This article introduces the paper "A novel automated heat-pipe cooling device for high-power LEDs".
1. Overview:
- Title: A novel automated heat-pipe cooling device for high-power LEDs
- Authors: Chengdi Xiao, Hailong Liao, Yan Wang, Junhui Li, Wenhui Zhu
- Year: 2016
- Journal/Conference: Applied Thermal Engineering
- Keywords: High-power LEDs, Heat pipe, Automatic cooling system, Numerical simulation
2. Research Background:
High-power LEDs are increasingly popular in various applications, offering advantages like long lifespan, high reliability, low energy consumption, fast response time, and color variability. However, their efficiency (15-25% power-to-light conversion) is limited, with over 80% of power dissipated as heat, leading to high junction temperatures. Maintaining junction temperatures below 120°C is crucial for performance and longevity. The challenge intensifies with higher-power LEDs (e.g., >3000 lm/lamp), where thermal management becomes a critical issue for mass production and widespread use. Existing cooling systems (active, passive, hybrid) have limitations, including insufficient cooling efficiency in passive systems and the risk of complete system failure if an active system’s fan malfunctions. A reliable, efficient, self-regulating or automatically controlled heat pipe radiator is needed.
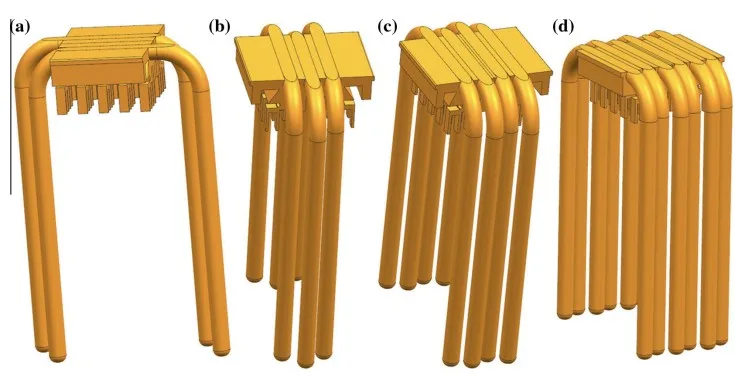
3. Research Objectives and Questions:
- Objective: To develop and evaluate a novel automated heat-pipe cooling device for high-power LEDs.
- Key Research Question: Can an automated cooling device integrating a microcontroller, heat pipes, and a fan effectively control substrate temperature, maintain suitable LED junction temperature, and improve LED performance and lifespan?
- Hypothesis: The automated cooling device will automatically control high-power LED substrate temperature, offer safe protection, and maintain the LED junction temperature within an acceptable range.
4. Research Methodology:
- Research Design: Experimental and numerical simulation-based approach.
- Data Collection: An automated cooling device (microcontroller, PWM fan, heat pipes, cooling fins) was built and tested with high-power LED modules. K-type thermocouples measured LED substrate and ambient temperatures. A numerical model of the cooling system was created using ANSYS Icepak 14.5 software and validated against experimental data.
- Analysis Methods: Experimental data assessed temperature control, reliability, and thermal performance. The numerical model performed steady-state thermal performance analysis, examining the effects of heat pipes, cooling fins, and the heat plate. A PID control algorithm was implemented in the control system.
- Subjects and Scope: The study used four 3W high-power LED modules, varying the number of heat pipes, cooling fin designs, and heat sink types.
5. Main Research Results:
- Key Findings: The automated cooling device effectively controlled high-power LED substrate temperature, maintaining suitable junction temperatures. At 12W, Rsa (heat sink to ambient) was 0.373 °C/W, and Rja (LED chip to ambient) was 5.953 °C/W. The total power consumption was below 1.58W. Increasing the number of heat pipes and cooling fins improved heat transfer.
- Statistical/Qualitative Analysis: Experimental data closely matched numerical model predictions, validating the model. Analyses explored the thermal performance variations with different design parameters.
- Data Interpretation: Results evaluated the automated cooling system's performance and assessed the influence of design variables.
- Figures: The paper included figures illustrating the device design, control system, temperature curves under various conditions, finite element models, thermal performance with different heat pipe numbers and fin designs, and velocity profiles and particle traces illustrating airflow patterns.
