1. Overview:
- Title: Application of cores and binders in metalcasting
- Author: F. Czerwinski, M. Mir, and W. Kasprzak
- Publication Year: 2014
- Publishing Journal/Academic Society: International Journal of Cast Metals Research
- Keywords: Casting, Die casting, Casting cores, Binders, Organic binders
2. Research Background:
In metalcasting, cores are essential components utilized to create internal geometries and voids within cast products. The selection and performance of cores are significantly influenced by the casting technique employed, ranging from gravity casting to high pressure die casting. As component designs become increasingly complex and environmental regulations more stringent, the demands on core technology have intensified. Traditional sand cores, while widely adopted, present challenges in removal, particularly in high-pressure casting scenarios. Furthermore, conventional organic binders used in these cores are known to emit volatile organic compounds (VOCs), contributing to environmental concerns. These limitations underscore the necessity for advanced research and development in core materials and binder systems to meet the evolving needs of the casting industry.
3. Research Purpose and Research Questions:
This paper aims to provide a comprehensive overview of the fundamental aspects and recent global advancements in cores and binders employed in metalcasting operations. While not explicitly structured around research questions, the paper implicitly addresses the following key areas:
- Examination of the technical characteristics of sand and salt cores.
- Analysis of organic and inorganic binder systems, with a focus on the renewed interest in inorganic binders.
- Description of research and development efforts driving innovation in core technology.
- Review of the historical progression and current status of commercial core solutions within the casting industry.
- Emphasis on new development directions aimed at fulfilling complex component designs and adhering to stringent environmental regulations.
4. Research Methodology
This paper adopts a review-based research design, drawing upon an extensive body of existing literature, patents, and commercially available solutions to synthesize a handbook-level overview of core and binder technology. The data collection method primarily involves a comprehensive literature review, encompassing academic publications, industry reports, and patent documentation. The analysis method is descriptive, categorizing and summarizing information related to various core types, binder systems, and their respective properties, applications, and developmental trends. The research scope is focused on sand cores, salt cores, organic binders, inorganic binders, and core coatings within the context of metalcasting, with a particular emphasis on die casting applications.
5. Main Research Results:
This review paper elucidates the critical role of core materials and binder systems in modern metalcasting. Key research results are presented through a structured overview of different core and binder technologies:
- Core Materials: The paper highlights two major types of cores: sand cores and salt cores. Sand cores, historically prevalent, are composed of silica, zirconia, or olivine sands. Salt cores, introduced to address core removal challenges, are water-soluble, simplifying removal post-casting. Hybrid ceramic-sand cores are also discussed for highly demanding applications requiring precision and small passages.
- Core Coatings: To enhance the performance of sand cores, particularly in high-pressure die casting, core coatings are employed. These coatings, comprising fire-resistant powdered materials and binders, prevent metal infiltration, facilitate core separation, and improve surface finish.
- Core Binders: The paper categorizes core binders into organic and inorganic types. Organic binders, such as phenolic urethanes and furans, offer high strength but are associated with VOC emissions. Inorganic binders, including silicates (e.g., sodium silicate), cements, and phosphates, are gaining prominence due to their environmentally friendly nature and improved casting quality. Specific binder systems discussed include:
- GMBond: An environmentally friendly organic binder based on protein and catalyst.
- Resin-CO2: A water-based phenolic resin binder cured with CO2 gas, developed by Honda, offering environmental and operational benefits.
- Ecolotec: An inorganic silicate-based binder from Foseco, known for its environmental advantages.
- Cordis: An inorganic binder system from Hüttenes-Albertus (HA) Group, utilizing liquid silicate and powder additives, designed for conventional core shooting machines.
- AWB (Alternative Warm-Box) binder: An inorganic sodium silicate binder with NaOH additive, developed by Nemak Dillingen, Audi, and Minelco, emphasizing energy efficiency and reduced emissions.
