simulating die-casting conditions was lacking.
*Necessity of the Research:
To bridge the gap between alloy design for enhanced properties and their manufacturability via die casting, this research was initiated. It is necessary to investigate the casting characteristics of newly developed aluminum die casting alloys to ensure they can be effectively and efficiently die cast. Understanding and mitigating issues like die soldering and sludge formation are critical for productivity and cost-effectiveness in the die casting industry. Evaluating fluidity and machinability is also crucial for ensuring part quality and manufacturing efficiency.
3. Research Purpose and Research Questions:
*Research Purpose:
The objectives of the research program are to:
- Evaluate the casting characteristics of selected aluminum die casting alloys.
- Identify the major factors that affect the casting characteristics of aluminum die casting alloys.
The project aims to investigate the die soldering tendency, sludge formation tendency, fluidity, and machinability of five experimental aluminum die casting alloys, projected to have superior properties, and compare them to commercial A380.0 alloy.
*Key Research Questions:
- What are the die soldering tendencies of the selected aluminum die casting alloys, and how are they influenced by alloy chemistry?
- What are the sludge formation tendencies of these alloys under different holding temperatures and cooling rates, and how do alloy chemistry and processing parameters affect sludge characteristics?
- What is the fluidity of these alloys under die casting conditions, and how does alloy chemistry influence their die filling capability?
- What are the machinability characteristics of these alloys, and are there potential machining issues related to sludge formation?
*Research Hypotheses:
The research implicitly hypothesizes that:
- Alloy chemistry, particularly Fe, Mn, Ni, Cr, and Si content, significantly affects die soldering and sludge formation tendencies.
- Processing parameters, such as melt temperature, die temperature, and cooling rate, play a crucial role in casting characteristics.
- Alloys with higher sludge factors will exhibit greater sludge formation tendencies.
- Adjustments to alloy chemistry and processing parameters can mitigate die soldering and sludge formation issues and optimize casting characteristics.
4. Research Methodology
*Research Design:
The research employs an experimental design to evaluate the casting characteristics of six aluminum alloys (five experimental and one commercial A380.0). It involves physical simulation tests for die soldering and fluidity, and controlled cooling experiments for sludge formation. Machinability is assessed based on the understanding of sludge formation and literature review, as direct testing was not feasible.
*Data Collection Method:
- Die Soldering Tendency: A physical simulation apparatus was used, dipping H-13 pins into molten alloy under controlled conditions (temperature, rotation speed, time). The intermetallic layer thickness on the pins was measured as an index of die soldering tendency.
- Fluidity: Die casting into a torturous cavity mold at SPX Corporation, measuring the filled length as an indicator of fluidity. Tests were conducted at a gate velocity of 2400 ips with a 0.5 mm die cavity thickness.
- Sludge Formation Tendency: Alloys were held at 670°C and 720°C for 3 hours and solidified under different cooling rates: slow cooling in a crucible, medium cooling in a permanent mold, and fast cooling in a copper wedge mold. Microstructure analysis was performed to characterize sludge.
- Machinability: Machinability was inferred from sludge formation tendency and literature review, without direct experimental measurement due to difficulties in specimen preparation.
*Analysis Method:
- Die Soldering: Measurement of intermetallic layer thickness using microscopy.
- Fluidity: Measurement of filled length in the die cavity. Statistical analysis of flow length data.
- Sludge Formation: Optical microscopy, Scanning Electron Microscopy (SEM), and Energy Dispersive X-rays (EDX) were used to characterize sludge quantity, size, morphology, distribution, and chemistry. Microhardness testing of sludge particles was also conducted.
- Machinability: Qualitative assessment based on sludge characteristics and literature.
*Research Subjects and Scope:
The research subjects are six aluminum die casting alloys: five experimental alloys (#1 to #5) designed for enhanced properties and commercial A380.0 alloy. The scope of the research is limited to evaluating die soldering tendency, sludge formation tendency, fluidity, and machinability. The study focuses on the influence of alloy chemistry and processing parameters on these casting characteristics under simulated die casting conditions.
5. Main Research Results:
*Key Research Results:
- Die Soldering: "The iron content of the alloy influences soldering the most." Alloy #1 (1.84% Fe) showed no soldering. "Mn has a beneficial effect on soldering." "Ni is detrimental to soldering." "Lack or absence of Ti is disadvantageous to soldering." Alloy #4, with low Fe and Mn and presence of Ni, exhibited the highest die soldering tendency, worse than A380.0.
