This paper summary is based on the article "A Novel Approach to Visualize Liquid Aluminum Flow to Advance Casting Science" presented at the "MDPI Materials"
1. Overview:
- Title: A Novel Approach to Visualize Liquid Aluminum Flow to Advance Casting Science
- Authors: Casey Bate, Philip King, Jay Sim and Guha Manogharan
- Publication Year: 2023
- Publishing Journal/Academic Society: Materials (MDPI)
- Keywords: mold filling; sand-casting; succinonitrile; casting hydrodynamics; water modeling; metal analog; flow simulation
![Figure 1. Casting geometry based on prior experimental study [17], units in mm](https://castman.co.kr/wp-content/uploads/image-361-png.webp)
2. Research Background:
Social/Academic Context of the Research Topic:
In sand-casting, turbulent filling of molten metal is a well-known precursor to casting defects such as bi-films, porosity, and oxide inclusions. These defects detrimentally affect mechanical properties and increase scrap rates. Therefore, understanding and controlling metal flow, or casting hydrodynamics, within sand molds is paramount for defect minimization. While numerical simulation methods have been extensively applied to model this phenomenon, experimental validation has been hindered by the harsh conditions of foundry environments and the limitations of expensive X-ray equipment.
Limitations of Existing Research:
Traditional experimental approaches for visualizing metal flow in sand molds face significant challenges. The opaque nature of sand molds, coupled with harsh foundry conditions (high temperature, outgassing, abrasive sand, humidity), restricts direct observation and data acquisition. Prior studies utilizing X-ray equipment for flow visualization are limited to qualitative data and constrained by feasible geometries, high costs, safety concerns, and 2D imaging limitations, which fail to capture complex 3D flow phenomena like vortexes. Water modeling has been used as a cost-effective analog, but its differing thermal-fluid properties and lack of solidification at room temperature raise concerns about its accuracy in representing molten metal behavior.
Necessity of the Research:
To advance casting science and minimize defects, there is a critical need for improved experimental techniques to accurately visualize and analyze liquid metal flow in sand molds. This research addresses the gap by proposing and validating a novel approach using an alternative metal analog material that can be tested under less restrictive conditions and provide more representative flow visualization compared to water.
3. Research Purpose and Research Questions:
Research Purpose:
The primary research purpose is to evaluate the suitability of Succinonitrile (SCN) as a more accurate analog to water for visualizing liquid metal flow, specifically molten aluminum, in sand casting experiments. The study aims to determine if SCN, with its unique properties, can effectively mimic the flow behavior of molten metal.
Key Research Questions:
- Can Succinonitrile (SCN) serve as a more accurate metal analog compared to water for visualizing liquid aluminum flow in casting processes?
- What are the critical dimensionless numbers that must be considered to achieve accurate metal flow analog testing using SCN?
- How does SCN flow behavior compare to both water and molten aluminum flow under similar casting conditions, both experimentally and through numerical simulation?
Research Hypotheses:
The research hypothesizes that Succinonitrile (SCN) is a superior metal analog to water due to its Body-Centered-Cubic (BCC) crystal structure and dendrite-like solidification, similar to molten aluminum, and its manageable melting temperature (~60 °C). The study further posits that Froude number and wall roughness are critical dimensionless variables for achieving accurate metal flow analogy in casting experiments.
4. Research Methodology
Research Design:
This research employed a mixed-methods approach, combining experimental investigations with numerical simulations to analyze liquid flow behavior.
Data Collection Method:
Experiments were conducted using both water and SCN as working fluids in transparent acrylic molds, replicating a benchmark sand casting geometry from a prior study [17] (Figure 1). Flow visualization was achieved through high-speed video recording at 300 fps, with green food dye added to SCN for enhanced visibility. Numerical simulations were performed using Flow3D Cast software to model the flow of aluminum, water, and SCN under comparable conditions.
