This article introduces the paper "An Initial Study of a Lightweight Die Casting Die Using a Modular Design Approach," published in the International Journal of Metalcasting in 2018.
1. Overview:
- Title: AN INITIAL STUDY OF A LIGHTWEIGHT DIE CASTING DIE USING A MODULAR DESIGN APPROACH
- Authors: Sebastian Müller, Klaus Dilger, Anke Müller, Felix Rothe, and Klaus Dröder
- Publication Year: 2018
- Publishing Journal/Academic Society: International Journal of Metalcasting, Volume 12, Issue 4
- Keywords: die casting, process modeling, die deflections, lightweight design, modular concept, energy reduction
2. Research Background:
- Social/Academic Context of the Research Topic:
High-pressure die casting (HPDC) is a crucial industrial process, particularly dominant in the automotive sector, accounting for approximately 70% of German production. It is favored for producing geometrically complex components in high lot sizes. However, traditional HPDC die design and manufacturing are characterized by significant drawbacks. Die casting dies are typically custom-designed and manufactured subtractively for each component, lacking standardization. Design improvements have been evolutionary, driven by designer experience and numerical methods. The conventional approach involves massive die designs to ensure stability during the casting process. - Limitations of Existing Research:
Current die casting die technology faces several limitations:- High investment costs: Limit the process to high-quantity production runs.
- High energy consumption: Operation of large dies leads to substantial energy consumption and slow die temperature control.
- High total weight: Requires robust and heavy die casting machines and drive units.
- Energy-intensive production: Quenched and tempered tool steels result in a high CO₂ footprint.
- Material waste: Die casting dies, especially mold bases, are often scrapped after use, contributing to material waste.
- Time and material-intensive machining: Manufacturing forming frames from tool steel is a lengthy and costly process.
- Necessity of the Research:
The research is motivated by the need to overcome the limitations of conventional die casting die design and manufacturing. There is a clear necessity to:- Simplify the design and manufacturing process: Reduce the time and cost associated with creating die casting dies.
- Enable rapid implementation of product variants: Increase flexibility in casting production to meet the growing demand for individualized products.
- Improve energy efficiency: Reduce energy consumption during die preheating and operation.
- Reduce material consumption: Explore lightweight designs to minimize material usage and waste.
3. Research Purpose and Research Questions:
- Research Purpose:
The primary research purpose is to conduct an initial study on a lightweight die casting die using a modular design approach. This involves analyzing the fundamental thermal and structural properties of this novel die design to assess its feasibility and potential benefits. The ultimate goal is to pave the way for a more efficient and flexible die casting die design principle that reduces the time and cost of design and manufacturing. - Key Research Questions:
This research seeks to answer the following key questions:- How does the energy consumption of a modular lightweight die casting die compare to a conventional die casting die during preheating and operation?
- What are the deformation and stress characteristics of a modular lightweight die casting die during the casting process, and how do they compare to a conventional die?
- Can a modular lightweight design maintain sufficient structural integrity and dimensional accuracy under typical HPDC process loads?
- What are the potential advantages and challenges of implementing a modular lightweight die casting die design in terms of energy efficiency and structural performance?
- Research Hypotheses:
Based on the design principles of lightweight structures and modularity, the research operates under the following hypotheses:- A modular lightweight die casting die will exhibit significantly lower energy consumption for preheating and during operation compared to a conventional die due to its reduced mass and material.
- Due to the reduced stiffness and material in the lightweight design, calculated deformations and stresses in the die will be considerably higher during the casting process compared to a conventional die.
- Despite potentially higher deformations and stresses, the modular lightweight die casting die can be designed to maintain acceptable levels of dimensional accuracy and structural integrity for the HPDC process.
