This introductory paper is the research content of the paper "Analysis of Induction Motor with die cast rotor" published by IJIREEICE.
This introduction is the research content of "Analysis of Induction Motor with die cast rotor" published by [Publisher].
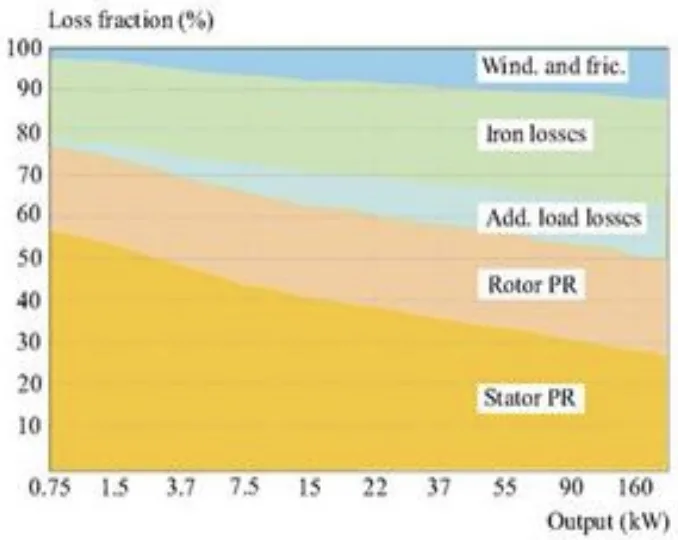
1. Overview:
- Title: Analysis of Induction Motor with die cast rotor
- Author: Rahul Tiwari¹, Dr.A.K.Bhardwaj²
- Publication Year: 2014
- Published Journal/Society: INTERNATIONAL JOURNAL OF INNOVATIVE RESEARCH IN ELECTRICAL, ELECTRONICS, INSTRUMENTATION AND CONTROL ENGINEERING (IJIREEICE), Vol. 2, Issue 6, June 2014
- Keywords: Induction motor, premium efficiency, efficiency improvement, die cast copper rotor, DCR technology, and efficiency standards
2. Abstract
This paper presents the choice between the utilizing a lower cost die cast or fabricated aluminium rotor versus the more expensive copper bar rotor. In industrialized countries Induction motors account for approximately 50% of the overall electricity use. Small increase in motor efficiency can make an overall big difference between the total electricity consumption. Using copper in place of aluminium would result in a motor efficiency higher than that of the original aluminium-based motor. This paper discusses the implementation of Die cast rotors, Motor efficiency, and increasing the prospect of the country by using DCR technology.
3. Research Background:
Background of the research topic:
The history of electric motor development starts since its invention by Nicola Tesla in 1888. The need for higher efficiency came into existence by the late 1970's.
Status of previous research:
Efficiency is the ratio of output power to input power. The Induction motor losses are classified into five categories: Iron losses, Stator I2R resistance losses, Rotor I2R resistance losses, Wind age and friction losses, Stray load losses. Mr. Fuchsloch and his SIEMENS colleagues provided the typical loss distribution, shown in Figure 1.
Need for research:
The factors responsible for the efficiency reduction and motor performances are inter dependent with each other. The cost of the motor and the commercial impact of the motor have to be considered as well.
4. Research purpose and research question:
Research purpose:
This paper deals with the various factors resulting the increase in the efficiency of the motors by using DCR technology.
Core research:
The advantages of using DCR technology, its technical issues, various trends in markets and overview of the competitor. About the adoption of the DCR technology in India.
5. Research methodology
{The paper presents a review and analysis of existing literature, standards, and technical data related to die-cast rotor technology, particularly focusing on copper die-cast rotors (CuDC) in induction motors. The research scope includes:}
- Historical review of motor efficiency standards (EPAct, NEMA, CEE, IEEMA, IEC).
- Analysis of induction motor loss components.
- Comparison of different rotor construction methods (ADC, CuDC, AlBar, CuBar).
- Examination of the challenges and advantages of CuDC technology.
- Discussion of the potential applications and market adoption of CuDC motors.
- The India's status of DCR adoption.
6. Key research results:
Key research results and presented data analysis:
- Induction motors with cast-copper rotor (CCR) bars rather than aluminum rotor bars operate at lower temperatures because they are more efficient.