Analysis Method:
The study compared the flow profiles of water, SCN, and simulated aluminum both qualitatively through visual analysis of flow patterns and quantitatively by measuring mold filling times and average velocities in the sprue and runner. Dimensionless numbers, specifically Froude number, Reynolds number, and Weber number, were calculated and analyzed to determine their influence on flow similarity between the different fluids. The experimental results were also compared to the numerical simulation outcomes and benchmark X-ray experimental data of aluminum flow [17].
Research Subjects and Scope:
The research focused on liquid flow behavior in a simplified bottom-gated sand casting geometry designed for casting a benchmark aluminum plate (10 mm × 200 mm × 100 mm) [17]. The study used water and SCN as analog fluids and targeted molten aluminum flow as the reference for comparison. The scope was limited to the mold filling stage, with solidification aspects considered primarily in the context of selecting SCN as an analog material.
5. Main Research Results:
Key Research Results:
The experimental results demonstrated that SCN flow testing more accurately replicated the flow profile of molten aluminum compared to water modeling. Specifically, "experimental results show that SCN flow testing was more accurate in recreating the flow profile of molten aluminum, thus validating its utility as a metal analog for metal flow research." The study identified Froude number and wall roughness as critical dimensionless variables for achieving accurate metal flow analogy.
Statistical/Qualitative Analysis Results:
Qualitative comparisons of flow patterns (Figure 7, Figure 8, Figure 9, Figure 11, Figure 12, Figure 13, Figure 14) visually demonstrated that SCN flow more closely resembled the aluminum flow from prior X-ray studies [17] than water flow. Quantitative analysis (Table 9, Table 10, Table 11) showed that while matching Reynolds number for water resulted in similar fill times, the flow behavior was still less representative of aluminum compared to SCN. The higher Froude number tests exhibited higher velocities and shorter fill times (Table 9).
Data Interpretation:
The findings suggest that while Reynolds number similarity in water modeling can provide some resemblance in fill times, it does not guarantee accurate representation of molten metal flow patterns. Froude number similarity appears to be more critical for capturing the overall flow dynamics. SCN, even with a lower Reynolds number (6800 for SCN vs. 28,000 for aluminum), exhibited flow patterns that were qualitatively more similar to molten aluminum than water, indicating the importance of material properties beyond just dimensionless number matching. The study also highlighted the potential influence of wall roughness and pressure drop on flow similarity, as indicated by the Moody diagram analysis (Figure 15).
Figure Name List:
- Figure 1. Casting geometry based on prior experimental study [17], units in mm.
- Figure 2. Filling images from [17] study.
- Figure 3. CAD design of mold parts.
- Figure 4. Example of assembled acrylic mold (from earlier test).
- Figure 5. Simulation results of SCN, aluminum, and water at (a) 0.7s (b) 0.9 s (c) 1 s (d) 1.2 s.
- Figure 6. Expected aluminum flow conditions.
- Figure 7. Water testing results for Fr unmatched (left) vs. Fr matched (right) (a) 0.5 s after pulling plug, (b) 0.74 s (c) 1 s, (d) 1.24 s.
- Figure 8. Water testing results for Re unmatched (left) vs. Re matched (right) (a) 0.5 s after pulling plug, (b) 0.74 s (c) 1 s, (d) 1.24 s.
- Figure 9. Succinonitrile testing results (a) 0.5 s after pulling plug, (b) 0.74 s (c) 1 s, (d) 1.24 s.
- Figure 10. Water (left) and SCN (right) in SLA printed channel.
- Figure 11. Aluminum in sand mold (left [17]), aluminum in sand mold simulation (middle) and matched SCN visualization (right).
- Figure 12. Aluminum in sand mold (left), Water in sand mold simulation (left middle), unmatched Froude's number water in acrylic (right middle), Matched Froude's number water in acrylic (right).
- Figure 13. Aluminum in sand mold (left), Water in sand mold simulation (left middle), Unmatched Reynold's number water in acrylic (right middle), Matched Reynold's number water in acrylic (right).
- Figure 14. Aluminum in sand mold (left), Succinonitrile in sand mold simulation (middle), Succinonitrile in acrylic (right).