- Inotec binder: An inorganic silicate-based binder used by Ashland, WD-Giesserei, Sud-Chemie, and BMW, suitable for high-temperature aluminum casting.
- α-starch composite binder: A binder composed of α-starch, kaolin, sodium silicate, dextrin, phosphate, and water, exhibiting good collapsibility and high-temperature strength.
- Comparative Analysis: The paper includes comparative data in tables and figures:
- Table 1: Comparison of process parameters between Phenolic-Urethane Cold-Box (PUCB) and Resin-CO2 processes.
- Table 2: Comparison of environmental performance between Phenolic-Urethane Cold-Box (PUCB) and Resin-CO2 processes.
- Table 3: Tensile strengths of selected binders at specific intervals.
- Table 4: Results for shake out test of selected binders.
- Figure 4: Effect of sand type on tensile strength of core manufactured using sodium silicate binder.
- Figure 12: Release gas comparison between Hot-box and Cordis cores and release gas pressure curves of two Cordis cores with different grain sizes.
- Figure 13: Comparison of condensate volume of Cordis binder with several other binder systems.
- Figure 11: High temperature stress-strain curves of cores manufactured with binder containing α-starch.
- Figure 10: Hot distortion test for cores manufactured with several types of binders.
- Visual Aids: The paper utilizes figures to illustrate key concepts and examples:
- Fig. 1: Examples of components manufactured with casting core⁴⁴
- Fig. 2: Casting core made of salt mixture²
- Fig. 3: Intake manifold casting using Cordis binding system (core is shown on top)³⁹
- Fig. 5: Flow chart showing production steps of sand core with surface coating³⁰
- Fig. 6: Cross-sectional view of surface region of sand core with surface coating³⁰
- Fig. 7: Schematics of core manufacturing using GMBond organic binder³³
- Fig. 8: Image (SEM) showing formation of bridge between silica sand grains in core, connected with GMBond organic binder³³
- Fig. 9: Core production cycle with organic binder Phenolic-Urethane Cold-Box (PUCB) by Honda³⁵
- Fig. 14: Schematics of bond formation by AWB binder⁴⁴
- Fig. 15: a connection bridge between sand grains in AWB binder and b binder morphology after core fracturing ⁴⁴
6. Conclusion and Discussion:
This paper concludes that cores and binders are integral to metalcasting, and their ongoing development is crucial for addressing the increasing complexity of casting designs and stringent environmental regulations. The review emphasizes the renewed interest in inorganic binders as a response to environmental and health concerns associated with organic binder emissions. Inorganic binders, alongside advancements in core coatings and core designs like salt and hybrid cores, represent promising avenues for enhancing casting performance and sustainability. The academic significance of this paper lies in its comprehensive overview of core and binder technologies, providing a valuable resource for researchers and industry professionals. Practically, the paper aids in informed decision-making regarding core material and binder selection, balancing performance requirements with environmental considerations. A limitation acknowledged is the review nature of the paper, which synthesizes existing research rather than presenting novel experimental data.
7. Future Follow-up Research:
The paper implicitly suggests several directions for future research and development. These include:
- Continued exploration and optimization of inorganic binder systems to match or exceed the performance of organic binders in all aspects, particularly strength and collapsibility.
- Development of novel core materials and designs that further simplify core removal and reduce casting defects.
- Research into advanced core coating technologies to enhance surface finish, thermal resistance, and shake-out properties.
- Investigation of sustainable and environmentally benign binder materials and core manufacturing processes to minimize the environmental footprint of metalcasting.
- Further investigation into the role of Inotec binder in casting porosity.⁴⁹
8. References:
Application of cores and binders in metalcasting
F. Czerwinski Canmet MATERIALSNatural Resources Canada, 183 Longwood Road South, Hamilton, Ontario, CanadaCorrespondence frank.czerwinski@nrcan.gc.ca
Abstract
This paper offers an overview of fundamentals and recent global developments of cores and binders used in metalcasting operations. The basic technical characteristics of salt and sand cores are provided along with organic and inorganic binder systems. A particular attention is paid to inorganic binders, receiving recently a renewed interest.
