This introduction paper is based on the paper "Studies on Die Filling of A356 Al alloy and Development of a Steering Knuckle Component using Rheo Pressure Die Casting System" published by "Journal of Materials Processing Technology".
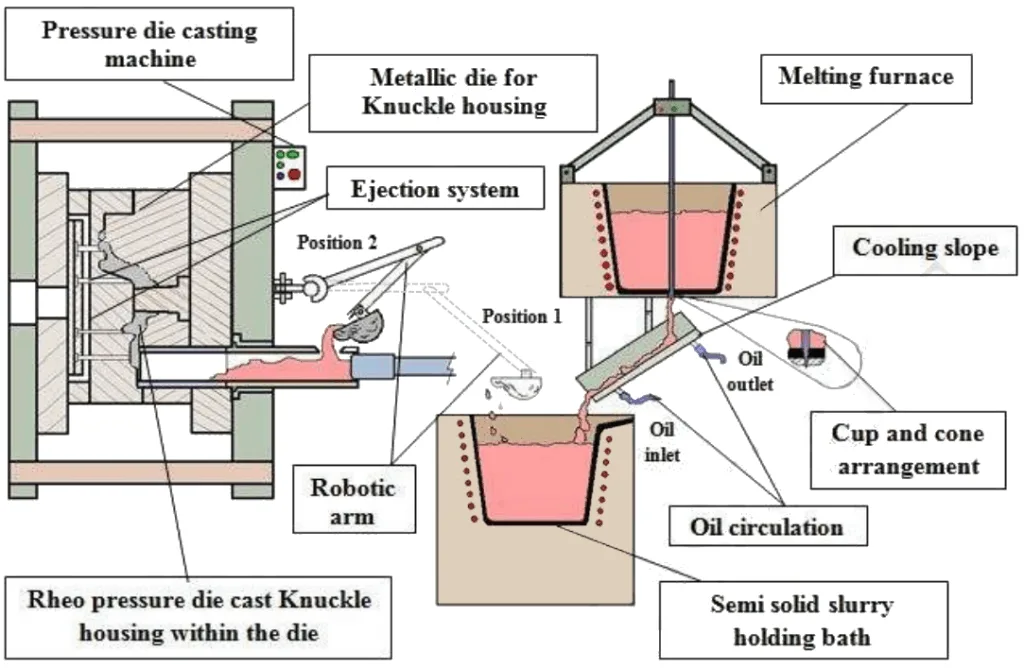
1. Overview:
- Title: Studies on Die Filling of A356 Al alloy and Development of a Steering Knuckle Component using Rheo Pressure Die Casting System
- Author: Prosenjit Das, Bikash Bhuniya, Sudip K. Samanta, Pradip Dutta
- Year of publication: 2019
- Journal/academic society of publication: Journal of Materials Processing Technology
- Keywords: Steering knuckle, Semi solid, RPDC, A356 alloy, Die filling
2. Abstract:
In this study, a computational fluid dynamics (CFD) model is developed to investigate die filling of semi solid slurry as part of rheo pressure die casting (RPDC) system. The die filling cavity corresponds to that of an automobile steering knuckle, and the slurry is made of A356 aluminium alloy. The rheological model used in the CFD simulation is determined experimentally. The results obtained from present numerical model includes flow field of the slurry within the die cavity, viscosity evolution, solid fraction distribution, temperature and pressure distribution during solidification within cavity during die filling stage. The main objective of the study is to determine the gating arrangement, pouring temperature, and injection conditions for desirable microstructure and mechanical properties of the developed component. To study the effect of injection conditions on die filling capability of the said alloy slurry, five injection profiles are studied, with a variation in final injection velocity between 2 to 3.2 m/s. In order to corroborate the findings of the present study, microstructural morphology and structure-property correlation have been studied, primarily in the form of optical microscopy and macro hardness measurements, by obtaining samples from different locations of the solidified component.
3. Introduction:
The automotive industry's drive for enhanced fuel efficiency motivates efforts towards lightweighting automobile components, particularly suspension parts which require superior strength-to-weight ratios and elongation values. Traditional manufacturing processes like forging and conventional die casting of aluminium and magnesium alloys present challenges such as multiple processing steps, inconsistent mechanical properties, dendritic microstructures, and liquid segregation. Semi solid die casting, particularly Rheo Die Casting (RDC) and its variant Rheo Pressure Die Casting (RPDC), has emerged as a promising single-step solution for producing sound, near-net-shape components with improved structural integrity and cost-effectiveness. The success of these processes heavily relies on preparing semi-solid slurry with near-spherical primary particles to ensure proper filling of complex die cavities. While numerous studies have explored Thixo Die Casting (TDC) and RDC, literature on CFD simulations of die filling in RPDC, especially with experimental validation, is relatively scarce. This study aims to address this gap by optimizing RPDC processing parameters for an A356 Al alloy steering knuckle using CFD simulations, validated by experimental work.