- Figure 15. Moody diagram 61 Water Re ≈ >28,000 in acrylic (2) SCN Re ≈ 6800 in acrylic (3) Relative roughness of substance at Re ≈ 28,000 correlated to pressure drop incurred by SCN.
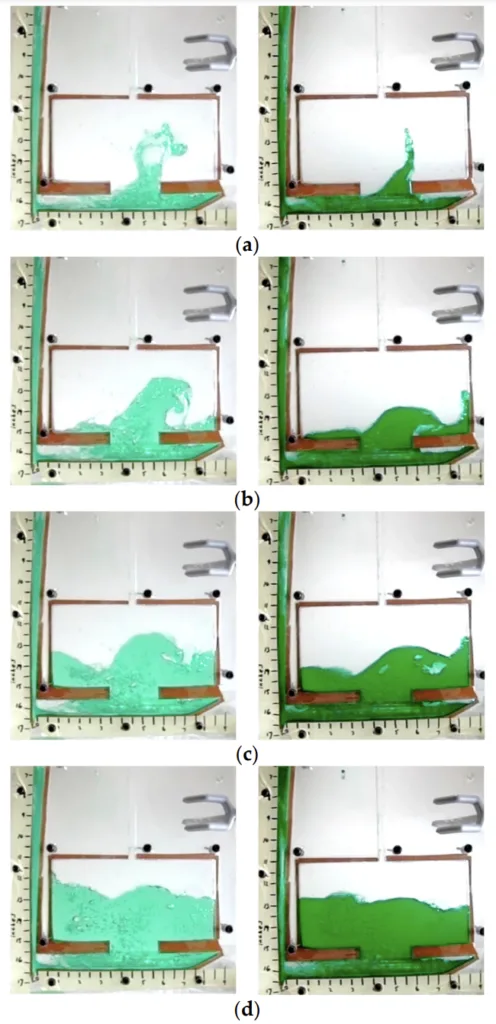
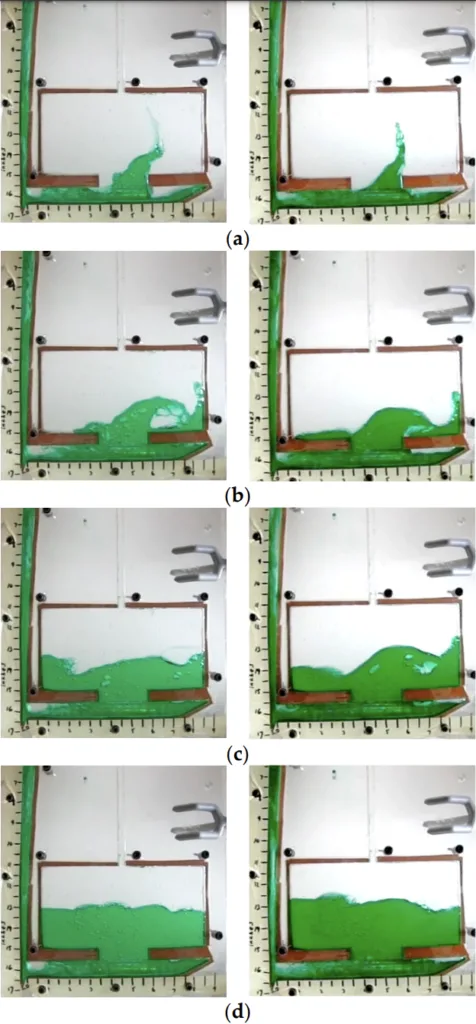
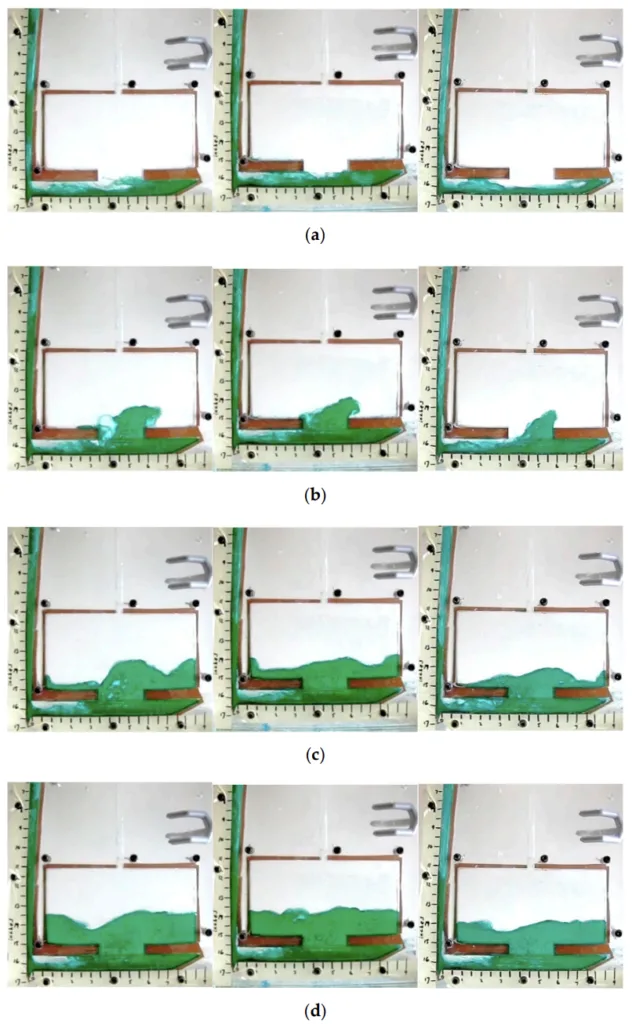
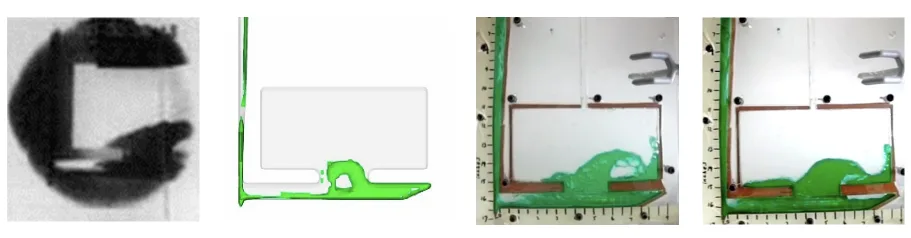
6. Conclusion and Discussion:
Summary of Main Results:
This study concludes that Succinonitrile (SCN) is a more effective metal analog than water for visualizing liquid aluminum flow in sand casting experiments. "Experimental results show that SCN flow testing was more accurate in recreating the flow profile of molten aluminum, thus validating its utility as a metal analog for metal flow research." While water modeling can offer a simplified representation, SCN, with its closer material property similarities to molten metals, provides a more accurate qualitative and potentially quantitative representation of flow behavior. The research emphasizes the importance of Froude number similarity in analog testing and suggests that wall roughness and pressure drop are significant factors influencing flow similarity, potentially more so than strict Reynolds number matching.
Academic Significance of the Research:
This research is the first reported study to apply SCN through novel casting hydrodynamics experiments to accurately visualize melt flow for casting studies. It contributes to the fundamental understanding of metal flow visualization techniques and validates the use of SCN as a valuable tool for casting research. The findings challenge the over-reliance on water modeling and Reynolds number similarity, highlighting the need to consider other dimensionless numbers and material properties for accurate analog testing.
Practical Implications:
The successful application of SCN as a metal analog opens new avenues for experimental investigation of casting hydrodynamics in a laboratory setting, reducing the reliance on expensive and complex foundry experiments or X-ray facilities. "Findings from this study can be used in future metal flow analysis such as: runner, in-gate and integrated filling-feeding-solidification studies." This approach can facilitate the design and validation of innovative gating systems, particularly for complex geometries enabled by additive manufacturing, and contribute to the development of more accurate numerical models for integrated flow-solidification simulations. The methodology detailed in this paper also provides "a roadmap for validation of innovative gating geometries."
