This article introduces the paper ['Mold structure design and casting simulation of the high-pressure die casting for aluminum automotive clutch housing manufacturing'] presented at the ['Int J Adv Manuf Technol']
1. Overview:
- Title: Mold structure design and casting simulation of the high-pressure die casting for aluminum automotive clutch housing manufacturing
- Author: Seong Il Jeong, Chul Kyu Jin, Hyung Yoon Seo, Jong Deok Kim, Chung Gil Kang
- Publication Year: 2015
- Publishing Journal/Academic Society: Int J Adv Manuf Technol
- Keywords: High-pressure die casting, Mold structure, Casting simulation, Casting defects, Aluminum alloy
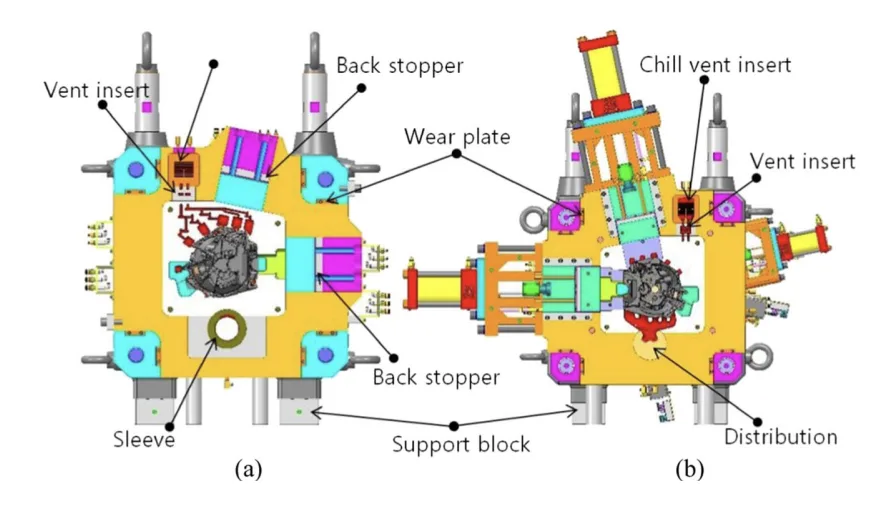
2. Research Background:
Background of the Research Topic:
The demand for aluminum die casting products has seen a continuous increase since Doehle's initial manufacturing efforts in 1915, particularly driven by the automotive industry's growth [1]. Among various aluminum automotive part casting methods, high-pressure die casting (HPDC), gravity die casting, and low-pressure die casting are prominent. While low-pressure and gravity die casting are suited for complex geometries like cylinder heads, HPDC is increasingly adopted for mass production of light-weighted automotive components, previously manufactured using low-pressure or gravity casting [2-7]. HPDC offers advantages in mass production of intricate and precise shapes within short cycle times, ranging from tens of seconds to 100–180 s.
Status of Existing Research:
Historically, die casting mold design relied on trial-and-error methods. Modern HPDC mold design leverages computer-aided engineering (CAE) to incorporate filling and solidification process simulations in the early design phase. This CAE-driven approach enables quality prediction and evaluation, leading to optimized mold designs [5, 8-10]. Current practices often integrate CAE with designers' practical experience to minimize defective parts, reduce costs, and accelerate development cycles. Furthermore, CAE's predictive capabilities extend to mold sticking and deformation, aiding in structural mold design.
Necessity of the Research:
This research addresses the critical need for robust mold designs in HPDC, especially for complex automotive components such as clutch housings. The study emphasizes the application of casting simulation to foresee and mitigate potential casting defects during the filling and solidification stages. It also aims to optimize gating system design and product geometry to achieve high-quality products with minimal defects, alongside structural simulation of the mold base to preemptively address potential mold damage and minimize experimental iterations, thereby reducing production costs and time.
3. Research Purpose and Research Questions:
Research Purpose:
This study aims to develop a mold design for manufacturing aluminum automotive clutch housing parts using high-pressure die casting. This is achieved through casting simulation and mold structural simulation to ensure efficient and defect-free production.