4. Summary of the study:
Background of the research topic:
The primary motivation is the need for lightweight automotive components to improve fuel efficiency. Automobile suspension parts, traditionally made from steel or cast iron, are being developed using aluminium and magnesium alloys. However, conventional manufacturing methods for these light alloys often lead to defects and inconsistent properties.
Status of previous research:
Previous research has explored various casting processes like conventional gravity die casting (GDC), high pressure die casting (HPDC), squeeze casting, and semi-solid metal (SSM) processing, including thixo die casting (TDC) and rheo die casting (RDC). Studies have highlighted defects like segregation bands, microporosity, and hot tears in HPDC. RDC is noted for its energy and cost efficiency over TDC. Several researchers have investigated RDC for different components and alloys, and some have used CFD to simulate die filling, employing various rheological models. However, a comprehensive understanding of RPDC, particularly with validated simulations for complex components like steering knuckles, is still developing.
Purpose of the study:
The main objective of this study is to optimize the processing parameters of a Rheo Pressure Die Casting (RPDC) system for developing an automobile steering knuckle component from A356 Al alloy. This involves using CFD simulation to investigate the die filling process and determine the ideal gating arrangement, pouring temperature, and injection conditions to achieve desirable microstructure and mechanical properties. The study also aims to experimentally validate the simulation findings.
Core study:
The core of the study involves developing a CFD model to simulate the die filling of A356 semi-solid slurry in a steering knuckle die cavity. This includes establishing an experimental rheological model for the A356 alloy. The study investigates the effects of pouring temperature, gating design (location and number of gates), and injection velocity profiles on die filling characteristics such as solid fraction distribution, entrained air, slurry viscosity, velocity, temperature field, and pressure distribution. The numerical results are then validated through experimental trials using an in-house developed RPDC facility, followed by microstructural characterization and mechanical property testing (hardness, tensile strength) of the cast steering knuckle.
5. Research Methodology
Research Design:
The research employs a two-pronged approach:
- Computational Fluid Dynamics (CFD) Modeling: A numerical model was developed to simulate the die filling process of semi-solid A356 Al alloy slurry in an RPDC system for a steering knuckle component. This involved solving conservation equations for mass, momentum, and energy, along with a volume-of-fluid (VOF) method for tracking the metal-air interface. An experimentally derived rheological model was incorporated.
- Experimental Validation: Physical experiments were conducted using an in-house RPDC facility. The optimal parameters derived from CFD simulations were used to cast steering knuckles. The cast components were then subjected to microstructural analysis and mechanical testing to validate the simulation predictions and assess the component quality.
Data Collection and Analysis Methods:
- CFD Simulation:
- Governing equations (continuity, momentum, energy, VOF) were solved using commercial CFD software FOLW-3D Cast.
- An Ostwald-De Waale power law based rheological model, with constants derived from experimental data (Das et al., 2015), was used to describe slurry viscosity (μ = (2.786 E - 05) e^(14430.50 / T) γ⁻¹, Eq. 10).
- A 3D CAD model of the knuckle housing with gating was created (Fig. 3a), and the domain was discretized using hexahedral grids (Fig. 3b). Grid independence was studied.
- Boundary conditions, vent locations (Fig. 3c), thermophysical properties of the alloy (Table 1, Table 2) and die material (Table 3) were specified.
- Solid fraction evolution was based on experimental DTA results (Fig. 4) and the Scheil equation (Eq. 11).
- Experimental Work:
- A356 Al alloy was melted, degassed, and processed via a cooling slope to generate semi-solid slurry.
- The slurry was held isothermally (Fig. 17 shows slurry morphology) before being transferred to the RPDC machine.
- Steering knuckles were cast using optimized parameters.
- Samples were sectioned from various locations of the cast component (Fig. 19) for:
- Microstructural analysis: Optical microscopy, FESEM (Fig. 22) to observe grain size, morphology, and eutectic structure. Grain diameter and sphericity were quantified (Eqs. 13, 14, Fig. 20).
- Mechanical testing: Macro hardness measurements (Fig. 21) and tensile tests (ASTM E8 guidelines) were performed. Fracture surfaces were analyzed (Fig. 23).
- Maximum cavity pressure was measured and compared with numerical predictions (Fig. 18).
