This technical brief is based on the academic paper "Pengendalian Kualitas Produk Downlight dengan Implementasi Simulasi Die Casting" by Trio Yonathan Teja Kusuma, Gunawan Budi Susilo, and M Zulhan Iswanda, published in REKAYASA, Journal of Science and Technology (2023). It is summarized and analyzed for HPDC professionals by the experts at CASTMAN.
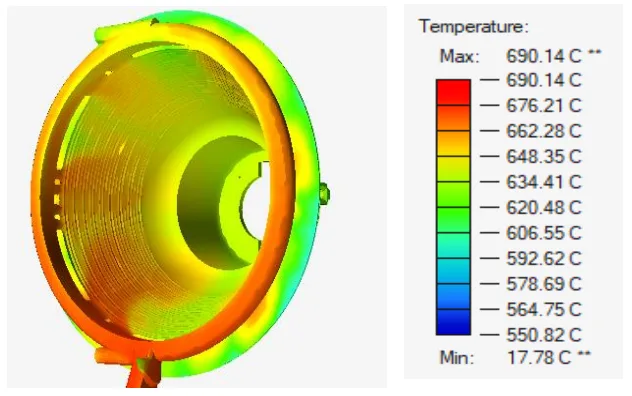
Keywords
- Primary Keyword: Die Casting Simulation for Quality Control
- Secondary Keywords: HPDC defects, Cold shot defect, Inspire Cast simulation, ADC12 aluminum casting, Casting process optimization, Microporosity analysis, Casting simulation
Executive Summary
- The Challenge: A high-pressure die casting operation for an ADC12 aluminum downlight product was experiencing significant quality issues, with cold shot defects accounting for 52% of all rejected parts, leading to costly waste and production delays.
- The Method: Researchers utilized Inspire Cast simulation software to visualize the existing injection process, identify the root cause of the defects, and then model two new, mathematically-derived process configurations before committing to physical trials.
- The Key Breakthrough: Simulation visually confirmed that the cold shot defects were caused by molten metal streams meeting at temperatures below the point of recrystallization. The optimized configurations demonstrated more uniform temperature profiles, leading to a predicted reduction in defects and microporosity.
- The Bottom Line: Investing in die casting simulation provides a clear and rapid return on investment by drastically reducing the costs and time associated with physical trial-and-error, allowing for the validation of process improvements in a virtual environment.
The Challenge: Why This Research Matters for HPDC Professionals
Achieving zero-defect production in high-pressure die casting is a constant challenge. Defects such as cold shot, shrinkage, porosity, and cracking are common hurdles that can lead to significant financial losses and compromise product integrity.. These issues often stem from suboptimal process parameters or die design..
This research addresses a pressing, real-world problem faced by a manufacturer producing a downlight component (model NN511) from ADC12 aluminum.. The operation suffered from a high rate of defects, with cold shot being the most frequent culprit, making up 52% of the total issues.. This scenario is familiar to many in the industry: a high-cost, trial-and-error approach to finding a stable process window, which consumes valuable time and materials. The study demonstrates a more scientific and cost-effective path forward..
The Approach: Unpacking the Methodology
To tackle this challenge, the researchers turned to process simulation. The study was centered on using Inspire Cast, a powerful simulation software, to analyze and optimize the die casting process..
The methodology involved several key steps:
- Baseline Analysis: The team first created a 3D CAD model of the existing die, including the shot sleeve, runner, gates, and overflow. This model was imported into Inspire Cast to run a simulation of the current, problematic production process..
- Parameter Calculation: New, optimized injection parameters were calculated, including the critical slow shot velocity (Vcss) and the travel distances for the plunger's first and second phases..
- Virtual Testing: Two new configurations, "Alternatif 1" and "Alternatif 2," were developed based on these calculations.. These alternative setups were then simulated in Inspire Cast to predict their effect on mold filling, temperature distribution, and potential microporosity before any physical changes were made to the machine..
This "simulate-first" approach allowed the researchers to virtually validate their new process parameters and compare them directly against the original, underperforming setup.
The Breakthrough: Key Findings & Data
The simulation results provided clear, actionable insights into the cause of the defects and the effectiveness of the proposed solutions.
