This article introduces the paper "Critical life cycle inventory for aluminum die casting: A lightweight-vehicle manufacturing enabling technology".
1. Overview:
- Title: Critical life cycle inventory for aluminum die casting: A lightweight-vehicle manufacturing enabling technology
- Authors: Weipeng Liu, Tao Peng, Yusuke Kishita, Yasushi Umeda, Renzhong Tang, Wangchujun Tang, Luoke Hu
- Publication Year: 2021
- Published Journal/Conference: Applied Energy
- Keywords:
- Life cycle inventory
- Aluminum die casting
- Energy conservation
- Emission reduction
- Lightweight vehicles
2. Research Background:
- Social/Academic Context of the Research Topic:
- The vehicle industry is driven by the target of carbon neutrality and is striving to implement energy conservation and emission reduction (ECER).
- Aluminum (Al) alloy is a dominant lightweight material for vehicles and an effective ECER solution.
- Die casting (DC) produces nearly 60% of vehicle Al components, achieving a 30-50% weight reduction.
- However, Al DC is highly energy intensive and environmentally polluting.
- Assessing the life cycle ECER effects of vehicle Al die castings (DCs) is necessary, particularly in the manufacturing stage, which is weakly supported by existing research.
- Effective implementation of ECER for Al DC is crucial but lacks attractive measures.
- Limitations of Existing Research:
- Five important aspects have not been considered:
- Die fabrication and heat treatment are rarely included.
- Most studies consider only energy consumption and emissions, but not material consumption and loss.
- Current rough process and data details make it difficult to configure the process and data for a specific product.
- Assessment results are sensitive to some production data, such as rejection rate, but these data are overlooked.
- Most studies focus on box-type parts, and few consider structural parts.
- Few studies have discussed two emerging technologies: high-vacuum die casting (HVDC) and semi-solid die casting (SSDC). Critical inventory data of both technologies are missing.
- Targeted, easy to implement, and low-cost measures for ECER of Al DC are lacking. Existing research rarely provides effective ECER suggestions due to insufficient process data and limited analyses and surveys.
- Five important aspects have not been considered:
- Necessity of Research:
- To bridge the gaps in existing research regarding the life cycle ECER effects of vehicle Al DCs, particularly in the manufacturing stage.
- To provide a more representative and configurable inventory for aluminum die casting.
- To analyze the benefits of HVDC and SSDC in terms of ECER.
- To offer targeted, easy to implement, and low-cost ECER measures for Al DC to support ECER in the vehicle industry.
3. Research Objectives and Research Questions:
- Research Objectives:
- To address three issues:
- The existing inventory data for Al DC are incomplete.
- The ECER effects of HVDC and SSDC are missing.
- There is a lack of attractive suggestions on ECER for Al DC.
- To present a detailed resource and emission flows analysis for Al DC supported by in-depth investigation and on-site data collection.
- To provide a representative and configurable inventory, analyze the benefits of HVDC and SSDC, and present suggestions on ECER of Al DC.
- To address three issues:
- Core Research Questions:
- What are the detailed resource and emission flows for aluminum die casting manufacturing, considering high-pressure DC, high-vacuum DC, and semi-solid DC?
- How does the manufacturing energy consumption differ between box-type and structural aluminum die castings?
- What are the ECER benefits of using HVDC and SSDC compared to conventional HPDC?
- What are the targeted, easy to implement, and low-cost measures for ECER in aluminum die casting?
- How sensitive is the inventory to the characteristics of Al DCs and energy generation methods?
- Research Hypothesis:
- The paper does not explicitly state a research hypothesis.
4. Research Methodology:
- Research Design:
- System boundary definition including three scenarios: high-pressure DC (HPDC), high-vacuum DC (HVDC), and semi-solid DC (SSDC).
- Detailed process division and data description for each scenario.
- Inventory analysis based on in-depth investigation and on-site data collection.
- Comparative analysis of inventory data with existing studies and databases.
- Sensitivity analysis of inventory to Al DC characteristics and energy generation.
