Mastering Shrinkage: A Simulation-Driven Approach to Defect-Free Precision Casting
This technical brief is based on the academic paper "Simulation of Hot Casting Shrinkage of Thermoplastic Beryllium Oxide Slurries with Ultrasonic Activation" by Uzak Zhapbasbayev, Zamira Sattinova, and Gaukhar Ramazanova, published in Engineered Science (2024). It is summarized and analyzed for HPDC professionals by the experts at CASTMAN.
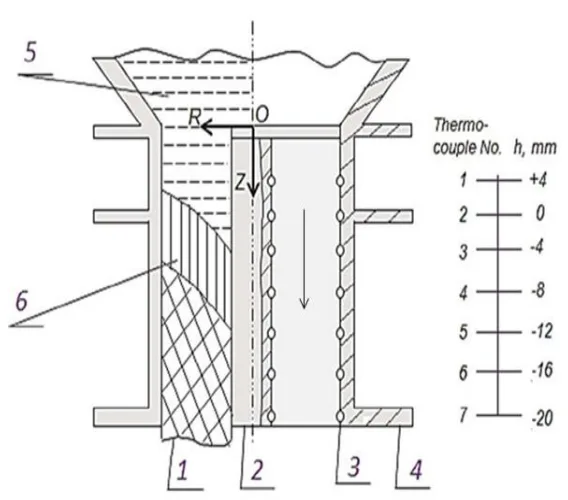
Keywords
- Primary Keyword: Casting Shrinkage Simulation
- Secondary Keywords: Solidification Modeling, Ultrasonic Activation, Casting Process Optimization, Rheological Properties, Thermoplastic Moulding, Beryllium Oxide, Defect Prediction
Executive Summary
- The Challenge: Predicting and compensating for shrinkage during the hot casting of complex materials is critical to prevent internal defects like porosity and shells, which compromise the integrity of the final product.
- The Method: Researchers developed a sophisticated mathematical model to simulate the hot casting of a thermoplastic beryllium oxide (BeO) slurry. The model calculates shrinkage by tracking the temperature, density, and concentration of "kinetically free binder" as the slurry cools and solidifies.
- The Key Breakthrough: The study successfully demonstrates that shrinkage can be precisely determined by modeling the distribution of the kinetically free binder. This allows for the prediction of how casting speed, temperature, and die design will affect the final part's homogeneity.
- The Bottom Line: This research provides a powerful simulation-based method for understanding and controlling shrinkage, offering a clear pathway to producing higher-quality, defect-free components by optimizing process parameters before physical production begins.
The Challenge: Why This Research Matters for HPDC Professionals
In any precision casting process, from HPDC of aluminum alloys to the thermoplastic molding detailed in this paper, shrinkage is a formidable enemy. As the material cools and transitions from a liquid to a solid state, volumetric changes occur. If not properly compensated for, this shrinkage leads to internal voids, porosity, and dimensional inaccuracies, resulting in rejected parts and increased production costs.
The paper tackles this universal challenge within the context of hot casting a BeO slurry—a material valued for its high thermal conductivity and electrical resistivity. The core problem is that inhomogeneous cooling across the die cavity leads to an uneven distribution of temperature, density, and material properties. This creates internal stresses and defects. As stated in the paper, "Achieving shrinkage compensation is the main technological task" (Ref. [12-15]). This research matters because it presents a novel, simulation-first approach to mastering this fundamental casting challenge.
The Approach: Unpacking the Methodology
To predict and control shrinkage, the researchers developed a comprehensive mathematical model based on the physics of the casting process. The study focuses on a thermoplastic slurry, which behaves as a viscoplastic (Schwedoff-Bingham) fluid.
The methodology involved:
1. Modeling Fluid Flow and Heat Transfer: The researchers used a system of equations (Eq. 12-14) to model the slurry's movement and temperature change as it flows through circular and annular die cavities.
2. Characterizing Material Properties: Extensive experimental work was done to define how the slurry's density, viscosity, and thermal properties change with temperature (Fig. 4, Eq. 8-9). The study also investigated the effect of ultrasonic activation, which was found to significantly reduce slurry viscosity and improve its casting properties (Fig. 5).
3. Defining Shrinkage: The novelty of the work, as the abstract states, "is the determination of shrinkage by the distribution of the concentration of the kinetically free binder." This binder is the portion of the liquid phase that can flow to compensate for shrinkage during solidification. By modeling its concentration (C_k^w), the researchers could precisely map where and when shrinkage occurs.