The description of research and development efforts is accompanied by history and present status of commercial solutions used by the casting industry. The new development directions, aimed at meeting the growing complexity of the component design requirements and ever-more stringent environmental regulations, are emphasised.
Keywords: CastingDie casting Casting cores Binders Organic binders
Introduction
Introduction In metalcasting, cores are mould parts used to form internal holes and cavities in a cast product. Depending on casting technique, the core can be completely integrated into the casting die/mould or loosely laid therein. After solidification of the metal, the die is taken apart and the cast product is released. Then the core is broken, removed from the product and usually disposed of, although there have been applications for re-usable cores.1
While some product cavities have functional purposes, such as cylinders in engine blocks, others are just for weight reduction. For example, some automotive engine parts such as camshafts or crankshafts have a designed hollow structure for a considerable weight reduction.
Depending on casting methods which include gravity casting, low pressure or high pressure die casting, the cores may require a high strength as the pressure increases with each technique. Examples of components manufactured with casting cores are shown in Fig. 1.
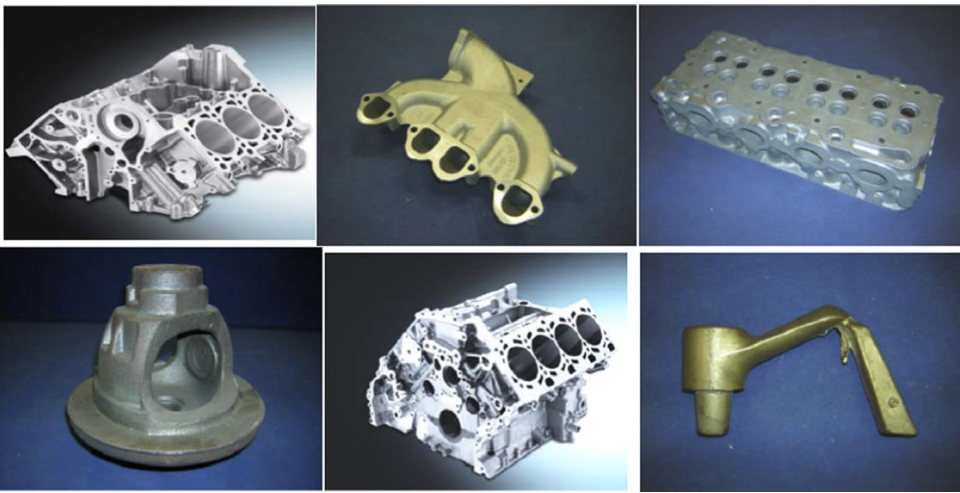
In order to make the casting core structurally strong to withstand operating pressures, binders are used. The core binder refers to the chemical mixture which adheres the filler to provide the core strength. Hence, the core represents a composite comprising the filler and the binder.
Since the typical volume of the latter is of the order of 1–3%, the filler is the predominant component of the core. However, despite such a low volume, conventional core binders emit up to 70% of a foundry volatile organic compound.2 The binder chemistry is, therefore, of key importance.
There are many types of cores in the casting industry; the primary focus of this paper is on sand cores with organic and inorganic binders as well as surface coatings for core strength increase. To provide the full picture, however, salt cores are also included. The objective is to provide an overview of fundamentals and the present status of commercial cores used by the global casting industry.
Core materials
The casting cores have to withstand tough requirements which depend on casting technique and alloy used. The temperature and its gradient represent one of many challenges. At the moment of casting the maximum temperature experienced by a core may exceed 1500uC on the metal side with a steep gradient through the core body.
