SHOT SLEEVE WITH INTEGRAL THERMAL REGULATION
How Integral Thermal Control Extends Service Life by Over 15x and Boosts Casting Quality
This technical brief is based on the academic paper "SHOT SLEEVE WITH INTEGRAL THERMAL REGULATION" by F. Miglierina (Omnia Press S.r.l.) and B. Vianello (Zanussi Metallurgica S.p.a.), published in the 6th International Tooling Conference. It is summarized and analyzed for HPDC professionals by the experts at CASTMAN.
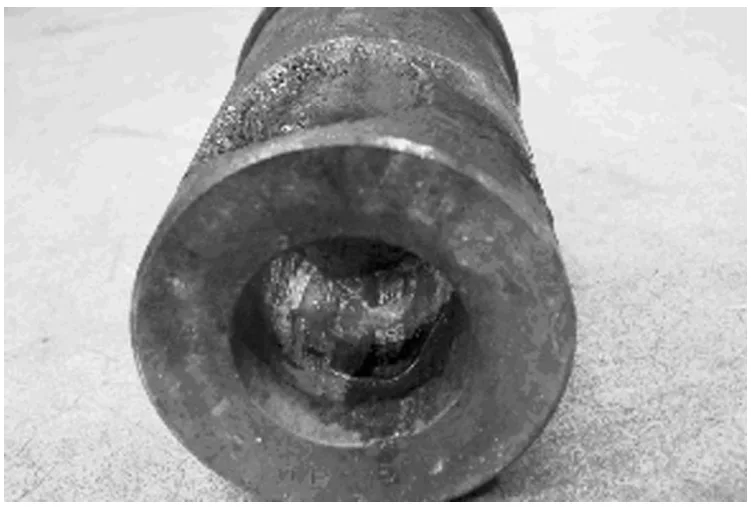
Keywords
- Primary Keyword: Shot Sleeve Thermal Regulation
- Secondary Keywords: HPDC shot sleeve life, Die casting thermal fatigue, Shot sleeve wear, Nipre Duplex treatment, Integral cooling circuit, Aluminum die casting, Large shot sleeve design
Executive Summary
- The Challenge: Standard shot sleeves in high-tonnage die casting suffer from extreme thermal shocks, leading to deformation (bending, ovalization), cracking, and rapid wear. This results in short service life (as few as 1,500 injections), poor casting quality, and costly downtime.
- The Method: Researchers designed, built, and tested a 980 mm shot sleeve featuring an integral, full-length oil thermal regulation circuit. The sleeve was manufactured from UNI 30CrMoV1227KU steel, hardened in a salt bath, and given a patented Nipre® Duplex surface treatment.
- The Key Breakthrough: The integral thermal regulation maintained a uniform and stable temperature across the entire sleeve surface. This eliminated the bending and ovalization effects that plague standard sleeves, drastically reducing thermal and mechanical stress.
- The Bottom Line: The thermoregulated shot sleeve achieved an operational life of 77,530 injections before being decommissioned—a more than 15-fold improvement over standard sleeves that fail after 5,000 injections. This technology offers a clear path to reducing tooling costs, minimizing downtime, and improving the quality of large die-cast parts.
The Challenge: Why This Research Matters for HPDC Professionals
In modern die casting, the push for larger, more complex parts at lower costs puts immense strain on press components. The shot sleeve, a critical part of the injection group, is at the epicenter of this stress. Every cycle, it endures a violent thermal shock as molten aluminum (around 700°C) is poured in, followed by intense mechanical forces during injection.
As detailed in the paper, this continuous cycle of extreme heating and cooling leads to two primary failure modes:
1. Thermal Fatigue: The rapid temperature changes cause the steel to lose its resistance, leading to the formation of thermal cracks ("web cracks") and fissures on the surface.
2. Mechanical Wear: The piston's abrasion, combined with freely moving silica particles in the aluminum alloy, causes severe erosion, especially in the material dropping area.
This often results in a hole forming in the sleeve, rapid piston wear, and potential seizures (Ref. [2]). Furthermore, the massive temperature difference between the bottom of the sleeve (in contact with molten metal) and the top causes significant deformation—the sleeve bends and the hole becomes oval-shaped (Figure 2, Figure 3). This distortion compromises the injection process, leading to inconsistent quality and a drastically shortened tool life.