- Data Collection Method:
- In-depth investigation and on-site data collection from 13 companies, including:
- Four HPDC factories
- Two Al melting and holding furnace manufacturers
- Two DC machine manufacturers
- Two die makers
- One heat treatment equipment manufacturer
- One vacuum equipment manufacturer
- One semi-solid feedstock equipment manufacturer
- Collaboration with an enterprise to develop a smart production and energy management system for its HPDC workshop.
- Remaining data acquired from literature or equipment specifications.
- In-depth investigation and on-site data collection from 13 companies, including:
- Analysis Method:
- Resource and emission flows analysis for each process in Al DC manufacturing.
- Calculation of embodied energy and CO2 emissions for die fabrication.
- Analysis of energy consumption and material flow for melting, casting, heat treatment, and finishing processes.
- Comparison of inventory data with selected studies and databases (GaBi, Heinemann, Salonitis, Cecchel).
- Sensitivity analysis using spider plots to assess the impact of parameter variations on total energy consumption.
- Research Subject and Scope:
- Focus on the manufacturing stage of vehicle Al DCs, including melting, casting, heat treatment, and finishing.
- Three casting scenarios: HPDC, HVDC, and SSDC.
- Consideration of both box-type and structural parts.
- Analysis of resource inputs and waste outputs in each process.
5. Key Research Results:
- Core Research Results:
- A critical and configurable inventory of aluminum die casting is complemented, providing more representative and configurable data compared to existing studies and LCA databases.
- The energy consumption in the manufacture of structural DCs is nearly 80% larger than that of box-type DCs.
- High-vacuum DC and semi-solid DC can reduce the total energy by "3.5%" and "9.9%", respectively.
- Several targeted ECER measures are proposed with intensive analyses and surveys.
- The sensitivity of specific Al DCs to the developed inventory is discussed, as are the suggested measures considering energy generation.
- Statistical/Qualitative Analysis Results:
- Inventory Comparison: Compared to existing studies, this research provides more detailed process division and data description, contributing to inventory reconfiguration for different Al DCs. Casting yield and production rejection rates significantly influence Al flow.
- Manufacturing Energy Comparison: Total energy consumption for box-type DCs is "5050.6 kWh" and for structural DCs is "9206.9 kWh".
- Benefits of HVDC and SSDC: HVDC can achieve a "5% energy reduction in the DC machine" and a "20% increase in the die life", saving "3.5% of the total energy consumption". SSDC can achieve a "5% reduction in the DC machine energy consumption" and a "100% increase in the die life", saving "9.9% of the total energy consumption".
- Sensitivity Analysis: Total energy consumption is most sensitive to "melting & holding energy efficiency" and "casting yield rate".
- Data Interpretation:
- Structural parts consume significantly more energy than box-type parts in Al DC manufacturing.
- HVDC and SSDC are effective ECER technologies for Al DC, offering energy reduction and improved die life.
- Operation optimization in melting and holding, improving casting yield rate, and increasing process stability are crucial ECER measures.
- Waste heat recovery and considering energy generation sources are important for comprehensive ECER strategies.
- Figure Name List:
- Fig. 1. Life cycle boundary of vehicle Al DCs and detailed processes in the manufacturing stage.
- Fig. 2. Harmonized energy, Al, and CO2 flows for producing 1000 kg of finished Al DCs.
- Fig. 3. Comparison of manufacturing energy consumption between the box-type and structural parts.
- Fig. 4. Spider plot of the total energy consumption sensitivity to selected parameters.
- Fig. 5. CED and CO2 emission flows.
