Beyond the Simulation: What 'Short Shots' Reveal About Real-World HPDC Defects and Model Validation
This technical brief is based on the academic paper "Short shots and industrial case studies: Understanding fluid flow and solidification in high pressure die casting" by Paul W. Cleary, Joseph Ha, Mahesh Prakash, and Thang Nguyen, published in Applied Mathematical Modelling (2010). It is summarized and analyzed for HPDC professionals by the experts at STI C&D.
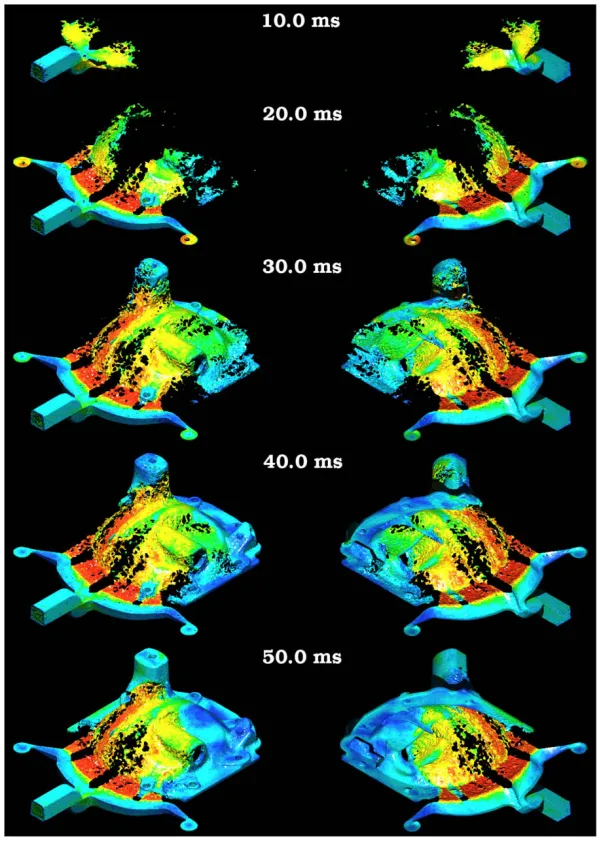
Keywords
- Primary Keyword: HPDC simulation validation
- Secondary Keywords: Smoothed Particle Hydrodynamics (SPH), short shot analysis, casting defects, fluid flow simulation, solidification modeling, porosity prediction
Executive Summary
- The Challenge: Accurately predicting and validating the complex, high-speed fluid flow in High-Pressure Die Casting (HPDC) is essential for minimizing defects like porosity, but the chaotic nature of the process makes this extremely difficult.
- The Method: The study utilizes Smoothed Particle Hydrodynamics (SPH), a grid-free simulation method, to model the filling of three industrial parts. Crucially, it uses experimental "short shots" (intentionally incomplete castings) to validate the simulation's flow and thermal predictions.
- The Key Breakthrough: While simulations captured the bulk filling process well, comparisons with short shots revealed a critical discrepancy in the initial moments of metal entry. The research hypothesizes that a solid metal/oxide skin forms and ruptures at the gate, a real-world phenomenon not captured in standard models, which significantly impacts early flow and defect formation.
- The Bottom Line: This research demonstrates that while SPH is a powerful predictive tool, achieving perfect simulation accuracy requires understanding and modeling complex surface physics. The use of short shots provides an invaluable, tangible link between the digital model and the physical reality on the foundry floor.
The Challenge: Why This Research Matters for HPDC Professionals
High-Pressure Die Casting (HPDC) is a cornerstone of modern manufacturing, enabling the high-volume production of complex metal components. However, the process is notoriously challenging to control. Injecting molten metal at speeds of 30–100 m/s into intricate die geometries creates a chaotic, three-dimensional flow with significant splashing and free-surface fragmentation. This turbulence is a primary cause of defects, particularly entrapped air that leads to porosity.
For engineers, predicting where and why these defects will form is critical for optimizing die design, gating systems, and venting. While numerical simulation offers a cost-effective way to study these flows, the central question remains: how accurate are the predictions? Validating a simulation against a finished part is difficult, as the final product hides the transient flow patterns that created the defects. This study tackles this validation challenge head-on, aiming to build greater confidence in simulation results and uncover deeper insights into the physics of die filling.
