The content of this introduction paper is based on the article 'DEVELOPMENT OF THE COPPER MOTOR ROTOR - MANUFACTURING CONSIDERATIONS AND MOTOR TEST RESULTS' published by ['Session - 4 : Paper - 1'].
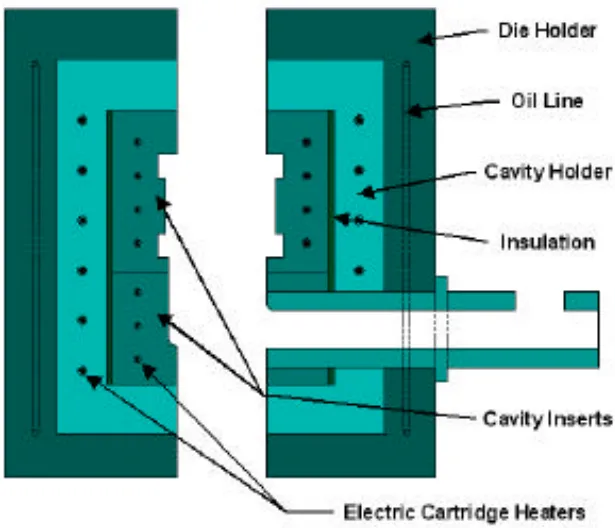
1. Overview:
- Title: DEVELOPMENT OF THE COPPER MOTOR ROTOR - MANUFACTURING CONSIDERATIONS AND MOTOR TEST RESULTS
- Author: Dr. D T Peters, Dr. J G Cowie, Dr. E F Brush, Jr., DJ Van Son, S P Midson, Prof. J L Kirtley, Jr.
- Year of publication: Not specified in the provided text.
- Journal/academic society of publication: Not specified in the provided text.
- Keywords: Copper motor rotor, die casting, die life, motor efficiency, thermal fatigue, slot design, porosity control.
2. Abstract:
The provided text does not contain an explicit abstract. However, the introduction and other sections summarize the work, which can serve as a basis for an abstract:
This paper summarizes the development of die-cast copper motor rotors, addressing the key challenge of short die life due to copper's high melting temperature. The research encompasses die material selection, die heating and insulation design, die casting process optimization, motor performance testing, and rotor bar design. Results indicate that nickel-base alloys operated at elevated temperatures (600-650°C) show promise for extended die life. Motors with die-cast copper rotors demonstrated significant efficiency improvements (1.2 percentage points or more) and loss reductions (averaging 14%) compared to aluminum rotors. Porosity control was achieved through shot profile optimization using Flow 3D simulations. Rotor bar design using the skin effect is also explored to further enhance motor performance.
3. Summary of the study:
Background of the research topic:
- Electrical conductivity of copper is nearly 60% higher than aluminum, suggesting potential for significant I2R loss reduction in motor rotors.
- Aluminum has been the material of choice due to the ease of manufacturing intricate squirrel cages via pressure die casting.
- Copper rotors have been limited to large motors and special applications due to the slow and costly fabrication methods.
- Die casting copper is required for cost-effective production, but short die life due to copper's high melting point has been a major obstacle.
Status of previous research:
- Motor modeling by manufacturers had shown potential for 15-20% overall loss reductions with copper rotors.
- Previous studies ([1], [2]) focused on die material selection and optimum conditions for maximizing die life.
- Some work on modeling of shot profiles to minimize porosity.
- Existing data on motors built with copper rotors were available.
Purpose of the study:
- To address the manufacturability of copper rotors, specifically the problem of short die life in pressure die casting.
- To evaluate the performance of motors incorporating die-cast copper rotors.
- To optimize rotor bar design to utilize copper effectively and minimize losses.
Core study:
- Investigation of high-temperature die materials and development of a practical die heating and insulation system.
- Die casting of copper rotors for evaluation by motor manufacturers.
- Dynamometer testing of motors with copper rotors and comparison with aluminum rotor performance.
- Frequency response modeling of rotor bars to guide slot design.
