Hot vs. Cold Chamber for Magnesium: A Data-Driven Guide to Choosing the Right HPDC Process
This technical brief is based on the paper "Properties of Diecasting Alloys and a Comparison of Hot and Cold Chamber Processes for Magnesium Die Casting" by Dr. Ing Norbert Erhard and Bob Tracy of Oskar Frech GmbH + Co. KG. It is summarized and analyzed for HPDC professionals by the experts at CASTMAN.
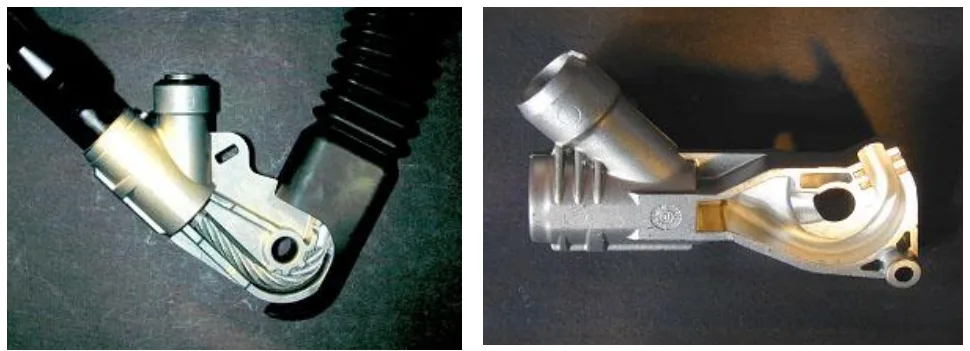
Keywords
- Primary Keyword: Hot vs Cold Chamber Magnesium Die Casting
- Secondary Keywords: Magnesium die casting process, HPDC process parameters, Thin-wall die casting, Die casting defects, Die casting alloy properties, Die casting process efficiency
Executive Summary
- The Challenge: With the rising demand for lightweight magnesium components, particularly in the automotive and electronics sectors, manufacturers face the critical decision of choosing between the hot chamber and cold chamber die casting processes to optimize quality, cost, and performance.
- The Method: The paper provides a comprehensive comparative analysis of the two processes, evaluating key parameters such as process pressure, cycle time, thermal management, air entrapment, die life, and their ultimate impact on the properties of the final cast part.
- The Key Breakthrough: The research clearly demonstrates that the hot chamber process is economically and qualitatively superior for producing thin-walled magnesium parts (wall thickness < 1.2 mm). Conversely, the cold chamber process is better suited for thick-walled parts or when specific mechanical properties and minimal porosity are the primary requirements.
- The Bottom Line: The selection of a die casting process for magnesium is not a one-size-fits-all decision. A strategic choice based on the part's wall thickness and required mechanical properties is essential for achieving optimal results.
The Challenge: Why This Research Matters for HPDC Professionals
The worldwide consumption of magnesium (Mg) alloys has increased significantly, with over 70% of light metal castings now used in the automotive industry. As the lightest of the common structural metals, magnesium is a key enabler for weight reduction in everything from engine components to electronic device housings (Figure 4, Figure 6).
However, producing these often complex and thin-walled components presents a significant manufacturing challenge. Engineers and procurement managers must select a production process that not only meets stringent quality standards for mechanical properties, dimensional accuracy, and surface finish but also remains economically viable. The fundamental choice between the hot chamber and cold chamber die casting process lies at the heart of this challenge, with each method offering a distinct set of advantages and disadvantages that directly impact the final product and the bottom line. This paper provides a clear, data-driven framework for navigating this critical decision.
The Approach: Unpacking the Methodology
Rather than a single, isolated experiment, this paper presents a holistic, comparative analysis grounded in the fundamental physics of die casting and extensive empirical data. The authors systematically deconstruct the hot and cold chamber processes for magnesium, comparing them across a wide range of operational and qualitative factors.
The study compares the processes on:
- Machine & Process Parameters: Locking force, injection pressure, cycle times, and injection velocities (Table 2).