The Approach: Unpacking the Methodology
To investigate HPDC flows, the researchers employed a powerful, grid-free simulation technique called Smoothed Particle Hydrodynamics (SPH). Unlike traditional grid-based methods, SPH approximates the fluid with moving particles, which makes it exceptionally well-suited for modeling the complex, fragmenting free-surface flows characteristic of HPDC without artifacts like "stair-stepping" (Ref. [4, 5]).
The study was twofold:
- Industrial Case Studies: SPH was used to simulate the filling of three real-world components: an automotive differential cover, an electronic housing, and a zinc door lock plate. These isothermal simulations focused on predicting the order of fill and identifying likely regions for air entrapment and porosity.
- Short Shot Validation: To validate the simulation's predictive power, the researchers conducted experiments on a simple coaster casting. They created "short shots" by injecting an insufficient volume of metal, which then freezes in place, capturing a snapshot of the flow pattern. These physical short shots were then compared against SPH simulations that included fully coupled thermal and solidification models. The sensitivity of the results to key process parameters like metal super-heat and die temperature was also systematically investigated.
The Breakthrough: Key Findings & Data
The research yielded critical insights into both HPDC flow behavior and the limitations of current modeling techniques.
- Finding 1: Predicting Defect-Prone Flow Patterns: The industrial case studies (Figures 1, 2, and 3) consistently showed that SPH could predict complex flow phenomena. A common pattern observed was the metal jetting to the far side of the die, then flowing backward toward the gate. This "back filling" process often traps large volumes of air by blocking vents early in the fill, guaranteeing the formation of gas porosity. The simulations clearly identified the final regions to fill, which are the most likely locations for these defects.
- Finding 2: Bulk Flow Agreement in Short Shots: For larger fill volumes (25% and above), the SPH simulations showed good agreement with the experimental short shots (Figure 6). The model successfully predicted the overall shape and distribution of the frozen metal, confirming its ability to capture the dominant flow and thermal behavior during the bulk of the filling process.
- Finding 3: The "Skin Rupture" Hypothesis: A major discrepancy was observed in the 10% fill short shot (Figure 7). The experiment showed asymmetric, jet-like protrusions, while the simulation predicted a more uniform, symmetric flow. The researchers hypothesize this is caused by a phenomenon not included in the simulation:
- As the runner fills, a thin, solidifying metal/oxide skin forms across the narrow gate, temporarily holding back the molten metal.
- As pressure builds, this skin ruptures at its weakest points.
- High-speed jets of metal erupt through these random tears, creating the asymmetric flow seen in the experiment.
This suggests a stochastic, difficult-to-control element in the very first moments of die filling.
- Finding 4: Sensitivity to Thermal Conditions: The study confirmed that the final short shot shape is highly sensitive to initial conditions. Simulations showed that lower metal super-heat (Figure 8) and colder dies (Figure 9) significantly reduced fragmentation and spray, leading to smoother, more contiguous metal fronts. By comparing various simulations to the experiment, the researchers could estimate the most likely injection temperature used in the physical trial.
Practical Implications for Your HPDC Operations
The findings from this paper offer valuable, data-driven insights that can be applied directly to improve manufacturing outcomes.
- For Process Engineers: The simulations reveal that flow is often counter-intuitive, with significant "back filling" towards the gate. This highlights the critical importance of vent placement and timing. Understanding that vents can be blocked very early in the fill (as shown in the differential cover case study, Figure 1) allows for more strategic vent design to maximize air evacuation before it's too late. The study also suggests that the initial moments of injection are inherently variable, which could explain shot-to-shot inconsistencies that are otherwise difficult to diagnose.
- For Quality Control: The "skin rupture" hypothesis (Figure 7) provides a physical explanation for random, asymmetric defects or flow lines that may appear near the gate. This research suggests that such variability is not necessarily a failure of process control but may be an inherent feature of the physics at the gate, especially with thin gates and alloys prone to oxide formation.
- For Die Design: This study reinforces that gating and runner design are paramount. The SPH simulations (Figures 1, 2, 3) demonstrate how the gate geometry directly dictates the initial fragmentation and distribution of the fluid stream. The short shot analysis further implies that for parts requiring exceptional cosmetic finish or minimal near-gate turbulence, increasing gate thickness could be a strategy to mitigate the "skin formation and rupture" effect, although this must be balanced with other design considerations.