Research Topics and Scope:
The research focused on:
- Investigating the die filling behavior of A356 Al alloy semi-solid slurry in a complex steering knuckle die cavity using the RPDC process.
- Developing and validating a CFD model for the RPDC process.
- Studying the effect of key processing parameters:
- Slurry pouring temperature (585°C, 600°C, 605°C, 610°C).
- Location and number of gates (single gate, two gates, three gates with different tensile bar positions, as shown in Fig. 11).
- Injection velocity profiles (five different profiles, Fig. 13).
- Analyzing die filling characteristics: solid fraction distribution, volume fraction of entrained air, slurry viscosity, slurry velocity, temperature distribution, and cavity pressure.
- Correlating processing parameters with the microstructure (primary Al grain size, sphericity, eutectic Si morphology) and mechanical properties (macrohardness, tensile strength) of the cast steering knuckle.
- Experimental validation of the optimal processing conditions predicted by the CFD model.
6. Key Results:
Key Results:
- Optimal Pouring Temperature: A slurry pouring temperature of 610°C was found to be optimal for die filling capability and component casting, ensuring uniform solid fraction distribution (Fig. 6a) and minimizing unfilled regions compared to lower temperatures. Modified vent locations further improved air evacuation at this temperature (Fig. 7d).
- Optimal Gating Design: A three-gate arrangement (as in Fig. 11e) was identified as the most effective for ensuring uniform solidification rate within the component, crucial for homogenous microstructural morphology.
- Optimal Injection Velocity Profile: Injection profile 1 (final velocity of 3 m/s, Fig. 13a) yielded the optimum slurry pressure and solid fraction distribution (Fig. 14a, Fig. 15a), facilitating smooth die filling and good structural integrity.
- Rheology and Flow Behavior: The experimentally determined rheological model effectively captured the shear-thinning behavior of the A356 slurry. Slurry viscosity was shown to be highly dependent on local shear rate and temperature within the die (Fig. 8).
- Experimental Validation:
- Experiments using optimized parameters (610°C slurry, three-gate, injection profile 1) successfully produced steering knuckles.
- The slurry could be held for approximately 14 minutes at 610°C without significant degradation of its globular microstructure (Fig. 17).
- Numerical predictions of maximum cavity pressure underpredicted experimental values, but trends were comparable (Fig. 18). An optimum cavity pressure was identified, beyond which defects due to turbulence and gas absorption increased.
- Microstructure: The RPDC cast knuckle exhibited a bimodal grain structure with generally uniform distribution of primary α-Al grains (approx. 55% area fraction). The median primary grain size was 24µm with an average sphericity of 0.88 (Fig. 20). Locations filled midway showed the best globular primary Al grains (Fig. 19).
- Mechanical Properties:
- Average macrohardness of the as-cast RPDC component was approximately 70 VHN (Fig. 21), a significant improvement over conventional HPDC parts.