- Finding 1: Pinpointing the Root Cause: The simulation of the original configuration (Gambar 1) clearly visualized the temperature distribution during mold filling. It showed that the molten metal streams from different gates were meeting at temperatures below the alloy's recrystallization point (<653°C), which is a classic recipe for the formation of cold shot defects..
- Finding 2: Validating a Better Process: The simulation for "Parameter Alternatif 1" showed a significant improvement. The temperature at the critical meeting points of the molten aluminum was more uniform and remained above the recrystallization temperature, leading to better fusion (Gambar 2).. Consequently, the predicted microporosity was reduced to a range of 1.35% - 1.8% of the product volume (Gambar 3)..
- Finding 3: Demonstrating Clear ROI: The research provides a compelling financial case for simulation. The paper notes that physical trials to find the best configuration resulted in a 29% defect rate and significant cost.. In contrast, the simulation-led approach, which involved only two physical trial alternatives, produced a lower 22% defect rate at a fraction of the cost (Rp 240,000 vs. Rp 708,000 for the initial trials).. This highlights the power of simulation in reducing expensive and time-consuming shop-floor experiments..
Practical Implications for Your HPDC Products
The findings of this study offer valuable lessons that can be directly applied to enhance real-world manufacturing operations.
- For Process Engineers: The research detailed in the "Pengolahan Data" section provides a clear framework for calculating and implementing a multi-phase injection profile.. By optimizing the 1st phase (slow shot) velocity and travel, you can effectively minimize air entrapment in the shot sleeve. The simulation results suggest that adjusting these parameters based on calculations can directly reduce defects caused by both turbulence and premature cooling..
- For Quality Control: The strong correlation shown between the simulated temperature profiles (Gambar 1, 2, 4) and the physical location of cold shot defects provides a powerful predictive quality tool.. Simulation can be used to identify "hot spots" or, in this case, "cold spots" in the die design, allowing for proactive adjustments before the first part is ever cast.
- For Die Design: This study underscores how injection parameters and die design are intrinsically linked. While the research focused on optimizing the injection process, the simulation results (Analisa 2nd Phase) clearly show how flow is dictated by the runner and gate design.. This implies that using simulation early in the die design phase is critical to ensure proper filling, minimize pressure requirements, and place gates and overflows for maximum effect, a conclusion supported by the paper's overall findings..
Paper Details
Pengendalian Kualitas Produk Downlight dengan Implementasi Simulasi Die Casting
1. Overview:
- Title: Pengendalian Kualitas Produk Downlight dengan Implementasi Simulasi Die Casting (Quality Control of Downlight Products with Implementation of Die Casting Simulation)
- Author: Trio Yonathan Teja Kusuma, Gunawan Budi Susilo, M Zulhan Iswanda
- Year of publication: 2023
- Journal/academic society of publication: REKAYASA, Journal of Science and Technology
- Keywords: die casting, casting defect, casting simulation
2. Abstract:
Die casting is a casting process in which molten metal is poured into a mold by injection using a piston driven by pneumatic/hydraulic energy. In some cases, the resulting product does not match the desired design because defects will occur if the configuration is not correct. There are several defects that commonly occur in the Die casting process such as cold shot, shrinkage, bubble, warping, undercut, etc. With the help of computers, these problems are expected to be reduced. Using inspire cast to visualize the injection process will facilitate the analysis of the Die casting process. With the help of this software, a better configuration can be created and implemented into the machine. However, the results are different, when simulating in the software it is said that the molten metal streams from different gates are above the recrystallization temperature of 665°C so it should harden and fuse better when the two molten metal streams meet. However, after implementing the new configurations into the machine, the process defects were still high at 23% for configuration 1 and 13% for configuration 2 compared to 6% for the existing configuration. However, implementing this software will reduce the cost of trial and error process to find a new configuration for a new material..
3. Introduction:
The paper begins by establishing die casting as a major manufacturing process for producing a wide variety of metal products.. It highlights that a primary challenge in the industry is the frequent occurrence of defects like cold shot, shrinkage, blowholes, and porosity.. These defects are often caused by improper die design or incorrect injection process configurations. The introduction sets the stage for the study by presenting computer simulation as a modern solution to visualize and analyze the complex fluid dynamics of high-pressure die casting, thereby enabling engineers to mitigate these common problems..
