This introduction paper is based on the paper "The Application of Magnesium Die Casting to Vehicle Closures" published by "SAE International".
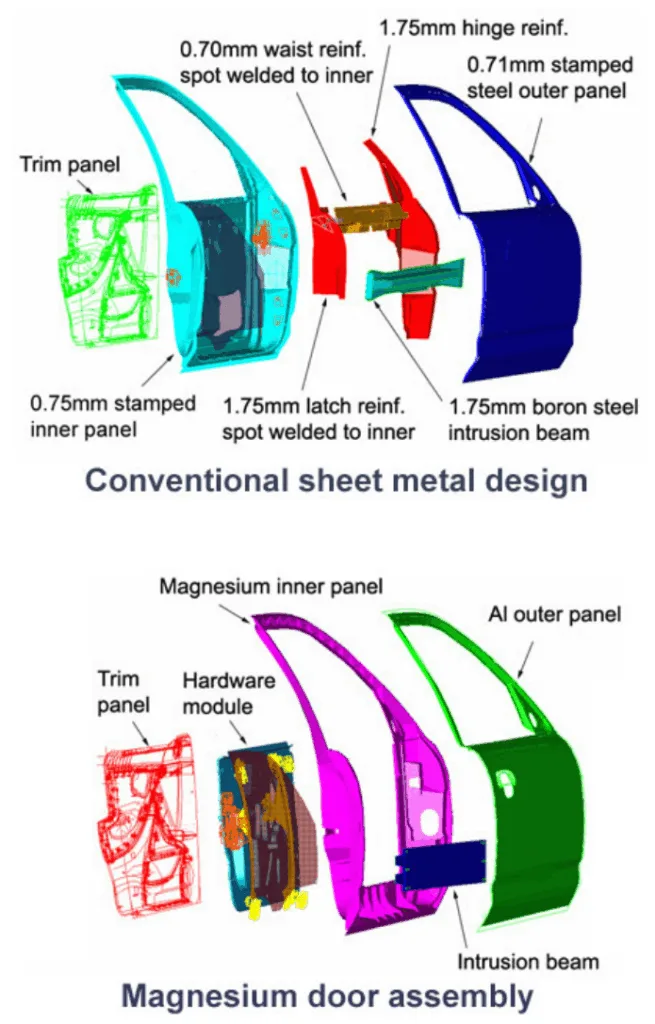
1. Overview:
- Title: The Application of Magnesium Die Casting to Vehicle Closures
- Author: Patrick J. Blanchard, Gregory T. Bretz, Saravanan Subramanian and James E. deVries (Ford Motor Company); Andrew Syvret, Andrew MacDonald and Peter Jolley (Aston Martin)
- Year of publication: 2005
- Journal/academic society of publication: SAE International
- Keywords: Not specified in the paper.
2. Abstract:
During the last decade, advances in magnesium die casting technology have enabled the production of large lightweight thin walled die castings that offer new approaches for low investment body construction techniques. As a result, many OEMs have expressed an interest in magnesium door closure systems due to investment reduction opportunities, coupled with potential weight savings of up to 50%. However, for such applications, product engineers are faced with the challenge of designing for stiffness and strength in crash critical applications with a material of lower modulus and ductility compared to wrought sheet product. Concept designs for side door systems have been presented in the literature, and indicate that structural performance targets can be achieved. However, to date, series production designs feature a multitude of supplementary sheet metal reinforcements, attached to die castings, to handle structural loads. While this approach can still offer performance benefits, the additional cost of tooling and assembly has a negative impact on both overall weight and the business rationale. On the contrary, the magnesium door concepts presented in this paper describe the development of side door systems designed to replace the bulk of sheet metal stampings by a single magnesium die casting. A summary of the design, analysis, prototyping and testing stages is reported, in addition to the development of a series production door system for a 2004 model year vehicle. A review of manufacturing and test results demonstrate how magnesium can be used effectively in the manufacture of low investment, lightweight vehicle closures.
3. Introduction:
The impact of vehicle mass on fuel economy is a significant factor in efforts to improve corporate average fuel economy. While vehicle curb weights declined in the early 1980s, the current trend of adding new features and functionality puts increased pressure on weight targets. OEMs have explored various materials and processes, including substituting steel with aluminum, though forming limitations of aluminum alloys can restrict their application. Hybrid door systems combining stampings, extrusions, and castings have been developed, but can increase assembly complexity and variable costs.