Limitations of the Research:
The study acknowledges limitations, including the use of acrylic molds, which have different thermal characteristics and surface roughness compared to sand molds. "The limited thermal capacity of acrylic molds prohibited pouring SCN at higher temperatures which could lead to severe cracking of the mold and alternative material to acrylic is a focus of future studies." Furthermore, the study primarily focused on flow visualization and did not fully explore the combined effects of flow conditions and resulting solidification behavior.
7. Future Follow-up Research:
Directions for Follow-up Research:
Future research should explore alternative transparent mold materials with improved thermal capacity and controllable surface roughness to better mimic sand mold conditions. Further investigation into the combined effects of flow and solidification using SCN is warranted to fully leverage its potential as a metal analog. "In addition, future work should explore analogous to liquid metal that forms oxides on the surface to more accurately emulate oxide bifilms that occur commonly in melt flow."
Areas Requiring Further Exploration:
Areas requiring further exploration include:
- Investigating advanced transparent materials with tailored thermal and surface properties.
- Studying the solidification behavior of SCN under casting conditions and its correlation with metal solidification.
- Developing methods to incorporate surface oxide formation in SCN experiments to better represent molten metal behavior.
- Integrating capacitive or other sensors into SCN-based experiments for quantitative, real-time velocity measurements within the mold. "Finally, incorporating capacitive sensors into the mold may provide a reference for detailed velocity of metal flow in traditional sand molds [62]."
8. References:
- EPA Metal Casting 2016. Available online: https://archive.epa.gov/sectors/web/html/casting.html (accessed on 7 December 2022).
- Shinde, V.D.; Mhamane, D.A. Evaluation of Sand Quality in Thermal Sand Reclamation System. Therm. Sci. Eng. 2018, 2, 538.
[CrossRef] - Campbell, J. Entrainment Defects. Mater. Sci. Technol. 2006, 22, 127–145. [CrossRef]
- Cross, M.; McBride, D.; Croft, T.N.; Williams, A.J.; Pericleous, K.; Lawrence, J.A. Computational Modeling of Mold Filling and
Related Free-Surface Flows in Shape Casting: An Overview of the Challenges Involved. Metall. Mater. Trans. B 2006, 37, 879–885.
[CrossRef] - Mi, J.; Harding, R.A.; Campbell, J. Effects of the Entrained Surface Film on the Reliability of Castings. Metall. Mater. Trans. A 2004,
35, 2893–2902. [CrossRef] - Campbell, J. Complete Casting Handbook, 1st ed.; Elsevier: Amsterdam, The Netherlands, 2015; ISBN 9780444635099.
- Dai, X.; Yang, X.; Campbell, J.; Wood, J. Effects of Runner System Design on the Mechanical Strength of Al-7Si-Mg Alloy Castings.
Mater. Sci. Eng. A 2003, 354, 315–325. [CrossRef] - Tiryakio ˘glu, M.; Campbell, J.; Alexopoulos, N.D. Quality Indices for Aluminum Alloy Castings: A Critical Review. Metall. Mater.
Trans. B 2009, 40, 802–811. [CrossRef] - Sama, S.R.; Wang, J.; Manogharan, G. Non-Conventional Mold Design for Metal Casting Using 3D Sand-Printing. J. Manuf.
Process. 2018, 34, 765–775. [CrossRef] - Sama, S.R.; Badamo, T.; Lynch, P.; Manogharan, G. Novel Sprue Designs in Metal Casting via 3D Sand-Printing. Addit. Manuf.
2019, 25, 563–578. [CrossRef] - Cleary, P.W.; Ha, J. Three-Dimensional Smoothed Particle Hydrodynamics Simulation of High Pressure Die Casting of Light
Metal Components. J. Light Met. 2002, 2, 169–183. [CrossRef] - Kermanpur, A.; Mahmoudi, S.; Hajipour, A. Numerical Simulation of Metal Flow and Solidification in the Multi-Cavity Casting
Moulds of Automotive Components. J. Mater. Process. Technol. 2008, 206, 62–68. [CrossRef] - Renukananda, K.H.; Ravi, B. Multi-Gate Systems in Casting Process: Comparative Study of Liquid Metal and Water Flow. Mater.