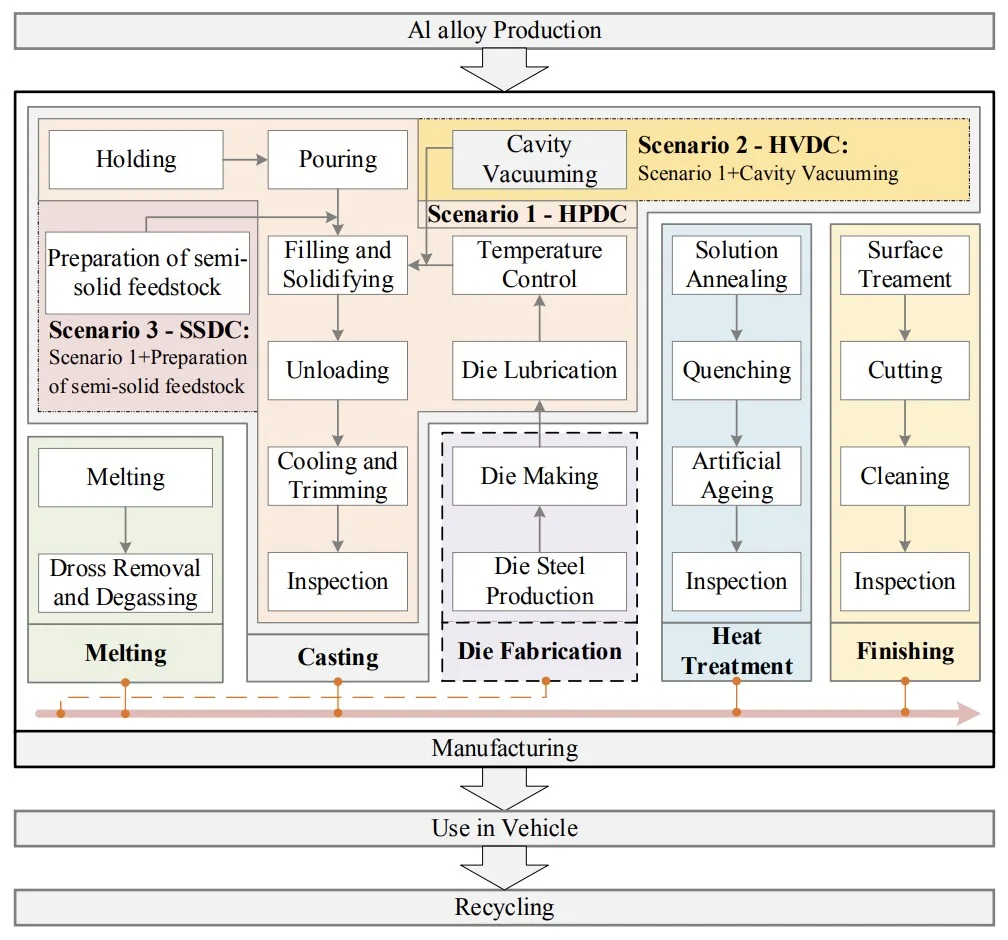
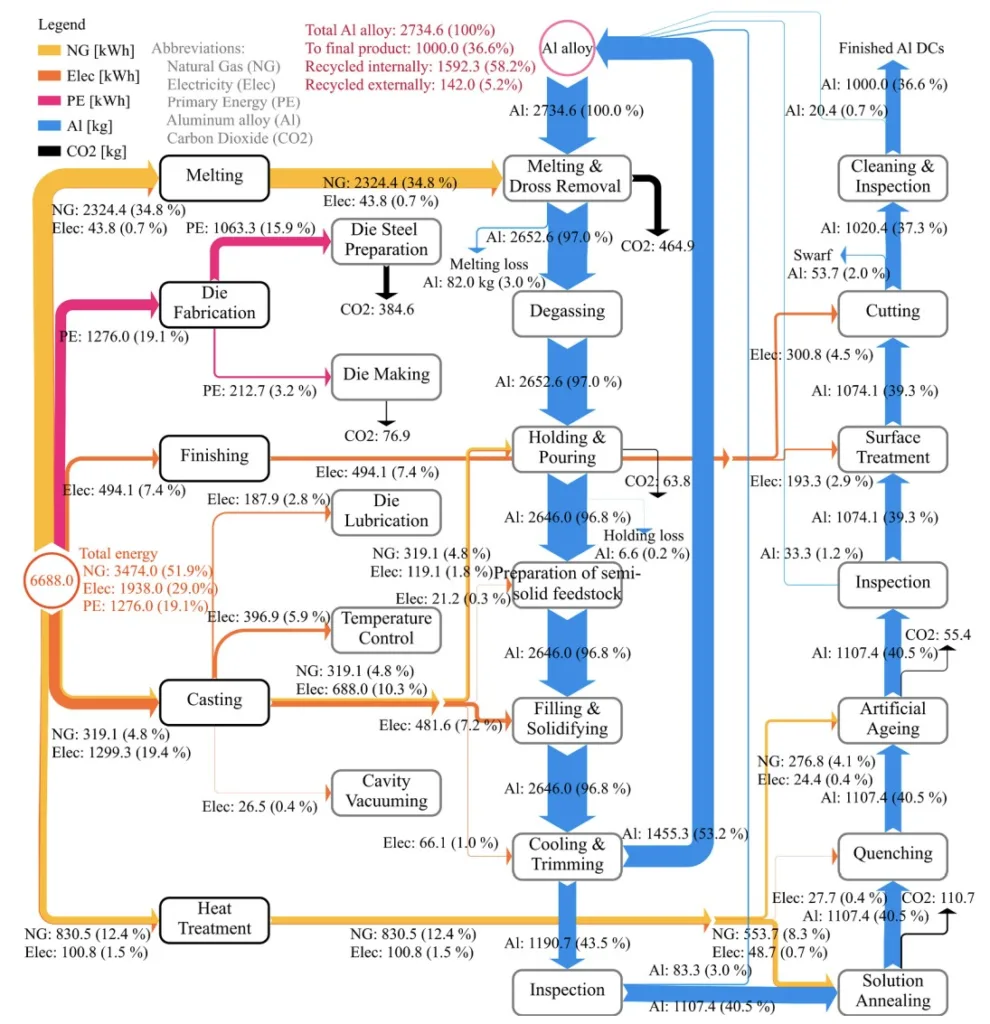
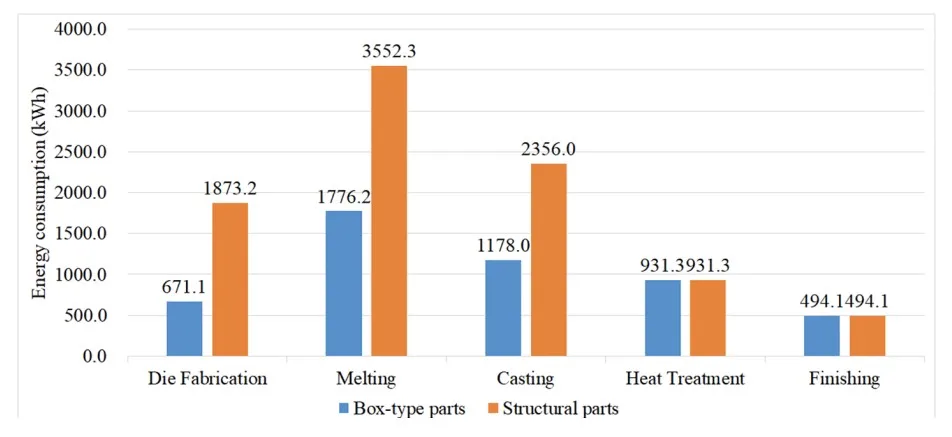
6. Conclusion and Discussion:
- Summary of Main Results:
- The study developed a representative and configurable inventory for vehicle Al DCs, considering HPDC, HVDC, and SSDC scenarios.
- Manufacturing structural Al DCs consumes significantly more energy than box-type Al DCs.
- HVDC and SSDC are identified as ECER enabling-technologies, offering energy savings.
- Targeted ECER suggestions are provided, focusing on melting & holding, casting yield, process stability, and heat treatment.
- The inventory is sensitive to product characteristics, and ECER strategies should consider energy generation impacts.
- Academic Significance of Research:
- Provides a detailed and comprehensive life cycle inventory for aluminum die casting, addressing gaps in existing research.
- Offers a configurable inventory adaptable to different Al DC types and manufacturing conditions.
- Quantifies the ECER benefits of HVDC and SSDC, contributing to the understanding of advanced die casting technologies.
- Highlights the importance of considering structural parts and die fabrication in LCA of Al DCs.
- Practical Implications:
- The developed inventory can be used by Al DC manufacturers to assess and optimize the environmental impact of their processes.
- ECER suggestions provide practical guidance for improving energy efficiency and reducing emissions in Al DC foundries.
- The findings emphasize the potential of HVDC and SSDC for producing lightweight vehicle components with reduced environmental footprint.
