This article introduces the paper 'An Automatic CAE Tool for autonomous feasibility assessment of aluminum gravity die castings – development and calibration' published by 'Rheinisch-Westfälischen Technischen Hochschule Aachen'.
1. Overview:
- Title: An Automatic CAE Tool for autonomous feasibility assessment of aluminum gravity die castings – development and calibration
- Author: Marcus Schopen, M.Sc.
- Publication Year: 2022
- Publishing Journal/Academic Society: Rheinisch-Westfälischen Technischen Hochschule Aachen
- Keywords: Not explicitly listed in the provided document excerpt, but based on the content, keywords would include: Automatic CAE Tool, Feasibility Assessment, Aluminum Gravity Die Castings, Development, Calibration, Casting Simulation, Solidification, Porosity, SDAS, Efficiency-enhancing methods.

length-dependent cooling rate 𝑇̇𝐹𝐿, engineering specification (eng. spec.), industrial prototypes (ind.
prot.)
2. Abstracts or Introduction
The paper addresses the increasing demand for fully automated CAE tools in next-generation development processes to enable multidisciplinary design optimization (MDO) and to allow design engineers to efficiently evaluate the feasibility and quality of cast part geometry variants in early design concept phases. The central research questions are:
I) "Is it possible to develop a fully Automatic CAE Tool which sets up, runs, and evaluates the simulation in a fast and efficient manner under the best initial conditions and needs no manual user intervention of a casting expert for a quantitative feasibility assessment?"
II) "Which level of test data quality is necessary to calibrate and validate the developed Automatic CAE Tool and its efficiency-enhancing methods – so accurate and reliable that the whole CAE method becomes transferable to similar parts with new challenges?"
The study focuses on "filling success, secondary dendrite arm spacing (SDAS) as a quality measure for the microstructure and shrinkage porosity" as key feasibility metrics. The developed CAE tool assumes "the best possible initial casting process conditions (upper limit) in terms of casting defect reduction" and is designed for "early design phases in between the topology optimization and the product design". The solution is based on "best-practice rules (upper limit)" and aims to provide "a recommendation for the final process design, e.g., number/position of feeder and inlets." The tool's calibration and validation are crucial, along with studying its "sensitivity and case-independence".
3. Research Background:
Background of the Research Topic:
The in-service performance of cast parts is influenced by both "part design" and "manufacturing effects like cast part orientation in mold, gating and feeders (size, location), and process parameters (filling rates, pouring, and mold temperatures)". "Casting process restrictions and requirements are of equal importance in design optimization as attribute requirements (strength, durability, noise vibration harshness NVH, crash)." The conventional CAE approach relies on "casting expert skills and expert-guided analysis loops", which limits the number of design iterations and restricts CAE application to later product development phases.
Status of Existing Research:
Existing CAE approaches for casting evaluation are often "manual, computer-aided engineering (CAE) approach" requiring expert intervention. Literature review highlights the importance of "filling success, microstructure (SDAS), and shrinkage porosity" as key quality metrics. Previous research has explored alloys for chassis parts, permanent mold casting, quality metrics, casting defects, and optimization strategies for castings. However, a fully automated CAE tool for early design phase feasibility assessment is needed.
Necessity of the Research:
"In next-generation development processes, fully automated CAE tools and expert systems are required to enable multidisciplinary design optimization (MDO) tools as well as design engineers to quantitatively and efficiently evaluate the feasibility and quality of geometry variants of the cast part upfront in early design concept phases." There is a clear necessity for an "Automatic CAE Tool" that can efficiently and autonomously assess casting feasibility in early design stages, reducing reliance on manual expert intervention and enabling faster design iterations.
4. Research Purpose and Research Questions:
Research Purpose:
The primary research purpose is to develop and validate an "Automatic CAE Tool" for "autonomous feasibility assessment of aluminum gravity die castings". This tool aims to "substitute an Automatic CAE Tool with open interfaces for integration in optimization loops or as a stand-alone tool for the casting expert-guided manual CAE approach".
Key Research:
The key research focuses on:
- Developing an "Automatic CAE Tool" that "sets up, runs, and evaluates the simulation in a fast and efficient manner under the best initial conditions and needs no manual user intervention".