Magnesium offers properties like low density and high strength-to-weight ratio, making it an attractive material for mass reduction. Consequently, several structural magnesium castings have been reported, with applications growing to include larger, more complex die castings. A particular focus has been the development of die cast vehicle closure panels, with some production versions of liftgates and side doors emerging, notably by Mercedes for their CL and SL models. However, a common trend is to limit the loading of the magnesium casting and use supplementary reinforcements, which can negatively impact overall weight and assembly cost.
This paper details the development of a new magnesium door inner panel designed to eliminate supplementary stampings by integrating key reinforcements directly into the die-casting. This makes the magnesium panel an integral part of the door structure, contributing to both static and dynamic crash performance. The paper summarizes the design, analysis, and testing of an early concept, followed by the development of a production-intent door system for the MY2004 Aston Martin DB9. It also provides a weight assessment for both designs and an economic analysis comparing the technology to conventional steel stamping.
4. Summary of the study:
Background of the research topic:
The automotive industry faces continuous pressure to reduce vehicle mass for improved fuel economy and performance. Magnesium die casting technology offers a promising avenue for producing large, lightweight, thin-walled components, particularly for vehicle closures, with potential for investment reduction and significant weight savings. However, designing with magnesium for crash-critical applications requires addressing its lower modulus and ductility compared to traditional steel.
Status of previous research:
Previous research includes concept designs for magnesium side door systems indicating achievable structural performance. However, existing series production designs often incorporate numerous supplementary sheet metal reinforcements attached to the die castings to manage structural loads. This approach, while offering some benefits, adds cost, complexity, and weight, diminishing the overall advantages. Notable examples of magnesium closures include those on Mercedes CL and SL models, which also tend to use reinforcements.
Purpose of the study:
The primary purpose of this study was to develop a new magnesium door inner panel that eliminates the need for supplementary stampings by integrating key reinforcements into the die casting itself. The study aimed to demonstrate that a magnesium panel can serve as an integral part of the door structure, contributing to static and dynamic crash performance. Specific objectives included:
- Summarizing the design, analysis, prototyping, and testing of an initial concept.
- Detailing the development of a series production door system for the MY2004 Aston Martin DB9.
- Providing a weight assessment for both designs.
- Conducting an economic analysis to identify technology costs relative to conventional steel stamping.
Core study:
The study was conducted in two main phases:
- Concept Prove-Out (Ford Contour based): This phase involved developing and evaluating a magnesium door architecture based on the MY2000 Ford Contour. It included design using CAE, fabrication of prototypes via gravity sand casting, static durability testing, and development of a business rationale assuming high-pressure die casting for production.
- Production Implementation (Aston Martin DB9): Following concept evaluation, a production-intent door design was developed for the MY2004 Aston Martin DB9. This phase focused on crash performance and corrosion protection. A production die casting tool was manufactured, and components were produced for comprehensive testing, including manufacturing validation and cyclic corrosion testing.
5. Research Methodology
Research Design:
The research followed a two-phase development approach:
- Phase 1: Concept Prove-out (Ford Contour):
- Design based on a fully framed side door assembly (MY2000 Ford Contour).
- Prototypes fabricated using gravity sand casting.
- Technology evaluation through a combination of CAE and prototype testing for static durability.
- Development of a business rationale for high-pressure die casting.
- Phase 2: Implementation (Aston Martin DB9):
- Development of a production-intent door design for the MY2004 Aston Martin DB9.
- Focus on crash performance and corrosion protection.
- Manufacture of components using a production die casting tool.
- Cyclic corrosion testing to evaluate protection systems.
Data Collection and Analysis Methods:
- Computer-Aided Engineering (CAE): Finite element models were used to simulate system response for key loading conditions, including stiffness (torsion, lateral rigidity, sag, drop-off) and non-linear crash analysis (e.g., FMVSS-214 side impact).
- Prototype Testing:
- Static durability tests on Ford Contour prototypes: torsional rigidity, frame lateral rigidity, door dropoff, door sag, and door slam (84,000 cycles).
- Experimental Validation (Aston Martin DB9):
- Local strain data obtained from die-cast door inner panels using sub-size tensile test coupons (ASTM E8) from specific locations.
- Full vehicle side impact crash testing (static FMVSS-214).