4. Summary of the study:
Background of the research topic:
The research was initiated to solve a persistent quality problem in the production of a downlight product (NN511) made of ADC12 aluminum.. The existing manufacturing process resulted in a high percentage of defects, particularly cold shot, which was the most significant issue at 52% of total defects..
Status of previous research:
The paper acknowledges previous work that establishes the causes of defects like cold shot (imperfect fusion of metal streams) and porosity (air entrapment).. It positions itself as an application of existing simulation technology (Inspire Cast) to a specific, practical industrial problem to find a better machine configuration and reduce trial-and-error costs..
Purpose of the study:
The main goal was to use die casting simulation to analyze the existing process, understand the root cause of the high defect rate, and develop and test new, optimized injection configurations to improve product quality and reduce manufacturing costs..
Core study:
The core of the study involved a comparative analysis. First, the existing factory configuration was simulated to create a baseline and validate the simulation against known defects.. Second, new process parameters were calculated, and two alternative configurations were designed.. These alternatives were then simulated in Inspire Cast, focusing on the temperature of the molten metal flow and the resulting microporosity.. The results of the simulations were then compared to the baseline to determine the most effective configuration.
5. Research Methodology
Research Design:
The research was designed as a case study using a pre-test/post-test framework. The "pre-test" was the analysis of the existing, flawed production setup, while the "post-test" was the analysis of the two new, optimized configurations..
Data Collection and Analysis Methods:
Data was collected by first modeling the die and process in CAD and Inspire Cast software.. The analysis was done by running simulations and examining the visual outputs, specifically the temperature gradients during the 2nd phase of injection (Gambar 1, 2, 4) and the predicted microporosity maps (Gambar 3, 5).. The study also compared the costs and defect rates of physical trials with and without prior simulation..