- Calibrating and validating the tool and its "efficiency-enhancing methods" to ensure accuracy, reliability, and transferability to similar parts with new challenges.
- Investigating "filling success, secondary dendrite arm spacing (SDAS) as a quality measure for the microstructure and shrinkage porosity" as key metrics.
Research Hypotheses:
The paper does not explicitly state research hypotheses in a traditional format. However, implicit hypotheses can be inferred from the research questions and objectives:
- It is hypothesized that a fully automatic CAE tool can be developed for autonomous feasibility assessment of aluminum gravity die castings.
- It is hypothesized that efficiency-enhancing methods can be implemented in the CAE tool to significantly reduce calculation time without compromising accuracy for directional feasibility assessment.
- It is hypothesized that experimental data can be used to calibrate and validate the Automatic CAE Tool and its efficiency-enhancing methods.
5. Research Methodology
Research Design:
The research employs a development and validation approach. It involves developing an "Automatic CAE Tool", calibrating it using experimental data from fluidity spiral tests, validating it with Multi-Tool experiments, and assessing its plausibility and sensitivity on industrial prototypes.
Data Collection Method:
Experimental data was collected from casting experiments using:
- Fluidity spiral mold to investigate cooling and filling degree.
- Multi-Tool demonstrator to evaluate cooling, filling behavior, and porosity.
- Thermocouples (TCs) to measure temperature curves during casting.
- X-ray and CT scans to analyze porosity.
- Metallography and SEM to characterize microstructure and porosity type.
- Archimedes density measurement and Blister test for porosity quantification.
Analysis Method:
The research utilizes a combination of:
- Literature review to establish best practices and design rules.
- CAE simulation using Inspire Cast® for tool development and validation.
- Analytical methods for filling success assessment.
- Statistical analysis (correlation matrix, regression analysis) to calibrate and validate the CAE tool and analyze experimental data.
- Quantitative and qualitative comparison of experimental and simulation results for validation and plausibility assessment.
Research Subjects and Scope:
The research focuses on:
- Aluminum gravity die castings, specifically using A356 alloy.
- Two demonstrator geometries: fluidity spiral and Multi-Tool.
- Industrial prototype chassis parts (FLCA and RLCA) for application and sensitivity study.
- Key quality metrics: filling success, SDAS, and shrinkage porosity.
- Process parameters: pouring temperature, mold temperature, and cooling conditions.
6. Main Research Results:
Key Research Results:
- Development of a fully "Automatic CAE Tool" for autonomous feasibility assessment of aluminum gravity die castings.
- Implementation of "efficiency-enhancing methods": substitution of filling simulation with pure solidification and analytical filling success assessment, and implementation of 1D-components instead of 3D-components.
- Calibration of the CAE tool using fluidity spiral experiments and validation using Multi-Tool experiments.
- Validation of the analytical filling criterion and 1D-feeder components through experiments.
- Demonstration of the tool's sensitivity and plausibility on industrial prototypes (FLCA and RLCA).
- Identification of the limitations of using default HTC data sets and the need for HTC component classes for different cast part designs.
Analysis of presented data:
The paper presents extensive data analysis, including:
- Temperature curves comparison between experiments and simulations, demonstrating good match after calibration.
- Comparison of geometrical flow length and spiral length, showing almost perfect match.
- Filling degree comparison between experiment and simulation, showing good agreement with =0.3.
- Porosity estimation comparison with CT-Scans, showing divergence in pore location due to inhomogeneous HTCs and limitations of porosity simulation in Inspire Cast®.
- Sensitivity study on FLCA design variants, demonstrating the tool's ability to identify relevant differences in filling success, SDAS, and porosity.