- Corrosion Testing: Cyclic corrosion testing (Ford test method BI123-01, 100 cycles) on cast magnesium samples bonded to aluminum coupons, evaluating various surface pretreatments and coatings.
- Dimensional Analysis: Measurement of die castings produced during process development to assess adherence to tolerances.
- Economic Evaluation: Comparison of the fully accounted cost of the magnesium door assembly versus conventional steel stamping for different production volume scenarios (low and high automation/investment).
Research Topics and Scope:
- Primary Topic: Application of magnesium die casting technology to vehicle closures, specifically side doors.
- Key Areas of Investigation:
- Design of magnesium die-cast door inner panels for stiffness, strength, and crashworthiness.
- Integration of reinforcements into the die casting to reduce part count and assembly complexity.
- Achievable weight reduction compared to conventional steel doors.
- Manufacturing feasibility and challenges of large, thin-walled magnesium die castings.
- Evaluation and selection of suitable corrosion protection systems for magnesium in bimetallic assemblies.
- Economic viability of magnesium die-cast doors at various production volumes.
- Scope: The study encompassed the development process from an initial concept (based on a Ford Contour) through to a production-intent design implemented on a low-volume luxury vehicle (Aston Martin DB9).
6. Key Results:
Key Results:
Ford Contour Concept Phase:
- Weight Reduction: The magnesium door assembly (9.62kg) achieved a weight reduction of 5.94kg (38%) compared to the conventional stamped steel design (15.56kg) (Table 1). The magnesium inner panel and hardware module weighed 5.83kg, a 28% reduction from the 8.09kg steel inner panel with all reinforcements.
- Stiffness Benefits: The higher stiffness of the magnesium inner panel enabled the use of a low-density aluminum/plastic laminate for the outer panel, contributing significantly to weight savings (3.67kg vs. steel outer).
- Performance Testing (Table 2):
- CAE predictions indicated compliance with all five key test specifications.
- Experimental testing revealed a failure in torsional stiffness (5.7mm actual vs. <4mm requirement) and a higher-than-predicted door sag (13.3mm actual vs. 5.4mm CAE), though still within specification (<38mm). These discrepancies were attributed to prototype hinge pin clearance and plastic deformation of prototype hinges.
- Door slam durability testing was successful, with no damage after 84,000 cycles (three times life).
- Economic Analysis (Figure 4 & 5):
- At low production volumes (e.g., 10,000 vehicles per year), the magnesium door assembly was 13% less expensive than its steel counterpart, primarily due to part integration and reduced tooling investment.
- The breakeven point where steel stamping becomes more cost-effective was around 30,000 vehicles per year.
- Material price (baseline $2.90/kg) and machine utilization were identified as major factors influencing cost.
Aston Martin DB9 Implementation Phase:
- Design: A frameless door system with a non-modular architecture was developed. Major reinforcements, including the outer belt reinforcement, were integrated into the die-cast inner panel.
- Weight Savings:
- The prototype Aston Martin DB9 door inner panel weighed 3.711kg (Table 3), contributing to a total door-in-white assembly weight of 9.749kg.
- Further analysis for die filling led to localized thickness increases, resulting in a final magnesium inner panel weight of 4.32kg.
- The final DB9 door assembly was projected to offer a 43% weight saving relative to an equivalent stamped steel assembly.
- Static Durability (Figure 8): Wall thickness was optimized based on CAE and die casting fill simulations. For instance, a 20% increase in wall thickness in the upper hinge attachment area (section 5) resulted in a 36.4% increase in stiffness for door drop deflection.
- Crash Performance (AM50 Alloy):
- CAE simulations (FMVSS-214) indicated the door assembly would far exceed requirements (Figure 10).
- Experimental tensile tests on die-cast samples showed mean strains to failure exceeding requirements: >15% for latch, beam attachment, and waist rail areas, and up to 28% for the hinge area. The rocker region showed a mean of 8% (Figure 11).
- Full vehicle static FMVSS-214 side impact tests demonstrated performance exceeding requirements by 97% at 6" ram displacement, 87% at 12", and 60% at 18" (Figure 12). Ductile behavior was observed.
- Dimensional Control (Figure 13): Global tolerances were generally held to +/- 0.5mm. For a pre-production inner panel, 21 out of 22 measured points met specifications; one position was outside by 0.039mm, which was addressed by further die casting process adjustments.