Paper Details
Short shots and industrial case studies: Understanding fluid flow and solidification in high pressure die casting
1. Overview:
- Title: Short shots and industrial case studies: Understanding fluid flow and solidification in high pressure die casting
- Author: Paul W. Cleary, Joseph Ha, Mahesh Prakash, Thang Nguyen
- Year of publication: 2010
- Journal/academic society of publication: Applied Mathematical Modelling
- Keywords: High pressure die casting, SPH, Solidification, Short shot, Fluid flow, Casting defects
2. Abstract:
The geometric complexity and high fluid speeds involved in high pressure die casting (HPDC) combine to give strongly three dimensional fluid flow with significant free surface fragmentation and splashing. A simulation method that has proved particularly suited to modelling HPDC is Smoothed Particle Hydrodynamics (SPH). Materials are approximated by particles that are free to move around rather than by fixed grids, enabling more accurate prediction of fluid flows involving complex free surface motion. Three practical industrial case studies of SPH simulated HPDC flows are presented; aluminium casting of a differential cover (automotive), an electronic housing and zinc casting of a door lock plate. These show significant detail in the fragmented fluid free surfaces and allow us to understand the predisposition to create defects such as porosity in the castings. The validation of flow predictions coupled with heat transfer and solidification is an important area for such modelling. One powerful approach is to use short shots, where insufficient metal is used in the casting or the casting shot is halted part way through, to leave the die cavity only partially filled. The frozen partial castings capture significant detail about the order of fill and the flow structures occurring during different stages of filling. Validation can occur by matching experimental and simulated short shots. Here we explore the effect of die temperature, metal super-heat and volume fill on the short shots for the casting of a simple coaster. The bulk features of the final solid castings are found to be in good agreement with the predictions, but the fine details appear to depend on surface behaviour of the solidifying metals. This potentially has significant implications for modelling HPDC.
3. Introduction:
HPDC is a critical manufacturing process for high-volume, low-cost components in industries like automotive and electronics. It involves injecting liquid metal at high speeds (30–100 m/s) into a die, resulting in highly three-dimensional and fragmented fluid flow. The order of fill and the placement of air vents are crucial for producing homogeneous parts with minimal porosity. Numerical simulation is a powerful tool for studying and optimizing die design and filling processes to improve product quality and productivity.
4. Summary of the study:
Background of the research topic:
The paper addresses the challenge of accurately modeling and validating simulations of HPDC processes. The high speeds and complex geometries lead to chaotic fluid flow with significant splashing, which is difficult to capture with traditional grid-based simulation methods. This makes predicting and mitigating defects like porosity a major industrial problem.
Status of previous research:
Several grid or mesh-based techniques (e.g., Flow3D, MagmaSoft, Fluent) have been used to simulate HPDC. However, these can suffer from issues like "stair-stepping" artifacts. Smoothed Particle Hydrodynamics (SPH) is presented as a Lagrangian (grid-free) method that is particularly effective for modeling the complex, splashing free-surface flows found in HPDC. Previous validation of SPH for casting has been mainly performed using water analogue experiments.
Purpose of the study:
This paper aims to achieve two goals:
- Demonstrate the use of SPH to predict the filling process and potential porosity distribution in three industrial-scale HPDC case studies.
- Explore the use of experimental "short shots" to validate SPH simulations that include both fluid flow and thermal/solidification models, and to study the effect of process parameters on the final casting shape.
Core study:
The core of the study involves two parts. First, isothermal SPH simulations are performed for an aluminum differential cover, an aluminum electronic housing, and a zinc door lock plate to analyze their filling patterns. Second, a detailed validation study is conducted using a simple coaster casting. Experimental short shots with varying fill volumes are created and compared to fully coupled thermal-flow SPH simulations. The researchers investigate how parameters like metal super-heat and initial die temperature influence the final frozen shape, and they analyze the discrepancies between simulation and experiment to uncover deeper physical insights.
5. Research Methodology
Research Design:
The research combines numerical simulation with physical experimentation. The simulation part uses the SPH method to model fluid flow, heat transfer, and solidification. The experimental part involves producing "short shots" by injecting a limited volume of aluminum into a die for a coaster part, effectively freezing the flow pattern at an intermediate stage.
Data Collection and Analysis Methods:
For the industrial case studies, the simulation results (visualizations of fluid flow over time) are analyzed to determine the order of fill, flow structures, and likely locations of trapped air. For the validation study, the physical short shot castings are photographed and visually compared to the final predicted shapes from the SPH simulations. A sensitivity analysis is performed by running simulations with a range of initial metal and die temperatures to find the best match with the experimental result.