A specific challenge occurs during die casting of aluminium alloys, known for having light weight, relatively high strength, high productivity, and high dimensional accuracy. For these reasons, it is widely being used in applications such as the automotive industry. Since more complicated shapes are required for die casting parts, it becomes difficult to manufacture such geometries without breaking the core. In general, in high pressure die casting, the flow velocity used exceeds 30 m s–1 at gates and the hydrostatic pressure is more than 60 MPa.
Such demanding casting conditions tend to cause high mechanical loading on the core.3 Thus, a core that is able to withstand these conditions is required. However, increasing the core strength causes a decrease in its collapsibility which translates to longer time for core removal.
Due to this, the total processing cost tends to increase, as well. To provide a solution, an extensive research has been conducted into producing the core that is able to withstand pressure and temperature, as required in die casting and at the same time it allows for its easy removal. Two major types of cores are explored here, sand and salt cores. Historically, sand cores were first commonly accepted by the general casting industry.
These cores are disposable ones, designed only to be used once. The problem with typical sand cores is that once the casting technique changes to that which requires higher pressure, the core becomes harder to remove from the cast product.4 To address the issue of core removal, salt cores were introduced.
The concept of salt cores is that once casting is completed, the core would not need to be broken down but rather dissolved with water.5 Using salt cores also helped to simplify manufacturing the complex shapes due to the good castability of salt mixtures without reinforcements.3 In applications where parts must be absolutely free of core sand residues, salt cores provide a solution. However, even the use of salt cores has some drawbacks.
The growing demand for shape complexity, strength and easy removal cause the industry to divert its attention between sand and salt cores. Moreover, a hybrid ceramic-sand core technology was developed for highly demanding applications.6 A casting process that combines aerospace ceramic cores with automotive sand cores was recently developed by Southwest Research Institute.7
This hybrid core is specifically suited for the purpose of allowing precision casting of extremely small passages in the automotive cast iron/steel components. It was designed to enable the production of heavy-duty diesel engines with the higher peak cylinder pressure capability than current state of the art engines. The ceramic section in the core is used where coolant passages between the engine gas exchange port walls and the fuel injector or spark plug are formed.
Salt cores
There are different mixtures to prepare a salt core. The most common use sodium carbonate (Na2CO3), potassium chloride (KCl) and sodium chloride (NaCl), melting these components and applying the moulding technique to create a core.8 This helps the core to obtain a high static compressive strength and dimensional stability, required during casting.
The detrimental features of salt mixtures are shrinkage cavities, microporosity and heat creaks. The latter may be created in the salt core when a volume change takes place such as during solidification.
Development directions of salt cores An example of the salt core chemistry includes bromine ions, carbonate ions, and at least one of sodium ions or potassium ions. As ion precursors, sodium bromide NaBr and sodium carbonate Na2CO3 are used.
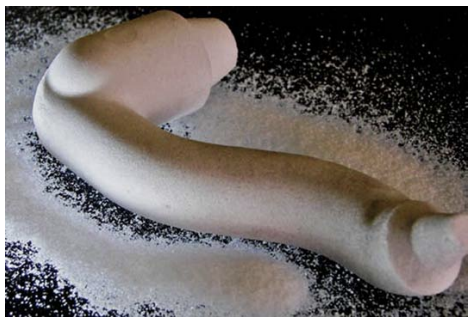
Since applications often require complex shapes than could be achieved by dry-compaction method, the ingredients are rather melted by heating to obtain a melt and then injected into the metal mould under high pressure. After solidification, the salt core is removed from the mould. An application of this core includes die casting and gravity casting.9,10 Another possible process to make a salt core uses a sodium chloride mixture, which is preheated to a temperature of maximum 30uC above liquidus and then poured into a mould.
The core is formed by solidifying the melt inside the mould.11 A semisolid processing technique was used in a concept to produce salt cores with a mixture of sodium carbonate, potassium carbonate, sodium chloride and potassium chloride.5
Since the salt core is formed by solidification in a metal mould after high pressure injection, having a precursor of semisolid mixture of sodium and potassium salts, instead of full liquid with a liquidus temperature of 700uC, allowed for precise reproduction of the shape required. To generate a semisolid slurry, the molten salt was undercooled into the 595–645uC temperature range, directly before injection.