- Average tensile properties were: Yield strength 170 MPa, Ultimate tensile strength 219 MPa, and % elongation 9.72. Fracture surfaces showed mixed-mode fracture (Fig. 23).
Figure Name List:
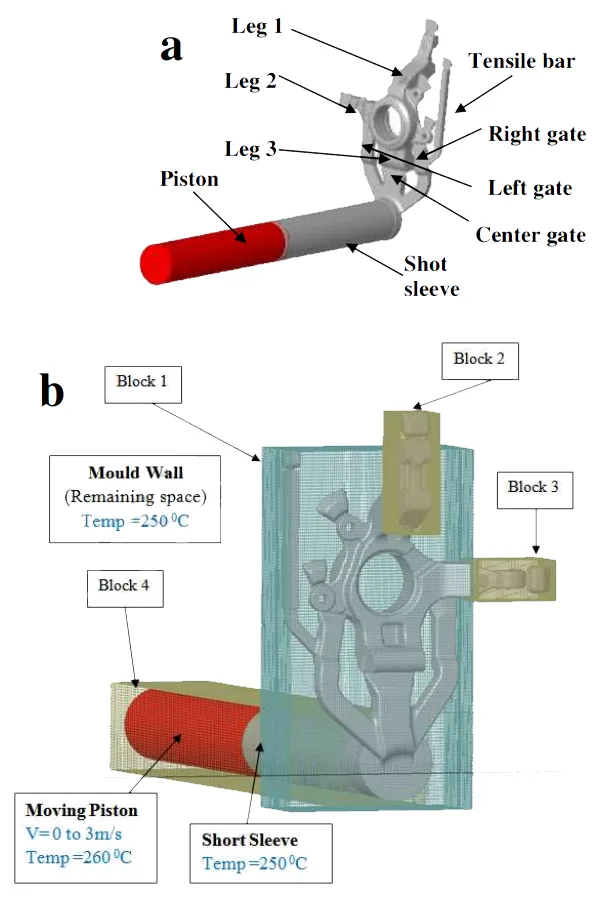
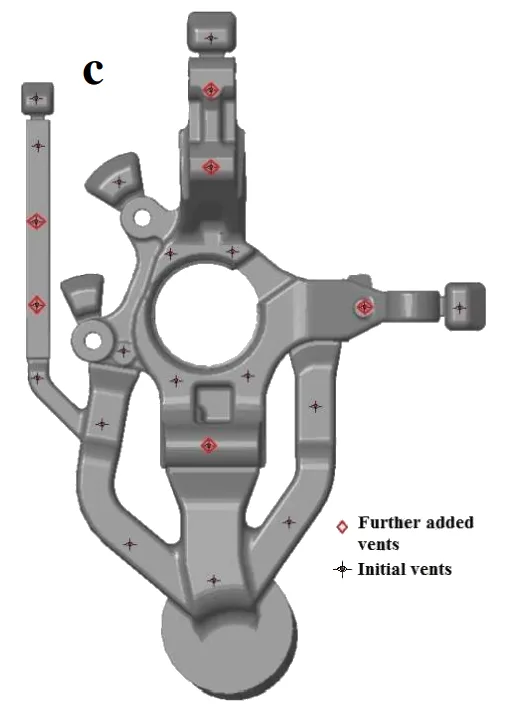
- Fig. 1: Schematic of the Rheo pressure die casting system, showing its functional parts.
- Fig. 2: Slurry viscosity as a function of (a) shear rate, and (b) temperature.
- Fig. 3: (a) Solid model of Knuckle housing with gating arrangement, (b) discretized solution domain, and (c) location of vents considered to perform die filling simulations.
- Fig. 4: (a) Solid fraction vs. temperature curve, and (b) DTA analysis results.
- Fig. 5: Flowchart of the numerical scheme.
- Fig. 6: Solid fraction and temperature distribution within the die cavity after filling completion: (a) Solid fraction and (b) Temperature (Das et al., 2015).
- Fig. 7: Volume fraction of entrained air within the die cavity for different slurry pouring temperatures: (a) 585°C, (b) 600°C, (c) 605°C, and (d) 610°C.
- Fig. 8: Slurry viscosity profiles for different slurry pouring temperatures: (a) 585°C, (b) 600°C, (c) 605°C, and (d) 610°C.
- Fig. 9: Variation of slurry velocity with filling time, for the central gate.
- Fig. 10: Slurry temperature distribution vs. filling time.
- Fig. 11: Slurry temperature distribution for different cavity designs: (a) with central gate, (b) with central and left gate, (c) with central and right gate, (d) three gates with tensile sample position 1, and (e) three gates with tensile sample position 2.
- Fig. 12: Effect of gate no. and locations on (a) solid fraction evolution, (b) viscosity, and (c) velocity of the semi solid slurry.
- Fig. 13: Injection velocity profiles considered for the present study: (a) profile 1, (b) profile 2, (c) profile 3, (d) profile 4, and (e) profile 5.
- Fig. 14: Cavity pressure distribution for different injection velocity profiles: (a) profile 1, (b) profile 2, (c) profile 3, (d) profile 4, and (e) profile 5.
- Fig. 15: Effect of injection velocity profile on solid formation: (a) profile 1, (b) profile 2, (c) profile 3, (d) profile 4, and (e) profile 5.
- Fig. 16: Temporal variation of slurry velocity during filling of the die cavity for different injection velocity profile: (a) profile 1, (b) profile 2, (c) profile 3, (d) profile 4, and (e) profile 5.
- Fig. 17: Representative optical micrographs of oil quenched samples showing slurry morphology, at different slurry formation stages.
- Fig. 18: Comparative plot of numerical and experimental findings of maximum cavity pressure and radiographs of Leg 1 (Fig. 2) of the solidified Knuckle housing for all five injection conditions.
- Fig. 19: Digital photograph of the Rheo pressure die cast prototype Knuckle housing, and optical micrographs of different locations of the solidified component.
- Fig. 20: Distribution of (a) primary Al particle size and their (b) sphericity for the samples taken from different sections of the solidified knuckle housing.
- Fig. 21: Distribution of macro hardness for the samples taken from different sections of the solidified knuckle housing.