- The study highlights the importance of casting yield rate and process stability as key areas for ECER improvement.
- Limitations of Research:
- The resource consumption in equipment manufacturing is neglected as it is amortized over a long service time.
- Transportation energy within the foundry is excluded.
- The study focuses on the manufacturing stage and does not provide a full life cycle assessment of vehicle Al DCs.
- The average values are used for inventory data, and specific product characteristics can influence the results.
7. Future Follow-up Research:
- Directions for Future Research:
- Perform a life cycle ECER assessment of vehicle Al DCs based on this study, expanding the scope beyond the manufacturing stage.
- Conduct research on operation optimization for melting, holding, and casting to further support ECER of Al DC.
- Explore practical and low-cost approaches for waste heat recovery in Al DC processes.
- Investigate the economic feasibility and environmental benefits of implementing HVDC and SSDC for a wider range of Al DC parts.
- Areas Requiring Further Exploration:
- Detailed analysis of the impact of specific Al DC characteristics (shape, mass, complexity) on resource and emission flows.
- Development of more precise and product-specific inventory data for Al DC manufacturing.
- Investigation of advanced control systems and IoT-enabled technologies for real-time monitoring and optimization of Al DC processes.
- Exploration of alternative energy sources and carbon capture technologies for further reducing CO2 emissions from Al DC.
8. References:
- [1] International Energy Agency. Energy consumption share of total final comsumption (TFC) by sector; 2020. https://www.iea.org/data-and-statistics/?cou ntry=WORLD&fuel=Energy%20consumption&indicator=TFCbySector.
- [2] Comello S, Glenk G, Reichelstein S. Transitioning to clean energy transportation services: life-cycle cost analysis for vehicle fleets. Appl Energy 2021;285:116408. https://doi.org/10.1016/j.apenergy.2020.116408.
- [3] Lewis AM, Kelly JC, Keoleian GA. Vehicle lightweighting vs. electrification: life cycle energy and GHG emissions results for diverse powertrain vehicles. Appl Energy 2014;126:13–20. https://doi.org/10.1016/j.apenergy.2014.03.023.
- [4] Kawajiri K, Kobayashi M, Sakamoto K. Lightweight materials equal lightweight greenhouse gas emissions?: A historical analysis of greenhouse gases of vehicle material substitution. J Cleaner Prod 2020;253:119805. https://doi.org/10.1016/ j.jclepro.2019.119805.
- [5] Herrmann C, Dewulf W, Hauschild M, Kaluza A, Kara S, Skerlos S. Life cycle engineering of lightweight structures. CIRP Ann 2018;67:651–72. https://doi.org/ 10.1016/j.cirp.2018.05.008.
- [6] Burd JTJ, Moore EA, Ezzat H, Kirchain R, Roth R. Improvements in electric vehicle battery technology influence vehicle lightweighting and material substitution decisions. Appl Energy 2021;283:116269. https://doi.org/10.1016/j. apenergy.2020.116269.
- [7] Ducker Worldwide. Aluminum content in North American light vehicles 2016 to 2028—Summary Report; 2017. https://transport.world-aluminium.org/modes/au tomotive/.
- [8] CM Group. Assessment of aluminum usage in china’s automobile industry 2016–2030; 2019. http://www.world-aluminium.org/media/filer_public/2019 /04/02/execsummary_china_auto_usage_2016-2030_21feb2019.pdf.
- [9] Fan Z, Yuan W, Wang D, Dong C, Yang H, Chen J. Research status and future development trend of die casting aluminum alloy (in Chinese). Foudry. 2020;68: 159–66. https://doi.org/10.3969/j.issn.1001-4977.2020.02.008.
- [10] Duckerfrontier. Aluminum content in European passsenger casrs; 2019. https: //www.european-aluminium.eu/media/2714/aluminum-content-in-european-ca rs_european-aluminium_public-summary_101019-1.pdf.
- [11] Cullen JM, Allwood JM. Mapping the global flow of aluminum: from liquid aluminum to end-use goods. Environ Sci Technol 2013;47:3057–64. https://doi. org/10.1021/es304256s.