The pressure applied on the cavity remained constant until mould opening, in order to obtain high strength. The concept was tested with the expendable salt cores used for water jacket in a closed-deck type, 4- cylinder engine block.
To remove the core, the engine block was submerged into a dissolution tank which contains liquids such as hydrochloric acid and hot water. Four binary systems for high pressure die casting cores, tested by Yamaha included NaCl–Na2CO3, KCl–K2CO3, KCl–NaCl, and K2CO3–Na2CO3. 3,12 To determine the core strength, a four point bending test was carried out.
It was found that the strength of NaCl–Na2CO3 was over 20 MPa in the Na2CO3 content region between 20 and 30 mol.-%, as well as 50 and 70 mol.-%. The highest strength for this system was 30 MPa at the composition of NaCl–70 mol.- %Na2CO3. For KCl–K2CO3 the strength was over 10 MPa in the K2CO3 region at 20 mol.-%, and between 50 and 60 mol.-%.
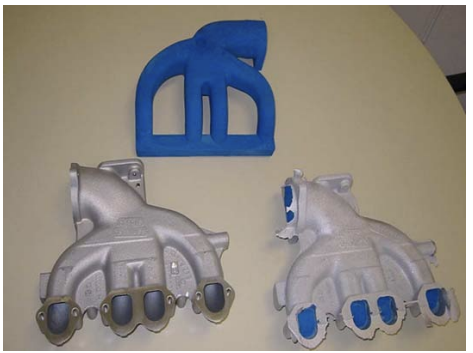
The highest strength for this system exceeded 25 MPa in between the K2CO3 content of 50 and 60 mol.- %. It was noticed that the strength of the systems KCl–NaCl and K2CO3–Na2CO3 was below 6 MPa. The reason was the solidification structure and the solid state phase transformations. It was also found that, in the NaCl–Na2CO3 system, the hardness value of the primary particles was higher than in the KCl–K2CO3 system, explaining why the NaCl– Na2CO3 strength was higher than that of KCl–K2CO3.
The salt cores for cast pistons produced by CeramTec AG and Austrian Foundry Institute have similar advantages as cores mentioned above. Their gas emission during core storage and casting is minimal, making it environmentally friendly as well (Fig. 2).
The cores are manufactured using a fully automated process.13 Another type of salt core that has a soluble and insoluble portion was developed by Brunswick Corporation.14 The aim was to make the soluble portion of the core to dissolve after casting was completed thus allowing removal of the insoluble portion.
Fraunhofer IFAM, is also researching salt cores, focusing attention on pressing, compaction and sintering. The density distribution and a selection of casting parameters are considered to control flow peaks in the salt core.15 The salt core technology was explored to produce a cylinder crankcase.16 To provide cooling, a water jacket usually surrounds a cylinder sleeve and is often open at the top on the cylinder side with crankcases.
The salt core is fixed when it is placed near the end of the cylinder sleeve on the cylinder head side. This increases the stability of the core during casting process. The salt core in Daimler’s patent16 comprises of a crown which is attached to a core shroud with the cylinder head. It is placed in the cylinder sleeve so that the crown covers one end of the sleeve on the cylinder head. As a result the salt core is connected to both the cylinder sleeve and the die casting tool. This helps the core to withstand the high pressure.
Based on the solution proposed, the salt core can be placed in different arrangements during the casting process thus changing some of the characteristics of the core. Besides improving the salt core properties, placement of the salt core can also help the process of casting a cylinder crankcase.
According to Daimler’s research,17 the salt core is able to support the water jacket against casting pressure and it is able to prevent undesired penetration of melt into the cavities at incorrectly sealed casting–mould contact surfaces. Since the salt core remains in the cylinder crankcase during the pressure die casting, this improves the stability of the cylinder liner during the encapsulation, where higher pressure occurs and increases the process safety.