Key Research:
- Design of a gating system with five gates to ensure uniform melt flow into the mold and even filling of the product section.
- Prediction and prevention of potential casting defects during the filling and solidification processes using MAGMAsoft, a casting simulation program.
- Determination of appropriate casting devices for manufacturing clutch housing products.
- Structural simulation of the mold base using ANSYS Workbench to anticipate potential damage to vulnerable mold sections during the mold design phase.
Research Hypotheses:
While not explicitly stated as hypotheses, the research operates under the premise that:
- Simulation-driven mold design, incorporating both casting and structural analyses, will result in a robust mold capable of producing aluminum automotive clutch housings with minimal casting defects.
- Optimized gating system design and mold structure, informed by simulation results, will enhance product quality and reduce manufacturing costs and time.
4. Research Methodology
Research Design:
The research employs a simulation-based design methodology, integrating casting and structural simulations, followed by experimental validation through actual shot tests.
Data Collection Method:
- Casting Simulation: MAGMAsoft was utilized to simulate the filling and solidification processes, predicting potential casting defects.
- Structural Simulation: ANSYS Workbench was employed to conduct structural analysis of the mold base, predicting potential damage.
- Experimental Validation: Actual shot tests were performed, manufacturing five clutch housing products. Post-casting analysis included visual inspection for surface defects, shrinkage porosity assessment, and Vickers hardness measurement.
- Temperature Measurement: Mold temperature during pre-heating and casting was measured using a non-contact thermo-graphic camera.
Analysis Method:
- Simulation Analysis: Analysis of MAGMAsoft simulation results to optimize gating system and predict casting defects like shrinkage porosity. Analysis of ANSYS Workbench results to optimize mold base structure and ensure structural integrity.
- Experimental Data Analysis: Comparison of predicted shrinkage porosity locations from MAGMAsoft with actual porosity observed in shot test samples. Evaluation of surface quality of cast parts. Measurement and analysis of Vickers hardness across different locations of the clutch housing. Comparison of simulated mold temperature distribution with thermo-graphic measurements.
Research Subjects and Scope:
The research focuses on the mold design and manufacturing process for an aluminum automotive clutch housing produced via high-pressure die casting. The scope encompasses:
- Mold design for HPDC of an aluminum automotive clutch housing.
- Simulation of the casting process, including filling and solidification.
- Structural simulation of the mold base.
- Experimental validation through shot tests and post-casting analysis of the clutch housing product.
- Material: ALDC12 aluminum alloy for the clutch housing and GCD500 ductile iron for the mold base.
5. Main Research Results:
Key Research Results:
- Gating System Design: A five-gate gating system was successfully designed to facilitate even melt flow and complete filling of the clutch housing mold cavity (Fig. 1).
- Casting Simulation and Defect Prediction: MAGMAsoft simulations effectively predicted the potential for shrinkage porosity within the casting. The location of predicted shrinkage porosity showed a close correlation with the actual occurrence observed in manufactured parts.
- Mold Structural Simulation and Optimization: Structural simulation using ANSYS Workbench was crucial in optimizing the mold base thickness. It was determined that a 23 cm mold base thickness was sufficient and safe without requiring additional support (Fig. 7d).
- Shot Test Validation: Actual shot tests successfully produced five aluminum clutch housing parts. All parts were fully filled, exhibiting no surface defects. The hardness of the manufactured clutch housings was consistently measured at approximately 84 HV, irrespective of location.
- Temperature Distribution Analysis: Temperature measurements using a thermo-graphic camera showed reasonable agreement with the temperature distribution predicted by casting simulations (Fig. 15).
Data Interpretation:
The results demonstrate a strong correlation between simulation predictions and experimental outcomes. The casting simulation accurately identified potential shrinkage porosity areas, and the structural simulation effectively guided the optimization of mold base thickness. The successful shot tests, producing defect-free clutch housings, validate the effectiveness of the simulation-based mold design approach employed in this study. The consistent hardness values across the parts indicate process stability and product uniformity.