Research Topics and Scope:
The scope includes:
- Isothermal SPH simulation of three complex industrial HPDC parts.
- Coupled thermal-flow SPH simulation of a simple coaster part.
- Experimental production of short shots for the coaster part.
- Validation of SPH simulations by comparing them against experimental short shots.
- Investigation of the effects of metal super-heat, initial die temperature, and fill volume on the short shot outcome.
6. Key Results:
Key Results:
- SPH simulations of industrial parts successfully predicted complex filling patterns, including back-filling and early vent blockage, which are precursors to porosity.
- For the coaster short shots, simulations showed good agreement with experiments for fill volumes of 25% or more, capturing the bulk features of the flow and solidification.
- A significant discrepancy was found at a low (10%) fill volume, where the experiment showed asymmetric jets not predicted by the standard simulation.
- This discrepancy led to the hypothesis that a solidifying metal/oxide skin forms and ruptures at the gate, a phenomenon that controls the very early, high-speed flow into the die cavity.
- The final shape of the short shot was shown to be sensitive to the metal's super-heat and the initial temperature of the die. Simulations indicated the most likely process temperature for the experiments was approximately 580 °C (a super-heat of -10 °C).
Figure Name List:
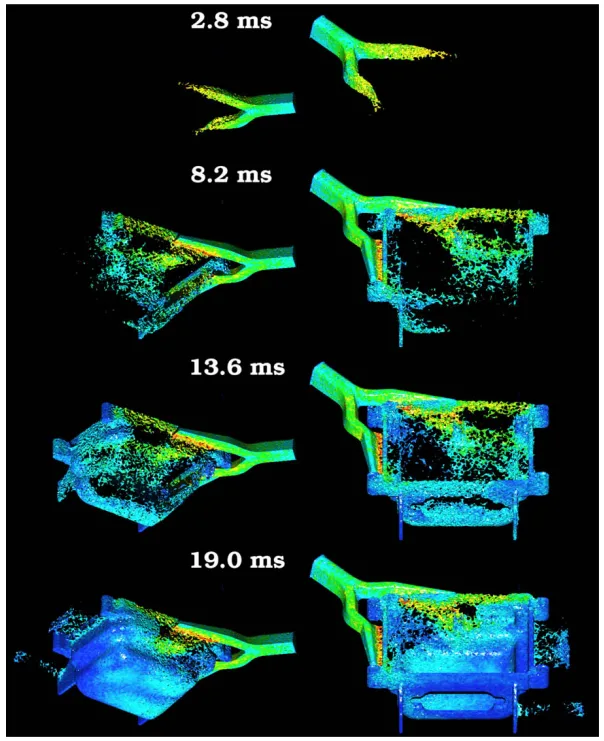
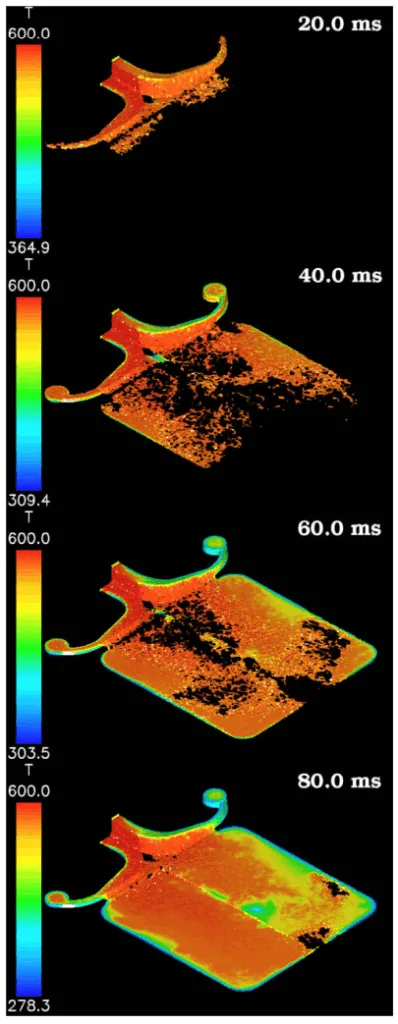
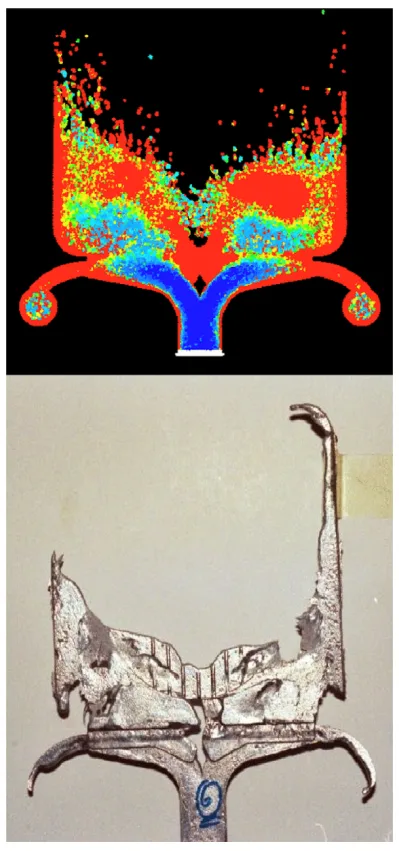
- Fig. 1. Filling of differential cover with the molten metal coloured by speed with blue being slow and red being fast. The casting is shown in top view on the left and bottom view on the right.