- Corrosion Protection:
- Anodized base layers with a top coat offered the most effective protection.
- A chrome-based conversion coating combined with an epoxy-polyester powder coat performed almost as well and was selected for use due to cost considerations, with a planned transition to chrome-free systems.
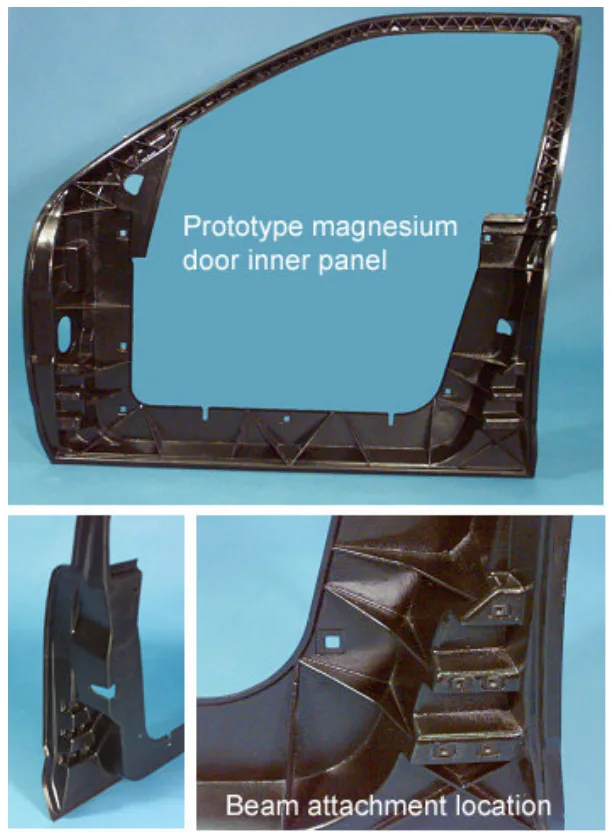
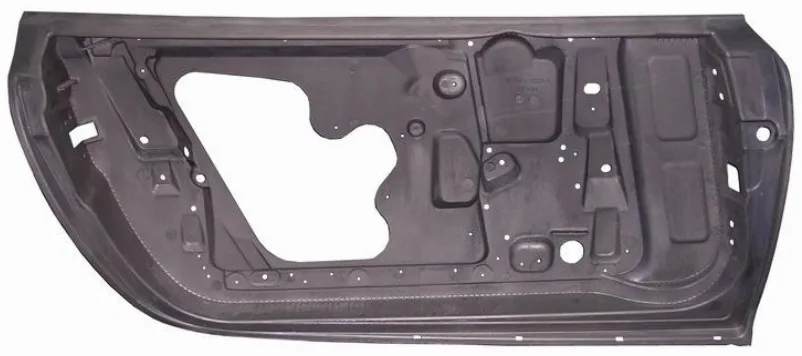
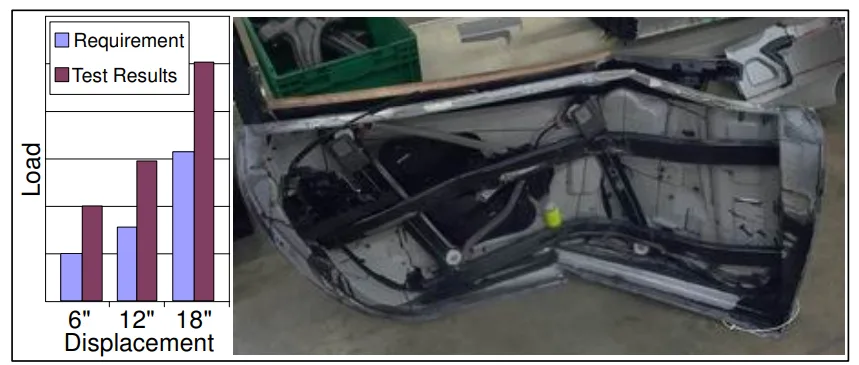
Figure Name List:
- Figure 1. Lightweight magnesium door architecture.
- Figure 2. Casting section thickness variations magnesium door inner panel.
- Figure 3. Magnesium door inner panel prototype based upon the MY2000 Ford Contour
- Figure 4. Economic comparison of conventional and magnesium door assemblies for the MY2000 Ford Contour.
- Figure 5. Sensitivity analysis of piece cost to model input data.