Figure Name List:
- Fig. 1 Gating system design of clutch housing
- Fig. 2 3D mold modeling: a fixed mold and b movable mold
- Fig. 3 Cooling line of mold
- Fig. 4 Locking force in each quadrant of movable mold
- Fig. 5 Shape condition of movable mold base for structural analysis
- Fig. 6 Molds assembled high-pressure die casting machine: a fixed mold and b movable mold
- Fig. 7 Results of structural analysis for movable mold base: a h=20 cm, b h=22 cm, c h=24 cm, and d h=23 cm
- Fig. 8 Filling behavior in mold cavity
- Fig. 9 Air pressure and air entrapment in mold cavity
- Fig. 10 Velocity distribution in mold cavity
- Fig. 11 Solidification behavior in mold cavity after filling finish
- Fig. 12 Shrinkage porosity after solidification finish
- Fig. 13 Mold soldering after solidification finish: a fixed mold and b movable mold
- Fig. 14 Temperature distribution of molds after pre-heating measured by thermo-graphic camera: a fixed mold and b movable mold
- Fig. 15 Comparison of mold temperature between simulation and real shot test: a simulation result and b real shot test
- Fig. 16 Fabricated clutch housing castings: a first shot, b second shot, c third shot, d fourth shot, and e fifth shot
- Fig. 17 Comparison of porosity distribution between simulation and real shot test
- Fig. 18 Microstructures of clutch housing in different positions: a normal thickness and b thick thickness