Figure Name List:
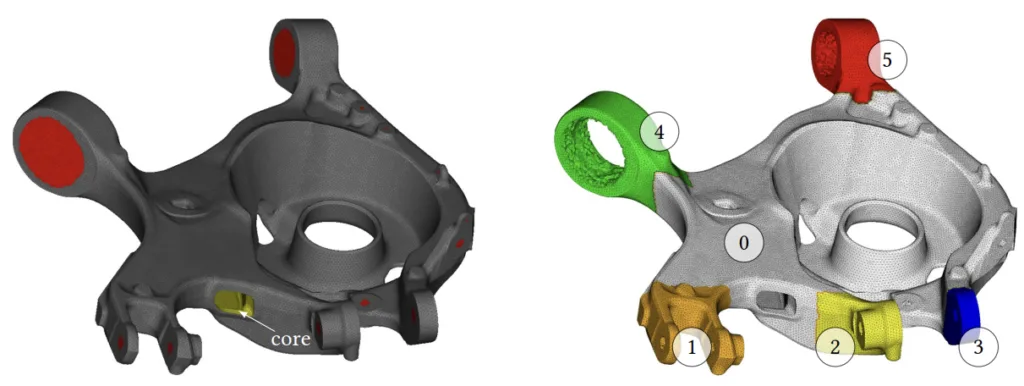
(b) mesh, critical area IDs CAID 0–5, only fullymachined (=evaluation) nodes visible
Fig. 0.2: Exemplary feature detection and critical areas of a rear lower control arm (RLCA)
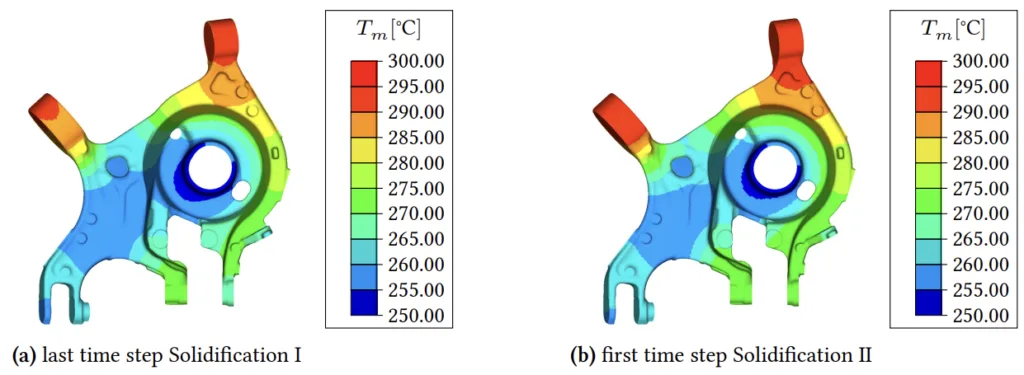
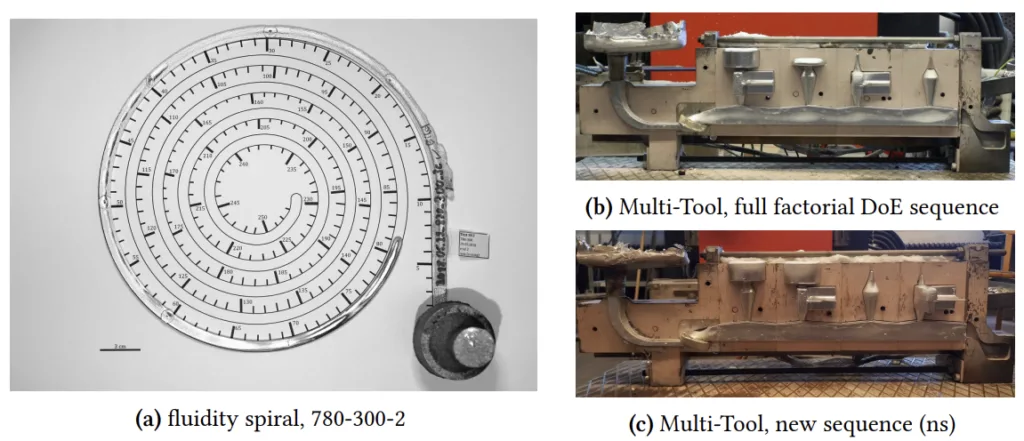
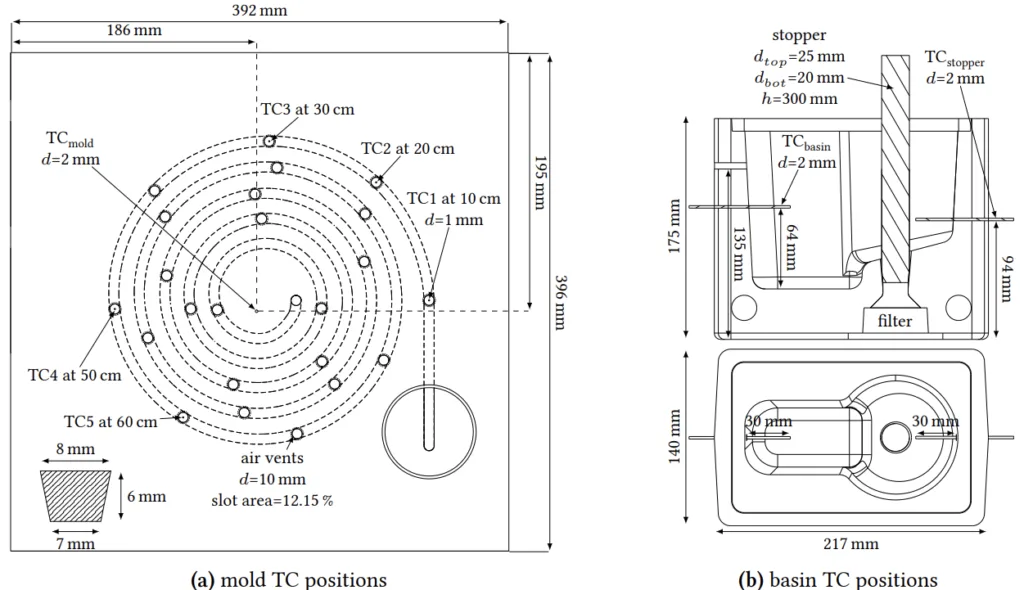
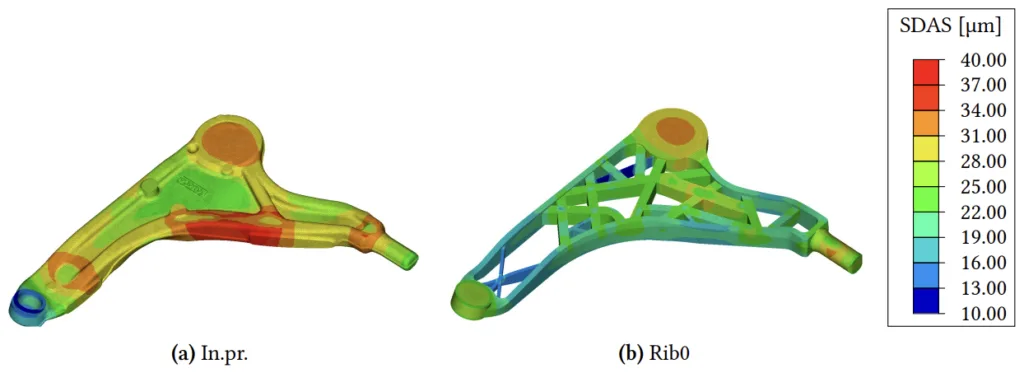
- Fig. 0.1: Automatic CAE Tool overview
- Fig. 0.2: Exemplary feature detection and critical areas of a rear lower control arm (RLCA)
- Fig. 0.3: Exemplary shrinkage porosity ℎ assessment of Solidification I results in feeder and inlet placement for Solidification II
- Fig. 0.4: Comparison of mold temperature fields
- Fig. 0.5: Final assessment of Solidification II
- Fig. 0.6: Exemplary output text file of Assessment II
- Fig. 0.7: The poured geometries, fluidity spiral and, the newly developed Multi-Tool with two different sequences
- Fig. 0.8: Fluidity spiral mold dimensions & instrumentation
- Fig. 0.9: Overview of cross and spindle dimensions
- Fig. 0.10: Multi-Tool design with instrumentation
- Fig. 0.11: Sample and thermocouples TC labeling definition for the Multi-Tool
- Fig. 0.12: Temperature calibration, experimental and calculated temperatures
- Fig. 0.13: Comparison of calculated geometrical flow length ∗ and spiral length
- Fig. 0.14: Spiral length comparison of the experiments with the simulation
- Fig. 0.15: Filling degree comparison of Cf and Cp between experiment and simulation
- Fig. 0.16: Spindle and cross with air pipe CT Scan results for different temperature setups
- Fig. 0.17: Calculated porosity values for Sp and Cp of full factorial DoE
- Fig. 0.18: Different FLCA design variants, wall thickness
- Fig. 0.19: FLCA design and multi-/single-inlet impact on maximum geometrical flow length ∗ , SDAS and number of critical pores
- Fig. 0.20: FLCA design, multi-/single-inlet, analytical filling time type
∗ −
and critical solid fraction value 0.3–0.7 impact on filling success - Fig. 0.21: RLCA temperature, analytical filling time type
∗ −