- Figure 6. Aston Martin DB9 magnesium door assembly.
- Figure 7. Aston Martin DB9 magnesium door inner panel.
- Figure 8. The effect of wall thickness on door drop off.
- Figure 9. FMVSS 214 test setup.
- Figure 10. Strain map of a preliminary magnesium door inner panel design following static FMVSS-214 testing.
- Figure 11. Mean tensile failure strains of castings by location (see Figure 10).
- Figure 12. FMVSS-214 side impact results for the DB9 magnesium door assembly.
- Figure 13. Dimensional data for a pre-production DB9 magnesium die cast door inner panel.
7. Conclusion:
The results from this two-stage development program demonstrate that a magnesium die casting can be effectively used as a fully structural member within a side door assembly. By replacing multiple metal stampings with a single magnesium casting that integrates key features, significant benefits were achieved. These include a reduction in part count, which simplifies the sub-assembly process, and a reduction in tooling investment. Furthermore, this approach provides an opportunity to optimize the design for both performance and weight. For the Aston Martin DB9 door in white assembly, projected weight savings were 43%.
An economic assessment indicated that for derivative programs at low to medium production volumes, this magnesium die casting technology could offer benefits at no cost penalty. However, for higher volume vehicles, the conventional stamped steel assembly remains the most cost-effective manufacturing route. A detailed analysis of the specific target application would be necessary to determine the precise breakeven volume for the two manufacturing technologies.
8. References:
- [1] http://www.nhtsa.dot.gov/cars/rules/cafe/NewPassengerCarFleet.htm.
- [2] Seksaria, D.C. and R.K. Patel. "An Ultra-Light Thin Sliding Door Design - A Multi Product Multi Material Solution." SAE Technical Paper Series, 2002-01-0391.
- [3] Balzer, J., et al. "Structural Magnesium Front End Support Assembly." SAE Technical Paper Series, 2003-01-0186.
- [4] Friedrich, H. and S. Schumann, "Research for a "new age in magnesium" in the automotive industry." Journal of Materials Processing Technology, 2001. 117(3): p. 276-281.
- [5] Jonason, P., et al. "MAGDOOR- Magnesium in Structural Application." SAE Technical Paper Series,1999-01-3198.
- [6] Schreckenberger, H., M. Papke, and S. Eisenberg. "The Magnesium Hatchback of the 3-Liter Car: Processing and Corrosion Protection." SAE Technical Paper Series, 2000-01-1123.
- [7] "Design of a magnesium/aluminum door frame", Automotive Engineering, 1993, Vol 101, 5,pp 57-60.
- [8] Federal Motor Vehicle Safety Standard 214, Side Impact Protection.
- [9] Ames, W. and W. Altenhof. "Observations of the Relative Performance of Magnesium and Aluminum Steering Wheel Skeletons with Identical Geometry." SAE Technical Paper Series, 2000-01-0784.
- [10] Aune, T. and L. Riopelle. "An Evaluation of the Mechanical Properties Critical to the Design of Interior Magnesium Components." SAE Technical Paper Series, 960415.
- [11] Alain, R. et al. "Robustness of Large Thin Wall Magnesium Die Castings for Crash Applications." SAE Technical Paper Series, 2004-01-0131.
- [12] Ford Laboratory Test Method BI 123-01. "Painted Sheet Metal Corrosion Test (Laboratory Simulated Arizona Proving Ground Test)", 2001.
- [13] Bretz, G.T., et al. "Adhesive Bonding and Corrosion Protection of a Die Cast Magnesium Automotive Door." The Minerals, Metals and Materials Society. 2004: Magnesium Technology 2004.
- [14] Blanchard, P.J., et al. "Evaluation of Corrosion Protection Methods for Magnesium Alloys in Automotive Applications." The Minerals, Metals and Materials Society, Magnesium Technology 2005.
9. Copyright:
- This material is a paper by "Patrick J. Blanchard, Gregory T. Bretz, Saravanan Subramanian, James E. deVries, Andrew Syvret, Andrew MacDonald and Peter Jolley". Based on "The Application of Magnesium Die Casting to Vehicle Closures".
- Source of the paper: https://doi.org/10.4271/2005-01-0338
This material is summarized based on the above paper, and unauthorized use for commercial purposes is prohibited.
Copyright © 2025 CASTMAN. All rights reserved.