- Fluidity: "For all the alloys, the data scatter was wide implying that factors other than alloy chemistry played a significant role in the alloy's ability to fill the die cavity." "In terms of alloy chemistry, the more the quantity of elements that formed high temperature compounds such as Fe, Mn, Cr, and Mg, the lower the fluidity of the alloy." Alloy 383 showed the highest average flow length, while Alloys #1 and #3, despite higher Si and Cu, showed lower fluidity, attributed to higher total content of Fe, Mn, Cr, and Mg.
- Sludge Formation: "The sludge factor (SF)¹ is most important in determining the sludge formation tendency of the alloy and the quantity of sludge that forms." Alloys #1 and #3, with high SF, formed significant sludge. "The morphology of sludge particles is influenced by the ratio of Fe:Mn:Cr in the alloy." "Cooling rate plays an important role in sludge formation. Slower cooling favors the formation of sludge." "Sludge does not form in the tested alloys during holding at either 670°C or 720°C" under fast cooling die casting conditions, but can form under slow cooling conditions in crucible.
- Machinability: "The alloys should not have machining problems when appropriate machining techniques and machining parameters are used." Machinability is inferred to be manageable with proper parameter adjustments, as sludge formation in die castings is not excessive for most alloys tested.
*Statistical/Qualitative Analysis Results:
- Die Soldering: Intermetallic layer thickness measurements (Table 4) quantified die soldering tendency, showing Alloy #4 with the highest value (44.5 µm) and Alloy #1 with 0 µm.
- Fluidity: Flow length measurements (Table 6) showed significant data scatter, indicating factors beyond alloy chemistry influence fluidity. Average flow lengths and ranges are provided for Alloys #1, #3, and 383.
- Sludge Formation: Sludge factor (SF) calculations (Table 7) correlated with observed sludge formation. Microhardness measurements (Table 8) quantified the hardness of different sludge phases. Micrographs (Figures 7-20) qualitatively illustrate sludge morphology and distribution under various conditions.
*Data Interpretation:
- High Fe content in Alloy #1 minimized die soldering due to Fe saturation. Mn showed a beneficial effect, while Ni and lack of Ti were detrimental.
- Fluidity test results were inconclusive regarding alloy chemistry due to high data scatter, suggesting process variations are dominant. However, higher content of high-temperature compound forming elements (Fe, Mn, Cr, Mg) appeared to reduce fluidity.
- Sludge factor effectively predicted sludge formation tendency under die casting cooling rates. Alloys with high SF formed significant sludge. Cooling rate and alloy chemistry significantly influenced sludge morphology and quantity. Sludge formation is more pronounced under slower cooling conditions.
- Machinability is expected to be manageable with appropriate machining parameters, as sludge formation in die castings is not severe for most alloys.
*Figure Name List:
- Figure 1. Sludge factor versus temperature [14, 16].
- Figure 2. Apparatus for simulating die soldering.
- Figure 3. Intermetallic layers on pin surfaces.
- Figure 4. Intermetallic layers on pin surfaces.
- Figure 5. Fluidity test results for alloy 383, die cavity thickness of 1 mm.
- Figure 6. Temperature versus sludge factor for the studied alloys.
- Figure 7. The Fe-rich needle and polyhedral particle surrounded by the primary Si in alloy #3 slowly cooled. S-Primary Si, P-Polyhedral, N-Needle (or Platelet).
- Figure 8. The microstructure of alloy #1, melt was held at 670°C for 3 hrs, cast in copper wedge mold, at wall thickness of 0.17”. T-Star-like, N-Needle (or Platelet), S-Primary Si.
- Figure 9. The microstructure of alloy #2, melt was held at 670°C for 3 hrs, cast in copper wedge mold, at wall thickness of 0.17”. C-Chinese script.
- Figure 10. The microstructure of alloy #3, melt was held at 670°C for 3 hrs, cast in copper wedge mold, at wall thickness of 0.17”. T-Star-like, S-Primary Si.
- Figure 11. The microstructure of alloy #4, melt was held at 670°C for 3 hrs, cast in copper wedge mold, at wall thickness of 0.17”. N-Needle (or Platelet).
