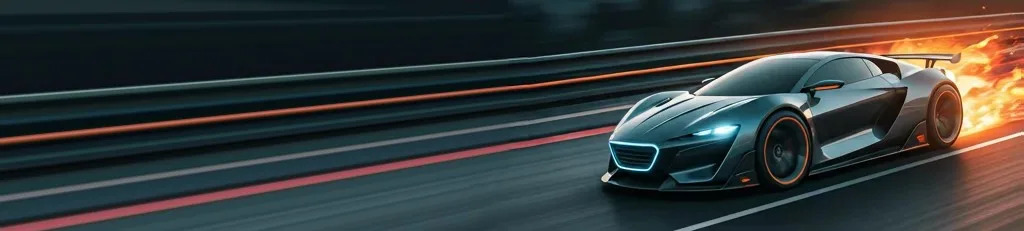
Automotive Parts Group Summary
1. Engine Accessories: Lightweight and precision-critical parts
Throttle body, fuel pump, fuel nozzle, tensioner, cylinder block, bearing bush, water pump, fuel injection, gasket, camshaft, valve plate, crankshaft, connecting rod assembly, piston, carburetor, fuel tank, water tank, fan, radiator, Pistons
2. Powertrain Accessories
- Precision gears and shafts: Gears, intermediate shaft, drive shaft assembly, drive shaft flange, synchronizer ring.
- Brake System Accessories: Brake disc, brake drum, brake master cylinder, brake cylinder.
- Steering System Accessories: Steering gear, steering knuckle, power pump.
- Suspension and Axle Accessories: Rear axle, half axle, balance weight.
- Electrical and Instrumentation Accessories: Precision and heat-dissipation-critical parts ( Ignition module, ignition coil, alternator housing )
- Automotive Lighting and Exterior Parts: Headlight housing, decoder housing, decorative automotive exterior parts.
- Body and Safety Components: Wiper housing, airbag casing, instrument panel housing.
- Maintenance Equipment and Others: Precision equipment casings and tool housings.
- Complex structural components:Transfer case, clutch disc, flange, planetary gear, wheel carrier.
![]() | ![]() RHT folding levers |
Automotive Parts Advantages:
High-pressure aluminum die casting has revolutionized the production of automotive parts, offering numerous advantages such as lightweighting, high strength, and the ability to create complex shapes.
![]() Rear connector sill frame member |
1. Weight Reduction (Lightweighting):
One of the core challenges in the automotive industry is reducing vehicle weight to improve fuel efficiency and lower emissions. Aluminum is a lightweight material, approximately one-third the weight of steel, while still maintaining excellent strength. Producing aluminum parts through high-pressure die casting significantly reduces the overall vehicle weight, leading to improved fuel economy, acceleration performance, and handling. Lightweighting is even more critical for electric vehicles (EVs) as it directly impacts battery efficiency and driving range.
2. High Strength and Durability:
High-pressure die casting involves injecting molten aluminum into a mold under high pressure. This process results in a dense metal structure with minimized porosity, leading to parts with high strength and durability. Aluminum also exhibits excellent corrosion resistance, reducing the likelihood of part damage due to rust. These characteristics make high-pressure aluminum die-cast parts suitable for components subjected to high loads and stress, such as engine blocks, transmission housings, and chassis components.
3. Complex Shape Capability:
High-pressure die casting is highly effective for mass-producing parts with complex and precise shapes. If the mold's precision is ensured, parts with intricate internal structures, curves, and thin walls can be produced with high accuracy. This allows for the integration of multiple parts into a single die-cast component, simplifying assembly processes and reducing production costs. It also increases design freedom, allowing for complex shapes that improve aerodynamic performance or differentiate designs.
4. High Productivity and Cost-Effectiveness:
High-pressure die casting is a very rapid production process. Large quantities of parts can be produced in a short time, making it suitable for mass production and leading to cost reductions. The use of precise molds minimizes the need for post-machining, further reducing additional processing costs. This cost-effectiveness makes high-pressure aluminum die casting widely used in the automotive industry.
5. Precise Dimensions and Excellent Surface Finish:
Because high-pressure die casting uses high-precision molds to form parts, dimensional accuracy is very high. Additionally, the molten aluminum conforms closely to the mold surface during solidification, resulting in parts with an excellent surface finish. This helps reduce the need for additional surface treatment processes, further lowering production costs.
6. Wide Range of Applications:
High-pressure aluminum die casting can be applied to produce various automotive parts. Typical examples include engine blocks, cylinder heads, transmission housings, oil pans, pump housings, chassis components, and structural parts. Recently, high-pressure aluminum die casting has also been actively applied to battery cases and motor housings for electric vehicles.
7. Thin-Wall Casting:
The high pressure used in this process allows for the creation of thin-walled castings, which further contributes to weight reduction without sacrificing structural integrity. This is particularly important for body and structural components where minimizing weight is crucial.
8. Integration and Consolidation:
As mentioned earlier, high-pressure die casting enables the integration of multiple parts into a single casting. This reduces the number of individual components, fasteners, and assembly operations, leading to cost savings, improved structural rigidity, and simplified logistics.