- Fig. 22: Representative FESEM micrographs: (a) distribution of globular primary solid grains and eutectic Si particles, (b) high magnification image of eutectic morphology.
- Fig. 23: Representative SEM factographs: (a) at 1000X magnification, and (b) at 1500X magnification.
7. Conclusion:
In this study, optimisation of die geometry and process variables to develop a knuckle housing, following Rheo pressure die casting route, has been presented. The conclusions emerging out of the present study are as follows;
- Based on the simulation findings, slurry pouring temperature of 610°C (corresponding to the solid fraction of 0.15), injection tip velocity of 3.0 m/s and three gated die cavity with preheat temperature of 250°C are found to be the optimum ones to successfully develop three legged knuckle housing with sound structural integrity.
- The microstructural morphology of primary Al grains are found to be isotropic throughout the RPDC cast component, with an average macrohardness of approx. 70 VHN. This is found to be notably improved compared to that of conventional High Pressure die cast (HPDC) components.
- It is observed that the cooling slope generated slurry can be kept for approx. 14 minutes within the isothermal slurry holding bath, without much degradation of its microstructural morphology, prior to utilising it for component development.
- It is evident from the numerical findings and representative radiographs of the solidified component that, upto a certain value of maximum cavity pressure, structural integrity of the RPDC cast part increases, and pressure beyond that leads to defect formation within the cast part, due to possible turbulence during die filling and subsequent gas absorption.
- Simulation studies on solidification stage of the filled component cavity, and detailed investigation of microstructural and tensile properties of the RPDC cast component, at as cast and heat treated state, is presently underway and the findings will be reported in our future publications.
8. References:
- Blanco, A., Azpilgain, Z., Lozares, J., Kapranos, P., Hurtado, I., 2010. Rheological characterization of A201 aluminum alloy. Trans. Nonferrous Met. Soc. China, 20, 1638-1642.
- Brabazon, D., Browne, D.J., Carr, A.J., 2003. Experimental investigation of the transient and steady state rheological behaviour of Al–Si alloys in the mushy state. Materials Science and Engineering A, 356, 69-80.
- Campbell, J., 2003. Castings. Butterworth-Heinemann: Oxford, UK; Chapter 9.
- Campo, K. N., Proni, C. T. W., Zoqui, E. J., 2013. Influence of the processing route on the microstructure of aluminum alloy A356 for thixoforming. Materials Characterization, 85, 26-37.
- Choi, B. H., Jang, Y. S., Sim, J. G., Kim, H. S., Hong, C. P., 2013. Application of Rheo-diecasting of a High Strength Al-Si-Mg Alloy to Automotive Suspension Arms. ISIJ International, 53, 502-510.
- Das, P., Dutta, P., 2016. Phase field modelling of microstructure evolution and ripening driven grain growth during Cooling Slope processing of A356 Al alloy. Computational Materials Science, 125, 8–19.
- Das, P., Samanta, S.K., Chattopadhyay, H., Dutta, P., 2012. Effect of pouring temperature on cooling slope casting of semi-solid Al-Si-Mg alloy. Acta Metallurgica Sinica (English Letters), 25, 329-339.
- Das, P., Samanta, S.K., Chattopadhyay, H., Sharma, B.B., Dutta, P., 2013. Eulerian two-phase flow simulation and experimental validation of semisolid slurry generation process using cooling slope. Material Science and Technology, 29, 83-92.
- Das, P., Samanta, S.K., Das, R., Dutta, P., 2014. Optimization of degree of sphericity of primary phase during cooling slope casting of A356 Al alloy: Taguchi method and regression analysis. Measurement, 55, 605–615.
- Das, P., Samanta, S.K., Dutta, P., 2015. Rheological Behavior of Al-7Si-0.3Mg Alloy at Mushy State, Metall. Mater. Trans. B. 46, 1302-1313.
- Das, P., Samanta, S.K., Tiwari, S., Dutta, P., 2015. Die Filling Behaviour of Semi Solid A356 Al Alloy Slurry During Rheo Pressure Die Casting, Trans Indian Inst Met. 68, 1215–1220.
- Das, P., Samanta, S.K., Mondal, B., Dutta, P., 2018. Multiphase Model of Semisolid Slurry Generation and Isothermal Holding During Cooling Slope Rheoprocessing of A356 Al Alloy. Metallurgical and Materials Transactions B, 49, 1925-1944.
- Gourlay, C. M., Laukli, H. I., Dahle, A. K., 2004. Segregation Band Formation in Al-Si Die Castings, Metall. Mater. Trans. A. 35, 2881-2891.