The Approach: Unpacking the Methodology
To combat these challenges, the researchers from Omnia Press and Zanussi Metallurgica took a holistic, four-pronged approach to redesign the shot sleeve from the ground up.
- Advanced Steel Choice: They selected UNI 30CrMoV1227KU (similar to H10), a Cr-Mo-V tool steel with high mechanical resistance, toughness, and excellent resistance to thermal oscillations at high temperatures (Page 8).
- Specialized Hardening Treatment: The sleeve underwent a multi-stage hardening and tempering process in a salt bath. This method provides superior cooling homogeneity compared to gas quenching, minimizing distortion and achieving the desired HRC 47-49 hardness with a tough tempered martensite structure (Page 11).
- Patented Superficial Treatment: The sleeve was treated with Nipre® Duplex, a patented process combining ionic nitriding with a 4-5 micron magnetite layer. The nitriding creates a hard (1050 Hv), wear-resistant surface, while the magnetite layer acts as a chemical barrier, preventing metallization and corrosion from the liquid aluminum (Page 11, 13).
- Innovative Engineering Modification: The core innovation was an integral thermal regulation circuit running along the entire 900 mm length of the sleeve. This 12-hole circuit, with a total development of 10.8 meters, uses diathermic oil to maintain a constant, uniform temperature across the whole sleeve, effectively eliminating the thermal gradients that cause deformation (Page 17).
This engineered sleeve was then tested in a real-world production environment on a 2000-ton press, casting a 21 kg aluminum part.
The Breakthrough: Key Findings & Data
The production trial delivered clear, quantifiable results demonstrating the superiority of the thermoregulated design.
- Finding 1: Uniform Temperature Distribution: In the exercise phase, the thermoregulated sleeve maintained a temperature difference of only ~20°C between its hottest and coolest points. In contrast, a non-thermoregulated sleeve under similar conditions would exhibit a temperature difference exceeding 100°C (Figure 22).
- Finding 2: Elimination of Deformation: By maintaining a uniform temperature, the bending and ovalization effects were "practically removed" (Page 17). This ensures the injection piston slides into a perfectly cylindrical hole, improving plunger life and injection consistency. The theoretical bending of the thermoregulated sleeve was calculated to be 0.62 mm, significantly less than what would occur in an unregulated sleeve (Table 1).
- Finding 3: Massively Extended Service Life: The wear phenomena on standard sleeves (erosion) appeared after just 1,500 injections, leading to failure around 5,000 injections. On the thermoregulated sleeve, the first signs of light pitting did not appear until 9,500 injections, and the sleeve went on to achieve 77,530 injections before being taken out of service (Page 23).
- Finding 4: Controlled Wear Progression: The evolution of wear was gradual and predictable. Even after 77,530 injections, the failure was not due to catastrophic wear but to a passing crack near the collar, demonstrating the core integrity of the sleeve's working surface (Figure 23).
Practical Implications for Your HPDC Operations
This research is not just academic; it provides a clear, evidence-based strategy for improving large-scale die casting operations.
- For Process Engineers: The stable and uniform temperature of the shot sleeve, as shown in Figure 22, translates directly to a more stable and repeatable injection process. This allows for tighter control over injection speed and pressure, leading to more consistent part quality shot after shot.
- For Quality Control & Maintenance: The elimination of sleeve bending and ovalization (Page 17) reduces wear on injection plungers, decreases the likelihood of flash, and minimizes costly unscheduled downtime for sleeve and plunger replacement. The paper concludes this allows for a "drastic reduction in costs" (Page 23).
- For Die Design & Procurement: This study proves that investing in advanced, integrally thermoregulated shot sleeves provides a significant return. It offers a "standardization about the integral thermoregulated big shot sleeve" (Page 24), moving it from a custom solution to a reliable, high-performance component for any demanding HPDC application.