and critical solid fraction value 0.3–0.7 impact on filling success - Fig. 1.1: Casting CAE Approach
- Fig. 1.2: The thesis work packages are divided into development and calibration and plausibility phase
- Fig. 2.1: Exemplary aluminum chassis parts
- Fig. 2.2: Alloys in chassis parts
- Fig. 2.3: Al-Si phase diagram
- Fig. 2.4: Schematic illustration of permanent mold setup
- Fig. 2.5: Standard molds for fluidity determination
- Fig. 2.6: Comparison of different fluidity spiral lengths
- Fig. 2.7: Schematic visualization of the coating or mold roughness effect
- Fig. 2.8: Schematic illustration of the interface between the melt and a coated mold
- Fig. 2.9: Literature values for heat transfer coefficients (HTC)
- Fig. 2.10: Schematic illustration of dendrite formation
- Fig. 2.11: A356 SDAS vs. liquidus time curves from literature
- Fig. 2.12: Impact of wall thickness on mean SDAS ̄ (SDAS)
- Fig. 2.13: SDAS values at different distances from the casting surface
- Fig. 2.14: Mold ( ) and pouring temperature ( ), wall thickness and location impact on SDAS of A356
- Fig. 2.15: Hydrogen solubility in pure aluminum at 1 atm
- Fig. 2.16: Characteristic pore morphology of shrinkage and gas pore for A356
- Fig. 2.17: Porosity results at macro-graphs related at different
- Fig. 2.18: Impact of wall thickness on porosity, CT defect volume def of ZL114A alloy plate casting
- Fig. 2.19: Geometric manufacturing constraints at castings
- Fig. 2.20: Steps in casting simulation and optimization
- Fig. 2.21: Gating systems variants of a box-shaped casting
- Fig. 2.22: Improved bottom-gated system due to progressively improved casting system by height reduction
- Fig. 2.23: Schematic illustration of the shrinkage porosity types
- Fig. 2.24: Schematic illustration of melt entering the mold at different initial velocities
- Fig. 2.25: Feeder optimization of a control arm resulted in better yield
- Fig. 2.26: Total amount of oxide particles total
oxid and oxide particles in cast part cast
oxid - Fig. 2.27: Simplification steps used in [120] related to development time
