This introduction paper is based on the paper "Effect of Core Temperature at HPDC on the Internal Quality of the Casting" published by "Archives of Foundry Engineering".
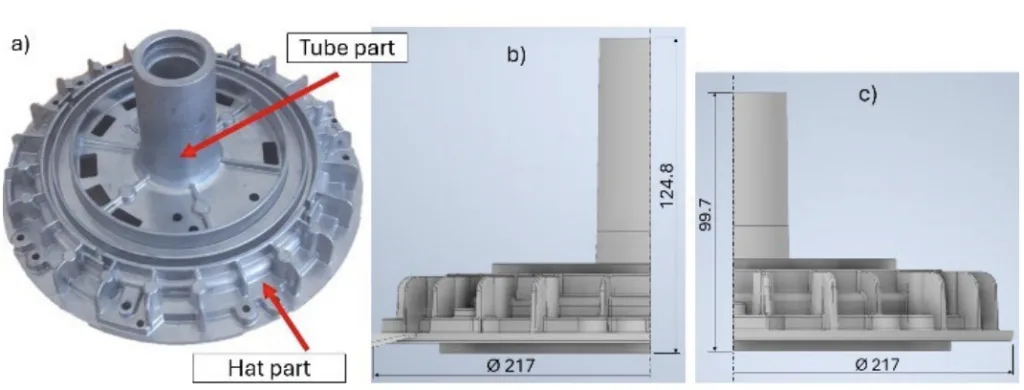
1. Overview:
- Title: Effect of Core Temperature at HPDC on the Internal Quality of the Casting
- Author: M. Matejka, D. Bolibruchová, R. Podprocká, P. Oslanec
- Year of publication: 2024
- Journal/academic society of publication: Archives of Foundry Engineering
- Keywords: HPDC, Al-Si-Cu alloy, Porosity, Microstructure
2. Abstract:
High pressure die casting (HPDC) is one of the most productive casting methods to produce a wide range of aluminum components with high dimensional accuracy and complex geometries. The process parameters of high-pressure casting generally directly affect the resulting quality of the castings, such as the presence of pores in the casting or the microstructure. In addition to air entrapment, porosity can also be caused by the dissolution of hydrogen. Hydrogen is released by the reaction of water vapor and melt at high temperatures and is released during solidification. These defects can lead to a significant reduction in mechanical properties such as strength and ductility and especially fatigue properties. The aim of the presented article is to describe the effect of the temperature of the core of the high-pressure mold on the presence and distribution of porosity and the microstructure of the aluminum casting in two geometric variants. The temperature of the core was changed due to the use of two flowing media in the thermoregulation circuit of the core, i.e. demineralized water and heat transfer oil and worked with a core temperature of 130 ± 5 and 165 ± 5 °C. With both geometric variants, a higher porosity was achieved when using water (core temperature 130 ± 5 °C) than when using oil (core temperature 165 ± 5 °C). The opposite results were observed for microporosity, where higher microporosity was observed for tempering oil. The microstructure of the casting with water-cooled cores was more characterized by finer grains of phase α (Al) and eutectic Si. In tempering oil, the microstructure was characterized by coarse grains of the α phase (Al) and the Si lamellae were in the form of sharp-edged formations.
3. Introduction:
High-pressure die casting is a complex process that takes into account a number of factors that significantly affect the final quality of the cast part. The basic parameters of the high-pressure die casting process are mainly the maintenance temperature, casting and molds temperature, hydrostatic pressure, or pressing pressure, and alloy flow rate in the inlet channel. The mechanical properties of a high-pressure die-cast product are primarily related to the temperature of the mold, the speed of the metal at the inlet and the applied casting pressure [1-3].
The combination of mold temperature, the fluidity of the molten metal, the complexity of the part geometry, and the cooling rate during high-pressure die casting all affect the integrity of the cast component. If these factors are not properly controlled, we can expect the appearance of various defects in the final casting. The thermal profile of the tool during operation is another important aspect of producing high quality components. Mold temperature is a key factor affecting heat removal from the molten metal, as well as for filling the mold and for correct setting of the casting properties [4-6]. A common source of defects in die casting is that the mold is not at the optimum temperature. This problem can be avoided by using a thermoregulating device [7,8].