4. Research Methodology:
- Research Design:
The research employs a comparative study design using finite element analysis (FEA) to evaluate and compare the performance of a lightweight modular die casting die concept against a conventional die casting die. Both die designs were modeled for the same 4-mm plate HPDC component to ensure a direct comparison of their thermal and structural behaviors. - Data Collection Method:
Data was collected through numerical simulations performed using ANSYS software. The simulation model was built using:- CAD data: CAD models for both the lightweight modular die casting die and a conventional die casting die were created. CAD data for the fixed and moving platens of a BUEHLER SC B53 die casting machine were provided by the manufacturer.
- Boundary Conditions: Boundary conditions for both thermal and mechanical analyses were carefully defined based on real production process parameters and relevant literature. These conditions are detailed in Table 1 and Table 2 of the paper.
- Analysis Method:
A coupled transient thermal and structural analysis was conducted using the finite element method. This approach allows for the simultaneous simulation of heat transfer and structural mechanics, capturing the interactions between thermal loads and mechanical stresses during the die casting process. The analysis included:- Thermal Analysis: Transient thermal simulations were performed to analyze die temperature evolution, thermal output of cooling channels, and energy consumption during preheating and casting cycles.
- Structural Analysis: Static structural simulations were conducted to evaluate die deflections, wall thickness deviations, and equivalent von Mises stresses under various loading conditions, including mechanical loads (locking force, injection pressure) and thermal loads.
- Research Subjects and Scope:
The research focused on a specific HPDC component: a 4-mm thick plate. This geometry was chosen because:- It allows for a straightforward deformation analysis.
- Its performance can be compared to a real die casting die.
- The cavity is located only in the moving die half, simplifying the design and analysis.
- It represents a critical application due to the concentrated load in the die center.
5. Main Research Results:
- Key Research Results:
The finite element calculations revealed several key findings:- Energy Reduction: The modular lightweight die casting die consumed considerably less energy for preheating and during operation compared to the conventional die. The total energy demand was reduced by a factor of approximately 5.2, regardless of the casting lot size (Figure 5). For preheating to an average cavity temperature of 200°C, the lightweight die required 4.2 MJ of heat, while the conventional die required 17.3 MJ (Figure 3).
- Deformations: Calculated deformations in the lightweight die were higher than in the conventional die when subjected to loads at room temperature (Figure 6). However, the difference in maximum wall thickness deviation was relatively small, around 0.05 mm. At operating temperature, the deviation between both designs remained approximately 0.05 mm in the center of the plate (Figure 7). Interestingly, under combined thermal and mechanical loads (setup #III), the lightweight design exhibited less deviation in wall thickness compared to the conventional design (Figure 8).
- Stresses: Equivalent von Mises stress analysis showed high stress concentrations at the notches of the lightweight load-bearing metal structural element, particularly in the radii at peripheral zones (Figure 10b). High stresses were also observed locally in the space frame composed of optimized 3D trusses (Figure 11).
- Time-Temperature Curves: Time-temperature curves for both die designs were comparable during preheating and casting cycles (Figure 3 and Figure 4). The conventional die even exhibited a slightly faster heating time (965 s to reach 200°C) compared to the lightweight die (1558 s). This was attributed to the smaller cooling channel surface area in the lightweight die, despite its lower mass.
- Statistical/Qualitative Analysis Results:
- Quantitative Energy Savings: The simulations quantitatively demonstrated the significant energy savings potential of the lightweight modular design, with a consistent reduction factor of approximately 5.2 in total energy demand across different casting lot sizes.
- Qualitative Deformation Behavior: Qualitative analysis of deformation patterns revealed that while the lightweight die exhibited higher deformations under mechanical load at room temperature, its behavior changed at operating temperature. Under combined thermal and mechanical loads, the lightweight design showed reduced wall thickness deviation compared to the conventional die.
- Stress Distribution: Stress analysis qualitatively identified critical areas of stress concentration in the lightweight design, particularly at notches and radii of the load-bearing structure and within the space frame.