Research Topics and Scope:
The study focused on the high-pressure die casting of a specific ADC12 aluminum downlight. The scope was limited to optimizing the injection parameters (plunger speed and position in multiple phases) to reduce defects, primarily cold shot and microporosity. It did not involve redesigning the die itself.
6. Key Results:
Key Results:
The key result was the successful use of simulation to identify the cause of cold shot and validate a new process that reduces defects. The initial configuration showed that metal streams were meeting below the 665°C recrystallization temperature.. The proposed "Alternatif 1" and "Alternatif 2" configurations improved the temperature profile at these meeting points.. "Alternatif 1" reduced predicted microporosity to 1.35%-1.8%, while "Alternatif 2" showed a range of 1.35%-2.25%.. The study concluded that simulation significantly cuts down on the cost of physical trials..
Figure Name List:
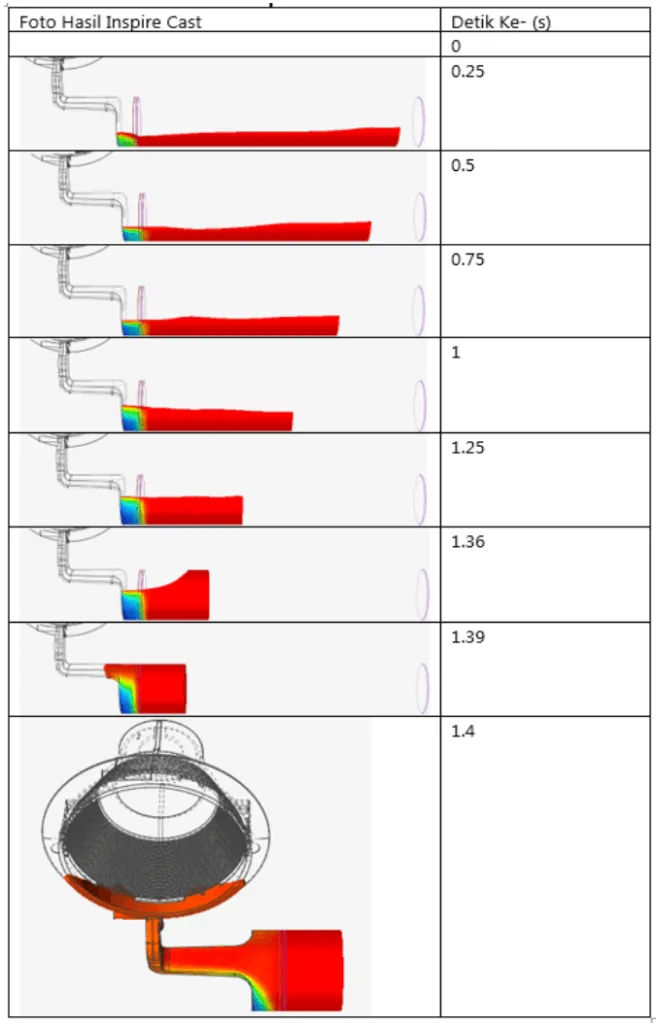
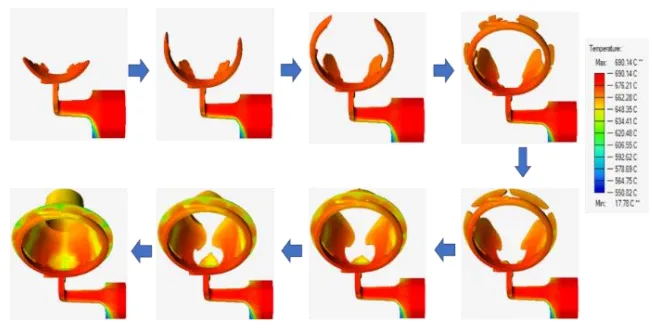
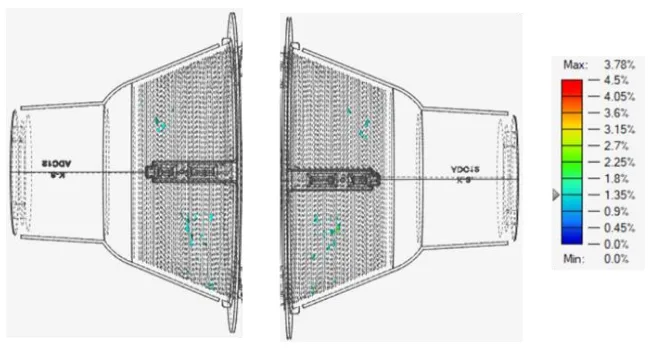
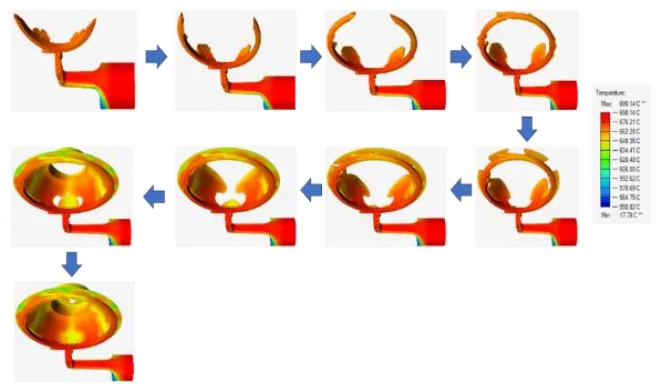
- Gambar 1. Hasil Simulasi Proses Casting pada Konfigurasi Awal
- Tabel 2. Konfigurasi Parameter Alternatif 1
- Tabel 3. Konfigurasi Parameter Alternatif 2
- Gambar 2. Hasil Simulasi Inpire Cast: 2nd Phase Parameter Alternatif 1
- Gambar 3. Hasil Simulasi Inpire Cast: Microporosity Parameter Alternatif 1
- Gambar 4. Hasil Simulasi Inpire Cast: 2nd Phase Parameter Alternatif 2
- Gambar 5. Hasil Simulasi Inpire Cast: Microporosity Parameter Alternatif 2
7. Conclusion:
The paper draws four main conclusions:
a. The most prevalent defect, cold shot, was caused by the temperature of the meeting aluminum streams being below the recrystallization temperature..
b. Simulation provides a clear depiction of the aluminum flow within the mold, allowing for analysis of potential defects before production begins, which helps reduce costs associated with trials..
c. While configurations developed using formulas are an improvement, they may not be fully optimal. Simulation helps refine these calculated parameters to achieve a better result, reducing the cost of physical trials..
d. Changes in the injection configuration have a direct impact on the final product quality..