- Figure 12. The microstructure of alloy #5, melt was held at 670°C for 3 hrs, cast in copper wedge mold, at wall thickness of 0.17”. C-Chinese script.
- Figure 13. The microstructure of alloy A380, melt was held at 670°C for 3 hrs, cast in copper wedge mold, at wall thickness of 0.17”. B-Blocky particle.
- Figure 14. The microstructure of alloy #2, melt was held at 720°C for 3 hrs, air cooled in crucible. C-Chinese script.
- Figure 15. The microstructure of alloy #4, melt was held at 720°C for 3 hrs, air cooled in crucible. P-Polyhedral.
- Figure 16. The microstructure of alloy A380, melt was held at 720°C for 3 hrs, air cooled in crucible. C-Chinese script, N-Needle (or Platelet), P-Polyhedral.
- Figure 17. The microstructure of alloy #1, melt was held at 670°C for 3 hrs, air cooled in crucible. S-Primary Si, N-Needle (or Platelet), P-Polyhedral.
- Figure 18. The microstructure of alloy #3, melt was held at 670°C for 3 hrs, air cooled in crucible. C-Chinese script, B-Blocky particle.
- Figure 19. The microstructure of alloy A380, melt was held at 670°C for 3 hrs, cast in copper wedge mold, at wall thickness of 0.36”. T-Star-like, B-Blocky particle.
- Figure 20. The microstructure of alloy A380, melt was held at 720°C for 3 hrs, cast in copper wedge mold, at wall thickness of 0.36”. T-Star-like, B-Blocky particle.
![Figure1. Sludge factor versus temperature [14, 16].](https://castman.co.kr/wp-content/uploads/Figure1.-Sludge-factor-versus-temperature-14-16.webp)
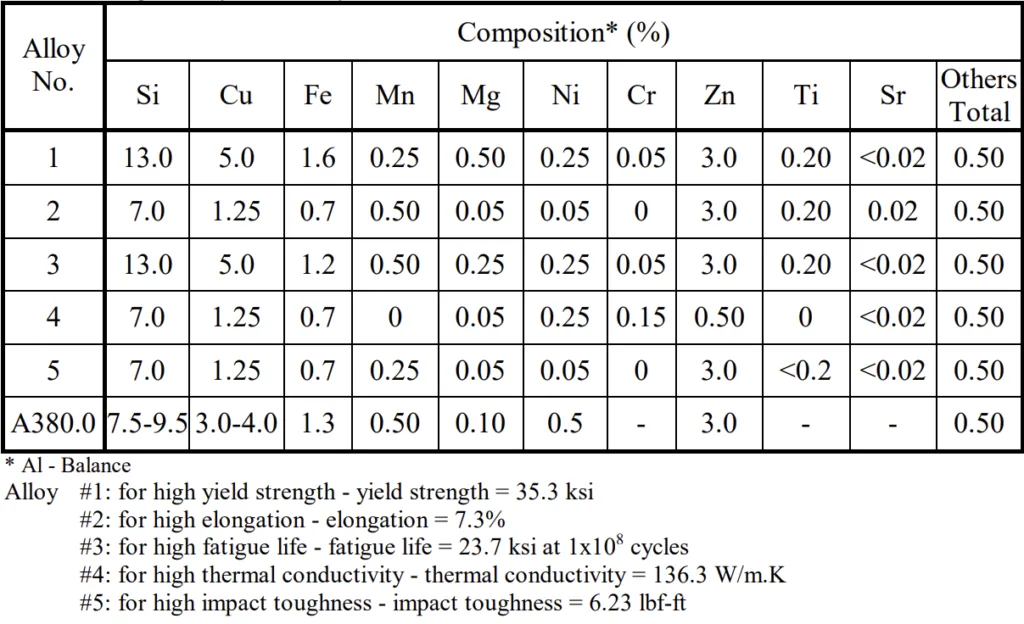
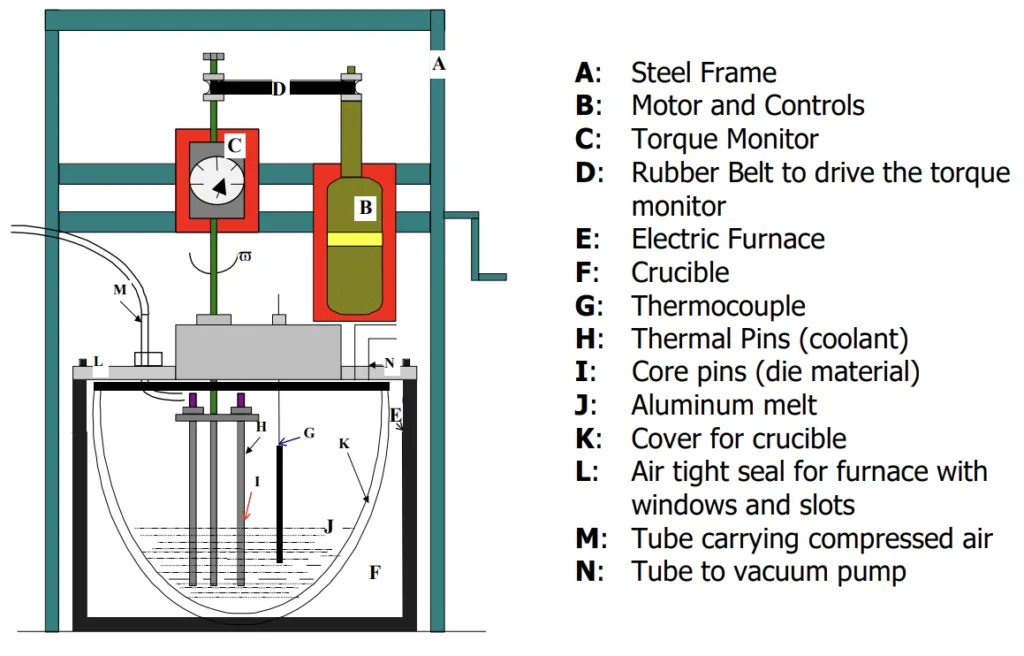
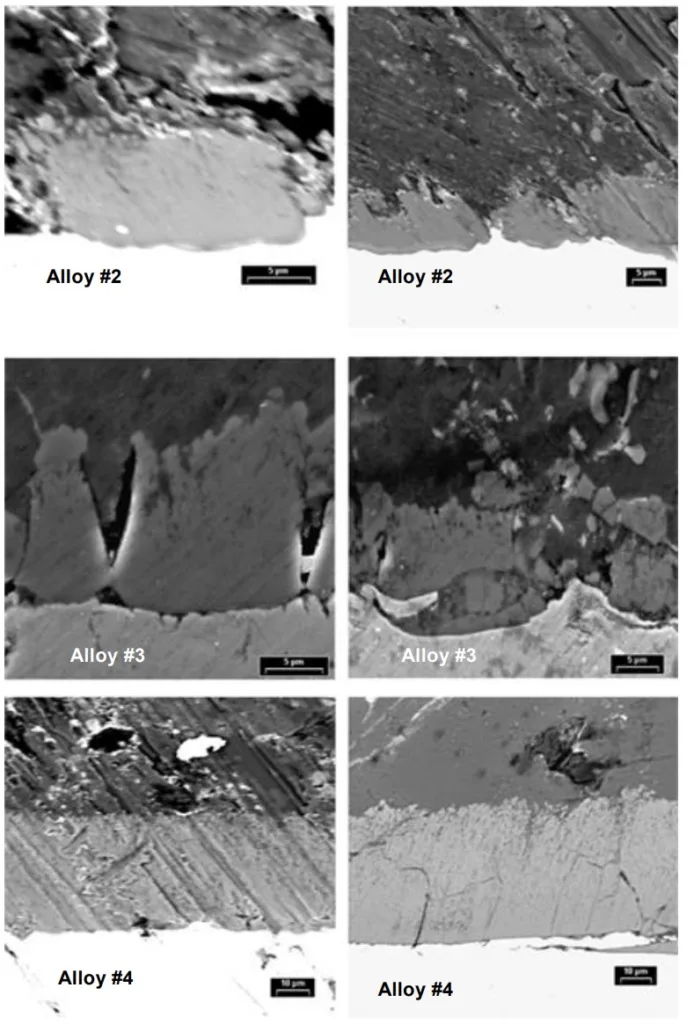
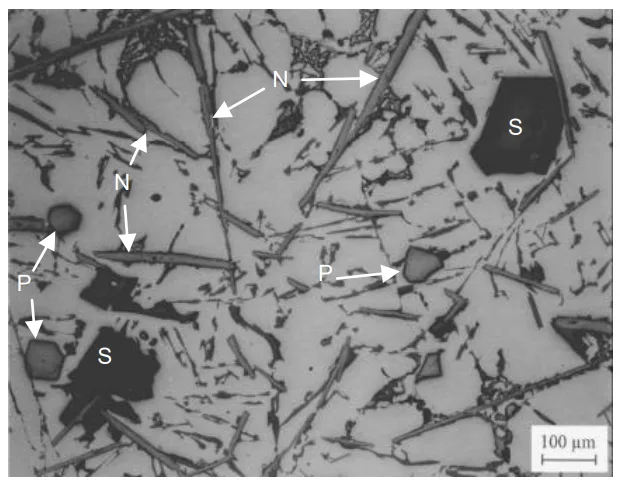
6. Conclusion and Discussion:
*Summary of Main Results:
