This article introduces the paper "Development of Aluminium Hollow Subframe Using High-Pressure Die Casting".
1. Overview:
- Title: Development of Aluminium Hollow Subframe Using High-Pressure Die Casting
- Authors:
- Akihiko Asami
- Tomoyuki Imanishi
- Yukio Okazaki
- Tomohiro Ono
- Kenichi Tetsuka
- Published Year: 2016
- Published Journal/Conference: SAE Technical Paper
- Keywords:
- High-Pressure Die Casting (HPDC)
- Aluminium Hollow Subframe
- Weight Saving
- Sand Core
- Al-Mg-Si Alloy
- Thin-walled Parts
2. Research Background:
- Social/Academic Context:
- The demand for automotive weight savings is increasing to reduce carbon emissions and conserve energy, contributing to global environmental protection.
- Weight reduction also enhances fuel efficiency and boosts dynamic performance of vehicles.
- High-tensile steel plates and lightweight aluminum are materials being employed to achieve weight savings in automotive subframes.
- Closed-section structures are commonly used to efficiently increase part stiffness compared to open sections.
- Aluminum hollow-cast subframes are already in practical use, manufactured using sand cores in Gravity Die Casting (GDC) or Low-Pressure Die Casting (LPDC) processes.
- Limitations of Existing Research:
- Conventional methods like GDC or LPDC for aluminum hollow-casting using sand cores face limitations in reducing product thickness.
- In GDC or LPDC, when thickness is reduced, the flow rate of aluminum declines during casting. Heat is drawn from the aluminum melt by the mold and the sand core, leading to aluminum solidification.
- These limitations in thickness reduction with GDC and LPDC hinder the achievement of significant weight reductions.
- High costs associated with welded aluminum subframes, including material, mold, and welding costs, impede their widespread adoption.
- Necessity of Research:
- There is a need for a manufacturing method that allows for the production of lightweight, thin-walled aluminum hollow subframes to overcome the limitations of existing methods and further reduce vehicle weight.
- Developing a technology to mold large cores and utilize a material with good flow performance is essential for realizing this technology.
3. Research Objectives and Research Questions:
- Research Objective:
- To develop a lightweight, hollow subframe technology employing High-Pressure Die Casting (HPDC), a method well-suited to reducing wall thickness, as the manufacturing method.
- To develop a sand core technology that balances pressure resistance with collapsibility for HPDC conditions, enabling the hollow-casting of large parts like subframes.
- To employ a non-heat-treated Al-Mg-Si alloy to reduce costs while ensuring castability and mechanical properties suitable for subframes.
- Core Research Question:
- Can HPDC, combined with optimized sand core technology and material selection, effectively produce thin-walled aluminum hollow subframes that achieve significant weight reduction compared to conventional steel subframes, while maintaining necessary structural integrity and performance?
- Research Hypothesis:
- By employing HPDC with a newly developed sand core technology and an optimized non-heat-treated Al-Mg-Si alloy, it is possible to manufacture a hollow aluminum subframe that is significantly lighter than a conventional subframe manufactured from welded steel plates, without compromising structural performance.
4. Research Methodology:
- Research Design:
- The research focused on the development and experimental validation of a new manufacturing process for aluminum hollow subframes using HPDC.
- The study involved designing and manufacturing product molds and core molds for a hollow aluminum subframe based on the shape of a mass-production subframe.
- The performance of the developed hollow aluminum subframe was compared to conventional steel subframes through static fracture tests and durability tests.
- Data Collection Method:
- Casting Experiments: HPDC experiments were conducted using varying casting conditions, sand core materials, baking conditions, and Al-Mg-Si alloy compositions.
- Mechanical Property Tests:
- Tensile tests were performed to evaluate the strength and elongation of the developed Al-Mg-Si alloy with varying Si content.
- Static fracture tests and durability tests were conducted on the manufactured hollow diecast aluminum subframe to assess its structural performance under conditions simulating actual vehicle inputs.
- Dimensional Accuracy Measurement: Dimensional accuracy of the cast products was assessed to evaluate the effectiveness of the core fixing method and melt flow optimization.
- Analysis Method:
- Mechanical Property Analysis: The results of tensile tests, static fracture tests, and durability tests were analyzed to evaluate the mechanical performance of the developed material and subframe.