Manuf. Process. 2016, 31, 1091–1101. [CrossRef] - Sutaria, M.; Ravi, B. Computation of Casting Solidification Feed-Paths Using Gradient Vector Method with Various Boundary
Conditions. Int. J. Adv. Manuf. Technol. 2014, 75, 209–223. [CrossRef] - Sutaria, M.; Gada, V.H.; Sharma, A.; Ravi, B. Computation of Feed-Paths for Casting Solidification Using Level-Set-Method. J.
Mater. Process. Technol. 2012, 212, 1236–1249. [CrossRef] - Lee, P.; Chirazi, A.; See, D. Modeling Microporosity in Aluminum–Silicon Alloys: A Review. J. Light Met. 2001, 1, 15–30. [CrossRef]
- Sirrell, B.; Holliday, M.; Campbell, J. Benchmark Testing the Flow and Solidification Modeling of Al Castings. JOM 1996, 48, 20–23.
[CrossRef] - Kashiwai, S.; Ohnaka, I.; Kimatsuka, A.; Kaneyoshi, T.; Ohmichi, T.; Zhu, J. Numerical Simulation and X-Ray Direct Observation
of Mould Filling during Vacuum Suction Casting. Int. J. Cast Met. Res. 2005, 18, 144–148. [CrossRef] - Di Sabatino, M.; Syvertsen, F.; Arnberg, L.; Nordmark, A. An Improved Method for Fluidity Measurement by Gravity Casting of
Spirals in Sand Moulds. Int. J. Cast Met. Res. 2005, 18, 59–62. [CrossRef] - Sulaiman, S.; Hamouda, A.M.S. Modelling and Experimental Investigation of Solidification Process in Sand Casting. J. Mater.
Process. Technol. 2004, 155–156, 1723–1726. [CrossRef] - Johnson, W.H.; Bishop, H.F.; Pellini, W.S. Gating Factors. Foundry 1954, 102–272.
- Richins, D.S.; Wetmore, W.O. Fluid Mechanics Applied to Founding. AFS Trans. 1951, 1–24.
- Skov-Hansen, S.; Green, N.R.; Tiedje, N.S. Experimental Analysis of Flow of Ductile Cast Iron in Stream Lined Gating Systems.
Giessereiforschung. 2009, 60. - Tiedje, N. Flow through Bends in Gating Systems in Vertically Parted Moulds. AFS Trans. 1999, 581–590.
- Tiedje, N.S.; Larsen, P. Investigation of the Stability of Melt Flow in Gating Systems. Metall. Mater. Trans. B Process Metall. Mater.
Process. Sci. 2011, 42, 189–201. [CrossRef] - Cao, H.; Shen, C.; Wang, C.; Xu, H.; Zhu, J. Direct Observation of Filling Process and Porosity Prediction in High Pressure Die
Casting. Materials 2019, 12, 1099. [CrossRef] [PubMed] - Thomas, B.G.; Mika, L.J.; Najjar, F.M. Simulation of Fluid Flow inside a Continuous Slab-Casting Machine. Metall. Trans. B 1990,
21, 387–400. [CrossRef] - Thomas, B.G.; Najjar, F.M. Finite Element Modelling of Turbulent Fluid Flow and Heat Transfer in Continuous Casting. Appl.
Math. Model. 1991, 15, 226–243. [CrossRef] - Sahai, Y.; Emi, T. Criteria for Water Modeling of Melt Flow and Inclusion Removal in Continuous Casting Tundishes. ISIJ Int.
1996, 36, 1166–1173. [CrossRef] - Kuyucak, S. Sponsored Research: Clean Steel Casting Production—Water Modeling Studies of Bottom-Pouring Ladle Operations.