The research concluded that the five experimental alloys, designed for enhanced mechanical properties, are die castable. They do not exhibit major issues in die soldering, sludge formation, fluidity, or machinability compared to A380.0 alloy. Specific findings include: Fe content being the primary factor in die soldering, Mn having a beneficial effect, and Ni being detrimental. Sludge formation tendency is predictable by the sludge factor, and is influenced by alloy chemistry and cooling rate. Fluidity data showed high variability, suggesting process factors are dominant, but higher levels of Fe, Mn, Cr, and Mg may reduce fluidity. Machinability is expected to be manageable with appropriate techniques.
*Academic Significance of the Research:
This research contributes to a deeper understanding of the casting characteristics of aluminum die casting alloys, particularly die soldering and sludge formation. It provides experimental validation of the sludge factor concept for predicting sludge tendency in die casting conditions. The study clarifies the roles of Fe, Mn, Ni, Cr, and Ti in die soldering and the influence of cooling rate on sludge morphology. It highlights the complexities of fluidity measurement in die casting and the need to consider process parameters alongside alloy chemistry.
*Practical Implications:
The findings offer practical guidelines for alloy design and process optimization in aluminum die casting.
- For alloys with low Fe and Mn, caution is needed regarding die soldering. Increasing Mn content and minimizing Ni can mitigate this. For example, for Alloy #4, "the Mn content of Alloy #4 should be raised to 0.25 - 0.5% and the Ni content should be reduced to a minimum".
- For alloys with high sludge factors, especially high Fe, "Fe content should be kept at its allowable lower level and Mn content is increased" to prevent hardspot formation. For example, for Alloy #1, "Fe can be reduced to 1.6% and Mn is increased to 0.5%."