- Thermal & Metal Handling: Furnace temperatures, temperature stability, oxidation risk, and the use of protective gas (Table 3).
- System Dynamics: Air entrapment, die filling, and dosing accuracy.
- Resulting Part Properties: Minimum wall thickness, strength, porosity, and surface quality.
This point-by-point comparison provides a clear and practical understanding of how the inherent differences in each process translate into tangible outcomes for the cast component.
The Breakthrough: Key Findings & Data
The paper's detailed comparison reveals critical differences between the two processes that directly influence part quality and production efficiency.
Finding 1: Pressure, Velocity, and Machine Size: The cold chamber process operates at significantly higher specific casting pressures (400-1400 bar) compared to the hot chamber process (160-250 bar), as shown in Table 2. This necessitates larger, more robust machines for cold chamber casting. The hot chamber's lower pressure requirements mean a die casting machine with up to 50% smaller locking force can be used for the same part.
Finding 2: Thermal Stability and Metal Purity: In the hot chamber process, the gooseneck is submerged in the molten metal, ensuring a constant temperature from the bath to the die nozzle. The cold chamber process involves transferring metal to a separate, colder sleeve, which introduces temperature variations, promotes oxidation, and requires lubricants that can contaminate the melt and the final casting. This leads to "an increased absorption of hydrogen in the melt" for cold chamber processes (Page 7, "Clean Metal").
Finding 3: Air Entrapment and Gas Porosity: A critical distinction lies in air management. The hot chamber sleeve is always 100% full of metal. In contrast, the cold chamber sleeve is only filled to a maximum of 2/3, meaning "considerably more air in the casting system of the cold chamber" is injected into the die with the metal (Page 9, "Gas porosity"). This makes the cold chamber process more susceptible to gas porosity defects.
Finding 4: Wall Thickness and Mechanical Properties: The processes excel in different part geometries. The hot chamber process is ideal for thin-walled parts, allowing for wall thicknesses "as little as 0.5 mm" (Page 9). For these thin-walled castings, the hot chamber process can produce parts with considerably higher tensile strength and elongation. For thick-walled parts (> 2 mm), the cold chamber process is capable of achieving higher strength and elongation values.
Practical Implications for Your HPDC Operations
The findings from this paper offer direct, actionable insights for optimizing your die casting operations.
For Process Engineers: The conclusion on page 10 strongly suggests that for thin-walled magnesium components (< 1.2 mm), specifying the hot chamber process is the "more economical" choice and results in "a better quality" casting. This can lead to faster cycle times and reduced scrap.
For Quality Control: The inherent risk of higher air entrapment and lubricant contamination in the cold chamber process (as noted on pages 7 and 9) means that QC protocols for parts made with this method should include rigorous inspection for gas porosity and surface impurities.
For Die Design: The lower operating pressures of the hot chamber process "do not stress the die thermal and mechanically" to the same extent as the cold chamber process (Page 8, "Life of die"). This suggests that specifying the hot chamber process can lead to longer die life and reduced tooling maintenance costs. Dies for cold chamber must be built to withstand higher pressures and require larger gating and venting to compensate for process characteristics.
Paper Details
Properties of Diecasting Alloys and a Comparison of Hot and Cold Chamber Processes for Magnesium Die Casting
1. Overview:
- Title: Properties of Diecasting Alloys and a Comparison of Hot and Cold Chamber Processes for Magnesium Die Casting
- Author: Dr. Ing Norbert Erhard, Bob Tracy
- Year of publication: Not specified
- Journal/academic society of publication: Oskar Frech GmbH + Co. KG Technical Paper
- Keywords: Magnesium, Diecasting, Hot Chamber, Cold Chamber, Zinc, Aluminium, Alloy Properties
2. Abstract:
This paper analyzes the physical and mechanical properties of common die casting alloys (Zn, Al, Mg) and provides an in-depth comparison of the hot chamber and cold chamber die casting processes, with a specific focus on magnesium. It evaluates the two processes based on machine parameters, process efficiency, metal quality, die considerations, and final part properties. The paper concludes that the hot chamber process is preferable for thin-walled magnesium castings (< 1.2 mm) due to better economy and quality, while the cold chamber process is better suited for thick-walled parts or those with demanding mechanical property requirements.
4. Summary of the study:
Background of the research topic:
The global consumption of die-cast alloys, particularly lightweight aluminum and magnesium, is increasing, driven largely by the automotive industry's need for weight reduction. This has intensified the need to understand and optimize the manufacturing processes for these materials to produce complex, high-quality parts.
Purpose of the study:
The purpose is to provide a clear, comparative analysis of the hot chamber and cold chamber die casting processes for magnesium. The study aims to guide die casters and engineers in selecting the appropriate process based on specific application requirements, such as part geometry (wall thickness) and desired mechanical properties.
Core study:
The core of the paper is a side-by-side comparison of the two processes across a comprehensive set of variables, including:
- Process Parameters: Locking force, casting capacity, cycle times, injection pressure.
- Process Conditions: Metal temperature, air in the system, oxide formation, wear parts.
- Die Design: Die life, gating, die temperature, venting.
- Part Properties: Minimum wall thickness, strength, porosity, surface hardness, and cleanliness.
5. Research Methodology
Research Design:
The study employs a comparative analysis methodology, contrasting the hot and cold chamber processes based on established principles of die casting technology and empirical data from industrial practice. It does not detail a single experiment but rather synthesizes knowledge about the two systems.
6. Key Results:
Key Results:
The key result is the clear delineation of applications for each process. Hot chamber is superior for thin-walled (< 1.2 mm) Mg parts, offering faster cycles, use of smaller machines, less air entrapment, and better metal purity. Cold chamber is necessary for alloys requiring higher melt temperatures and is better for thick-walled parts where higher injection pressures can help feed shrinkage and achieve specific mechanical properties.
Figure Name List:
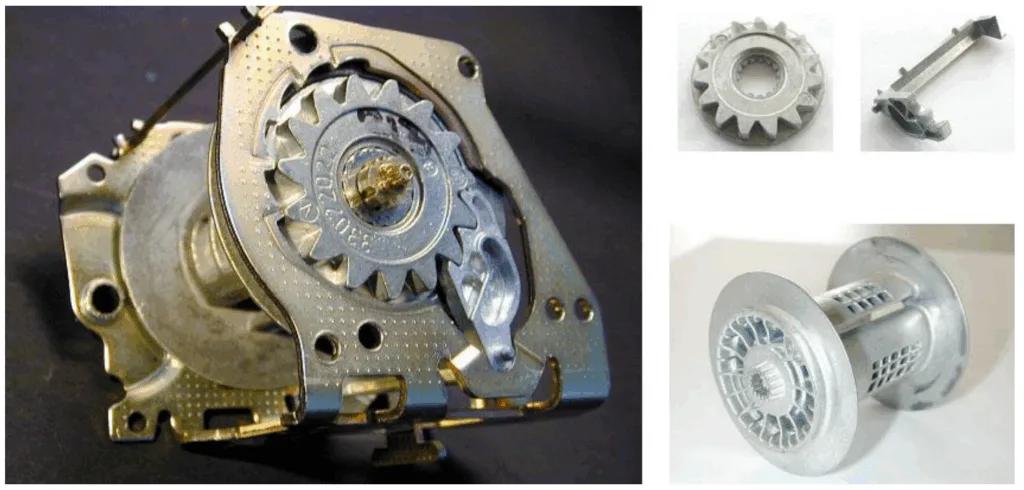
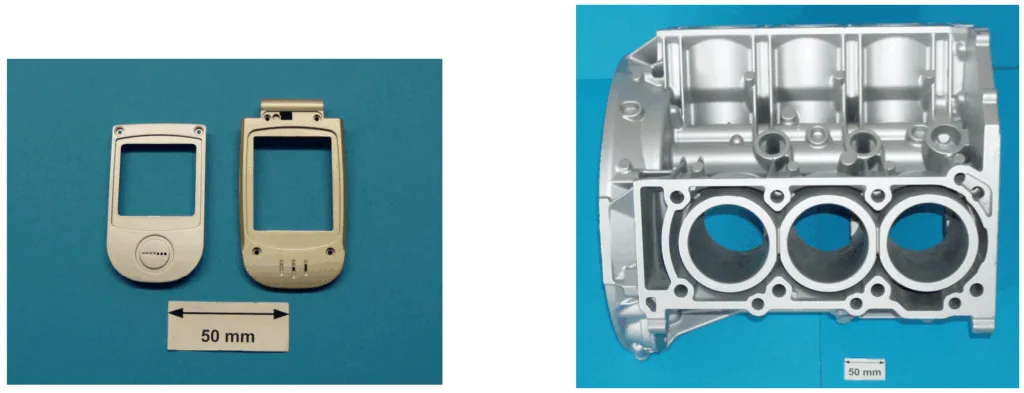
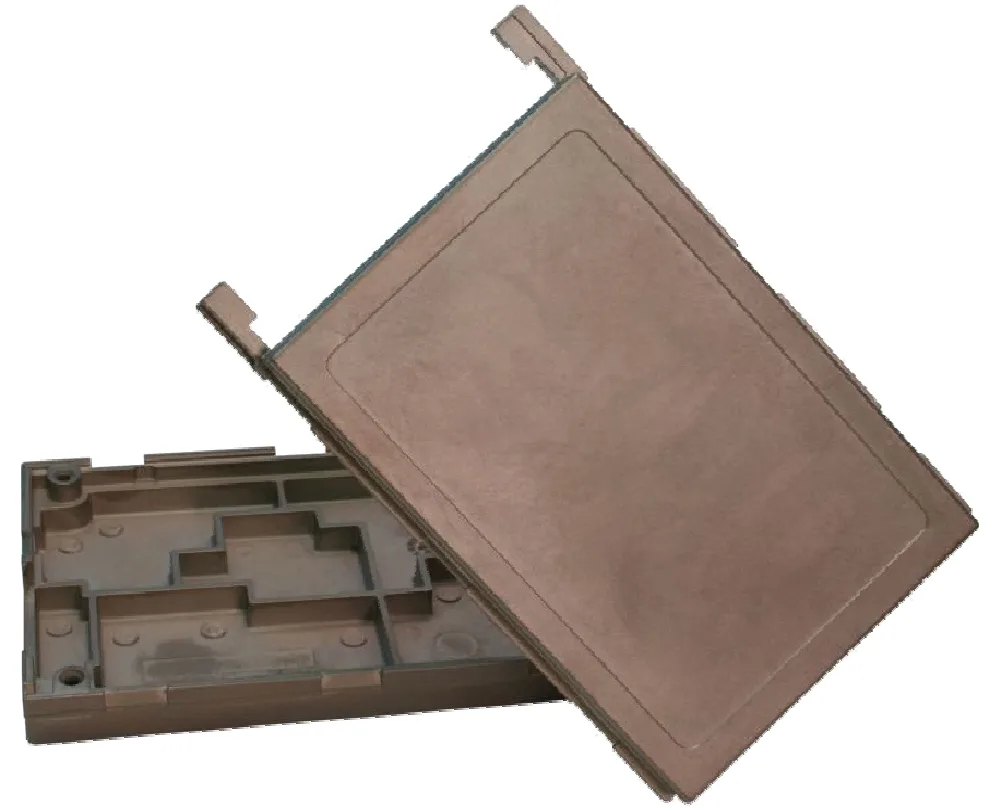
- Figure 1 - Casting „Belt-taut“ (Zinc) (source: Foehl, Germany)
- Figure 2 - Supporting Frame with wall thickness up to 0.6mm (project Fohl, Germany)
- Figure 3 - Belt roll (Zinc) (source: Foehl, Germany)
- Figure 4 - Mobile phone (Mg)
- Figure 5 - Zylinder crank housing (Al) (source: Honsel, Germany)
- Figure 6 - Electronic Device (Mg), Fishercast, CANADA
- Figure 7 - Ventilation of die in hot chamber process
- Figure 8 - Ventilation of die in cold chamber process
- Figures 9 - Gating for the hot chamber process
- Figures 9 - Gating for the cold chamber processes
7. Conclusion:
The paper concludes that "it is better to cast thin-wall parts (< 1,2 mm) on hot chamber machines." This approach is more economical and yields higher quality castings. For "thick-wall parts or a casting quality with fewer porosity is demanded, it is better to cast such parts on a cold chamber machine." The choice of process should be made according to the requested properties of the casting.
8. References:
- The paper does not contain a formal list of external references.
Conclusion & Next Steps
This research provides a valuable roadmap for enhancing quality and efficiency in magnesium HPDC. The findings offer a clear, data-driven path for selecting the optimal manufacturing process, directly impacting part quality, production speed, and overall cost.
At CASTMAN, we are dedicated to applying the latest industry research to solve our customers' most challenging die casting problems. If the issues discussed in this paper resonate with your operational goals, contact our engineering team to discuss how we can help you implement these advanced principles in your components.
Expert Q&A: Your Top Questions Answered
Q1: What was the single most critical factor identified in this study for choosing a process for magnesium parts?
A1: The study's conclusion identifies the part's wall thickness as the most critical factor. It explicitly states, "it is better to cast thin-wall parts (< 1,2 mm) on hot chamber machines," while the cold chamber process is better for "thick-wall parts."
Q2: What is the main difference in capability regarding wall thickness between the two processes?
A2: According to the "Parts Properties" section on page 9, the hot chamber process allows for casting wall thicknesses "as little as 0.5 mm for short distances." The paper indicates the cold chamber process is better for parts with a wall thickness greater than 2 mm where higher strength and elongation values are required.
Q3: Are all magnesium alloys suitable for the hot chamber process?
A3: No. The paper states that the metal bath temperature is the limit for the hot chamber process. As shown in Table 3 on page 7, temperatures greater than 650°C cause issues. Therefore, alloys like AM20 HP are listed as "not possible" for hot chamber, while AZ91 and AM60 are noted as the "preferred alloys" for the process (Page 10).
Q4: Why does the cold chamber process typically lead to more gas porosity in the casting?
A4: The paper explains in the "Air Vents" section on page 8 that the cold chamber sleeve "can only be filled up to a maximum of 2/3." This means a significant volume of air is injected into the die with the metal. In contrast, the hot chamber sleeve is "always filled up to 100%," resulting in a lower air volume in the casting system.
Q5: According to the paper, what is a key limitation or trade-off of the hot chamber process?
A5: A key limitation, described on page 9 under "Magnesium alloy," is the temperature limit of the casting unit. Temperatures above 650°C cause "more leakages between piston rings and sleeve." Additionally, the "Costs of Wear Parts" section on page 7 notes that the gooseneck is an expensive hot-working steel component that requires significant time for replacement and reworking.
Q6: What is the direct, practical takeaway from this paper for a die casting facility?
A6: The core takeaway, based on the paper's conclusion, is to strategically match the casting process to the product's design. For maximum economy and quality on thin-walled magnesium parts, use the hot chamber process. For thick-walled parts or when specific mechanical properties or low porosity are paramount, the cold chamber process is the better choice.
Copyright
- This material is an analysis of the paper "Properties of Diecasting Alloys and a Comparison of Hot and Cold Chamber Processes for Magnesium Die Casting" by Dr. Ing Norbert Erhard and Bob Tracy.
- Source of the paper: Oskar Frech GmbH + Co. KG.
- This material is for informational purposes only. Unauthorized commercial use is prohibited.
- Copyright © 2025 CASTMAN. All rights reserved.