- Data Interpretation:
- Energy Efficiency: The results strongly support the hypothesis that a modular lightweight die casting die can significantly reduce energy consumption in the HPDC process. This reduction is primarily attributed to the lower mass of the lightweight design, requiring less energy for heating.
- Structural Performance: While the lightweight die exhibited higher deformations and stresses in certain scenarios, the overall deformation remained relatively small and comparable to the conventional die. Under realistic casting conditions (setup #III), the lightweight design even showed improved deformation performance. The stress analysis highlighted areas requiring careful material selection and structural optimization.
- Modular Design Feasibility: The initial simulation results suggest that the modular lightweight design concept is feasible and holds promise for improving the efficiency and flexibility of die casting dies.
- Figure Name List:
- Figure 1. Cross-sectional (a) and isometric (b) view of the lightweight design die.
- Figure 2. Illustration of boundary conditions for the finite element model; (a) conventional die casting die, (b) lightweight design die; see Table 1 for notes on 1-8.
- Figure 3. Calculated transient thermal output of cooling channels and average cavity temperature during preheating of a lightweight and conventional die casting die.
- Figure 4. Calculated transient thermal output and average cavity temperature after 20 casting cycles.
- Figure 5. Total energy demand for three different casting lot sizes.
- Figure 6. Graphical representation of the wall thickness deviation according to boundary conditions I (see Table 3).
- Figure 7. Graphical representation of the wall thickness deviation according to boundary conditions II (see Table 3).
- Figure 8. Graphical representation of the wall thickness deviation according to boundary conditions II (see Table 3).
- Figure 9. Calculated displacement in y-direction of the functional unit of a high-pressure die casting machine, equipped with a conventional and lightweight die casting die; boundary conditions according to #Ill, Table 3; magnification of 40x.
- Figure 10. Graphical visualization of the equivalent stresses at the cross section of the lightweight design die.
