This introductory paper is the research content of the paper "A NOVEL ALUMINIUM ALLOYS DESIGN STRATEGY FOR LOW USAGE OF CRITICAL RAW MATERIALS AND HIGH CASTING PROCESSIBILITY FOR AUTOMOTIVE APPLICATIONS" published by International Journal of Metalcasting.
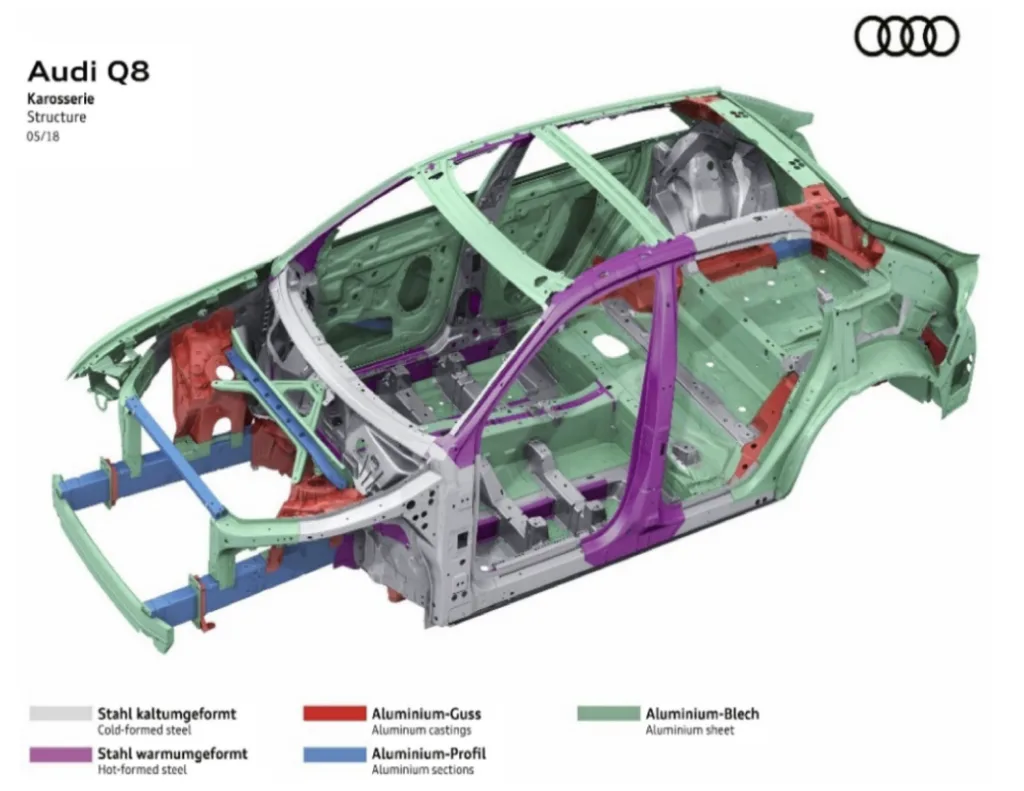
1. Overview:
- Title: A NOVEL ALUMINIUM ALLOYS DESIGN STRATEGY FOR LOW USAGE OF CRITICAL RAW MATERIALS AND HIGH CASTING PROCESSIBILITY FOR AUTOMOTIVE APPLICATIONS
- Author: Osama Asghar, Mattia Franceschi, Paolo Ferro and Franco Bonollo
- Publication Year: 2025
- Published Journal/Society: International Journal of Metalcasting
- Keywords: aluminium alloys, critical raw materials, high pressure die casting, alloy design
2. Abstract
The fifth critical raw materials (CRMs) list published by the European Commission (EC) in 2023 poses new restrictions to the usage of lightweight materials in the transportation industry. As per the publication, aluminium (one of the most widely used lightweight metals in the aerospace and automotive industry) has been declared as CRM and an increased criticality trend in its major alloying elements e.g. silicon and magnesium has been observed. Therefore, a novel approach is required to implement the criticality concept in developing new aluminium alloys and their processing for different components in the automotive industry. The present study aims to describe the strategy required to reduce the usage of CRMs in aluminium alloys along with enhanced high-pressure die casting (HPDC) processibility. By integrating criticality and castability assessment, a contribution to the development of sustainable and high-strength aluminium alloys to meet the demands of modern manufacturing while addressing the global resource challenges is presented. This study will also support the implementation of the CRMs concept in materials research and development.
3. Research Background:
Background of the research topic:
Sustainability is a major driver for industrial innovation. The automotive industry is focused on optimizing energy efficiency and reducing CO2 emissions. Material selection and design are key to achieving environmental sustainability.
Status of previous research:
Lightweight metals, particularly aluminium alloys, are crucial for reducing vehicle weight and improving fuel efficiency. However, the European Commission has identified aluminium and its key alloying elements (Si, Mg) as Critical Raw Materials (CRMs) due to supply risks and economic importance. Previous research has focused on lightweighting, but not explicitly on minimizing CRM usage in alloy design.
Need for research:
A new approach is needed to design aluminium alloys that minimize the use of CRMs while maintaining or improving the processability, especially for High-Pressure Die Casting (HPDC), a key manufacturing process in the automotive industry.
4. Research purpose and research question:
Research purpose:
To propose a methodology to reduce CRMs in lightweight material selection, specifically aluminium alloys, while ensuring high HPDC processability.
Core research:
Develop a strategy that integrates criticality assessment (minimizing CRM content) and castability assessment (optimizing HPDC processability) for designing new aluminium alloys.
5. Research methodology
The research methodology combines the material selection methodology of Ashby et al.44 with computational tools, primarily the CALPHAD (CALculation of PHAse Diagram) approach. The design process involves:
- Material Library Creation: Selecting a starting aluminium alloy and creating a library of alloys by substituting CRMs (Si, Mg) with non-CRM elements.
- Mechanical Performance Estimation: Assessing the mechanical properties achievable with the modified compositions.
- Castability Evaluation: Evaluating key castability characteristics (fluidity, solidification shrinkage, slag/dross formation, die soldering, hot tearing) using CALPHAD and newly developed models.
- Criticality Assessment: Calculating a criticality index for each alloy composition based on the work of Ferro et al.22,59,60.
- Optimization: Selecting alloy systems that offer the best compromise between processing properties, mechanical performance, and low criticality.
- Experimental Validation: Future experimental campaigns to verify the optimal solutions.
6. Key research results:
Key research results and presented data analysis:
The paper presents a framework for alloy design, not specific alloy compositions or experimental data. Key results include:
- A detailed explanation of the criticality concept and its relevance to aluminium alloys.
- Identification of key castability characteristics for HPDC: fluidity, solidification shrinkage, slag/dross formation, die soldering, and hot tearing.
- Description of methods to evaluate these characteristics using CALPHAD and other models.
- Presentation of equations for calculating a criticality index (CICRM) for individual raw materials and an overall alloy criticality index (CIA).
- Proposal of a multi-objective strategy to combine criticality and castability indexes, leading to a ranking of alloy compositions.
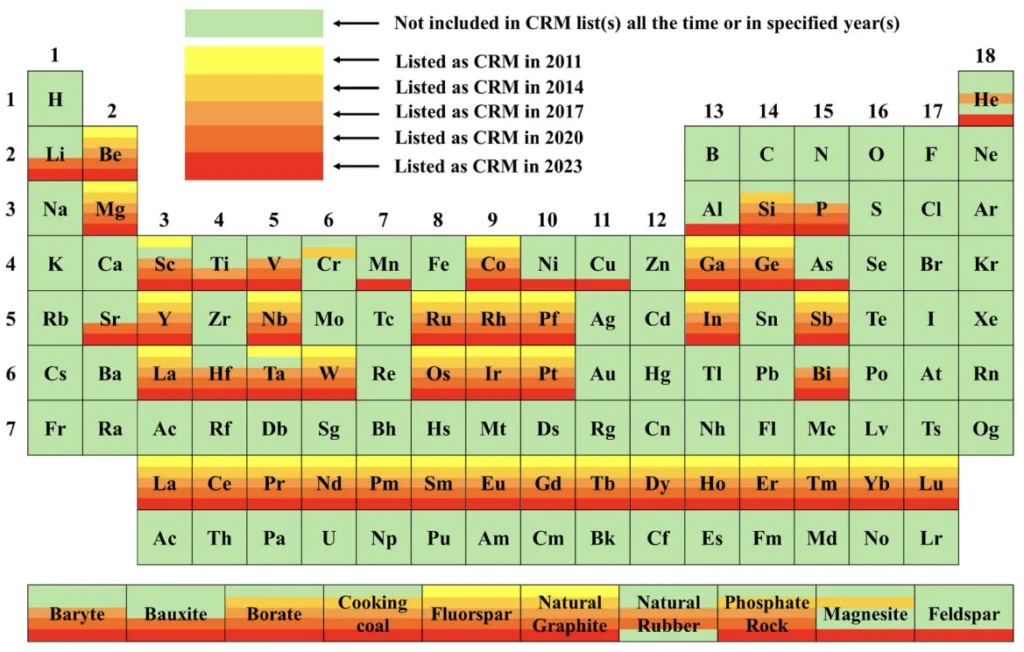
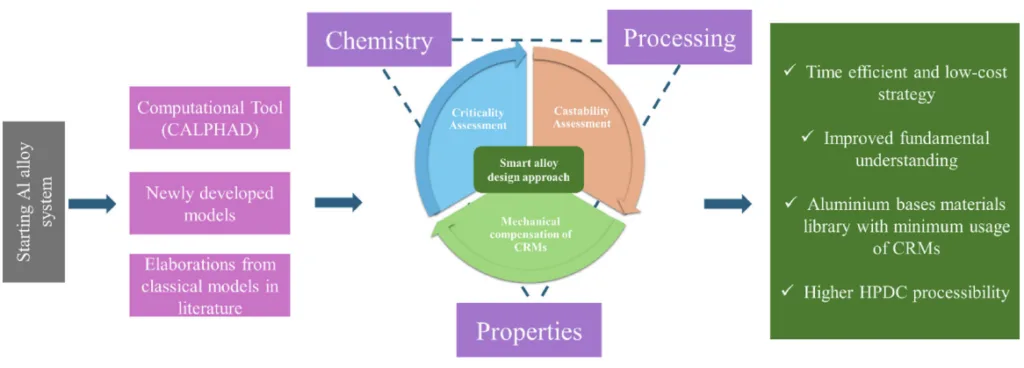
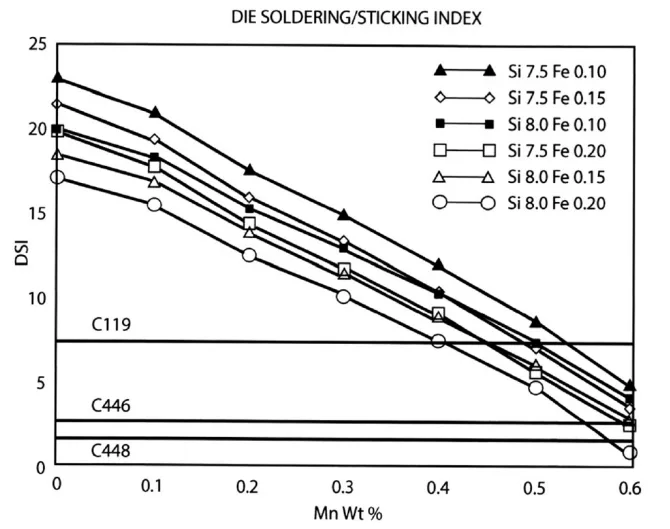
List of figure names:
- Figure 1. European CRMs assessment from 2011 to 2023.
- Figure 2. Classification of aluminium forming processes used in Audi Q8 BIW structure; adapted from Ref 30.
- Figure 3. Novel alloy design and development strategy for innovative aluminium alloys.
- Figure 4. Solidus temperatures for an aluminum-4 wt pct iron-X system.74
- Figure 5. Die soldering index in several die casting alloys.75
7. Conclusion:
Summary of key findings:
A new theoretical and systematic approach has been developed to design lightweight aluminium alloys for the automotive industry with low content of CRMs, with adequate processability and good mechanical performance. The developed procedure consists of defining indexes that consider the content of critical raw materials and the main parameters influencing the processability of alloys produced by casting processes.
The research provides a framework for designing sustainable aluminium alloys by minimizing reliance on critical raw materials. It has both academic significance (integrating criticality into alloy design) and practical implications (developing alloys suitable for automotive HPDC applications). The multi-objective approach allows for a balanced consideration of performance, processability, and resource sustainability.
8. References:
- [1] C. Fetting, The European green deal. ESDN Rep. 53, 24 (2020)
- [2] P.K. Mallick, Materials, design and manufacturing for lightweight vehicles. (2020) pp. 25–32, https://doi.org/10.1016/C2018-0-04153-5
- [3] A. Morita, Aluminum alloys for automobile applications. In Proceedings of the Proc. 6th (ICAA 1998), pp. 25-32
- [4] M. Franceschi, R. Bertolini, A. Fabrizi, M. Dabalà, L. Pezzato, Effect of ausforming temperature on bainite morphology in a 3.2% Si carbide-free bainitic steel. Mater. Sci. Eng. A (2023). https://doi.org/10.1016/j.msea.2022.14455
- [5] M. Franceschi, C. Soffritti, A. Fortini, L. Pezzato, G.L. Garagnani, M. Dabalà, Evaluation of wear resistance of a novel carbide- free bainitic steel. Tribol. Int. (2023). https://doi.org/10.1016/j.triboint.2022.108071
- [6] B. Ravishankar, S.K. Nayak, M.A. Kader, Hybrid composites for automotive applications—a review. J. Reinf. Plast. Compos. 38, 835–845 (2019). https://doi.org/10.1177/0731684419849708
- [7] A.A. Luo, Recent advances in light metals and manufacturing for automotive applications. CIM J. 12, 79–87 (2021). https://doi.org/10.1080/19236026.2021.1947088
- [8] S. Ray, R.P. Cooney, Thermal degradation of polymer and polymer composites. In Handbook of Environmental Degradation of Materials 3rd Edn. (2018; pp. 185-2026)
- [9] A.L. Robinson, A.I. Taub, G.A. Keoleian, Fuel efficiency drives the auto industry to reduce vehicle weight. MRS Bull. 44, 920–922 (2019). https://doi.org/10.1557/mrs.2019.298
- [10] W.S. Miller, L. Zhuang, J. Bottema, A.J. Wittebrood, P. De Smet, A. Haszler, A. Vieregge, Recent development in aluminium alloys for the automotive industry. Mater. Sci. Eng. A 280, 37–49 (2000). https://doi.org/10.1016/S0921-5093(99)00653-X
- [11] E. Georgantzia, M. Gkantou, G.S. Kamaris, aluminium alloys as structural material: a review of research. Eng. Struct. (2021). https://doi.org/10.1016/j.engstruct.2020.111372
- [12] T. Dursun, C. Soutis, Recent developments in advanced aircraft aluminium alloys. Mater. Des. 56, 862–871 (2014). https://doi.org/10.1016/j.matdes.2013.12.002
- [13] N. Prasad Rambabu, V.V.K. Eswara Prasad, R.J.H. Wanhill, Aerospace materials and material technologies volume 1: aerospace material technologies. Aerosp. Mater. Mater. Technol. (2017). https://doi.org/10.1007/978-981-10-2134-3
- [14] D. Zhou, Z. Kang, X. Su, Study on squeeze casting process of the integrated aluminum alloy subframe. Int. J. Met. 18, 1085–1106 (2024). https://doi.org/10.1007/s40962-023-01087-6
- [15] Q. Wang, A. Bobel, M. Walker, D. Hess, H. Doty, D. Gerard, Evaluation of two new cast aluminum alloys for high performance cylinder heads. Int. J. Met. (2024). https://doi.org/10.1007/s40962-024-01341-5
- [16] Duckerfrontier Aluminium content in European passenger cars. Eur. Alum. 1–23 (2019)
- [17] COMMISSION OF THE EUROPEAN COMMUNITIES The raw materials initiative—meeting our critical needs for growth and jobs in Europe. (2008), 14
- [18] COMMISSION OF THE EUROPEAN COMMUNITIES Tackling the challenges in commodity markets and on raw materials. (2011)
- [19] COMMISSION OF THE EUROPEAN COMMUNITIES On the review of the list of critical raw materials for the EU and the implementation of the raw materials initiative. Eur. Comm. Brussels, Belgium COM no. 297 (2014)
- [20] COMMISSION OF THE EUROPEAN COMMUNITIES Comunication from the Commission to EU Parliament on the 2017 List of Critical Raw Materilas for EU 490 (2017)
- [21] COMMISSION OF THE EUROPEAN COMMUNITIES Study on the Review of the List of Critical Raw Materials - Critical Raw Materials Factsheets (2020)
- [22] M. Grohol, C. Veeh, OMMUNITIES, C.O.T.E. Study on the Critical Raw Material for the EU; Publication Office of the European Union (2023)
- [23] V. Kumar, H. Mehdi, A. Kumar, Effect of silicon and lead contents on the mechanical properties of aluminum alloy. Int. J. Mech. Eng. Technol. 2, 1326–1330 (2015)
- [24] S. Ji, D. Watson, Z. Fan, M. White, Development of a super ductile diecast Al-Mg-Si alloy. Mater. Sci. Eng. A 556, 824–833 (2012). https://doi.org/10.1016/j.msea.2012.07.074
- [25] M. Król, T. Tański, P. Snopiński, B. Tomiczek, Structure and properties of aluminium-magnesium casting alloys after heat treatment. J. Therm. Anal. Calorim. 127, 299–308 (2017). https://doi.org/10.1007/s10973-016-5845-4
- [26] M. Hofmann, H. Hofmann, C. Hagelüken, A. Hool, Critical raw materials: a perspective from the materials science community. Sustain. Mater. Technol. 17, e00074 (2018). https://doi.org/10.1016/j.susmat.2018.e00074
- [27] M. Tanwir Alam, A. Husain Ansari, Review on aluminium and its alloys for automotive applications Maulana Mukhtar Ahmad Nadvi Technical Campus Malegaon. pp. 278–294 (2017)
- [28] N. Parson, J. Fourmann, J.F. Beland, aluminum extrusions for automotive crash applications. SAE Tech. Pap. (2017). https://doi.org/10.4271/2017-01-1272
- [29] J. Mendiguren, E.S. De Argandona, L. Galdos, Hot Stamping of AA7075 Aluminum Sheets. IOP Conference Series Material Science English 159, (2016). https://doi.org/10.1088/1757-899X/159/1/012026.
- [30] Centre, A.M. Audi Q8 Body Available online: https://www.audi-mediacenter.com/en/the-audi-q8-the-new-top-model-of-the-q-family-10412/body-10419
- [31] M. Jinta, Y. Sakai, M. Oyagi, S. Yoshizawa, K. Matsui, K. Noda, Press Forming analysis of aluminum auto body panel: wrinkle behavior in 5000 and 6000 series aluminum alloy sheet forming. JSAE Rev. 21, 407–409 (2000). https://doi.org/10.1016/S0389-4304(00)00039-4
- [32] F. Bonollo, N. Gramegna, G. Timelli, High-pressure die-casting: contradictions and challenges. Jom 67, 901–908 (2015). https://doi.org/10.1007/s11837-015-1333-8
- [33] X. Dong, H. Yang, X. Zhu, S. Ji, High strength and ductility aluminium alloy processed by high pressure die casting. J. Alloys Compd. 773, 86–96 (2019). https://doi.org/10.1016/j.jallcom.2018.09.260
- [34] X. Dong, X. Huang, L. Liu, L. He, P. Li, A liquid aluminum alloy electromagnetic transport process for high pressure die casting. J. Mater. Process. Technol. 234, 217–227 (2016). https://doi.org/10.1016/j.jmatprotec.2016.03.028
- [35] H. Blala, C. Pengzhi, Z. Shenglun, C. Gang, R. Shangwen, M. Zhang, Innovative hybrid high-pressure die-casting process for load-bearing body-in-white structural components. Int. J. Met. (2024). https://doi.org/10.1007/s40962-024-01280-1
- [36] N. Gramegna, F. Bonollo, Smart control and cognitive system applied to the HPDC foundry 4.0: a robust and competitive methodology developed under EU-FP7 music project. (2016)
- [37] A. Rai, S. Shrimant Sawant, P. Winber, M. Burgess, T. Spencer, P. Kornmayer, G. Pattinson, P.D. Edwards, C. Rinaldi, A. Reikher et al., Integrated absorbing castings (2023)
- [38] C. Bharambe, M.D. Jaybhaye, A. Dalmiya, C. Daund, D. Shinde, Analyzing casting defects in high-pressure die casting industrial case study. Mater. Today Proc. 72, 1079–1083 (2023). https://doi.org/10.1016/j.matpr.2022.09.166
- [39] E. Fiorese, F. Bonollo, G. Timelli, L. Arnberg, E. Gariboldi, New classification of defects and imperfections for aluminum alloy castings. Int. J. Met. 9, 55–66 (2015). https://doi.org/10.1007/BF03355602
- [40] G. Timelli, A. Fabrizi, The effects of microstructure heterogeneities and casting defects on the mechanical properties of high-pressure die-cast AlSi9Cu3(Fe) alloys. Metall. Mater. Trans. A Phys. Metall. Mater. Sci. 45, 5486–5498 (2014). https://doi.org/10.1007/s11661-014-2515-7
- [41] Driving Sustainable Aluminium (SALEMA) Available online: https://salemaproject.eu/
- [42] R.K. Helling, D. Russell, A investigation of the trade-off between lightweight and battery cost for an aluminium-intensive. Green Chem. 11, 380 (2009)
- [43] F. Bonollo, N. Gramegna, The MUSIC Guide to Key-Parameters in High Pressure Die Casting (2015)
- [44] M.F. Ashby, Y.J.M. Bréchet, D. Cebon, L. Salvo, Selection strategies for materials and processes. Mater. Des. 25, 51–67 (2004). https://doi.org/10.1016/S0261-3069(03)00159-6
- [45] Z. Lu, L. Zhang, Thermodynamic description of the quaternary Al-Si-Mg-Sc system and its application to the design of novel Sc-additional A356 alloys. Mater. Des. 116, 427–437 (2017). https://doi.org/10.1016/j.matdes.2016.12.034
- [46] U.R. Kattner, The calphad method and its role in material and process development. Tecnol. em Metal. Mater. e Mineração 13, 3–15 (2016). https://doi.org/10.4322/2176-1523.1059
- [47] D. Raabe, J.R. Mianroodi, J. Neugebauer, Accelerating the design of compositionally complex materials via physics-informed artificial intelligence. Nat. Comput. Sci. 3, 198–209 (2023). https://doi.org/10.1038/s43588-023-00412-7
- [48] M. Hu, Q. Tan, R. Knibbe, M. Xu, B. Jiang, S. Wang, X. Li, M.X. Zhang, Recent applications of machine learning in alloy design: a review. Mater. Sci. Eng. R. Rep. 155, 100746 (2023). https://doi.org/10.1016/j.mser.2023.100746
- [49] P. Krall, I. Weißensteiner, S. Pogatscher, Recycling aluminum alloys for the automotive industry: breaking the source-sink paradigm. Resour. Conserv. Recycl. (2024). https://doi.org/10.1016/j.resconrec.2023.107370
- [50] D. Raabe, D. Ponge, P.J. Uggowitzer, M. Roscher, M. Paolantonio, C. Liu, H. Antrekowitsch, E. Kozeschnik, D. Seidmann, B. Gault et al., Making sustainable aluminum by recycling scrap: the science of "Dirty" alloys. Prog. Mater. Sci. (2022). https://doi.org/10.1016/j.pmatsci.2022.100947
- [51] M. Bertram, S. Ramkumar, H. Rechberger, G. Rombach, C. Bayliss, K.J. Martchek, D.B. Müller, G. Liu, A regionally-linked, dynamic material flow modelling tool for rolled, extruded and cast aluminium products. Resour. Conserv. Recycl. 125, 48–69 (2017). https://doi.org/10.1016/j.resconrec.2017.05.014
- [52] D. Raabe, C.C. Tasan, E.A. Olivetti, Strategies for improving the sustainability of structural metals. Nature 575, 64–74 (2019). https://doi.org/10.1038/s41586-019-1702-5
- [53] L.B. Chappuis, (Vehicle P.E.-M.F.M.C. Material Specifications and Recycling for the 2015 Ford F-150 (2015)
- [54] G. Rombach, Raw material supply by aluminium recycling-efficiency evaluation and long-term availability. Acta Mater. 61, 1012–1020 (2013). https://doi.org/10.1016/j.actamat.2012.08.064
- [55] European Aluminium Circular Aluminium Action Plan. A Strategy for Achieving Aluminium's Full Potential for Circular Economy by 2030. Executive Summary.
- [56] B. Mathai, C. Mathew, Effect of silicon on microstructure and mechanical properties of Cu-Fe alloys. J. Alloys Compd. 707, 184–188 (2017). https://doi.org/10.1016/j.jallcom.2016.12.352
- [57] G.K. Sigworth, R.J. Donahue, The metallurgy of aluminum alloys for structural high-pressure die castings. Int. J. Met. 15, 1031–1046 (2021). https://doi.org/10.1007/s40962-020-00535-x
- [58] L. Zhang, J. Li, Investigating thermal and mechanical characteristics of die-casting aluminum alloys: a comprehensive investigation via thermal analysis. Int. J. Met. (2024). https://doi.org/10.1007/s40962-024-01258-z
- [59] P. Ferro, F. Bonollo, lightweight design versus raw materials criticalities. Sustain. