The content of this introduction paper is based on the article [Fabrication and Investigation of Copper Rotor Bar on 0.5HP Induction Motor-A Performance and Economical Study] published by [Australian Journal of Basic and Applied Sciences].
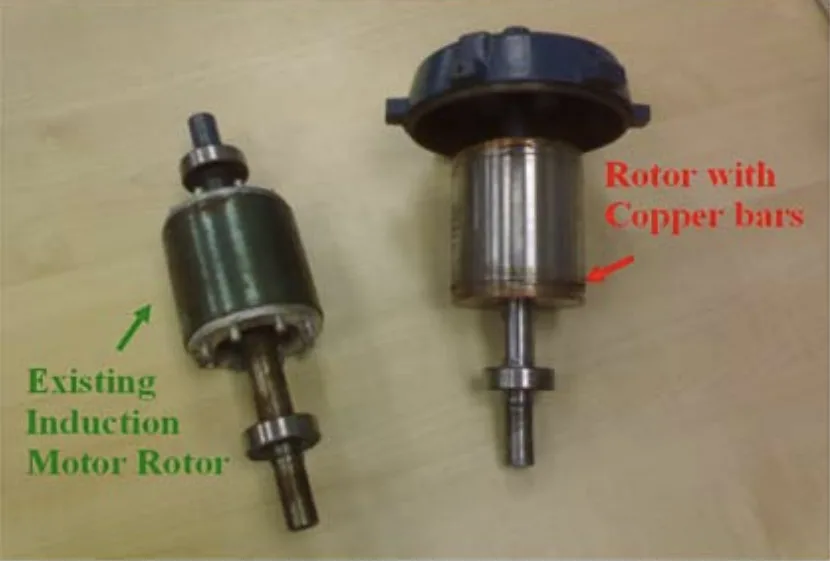
1. Overview:
- Title: Fabrication and Investigation of Copper Rotor Bar on 0.5HP Induction Motor-A Performance and Economical Study
- Author: I. Daut, N. Gomesh, Y. Yanawati, S. Nor Shafiqin, M. Irwanto, Y.M. Irwan, K. Anayet
- Year of publication: 2011
- Journal/academic society of publication: Australian Journal of Basic and Applied Sciences
- Keywords: Induction motor, Copper Rotor Bars, Efficiency, Losses, Energy Saving
2. Abstract:
The paper deals with the fabrication of copper rotor bars for a 0.5HP induction motor and then comparing it with the existing aluminium rotor bars. From this experiment the rotors are compared in terms of efficiency increment as well as losses reduction capabilities and an economical aspect is analyzed and explained. From this investigation it shows that copper rotor bars losses are reduced to ± 5 watts and 1% efficiency increment compared to aluminium rotor bars. The copper rotor has an annual energy savings (AES) of 40.32kWh/year per motor and total saving cost (TSC) per copper rotor motor is RM13.54. Finally a rough estimation of 100,000 pieces induction motor that have been replaced with the copper rotor bars is assumed and shows that it will save approximately RM1.3 million.
3. Introduction:
Induction motors are extensively used in various sectors. Motor systems are the largest industrial loads, accounting for more than 70 percent of all electricity consumption. In Malaysia, industrial sectors consume about 51.9% of the total electricity. Studies indicate that electrical motors use the highest amount of energy in industrial production. Using energy-efficient motors or copper rotor bars in place of conventional rotors are measures to reduce energy use. While aluminium has been considered for induction motors, it is noted that aluminium rotor bars are not suitable for high slip machines or machines with extremely high inertia loads due to higher temperature generation. Tempered copper alloys generally have a yield strength almost double that of tempered aluminium alloys. Fatigue failures in induction motor cages, including creep failures in copper bars at elevated temperatures and crack propagation due to thermal stresses during starting and cooling, have been observed. Negative sequence unbalance can also lead to excessive heating in rotor bars and vibrations.
4. Summary of the study:
Background of the research topic:
The research addresses the significant energy consumption of induction motors in industrial applications and explores the potential of using copper rotor bars as a means to improve efficiency and reduce losses compared to conventional aluminium rotor bars.
Status of previous research:
Previous research has discussed energy efficiency in motors, rotor failures in squirrel cage induction motors, and the use of aluminium in induction motors. Some studies highlighted the limitations of aluminium in high-slip or high-inertia applications due to temperature considerations. The fatigue life of induction motor cages and failure modes related to thermal stresses have also been reviewed.