Trans. Am. Foundry Soc. 2006, 114, 811–818. - Beckermann, C. Water Modeling of Steel Flow, Air Entrainment and Filtration. In Proceedings of the 46th SFSA Technical and
Operating Conference, Chicago, IL, USA, 4–7 November 1992; pp. 1–18. - Derollez, P.; Lefebvre, J.; Descamps, M.; Press, W.; Fontaine, H. Structure of Succinonitrile in Its Plastic Phase. J. Phys. Condens.
Matter 1990, 2, 6893–6903. [CrossRef] - Glicksman, M.E.; Schaefer, R.J.; Ayres, J.D. Dendritic Growth—A Test of Theory. Metall. Trans. A 1976, 7, 1747–1759. [CrossRef]
- Janz, G.J.; Fitzgerald, W.E. Infrared Spectrum and Molecular Structure of Succinonitrile. J. Chem. Phys. 1955, 23, 1973–1974.
[CrossRef] - Fitzgerald, W.E.; Janz, G.J. Vibrational Spectra and Molecular Structure of 1,2-Dicyanoethane. J. Mol. Spectrosc. 1957, 1, 49–60.
[CrossRef] - Weinberg, F.; Chalmers, B. Dendritic Growth in Lead. Can. J. Phys. 1951, 29, 382. [CrossRef]
- Weinberg, F.; Chalmers, B. Further Observations on Dendritic Growth in Metals. Can. J. Phys. 1952, 30, 488. [CrossRef]
- Chalmers, B. The Preparation of Single Crystals and Bicrystals by the Controlled Solidification of Molten Metals. Can. J. Phys.
1953, 31, 132. [CrossRef] - Huang, S.C.; Glicksman, M.E. Overview 12: Fundamentals of Dendritic Solidification-I. Steady-State Tip Growth. Acta Metall.
1981, 29, 701–715. [CrossRef] - Teng, J.; Liu, S. Re-Determination of Succinonitrile (SCN)–Camphor Phase Diagram. J. Cryst. Growth 2006, 290, 248–257. [CrossRef]
- Shang, S.; Han, Z.; Luo, A.A. Study on the Response of Dendritic Growth to Periodic Increase–Decrease Pressure in Solidification
via in Situ Observation Using Succinonitrile. J. Cryst. Growth 2018, 498, 85–92. [CrossRef] - Losert, W.; Shi, B.Q.; Cummins, H.Z. Evolution of Dendritic Patterns during Alloy Solidification: From the Initial Instability to the
Steady State. Proc. Natl. Acad. Sci. USA 1998, 95, 439–442. [CrossRef] - Karma, A.; Lee, Y.H.; Plapp, M. Three-Dimensional Dendrite-Tip Morphology at Low Undercooling. Phys. Rev. E 2000, 61,
3996–4006. [CrossRef] - Jeong, J.-H.; Dantzig, J.A.; Goldenfeld, N. Dendritic Growth with Fluid Flow in Pure Materials. Metall. Mater. Trans. A 2003, 34,
459–466. [CrossRef] - Trivedi, R.; Shen, Y.; Liu, S. Cellular-to-Dendritic Transition during the Directional Solidification of Binary Alloys. Metall. Mater.
Trans. A 2003, 34, 395–401. [CrossRef] - Chopra, M.A.; Glicksman, M.E.; Singh, N.B. Dendritic Solidification in Binary Alloys. Metall. Trans. A Phys. Metall. Mater. Sci.
1988, 19, 3087–3096. [CrossRef] - Shen, H.F.; Beckermann, C. An Experimental Study of Deformation of a Columnar Dendritic Mushy Zone Using a Transparent
Succinonitrile-Acetone Alloy. Metall. Mater. Trans. B Process Metall. Mater. Process. Sci. 2002, 33, 69–78. [CrossRef] - Esaka, H.; Wakabayashi, T.; Shinozuka, K.; Tamura, M. Origin of Equiaxed Grains and Their Motion in the Liquid Phase. ISIJ Int.
2003, 43, 1415–1420. [CrossRef] - Khalifa, W.; Tsunekawa, Y.; Okumiya, M. Ultrasonic Grain Refining Effects in A356 Al-Si Cast Alloy. AFS Trans. 2010, 91–98.