- [12] Wang Z, Zhang X. Aluminum alloy for automobile usage (in Chinese). Light Alloy Fabricat Technol 2011;39:1–14. https://doi.org/10.3969/j.issn.1007- 7235.2011.02.001.
- [13] Cecchel S, Chindamo D, Collotta M, Cornacchia G, Panvini A, Tomasoni G, et al. Lightweighting in light commercial vehicles: cradle-to-grave life cycle assessment of a safety-relevant component. Int J Life Cycle Assess 2018;23:2043–54. https:// doi.org/10.1007/s11367-017-1433-5.
- [14] Neto B, Kroeze C, Hordijk L, Costa C. Modelling the environmental impact of an aluminium pressure die casting plant and options for control. Environ Modell Software 2008;23:147–68. https://doi.org/10.1016/j.envsoft.2007.05.005.
- [15] Neto B, Kroeze C, Hordijk L, Costa C. Inventory of pollution reduction options for an aluminium pressure die casting plant. Resour Conserv Recycl 2009;53:309–20. https://doi.org/10.1016/j.resconrec.2009.01.003.
- [16] Salonitis K, Jolly M, Pagone E, Papanikolaou M. Life-cycle and energy assessment of automotive component manufacturing: the dilemma between aluminum and cast iron. Energies 2019;12:2557. https://doi.org/10.3390/en12132557.
- [17] Salonitis K, Zeng B, Mehrabi HA, Jolly M. The challenges for energy efficient casting processes. Procedia CIRP 2016;40:24–9. https://doi.org/10.1016/j. procir.2016.01.043.
- [18] Brevick JR, Mount-Campbell CA, Mobley C. Energy consumption of die casting operations. The Ohio State University 2004. https://doi.org/10.2172/822409.
- [19] Rissman J, Bataille C, Masanet E, Aden N, Morrow WR, Zhou N, et al. Technologies and policies to decarbonize global industry: review and assessment of mitigation drivers through 2070. Appl Energy 2020;266:114848. https://doi.org/10.1016/j. apenergy.2020.114848.
- [20] Giampieri A, Ling-Chin J, Ma Z, Smallbone A, Roskilly AP. A review of the current automotive manufacturing practice from an energy perspective. Appl Energy 2020; 261:114074. https://doi.org/10.1016/j.apenergy.2019.114074.
- [21] Thollander P, Backlund S, Trianni A, Cagno E. Beyond barriers – A case study on driving forces for improved energy efficiency in the foundry industries in Finland, France, Germany, Italy, Poland, Spain, and Sweden. Appl Energy 2013;111: 636–43. https://doi.org/10.1016/j.apenergy.2013.05.036.
- [22] Haraldsson J, Johansson MT. Review of measures for improved energy efficiency in production-related processes in the aluminium industry – From electrolysis to recycling. Renew Sustain Energy Rev 2018;93:525–48. https://doi.org/10.1016/j. rser.2018.05.043.
- [23] Sun W, Wang Q, Zhou Y, Wu J. Material and energy flows of the iron and steel industry: status quo, challenges and perspectives. Appl Energy 2020;268:114946. https://doi.org/10.1016/j.apenergy.2020.114946.
- [24] Papetti A, Menghi R, Di Domizio G, Germani M, Marconi M. Resources value mapping: a method to assess the resource efficiency of manufacturing systems. Appl Energy 2019;249:326–42. https://doi.org/10.1016/j.apenergy.2019.04.158.
- [25] Roberts MJ, Hu EJ, Nahavandi S. A life cycle inventory of aluminium die casting. Macro Rev 2003;16:256–60. https://doi.org/10.11286/jmr1988.16.256.
- [26] Dalquist S, Gutowski T. Life cycle analysis of conventional manufacturing techniques: die casting. In: ASME 2004 International Mechanical Engineering Congress and Exposition. American Society of Mechanical Engineers; 2004. p. 631–41. http://web.mit.edu/ebm/Publications/Die%20Casting%20Dalquist% 20Gutowski.pdf.
- [27] Neto B. MIKADO: a decision support tool for pollution reduction in aluminium pressure die casting
- [Doctor]. Wageningen University; 2007.
- [28] Tharumarajah A. Benchmarking aluminium die casting operations. Resour Conserv Recycl 2008;52:1185–9. https://doi.org/10.1016/j.resconrec.2008.06.007.