- If die filling issues arise, process adjustments should be considered before altering alloy chemistry. Elements forming high-temperature compounds should be minimized in alloy chemistry to improve fluidity.
- Appropriate machining techniques and parameters are crucial for these alloys, and adjustments may be needed based on alloy type and potential hardspots from sludge.
*Limitations of the Research:
The fluidity test showed high data scatter, limiting definitive conclusions about alloy chemistry effects. Direct machinability testing was not conducted, and assessments are based on inference. The study focused on a limited set of alloys and processing conditions. The sludge formation study, while informative, may not fully replicate the complex melt handling and cooling conditions in industrial die casting operations.
7. Future Follow-up Research:
*Directions for Follow-up Research:
- Further investigation into the factors causing data scatter in fluidity tests to develop more robust fluidity measurement methods for die casting alloys.
- Direct machinability testing of these alloys under various machining conditions to quantify machinability characteristics and optimize machining parameters.
- More detailed studies on the interaction between alloy chemistry, holding temperature, and cooling rate on sludge formation under conditions that more closely simulate industrial die casting processes, including melt transfer and shot sleeve cooling.
- Investigation of the long-term effects of sludge particles on the mechanical properties and performance of die cast components.
- Exploring the effectiveness of different die coatings and lubricants in mitigating die soldering for these alloys.
*Areas Requiring Further Exploration:
- The precise mechanisms by which Mn and Ti influence die soldering tendency.
- The critical cooling rates and holding temperatures that trigger sludge formation in different alloy systems under die casting conditions.