Paper Details
SHOT SLEEVE WITH INTEGRAL THERMAL REGULATION
1. Overview:
- Title: SHOT SLEEVE WITH INTEGRAL THERMAL REGULATION
- Author: F. Miglierina, B. Vianello
- Year of publication: [Not specified in document]
- Journal/academic society of publication: 6TH INTERNATIONAL TOOLING CONFERENCE
- Keywords: Die-casting technique, injection group, shot sleeve, aluminum;
2. Abstract:
The modern die-casting technique is mainly focused on processing more complex and bigger pieces maintaining a high quality level and very low costs. This aim can be achieved by producing, with the use of faster and faster die forming cycles, aluminum alloy die-cast pieces weighing more than 20 kilos and by improving the life of the press mechanical parts, such as the shot sleeves. The company Zanussi Metallurgica decided to equip a horizontal die-casting machine featured by a 2000-ton cold room and a 21-kilo aluminum dying capacity with a shot sleeve (length: 980 mm, hole diameter: 140 mm) supplied with an Omnia Press integral thermal regulation circuit made of warm processed steel, hardened in a salt bath and with a surface covered with Nipre® Duplex. Thanks to the user care and to the special design, the shot sleeve could reach 80,000 injections at the end of the working cycle. The aim of this report is to introduce those technical solutions which brought to this successful conditions and to suggest shot sleeves with a long life granting a constant casting quality.
3. Introduction:
The paper begins by highlighting a disparity in HPDC research: while significant advancements have been made in die-casting molds, the shot sleeve and injection group have often been overlooked. The authors state that the reliability and, above all, the life of a shot sleeve are fundamental to obtaining high-quality, low-cost die-cast parts. The introduction identifies the two main reasons for sleeve deterioration: thermal fatigue from repeated thermal shocks and mechanical wear from the piston and molten aluminum. These issues lead to common failures like holes in the dropping area, thermal cracks, and deformation, which compromise the entire casting process.
4. Summary of the study:
Background of the research topic:
The research is set against the backdrop of modern die casting, which demands the production of large, complex aluminum parts with high quality and low cost. This requires faster cycle times and improved longevity of critical press components like the shot sleeve. The paper establishes that a standard, un-regulated shot sleeve is highly susceptible to thermal and mechanical stresses that cause severe deformation (ovalization and bending) and premature failure. The temperature difference between the lower section (touching molten metal at ~600°C) and the upper section can be hundreds of degrees, causing significant distortion and stress.
Status of previous research:
The paper acknowledges existing methods for controlling shot sleeve temperature, such as external copper plates, water-cooled jackets, and partial oil-regulated circuits in the lower section (Page 14-15). However, it implicitly critiques these as incomplete solutions, noting they do not fully address the deformation (bending and ovalization) caused by the temperature difference between the upper and lower sections of the sleeve.
Purpose of the study:
The aim of the report is to introduce the technical solutions that led to a highly successful, long-life shot sleeve and to suggest this design for achieving constant casting quality. The study sought to prove that a holistic approach—combining advanced material, specific thermal treatments, and an innovative integral thermal regulation system—could overcome the traditional limitations of shot sleeves in high-tonnage applications.
Core study:
The core of the study involved designing, manufacturing, and implementing a shot sleeve with an integral, full-length thermal regulation circuit. This sleeve was installed on a 2000-ton die-casting press for a real-world production run of a 21 kg aluminum casting. The researchers meticulously documented the entire process, including the pre-heating ramps, the temperature profiles during operation (Figure 22), and the evolution of wear over its entire service life (Figure 23). This empirical data was then compared to the theoretical behavior and known failure modes of standard shot sleeves.
5. Research Methodology
Research Design:
The research was an applied case study. A shot sleeve was designed with specific technical solutions and then tested in a live industrial production environment. The key design choices were:
1. Material: UNI 30CrMoV1227KU steel.
2. Hardening: A specific multi-step salt bath hardening and tempering cycle to achieve HRC 47-49.
3. Surface Treatment: A patented Nipre® Duplex treatment (ionic nitriding + magnetite layer).
4. Engineering: An integral 12-hole thermal regulation circuit running the length of the sleeve, controlled by an 18 kW oil temperature control unit.
Data Collection and Analysis Methods:
Temperatures were measured using an infrared thermometer with laser laying and a contact electronic thermometer with a K-type thermocouple. The sleeve's condition was visually inspected and documented with photographs at various stages of its life (9,500, 21,000, 58,000, and 77,530 injections). After decommissioning, a microstructure analysis was performed on a sample from the material fall area to assess the condition of the steel and the nitrided layer.
Research Topics and Scope:
The research focused on a single, large-scale application: a 140 mm diameter, 980 mm long shot sleeve used on a 2000-ton cold chamber press to cast a 21 kg aluminum (EN AC-46000) part. The study scope covered the sleeve's entire lifecycle, from manufacturing and initial pre-heating to production use and final analysis.
6. Key Results:
Key Results:
The use of the thermoregulated shot sleeve resulted in a dramatic improvement in performance and lifespan.
- The integral thermal regulation successfully maintained a uniform temperature across the sleeve, with a measured thermal profile showing minimal variation between the top, bottom, and sides (Figure 22). This effectively eliminated the bending and ovalization common in standard sleeves.
- The first signs of wear (light pitting) did not appear until 9,500 injections. In contrast, sleeves without thermoregulation show erosion after only 1,500 injections (Page 23).
- The shot sleeve achieved a total service life of 77,530 injections. It was taken out of commission not due to wear degeneracy in the main bore, but due to a passing crack near the collar (Page 23).
- Microstructure analysis after 77,530 injections showed the nitrided zone was still present at a thickness of 0.4 mm, though the outer magnetite layer was no longer found (Page 23, Figure 24).
Figure Name List:
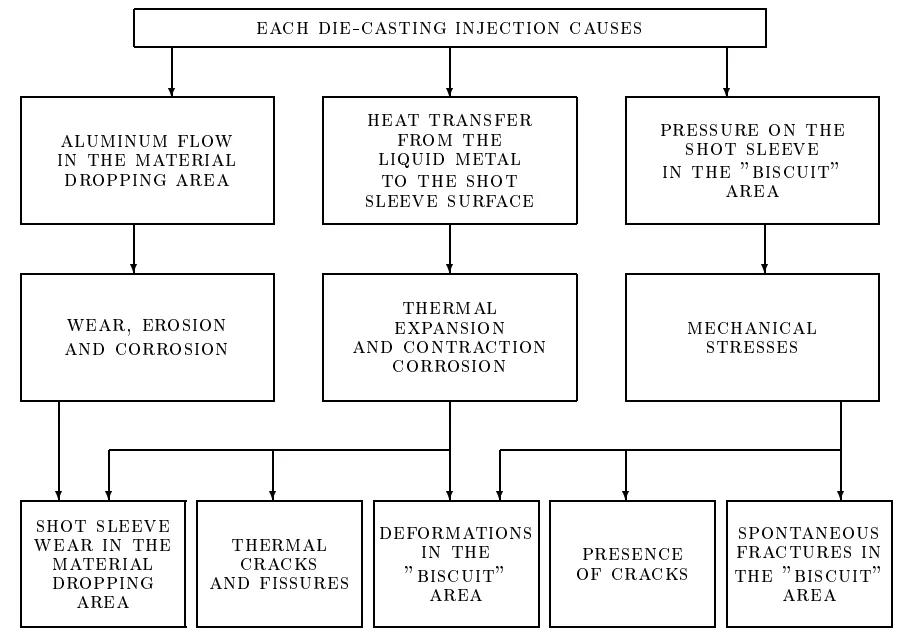
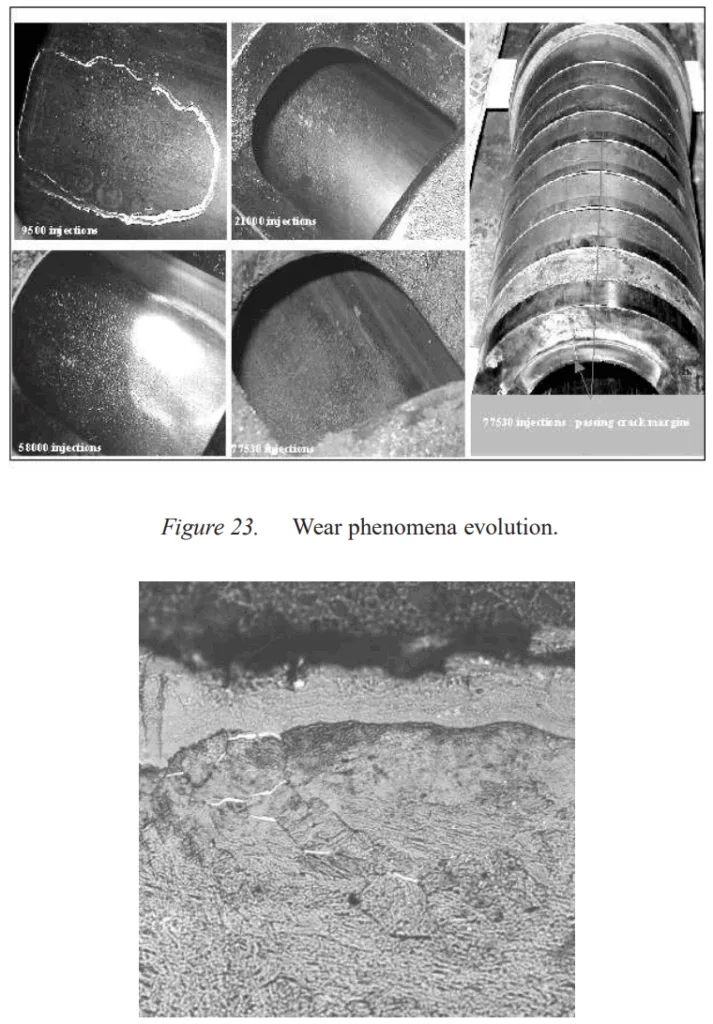
- Figure 1. Hole in the material dropping area.
- Figure 2. Theoretical ovalization in a shot sleeve with a 110-mm diameter hole.
- Figure 3. Bending Effect theoretical calculation.
- Figure 4. Micrographies of annealed steel (×100; ×500).
- Figure 5. Time-temperature-transformation continuous diagram.
- Figure 6. Warm resistance curve.
- Figure 7. Tempering diagram.
- Figure 8. Creep.
- Figure 9. Plant for hardening in salt bath – T.T.N. s.p.a. Nerviano-MI.
- Figure 10. Micrographies of hardened and tempered steel (100X; 500X).
- Figure 11. Micrography with NIPRE Duplex.
- Figure 12. Drawings of heat earth plates in copper alloy.
- Figure 13. Drawing of the cooling system with water in the material dropping area.
- Figure 14. Drawing of the oil thermal regulated circuit in the material dropping area and in the "biscuit" area.
- Figure 15. Photo showing the section of the thermal regulated circuit.
- Figure 16. Photo showing the material dropping area with thermal regulation holes.
- Figure 17. Web cracks.
- Figure 18. Passing crack.
- Figure 19. Hole in the material fall area.
- Figure 20. Pre-heating temperature trend.
- Figure 21. Thermal profile at the end of pre-heating.
- Figure 22. Thermal profile of the thermoregulated and no thermoregulated shot sleeves.
- Figure 23. Wear phenomena evolution.
- Figure 24. Micrograph of material fall area zona after 77530 injections.
7. Conclusion:
The study concludes that the use of a thermoregulated shot sleeve allows for a drastic reduction in costs associated with frequent replacement of both shot sleeves and injection plungers. It also improves the casting quality by ensuring a more stable and consistent injection process. The research and its successful outcome led to an interesting study and a standardization for integral thermoregulated big shot sleeves, proving the technology's viability and significant benefits for the die-casting industry.
8. References:
- [1] ANDREONI, Casè, Pomesano " Il processo della pressofusione" Edimet, I Edizione 1993.
- [2] M. SUNDQVIST and S. HOGMARK "The mechanism of erosive wear of die casting dies for aluminium" New materials process experience for tooling, Mat. Search 1992.
- [3] R. BREITLER, A. RIVOLTA "I processi di rifusione degli acciai per stampi per pressocolata" Böhler, 2000
- [4] C. CIBALDI, "I criteri di scelta e di trattamento degli acciai da costruzione e da utensili", Edito dall'autore, Ila Edizione 1990.