- [29] Brevick JR, Mount-Campbell AF, Mount-Campbell CA, Horn AJ. Modeling alloy and energy utilization in high volume die casting. Clean Technol Environ Policy 2013;16:201–9. https://doi.org/10.1007/s10098-013-0604-8.
- [30] Heinemann T. Energy and resource efficiency in aluminium die casting: Springer; 2016. https://doi.org/10.1007/978-3-319-18815-7.
- [31] Gonçalves M, Jolly MR, Salonitis K, Pagone E. Resource efficiency analysis of high pressure die casting process. In: Martin O, editor. Light Metals 2018. Cham:Springer International Publishing; 2018. p. 1041–7. https://doi.org/10.1007/97 8-3-319-72284-9_136.
- [32] Uchida M. Development of vacuum die-casting process. China Foundry. 2009;6: 137–44. http://d.wanfangdata.com.cn/periodical/zhonggzz200902009.
- [33] Lu H. Current state of Chinese vehicle structural parts by die casting (in Chinese). 2017 Development Forum on Nonferrous Alloys and Special Casting. Shanghai 2017. p. 22. https://doi.org/10.26914/c.cnkihy.2017.007941.
- [34] Kapranos P. Current state of semi-solid net-shape die casting. Metals. 2019;9:1301. https://doi.org/10.3390/met9121301.
- [35] Pagone E, Salonitis K, Jolly M. Energy-efficient casting processes. In: Gupta K, editor. Innovations in manufacturing for sustainability: Springer Cham; 2019. p. 77–98. https://doi.org/10.1007/978-3-030-03276-0_4.
- [36] Sato FEK, Nakata T. Analysis of the impact of vehicle lightweighting on recycling benefits considering life cycle energy reductions. Resour Conserv Recycl 2021;164: 105118. https://doi.org/10.1016/j.resconrec.2020.105118.
- [37] Nunez P, Jones S. Cradle to gate: life cycle impact of primary aluminium production. Int J Life Cycle Assess 2016;21:1594–604. https://doi.org/10.1007/ s11367-015-1003-7.
- [38] Hao H, Geng Y, Hang W. GHG emissions from primary aluminum production in China: regional disparity and policy implications. Appl Energy 2016;166:264–72. https://doi.org/10.1016/j.apenergy.2015.05.056.
- [39] Liu W, Tang R, Peng T. An IoT-enabled approach for energy monitoring and analysis of die casting machines. Procedia CIRP. 2018;69:656–61. https://doi.org/ 10.1016/j.procir.2017.11.109.
- [40] Liu W, Peng T, Tang R, Umeda Y, Hu L. An Internet of Things-enabled model-based approach to improving the energy efficiency of aluminum die casting processes. Energy. 2020;202:117716. https://doi.org/10.1016/j.energy.2020.117716.
- [41] He K, Tang R, Jin M, Cao Y, Nimbalkar SU. Energy modeling and efficiency analysis of aluminum die-casting processes. Energ Effi 2018. https://doi.org/ 10.1007/s12053-018-9730-9.
- [42] Lu H, Lu M, Song Q, Wang Y. Die casting automobile structural components (in Chinese). Special Cast Nonferr Alloys. 2012;32:251–4. http://d.wanfangdata.com. cn/periodical/tzzzjyshj201203013.
- [43] World Steel Association. Life cycle inventory study of steel—2019 data release; 2020. https://www.worldsteel.org/zh/steel-by-topic/life-cycle-thinking.html.
- [44] World Steel Association. Sustainability indicators for the steel production. 2020. https://www.worldsteel.org/steel-by-topic/sustainability/sustainability-indicators .html.
- [45] Wang T. Calculation and analysis of energy consumption of al alloy melt preparation and supplying (in Chinese)
- [Master]: Chongqing University; 2015. htt p://www.wanfangdata.com.cn/details/detail.do?_type=degree&id=D684835.
- [46] Wang J. Numerical Simulation and optimization of melting process of a regenerative aluminum melting furnace (in Chinese)
- [Doctor]: Central South University; 2012. https://doi.org/10.7666/d.y2198497.