- The higher conductivity characteristic of copper reduces motor energy losses by 10 to 20 percent.
- The problem with manufacturing CCRs was that copper's melting point is more than 400 degrees Celsius (760 degrees Fahrenheit)-higher than that of aluminum.
- In 2006, Siemens became the first manufacturer to offer CCR motors to the North American market.
- By using copper rotor the energy loss can be reduced by 15-23%.
- The cost of power consumed by the motor becomes 60-100 times the initial cost of the motor.
- The advantage of using copper rotor motor is of high torque at running speed and starting torque is lower than in aluminium rotor motors.
- The lower electrical resistance of copper results in a highly start up current keeping the slot area same.
- India is facing a shortage of power up to 20% during peak periods.
- 30-40% of electrical energy consumption is by motorized pump sets employed in agricultural sector.
- By merely replacing CFR with reduced core length DCR we can save 20% of the initial cost without sacrificing the overall efficiency of the pump.
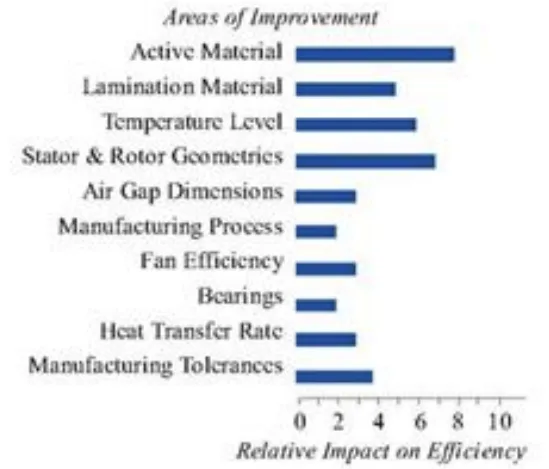
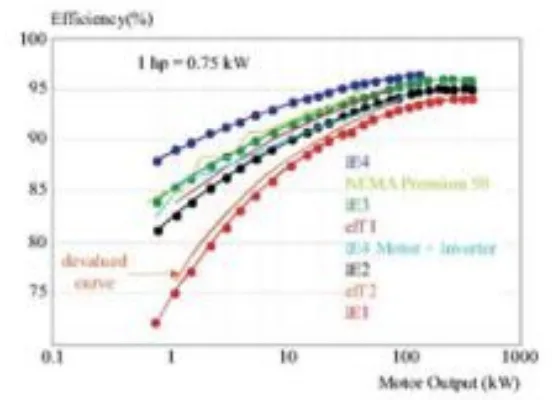
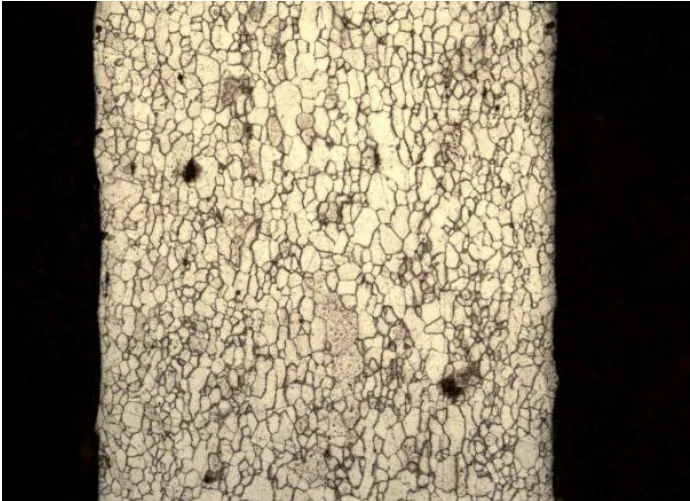
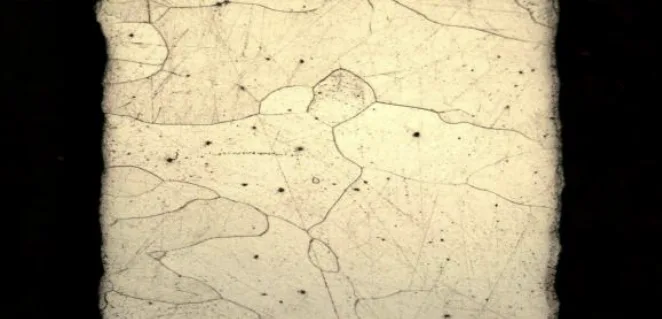
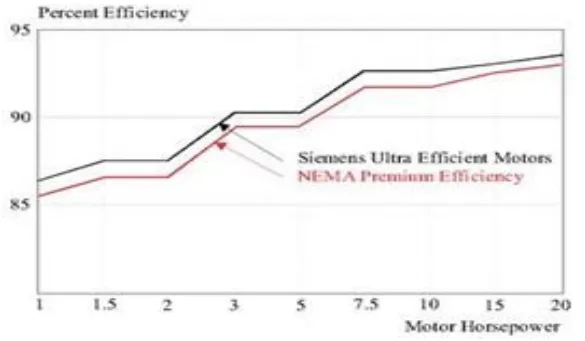
List of figure names:
- Fig. 1 Loss distribution for a 4-pole induction motor
- Fig. 2. Impact of the possible areas for improving the motor performance
- Fig. 3. Different efficiency levels comparison by CEMEP
- Fig:4- Not annealed laminate
- Fig:5- Annealed laminate
- Fig:6- Torque-speed and current-speed curve For a 5.5 kW motor
- Fig.7- Siemens Ultra Efficient Motor and its efficiency compared with Premium Efficiency (IE3)
7. Conclusion:
Summary of key findings:
The paper highlights the potential of Die Cast Copper Rotor (DCR) technology to significantly improve induction motor efficiency. It discusses the historical context of motor efficiency standards, the challenges in manufacturing copper rotors, and the advantages of DCR in terms of reduced losses, lower operating temperatures, and potential cost savings. The paper also explores the technical issues, such as starting torque and current, and presents a comparative analysis of DCR and aluminum die-cast rotors.