- Investigation into the origins of porosity and development of methods to eliminate it.
4. Research Methodology
Research Design:
- Multi-phase approach: die material study, die casting process development, motor performance testing, and rotor design optimization.
- Experimental: Die material testing using a test die simulating a single gate of a rotor die.
- Comparative: Motor performance testing comparing copper and aluminum rotors.
- Modeling: 3-D thermal modeling of die temperature profiles, frequency response modeling of rotor bars, and computational fluid dynamics (Flow 3D) for shot profile optimization.
Data Collection and Analysis Methods:
- Die Material Testing: Visual inspection for heat checking and cracking, chemical analysis of castings.
- Motor Performance Testing: Dynamometer testing according to IEEE Specification 112, test method B, and IEC 34-2 test method. Measurement of losses (iron core, stator resistance, rotor resistance, windage and friction, stray load), efficiency, temperature rise, full load speed, and power factor.
- Porosity Analysis: Sectioning of end rings and visual inspection, Flow 3D simulations.
Research Topics and Scope:
- Die materials: H-13 tool steel, molybdenum alloy TZM, tungsten alloy Anviloy, INCONEL alloys 617, 718, 754, 601, and 625.
- Motor sizes: 15 Hp (11.2 kW), 25 Hp (18.5 kW), 4 Hp (3 kW), and 5 Hp (3.7 kW).
- Process variables: Die temperature, shot speed profile, injection pressure, cooling method (water quench vs. air cool).
- Rotor design: Slot shape, skin effect utilization.
5. Key Results:
Key Results:
- INCONEL alloys 617 and 625 operated at 600-650°C showed promise as die materials for copper rotor die casting.
- A practical die heating and insulation design was developed (Fig. 1).
- Die-cast copper rotors showed high electrical conductivity (averaging no lower than 98% IACS).
- Motors with copper rotors exhibited significantly improved efficiency (1.2 percentage points or higher) and reduced losses (averaging 14%) compared to aluminum rotors (Table I, Table II, Table V).
- Rotor resistance losses were reduced by 40% in a 15 Hp motor (Table I).
- Stray load losses were reduced due to improved casting consistency.
- Slow pre-fill of the die cavity (40-55%) was found to be a strategy for avoiding large pore formation (Fig. 7).
- Rotor bar design using the skin effect can be used to tailor motor behavior (Fig. 12, Fig. 15).
Fig. 2 - Cross-section of rotor for three-phase motor showing copper filling the conductor bar slots.
Fig. 3 - Photographs of sectioned end rings from copper rotors typical of baseline die casting conditions.
Fig. 4 - Model of squirrel cage with gates and runner. Symmetry of the part allows simulation of the fill to be done on half of the model thereby saving computer run time.
Fig. 5 - Simulation of the gate end ring fill for the baseline shot profile used for production of copper rotors early in the program.
Fig. 6 - Photograph of copper rotor turned on the OD to expose the conductor bars. Trapped air bubbles are not seen in the bars but are clearly visible in the end ring.
Fig. 7 - Photographs of sectioned end rings with increasing pre-fill. Ejector end rings on left; gate end rings on right.
Figure Name List:
- Fig. 1 - Schematic illustration of the placement of electric resistance heaters and insulation in the die material tests.
- Fig. 2 - Cross-section of rotor for three-phase motor showing copper filling the conductor bar slots.
- Fig. 3 - Photographs of sectioned end rings from copper rotors typical of baseline die casting conditions.
- Fig. 4 - Model of squirrel cage with gates and runner. Symmetry of the part allows simulation of the fill to be done on half of the model thereby saving computer run time.
- Fig. 5 - Simulation of the gate end ring fill for the baseline shot profile used for production of copper rotors early in the program.
- Fig. 6 - Photograph of copper rotor turned on the OD to expose the conductor bars. Trapped air bubbles are not seen in the bars but are clearly visible in the end ring.
- Fig. 7 - Photographs of sectioned end rings with increasing pre-fill. Ejector end rings on left; gate end rings on right.