- Figure 11. Graphical visualization of the equivalent stresses at the space frame of the lightweight design die.
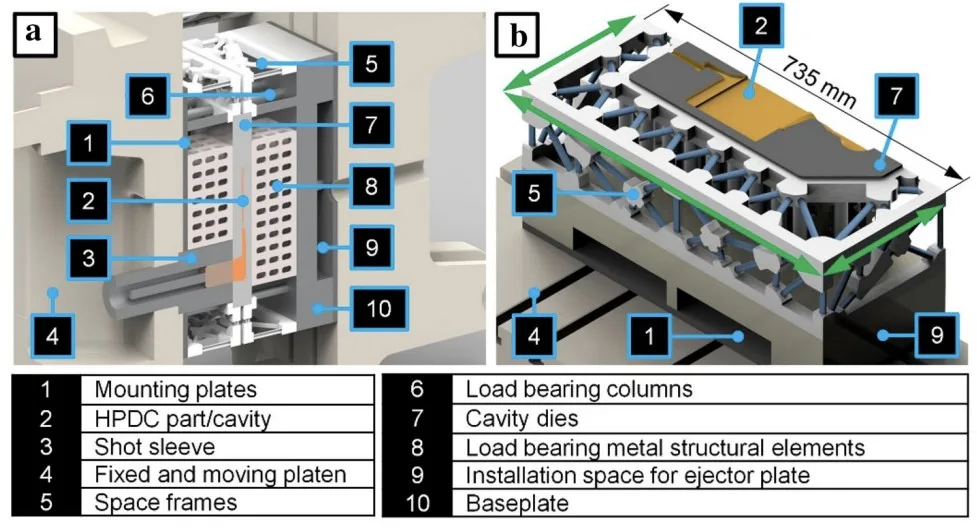
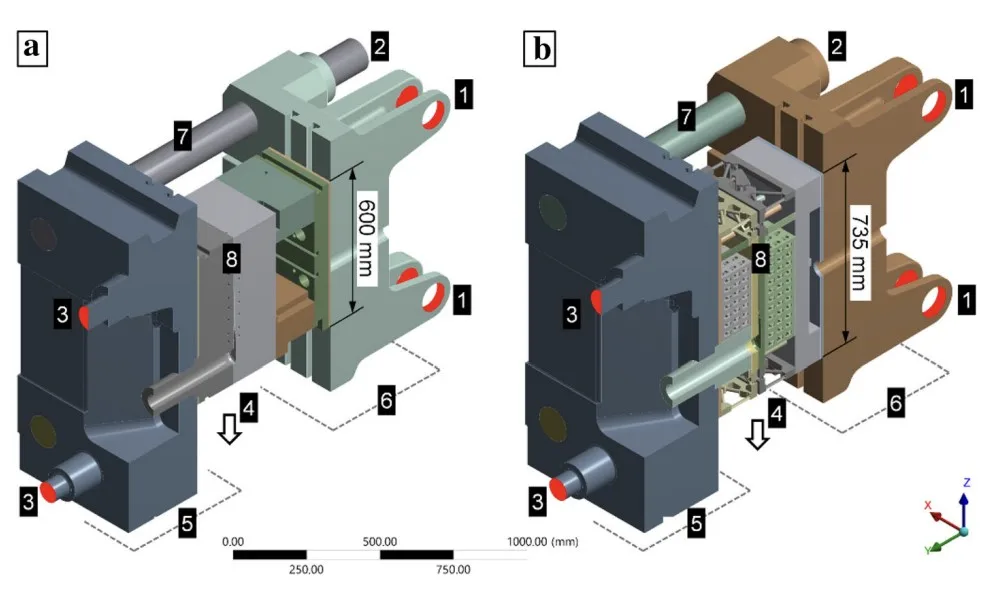
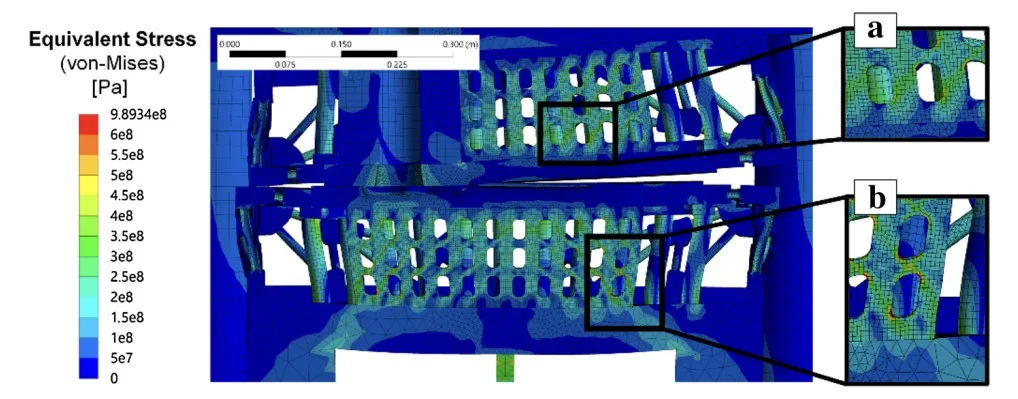
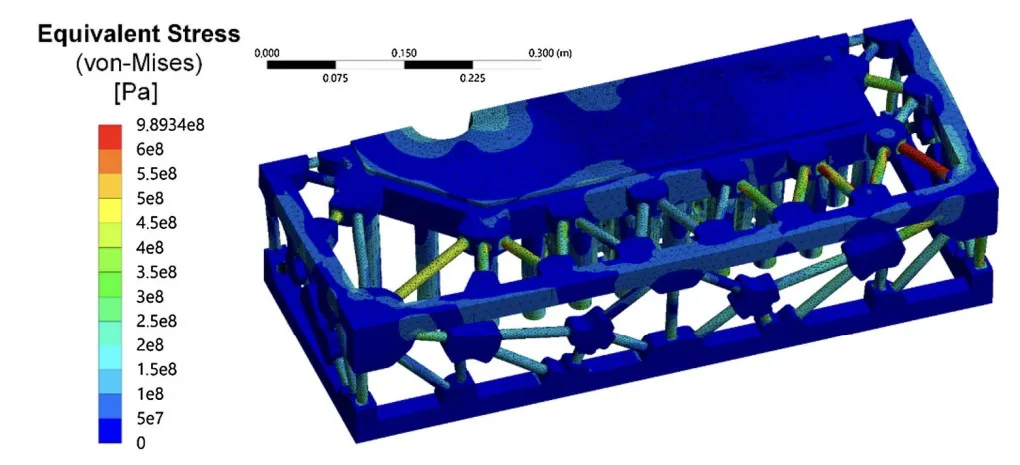
6. Conclusion and Discussion:
- Summary of Main Results:
This initial study demonstrated the potential of a modular lightweight die casting die design to significantly reduce energy consumption in the HPDC process. Simulation results indicated an approximate 5.2-fold reduction in total energy demand compared to a conventional die. While calculated deformations and stresses were higher in the lightweight design, they remained within a manageable range and, under realistic casting conditions, even showed improved deformation performance. - Academic Significance of the Research:
This research provides valuable initial insights into the feasibility and performance characteristics of lightweight modular die casting dies. It contributes to the academic understanding of die casting die design by exploring a novel approach focused on energy efficiency and modularity. The study highlights the potential of lightweight design principles in the context of HPDC and provides a foundation for further research and development in this area. - Practical Implications:
The findings have significant practical implications for the die casting industry:- Reduced Energy Costs: The substantial energy savings potential of lightweight dies can lead to significant reductions in operational costs for die casting companies, especially with increasing energy prices and environmental concerns.
- Smaller Lot Sizes: Lower energy consumption and potentially reduced die manufacturing costs could make HPDC more economically viable for smaller production lot sizes, increasing the flexibility and applicability of the process.
- Sustainable Manufacturing: Reduced energy consumption and material usage contribute to a more sustainable and environmentally friendly die casting process.
- Lower Power Requirements: The reduced thermal output of cooling channels in the lightweight die suggests the possibility of using temperature control units with lower power requirements.
