A Three-Pronged Approach to Slashing Lead Times with Simulation, Rapid Tooling, and Collaboration
This technical brief is based on the academic paper "Rapid Casting Development" by B. Ravi, Dinesh Kumar Pal, and Nagahanumaiah, presented at the Rapid Manufacturing Seminar, TEAMTECH 2006. It is summarized and analyzed for casting professionals by the experts at CASTMAN.
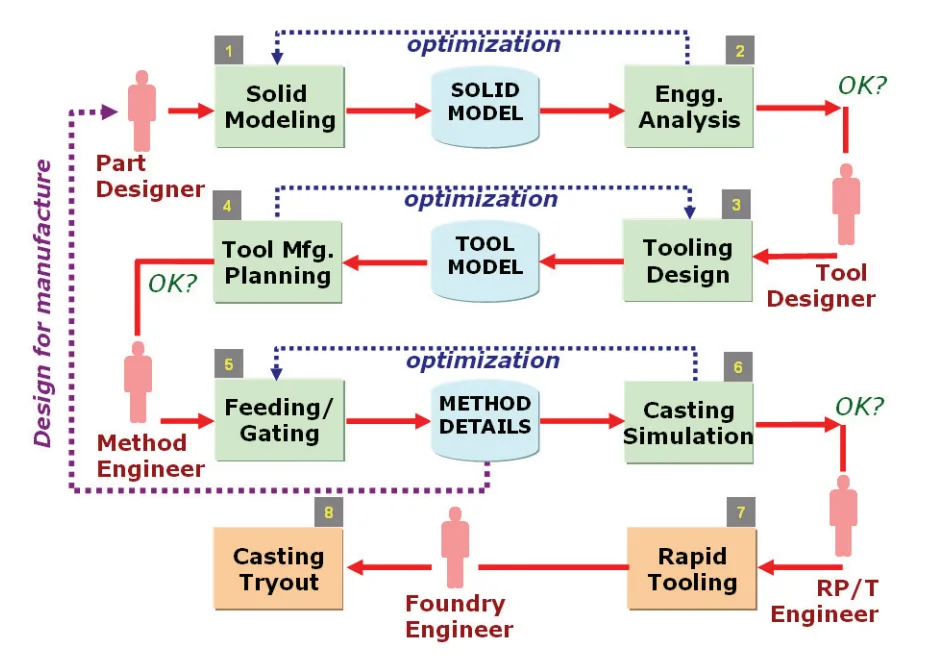
Keywords
- Primary Keyword: Rapid Casting Development
- Secondary Keywords: Casting Process Simulation, Rapid Tooling, Collaborative Engineering, Rapid Prototyping (RP), Casting Lead-Time Reduction, Casting Defect Prediction, AutoCAST
Executive Summary
- The Challenge: Traditional casting development, taking 8-12 weeks, is too slow for today's rapid product innovation cycles, where new components are needed in days, not months.
- The Method: The research integrates three key technologies: (1) Casting Process Simulation to optimize design and predict defects virtually, (2) Rapid Tooling (RT) using rapid prototyping to fabricate patterns quickly, and (3) Web-Based Collaborative Engineering to streamline communication between design, tooling, and foundry teams.
- The Key Breakthrough: Combining these three techniques significantly compresses the development lead-time. An industrial case study demonstrated a reduction in casting rejections from 35% down to less than 6% using simulation, while rapid tooling methods were shown to be faster and more cost-effective than conventional pattern making.
- The Bottom Line: This integrated approach enables the development of predictable, high-quality castings in a fraction of the traditional time, meeting the modern demands for speed, quality, and cost reduction.
The Challenge: Why This Research Matters for Casting Professionals
In an era where a new automobile can be developed in just 12-15 months, the casting industry faces immense pressure to deliver new components faster than ever. The traditional development cycle, often stretching over two months, is no longer acceptable. This lengthy timeline is primarily consumed by tooling development and multiple, costly shop-floor trials to resolve manufacturing defects.