- Comparison Analysis: The weight and performance of the developed hollow aluminum subframe were compared to those of conventional steel subframes to quantify the weight reduction and performance characteristics.
- Process Parameter Optimization: The effects of varying casting conditions, sand core parameters, and alloy composition on the quality and performance of the cast subframe were analyzed to optimize the manufacturing process.
- Research Subject and Scope:
- The research focused on the development of an aluminum hollow subframe for automotive applications.
- The scope included:
- Development of sand core molding technology suitable for HPDC.
- Material selection and optimization of a non-heat-treated Al-Mg-Si alloy for HPDC hollow-casting.
- Design and manufacturing of molds for HPDC of a hollow subframe.
- Experimental validation of the mechanical performance of the developed subframe through static fracture and durability tests.
- Comparison of the developed aluminum subframe with conventional steel subframes in terms of weight and performance.
5. Key Research Findings:
- Core Research Findings:
- A lightweight, hollow subframe technology employing HPDC was successfully developed for large, thin-walled parts.
- A sand core molding technology suitable for HPDC was established, addressing the issue of balancing pressure resistance and collapsibility of sand cores.
- An optimized non-heat-treated Al-Mg-Si alloy with added Si was developed, enhancing castability and mechanical properties for HPDC hollow-casting.
- The developed hollow aluminum subframe achieved an approximate 40% weight reduction compared to a conventional subframe manufactured from welded steel plates (Fig. 1).
- The developed hollow diecast aluminum subframe cleared all set conditions in static fracture and durability tests, demonstrating its suitability for mass-produced parts.
- Statistical/Qualitative Analysis Results:
- Static Fracture Test Results (Table 1): The hollow diecast aluminum subframe demonstrated clearance rates exceeding set conditions in static fracture tests at various locations and directions. For example, at the "Lower Arm mounting section FT+", the rate of clearance was 207% for both Maximum and Yield conditions.
- Durability Test Results (Table 2): The hollow diecast aluminum subframe cleared set conditions in all durability tests, including suspension assembly durability, torque-rod mounting section, steering gear box mounting section, stabilizer mounting section, and suspension impact test. All results were marked as "OK".
- Mechanical Properties of Al-Mg-Si Alloy (Fig. 10, Fig. 15):
- The addition of Si to Al-5Mg material improved mechanical properties.
- An Al-5Mg-1.8Si composition was found to be optimal, achieving a balance between elongation and strength. This composition enabled stable realization of elongation of 5% and higher, and strength of 150MPa and higher.
- Casting tests using plate-shaped test molds showed that with approximately 2.0% Si addition, the balance between strength and elongation was judged optimal for a subframe (Fig. 10).
- Data Interpretation:
- HPDC, when combined with the developed sand core technology and optimized Al-Mg-Si alloy, is a viable and effective method for manufacturing lightweight, high-performance aluminum hollow subframes.
- The 40% weight reduction achieved by the developed hollow aluminum subframe represents a significant improvement over conventional steel subframes, contributing to vehicle weight savings and improved fuel efficiency.
- The successful clearance of static fracture and durability test conditions validates the structural integrity and reliability of the developed hollow aluminum subframe for automotive applications.