4. Numerical Simulation: The model was solved numerically to generate detailed 2D maps showing the fields of temperature, density, and kinetically free binder concentration throughout the die cavity under various casting conditions.
The Breakthrough: Key Findings & Data
The simulation results provided a clear, visual understanding of the complex solidification process and were validated against experimental and production data.
Visualizing Solidification: The simulations successfully mapped the temperature gradients, density increases, and shrinkage zones within the die. As shown in Figure 7, the slurry cools from the outside wall inward, creating an inhomogeneous temperature field. This directly impacts density (Figure 7b) and the concentration of the kinetically free binder (Figure 7c).
ntration of kinetically free binder (Ck^w) proved to be a perfect proxy for shrinkage. Where Ck^w is high, the slurry is liquid and can flow to compensate for volume loss. As the slurry solidifies, C_k^w drops to zero, indicating that shrinkage in that region is complete and can no longer be compensated by liquid inflow. This is clearly visualized in the progression from the inlet to the outlet in Figures 7c, 8c, 9c, and 10c.
Impact of Process Parameters: The study confirmed that casting speed and binder composition are critical.
- Increasing casting speed from 0.120 m/min (Figure 7) to 0.160 m/min (Figure 8) extends the solidification zone deeper into the die.
- A higher mass fraction of binder (w = 0.117 vs. w = 0.100) resulted in a larger initial concentration of kinetically free binder, leading to a greater density increase (1.097 vs. 1.055) and, as noted in Table 5, better shrinkage compensation when combined with ultrasonic treatment.
Practical Implications for Your HPDC Operations
While this study focuses on a ceramic slurry, the principles of using advanced simulation to deconstruct and control the casting process are directly relevant to HPDC.
For Process Engineers: This research underscores the power of simulation to optimize parameters before a single part is cast. The finding that casting speed directly influences the solidification profile (Figure 3) reinforces the need for precise process control in HPDC to manage cooling rates and prevent premature freezing at the gate.
For Quality Control: The concept of tracking a specific metric (like "kinetically free binder") to predict defects is powerful. For HPDC, this translates to using simulation software to track metrics like "liquid fraction" or "Niyama criterion" to predict porosity hotspots with greater accuracy. The paper's success validates this simulation-driven approach to quality assurance.
For Die Design: The study's comparison of circular and annular cavities (Figures 7-14) highlights how die geometry fundamentally dictates the thermal and solidification behavior. This reinforces the critical importance of die design in HPDC, particularly the strategic placement of cooling channels and gates to ensure homogeneous solidification and feed shrinkage-prone areas effectively.
Paper Details
Simulation of Hot Casting Shrinkage of Thermoplastic Beryllium Oxide Slurries with Ultrasonic Activation
1. Overview:
- Title: Simulation of Hot Casting Shrinkage of Thermoplastic Beryllium Oxide Slurries with Ultrasonic Activation
- Author: Uzak Zhapbasbayev, Zamira Sattinova, Gaukhar Ramazanova
- Year of publication: 2024
- Journal/academic society of publication: Engineered Science
- Keywords: Hot casting; Thermoplastic slurry moulding; Shrinkage; Beryllium oxide; Ultrasonic activation.
2. Abstract:
The article proposes a method for calculating the shrinkage of hot casting of thermoplastic beryllium oxide slurries. The thermoplastic slurry (hereinafter referred to as slurry) is a composition system with a dispersed phase (binder) having a low thermal conductivity compared to the dispersed phase (beryllium oxide). Ultrasonic treatment reduces the viscosity of the slurry and improves its casting properties. The hot casting of beryllium oxide slurry is carried out without breaking the continuity of the system and depends on speed and temperature factors. Cooling-solidification of the slurry in the casting unit takes place in stages in a liquid state, a crystallization state with a phase transition, and a plastic state of the casting. The cooling rate of the casting at all stages depends on the design of the cavity, the rheological properties of the slurry, and the casting speed. The novelty of the work is the determination of shrinkage by the distribution of the concentration of the kinetically free binder. The slurry near the cooled wall is in a state of crystallization and plasticity, and the other part may still be in the liquid phase. Along the cavity cross-section, there is the inhomogeneous distribution of temperature, density, and concentration of kinetically free binder. This leads to compensation of shrinkage by the inflow of slurry from the liquid into the crystallization zones and the plasticity of the casting.