- Limitations of the Research:
This study is an initial investigation and has several limitations:- Simulation-Based Study: The results are based on numerical simulations and require experimental validation to confirm their accuracy and applicability in real-world casting scenarios.
- Specific Geometry and Process Conditions: The analysis was conducted for a specific 4-mm plate geometry and set of process conditions. The generalizability of the findings to other component geometries and casting parameters needs further investigation.
- Simplified Boundary Conditions: Certain boundary conditions, such as the interface heat transfer coefficient and the frictionless assumption for sliding, were simplified due to data limitations. More refined models and experimental data are needed for improved accuracy.
- Effective Cavity Pressure Coupling: The effective cavity pressure was not dynamically coupled with material solidification in the simulations, which could affect the accuracy of deformation and stress predictions.
- Component Quality Beyond Deformation: The study primarily focused on die deformation. Other aspects of HPDC component quality, such as porosity and mechanical properties, were not directly assessed.
7. Future Follow-up Research:
- Directions for Follow-up Research:
Future research should focus on the following directions to further develop and validate the modular lightweight die casting die concept:- Experimental Validation: Manufacturing a prototype modular lightweight die casting die and conducting experimental casting trials to validate the simulation results and assess its performance in a real production environment.
- Structural Optimization: Further optimize the lightweight structure, particularly the load-bearing metal structural element and space frame, to reduce stress concentrations and minimize deformations.
- Advanced Die Materials: Investigate the use of advanced die materials with higher thermal conductivity and tensile strength to further improve thermal management and structural integrity.
- Advanced Temperature Control: Explore and integrate advanced die temperature control methods, such as conformal cooling channels, to optimize die temperature uniformity and cycle times.