- Fig. 2.28: Comparing the Hot Spots FSTime as a measure of defect probability
- Fig. 2.29: Solidification simulation comparison of standard and improved optimization
- Fig. 2.30: Integrated casting simulation
- Fig. 2.31: Typical flow chart of Integrated Computational Materials Engineering (ICME)
7. Conclusion:
Summary of Key Findings:
The study successfully developed and calibrated an "Automatic CAE Tool" for autonomous feasibility assessment of aluminum gravity die castings. The tool effectively integrates efficiency-enhancing methods like substituting filling simulation with pure solidification analysis and utilizing 1D-components. Experimental validation confirmed the tool's directional accuracy and identified areas for further improvement, particularly regarding HTC modeling and gas porosity prediction. The tool demonstrates sensitivity to design variations and process parameters, providing valuable insights for early design phase optimization.
Academic Significance of the Study:
This research contributes to the field of die casting by providing a novel, automated CAE tool that addresses the need for efficient feasibility assessment in early design stages. The tool's development and validation methodology, including the calibration approach and the investigation of efficiency-enhancing methods, offer valuable insights for researchers in casting simulation and MDO. The study also highlights the limitations of current measurement techniques for accurate simulation calibration and points towards future research directions in HTC modeling and gas porosity simulation.
Practical Implications:
The Automatic CAE Tool has significant practical implications for the die casting industry. It offers:
- Reduced reliance on manual expert intervention, enabling faster and more efficient feasibility assessments.
- Integration into MDO workflows, facilitating rapid exploration of design variants and optimization for casting feasibility and quality.
- Directional, yet plausible results for early design phase decision-making, guiding design engineers towards feasible and high-quality cast part designs.