6. Conclusions and Discussion:
The novel automated heat-pipe cooling device effectively manages high-power LED thermal dissipation, automatically controlling substrate temperature and maintaining suitable junction temperatures. Increasing the number of heat pipes and cooling fins enhances thermal performance. The numerical model accurately predicted experimental results. The system is highly reliable, energy-efficient, and exhibits excellent cooling performance. Limitations included the experimental setup and specific LED types used, warranting further investigation.
7. Future Research:
Future research should involve more extensive testing under diverse conditions (different LED types and real-world environments), optimization of the control algorithm and system design, and exploration of alternative heat pipe and fin configurations.
References
- [1] I. Takai, S. Ito, K. Yasutomi, K. Kagawa, M. Andoh, S. Kawahito, LED and CMOS image sensor based optical wireless communication system for automotive applications, IEEE Photonics J. 5 (5) (2013) 6801418–6801419.
- [2] D.F. Feezell, J.S. Speck, S.P. DenBaars, S. Nakamura, Semipolar InGaN/GaN lightemitting diodes for high-efficiency solid-state lighting, J. Display Technol. 9 (4) (2013) 190–198.
- [3] J. Cho, E.F. Schubert, J.K. Kim, Efficiency droop in light-emitting diodes: challenges and countermeasures, Laser Photonics Rev. 7 (3) (2013) 408–421.
- [4] C.C. Hsieh, Y.H. Li, C.C. Hung, Modular design of the LED vehicle projector headlamp system, Appl. Opt. 52 (21) (2013) 5221–5229.
- [5] K.S. Yang, C.H. Chung, M.T. Lee, S.B. Chiang, C.C. Wong, C.C. Wang, An experimental study on the heat dissipation of LED lighting module using metal/carbon foam, Int. Commun. Heat Mass Transfer 48 (2013) 73–79.
- [6] N. Narendran, Y. Gu, J.P. Freyssinier, H. Yu, L. Deng, Solid-state lighting: failure analysis of white LEDs, J. Cryst. Growth 268 (3–4) (2004) 449–456.
- [7] N. Narendran, Y. Gu, Life of LED-based white light sources, J. Display Technol. 1 (1) (2005) 167–171.
- [8] Y. Tang, X. Ding, B. Yu, Z. Li, B. Liu, A high power LED device with chips directly mounted on heat pipes, Appl. Therm. Eng. 66 (1–2) (2014) 632–639.
- [9] S.S. Hsieh, Y.F. Hsu, M.L. Wang, A microspray-based cooling system for high powered LEDs, Energy Convers. Manage. 78 (2014) 338–346.
- [10] S. Liu, J. Yang, Z. Gan, X. Luo, Structural optimization of a microjet based cooling system for high power LEDs, Int. J. Therm. Sci. 47 (8) (2008) 1086– 1095.
- [11] S.F. Sufian, Z.M. Fairuz, M. Zubair, M.Z. Abdullah, J.J. Mohamed, Thermal analysis of dual piezoelectric fans for cooling multi-LED packages, Microelectron. Reliab. 54 (8) (2014) 1534–1543.
- [12] J. Li, X.R. Zhang, C. Zhou, J.G. Zheng, D.S. Ge, W.H. Zhu, New applications of an automated system for high-power LEDs, IEEE-ASME Trans. Mechatron. 21 (2) (2016) 1035–1042.
- [13] J. Li, B. Ma, R. Wang, L. Han, Study on a cooling system based on thermoelectric cooler for thermal management of high-power LEDs, Microelectron. Reliab. 51 (12) (2011) 2210–2215.
- [14] Y. Deng, J. Liu, A liquid metal cooling system for the thermal management of high power LEDs, Int. Commun. Heat Mass Transfer 37 (7) (2010) 788–791.
- [15] Y. Lai, N. Cordero, F. Barthel, F. Tebbe, J. Kuhn, R. Apfelbeck, D. Würtenberger, Liquid cooling of bright LEDs for automotive applications, Appl. Therm. Eng. 29 (5) (2009) 1239–1244.
- [16] X.Y. Lu, T.C. Hua, Y.P. Wang, Thermal analysis of high power LED package with heat pipe heat sink, Microelectron. J. 42 (11) (2011) 1257–1262.
- [17] X.Y. Lu, T.C. Hua, M.J. Liu, Y.X. Cheng, Thermal analysis of loop heat pipe used for high-power LED, Thermochim. Acta 493 (1) (2009) 25–29.
- [18] J.C. Hsieh, H.J. Huang, S.C. Shen, Experimental study of microrectangular groove structure covered with multi mesh layers on performance of flat plate heat pipe for LED lighting module, Microelectron. Reliab. 52 (6) (2012) 1071– 1079.