9. Recyclability:
Aluminum is a highly recyclable material, making high-pressure aluminum die casting a more sustainable manufacturing process. Recycled aluminum can be used to produce new parts, reducing the demand for primary aluminum production and its associated environmental impact.
10. Tight Tolerances and Repeatability:
The process offers excellent repeatability, ensuring consistent part quality and tight tolerances. This is crucial for automotive applications where precise fit and function are essential.
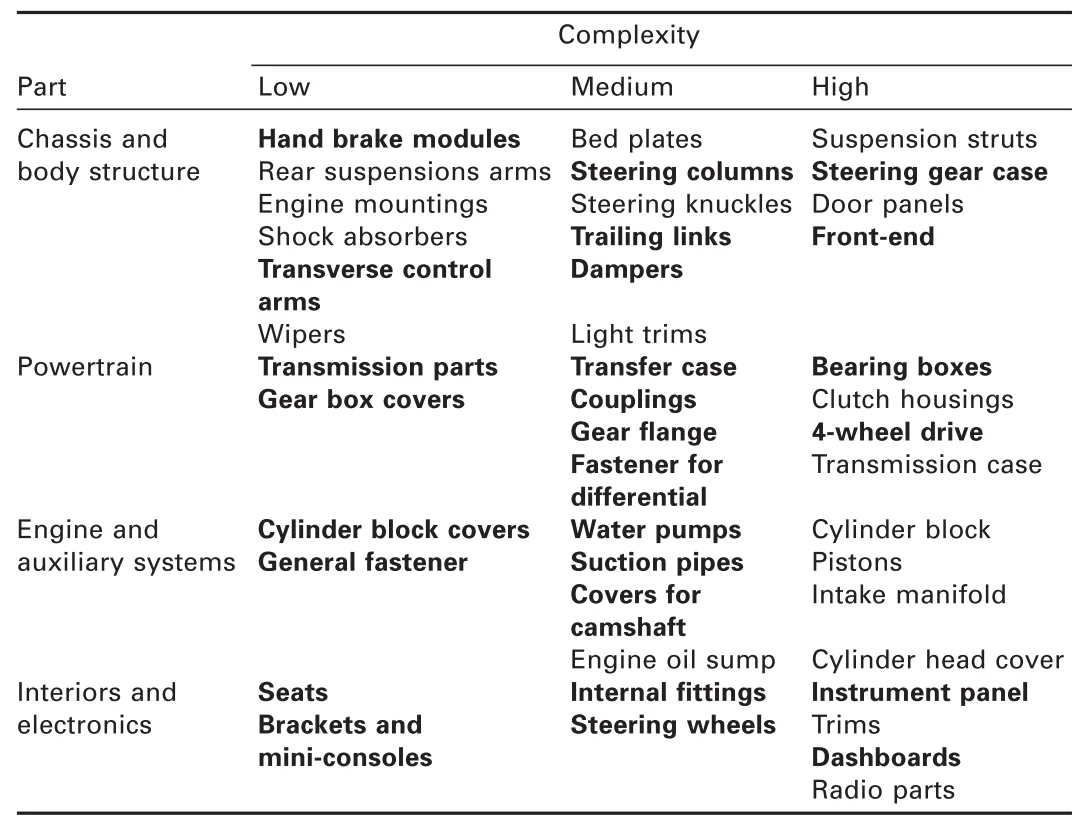
HPDC Automotive Parts Lists Examples:
Transmission Related:
![]() Engine mounting | ![]() |
![]() Integral crossbeam | ![]() Suspension strut bracket for SUVs |
Body Related:
![]() Door frame | ![]() High-pressure die-casting nodes of the A-pillar |
![]() Gearbox crossbeams | ![]() Inner door panels |
![]() Rear lid frames | ![]() Side door panel |
![]() | ![]() Steering wheel from "6 - High-pressure die-cast (HPDC) aluminium alloys for automotive applications" |
![]() | ![]() Hinge and latch door panels |
Technical Resource For Automotive
Unlocking Superior Vibration Damping: How Stress Enhances the Performance of CuZnAl Shape Memory Alloys
Beyond Poppet Valves: How Rotary Valve Engines Deliver Unmatched Power and Multi-Fuel Capability
Mastering Thermal Dynamics: The Core Technology for a High-Performance Future
STUDIES CONCERNING THE INFLUENCE OF THE HIGH PRESSURE DIE CASTING PROCESS PARAMETERS TO THE STRUCTURAL RESISTANCE OF PINION HOUSINGS
Surface Engineering and its Role in Preventing Early Failures
From Melt to Machining: A Detailed Guide to HPDC Bracket Production
Systematic approach for automated determination of parting line for die-cast parts
Unlocking Hidden Strength: How Novel Heat Treatments Transform HPDC Aluminum Alloys
Unlocking Performance: A Deep Dive into Modern Structural Die Casting Alloys
Contact Us
Please feel free to contact us for product production. We can help.
Tel : +82-31-351-5022
Fax: +82-31-351-5033
E-mail : sales@castman.co.kr