- A basis for developing more predictive CAE tools by highlighting areas for further research, such as HTC modeling and gas porosity simulation.
Limitations of the Study and Areas for Future Research:
The study acknowledges limitations, primarily related to:
- Incomplete metric coverage (e.g., cost aspects, supplier facility specifics), limiting the CAE evaluation to directional, not fully predictive results.
- Accuracy limitations due to the HTC problem and the lack of gas porosity simulation in Inspire Cast®.
- Simplifications inherent in CAE modeling, requiring calibration and validation against experimental data.
- The need for further refinement of measurement techniques to obtain more accurate data sets for simulation calibration.
Areas for future research include:
- Development of physically based, efficient methods for casting process simulation, particularly for gap-dependent HTC and gas porosity.
- Determination of HTC component classes for different cast part designs to improve simulation accuracy.
- Further investigation of the impact of process parameters and design variations on porosity formation.
- Exploration of coupling casting simulation with thermomechanical simulation for more accurate HTC estimation.
- Development of more sophisticated methods for handling complex flow phenomena and melt behavior in CAE tools.
8. References:
- [1] Ahmadein, M.; Pustal, B.; Wolff, N.; BÜhRig-PolaczeK, A.: “Determination and verification of the gap dependent heat transfer coefficient during permanent mold casting of A356 aluminum alloy.” In: Materialwissenschaft und Werkstofftechnik 48.12 (2017), pp. 1249–1256.
- [2] AichbeRgeR, W.; RieneR, H.; DannbaueR, H.: “Regarding Influences of Production Processes on Material Parameters in Fatigue Life Prediction.” In: SAE Technical Paper. SAE International, 2007.
- [3] AKhtaR, S.; ARnbeRg, L.; Di Sabatino, M.; DispinaR, D.; SyveRtsen, M.: “A comparative study of porosity and pore morphology in a directionally solidified A356 alloy.” In: International Journal of Metalcasting 3.1 (2009), pp. 39–52.
- [4] AllaiRe, G.; Jouve, F.; Michailidis, G.: “Molding direction constraints in structural optimization via a level-set method.” In: Variational Analysis and Aerospace Engineering. Springer, 2015, pp. 1–39.
- [5] Allison, J.: “Integrated Computational Materials Engineering: A Perspective on Progress and Future Steps.” English. In: JOM 63.4 (2011), pp. 15–18.
- [6] Allison, J.; Li, M.; WolveRton, C.; Su, X.: “Virtual aluminum castings: An industrial application of ICME.” In: JOM 58.11 (2006), pp. 28–35.
- [7] AltaiR EngineeRing, Inc: Altair HyperMesh™ – High-Fidelity Finite Element Modeling. 2019.
- [8] AltaiR EngineeRing, Inc: Altair HyperView™ – CAE Results Visualization and Reporting. 2019.
- [9] AltaiR EngineeRing, Inc: Altair SimLab™ – Multiphysics Workflows with CAD Associativity. 2020. uRl: https://www.altair.com/simlab/ (visited on 12/08/2020).
- [10] AltaiR EngineeRing, Inc: Show Simulation Results. 2019. uRl: https://solid%5Cthink%5C-ing.com/helpst/2019.2/cast/en_us/topics/cast/analysis/view_simulation_results_t.htm#view_simulation_results_t (visited on 11/26/2019).
- [11] AmeRican FoundRy Society: Aluminum Permanent Mold Handbook. Des Plaines, Illinois, 2001.
- [12] Anastasiou, K. S.: “Optimization of the aluminium die casting process based on the Taguchi method.” In: Proceedings of the Institution of Mechanical Engineers, Part B: Journal of Engineering Manufacture 216.7 (2002), pp. 969–977.
- [13] “356.0 and A356.0: Al-Si-Mg High-Strength Casting Alloys.” In: Properties and Selection of Aluminum Alloys. Ed. by AndeRson, K.; WeRitz, J.; Kaufman, J. G. ASM International, 2019.
- [14] ASM: “Al (Aluminum) Binary Alloy Phase – Diagrams, Alloy Phase Diagrams.” In:ASM Handbook. Vol. 3. ASM International, 2016, pp. 113–139.
- [15] ASTM InteRnational: E155-15. Reference Radiographs for Inspection of Aluminum and Magnesium Castings. Standard. 2015.