Purpose of the study:
The purpose of this study is to fabricate copper rotor bars for a 0.5HP induction motor and experimentally compare its performance (efficiency and losses) with a motor using conventional aluminium rotor bars. The study also aims to analyze the economical benefits of using copper rotor bars in terms of energy savings and cost reduction.
Core study:
The core study involves the fabrication of a rotor with copper bars for a 0.5HP AC induction motor. This involved designing the rotor using AUTOCAD, ensuring it fits the existing stator frame. The fabrication process included stacking and welding lamination sheets, compressing copper powder into the rotor slots using a pressing station, and a multi-stage baking process in a furnace at different temperatures (200°C and 900°C) with controlled cooling. Copper end rings were then joined to the copper rotor. Argon gas purging was used during the process. The final step involved using an EDM wire cutter machine to shape the rotor. The performance of the motor with the copper rotor was then experimentally tested using no-load, blocked rotor, and DC resistance tests to determine efficiency and losses at the rated current. These results were compared with the performance of the same motor using its original aluminium rotor. An economic analysis was conducted to estimate annual energy savings and cost reduction based on the improved efficiency.
5. Research Methodology
Research Design:
The research employed an experimental design where a 0.5HP induction motor was modified by replacing its aluminium rotor bars with fabricated copper rotor bars. The performance of the motor with both types of rotors was then compared through laboratory testing.
Data Collection and Analysis Methods:
Data was collected through no-load, blocked rotor, and DC resistance tests conducted on the 0.5HP induction motor with both aluminium and copper rotor bars. The losses were segregated, and the efficiency was calculated using the measured data. The formula used for efficiency (η) calculation with the copper rotor is given as:
η = (1 - P_losses / P_in) × 100%
Economic analysis involved using the measured efficiency improvement and local electricity tariffs to calculate annual energy savings (AES) and total saving cost (TSC). The following equations were used for economic analysis:
AES = hp × L × 0.746 × hr × (100/E_std - 100/E_cr)
TSC = (AES × 12 × MonthlyDemandCharge) + (kWh_savings × Energycharge)
Research Topics and Scope:
The research focused on the fabrication and performance evaluation of copper rotor bars in a 0.5HP induction motor. The scope included comparing the losses and efficiency with the original aluminium rotor and conducting a preliminary economic feasibility assessment based on the observed improvements.
6. Key Results:
Key Results:
The experimental results showed that the induction motor with copper rotor bars exhibited reduced losses and increased efficiency compared to the motor with aluminium rotor bars. Specifically:
- Copper rotor bars reduced total losses by 5.11 Watts.
- The efficiency of the motor increased from 81.8% with aluminium rotor to 82.7% with copper rotor, an approximate increase of 1%.
- The annual energy savings (AES) per motor with copper rotor bars was estimated to be 40.32kWh/year.
- The total saving cost (TSC) per motor with copper rotor bars was calculated to be RM13.54 per year.
- A projection based on replacing 100,000 motors with copper rotor bars suggested a potential annual saving of approximately RM1.3 million.