- [5] B. VIANELLO, "Studio sull'andamento delle temperature superficiali nei contenitori integrali", Comunicazione Interna Zanussi Metallurgica, 1999.
- [6] P. ROBBINS "A plunger system for future" Die Casting Technology-NADCA 1993.
- [7] P. ROBBINS, Glenn Mackie" Controlling Thermal expansion of plunger tips and shot sleeves in cold chamber die casting" Die Casing Innavation NADCA 1995.
- [8] "Acciai da utensili "Thyssen acciai speciali s.p.a."1992.
- [9] "Acciai per utensili" Cogne Acciai Speciali.
- [10] "Il trattamento termico degli acciai per utensili" Uddeholm S.p.a.
- [11] Piana "Acciai da lavorazione a caldo" Aubert&Duval
- [12] M. PIROVANO "NIPRE" TTN S.p.a. Nerviano
- [13] Brevik, Gruber, Sobol, Park, Udvardy "Optimization of shot sleeves performace" NADCA publication #203, 1998.
- [14] ROBBINS, SINGH "Bigger casting, Bigger problem" Die casting technology for the new century NADCA publication.
Conclusion & Next Steps
This research provides a valuable roadmap for enhancing shot sleeve performance in demanding HPDC applications. The findings offer a clear, data-driven path toward improving tool life, reducing operational costs, and achieving higher, more consistent casting quality.
At CASTMAN, we are dedicated to applying the latest industry research to solve our customers' most challenging die casting problems. If the issues discussed in this paper resonate with your operational goals, contact our engineering team to discuss how we can help you implement these advanced principles in your components.
Expert Q&A: Your Top Questions Answered
Q1: What was the single most critical factor identified in this study for improving shot sleeve life?
A1: The study's results overwhelmingly point to the integral thermal regulation circuit as the most critical factor. The paper's conclusion states that the use of the "thermoregulated shot sleeve" allowed for the drastic cost reductions and improved quality, a finding supported by the temperature data in Figure 22 and the wear evolution in Figure 23.
Q2: How does this integral system compare to other cooling methods mentioned in the paper?
A2: The paper describes other methods like external copper plates or partial 4-hole water/oil circuits (Page 14-15). However, the integral system is superior because it addresses the entire sleeve's length and circumference. This is the only method discussed that "practically removed" the bending and ovalization effect, which partial systems cannot do (Page 17).
Q3: What specific aluminum alloy was used for the casting in this test?
A3: The research, as described in the "THERMOREGULATED SHOT SLEEVE, PRODUCT AND PRODUCTIVE PROCESS" section, was conducted using an EN AC-46000 alloy for a 21 kg casting (Page 19).
Q4: What exactly is the Nipre® Duplex surface treatment?
A4: According to the "SUPERFICIAL TREATMENT" section, Nipre® Duplex is a patented process that creates a double hardening layer. It consists of ionic nitriding to create a hard, wear-resistant layer (0.20-0.25 mm thick), followed by the creation of a 4-5 micron magnetite layer that acts as a chemical barrier against the molten aluminum (Page 11).
Q5: What was the ultimate reason for taking the sleeve out of service after 77,530 shots? Was it worn out?
A5: No, the sleeve was not taken out of service due to wear degeneracy. The "ACHIEVED RESULTS" section states it was decommissioned "due to a passing crack caused by a sharp edge of the collar," indicating the main working surface of the sleeve was still performing well (Page 23).
Q6: What is the direct, practical takeaway from this paper for a die casting facility making large parts?
A6: The core takeaway, based on the paper "SHOT SLEEVE WITH INTEGRAL THERMAL REGULATION," is that by implementing a shot sleeve with an integral, full-length thermal regulation system, it is possible to dramatically increase tool life, reduce downtime for sleeve and plunger changes, and improve the consistency and quality of the final casting.
Copyright
- This material is an analysis of the paper "SHOT SLEEVE WITH INTEGRAL THERMAL REGULATION" by F. Miglierina and B. Vianello.
- Source of the paper: 6th International Tooling Conference proceedings.
- This material is for informational purposes only. Unauthorized commercial use is prohibited.
- Copyright © 2025 CASTMAN. All rights reserved.