The media connections of the coolant in the water jacket make it easier to dissolve the salt core as well when the casting process is completed.
The following is omitted. For more detailed information, please use the PDF View at the bottom.
References
- T. Arakawa, H. Tako and T. Tohata: ‘Casting core composition’, Nissan, Motor Patent US 5,612,393, 1997.
- F. S. Cannon, J. T. Fox, H. Huang, R. C. Voigt, J. C. Furness, P. D. Paulsen, G. Sanders, M. R. Lumadue, A. M. Jiles, P. J.
Munson, S. Komarneni, N. R. Brown and J. A. Devenne Jr: ‘Binder material’, USA Patent 20110108232, 2011. - Y. Yamada: ‘Method of manufacturing expendable salt core casting’, Yamaha Patent US 2011/0062624 A1, 2011.
- J. Campbell: ‘Complete casting handbook’; 2011, Kidlington, Elsevier.
- J. Yaokawa: ‘Method of manufacturing expendable salt core for casting and expendable salt core for casting’, Yamaha Patent US2009/0205801, 2009.
- M. C. Megel, D. A. Mckee, B. E. Westmoreland and K. E. Denholm: ‘Hybrid ceramic/sand core for casting metal parts having small passages’, USA Patent US 8,267,148 B1, 2012.
- Hybrid ceramic-sand core casting technology wins R&D 100 award, 2012, available at: www.asm.international.org
- P. Jelinek, F. Miksovsky, J. Beno and E. Adamkova: ‘Development of foundry cores based on inorganic cores’, Mater. Technol., 2013, 47, (6), 689–693.
- H. Rockenschaub and R. Gschwandter: ‘Salt cores’, Gieserei Institut, Leoben, Austria, 2012, available at: www.ogi.at
- The aluminum automotive manual; Applications, power train, pistons’, European Aluminum Association, 2011, available at: www.alueurope.eu
- K. Anzai: ‘Method for producing salt core for casting’, Tohoku University Patent EP 2 425 910 A1, 2012.
- J. Yaokawa, D. Miura, K. Anzai, Y. Yamada and H. Yoshii: ‘Strength od salt core composed of alkali carbonate and alkali chloride mixtures made by casting technique’, Mater. Trans., 2007, 48, (5), 1034–1041.
- H. Rockenschaub: ‘Completely water soluable salt cores for foundries’, Osterreichisches Giesserei Institute.
- D. Grebe: ‘Composite core for casting metallic objects’, Brunswick Co. Patent US 6,478,073 B1, 2002.
- M. Haesche: ‘Casting with complex geometries’, Casting Technology Fraunhofer IFAM.
- E. Graf: ‘Diecasting tool arrangement’, Daimler AG Patent US 2010/0116230, 2010.
- E. Graf: ‘Method for producing a cylinder crankase’, Daimler AG Patent US 2011/0174246 A1, 2011.
- A. Rabbi: ‘Sodium silicate glass as an inoganic binder in foundry industry’, Iranian Polym. J., 2002, 4, 10.
- J. Yaokawa: ‘Expendable salt core for casting’, Yamaha Patent US 2009/0288797 A1, 2009.
- D. H. T. Howell and R. Niekamp: ‘Casting sand core composition’, Honda Motor Company Patent US 2012/0118200 A1, 2012.
- V. LaFay: ‘Application of no-bake sodium silicate binder system,’ Int. J. Metalcast., 2012, Summer, 19–25.
- K. P. Group: ‘High pressure die cast ans sqeeze cast cyllinder block’, Alum. Technol., 2005, September, 2.
- B. Koch and R. Badenhope: ‘Mandrel holds expendable core in casting die’, Farley Inc. Patent US 4,981,168, 1991.
- R. Badenhope: ‘Framed printiut core for die and casting’, DoehlerJarvis Limited Partnership Patent US 5,259,438, 1993.