- Fig. 2. An electronic housing filled from a Y-shaped runner (coloured by speed).
- Fig. 3. Filling of the front and back plates of a zinc door lock (coloured by speed).
- Fig. 4. Variation of liquid aluminium properties with temperature; (a) viscosity and (b) enthalpy per unit mass.
- Fig. 5. Filling of coaster (including heat transfer and solidification) with fluid coloured by temperature.
- Fig. 6. Short shot with 25% volume fill: simulation (top) with colour representing viscosity, blue being low and red high; and experiment (bottom).
- Fig. 7. Short shot with 10% volume fill: simulation (top) and experiment (bottom).
- Fig. 8. Short shot variation for a 10% fill with different initial metal temperatures (degree of super-heat).
- Fig. 9. Short shot variation for a 10% fill for different initial die temperatures.
7. Conclusion:
The study concludes that SPH is a highly effective method for simulating the 3D filling of complex industrial components in HPDC, providing detailed insight into flow patterns and identifying likely locations for porosity. The validation process using experimental short shots proved to be a powerful tool. While simulations can capture the bulk flow and thermal behavior well, the research uncovered that the very early stages of filling are likely controlled by complex surface physics, specifically the formation and bursting of a solid/oxide skin at the gate. This introduces a stochastic element to the process and presents a significant challenge for both experimentalists and modelers, highlighting the need to incorporate these fine-scale surface effects into future simulation models to achieve even greater accuracy.
8. References:
- [1] T. Yoshimura, K. Yano, T. Fukui, S. Yamamoto, S. Nishido, M. Watanabe, Y. Nemoto, Optimum design of die casting plunger tip considering air entrainment, in: Proceedings of the 10th Asian Foundry Congress, Nagoya, Japan, 2008.
- [2] V. Kokot, P. Bernbeck, What is a good gating system? or Quantifying quality but how? Paper No.: 179041, in: Proceedings of the XX MCWASP Conference, France, 2006.
- [3] L.X. Kong, F.H. She, W.M. Gao, S. Nahavandi, P.D. Hodgson, Integrated optimisation system for high pressure die casting processes, J. Mater. Process. Technol. 201 (2008) 629-634.
- [4] J.J. Monaghan, Smoothed particle hydrodynamics, Ann. Rev. Astron. Astrophys. 30 (1992) 543-574.
- [5] J.J. Monaghan, Simulating free surface flows with SPH, J. Comput. Phys. 110 (1994) 399-406.
- [6] P.W. Cleary, M. Prakash, J. Ha, N. Stokes, C. Scott, Smooth particle hydrodynamics: status and future potential, Prog. Comput. Fluid Dynam. 7 (2007) 70-90.
- [7] P.W. Cleary, J.J. Monaghan, Conduction modelling using smoothed particle hydrodynamics, J. Comput. Phys. 148 (1999) 227-264.
- [8] P.W. Cleary, Modelling confined multi-material heat and mass flows using SPH, Appl. Math. Model. 22 (1998) 981-993.