The aim of the presented article is to assess the influence of the medium flowing in the thermoregulation circuit of the high-pressure die mold core on the change of the internal quality of castings in two geometric variants of the height of the casting tube. In the experimental part of the paper, we worked with demineralized water and heat transfer oil used as a medium for core temperature regulation. The internal quality of high-pressure die castings was evaluated by a combination of porosity analysis and structural analysis of selected critical locations on the casting. This evaluation should help us better understand how changing the thermoregulating medium affects the internal quality of castings.
4. Summary of the study:
Background of the research topic:
High-pressure die casting (HPDC) is a highly productive method for manufacturing aluminum components with precise dimensions and intricate shapes. The quality of HPDC parts is significantly influenced by process parameters, especially concerning porosity and microstructure. Porosity, beyond air entrapment, can arise from hydrogen dissolution and release during solidification, compromising mechanical properties like strength and fatigue resistance. Maintaining optimal mold temperature is crucial in HPDC to minimize defects and ensure casting integrity, often achieved through thermoregulating devices.
Status of previous research:
Previous research has established the critical role of mold temperature in high-pressure die casting. Factors such as mold temperature, molten metal fluidity, part geometry complexity, and cooling rates are known to affect casting integrity. Maintaining the correct mold temperature is essential for heat removal, mold filling, and setting casting properties. Existing studies emphasize the use of thermoregulating devices to address the common problem of molds not being at optimum temperatures in die casting [7, 8]. Research has also explored methods like conformal cooling [8] and alternative cooling systems [9] to improve mold temperature control.
Purpose of the study:
This study aims to investigate the impact of core temperature in high-pressure die casting molds on the internal quality of aluminum castings. Specifically, it focuses on how different cooling media within the thermoregulation circuit of the mold core affect porosity and microstructure. The research uses two geometric variations of a casting tube to assess these effects, aiming to enhance understanding of how thermoregulating media influence casting quality.
Core study:
The core study experimentally investigates the effect of core temperature, regulated by different cooling media (demineralized water and heat transfer oil), on the porosity and microstructure of AlSi12Cu1(Fe) alloy castings produced by HPDC. Two geometric variants of a casting, Statorbuchse EC 75 and EC 55, differing in tube height, were cast using both water (130 ± 5 °C core temperature) and heat transfer oil (165 ± 5 °C core temperature) as cooling media. The internal quality was assessed through porosity analysis using CT scanning and microstructure analysis using optical and scanning electron microscopy, focusing on critical locations of the castings.
5. Research Methodology
Research Design:
The research employed an experimental design comparing the effects of two different core cooling media (demineralized water and heat transfer oil) on the internal quality of HPDC aluminum alloy castings. Two geometric variants of a casting part (Statorbuchse EC 75 and EC 55) were used to assess the consistency of these effects across different geometries. The core temperature was controlled at two levels (130 ± 5 °C with water and 165 ± 5 °C with oil) while keeping other HPDC parameters constant.
Data Collection and Analysis Methods:
- Porosity Evaluation: Computed Tomography (CT scanning) using a NIKON - XT H225 ST device was utilized to evaluate porosity. CT images were analyzed quantitatively using Quickphoto industrial 3.2 program to determine the area share of pores and maximum pore length (Feret Diameter) in sections of the castings.
- Microstructure Analysis: Samples from critical locations were prepared and analyzed using:
- Optical Microscopy (OM) with a NEOPHOT 32 optical microscope.
- Scanning Electron Microscopy (SEM) with a VEGA LMU II scanning electron microscope.
- Energy Dispersive X-ray Spectroscopy (EDX) for elemental analysis.
Research Topics and Scope:
The research focused on the following topics:
- Effect of core temperature (regulated by water vs. oil cooling) on macro-porosity and micro-porosity in HPDC AlSi12Cu1(Fe) alloy castings.
- Influence of cooling media on the microstructure, specifically grain size of α-phase (Al), eutectic silicon morphology, and intermetallic phases.