- J. Cestaro and R. Downing: ‘Web reinforced expandable core’, Doehler-Jarvis Limited Partnership Patent US 5,236,034, 1993.
- K. Nakamura and K. Maekawa: ‘Core for thin wall casting and thin wall hollow casting’, Honda Motor Co. Patent US 2010/ 0139586 A1, 2010.
- R. Downing: ‘Coated expendable cores for die casting dies’, Doehler Jarvis Limited Partneship Patent EP 0 373 196 B1, 1993.
- U. Mitsuki: ‘Sand core casting and method for producing the same’, Honda Motor Co. Patent EP 2 292 349 A1, 2009.
- B. Eshleman and T. Hider: ‘Vent passage heaters to remove core gas from casting dies’, Honda Motor Co. Patent US 8,176,968 B1, 2012.
- M. Ueno, H. Fujita, K. Yoshiara, K. Tomeba and H. Furusawa: ‘Sand core for casting and process for producing teh same’, Honda Motor Co. Patent US 2011/0094697, 2011.
- H. Bawa: ‘Manufacturing process - II, Tata McGraw-Hill Education, 2004.
- Y. Wang and F. Caannon: ‘Characterization of hydrocarbon emmisions from green sand foundry core binders by analytical pyrolysis’, Environ. Sci. Technol., 2007, 41, (22), 7922–7929.
- ‘GMBound the sand binder of the future, presentation to EPA’, Hormel Foods, 2005.
- D. Parker: ‘Benefits of organic sand binders in the core making process’, Foundry Trade J., 2005, 179, 238–239.
- T. Cordas and J. Griffin: ‘Honda’s iron foundry gets greener’, Foundry Manag. Technol., 2000, March, 32–36.
- ‘The Ecolatec process for clean and rapid production of core molds’, 2012, available at: www. foseco.com.
- J. Fox, F. Cannon, N. Brown, H. Huang and J. Furness: ‘Comparison of a new green foundry binder with conventional
foundry binders’, Int. J. Adhes. Adhes., 2012, 34, 34–45. - X. Zhou, J. Yang, D. Su and G. Qu: ‘The high temperature resistant mechanism of a-starch binder for foundry’, J. Mater. Process. Technol., 2009, 209, 5394–5398.
- K. Lochte et al.: ‘The inorganic binder system properties and experience’, Huttenes-Albertus Group, 2005.
- HA Cordis Presentation, HA Cordis International, 2009.
- K. Lochte et al.: ‘Properties and experience of an inorganic binder’, Foundry Trade J., 2006, 180, 28–30.
- Cordis Video, SkyCreation Video 2007, HA international’, available at: www.ha-international.com
- ‘EU Life money for innovations in the core package system (CPS) at NEMAK Dillingen, Germany Nemak’, available at: www.nemak.com
- ‘AWB-the binder system for a clean foundry MINELCO’, Presented at USEPA Meeting, Research Triangle Park, NC,
USA, October 2005. - R. Gerlach: ‘Facing the environmental challenges of today and tomorrow’, Foundary Trade J., 2008, 181, 130–131.
- A. Wolf: ‘AWB an environment- friendly core production technology’, Giesserei, 2004, 91, (6), 80–84.
- ‘Das Anorganische Warm-Box-Verfahren AWB Minelco’, available at: www.awb-online.com
- ‘Sud-Chemie successfully runs new environmentally-friendly production process for casting cores for BMW Group Sud-Chemie’,
- available at: www.sud-chemie.com
- T. Pabel: ‘Improved Properties of aluminum cast parts through the
- use of inorganic cores’, Int. Foundry Res., 2011, February.
- R. Bambauer: ‘New binder system friendly for environment’,
- Foundry Manag. Technol., 1993, February, 1.
- ‘Inorganic binder properties study - Casting Emission Reduction
- Program’, US Army contract W15QKN-05-D-0030, available at:
- www.cerp-us.org (accessed 2012).