This introduction paper is based on the paper "Numerical and experimental analysis of a high pressure die casting Aluminum suspension cross beam for light commercial vehicles" published by "La Metallurgia Italiana".

1. Overview:
- Title: Numerical and experimental analysis of a high pressure die casting Aluminum suspension cross beam for light commercial vehicles
- Author: S. Cecchel, D. Ferrario
- Year of publication: 2016
- Journal/academic society of publication: La Metallurgia Italiana - n. 6 2016
- Keywords: ALUMINUM - HIGH PRESSURE DIE CASTING - SUSPENSION - CROSS BEAM - COMMERCIAL VEHICLE - LIGHTWEIGHT - AUTOMOTIVE
2. Abstract:
The purpose of the present paper is to enhance and deepen the lightweight optimization in automotive, in particular for commercial vehicles and buses. In detail, aim of this research is to develop a technically reliable and cost effective safety component for Light Commercial Vehicles (LCVs) in aluminum alloy. At this purpose, different solutions of Aluminium Cross beams for an independent front suspension for LCVs have been analyzed, with a weight saving target in comparison with the traditional welded sheet metal structure of almost 40/50%. Moreover, further environmental advantages have to be considered; for instance improved corrosion resistance, no painting or cataphoresis required, benefits on recyclability and residual value at the end of life. In detail, the goal of this project has been achieved through: technical and economical study of some different lightweighting solution and selection of the best case; improvement of the solution selected with the help of structural FEA and casting process simulations, a Life Cycle Assessment from cradle to grave (not here described), prototypes realization and preliminary experimental correlation.
3. Introduction:
Vehicle weight decrease is crucial for reducing the automotive carbon footprint, fuel consumption, and emissions, while also improving power-to-weight ratio, passenger safety, and payload capacity [1]. Consequently, lightweighting design in automotive has significantly increased. However, steel and iron remain predominant in commercial vehicles and buses, particularly for safety-relevant components [2], due to requirements for high stress resistance, stiffness, and cost limitations. Currently, no aluminum suspension cross beams are known to be developed for this vehicle range. The suspension cross beam is a critical component connecting the suspension, steering, and driveline elements to the vehicle frame, ensuring connection of kinematic "hard points". It must withstand fatigue, overload, and impulsive loads, provide high stiffness for handling, reduce vibrations, support potential overloads common in LCVs, and distribute stress effectively to the chassis frame. Traditionally, these are made from welded metal sheet parts or steel tubes, requiring corrosion protection. This research aims to overcome the current state of the art by developing a technically reliable and cost-effective aluminum alloy suspension cross beam for LCVs, optimizing both mechanical properties and material usage to be comparable or better than traditional steel systems.
4. Summary of the study:
Background of the research topic:
The automotive industry seeks lightweighting solutions to improve fuel efficiency, reduce emissions, and enhance vehicle performance and payload. For commercial vehicles (LCVs), safety components like suspension cross beams are traditionally made of steel due to high mechanical demands and cost constraints. Developing lightweight alternatives using materials like aluminum presents challenges but offers significant benefits.
Status of previous research:
While alternative materials like Advanced High Strength Steel, light alloys, and composites are explored for lightweighting, their application in LCV safety components is limited by cost and the need for high stress resistance and stiffness [2]. Specific technologies for creating hollow structures in die casting, such as salt cores, ceramic cores, or gas injection processes [3, 4], exist but require further development for sustainable industrialization in applications like LCV cross beams. At the time of the study, no aluminum suspension cross beam was known to be developed for this range of vehicles.
Purpose of the study:
The primary goal was to develop a technically reliable and cost-effective aluminum alloy suspension cross beam for LCVs, achieving a weight saving of 40-50% compared to traditional welded steel structures. Additional aims included leveraging environmental benefits like improved corrosion resistance (eliminating painting/cataphoresis), recyclability, and end-of-life value.
Core study:
The research involved analyzing different lightweighting solutions for an LCV front suspension cross beam (Fig. 1). Four concepts were initially considered: 1) HPDC aluminum, 2) LPDC and extruded aluminum, 3) LPDC and CFRP, 4) Extruded aluminum. After technical-economic analysis and preliminary FEA (structural MSC/MarcMentat, process ESI PROCAST), HPDC aluminum was selected as the most promising solution. The design was enhanced through further structural and process FEA iterations, using load inputs derived from elastokinematic multibody simulations (MSC/AdamsCar). A key innovation was substituting the traditional plane or "U" shape with a completely hollow structure, achieved using sliders along the total length of the component (Fig. 2), combined with the selection of AlSi9MgMn alloy (Tab. 1) for its favorable as-cast mechanical properties. Prototypes were produced using a high-tonnage (>= 3000 t) vacuum HPDC machine (Fig. 3) and analyzed experimentally (X-ray, 3D scanning) to validate FEA predictions regarding porosity and deformation (Fig. 4), leading to process optimization.