3. Introduction:
Beryllium oxide (BeO) is a ceramic material with outstanding properties like high thermal conductivity and radiation resistance, making it suitable for applications in nuclear reactors, electronics, and microwave devices. Hot casting of thermoplastic BeO slurries is a key manufacturing process, but it presents significant challenges. The physical and chemical properties of the slurry are highly dependent on temperature and phase transformations during cooling. A primary challenge is managing volume change (shrinkage) during solidification, which can cause internal defects like shells and porosity. Compensating for this shrinkage is a main technological task to ensure the quality of the final ceramic product.
4. Summary of the study:
Background of the research topic:
The technology for hot casting thermoplastic slurries is similar to that for metals and plastics. However, the unique properties of composite powder materials like beryllium oxide require specific study. Shrinkage occurs in three stages: in the liquid state, during the phase transition from liquid to plastic, and in the plastic state. Incomplete compensation of this shrinkage is a primary cause of defects in castings.
Status of previous research:
Previous experimental studies have shown that the hot molding process has strict requirements. The properties of the slurry depend on temperature, phase transformations, and cooling conditions. Shrinkage compensation is typically achieved by the inflow of hot slurry into the liquid and crystallization zones. However, a detailed method for calculating and predicting this shrinkage based on the fundamental properties of the slurry was needed.
Purpose of the study:
The article proposes a method to calculate the shrinkage of the slurry by developing a model of the physical processes and conducting computational experiments. The goal is to track the changes in the temperature-phase fields in detail and clearly represent the shrinkage and solidification kinetics as a function of casting modes and die configuration. The novelty lies in determining shrinkage from the concentration distribution of the "kinetically free binder."
Core study:
The core of the study is a mathematical model that simulates the hot casting process. It incorporates the rheological properties of the BeO slurry, which behaves as a viscoplastic (Schwedoff-Bingham) fluid. The model accounts for heat transfer, fluid dynamics, and phase changes. It specifically tracks the concentration of the kinetically free binder (C_k^w) as a key indicator of shrinkage. The model was applied to both circular and annular die cavities, and the simulation results were compared with experimental data obtained from a pilot plant that uses ultrasonic activation to improve slurry properties.
5. Research Methodology
Research Design:
The study combined experimental investigation with numerical simulation. An experimental pilot plant (Fig. 1) was used to perform hot casting of BeO slurries and to measure material properties and temperature profiles under various conditions (Table 2). A mathematical model consisting of continuity (Eq. 12), motion (Eq. 13), and heat transfer (Eq. 14) equations was developed to describe the process.
Data Collection and Analysis Methods:
Experimental data on slurry properties (density, viscosity, etc.) as a function of temperature were collected and approximated by empirical formulas (Eq. 6, 8, 9). The mathematical model was solved using a numerical method (finite-difference method, control volume method) to generate simulation results. The iterative numerical scheme involved solving for temperature, then updating material properties (density, viscosity), then solving for velocity and pressure, and repeating until convergence was achieved.
Research Topics and Scope:
The research focused on the hot casting of thermoplastic beryllium oxide slurries in two different die geometries: a circular cavity and an annular cavity. The study investigated the influence of key process parameters, including casting speed and the mass fraction of the binder in the slurry, on the solidification process and resulting shrinkage.
6. Key Results:
Key Results:
The study successfully simulated the temperature, density, and kinetically free binder concentration fields for various casting scenarios. The results showed that as the slurry moves through the die, it cools from the walls inward, leading to a non-uniform solidification front. The concentration of the kinetically free binder (C_k^w) was shown to be an effective measure of shrinkage, decreasing from its initial value at the inlet to zero in the fully solidified regions. The simulations demonstrated that higher casting speeds and different binder compositions significantly alter the solidification dynamics and the final density of the casting, which aligns with experimental findings (Table 5, Table 6).