- [16] ASTM InteRnational: E2422-17. Digital Reference Images for Inspection of Aluminum Castings. Standard. 2017.
- [17] Baez, J. C.; Gonzalez, C.; Chavez, M. R.; CastRo, M.; JuaRez, J.: “Fourier thermal analysis of the solidification kinetics in A356/SiCp cast composites.” In: Journal of Materials Processing Technology 153-154 (2004). Proceedings of the International Conference in Advances in Materials and Processing Technologies, pp. 531–536.
- [18] BÄhR, R.; Rehse, C.; StRoppe, H.: “Auswirkung von Porosität auf Festigkeit und Lebensdauer von Gussteilen - theoretische Modellierung.” de. In: Deutscher Gießereitag 2014. 2014.
- [19] Bazhenov, V. E.; PetRova, A. V.; Koltygin, A. V.: “Simulation of Fluidity and Misrun Prediction for the Casting of 356.0 Aluminum Alloy into Sand Molds.” In: International Journal of Metalcasting 12.3 (2018), pp. 514–522.
- [20] BDG: P202. Volumendefizite von Gussstücken aus Aluminium-, Magnesium- und Zinkgusslegierungen. 2010.
- [21] BDG: P203. Porositätsanalyse und -beurteilung mittels industrieller Röntgen-Computertomographie (CT). 2019.
- [22] Beganovic, T.: “Evolution im Aluminium-Guss von Fahrwerk-Komponenten.” PhD thesis. Fakultät für Werkstoffwissenschaft und Werkstofftechnologie der Technischen Universität Bergakademie Freiberg, 2016.
- [23] BETA Simulation Solutions: ANSA – The advanced CAE pre-processing software for complete model build up. 2018.
- [24] BETA Simulation Solutions: META – The high performance multi-disciplinary CAE post-processor. 2018.
- [25] Biancolini, M. E.: “Mesh Morphing and Smoothing by Means of Radial Basis Functions (RBF).” In: Handbook of Research on Computational Science and Engineering. IGI Global, 2012, pp. 347–380.
- [26] Bonollo, F.; Timelli, G.; GRamegna, N.; B.Molinas: “Permanent Mold Casting of Aluminum Alloys: Correlation among Processing, Microstructure and Simulation.” In: Proceeding of 3ʳd International Conference High Tech Die Casting. 2006.
- [27] BousKa, O.: “The effect of different casting parameters on the relationship between flowability, mould filling capacity and cooling conditions of Al-Si alloys.” In: Metalurgija-Journal of Metallurgy 14 (2008), pp. 18–30.
- [28] BRabazon, D.; BRowne, D. J.; CaRR, A. J.: “Experimental investigation of the transient and steady state rheological behaviour of Al–Si alloys in the mushy state.” In: Materials Science and Engineering: A 356.1 (2003), pp. 69–80.
- [29] BRamann, H.; PavlaK, L.: “Innovatives Produktdesign und robuste Prozessauslegung durch virtuelles Experimentieren mit der Gießprozess-Simulation.” In:GIESSEREI 102.3 (2015), pp. 28–39.
- [30] BRamann, H.; LeinewebeR, L.; StuRm, J. C.: “Innovatives Produktdesign und robuste Prozessauslegung im Druckgießprozess mit Autonomous Engineering.” In: GIESSEREI 105.1 (2018), pp. 34–45.
- [31] BRandenbeRgeR, U.: Giess- und Anschnitttechnik nach Friedrich Nielsen. Ed. by BRandenbeRgeR, U. online. 2009.
- [32] BRandenbeRgeR, U. et al.: Sand- und -Kokillenguss aus Aluminium. Bundesverband der Deutschen Gießerei-Industrie (BDG), 2010.
- [33] BRůna, M.; SlÁdeK, A.; KuchaRčiK, L.: “Formation of porosity in Al-Si alloys.” In: ́ Archives of Foundry Engineering 12.1 (2012), pp. 5–8.
- [34] BRůna, M.; BolibRuchovÁ, D.; PastiRčÁK, R.: “Numerical Simulation of Porosity for Al Based Alloys.” In: 177 (2017), pp. 488–495.
- [35] BRunhubeR, E.: Leichtmetall- und Schwermetall-Kokillenguss. Schiele & Schön, 1966.