- Manufacturing Concepts: Develop manufacturing concepts and strategies for the cost-effective production of modular lightweight die casting dies, considering the specific requirements of the design.
- Areas Requiring Further Exploration:
Further exploration is needed in the following areas:- Real Die Casting Die Implementation and Testing: Moving beyond simulations to real-world implementation and testing is crucial to assess the practical viability of the concept.
- HPDC Component Quality Assessment: Comprehensive evaluation of HPDC component quality produced using lightweight dies, including dimensional accuracy, surface finish, and mechanical properties.
- Consideration of Sliders and Complex Geometries: Extending the design concept to accommodate sliders and more complex component geometries with undercuts, which are common in industrial applications.
- Manufacturing Cost Analysis: Conducting a detailed manufacturing cost analysis to compare the production costs of modular lightweight dies with conventional dies and assess the overall economic benefits.
- Coupling of Cavity Pressure and Solidification: Implementing a more sophisticated simulation approach that dynamically couples cavity pressure with material solidification to improve the accuracy of deformation and stress predictions.
8. References:
- H. Lickfett, NE-Metallgießereien in Deutschland: Strukturentwicklung und Strategische Investitionen pro Standort Deutschland (Leichtbau in Guss, Saarbru¨cken, 2013)
- R. Scho¨ngrundner, W. Ecker, S. Marsoner et al., Development of a simulation aided design strategy for casting die frames. In: 9th International Tooling Conference, Leoben, Austria, (2012)
- C. Brecher, D. O¨ zdemir (eds.), Integrative Production Technology: theory and Applications (Springer, Cham, 2017)
- Y. Queudeville, T. Ivanov, C. Nußbaum et al., Decision and design methodologies for the lay-out of modular dies for high-pressure-die-cast-processes. in Materials Science Forum, (RWTH Aachen, Aachen, 2009), pp. 345–348
- B. Hummler-Schaufler, C. Schlumpberger, Produktentwicklung auf hohem Niveau. Druckgusspraxis 1, 39–42 (2004)
- Y. Queudeville, U. Vroomen, A. Bu¨hrig-Polaczek, Modularization methodology for high pressure die casting dies. Int. J. Adv. Manuf. Technol. 71(9–12), 1677–1686 (2014). https://doi.org/10.1007/s00170-013-5582-9
- O. Eitelwein, J. Weber, Unternehmenserfolg durch Modularisierung von Produkten, Prozessen und Supply Chains: WHU Benchmarking-Studie Modularisierung (Books on Demand, Norderstedt, 2011)
- J.H. Mikkola, O. Gassmann, Managing modularity of product architectures: toward an integrated theory. IEEE Trans. Eng. Manag. 50(2), 204–218 (2003). https://doi.org/10.1109/TEM.2003.810826
- H. Goehler, J. Meinert, T. Doll et al., Steel hollow sphere structures for energy efficient foaming tools. in Cellular Materials—CellMat (International Congress Center Dresden, Dresden, Germany, 2014)
- M.R. Barone, D.A. Caulk, A new method for thermal analysis of die casting. Trans. ASME J. Heat Transf. 115, 284–293 (1993)
- K. Hegde, H. Ahuett-Garza, G. Padiyar, NADCASponsored research: FEM analysis of die casting die deflections: Part I—modeling and simulation. in 18th International Die Casting Congress and Exposition, IN, USA, (1995)