As stated in the paper's introduction, the demand for shorter lead times is coupled with stricter requirements for quality assurance and cost reduction. Achieving all three simultaneously is impossible with conventional methods. This research directly addresses this critical industry bottleneck by presenting a systematic, technology-driven methodology to make casting development a matter of days, not weeks.
The Approach: Unpacking the Methodology
The researchers developed and validated a comprehensive framework for rapid casting development built on three pillars, as illustrated in Figure 1 of the paper.
- Process Simulation (Virtual Trials): The study utilized a software program, AutoCAST, to perform virtual casting trials. This allows engineers to optimize the "methoding" (the design of feeders and gating systems) and process parameters without pouring a single drop of metal. The software simulates mould filling and solidification to accurately predict and pinpoint potential defects like shrinkage porosity, cold shuts, and mould erosion (Ref. [3]).
- Rapid Tooling (Accelerated Pattern Making): The research benchmarked various Rapid Prototyping (RP) technologies—such as Fused Deposition Modeling (FDM), Stereolithography (SLA), and Layered Object Manufacturing (LOM)—for fabricating casting patterns directly from 3D CAD data. This bypasses the slow, manual process of creating conventional wooden or metal patterns. The study compared these routes on the basis of time, cost, and quality (Ref. [5]).
- Collaborative Engineering (Integrated Teamwork): A web-based framework called WebICE was developed to facilitate seamless project management and information exchange between product designers, tooling engineers, and foundry experts. Using a specialized data format (CastML), the system ensures all stakeholders are working with the latest information, enabling early identification and prevention of design-for-manufacturability issues (Ref. [7]).
The Breakthrough: Key Findings & Data
The paper provides compelling evidence that this integrated approach yields superior results in speed, cost, and quality.
- Finding 1: Simulation Drastically Reduces Defects: In an industrial case study of an aluminum-alloy switchgear tank, the initial rejection rate was 35% due to leakage from shrinkage porosity. As shown in Figure 3, simulation with AutoCAST accurately located the problem areas. A revised methoding design, validated by simulation, reduced the rejection rate to less than 6% without any additional shop-floor trials.
- Finding 2: Rapid Tooling is Faster and More Economical: The study compared the time and cost of producing an impeller pattern using various RP routes versus conventional methods. Table 2 clearly shows that several RP routes, such as FDM3 ($82.20) and TJP1 ($81.18), were significantly cheaper than a conventional wooden pattern ($200.00) and vastly more economical than a metal pattern ($450.00). The fabrication time was also reduced from days to hours.
- Finding 3: Hard Tooling is Feasible for Higher Volumes: The research explored Direct Metal Laser Sintering (DMLS) to create hard tooling inserts. As seen in Figure 5, a DMLS mold was successfully used to produce 5,000 polymer parts, demonstrating its utility for creating wax patterns for high-volume investment casting (Ref. [6]).
Practical Implications for Your Casting Operations
The findings from this paper offer actionable insights for modern foundries and OEMs.
- For Process Engineers: The simulation-driven approach detailed in the paper allows you to move from a "trial-and-error" methodology to a "predict-and-prevent" one. By using tools like AutoCAST to optimize feeder and gating systems virtually, you can significantly reduce scrap rates and eliminate entire rounds of costly physical trials.
- For Quality Control: The ability to predict the exact location and extent of shrinkage defects (as shown in Figure 3) provides a powerful tool for quality assurance. This allows for targeted inspection and provides data-driven confidence in the casting's integrity before it even reaches the testing phase.
- For Tooling and Design: The comprehensive benchmarking of RP technologies in Table 1 and Table 2 serves as a practical guide for selecting the most appropriate rapid tooling method for your specific project, balancing cost, speed, and material requirements. This enables the creation of prototype and small-batch tooling in days instead of weeks.
- For Project Management: The web-based collaboration model (Figure 6) highlights the importance of an integrated digital workflow. Implementing such a system can break down silos between departments, leading to better design-for-manufacturability, fewer late-stage changes, and a compressed overall project timeline.