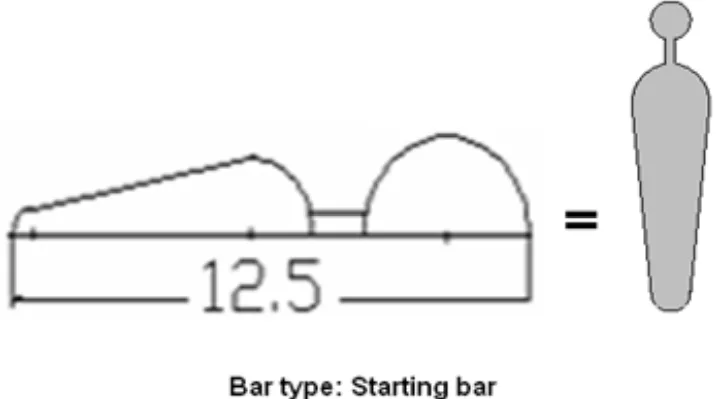
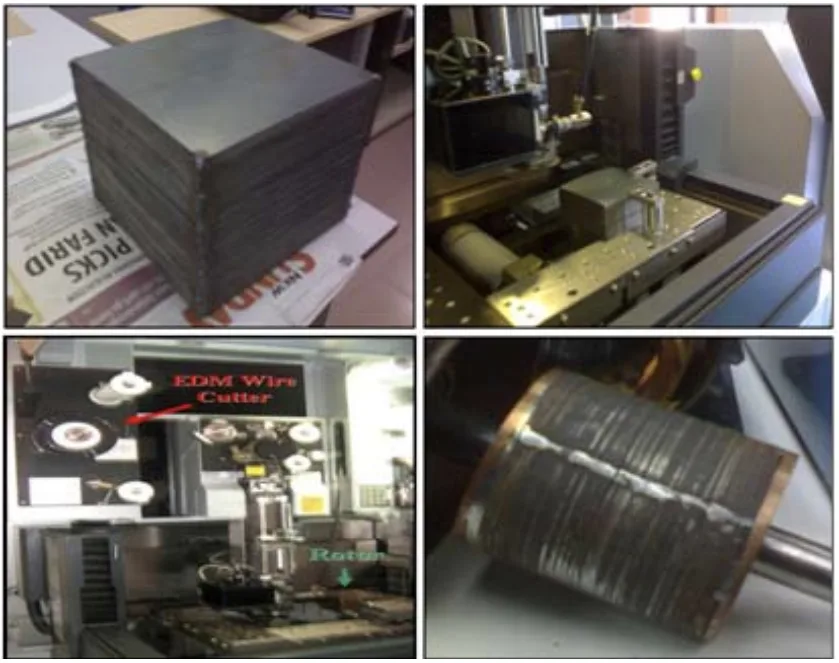
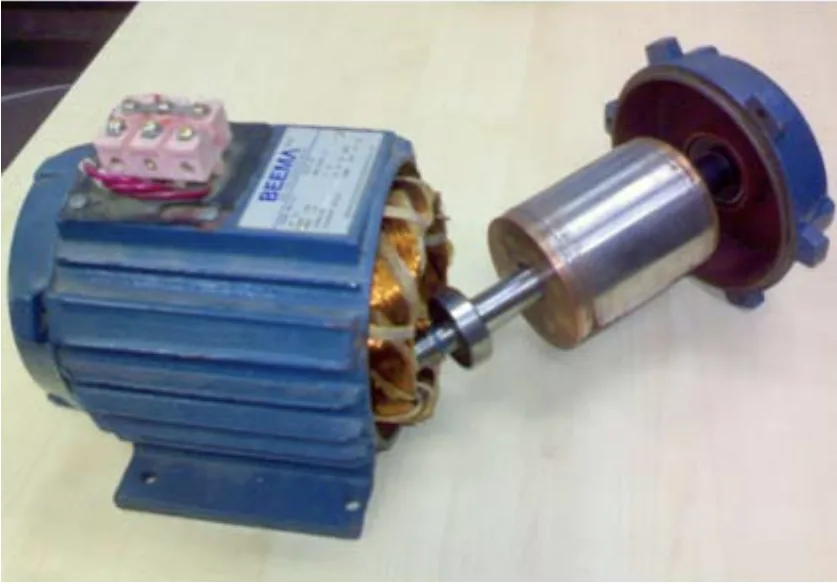
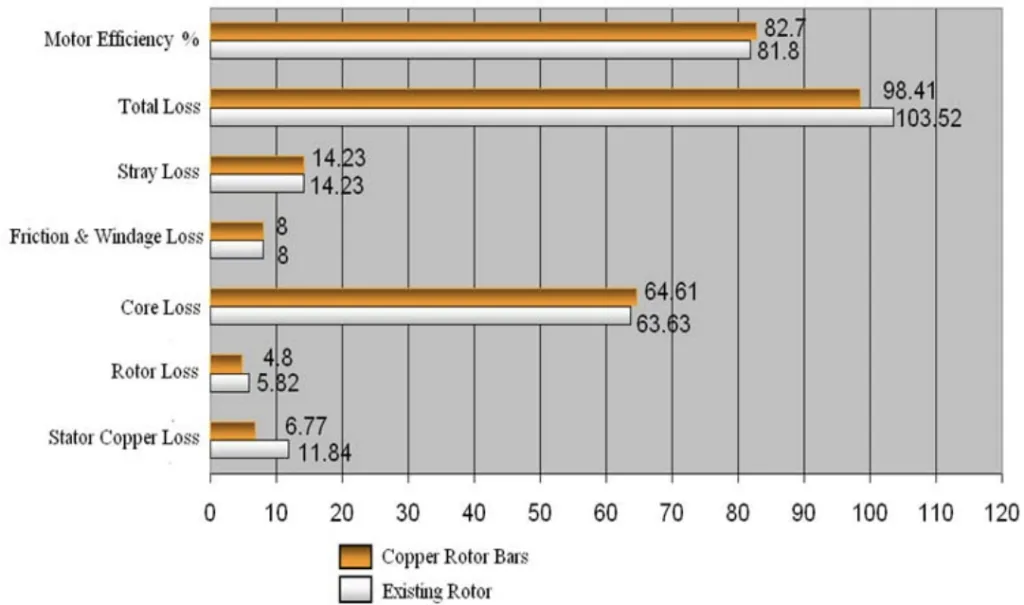
Figure Name List:
- Fig. 1: Dimension of Half Rotor Slot.