8. References:
- Kwon & Kwon, 2019
- Shankar Kamble & Kadane, 2016
- Laukli, 2004
- Rahimi, A.(2003). Introduction Of High Pressure Die-Casting And Common Defects In Die-Casting. Islamic Azad Univercity Of Saveh
- Krisbianto, D., Rahmalina, D., & Suwandi, A. (2019). Optimasi Desain Gating System Proses Die Casting Cold Chamber Menurunkan Cacat Produk. Jurnal Kajian Teknik Mesin, 4(2), 50-67.
Expert Q&A: Your Top Questions Answered
Q1: What was the single most critical factor identified in this study for improving the quality of the downlight product?
A1: The study concluded that optimizing the injection configuration to manage the temperature of the molten aluminum during mold filling was the most critical factor. This prevented the metal streams from falling below the recrystallization temperature before fusing, which directly addressed the primary cause of cold shot defects. (Source: "KESIMPULAN DAN SARAN", "[Paper Title]")..
Q2: How does this research compare to traditional methods for addressing casting defects?
A2: The paper's conclusion highlights that traditional methods rely on physical "Trial tanpa adanya simulasi" (Trial without simulation).. This research introduces a simulation-first approach, which demonstrated a significant reduction in the cost and number of trials required to achieve an optimized process. (Source: "KESIMPULAN DAN SARAN", "[Paper Title]")..
Q3: Is this finding applicable to all types of alloys, or a specific one?
A3: The research, as described in the "Pada penelitian ini" section, was specifically conducted using ADC12 aluminum.. The paper does not make claims regarding the direct applicability of these specific temperature values or parameters to other alloys, which would require further investigation.
Q4: What specific measurement or simulation technique did the researchers use to arrive at this conclusion?
A4: The researchers utilized "software inspire cast" to create a visual simulation of the injection process.. This software allowed them to analyze the temperature of the molten metal flow and predict areas of microporosity, as explained in the "Metode Penelitian" and "Hasil Pembahasan" sections..
Q5: According to the paper, what is the main limitation or area for future research?
A5: The authors state in the "Kesimpulan" (Conclusion) that a configuration developed using only mathematical formulas is still "kurang optimal" (less than optimal) compared to one refined with simulation.. The "Saran" (Suggestions) section recommends that future work should always use the calculated configuration as an input for simulation to achieve the best results, rather than taking it directly to the machine..
Q6: What is the direct, practical takeaway from this paper for a die casting facility?
A6: The core takeaway is that by using simulation software like Inspire Cast to model and optimize injection parameters before conducting physical trials, it is possible to significantly reduce the costs and time required to solve defect issues like cold shot, a conclusion strongly supported by the overall results of the paper, "Pengendalian Kualitas Produk Downlight dengan Implementasi Simulasi Die Casting"..
Conclusion & Next Steps
This research provides a valuable roadmap for enhancing quality control in HPDC operations. By moving from a reactive, trial-and-error approach to a proactive, simulation-driven methodology, manufacturers can gain precise control over complex casting processes. The findings offer a clear, data-driven path toward improving quality, reducing defects like cold shot, and ultimately, optimizing production costs.
At CASTMAN, we are dedicated to applying the latest industry research to solve our customers' most challenging die casting problems. If the issues discussed in this paper resonate with your operational goals, contact our engineering team to discuss how we can help you implement these advanced principles in your components.
Copyright
- This material is a paper by "Trio Yonathan Teja Kusuma, Gunawan Budi Susilo, M Zulhan Iswanda". Based on "Pengendalian Kualitas Produk Downlight dengan Implementasi Simulasi Die Casting".
- Source of the paper: https://doi.org/10.21107/rekayasa.v16i1.18839
This material is for informational purposes only. Unauthorized commercial use is prohibited.
Copyright © 2025 CASTMAN. All rights reserved.