- Gourlay, C. M., Laukli, H. I., Dahle, A. K., 2007. Defect Band Characteristics in Mg-Al and Al-Si High-Pressure Die Castings, Metall. Mater. Trans. A. 38, 1833-1844.
- Guanglei, Z., Jun, X., Zhifeng, Z., Guojun, L., 2010. Numerical simulation of die filling behavior of AZ91D in the semisolid process, China Foundry. 7(2), 127-131.
- Guan-hai, Y., Sheng-dun, Z., Zheng-hui S., 2010. Simulation of semisolid diecasting process of four-way valve of HPb59-1 alloy for air-conditioner, Nonferrous Met. Soc. China. 20, s931-s936.
- Hirt, C. W., 2012. Modeling Turbulent Entrainment of Air at a Free Surface, Flow Science Report, 01-12.
- Hirt, C. W., 2013. Void Regions and Bubble Models in FLOW-3D, Flow Science Report, 01-13.
- Hitchcock, M., Wang, Y., Fan, Z., 2007. Secondary solidification behaviour of the Al–Si-Mg alloy prepared by the rheo-diecasting process. Acta Materialia, 55, 1589–1598.
- Hongmin, G., Xiangjie, Y., Bin, H., Guanglei, Z., 2007. Rheo-diecasting Process for Semi-solid Aluminum Alloys, Journal of Wuhan University of Technology-Mater. Sci. Ed. 22(4), 590-595.
- Kang, C. G., Lee, S. M., 2008. Effect of Solid Fraction and Pressure on Microstructure and Mechanical Properties and Reduction in Liquid Segregation in the Thixo-Die-Casting Process with Al-7 Pct Si Alloy, Metallurgical and Materials Transactions A, 39, 1213-1224.
- Kang, C. G., Lee, S. M., Kim, B. M., 2008. A study of die design of semi-solid die casting according to gate shape and solid fraction, Journal of Materials Processing Technology. 204, 8-21.
- Kang, C.G., Seo, P.K., 2003. The effect of gate shape on the filling limitation in the semi-solid forging process and the mechanical properties of the products, Journal of Materials Processing Technology. 135, 144–157.
- Kang, C.G., Seo, P.K., Kang, S. S., 2006. The effect of injection velocity on liquid segregation and mechanical properties in arm part fabricated by semi-solid die casting process, Journal of Materials Processing Technology. 176, 32-40.
- Kapranos, P., Haga, T., Bertoli, E., Pola, A., Azpilgain, Z., Hurtado, I., 2008. Thixo-extrusion of 5182 aluminium alloy. Solid State Phenom. 141–143, 115–120.
- Kleiner, S., Ogris, E., Beffort, O., Uggowitzer, P. J., 2003. Semi Solid Metal Processing of Aluminum Alloy A356 and Magnesium Alloy AZ91: Comparison Based on Metallurgical Considerations. 5, 653–658.
- Lakshmi, H., Kumar, M.C.V., Raghunath, Kumar, P., Ramanarayanan, V., Murthy, K. S. S., Dutta, P., 2010. Induction Reheating of Aluminum Alloy A356 and Thixocasting of an Automobile Component, Transaction of Nonferrous Metals Society of China. 20, S961-S967.
- Laukli, H.I., Gourlay, C.M., Dahle, A.K., 2005. Migration of Crystals during the Filling of Semi-Solid Castings, Metall. Mater. Trans. A, 36, 805-818.
- Liu, Z. Y., Mao, W. M., Wang, W. P., Zheng, Z. K., Yue, R., 2017. Investigation of rheo-diecasting mold filling of semi-solid A380 aluminum alloy slurry, International Journal of Minerals, Metallurgy and Materials, 24, 691-700.
- Pola, A., Tocci, M., Kapranos, P., 2018. Microstructure and Properties of Semi-Solid Aluminum Alloys: A Literature Review, Metals, 8, 181, doi:10.3390/met8030181.
- Ri, K., Mao, W. M., Zheng, Z. K, Kim, M., Sin, Y., 2016. Effect of rheo-diecast process on the mechanical properties of A390 alloy by serpentine channel, International Journal of Minerals, Metallurgy and Materials, 23, 1177-1186.
- Otarawanna, S., Gourlay, C. M., Laukli, H. I., Dahle, A. K., 2009. Microstructure Formation in AlSi4MgMn and AlMg5Si2Mn High-Pressure Die Castings, Metall. Mater. Trans. A, 40, 1645-1659.
- Otarawanna, S., Gourlay, C. M., Laukli, H. I., Dahle, A. K., 2009. The thickness of defect bands in high-pressure die castings, Materials Characterisation, 60, 1432-1441.