Paper Details
Rapid Casting Development
1. Overview:
- Title: Rapid Casting Development
- Author: B. Ravi, Dinesh Kumar Pal, Nagahanumaiah
- Year of publication: 2006
- Journal/academic society of publication: Rapid Manufacturing Seminar, TEAMTECH 2006, Bangalore, Feb 28- Mar 2, 2006
- Keywords: Casting; Computer-Aided Design; Collaborative Engineering; Process Simulation; Rapid Prototyping (RP); Rapid Tooling (RT).
2. Abstract:
Rapid product innovation cycles prevalent today demand development of new castings in days instead of months. This is possible only by adopting new technologies and methodologies. We present three areas of our work contributing to rapid casting development: process simulation, rapid tooling and collaborative engineering. Casting process simulation enables optimising the methoding and process parameters without shop-floor trials. Several rapid prototyping-based routes are available today for casting pattern fabrication; and the most widely-used routes have been benchmarked for their impact on fabrication time, development cost, dimensional accuracy and surface quality. A web-based framework for exchange of casting project information between product, tooling and foundry engineers enables early identification of potential problems, and their prevention by more compatible product-process designs. The use of all three techniques significantly compresses the lead-time for developing a casting. The entire approach is illustrated through examples of industrial castings, and shown to be superior to the traditional approach in also achieving more predictable and consistent quality castings.
3. Introduction:
In the last century, developing a typical casting took 8-12 weeks, with over 70% of that time spent on tooling development and production trials. Modern OEMs, however, expect new castings in days. This demand for speed, along with needs for quality assurance and cost reduction, cannot be met by traditional methods. New technologies like CAD and simulation, and methodologies like collaborative engineering, are essential for modern casting development.
4. Summary of the study:
Background of the research topic:
The development of a new casting generally involves three phases: product design (at the OEM), tooling development (in a tool room), and casting production (in a foundry). While CAD is common for product design, the subsequent stages of methoding (designing feeders and gating), simulation, and tooling fabrication are often bottlenecks.
Status of previous research:
Commercial simulation software (e.g., Magma, Procast) exists but is often too expensive and complex for small and medium-sized foundries. Similarly, while rapid prototyping (RP) technologies are available, there is a need for clear benchmarking to guide their application in metal casting. Feedback loops between foundry, tooling, and design are often informal and inefficient, leading to preventable production problems.
Purpose of the study:
This work aims to address the lead-time bottleneck by developing and integrating three key areas:
- A user-friendly, semi-automatic software for casting methoding and simulation (AutoCAST).
- A techno-economic benchmark of widely used rapid prototyping routes for tooling (pattern) fabrication.
- A web-based framework for collaborative engineering to improve communication and information flow.
Core study:
The paper details the development and application of these three components. It describes the functions of the AutoCAST software for feeder design, gating design, and solidification/filling simulation. It presents a comparative study where an impeller pattern was fabricated using multiple RP techniques (SLA, FDM, LOM, etc.) and evaluated for time, cost, and other parameters. Finally, it outlines the architecture of the WebICE collaborative platform, which uses an XML-based format (CastML) to manage project data. The entire approach is illustrated with an industrial case study.
5. Research Methodology
Research Design:
The research was designed as a three-part investigation into the primary bottlenecks of casting development:
- Simulation: Development of a new simulation tool (AutoCAST) using the Vector Element Method and geometric reasoning, designed for ease of use in foundries.
- Rapid Tooling: An empirical benchmarking study. A single part (an impeller) was fabricated using nine different RP routes and two conventional methods. The outcomes (time, cost, material usage) were systematically compared.
- Collaboration: Development of a web-based software framework (WebICE) to demonstrate a new methodology for collaborative project management in casting.
Data Collection and Analysis Methods:
Data was collected through software development and validation, physical fabrication of RP patterns, and an industrial case study. For the RP study, fabrication time, machine cost, material cost, and part weight were recorded to calculate total costs (Table 2). For the simulation study, predicted defect locations were compared with actual results from an industrial casting (Figure 3).