- Summary of research results: DCR technology offers a viable path to higher motor efficiency, exceeding existing standards. While manufacturing challenges have historically limited its adoption, recent advancements have made it more feasible.
- Academic significance of the research: The paper contributes to the body of knowledge on motor efficiency by providing a comprehensive analysis of DCR technology, including its technical aspects, benefits, and limitations.
- Practical implications of the research: The findings suggest that DCR motors can play a significant role in reducing energy consumption, particularly in applications like agricultural pumps, where efficiency improvements can lead to substantial cost savings and environmental benefits. The paper also highlights the potential for wider adoption of DCR technology in various industrial and commercial sectors.
8. References:
- [1] BOGLIETTI, A.–CAVAGNINO, A.-LAZZARI, M.- PASTORELLI, M.: Induction Motor Efficiency Measurements in Accordance to IEEE 112-B, IEC 34-2 and JEC 37 International standards, in Conf. Rec. IEEE-IEMDC'03, Madison, WI, 2003, pp. 1599-1605.
- [2] FUCHSLOCH. J. F.-FINLEY, W. R. WALTER, R. W.: The Next Generation Motor-Designing a New Approach to Improve the Energy Efficiency of NEMA Premium Motors, IEEE Ind. Appl. Magazine (Jan/Feb. 2008).
- [3] NEMA Standards Publication No. MG1, National Electrical Manufacturers Association (NEMA), Washington, D.C., 1993.
- [4] MANOHARAN, S.-DEIVASAHAYAM, M.- RANGANATHAN, G.: "Energy Efficient Motors - An Overview, SIEMA News Letter, Coimbatore 5 No. 12 (Dec 2006), 2-7.
- [5] KUSHARE, B. E. WAGH, K. K. KULKARNI, S. Y.: The Complete Guide to Energy Efficient Motors, International Copper Promotion Council (India) (2003), 18-20.
- [6] PARASILITI, F.-VILLANI, M.-PARIS, C.-WALTI, O.SONGINI, G.-NOVELLO, A. ROSSI, T. Three-Phase Induction Motor Efficiency Improvements with Die-Cast Copper Rotor Cage and Premium Steel, SPEEDAM 2004, Capri, June 16- 18, pp. 3-4.