- [47] Das SK, King PE, Han Q, Saito K. Improving energy efficiency in aluminum melting. The University of Kentucky; 2007.
- [48] Li G, Lu H, Luo M, Qu W, Hu X, Zhu Q. Research progress in semi-solid rheoforming of aluminium alloys (in Chinese). J Netshape Form Eng 2020;12:29–48. http://d. wanfangdata.com.cn/periodical/jmcxgc202003004.
- [49] Li DQ, Zhang F, Midson SP, Liang XK, Yao H. Recent developments of rheo-diecast components for transportation markets. Solid State Phenom 2019;285:417–22. https://doi.org/10.4028/www.scientific.net/SSP.285.417.
- [50] Cot ˆ ´e P, Vlastimil B, Stunova ´ BB. Case study: engine bracket made by rheocasting using the SEED process. Solid State Phenom 2019;285:441–5. https://doi.org/ 10.4028/www.scientific.net/SSP.285.441.
- [51] Wannasin J, Fuchs M, Lee JY, Lee CU, Narasimha Rao TVL, Flemings MC. GISS technology: principle and applications in die casting. Solid State Phenom 2019; 285:470–5. https://doi.org/10.4028/www.scientific.net/SSP.285.470.
- [52] Jarfors AEW, Zheng JC, Chen L, Yang J. Recent advances in commercial application of the rheometal process in China and Europe. Solid State Phenom 2019;285:405–10. https://doi.org/10.4028/www.scientific.net/SSP.285.405.
- [53] Yurko JA, Martinez RA, Flemings MC. Commercial development of the semi-solid rheocasting (SSRTM) process. Metall Sci Technol 2003;21. https://www.fracturae. com/index.php/MST/article/view/1092.
- [54] Chen Y, Chen L, Sheng K. Production line of T6 solution and aging heat treatment for aluminum alloy (in Chinese). Heat Treat Technol Equip 2017;38:64–7. https:// doi.org/10.19382/j.cnki.1673-4971.2017.01.017.
- [55] Bonilla-Campos I, Nieto N, del Portillo-Valdes L, Egilegor B, Manzanedo J, Gaztanaga ˜ H. Energy efficiency assessment: process modelling and waste heat recovery analysis. Energy Convers Manage 2019;196:1180–92. https://doi.org/ 10.1016/j.enconman.2019.06.074.
- [56] Jiangsu Fengdong Thermal Technology Co. Ltd. Heat treatment of cast aluminium alloys. GB/T 25745-2010: General Administration of Quality Supervision, Inspection and Quarantine of the People’s Republic of China; Standardization Administration of the People’s Republic of China; 2010. p. 14. http://www. wanfangdata.com.cn/details/detail.do?_type=standards&id=GB/T 25745-2010.
- [57] Chen L, Chen Y, Sheng K. Solution-aging production line for aluminum alloy and its application (in Chinese). Heat Treatment. 2016;31:41–3. https://doi.org/10.3969/ j.issn.1008-1690.2016.06.014.
- [58] Chen E, Cao H, He Q, Yan J, Jafar S. An IoT based framework for energy monitoring and analysis of die casting workshop. Procedia CIRP. 2019;80:693–8. https://doi.org/10.1016/j.procir.2018.12.002.
- [59] Cecchel S, Cornacchia G, Panvini A. Cradle-to-gate impact assessment of a highpressure die-casting safety-relevant automotive component. Jom. 2016;68:2443–8. https://doi.org/10.1007/s11837-016-2046-3.
- [60] Chen L, Zhu D. Effects of solution treatment on microstructure and mechanical propertiesof high vacuum die-casting automobile shock absorption tower (in Chinese). Hot Work Technol 2020;49:107–10. http://dx.chinadoi.cn/10.14158/j. cnki.1001-3814.20192960.
9. Copyright:
This material is based on the paper by Weipeng Liu et al.: Critical life cycle inventory for aluminum die casting: A lightweight-vehicle manufacturing enabling technology.
Paper Source: https://doi.org/10.1016/j.apenergy.2021.117814
This material is a summary based on the above paper and is for informational purposes only. Unauthorized use for commercial purposes is prohibited.
Copyright © 2025 CASTMAN. All rights reserved.