- H. Ahuett-Garza, K. Hegde, R.A. Miller et al., NADCA-sponsored research: FEM analysis of die casting die deflections: Part ll—results. in 18th International Die Casting Congress and Exposition, IN, USA, (1995)
- H. Ahuett-Garza, R.A. Miller, The effects of heat released during fill on the deflections of die casting dies. J. Mater. Process. Technol. 142(3), 648–658 (2003). https://doi.org/10.1016/S0924-0136(03)00685-X
- A. Long, D. Thornhill, C. Armstrong et al., Stress correlation between instrumentation and simulation analysis of the die for high pressure die casting. Int. Metalcast 7(2), 27–41 (2013). https://doi.org/10.1007/BF03355551
- S.I. Jeong, C.K. Jin, H.Y. Seo et al., Mold structure design and casting simulation of the high-pressure die casting for aluminum automotive clutch housing manufacturing. Int. J. Adv. Manuf. Technol. 228(12), 1599 (2015). https://doi.org/10.1007/s00170-015-7566-4
- H. Yamagata, Y. Shigenaga, S. Tanikawa et al., Deflection simulation of a die installed in a highpressure die-casting machine. Trans. Jpn. Soc. Mech. Eng. 79(806), 3920–3929 (2013)
- C.V. Camp, M. Farshchin, Design of space trusses using modified teaching–learning based optimization. Eng. Struct. 62–63, 87–97 (2014). https://doi.org/10.1016/j.engstruct.2014.01.020
- M. Farshchin, C.V. Camp, M. Maniat, Multi-class teaching–learning-based optimization for truss design with frequency constraints. Eng. Struct. 106, 355–369 (2016). https://doi.org/10.1016/j.engstruct.2015.10.039
- B. Yalc¸in, M. Koru, O. Ipek et al., Effect of injection parameters and vacuum on the strength and porosity amount of die-casted A380 alloy. Int. Metalcast 11(2), 195–206 (2017). https://doi.org/10.1007/s40962-016-0046-2
- G. Dour, M. Dargusch, C. Davidson et al., Development of a non intrusive heat transfer coefficient gauge and its application to high pressure die casting. Metall. Sci. Technol. 22(1), 16–21 (2004)
- Y. Cao, Z. Guo, S. Xiong, Determination of the metal/ die interfacial heat transfer coefficient of high pressure die cast B390 alloy. IOP Conf. Ser.: Mater. Sci. Eng. 33, 12010 (2012). https://doi.org/10.1088/1757-899X/33/1/012010
- Z. Guo, S. Xiong, S. Cho et al., Interfacial heat transfer coefficient between metal and die during high pressure die casting process of aluminum alloy. Front. Mech. Eng. China 2(3), 283–287 (2007). https://doi.org/10.1007/s11465-007-0049-z
- Z. Guo, S. Xiong, B. Liu et al., Understanding of the influence of process parameters on the heat transfer behavior at the metal/die interface in high pressure die casting process. Sci. China Ser. E-Technol. Sci. 52(1), 172–175 (2009). https://doi.org/10.1007/s11431-008-0295-2
- Z.-P. Guo, S.-M. Xiong, B.-C. Liu et al., Effect of process parameters, casting thickness, and alloys on the interfacial heat-transfer coefficient in the highpressure die-casting process. Metall. Mater. Trans. A 39(12), 2896–2905 (2008). https://doi.org/10.1007/s11661-008-9640-0
- A. Hamasaiid, G. Dour, M.S. Dargusch et al., Heattransfer coefficient and in-cavity pressure at the casting-die interface during high-pressure die casting of the magnesium alloy AZ91D. Metall. Mater. Trans. A 39(4), 853–864 (2008). https://doi.org/10.1007/s11661-007-9452-7
- G. Zhi-peng, X. Shou-mei, L. Bai-cheng et al., Determination of the heat transfer coefficient at metal– die interface of high pressure die casting process of AM50 alloy. Int. J. Heat Mass Trans. 51(25–26), 6032–6038 (2008). https://doi.org/10.1016/ j.ijheatmasstransfer.2008.04.029