Figure Name List:
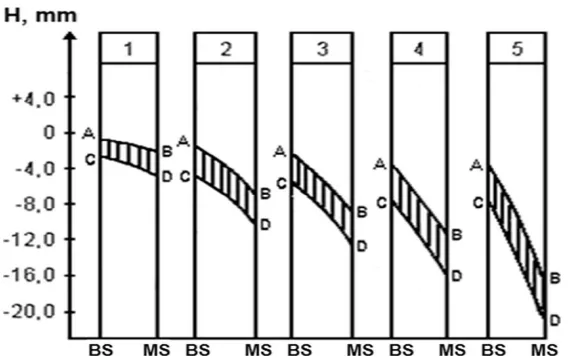
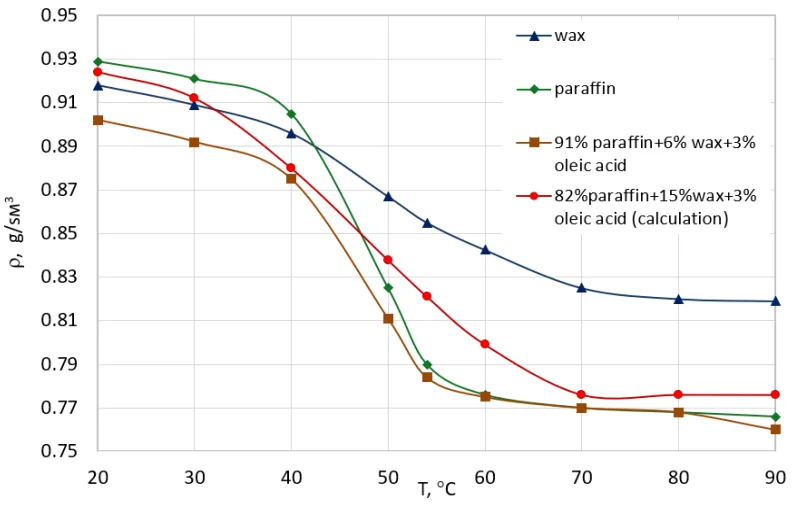
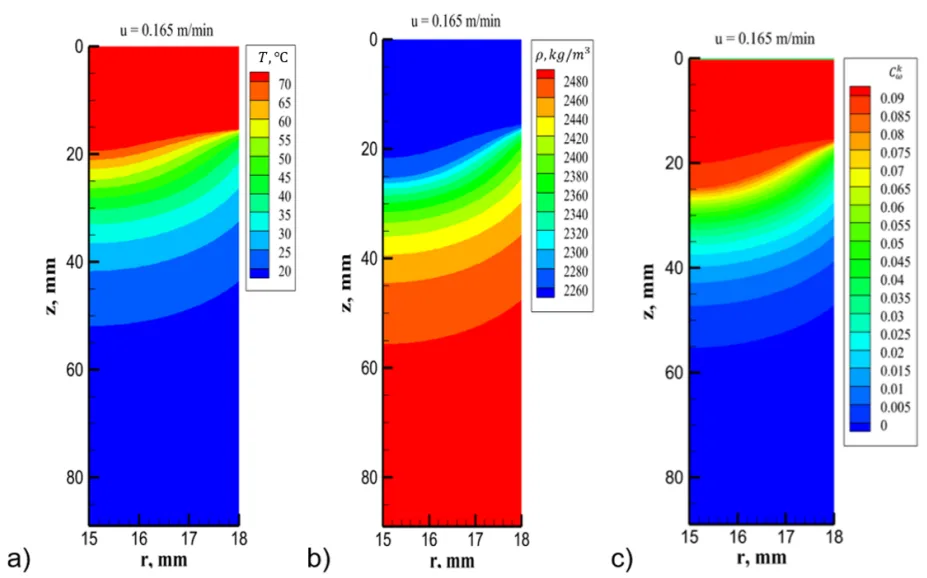
- Fig. 1 Schematic diagram of a pilot plant for ultrasonic slurry casting.
- Fig. 2 Schematic diagram of a pilot die.
- Fig. 3 Position of the solidification zone depending on casting speed.
- Fig. 4 Experimental data on the density of binders and their components as a function of temperature.
- Fig. 5 Changes of viscosity (a) and yield strength, (b) depending on temperature and duration of US processing.
- Fig. 6 Diagram of the die (a) circular cavity, (b) annular cavity.
- Fig. 7 The field of temperature, density, and kinetically free concentration of slurry in the circular cavity with the mass fraction of the binder w = 0.100.
- Fig. 8 The field of temperature, density and kinetically free concentration of slurry in the circular cavity at the mass fraction of the binder w = 0.100.
- Fig. 9 The field of temperature, density and kinetically free concentration of the slurry in the circular cavity at the mass fraction of the binder w = 0.117.