- Figure Name List:
- Figure 1. Developed hollow aluminum subframe
- Figure 2. Motorcycle frame parts (CBR600RR)
- Figure 3. Comparison of casting conditions for each manufacturing method
- Figure 4. Manufacturing process
- Figure 5. Section of core following primary baking
- Figure 6. Change in temperature and phenol resin melt viscosity
- Figure 7. Change in temperature and amount of residual phenol resin
- Figure 8. Time to baking of center of thick part of core
- Figure 9. Relationship between gate speed and strength
- Figure 10. Effect of amount of added Si on change in mechanical properties of Al-Mg material
- Figure 11. Shape of product and shape of core
- Figure 12. Position of boards
- Figure 13. Position of core holding pin and sand removal window
- Figure 14. Position for cutting of test piece
- Figure 15. Mechanical properties of test pieces cut from subframe
- Figure 16. Static fracture test and durability test
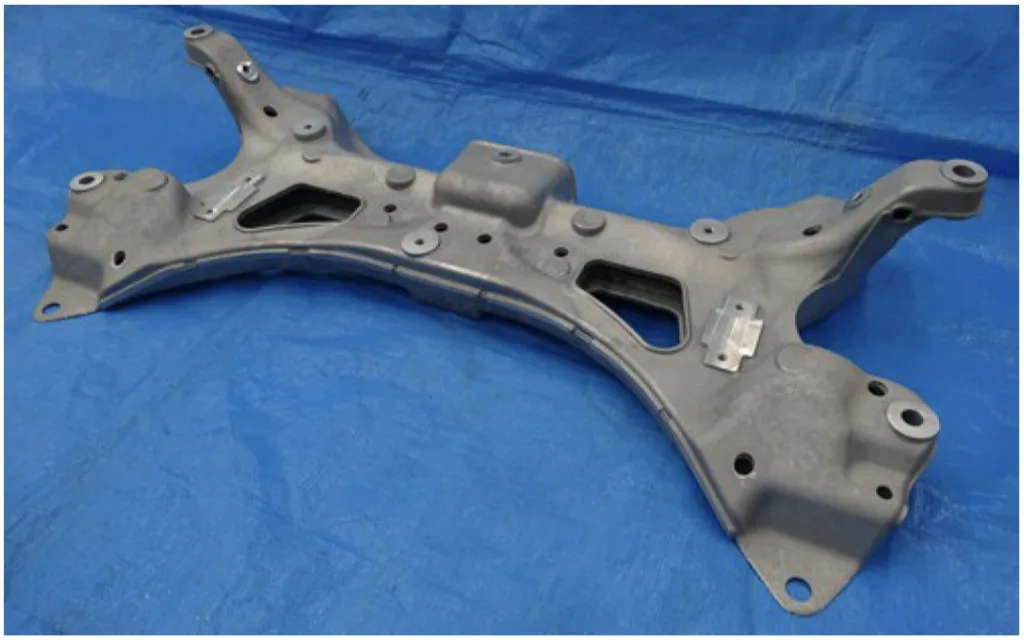
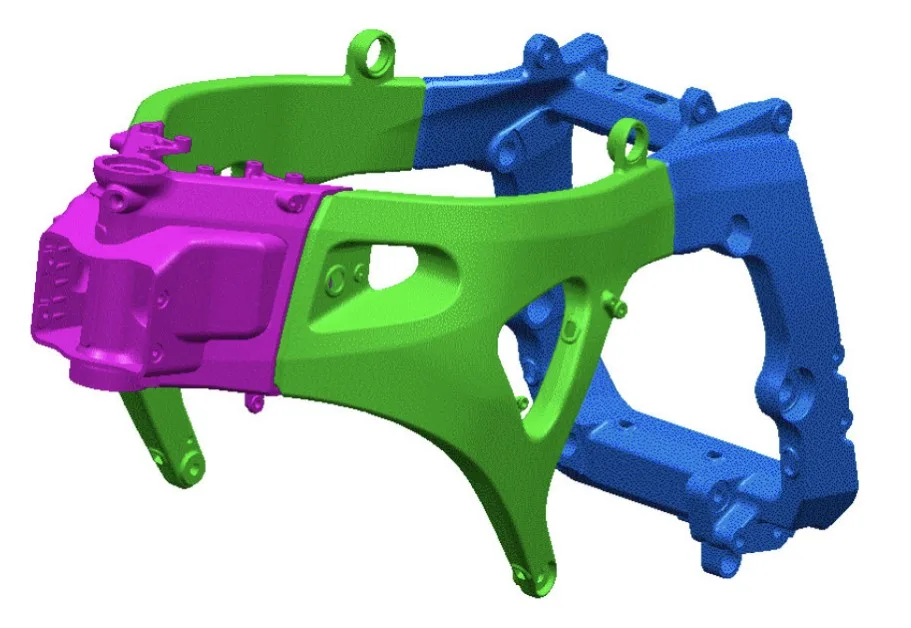
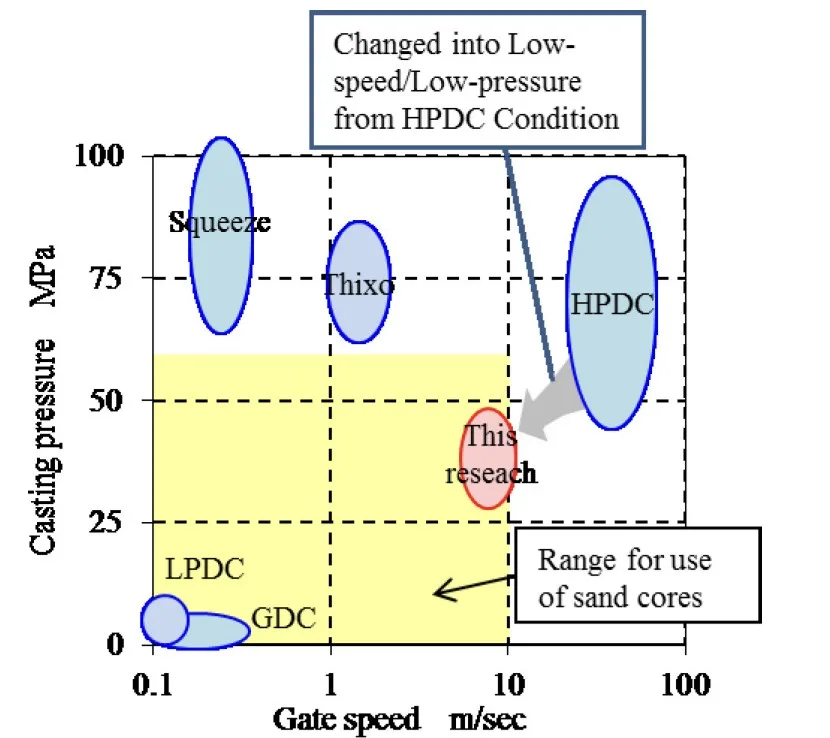
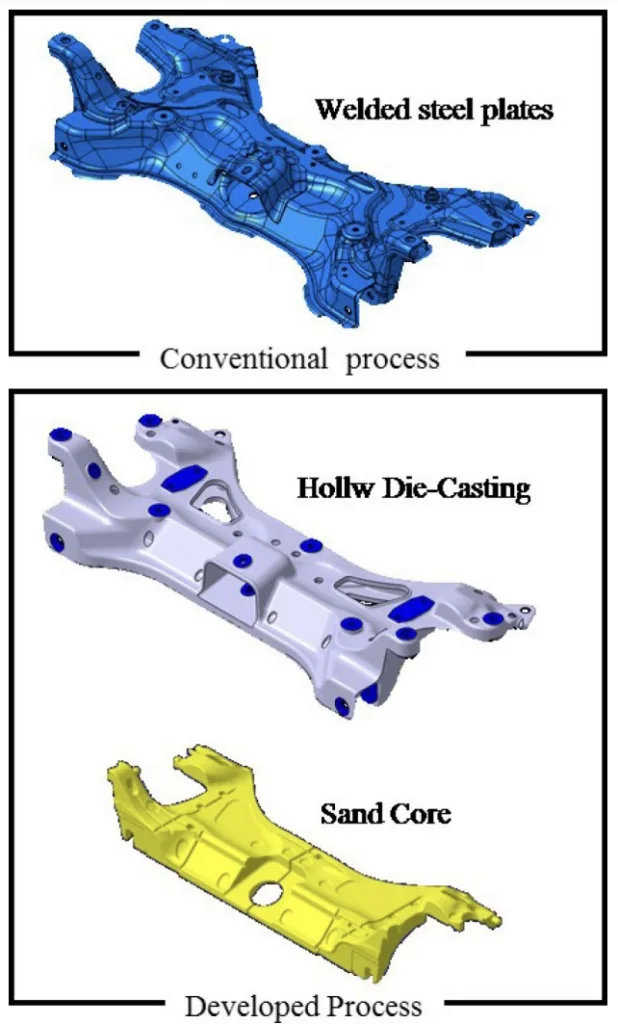
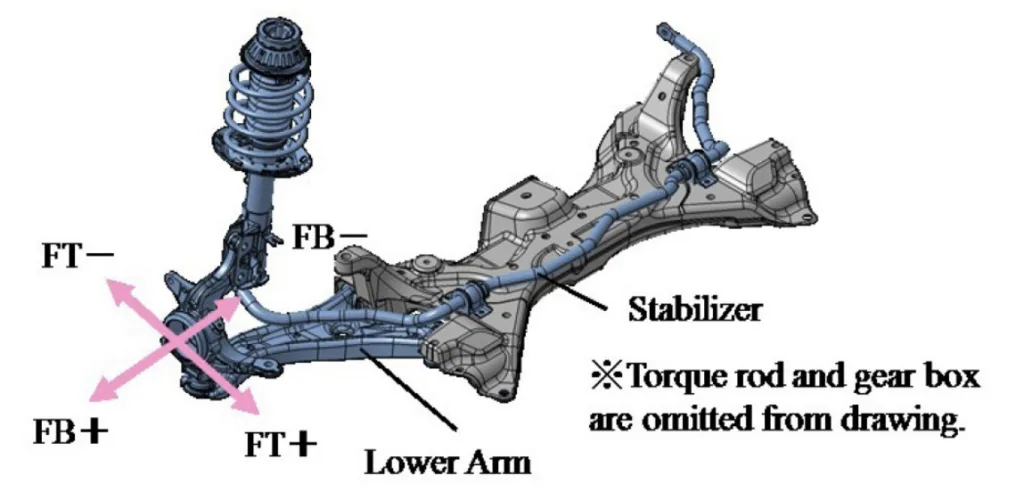
6. Conclusion and Discussion:
- Summary of Key Results:
- The research successfully developed a hollow-casting technology using HPDC for manufacturing large, thin-walled aluminum subframes.