Research Topics and Scope:
The research covers computer-aided casting development, focusing on sand and investment casting of ferrous and non-ferrous alloys. The scope includes:
- Semi-automatic methoding and simulation.
- Techno-economic analysis of RP-based tooling for patterns.
- Development of a web-based collaborative engineering platform.
6. Key Results:
Key Results:
- The AutoCAST simulation software successfully predicted shrinkage porosity in an industrial aluminum casting, enabling a methoding redesign that reduced rejections from 35% to under 6% (Figure 3).
- The rapid tooling benchmark showed that RP-based patterns can be produced significantly faster and at a lower cost than conventional wooden or metal patterns. For the test part, costs ranged from $81.18 (TJP1) to $178.08 (SLA1), compared to $200 for wood and $450 for metal (Table 2).
- Direct Metal Laser Sintering (DMLS) was demonstrated as a viable method for creating hard tooling inserts capable of producing thousands of parts, suitable for wax pattern injection molding (Figure 5).
- A functional web-based framework (WebICE) was created to manage casting project data, including 3D models, process plans, and simulation results, facilitating collaboration among distributed teams (Figure 6).
Figure Name List:
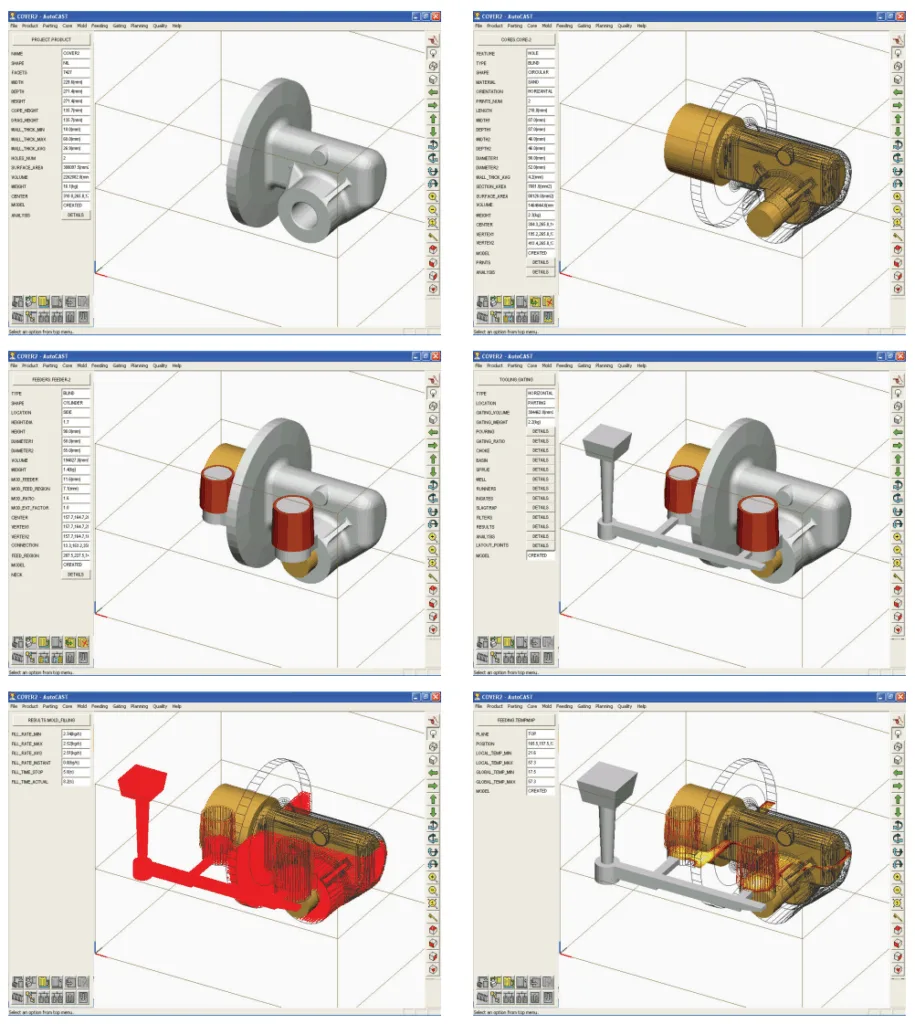
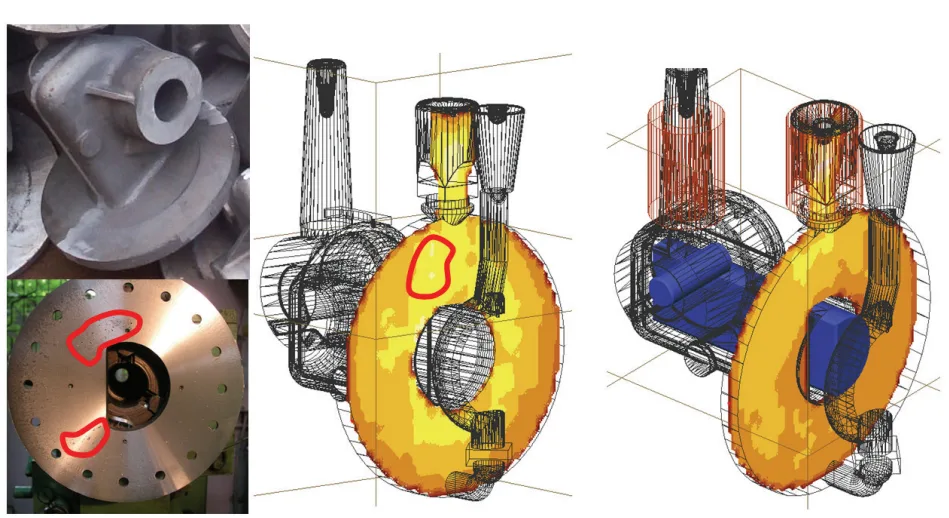
- Fig. 1 Computer-aided rapid casting development
- Fig. 2 Casting methoding and simulation program showing part model import, core design, feeding and gating design, and casting simulation