- [9] W. Thorpe, P.W. Cleary, J. Ha, N. Stokes, V. Ahuja, M. Jahedi, Simulation of fluid flow within the die cavity in high pressure die casting using smooth particle hydrodynamics, in: Proceedings of the 20th International Die Casting Congress and Exposition, 1999, pp. 23-36.
- [10] P.W. Cleary, J. Ha, V. Ahuja, High pressure die casting simulation using smoothed particle hydrodynamics, Int. J. Cast Metal. Res. 12 (2000) 335-355.
- [11] P.W. Cleary, J. Ha, M. Prakash, T. Nguyen, 3D SPH flow predictions and validation for high pressure die casting of automotive components, Appl. Math. Model. 30 (2006) 1406-1427.
- [12] J. Ha, P.W. Cleary, Simulation of high pressure die filling of a moderately complex industrial object using Smoothed Particle Hydrodynamics, Int. J. Cast Metal. Res. 18 (2005) 81-92.
- [13] J. Ha, P.W. Cleary, Comparison of SPH simulations of high pressure die casting with the experiments and VOF simulations of Schmidt and Klein, Int. J. Cast Metal. Res. 12 (2000) 409-418.
- [14] J. Ha, P.W. Cleary, V. Alguine, T. Nguyen, Simulation of die filling in gravity die casting using SPH and MAGMAsoft, in: Proceedings of the Second International Conference on CFD in Minerals and Process Industries, Melbourne, Australia, 1999, pp. 423-428.
Conclusion & Next Steps
This research provides a valuable roadmap for enhancing the accuracy and utility of HPDC simulation. The findings offer a clear, data-driven path toward better understanding flow behavior, improving quality, reducing defects, and optimizing production.
STI C&D is committed to applying cutting-edge industry research to solve our customers’ most challenging technical problems. If the problem discussed in this white paper aligns with your research goals, please contact our engineering team to discuss how we can help you apply these advanced principles to your research.
Expert Q&A:
- Q1: Why is the Smoothed Particle Hydrodynamics (SPH) method particularly well-suited for simulating HPDC?
- A: According to the paper, SPH is a Lagrangian (grid-free) method where the material is approximated by particles that are free to move. This allows it to model the complex, fragmenting, and splashing free-surface flows common in HPDC more easily and naturally than traditional fixed-grid methods, avoiding issues like "stair-stepping" artifacts in the flow.
- Q2: What is a "short shot," and why is it a powerful tool for validating casting simulations?
- A: A short shot is a casting made with an insufficient amount of metal, so the die cavity is only partially filled. As stated in the abstract, "The frozen partial castings capture significant detail about the order of fill and the flow structures occurring during different stages of filling." This provides a physical "snapshot" of the transient flow that can be directly compared to simulation predictions, offering a more rigorous validation than just looking at the final part.
- Q3: The paper identifies a common flow pattern that leads to porosity. What is it?
- A: The simulations of industrial parts, such as the differential cover in Figure 1, show that fluid jets often travel rapidly to the opposite side of the die and then begin "back filling" toward the gate. This flow pattern can block the air vents early in the process, trapping large volumes of air that then cause porosity in the final casting.
- Q4: Why did the simulation for the 10% fill short shot not match the experiment perfectly?
- A: The paper hypothesizes that the discrepancy, seen in Figure 7, is due to surface physics not included in the model. It suggests that as the runner fills, a thin solid metal or oxide "skin" with mechanical strength forms at the narrow gate. As pressure builds, this skin ruptures at random weak points, causing high-speed, asymmetric jets of metal to erupt into the die, a phenomenon the standard fluid dynamics model does not account for.
- Q5: How do metal and die temperatures influence the filling process?
- A: The study shows these thermal conditions have a significant impact. The simulations in Figure 8 demonstrate that lower metal super-heat (i.e., closer to the liquidus temperature) reduces spray and fragmentation, resulting in a smoother metal front. Similarly, Figure 9 shows that a colder die also reduces spray and causes the metal to solidify closer to the gate. These factors strongly influence the final shape of the short shot and the potential for defects.
Copyright
Copyright © 2025 STI C&D. All rights reserved.
This material is an analysis of the paper "Short shots and industrial case studies: Understanding fluid flow and solidification in high pressure die casting" by Paul W. Cleary, Joseph Ha, Mahesh Prakash, and Thang Nguyen.
Source of the paper: doi:10.1016/j.apm.2009.10.015
This material is for informational purposes only. Unauthorized commercial use is prohibited.