- Bryne, O. Performance Comparison of C-Si, Mc-Si and a-Si Thin Film PV by PVsyst Simulation. J. Optoelectron. Adv. Mater. 2013,
15, 326–334. [CrossRef] - Tin, P.; de Groh, H.C., III. Surface Tension and Viscosity of Succinonitrile—Acetone Alloys Using Surface Light Scattering
Spectrometer. Int. J. Thermophys. 2004, 25, 1143–1153. [CrossRef] - Ceynar, D.L.; Beckermann, C. Measurement of the Density of Succinonitrile—Acetone Alloys. J. Cryst. Growth 2001, 222, 380–391.
[CrossRef] - Petrakis, L.; Rao, A. Rotational Transition and Self-Diffusion in Polycrystalline Succinonitrile. J. Chem. Phys. 1963, 39, 1633–1635.
[CrossRef] - Sigma-Aldrich. Material Safety Data Sheet. 2018, pp. 1–8. Available online: https://www.sigmaaldrich.com/US/en/sds/
aldrich/160962 (accessed on 7 December 2022). - Hockaday, L.A. Rapid 3D Printing of Anatomically Accurate and Mechanically Heterogeneous Aortic Valve Hydrogel Scaffolds.
Int. Soc. Biofabr. 2012, 4, 035005. [CrossRef] [PubMed] - Morgan, A.J.L.; Hidalgo, L.; Jose, S.; Jamieson, W.D.; Wymant, M.; Song, B.; Stephens, P.; Barrow, D.A.; Castell, O.K. Simple and
Versatile 3D Printed Microfluidics Using Fused Filament Fabrication. PLoS ONE 2016, 11, e0152023. [CrossRef] [PubMed] - Cooper, D.E.; Stanford, M.; Kibble, K.A.; Gibbons, G.J. Additive Manufacturing for Product Improvement at Red Bull Technology.
J. Mater. 2012, 41, 226–230. [CrossRef] - Amili, O.; Schiavazzi, D.; Moen, S.; Jagadeesan, B. Hemodynamics in a Giant Intracranial Aneurysm Characterized by in Vitro 4D
Flow MRI. PLoS ONE 2018, 13, e0188323. [CrossRef] - Kinstlinger, I.S.; Miller, J.S.; Miller, J.S.; Miller, J.S. 3D-Printed Fluidic Networks as Vasculature for Engineered Tissue. Lab Chip
2016, 16, 2025–2043. [CrossRef] - Klein, J.; Stern, M.; Franchin, G.; Kayser, M.; Inamura, C.; Dave, S.; Weaver, J.C.; Houk, P.; Colombo, P.; Yang, M.; et al. Additive
Manufacturing of Optically Transparent Glass. 3D Print. Addit. Manuf. 2015, 2, 92–105. [CrossRef] - Munson, B.R.; Young, F.D.; Okiishi, T.H. Fundamentals of Fluid Mechanics; John Wiley & Sons: Hoboken, NJ, USA, 2006; ISBN
978-0-471-67582-2. - Sama, S.R.; MacDonald, E.; Voigt, R.; Manogharan, G. Manogharan Measurement of Metal Velocity in Sand Casting during Mold
Filling. Metals 2019, 9, 1079. [CrossRef]
Disclaimer/Publisher’s Note: The statements, opinions and data contained in all publications are solely those of the individual
author(s) and contributor(s) and not of MDPI and/or the editor(s). MDPI and/or the editor(s) disclaim responsibility for any injury to
people or property resulting from any ideas, methods, instructions or products referred to in the content.
9. Copyright:
This material is "[Casey Bate, Philip King, Jay Sim and Guha Manogharan]"'s paper: Based on "A Novel Approach to Visualize Liquid Aluminum Flow to Advance Casting Science".
Paper Source: https://doi.org/10.3390/ma16020756
This material was summarized based on the above paper, and unauthorized use for commercial purposes is prohibited.
Copyright © 2025 CASTMAN. All rights reserved.