- [7] BRUNNER, C. U.: International Harmonization of Motor Standards Saves Energy, APEC Workshop, Beijing, 3 December 2007.
- [8] BONNETT, A. H.-YUNG, C.: Increased Efficiency versus Increased Reliability, IEEE Industrial Applications Magazine (Jan/Feb. 2008).
- [9] HSU, J. S. FRANCO-FERREIRA, E. A. : Method of Manufacturing Squirrel Cage Rotors, U.S. Patent NO. 6,088,906, July 18, 2000.
- [10] FINLEYW. R.-HODOWANEC, M. M.: Selection of Copper versus Aluminium Rotors for Induction Motors, IEEE Transactions on Industry Applications 37 No. 6 (Nov/Dec 2001), 1563-1573.
- [11] PETERS, D. T. COWIE, J. G. BRUSH, E. F. Jr. MIDSON, S. P.: Use of High Temperature Die Materials and Hot Dies for High Pressure Die Casting Pure Copper and Copper Alloys, Proceedings of the 2002 Die Casting Congress, Rosemont, IL, Sept 30-Oct 2, 2002.
- [12] PETERS, D. T.—COWIE, J. G.—BRUSH, E. F. Jr.—MIDSON, S. P.: Advances in Pressure Die Casting of Electrical Grade Copper, Amer. Foundry Society Congress, Paper No. 02-002, Kansas City, MO, 2002.
- [13] PETERS, D. T.-MIDSON, S. P.-WALKINGTON, W. G.BRUSH, E. F, JR. COWIE, J. G.: Porosity Control in Copper Rotor die Castings, Transactions of the North American Die Casting Association Congress, Indianapolis, IN, 2003.
- [14] PETERS, D. T.-COWIE, J. G.-BRUSH, E. F. Jr. : Advantages of the Copper Rotor Motor Performance, Energy Savings and Environmental, Copper (Dr. Jean-Marie Welter, ed.), Published Online: 22 Oct 2007, Wiley-VCH Verlag GmbH & Co KgaA, 2006.
- [15] LIE, S.-Di PIETRO, C. Copper Die Cast Efficiency Improvement and Economic Consideration IEEE Transaction on Energy Conversion 10 No. 3 (Sep 1995), 419-424.
- [16] COWIE, J. G.-BRENDER, D. T. PETERS, D. T.: Die-Cast Copper Rotors for Improved Motor Performance, IEEE Pulp and Paper Conference, Charleston, SC, 2003.
- [17] PARASILITI, F.—VILLANI, M. : Design Strategies and Different Materials for High Efficiency Induction Motors. A Comparison, EEMODS, Heidelberg.
- [18] POLOUJADOFF, M.-MIPO, J. C.-NURDIN, M.: Some Economical Comparisons between Aluminum and Copper Squirrel Cages, IEEE Transactions on Energy Conservation 10 No. 3(Sep 1995), 415-418.
- [19] MALINOWSKI, J.-McCORMICK, J.-DUNN, K.: Advances in Construction Techniques of ac Induction Motors Preparation for Super-Premium Efficiency Levels, IEEE Transaction on Industry Applications 40 No. 6 (Nov/Dec 2004), 206-211.
- [20] PETERS, D. T.-COWIE, J. G.-BRUSH, E. F. Jr.-MIDSON, S. P. Die Cast Copper Motor Rotors: Die materials and process Considerations for Economical Copper Rotor Production, Energy Efficiency in Motor Driven Systems (EEMODS) conference, Treviso, Italy, 2002.
- [21] SAKHUJA, A. BREVICK, J. R.: Prediction of Thermal Fatigue in Tooling for Die Casting Copper via Finite Element Analysis, Materials Processing and Design: Modelling, Simulation and Applications, Proceedings of the 8th International Conference on Numerical Methods in Industrial Forming Process, AIP conference Proceedings, vol. 712, Columbus OH, 2004,
9. Copyright:
- This material is a paper by "Rahul Tiwari¹, Dr.A.K.Bhardwaj²": Based on "Analysis of Induction Motor with die cast rotor".
- Source of paper: Not provided in the document.
This material was created to introduce the above paper, and unauthorized use for commercial purposes is prohibited. Copyright © 2025 CASTMAN. All rights reserved.