- Comparison of these effects in two geometric variants (EC 75 and EC 55) of a stator housing casting.
- Investigation of porosity distribution and morphology in relation to the cooling medium used.
6. Key Results:
Key Results:
- Porosity: Higher macro-porosity was observed in castings produced with water-cooled cores (lower core temperature of 130 ± 5 °C) compared to oil-cooled cores (higher core temperature of 165 ± 5 °C) for both EC 55 and EC 75 variants. Conversely, higher micro-porosity was found in oil-tempered castings.
- Microstructure: Water-cooled castings exhibited finer grains of α-phase (Al) and eutectic Si with rounded shapes and lamellae. Oil-tempered castings showed coarser α-phase (Al) grains and sharp-edged lamellae of eutectic Si.
- Pore Distribution: Water cooling resulted in pores distributed throughout the entire volume of the casting, while oil cooling limited pore occurrence primarily to the upper 2/3 of the tube height in EC 55 castings. In EC 75 castings, water cooling significantly increased pore size and number, especially in critical areas.
- Cooling Rate: Water cooling, with its higher heat transfer coefficient, increased the cooling rate, leading to reduced macro-porosity but increased micro-porosity and refined microstructure. Heat transfer oil, with a lower cooling rate, resulted in higher macro-porosity but reduced micro-porosity and coarser microstructure.
Figure Name List:
- Fig. 1. Statorbuchse EC, a) Geometry, b) EC 75, c) EC 55
- Fig. 2. Section through the core and location of the core in the cast and marking of critical places on the cast with a red ellipse and sampling locations for microstructural analysis with a red ellipse
- Fig. 3. CT image of EC 55 casting; a) water-cooled (core temperatures 130 ± 5 °C), b) oil-tempered (core temperatures 165 ± 5 °C)
- Fig. 4. CT image of EC 75 casting; a) water-cooled (core temperatures 130 ± 5 °C), b) oil-tempered (core temperatures 165 ± 5 °C)
- Fig. 5. CT image of EC 75 casting after evaluating pore area fraction and average maximum pore length; a) water-cooled (core temperatures 130 ± 5 °C), b) oil-tempered (core temperatures 165 ± 5 °C)
- Fig. 6. EC 55 casting microstructure; a) cooled by water, b) tempered by oil
- Fig. 7. EC 75 casting microstructure; a) cooled by water, b) tempered by oil
- Fig. 8. Detail of eutectic Si in EC 55 casting; a) cooled by water, b) tempered by oil
- Fig. 9. EC 55 casting microstructure; a) cooled by water, b) tempered by oil
7. Conclusion:
The study concludes that the choice of cooling medium in the core thermoregulation circuit significantly affects the internal quality of HPDC aluminum castings. Using heat transfer oil resulted in lower macro-porosity, while using water led to a refined microstructure with finer grains and reduced micro-porosity in critical areas, albeit with increased macro-porosity. The results suggest that for applications where minimizing macro-porosity is paramount, heat transfer oil might be preferable. Conversely, for applications prioritizing refined microstructure and potentially accepting higher macro-porosity, water cooling could be advantageous. Maintaining precise temperature control of the work surface is crucial, and in this study, heat transfer oil was deemed more optimal for minimizing gas porosity, despite potential trade-offs in microstructure and increased shrinkage related porosity.
8. References:
- [1] Kalpakjian, S., Schmid, S.R. (2009). Manufacturing Engineering and Technology. (6th ed.). Pearson Ed Asia.
- [2] Sadeghi, M. & Mahmoudi, J. (2012). Experimental and theoretical studies on the effect of die temperature on the quality of the products in high-pressure die-casting process. Advances in Materials Science and Engineering. 1, 1-9. https://doi.org/10.1155/2012/434605.
- [3] Bruna, M., Bolibruchová, D., Pastircák, R. & Remisová, A. (2019). Gating system design optimization for investment casting process. Journal of Materials Engineering and Performance. 28(54), 3887-3893. DOI: 10.1007/s11665-019-03933-3.