- Fig. 3 Troubleshooting and improvement of an aluminium-alloy casting
- Fig. 4. Fabrication of RP patterns by direct routes: (a) FDM1, (b) FDM2, (c) FDM3, (d) SLA1, (e) SLA2, (f) SLAQ1, (g) TJP1, (h) LOM1, and indirect route (i-k).
- Fig. 5: DMLS rapid hard mold along with PBT, LDPE and Nylon 66 moldings
- Fig. 6 Web-based framework for exchanging casting project data
7. Conclusion:
The bottlenecks in casting development can be eliminated by adopting CAD, simulation, rapid tooling, and web-based collaboration technologies. The authors successfully developed and demonstrated these technologies through academic projects and industrial applications. The integrated approach has been shown to not only reduce development lead-time to a few days but also to ensure quality and enable continuous cost reduction. The paper concludes that wide-scale deployment of these technologies requires better education of engineers and support from industry, professional bodies, and government agencies.
8. References:
- 1. B. Ravi, “Metal Casting – Back to Future," 52nd Indian Foundry Congress, Institute of Indian Foundrymen, Hyderabad, Feb 2004.
- 2. B. Ravi, R.C. Creese and D. Ramesh, “Design for Casting – A New Paradigm to Prevent Potential Problems," Transactions of the AFS, 107, 1999.
- 3. B. Ravi and M.N. Srinivasan, “Casting Solidification Analysis by Modulus Vector Method," International Cast Metals Journal, 9(1), 1-7, 1996.
- 4. B. Ravi, “Intelligent Design of Gating Channels for Casting,” Materials Science and Technology, 13(9), 785-790, 1997.