- Fig. 10 The field of temperature, density and kinetically free concentration of the slurry in the circular cavity at the mass fraction of the binder ω = 0.117.
- Fig. 11 The field of temperature, density and kinetically free concentration of the slurry in the annular cavity at the mass fraction of the binder ω = 0.100.
- Fig. 12 The field of temperature, density, and kinetically free concentration of the slurry in the annular cavity with the mass fraction of the binder w = 0.117.
- Fig. 13 Calculated data of temperature, density, and kinetically free concentration of slurry in the annular cavity at a mass fraction of binder w = 0.100.
- Fig. 14 Calculated data on temperature, density, and kinetically free concentration of slurry in the annular cavity at the mass fraction of the binder w = 0.117.
7. Conclusion:
The paper concludes that the developed shrinkage calculation method, based on the distribution of kinetically free binder, successfully models the molding of a homogeneous structure in beryllium ceramics and can predict the occurrence of defects. The simulations show that solidification begins at the surface and progresses inward. The study confirms that up to 80% of volumetric changes occur in the temperature range of 59-40 °C. The calculations demonstrated how to find molding conditions that properly manage shrinkage, allowing for the production of a solidified, homogeneous product at the cavity outlet.
8. References:
- [List of 26 references as provided in the original paper, from [1] R. G. Larson, Y. Wei... to [26] T. Cebeci, P. Bradshaw...]
Conclusion & Next Steps
This research provides a valuable roadmap for enhancing process control in precision casting. By linking a fundamental material property—the kinetically free binder—to the macroscopic problem of shrinkage, the findings offer a clear, data-driven path toward improving quality, reducing defects, and optimizing production through simulation.
At CASTMAN, we are dedicated to applying the latest industry research to solve our customers' most challenging die casting problems. If the issues discussed in this paper resonate with your operational goals, contact our engineering team to discuss how we can help you implement these advanced principles in your components.
Expert Q&A: Your Top Questions Answered
Q1: What was the single most critical factor identified in this study for calculating shrinkage?
A1: The study's novelty and most critical factor was the determination of shrinkage by modeling the distribution of the "concentration of the kinetically free binder (C_k^w)," as stated in the Abstract
. This concentration directly represents the slurry's ability to compensate for volume loss during cooling.
Q2: How does ultrasonic activation help in this process?
A2: According to the Abstract
and Section 2.1
, ultrasonic treatment reduces the viscosity of the slurry. Figure 5 shows that ultrasonic processing significantly lowers both viscosity and yield strength, which improves the slurry's casting properties and flowability within the die.
Q3: Is this finding applicable to all types of casting, or just this specific slurry?
A3: The research, as detailed throughout the paper, was specifically conducted on a thermoplastic beryllium oxide (BeO) slurry. While the fundamental principles of using simulation to model heat transfer and solidification to predict shrinkage are universal to all casting processes, the specific material properties and the "kinetically free binder" concept are unique to this system.
Q4: What specific simulation technique did the researchers use to arrive at this conclusion?
A4: The researchers used a numerical method based on a finite-difference scheme to solve the governing equations of motion, continuity, and heat transfer, as described in the Numerical method of solution
section (Section 3.5). This allowed them to create detailed 2D maps of the process variables inside the die.
Q5: According to the paper, what is the main practical outcome of this research?
A5: The main practical outcome, as stated in the Conclusion
, is that the calculations allow for finding "conditions of moulding with shrinkage of slurry by hot casting method," which in turn "allow to obtain at the cavity outlet a solidified product with a homogeneous structure of beryllium oxide." In short, it provides a predictive tool to achieve defect-free parts.
Q6: How does casting speed affect the solidification process?
A6: As shown in Figure 3 and discussed in Section 2.2
, an increase in casting speed leads to the expansion of the solidification zone and its displacement further down the die. This is because at higher speeds, the slurry has less time to cool, so the transition from liquid to solid occurs over a longer distance.
Copyright
- This material is an analysis of the paper "Simulation of Hot Casting Shrinkage of Thermoplastic Beryllium Oxide Slurries with Ultrasonic Activation" by Uzak Zhapbasbayev, Zamira Sattinova, and Gaukhar Ramazanova.
- Source of the paper: https://dx.doi.org/10.30919/es1294
- This material is for informational purposes only. Unauthorized commercial use is prohibited.
- Copyright © 2025 CASTMAN. All rights reserved.