- M. Ciofalo, I. Di Piazza, V. Brucato, Investigation of the cooling of hot walls by liquid water sprays. Int. J. Heat Mass Trans. 42(7), 1157–1175 (1999). https://doi.org/10.1016/S0017-9310(98)00250-6
- G.W. Liu, Y.S. Morsi, B.R. Clayton, Characterisation of the spray cooling heat transfer involved in a high pressure die casting process. Int. J. Therm. Sci. 39(5), 582–591 (2000). https://doi.org/10.1016/S1290-0729(00)00207-6
- A.S. Sabau, R.B. Dinwiddie, Characterization of spray lubricants for the high pressure die casting processes. J. Mater. Process. Technol. 195(1–3), 267–274 (2008). https://doi.org/10.1016/j.jmatprotec.2007.05.021
- J.H. Hattel, P.N. Hansen, A 1-D analytical model for the thermally induced stresses in the mold surface during die casting. Appl. Math. Model. 18(10), 550–559 (1994). https://doi.org/10.1016/0307-904X(94)90140-6
- S. Mu¨ller, Ermittlung der Lebensdauer von Aluminium-Druckgießformen aufgrund thermischer Ermu¨dung. Zugl.: Braunschweig, Techn. Univ., Diss., 2015. Forschungsberichte des Instituts fu¨r Fu¨ge- und Schweißtechnik, Shaker, Aachen, 40 (2015)
- M. Ayabe, T. Nagaoka, K. Shibata et al., Effect of high thermal conductivity die steel in aluminum casting. Int. Metalcast 2(2), 47–55 (2008). https://doi.org/10.1007/BF03355427
- E. Kaschnitz, P. Hofer, W. Funk, Thermophysikalische Daten eines Warmarbeitsstahls mit hoher Wa¨rmeleitfahigkeit. GIESSEREI 97(9), 46–49 (2010)
- A. Armillotta, R. Baraggi, S. Fasoli, SLM tooling for die casting with conformal cooling channels. Int. J. Adv. Manuf. Technol. 71(1–4), 573–583 (2014). https://doi.org/10.1007/s00170-013-5523-7
- T. Kimura, H. Yamagata, S. Tanikawa, FEM stress analysis of the cooling hole of an HPDC die. IOP Conf. Ser.: Mater. Sci. Eng. 84, 12052 (2015). https://doi.org/10.1088/1757-899X/84/1/012052
- H. Hu, F. Chen, X. Chen et al., Effect of cooling water flow rates on local temperatures and heat transfer of casting dies. J. Mater. Process. Technol. 148(1), 57–67 (2004). https://doi.org/10.1016/j.jmatprotec.2004.01.040
- T. Kim, K. Jin, N. Kim et al., Numerical analysis and optimal design to reduce residual stresses and deformations of die casting baseplate after ejection. J. Mech. Sci. Technol. 29(7), 2949–2956 (2015). https://doi.org/10.1007/s12206-015-0625-9
- D. Klobcˇar, L. Kosec, B. Kosec et al., Thermo fatigue cracking of die casting dies. Eng. Fail. Anal. 20, 43–53 (2012). https://doi.org/10.1016/j.engfailanal.2011.10.005
- D. Klobcˇar, J. Tusˇek, B. Taljat, Thermal fatigue of materials for die-casting tooling. Mater. Sci. Eng. A 472(1–2), 198–207 (2008). https://doi.org/10.1016/j.msea.2007.03.025
- S. Naimi, S.M. Hosseini, Tool steels in die-casting utilization and increased mold life. Adv. Mech. Eng. 7(1), 286071 (2014). https://doi.org/10.1155/2014/286071
9. Copyright:
*This material is Sebastian Müller, Klaus Dilger, Anke Müller, Felix Rothe, and Klaus Dröder's paper: Based on AN INITIAL STUDY OF A LIGHTWEIGHT DIE CASTING DIE USING A MODULAR DESIGN APPROACH.
*Paper Source: https://doi.org/10.1007/s40962-018-0218-3
This material was summarized based on the above paper, and unauthorized use for commercial purposes is prohibited.
Copyright © 2025 CASTMAN. All rights reserved.