- [4] Tavakoli, S., Ranc-Darbord, I. & Wagner, D. (2014). Thermal behavior of the mold surface in HPDC process by infrared thermography and comparison with simulation. In Proceedings of the 12th International Conference on Quantitative Infrared Thermography, July 2014. France, Bordeaux. DOI: 10.21611/qirt.2014.054.
- [5] Shin, S.-S. & Lee, S.-K., Kim, D. & Lee, B. (2021). Enhanced cooling channel efficiency of high-pressure die-casting molds with pure copper linings in cooling channels via explosive bonding. Journal of Materials Processing Technology. 297. 117235, 1-19. DOI: 10.1016/j.jmatprotec.2021.117235.
- [6] Pastircák, R., Scury, J. & Moravec, J. (2017). The effects of pressure during the crystallization on properties of the AlSi12 alloy. Archives of Foundry Engineering. 17(3), 103-106. DOI: 10.1515/afe-2017-0099.
- [7] Hu, H., Chen, F. Chen, X., Chu, Y. & Cheng, P. (2004). Effect of cooling water flow rates on local temperatures and heat transfer of casting dies. Journal of Materials Processing Technology. 148(1). 57-67. DOI: 10.1016/j.jmatprotec.2004.01.040.
- [8] Jarfors, A., Sevastopol, R., Karamchedu, S., Zhang, Q., Steggo, J. & Stolt, R. (2021). On the use of conformal cooling in high-pressure die-casting and semisolid casting. Technologies. 9(2), 39. https://doi.org/10.3390/technologies9020039.
- [9] Fiorentini, F., Curcio, P., Armentani, E., Rosso, C. & Baldissera, P. (2019). Study of two alternative cooling systems of a mold insert used in die casting process of light alloy components. Procedia Structural Integrity. 24, 569-582. DOI: 10.1016/j.prostr.2020.02.050.
- [10] Kimura, T, Yamagata, H. & Tanikawa, S. (2015). FEM stress analysis of the cooling hole of an HPDC die. IOP Conference Series: Materials Science and Engineering. 84, 012052, 1-7. DOI: 10.1088/1757-899X/84/1/012052.
- [11] Tool-Temp. (2023 April). Die casting - we provide you with perfect tool tempering. Retrieved April 08, 2024, form https://tool-temp.ch/en/industries-temperature-control-units/die-casting-industry-temperature-control-unit/.
- [12] Wang, R., Zuo, Y., Zhu, Q., Liu, X. & Wang, J. (2022). Effect of temperature field on the porosity and mechanical properties of 2024 aluminum alloy prepared by direct chill casting with melt shearing. Journal of Materials Processing Technology. 307, 117687, 1-13. https://doi.org/10.1016/j.jmatprotec.2022.117687.
- [13] Shen, X., Liu, S., Wang, X., Cui, C., Gong, P., Zhao, L., Han, X. & Li, Z. (2022). Effect of cooling rate on the microstructure evolution and mechanical properties of iron-rich Al-Si alloy. Materials. 15(2), 411, 1-10. DOI: 10.3390/ma15020411.
- [14] Li, L., Li. D., Mao. F., Feng, J., Zhang, Y. & Kang, Y. (2020). Effect of cooling rate on eutectic Si in Al-7.0Si-0.3Mg alloys modified by La additions. Journal of Alloys and Compounds. 826, 154206, 1-10. https://doi.org/10.1016/j.jallcom.2020.154206.
- [15] Niklas, A., Abaunza, U., Isabel, F. Lacaze, J. & Suarez, R. (2010). Thermal analysis as a microstructure prediction tool for A356 aluminium parts solidified under various cooling conditions. China Foundry. 59(11), 1167-1171.
9. Copyright:
- This material is a paper by "M. Matejka, D. Bolibruchová, R. Podprocká, P. Oslanec". Based on "Effect of Core Temperature at HPDC on the Internal Quality of the Casting".
- Source of the paper: https://doi.org/10.24425/afe.2024.151295
This material is summarized based on the above paper, and unauthorized use for commercial purposes is prohibited.
Copyright © 2025 CASTMAN. All rights reserved.