- [36] BÜhRig-PolaczeK, A.; Michaeli, W.; SpuR, G.: Handbuch Urformen. Carl Hanser Verlag GmbH & Co. KG, 2013.
- [37] Cabannes, P. M.; FoRRest, R.; MuRatoRe, G.; RÖdteR, H.; GagnÉ, M.: Gusseisen mit Kugelgraphit - Das Wichtigste über Anschnitt und Speisertechnik. Rio Tinto iron & Titanium Inc., 2002.
- [38] CaliaRi, D.; Timelli, G.; Bonollo, F.; AmalbeRto, P.; GioRdano, P.: “Fluidity of aluminium foundry alloys: Development of a testing procedure.” In: Metallurgia Italiana 107.6 (2015), pp. 11–18.
- [39] Cambell, J.; HaRding, A.: “3201: Introduction to Casting Technology.” In: TALAT Lecture. Birmingham: EAA – European Aluminium Association, 1994.
- [40] Campbell, J.: “Invisible macrodefects in castings.” In: Le Journal de Physique IV 3.C7 (1993), pp. 861–872.
- [41] Campbell, J.: “Review of fluidity concepts in casting.” In: Cast Metals 7 (4 1995), pp. 227–237.
- [42] Campbell, J.: “Chapter 10 - The 10 Rules for Good Castings.” In: Complete Casting Handbook (Second Edition). Ed. by Campbell, J. Second Edition. Boston: Butterworth-Heinemann, 2015, pp. 535–638.
- [43] Campbell, J.: “Chapter 11 - Filling system design fundamentals.” In: Complete Casting Handbook. Ed. by Campbell, J. Oxford: Butterworth-Heinemann, 2011, pp. 741–756.
- [44] Campbell, J.: “Chapter 2 - Entrainment.” In: Complete Casting Handbook. Ed. by Campbell, J. Oxford: Butterworth-Heinemann, 2011, pp. 19–103.
- [45] Campbell, J.: “Chapter 3 - Flow.” In: Complete Casting Handbook. Ed. by Campbell, J. Oxford: Butterworth-Heinemann, 2011, pp. 105–153.
- [46] Campbell, J.: “Chapter 4 - Molds and cores.” In: Complete Casting Handbook. Ed. by Campbell, J. Oxford: Butterworth-Heinemann, 2011, pp. 155–186.
- [47] Campbell, J.: “Chapter 5 - Solidification structure.” In: Complete Casting Handbook. Ed. by Campbell, J. Oxford: Butterworth-Heinemann, 2011, pp. 187–253.
- [48] Campbell, J.: “Chapter 6 - Casting alloys.” In: Complete Casting Handbook. Oxford: Butterworth-Heinemann, 2011, pp. 255–390.
- [49] CaRl Zeiss MicRoscopy GmbH: AxioVision 4 Modul MosaiX. 2019. uRl: https : / / www.micro-shop.zeiss.com/de/de/system/axiovision+software/software+axiovision/module+biomed%252Fmat/000000-1235-913 (visited on 11/18/2019).
- [50] CaRlson, K. D.; BecKeRmann, C.: “Prediction of Shrinkage Pore Volume Fraction Using a Dimensionless Niyama Criterion.” In: Metallurgical and Materials Transactions A 40.1 (2009), pp. 163–175.
- [51] Chen, R.; Shi, Y.-F.; Xu, Q.-Y.; Liu, B.-C.: “Effect of cooling rate on solidification parameters and microstructure of Al-7Si-0.3Mg-0.15Fe alloy.” In: Transactions of Nonferrous Metals Society of China 24.6 (2014), pp. 1645–1652.
- [52] Chen, R. et al.: “Correlation of solidification microstructure refining scale, Mg composition and heat treatment conditions with mechanical properties in Al-7Si-Mg cast aluminum alloys.” In: Materials Science and Engineering: A 685 (2017), pp. 391–402.
9. Copyright:
- This material is "Marcus Schopen"'s paper: Based on "An Automatic CAE Tool for autonomous feasibility assessment of aluminum gravity die castings – development and calibration".
- Paper Source: 10.18154/RWTH-2022-07470
This material was summarized based on the above paper, and unauthorized use for commercial purposes is prohibited.
Copyright © 2025 CASTMAN. All rights reserved.