- The impact of minor alloying elements and impurities on the casting characteristics of aluminum die casting alloys.
- Development of predictive models for die soldering, sludge formation, and fluidity based on alloy chemistry and processing parameters.
8. References:
- 1 M. M. Makhlouf, D. Apelian, and L. Wang, Microstructure and Properties of Aluminum Die Casting Alloys, NADCA, 1999.
- 2 Y. L. Chu, P. S. Cheng, and R. Shivpuri, “Soldering Phenomenon in Aluminum Die Casting: Possible Causes and Cures”, NADCA Transactions, 1993, pp361-371.
- 3 Y. L. Chu, P. S. Cheng, and R. Shivpuri, “A Study of Erosive Wear in Die Casting Dies: Surface Treatments and Coatings”, NADCA Transactions, 1993, pp199-208.
- 4 R. Shivpuri, S. I. Chang, Y. I. Chu, M. Kuthirakulathu, “An Evaluation of H-13 Die Steel, Surface Treatments and Coatings for Wear in Die Casting Dies”, NADCA Transactions, 1991, p.391-397.
- 5 K. Venkatesan, R. Shivpuri, “An Investigation of the Effect of Process Parameters on the Washout in Die Casting Dies”, NADCA Transactions, 1995, pp361-371.
- 6 W. Kajoch and A. Fajkiel, “Testing the Soldering Tendencies of Aluminum Die Casting Alloys”, NADCA Transactions, 1991, pp67-74.
- 7E. K. Holz, “Trouble-Shooting Aluminum Die Casting Quality Problems” Transactions of 7th. SDCE International Die Casting Congress, 1972, Paper No. 4372.
- 8 S. Shankar and D. Apelian, “DIE SOLDERING: Mechanism Of The Interface Reaction Between Molten Aluminum Alloy And Tool Steel – Part I, Submitted to Met Trans.
- 9 S. Shankar and D. Apelian, “DIE SOLDERING: Mechanism Of The Interface Reaction Between Molten Aluminum Alloy And Tool Steel – Part II, Submitted to Met Trans.
- 10 M. Yu, Y. L. Chu, and R. Shivpuri, Ohio State University, Columbus, OH, unpublished research, 1997.
- 11 A. C. Paladino, “Die Lubricant Research Meets Die Casters' Needs”, Die Casting Engineers, May-June 1991, pp. 16-18.
- 12 H. G. Munson, T. H. Camel, “Development of a Semi-Permanent Release Coating for Die Casting”, NADCA Transactions, 1991, pp351-354.
- 13 P. N. Crepeau, B. L. Tiwari, and K. M. Rahmoeller, “ Characterization of Oxide Sludge, Dross and Inclusions in Aluminum Melting and Holding Furnaces”, Proc. Of the 3rd International Conference on Molten Aluminum Processing, Orlando, Fl, November 1992, pp 51-57.
- 14 J. L. Jarstad, "Understanding Sludge", Proc. Of the 14th SDCE International Die Casting Congress and Exposition, Toronto, Ont, Canada, May 11-14, 1987, Paper No. G-T87-011.
- 15 D. E. Groteke, “Elimination Hard Spots from Aluminum Die Castings”, Die Casting Engineer, Vol. 29, No. 5, Sept/Oct. 1985, pp 16-18, 20, 22, 24.
- 16 J. Gobrecht, “Gravity-Segregation of Iron, Manganese and Chromium in an Aluminum-Silicon Casting, Part I”, Giesserei, Vol. 61, No. 10, 1975, pp 263-265.
- 17 S. G. Shabestari, and J. E. Druzleski, “The Effecet of Solidification Condition and Chemistry on the Formation and Morphology of Complex Intermetallic Compounds in Aluminum-Silicon Alloys”, Cast Metals, Vol. 6, No. 4, 1994, pp 217-224.
- 18 A. Flores, J. C. Escobedo, M. Mendez, and J. Mendez, “Kinetics of the Formation, Growth and Sedimentation of the Al15(Fe, Mn)3Si2 Phase in Al-Si-Cu Alloys”, Trans. of International Die Casting Congress and Exposition, Drtroit, Michigan, USA, Sept. 30 – Oct. 3, 1991, pp 293-297.