- Fig. 8 - Simple induction motor model.
- Fig. 9 - Torque speed curve as influenced by rotor resistance.
- Fig. 10 - Aluminum bar.
- Fig. 11 - Copper rotor bar.
- Fig. 12 - Rotor bar impedance.
- Fig. 13 - Copper vs. aluminum.
- Fig. 14 - Copper rotor bar.
- Fig. 15 - Comparison of two copper rotor bar impedances.
6. Conclusion:
Summary of Key Results:
- The research demonstrated the feasibility of die-casting copper motor rotors with improved die life and enhanced motor performance.
- Nickel-base alloys, operated at elevated temperatures, are promising die materials.
- Significant efficiency improvements and loss reductions are achievable with copper rotors.
- Porosity can be controlled through optimized shot profiles.
- Rotor bar design can be tailored to utilize the skin effect and improve motor characteristics.
Limitations of the Study:
- The die material tests were not extended production runs.
- Some motor tests were conducted with laminations designed for aluminum rotors, not optimized for copper.
- The economic analysis was preliminary.
7. Future Follow-up Research:
- Directions for Follow-up Research
- Conduct extended production runs to fully validate die material performance.
- Optimize lamination slot design and other motor components for copper rotors.
- Conduct a complete economic analysis.
- Further investigate the limits of pre-fill for porosity control.
- Areas for Further Exploration
- Explore other candidate die materials, such as Haynes alloy 230.
- Develop and test additional rotor bar designs to optimize torque characteristics and minimize stray load losses.
8. References:
- [1] Peters D T, Cowie J G, Brush E F Jr., and Midson S P: Advances in Pressure Die Casting of Electrical Grade Copper; Amer. Foundry Society Congress Paper No. 02-002, Kansas City, MO., 2002.
- [2] Peters D T, Cowie J G, Brush E F Jr., and Midson S P: Use of High Temperature Die Materials and Hot Dies for High Pressure Die Casting Pure Copper and Copper Alloys; Trans. of the North Amer. Die Casting Assoc. Congress, Rosemont, IL, 2002.
- [3] DOE/CS-0147 - U. S. Department of Energy; Classification and Evaluation of Electric Motors and Pumps; February, 1980.
- [4] Benedyk J C, Moracz D J and Wallace J F: Thermal Fatigue Behavior of Die Materials for Aluminum Die Castings; Trans. of SDCE, Paper No. 111, 1970.
- [5] Herman E A, Wallace J F and Machonis A A: Copper Alloy Pressure Die Casting, p 52 - Book; International Copper Research Assoc., Inc. 1975.
- [6] Doehler H H: Die Casting, pp 163-165 - Book; McGraw-Hill Book Co., Inc., New York, 1951.
- [7] Lie S and Di Pietro C: Copper Die-Cast Rotor Efficiency, Improvement and Economic Consideration; IEEE Trans. Energy Convers., vol 10, no. 3, pp 419-424, September 1995.
- [8] Poloujadoff M, Mipo J C and Nurdin M: Some Economical Comparisons Between Aluminum and Copper Squirrel Cages; IEEE Trans. Energy Convers., vol 10, no. 3, pp 415-418, September 1995.
- [9] Private communication with manufacturer.
- [10] Peters D T, Midson, S P, Walkington, W G, Brush, E F Jr. and Cowie J G: Porosity Control in Copper Rotor Die Castings; Trans. of the North Amer. Die Casting Assoc. Congress, Indianapolis, IN, 2003.
9. Copyright:
- This material is a paper by "Dr. D T Peters, Dr. J G Cowie, Dr. E F Brush, Jr., DJ Van Son, S P Midson, Prof. J L Kirtley, Jr.". Based on "DEVELOPMENT OF THE COPPER MOTOR ROTOR - MANUFACTURING CONSIDERATIONS AND MOTOR TEST RESULTS".
- Source of the paper: Not provided in the document.
This material is summarized based on the above paper, and unauthorized use for commercial purposes is prohibited.
Copyright © 2025 CASTMAN. All rights reserved.