- Pirovano, R., Mascetti, S., 2016. Tracking of collapsed bubbles during a filling simulation Die-casting. Metall. Ital., 6, 37–40.
- Qi, M., Kang, Y., Zhou, B., Liao, W., Zhu, G., Li, Y., Li, W., 2016. A forced convection stirring process for Rheo-HPDC aluminum and magnesium alloys, Journal of Materials Processing Technology, 234, 353-367.
- Qi, M., Kang, Y., Qiu, Q., Tang, W., Li, J., Li, B., 2018. Microstructures, mechanical properties, and corrosion behavior of novel high-thermal-conductivity hypoeutectic Al-Si alloys prepared by rheological high pressure die-casting and high pressure die-casting, Journal of Alloys and Compounds, 749, 487-502.
- Reikher, A., Pillai, K.M., 2013. A fast simulation of transient metal flow and solidification in a narrow channel. Part I: Model development using lubrication approximation, International Journal of Heat and Mass Transfer. 60, 797-805.
- Reikher, A., Pillai, K.M., 2013. A fast simulation of transient metal flow and solidification in a narrow channel. Part II. Model validation and parametric study, International Journal of Heat and Mass Transfer. 60, 806-815.
- Rosso, M., 2012. Thixocasting and rheocasting technologies, improvements going on, Journal of Achievements in Materials and Manufacturing Engineering. 54(1), 110-119.
- Sabau, A. S., Porter, W. D., Frankel, J. I., 2004. Conduction and Radiation parameters for analytical models of Differential Scanning Calorimetry instruments, TMS (The Minerals, Metals & Materials Society), 1-10.
- Seo, P.K., Kim, D.U., Kang, C.G., 2006. Effects of die shape and injection conditions proposed with numerical integration design on liquid segregation and mechanical properties in semi-solid die casting process, Journal of Materials Processing Technology. 176, 45-54.
- Seo, P.K., Kim, D.U., Kang, C.G., 2007. The effect of the gate shape on the microstructural characteristic of the grain size of Al–Si alloy in the semi-solid die casting process, Materials Science and Engineering A, 20–30, 445–446. (Note: The page range in the paper is "445-446", while the year is 2007. The previous entry for Seo, P.K., Kim, H.C., Kang, C.G., 2007 has page range 18-32. This seems to be a distinct paper or a typo in the original reference list. I will keep it as is from the paper.)
- Seo, P.K., Kim, H.C., Kang, C.G., 2007. Numerical integration design process to development of suspension parts by semi-solid die casting process, Journal of Materials Processing Technology, 183, 18-32.
- Sigworth, G.K., 1996. Rheological Properties of Metal Alloys in the Semi-Solid State, Can. Metall. Q., 35, 101–22.
- Taghavi, F., Ghassemi, A. 2009. Study on the effects of the length and angle of inclined plate on the thixotropic microstructure of A356 aluminum alloy, Mater. Des., 30, 1762–1767.
- Wei-min, M., Qiu, Z., Da-ping, Z., 2010. Rheo-squeeze casting of semi-solid A356 aluminum alloy slurry, Trans. Nonferrous Met. Soc. China, 20, 1769-1773.
- Xu, C., Zhao, J., Guo, A., Li, H., Dai, G., Zhang, X., 2017. Effects of injection velocity on microstructure, porosity and mechanical properties of a rheo-diecast Al-Zn-Mg-Cu aluminum alloy, Journal of Materials Processing Tech., 249, 167–171.
- Yue-long, B., Wei-min, M., Jun, X., Hong, X., Hua, H., 2008. Numerical simulation on rheo-diecasting mould filling of semi-solid key-shaped component, Nonferrous Met. Soc. China, 18, 682-685.
- Zhang, F., Song, N., Zhang, J., Kang, Y., Zhu, Q., 2013. Numerical simulation on the filling process of rheological die casting and forming defects analysis, Solid State Phenomena, 192-193, 293-298.
- Zhang, F., Hu, X. G., Li, D. Q., He, Y. F., Xu, X. J., Zhu, Q., 2015. Simulation on the Thixocasting Process of the Turbocharger Impellers and Selection of the Viscosity Models, Solid State Phenomena, 217-218, 219-224.
- Zheng, Z. K., Ji, Y. J., Mao, W. M., Yue, R., Liu, Z.Y., 2017. Influence of rheo-diecasting processing parameters on microstructure and mechanical properties of hypereutectic Al-30%Si alloy, Trans. Nonferrous Met. Soc. China, 27, 1264–1272.
9. Copyright:
- This material is a paper by "Prosenjit Das, Bikash Bhuniya, Sudip K. Samanta, Pradip Dutta". Based on "Studies on Die Filling of A356 Al alloy and Development of a Steering Knuckle Component using Rheo Pressure Die Casting System".
- Source of the paper: https://doi.org/10.1016/j.jmatprotec.2019.04.014
This material is summarized based on the above paper, and unauthorized use for commercial purposes is prohibited.
Copyright © 2025 CASTMAN. All rights reserved.
Summarize:
This paper presents a comprehensive study on optimizing the Rheo Pressure Die Casting (RPDC) process for manufacturing an A356 aluminum alloy steering knuckle. Through computational fluid dynamics (CFD) simulations and experimental validation, optimal parameters for slurry pouring temperature (610°C), injection velocity (3.0 m/s), and die gating (three-gate system) were determined. The research demonstrates that these optimized conditions lead to sound castings with improved microstructural homogeneity (median grain size 24µm, sphericity 0.88) and enhanced mechanical properties (average macrohardness ~70 VHN, UTS 219 MPa) compared to conventional die casting methods, highlighting the potential of RPDC for producing high-integrity lightweight automotive components.
Key questions and answers about the research:
This study aimed to optimize the Rheo Pressure Die Casting (RPDC) process parameters for producing an A356 Al alloy steering knuckle by developing and validating a computational fluid dynamics (CFD) model. The research successfully identified optimal conditions, including a slurry pouring temperature of 610°C, an injection velocity of 3.0 m/s, and a three-gate die design, which were experimentally validated. The resulting components exhibited improved microstructural homogeneity and mechanical properties, such as an average macrohardness of 70 VHN, compared to conventional die casting methods.
Q1. What was the primary objective of this research regarding the RPDC process for the A356 Al alloy steering knuckle?
A1. The main objective was to determine the optimal gating arrangement, pouring temperature, and injection conditions to achieve desirable microstructure and mechanical properties in the steering knuckle component using a CFD model and experimental validation. (Source: Abstract; Studies on Die Filling of A356 Al alloy and Development of a Steering Knuckle Component using Rheo Pressure Die Casting System)
Q2. What were the key optimal processing parameters identified by the simulation for the RPDC system?
A2. The simulation findings indicated that a slurry pouring temperature of 610°C (corresponding to a solid fraction of 0.15), an injection tip velocity of 3.0 m/s, and a three-gated die cavity with a preheat temperature of 250°C are optimum for producing a sound steering knuckle. (Source: Section 6. Conclusions; Studies on Die Filling of A356 Al alloy and Development of a Steering Knuckle Component using Rheo Pressure Die Casting System)
Q3. How did the mechanical properties of the RPDC cast steering knuckle compare to conventional methods?
A3. The RPDC cast component showed an average macrohardness of approximately 70 VHN, which is notably improved compared to conventional High Pressure Die Cast (HPDC) components. Tensile properties were also comparable to those reported for RDC A356 Al alloy samples. (Source: Section 5.2 Mechanical properties, Section 6. Conclusions; Studies on Die Filling of A356 Al alloy and Development of a Steering Knuckle Component using Rheo Pressure Die Casting System)
Q4. What was the significance of the rheological model developed in this study?
A4. An experimentally determined rheological model, based on the Ostwald-De Waale power law, was developed to accurately describe the shear thinning behavior of the A356 semi-solid slurry, which is crucial for the predictive capability of the CFD simulations of the die filling process. (Source: Section 2.2 Rheology model; Studies on Die Filling of A356 Al alloy and Development of a Steering Knuckle Component using Rheo Pressure Die Casting System)
Q5. What effect did the pouring temperature have on the die filling capability and final component quality?
A5. A pouring temperature of 610°C was found to be suitable for complete die filling and uniform solid content distribution, whereas lower temperatures (e.g., 585°C) resulted in incomplete filling and non-uniform solid fractions, making them unsuitable for component development. (Source: Section 4.1.1 Solid fraction distribution; Studies on Die Filling of A356 Al alloy and Development of a Steering Knuckle Component using Rheo Pressure Die Casting System)
Q6. How long could the cooling slope generated slurry be held before casting without significant degradation?
A6. It was observed that the cooling slope generated slurry could be kept for approximately 14 minutes within the isothermal slurry holding bath without much degradation of its microstructural morphology prior to component casting. (Source: Section 5. Experimental validation, Section 6. Conclusions; Studies on Die Filling of A356 Al alloy and Development of a Steering Knuckle Component using Rheo Pressure Die Casting System)