- [19] L. Kim, J.H. Choi, S.H. Jang, M.W. Shin, Thermal analysis of LED array system with heat pipe, Thermochim. Acta 455 (1) (2007) 21–25.
- [20] P. Anithambigai, K. Dinash, D. Mutharasu, S. Shanmugan, C.K. Lim, Thermal analysis of power LED employing dual interface method and water flow as a cooling system, Thermochim. Acta 523 (1) (2011) 237–244.
- [21] K.S. Yang, T.Y. Yang, C.W. Tu, C.T. Yeh, M.T. Lee, A novel flat polymer heat pipe with thermal via for cooling electronic devices, Energy Convers. Manage. 100 (2015) 37–44.
- [22] S.H. Yu, K.S. Lee, S.J. Yook, Optimum design of a radial heat sink under natural convection, Int. J. Heat Mass Transf. 54 (11–12) (2011) 2499–2505.
- [23] T.J. Lu, Thermal management of high power electronics with phase change cooling, Int. J. Heat Mass Transf. 43 (13) (2000) 2245–2256.
- [24] X. Luo, W. Xiong, T. Cheng, S. Liu, Temperature estimation of high-power light emitting diode street lamp by a multi-chip analytical solution, IET Optoelectron. 3 (5) (2009) 225–232.
- [25] J.C. Wang, Thermal investigations on LED vapor chamber-based plates, Int. Commun. Heat Mass Transfer 38 (9) (2011) 1206–1212.
- [26] R. Baby, C. Balaji, Thermal management of electronics using phase change material based pin fin heat sinks, in: 6th European Thermal Sciences Conference (Eurotherm 2012), vol. 395, no. 1, 2012, pp. 012134.
- [27] J. Li, F. Lin, D.M. Wang, W.K. Tian, A loop-heat-pipe heat sink with parallel condensers for high-power integrated LED chips, Appl. Therm. Eng. 56 (1-2) (2013) 18–26.
- [28] Y.H. Ye, L.H. Saw, Y.X. Shi, A.A.O. Tay, Numerical analyses on optimizing a heat pipe thermal management system for lithium-ion batteries during fast charging, Appl. Therm. Eng. 86 (2015) 281–291.
- [29] D. Jang, S.J. Park, S.J. Yook, K.S. Lee, The orientation effect for cylindrical heat sinks with application to LED light bulbs, Int. J. Heat Mass Transf. 71 (2014) 496–502.
- [30] H.B. Ma, C. Wilson, B. Borgmeyer, K. Park, Q. Yu, S.U.S. Choi, Murli. Tirumala, Effect of nanofluid on the heat transport capability in an oscillating heat pipe, Appl. Phys. Lett. 88 (14) (2006) 143116.
- [31] D. Lee, S.W. Cho, Y.J. Kim, Numerical study on the heat dissipation characteristics of high-power LED module, Sci. China Technol. Sci. 56 (9) (2013) 2150–2155.
- [32] X.C. Liu, Y.M. Xiao, K. Inthavong, J.Y. Tu, Experimental and numerical investigation on a new type of heat exchanger in ground source heat pump system, Energ. Effi. 8 (5) (2015) 845–857.
- [33] C. Xiao, Q. Tian, C. Zhou, J. Li, W. Zhu, A novel cooling system based on heat pipe with fan for thermal management of high-power LEDs, J. Opt. (2016) 1–8, online.
- [34] Y. Nishikawa, N. Sannomiya, T. Ohta, H. Tanaka, A method for auto-tuning of PID control parameters, Automatica 20 (3) (1984) 321–332.
- [35] H.M. Qu, X.H. Yang, Q. Zheng, X.T. Wang, Q. Chen, Thermal management technology of high-power light-emitting diodes for automotive headlights, IEICE Electr. Exp. 11 (23) (2014) 1–11.
- [36] Y.S. Chen, K.H. Chien, Y.S. Tseng, Y.K. Chan, Determination of optimized rectangular spreader thickness for lower thermal spreading resistance, J. Electron. Packag. 131 (1) (2009) 011004-1–011004-8.
Copyright:
This summary is based on the paper "A novel automated heat-pipe cooling device for high-power LEDs" by Chengdi Xiao et al.
http://dx.doi.org/10.1016/j.applthermaleng.2016.10.041
Copyright © 2023 CASTMAN. All rights reserved.