- 19 M. R. Ghomashchi, “Intermetallic Compounds in an Al-Si Alloy Used in High Pressure Die-Casting”, Z Metallkunde, 78 (1987), 11, pp 784-787.
- 20 G. Gustafsson, T. Thorvaldsson, and G. L. Dunlop, “The Influence of Fe and Cr on the Microstructure of Cast Al-Si_Mg Alloys”, Met. Trans. A. 17A (1986), pp 45-52.
- 21 M. C. Flemings, “Solidification Processing", McGraw., London, 1974.
- 22 L. Arnberg, L. Backerud, and A. Dahle, “Castability of Aluminum Foundry Alloys”, An AFS Research Report, AFS, 1999, pp24-31.
- 23 J. Campbell, “Review of Fluidity Concepts in Casting”, Cast Metals, Vol. 7, No. 4, 1995, pp227-237.
- 24 M. Tiryakioglu, D. R. Askeland, and C. W. Ramsay, “Fluidity of 319 and A356: An Experimental Design Approach”, AFS Trans. Vol. 102, 1994, pp17-25.
- 25 M. C. Flemings, E. F. Niiyama, and H. F. Taylor, “Fluidity of Aluminum: An Experimental and Quantitative Evaluation”, AFS Trans. Vol. 69, 1961, pp625-635.
- 26 M. C. Flemings, F. R. Mollard, E. F. Niiyama, and H. F. Taylor, “Fluidity of Aluminum: Surface Tension, Vibration and Heat Losses in Runner Systems Effect”, AFS Trans. Vol. 70, 1962, pp1029-1039.
- 27 S. Floreen and D. V. Ragone, “The Fluidity of Some Aluminum Alloys”, AFS Trans. Vol. 65, 1957, pp391-393.
- 28 M. R. Sheshradri and A. Ramachandran, “Casting Fluidity and Fluidity of Aluminum and its Alloys”, AFS Trans. Vol. 73, 1965, pp292-304.
- 29 E. N. Pan and J. F. Hu, “Study on Fluidity of Al-Si Alloys”, AFS Trans. Vol. 105, 1997, pp413-418.
- 30 G. W. P. Rengstorff and T. R. Baruch, “Surface Energy Effect on Flow of Molten Metal in Thin Section”, AFS Trans. Vol. 70, 1962, pp920-923.
- 31 P. Bastien, J. C. Armbruster, and P. Azou, “Flowability and Viscosity”, AFS Trans. Vol. 70, 1962, pp400-409.
- 32 J. L. Jorstad, “Machinability of 380 Alloy: Effect of Minor Elements and Impurities", 10th SDCE International Die Casting Exposition & Congress, March 19-22, 1979, St. Louis, Missouri, Paper No. G-T79-072.
- 33 J. L. Jorstad, “Influence of Aluminum Casting Alloy Metallurgical Factor on Machinability", Modern Casting, December 1980, pp47-51.
- 34 R. C. Lemon, “Metallurgical Factor Related to Machining Aluminum Castings”, SAE Congress and Exposition, January 1967, Paper No. 607465.
- 35 D. L. Colwell, “Zinc in Aluminum Casting Alloys”, AFS Trans. Vol. 60, 1952, pp517-524.
- 36 R. C. Lemon, “Free Machining Aluminum Casting Alloys X310 and X335”, AFS Trans. Vol. 71, 1963, pp315-318.
- 37 C. A. Queener and W. L. Witchell, “Effect of Iron Content and Sodium Modification on the Machinability of Aluminum Alloy Die Castings”, AFS Trans. Vol. 73, 1965, pp14-19.
- 38 J. M. Fox, “Aluminum Alloy Casting Inclusions”, AFS Trans. Vol. 69, 1961, pp737-742.
- 39 G. L. Armstrong, “Metallurgical Defects Encountered in Machining Aluminum Die Castings", Trans. of the Society of Die Casting Engineers, March 1975, Paper No. G-T75-011.
9. Copyright:
*This material is Makhlouf M. Makhlouf and Diran Apelian's paper: Based on "Casting Characteristics of Aluminum Die Casting Alloys".
*Paper Source: [DOI URL] (DOI URL was not provided in the document, please add if available)
This material was summarized based on the above paper, and unauthorized use for commercial purposes is prohibited.
Copyright © 2025 CASTMAN. All rights reserved.