- Fig. 19 Vickers hardness at different positions
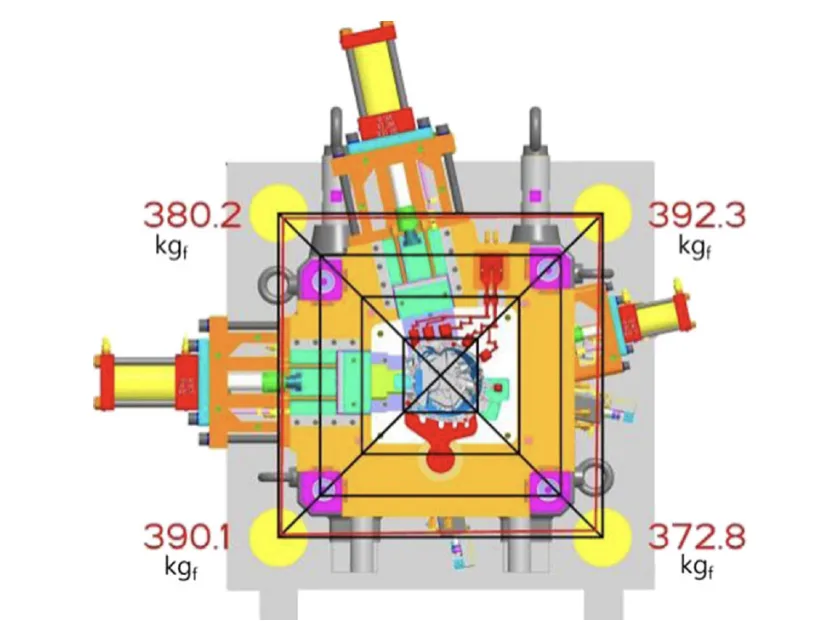
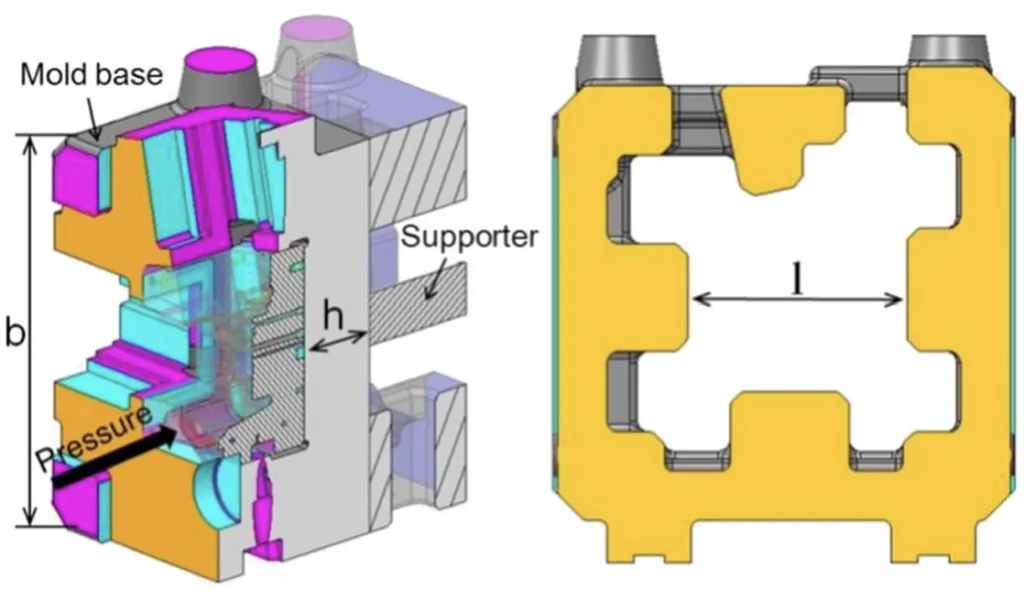
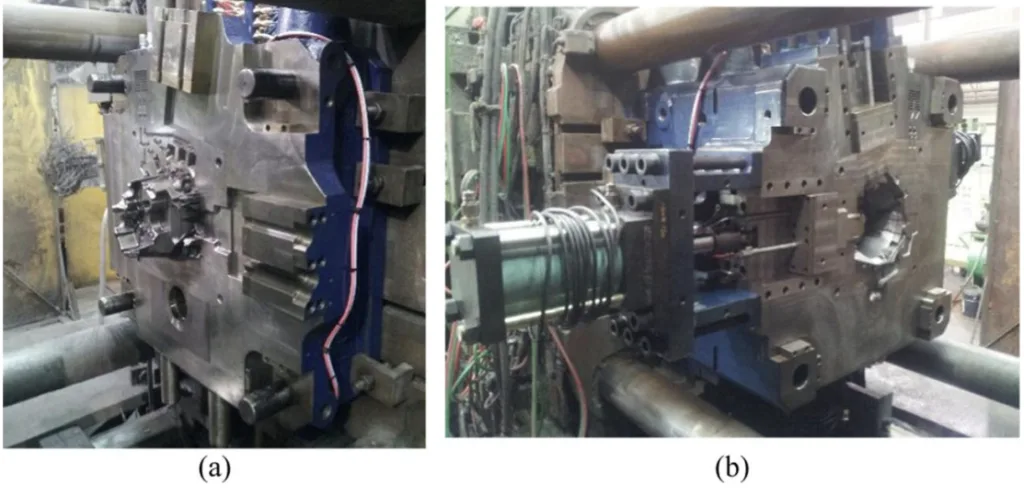
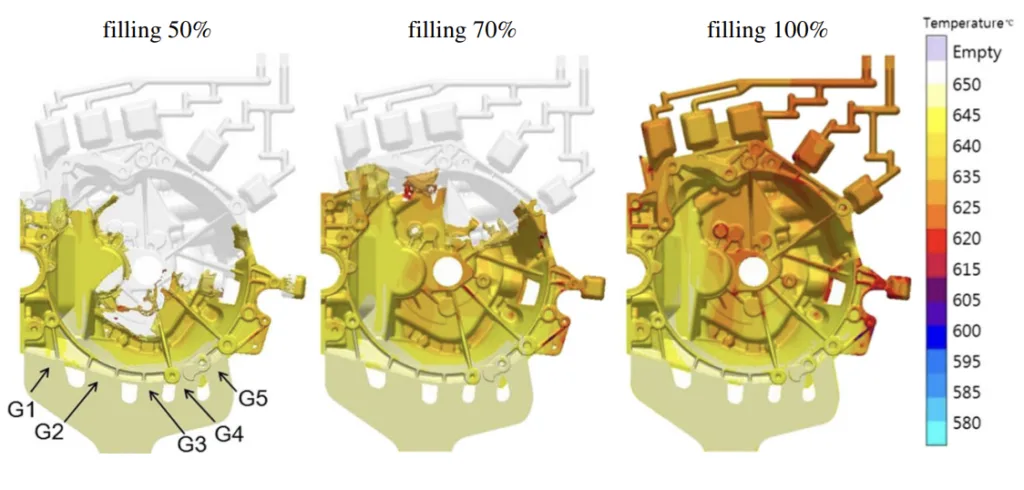
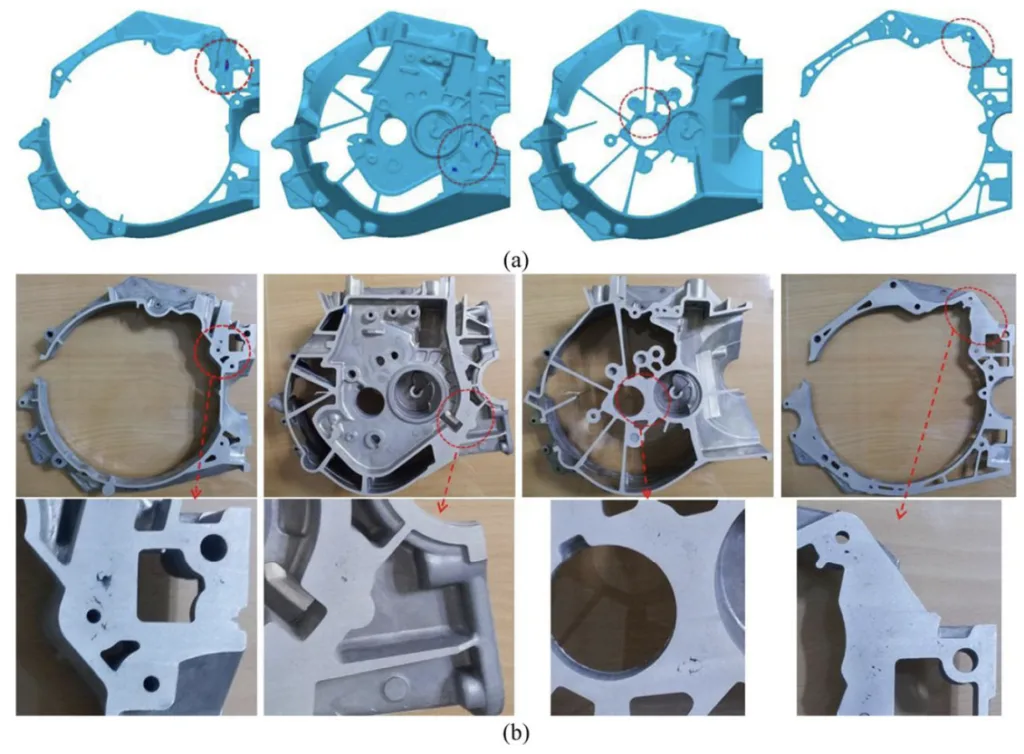
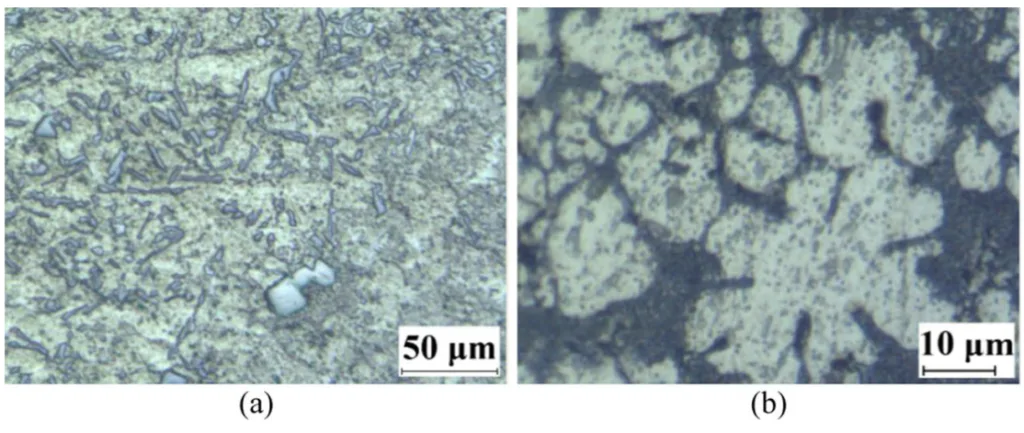
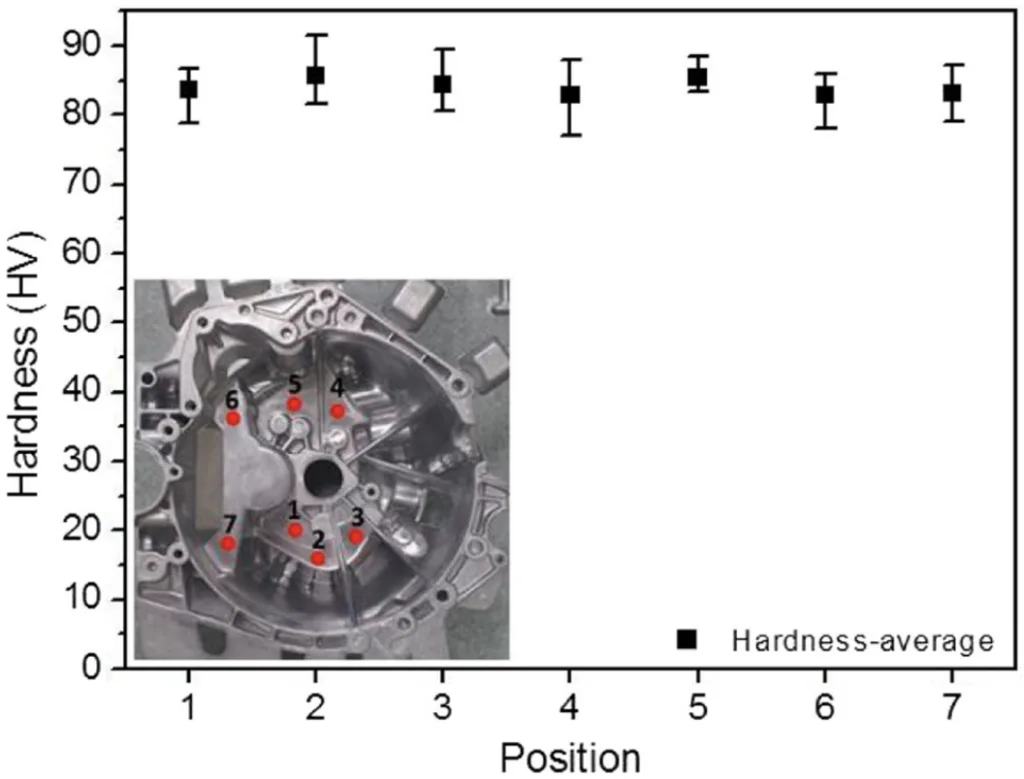
6. Conclusion:
Summary of Main Results:
This research successfully demonstrated a simulation-driven approach to mold design for high-pressure die casting of aluminum automotive clutch housings. By integrating casting and structural simulations using MAGMAsoft and ANSYS Workbench, respectively, the study optimized a five-gate gating system and a 23 cm thick mold base. Experimental validation through shot tests confirmed the simulation predictions, resulting in the production of defect-free clutch housings with consistent hardness.
Academic Significance of the Research:
This study underscores the academic significance of employing CAE tools in die casting mold design. It provides a detailed and validated methodology for designing molds for complex HPDC components. The research contributes to the body of knowledge concerning casting defect prediction, mold structural behavior under HPDC conditions, and the effectiveness of simulation-based optimization in manufacturing processes.