5. Research Methodology
Research Design:
The study employed a comparative analysis of different lightweighting concepts, followed by an iterative design optimization process for the selected HPDC aluminum solution. This involved integrating structural FEA, casting process simulation, and multibody dynamics simulation. The optimized design was then prototyped and subjected to experimental validation, correlating simulation results with physical measurements.
Data Collection and Analysis Methods:
Methods included:
- Benchmarking of suspension components.
- Technical and economical analysis of different lightweighting solutions.
- Finite Element Analysis (FEA): Structural analysis (MSC/MarcMentat) and casting process simulation (ESI PROCAST).
- Elastokinematic multibody modeling (MSC/AdamsCar) to determine load conditions.
- Material characterization (using data for AlSi9MgMn, Tab. 1).
- High Pressure Die Casting (HPDC) for prototype manufacturing.
- Non-destructive testing: X-ray analysis to identify internal porosity.
- Dimensional analysis: 3D scanning to measure deformation and verify hard point alignment.
- Comparison and correlation between simulation predictions (porosity, deformation) and experimental results.
Research Topics and Scope:
The research focused specifically on the design, analysis, and manufacturing of a lightweight aluminum suspension cross beam for Light Commercial Vehicles (LCVs). The scope included:
- Evaluation of different lightweight materials and processes (HPDC, LPDC, extrusion, CFRP).
- Selection and application of a specific aluminum alloy (AlSi9MgMn).
- Development and analysis of an innovative hollow component design using HPDC with full-length sliders.
- Simulation of structural performance and casting process feasibility.
- Consideration of manufacturing requirements (large HPDC machine, die design).
- Prototyping and experimental validation (porosity, dimensional accuracy).
- Comparison with the traditional steel component baseline in terms of weight and stiffness.
6. Key Results:
Key Results:
- High Pressure Die Casting (HPDC) aluminum was identified as the most lightweight and economically viable solution among the options considered.
- AlSi9MgMn alloy was selected (Tab. 1), providing good as-cast mechanical properties, crucial for avoiding deformations associated with high-temperature T6 heat treatment. A lower temperature T5 treatment was also evaluated for potential resistance increase.
- A novel, completely hollow cross beam structure was successfully designed and achieved using HPDC with sliders covering the entire component length (Fig. 2).
- This hollow design resulted in a component stiffness improvement of about 40% in the main vertical load direction compared to the steel baseline, confirmed by FEA.
- An overall lightweighting of 47% was achieved compared to the initial 35% target during optimization iterations, meeting the 40-50% goal versus the steel baseline.
- The high corrosion resistance of the low-iron, low-copper AlSi9MgMn alloy eliminated the need for cataphoresis and painting treatments.
- Prototypes were successfully manufactured on a high tonnage (at least 3000 t) vacuum HPDC machine, validating the feasibility of producing the large component (~1260x450 mm) with complex sliders (Fig. 3).
- X-ray analysis confirmed the presence of porosity in the thickest sections, consistent with FEM simulation predictions (Fig. 4a, 4b). Subsequent die modifications and iterative process parameter optimization minimized these porosities (Fig. 4c).
- Dimensional analysis showed maximum bending deformation of ~1.8 mm/edge, less than the simulated 3.8 mm, but coherent in direction. Correct hard points' alignment was achieved after optimization.
Fig. 1 - Cross beams: -1) HPDC aluminum, 2) LPDC and extruded aluminum, 3) LPDC and CFRP, 4) Extruded aluminum
Fig. 2 - a) Sliders layout b) Cross beam hollowed longitudinal section c) remarkable hollow sections
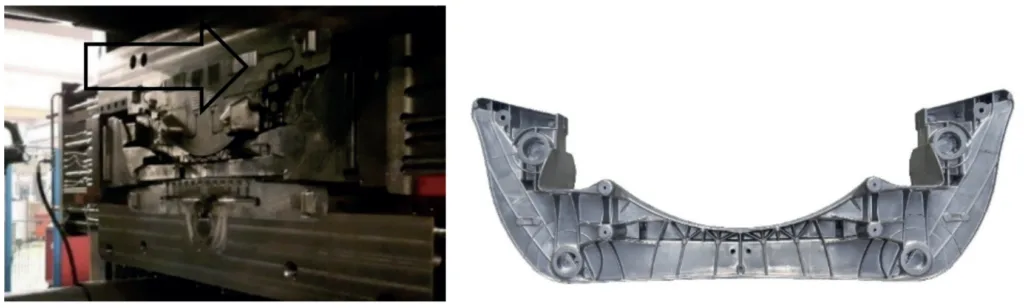
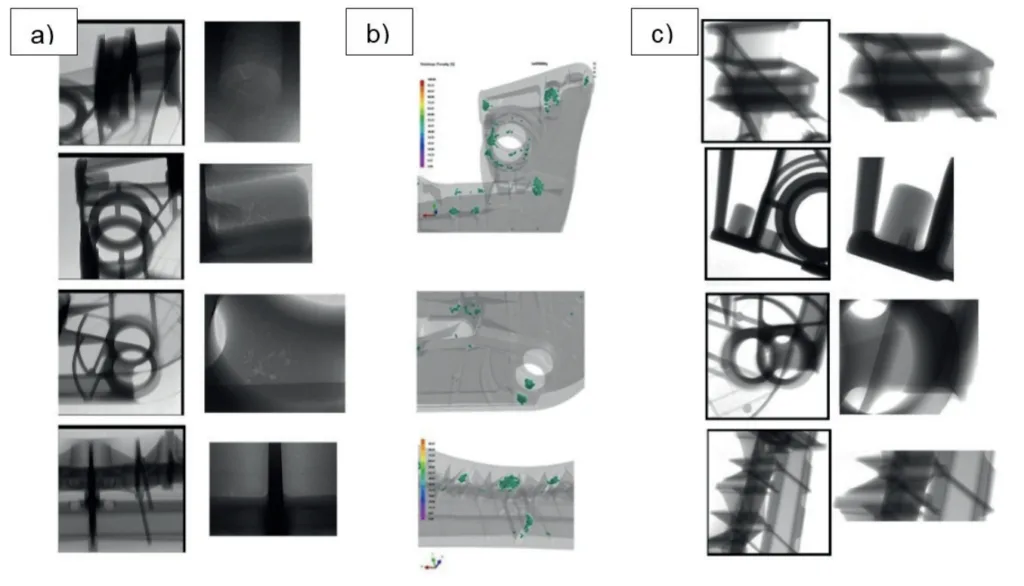
Figure Name List:
- Fig. 1 - Cross beams: -1) HPDC aluminum, 2) LPDC and extruded aluminum, 3) LPDC and CFRP, 4) Extruded aluminum
- Tab. 1 - Chemical composition AlSi9MgMn (left) [5], Mechanical properties AlSi9MgMn (right)[5]
- Fig. 2 - a) Sliders layout b) Cross beam hollowed longitudinal section c) remarkable hollow sections
- Fig. 3 - Dies and prototypes
- Fig. 4 - Porosity identify by a) X-ray on components from the first experimental activity, b) FEM simulations, c) X-ray on components from the final experimental activity (optimization of process parameters)
7. Conclusion:
The research successfully demonstrated the development of a technically reliable and cost-effective lightweight aluminum alloy suspension cross beam for LCVs using HPDC. By selecting the AlSi9MgMn alloy and implementing an innovative hollow structure design achieved through the use of full-length sliders, significant weight savings (47%) and stiffness improvements (~40% vs. steel) were realized. The feasibility of manufacturing this complex, large component via HPDC was confirmed through prototyping. Experimental analysis validated simulation predictions, and subsequent process optimization successfully minimized porosity and ensured correct dimensional accuracy, including hard point alignment. The project overcame traditional limitations, offering a viable lightweight alternative to steel for safety-critical LCV components. Next steps involve detailed validation through test bench road simulation, mechanical testing, and corrosion testing (salt spray).
8. References:
- [1] J. HIRSCH, Materials forum volume 28, (2004), p 15.
- [2] S.DAS, JOM, 8, (2000), p.41-44.
- [3] L. KALLIEN, T. WEIDLER, M. BECKER, International foundry research, 4, (2014), p. 20-27.
- [4] R.MOSCHINI, R.MOLINA, XXXI Congresso tecnico di fonderia ASSOFOND, (2012).
- [5] RHEINFELDEN, Leghe d'alluminio da pressocolata.
9. Copyright:
- This material is a paper by "S. Cecchel, D. Ferrario". Based on "Numerical and experimental analysis of a high pressure die casting Aluminum suspension cross beam for light commercial vehicles".
- Source of the paper: [DOI URL Not Provided in Paper]
This material is summarized based on the above paper, and unauthorized use for commercial purposes is prohibited.
Copyright © 2025 CASTMAN. All rights reserved.