- Key innovations included a sand core molding technology suitable for HPDC and the optimization of a non-heat-treated Al-Mg-Si alloy with Si addition.
- The developed hollow aluminum subframe achieved a significant 40% weight reduction compared to conventional steel subframes while meeting all performance requirements in static fracture and durability tests.
- Research's Academic Significance:
- This research demonstrates the feasibility and effectiveness of using HPDC for producing complex, hollow automotive structural components like subframes.
- The development of a sand core technology specifically tailored for HPDC expands the application range of this high-productivity casting method.
- The optimized Al-Mg-Si alloy provides a cost-effective material solution for lightweight aluminum castings, balancing castability, mechanical properties, and cost.
- Practical Implications:
- The developed HPDC hollow-casting technology offers a viable manufacturing solution for producing lightweight aluminum subframes for the automotive industry.
- The significant weight reduction achieved contributes to improved fuel efficiency, reduced carbon emissions, and enhanced vehicle performance.
- The use of a non-heat-treated Al-Mg-Si alloy helps to minimize production costs, making aluminum hollow subframes more economically attractive for wider adoption.
- Limitations of Research:
- The research focused on a specific subframe design and material composition. The generalizability of the developed technology to other subframe designs or aluminum alloys may require further investigation.
- The study primarily focused on mechanical performance. Other aspects, such as corrosion resistance and long-term durability in real-world vehicle operating conditions, could be further explored.
7. Future Follow-up Research:
- Future Research Directions:
- Further optimization of the HPDC process parameters, including injection speed, casting pressure, and cooling conditions, to enhance productivity and casting quality.
- Exploration of other aluminum alloys and compositions to further improve mechanical properties, castability, and cost-effectiveness of HPDC hollow-cast subframes.
- Application of the developed HPDC hollow-casting technology to other automotive components and structural parts to maximize weight reduction and performance benefits across the vehicle.
- Additional Areas for Exploration:
- Conducting long-term durability studies and real-world vehicle testing to validate the long-term performance and reliability of the developed hollow aluminum subframe.
- Performing a comprehensive cost-effectiveness analysis, considering material costs, manufacturing costs, and performance benefits, to assess the economic viability of mass production.
- Investigating the potential for further weight reduction through design optimization of the hollow subframe structure and topology.
8. References:
- Koya, E., Suzuki, T., Nakagawa, M., Fujimoto, G. et al., "Development of Hollow, Weld-able Die-Cast Parts for Aluminum Motorcycle Frames," SAE Technical Paper 2003-32-0055, 2003, doi:10.4271/2003-32-0055.
9. Copyright:
This material is based on the paper by [Akihiko Asami, Tomoyuki Imanishi, Yukio Okazaki, Tomohiro Ono, and Kenichi Tetsuka]
titled: [Development of Aluminium Hollow Subframe Using High-Pressure Die Casting].
Paper Source: [https://doi.org/10.1146/annurev-matsci-070218-010134]
This material is a summary based on the above paper and is for informational purposes only. Unauthorized commercial use is prohibited.
Copyright © 2025 CASTMAN. All rights reserved.