Practical Implications:
The practical implications of this research are substantial for the die casting industry. The presented methodology offers a pathway to design robust molds for intricate automotive parts, minimizing reliance on costly and time-consuming trial-and-error approaches. By leveraging casting and structural simulations, manufacturers can reduce production costs, shorten development cycles, and enhance the quality and reliability of HPDC components.
Limitations of the Research
The study's limitations include its focus on a single component (clutch housing) and material (ALDC12). While the methodology is robust, its direct generalizability to significantly different part geometries or alloy systems requires further investigation. Furthermore, while shrinkage porosity predictions were reasonably accurate, discrepancies between simulated and actual locations suggest potential areas for refinement in simulation models or the consideration of additional influencing factors in future research.
7. Future Follow-up Research:
- Directions for Follow-up Research
Future research should focus on refining the simulation models to enhance the accuracy of defect prediction, particularly concerning the precise location and extent of shrinkage porosity. Further investigation into the influence of various process parameters, such as injection speed profiles and cooling strategies, and material variations on casting quality is warranted. - Areas Requiring Further Exploration
Areas requiring further exploration include a more detailed analysis of mold erosion and die sticking phenomena, which were predicted but not extensively experimentally validated in this study. Applying the developed methodology to a broader range of complex HPDC parts and different aluminum alloys would further validate its versatility and industrial applicability.
8. References:
- [1] Doehler die-casting co (1916) Creating and industry. Brooklyn, New York
- [2] Jin CK, Bae JW, Kang CG (2014) Development of rheology vacuum low-pressure die casting with electromagnetic stirrer and vacuum system. Proc IMechE Part B J Eng Manuf 228(12):1599-1610
- [3] Zhang L, Wang R (2013) An intelligent system for low-pressure die-cast process parameters optimization. Int J Adv Manuf Technol 65:517-524
- [4] Hsu FY, Jolly MR, Campbell J (2009) A multiple-gate runner system for gravity casting. J Mater Process Technol 209:5736–5750
- [5] Jin CK, Kang CG (2011) Fabrication process analysis and experimental verification for aluminum bipolar plates in fuel cells by vacuum die-casting. J Power Sources 196:8241-8249
- [6] Kim ES, Lee KH, Moon YH (2000) A feasibility study of the partial squeeze and vacuum die casting process. J Mater Process Technol 105:42-48
- [7] Jin CK, Kang CG (2012) Fabrication by vacuum die casting and simulation of aluminum bipolar plates with micro-channels on both sides for proton exchange membrane (PEM) fuel cells. Int J Hydrog Energy 37:1661-1676
- [8] Chang QM, Chen CJ, Zhang SC, Schwam D, Wallace JF (2010) Effects of process parameters on quality of squeeze casting A356 alloy. Int J Cast Met Res 23:30-36
- [9] Hu BH, Tong KK, Niu XP, Pinwill I (2000) Design and optimisation of runner and gating systems for the die casting of thin-walled magnesium telecommunication parts through numerical simulation. J Mater Process Technol 105:128-133
- [10] Chen JH, Hwang WS, Wu CH, Lu SS (2011) Design of die casting process of top cover of automobile generator through numerical simulations and its experimental validation. Int J Cast Met Res 24:163-169
- [11] Jang JCH (1994) Casting plan of aluminum die castings. J Korean Foundry Soc 14(4):294-304
- [12] Kim ES, Lee KH (1998) High casting technology for aluminum alloy die casting (I). J Korean Foundry Soc 18(3):211-221
9. Copyright:
- This material is "Seong Il Jeong, Chul Kyu Jin, Hyung Yoon Seo, Jong Deok Kim, Chung Gil Kang"'s paper: Based on "Mold structure design and casting simulation of the high-pressure die casting for aluminum automotive clutch housing manufacturing".
- Paper Source: https://doi.org/10.1007/s00170-015-7566-4
This material was summarized based on the above paper, and unauthorized use for commercial purposes is prohibited.
Copyright © 2025 CASTMAN. All rights reserved.