- 5. D.K. Pal, B. Ravi, L.S. Bhargava and U. Chandrasekhar, “Rapid Casting Development using Reverse Engineering, Rapid Prototyping and Process Simulation,” Indian Foundry Journal, 53(4), 23-34, 2005.
- 6. Nagahanumaiah, B. Ravi and N.P. Mukherjee, “Rapid Hard Tooling Process Selection using QFD-AHP Methodology,” Journal of Manufacturing Technology Management, 17(6), 2005.
- 7. M.M. Akarte and B. Ravi, “Casting Data Markup Language for Web-based Collaborative Engineering," Transactions of the AFS, 110, 93-108, 2002.
- 8. R.G. Chougule and B. Ravi, “Casting Cost Estimation in an Integrated Product and Process Design Environment,” International Journal of Computer Integrated Manufacturing, in press.
Conclusion & Next Steps
This research provides a valuable roadmap for enhancing casting development. The findings offer a clear, data-driven path toward improving quality, reducing defects, and optimizing production by integrating simulation, rapid tooling, and collaboration.
CASTMAN is committed to applying cutting-edge industry research to solve our customers’ most challenging technical problems. If the problem discussed in this white paper aligns with your research goals, please contact our engineering team to discuss how we can help you apply these advanced principles to your research.
Expert Q&A:
- Q1: What are the three main techniques proposed for rapid casting development?
- A: The paper proposes a three-pronged approach: (1) Casting Process Simulation to optimize methoding and predict defects without physical trials; (2) Rapid Tooling (RT), which uses Rapid Prototyping (RP) to quickly fabricate casting patterns; and (3) Web-Based Collaborative Engineering to facilitate information exchange and teamwork between designers, toolmakers, and foundry engineers. This integrated approach is detailed in the "Rapid Casting Development" paper.
- Q2: How does casting process simulation help reduce lead time and improve quality?
- A: According to the paper, process simulation enables the optimization of methoding (feeder and gating design) and process parameters in a virtual environment. This allows engineers to detect and eliminate potential defects like shrinkage porosity before any metal is poured, thus avoiding time-consuming and costly shop-floor trials. The industrial case study in Figure 3 shows this in practice, where simulation helped reduce casting rejections from 35% to less than 6%.
- Q3: What is "Rapid Tooling" and how does it compare to conventional methods in this study?
- A: In the context of this paper, "Rapid Tooling" refers to using Rapid Prototyping (RP) techniques like FDM, SLA, and LOM to directly fabricate casting patterns from 3D CAD data. The study's comparison in Table 2 shows that several RP routes are significantly faster and more cost-effective than traditional methods. For example, the FDM3 and TJP1 routes produced a pattern for around $82, whereas a conventional wooden pattern cost $200 and a metal one cost $450.
- Q4: Can Rapid Prototyping (RP) be used for hard tooling for higher volume casting?
- A: Yes. The paper explores this by using Direct Metal Laser Sintering (DMLS) to fabricate hard tool cavity inserts from a Cu-Ni-Sn based alloy powder. This DMLS mold, shown in Figure 5, was successfully used to produce 5,000 polymer parts. The paper suggests this method is "certainly useful for injection molding of wax patterns for investment casting," making it a viable route for higher volume production (Ref. [6]).
- Q5: What is the purpose of the web-based collaborative engineering framework mentioned in the paper?
- A: The framework, named WebICE, was developed to facilitate collaboration among the casting development team members (product, tooling, and foundry engineers) who may be in different locations. As described in the paper and shown in Figure 6, it uses a specific data format (CastML) to store and exchange all project information, including 3D models and process plans. This enables early identification of potential problems and fosters the creation of more compatible product-process designs, ultimately saving time and cost (Ref. [7]).
Copyright
- This material is an analysis of the paper "Rapid Casting Development" by B. Ravi, D. K. Pal, and Nagahanumaiah.
- Source of the paper: https://www.researchgate.net/publication/268290249
- This material is for informational purposes only. Unauthorized commercial use is prohibited.
- Copyright © 2025 CASTMAN. All rights reserved.