- Fig. 2: Copper Rotor Fabrication Procedures.
- Fig. 3: Copper Rotor of Induction Motor after Milling Process.
- Fig. 4: Copper Rotor assemble into the Induction Motor Stator.
- Fig. 5: Copper Rotor and Existing Rotor Performance.
7. Conclusion:
The study successfully fabricated and tested copper rotor bars in a 0.5HP induction motor. The experimental results demonstrate that using copper rotor bars leads to a reduction in losses and an increase in efficiency compared to the conventional aluminium rotor bars. The economic analysis indicates significant annual energy and cost savings per motor, with substantial potential savings if implemented on a larger scale. The findings suggest that replacing aluminium rotor bars with copper rotor bars in induction motors is a viable approach for improving energy efficiency and reducing operational costs.
8. References:
- Bonnett, A.H. and G.C. Soukup, 1988. “Analysis of Rotor Failures in Squirrel-Cage Induction Motors”, IEEE Trans. IA-24, Nov. /Dec., 1988: 1124-1130.
- Brandolino, J. and R.D. Findlay, 1994. “Practical Measurement of Symmetrical Component Currents in Induction Motors," Canadian Conference on Electrical and Computer Engineering, Halifax, NS, Canada, Sept. 25-28, 4pages.
- Craggs, J.L., 1976. “Fabricated Aluminum Cage Construction in Large Induction Motors,” IEEE Trans. IA-12, MaylJune, pp: 261-267.
- Dymond, J.H. and R.D. Findlay, 1995. “Some Commentary on the Choice of Rotor bar Material for Induction Motors", Ontario, Canada, IEE Transactions on Energy Conversion, 10(3).
- Hartung, E.C., 1994. “Fabricated Aluminum Rotor Construction for Induction Motors,” IEEE Conf. Pub. 0-7 803 -2028-x-June.
- Hassan, M.Y., M.S. Majid, and Abdul Rahman, Hasimah, 2000. Application Of Energy Efficient Motor In Malaysian Industries. TENCON 2000. Proceedings, 2: 97-102.
- Lomax, I.D., 1991. “Assessment of Induction Motor Cage Fatigue Life," 5th International Conference on ElectricalMachins and Drives, 11-13 Sept., 1991, London, UK, IEE Pub., 341: 281-284.
- Saidur, R., N.A. Rahim, H.H. Masjuki, S. Mekhilef, H.W. Ping, M.F. Jamaluddin, 2009. “End-use energy analysis in the Malaysian industrial sector", Energy 34 (2009) 153–158, University of Malaya, Kuala Lumpur, Malaysia.
9. Copyright:
- This material is a paper by "I. Daut, N. Gomesh, Y. Yanawati, S. Nor Shafiqin, M. Irwanto, Y.M. Irwan, K. Anayet". Based on "Fabrication and Investigation of Copper Rotor Bar on 0.5HP Induction Motor-A Performance and Economical Study".
- Source of the paper: [DOI URL will be added if available]
This material is summarized based on the above paper, and unauthorized use for commercial purposes is prohibited.
Copyright © 2025 CASTMAN. All rights reserved.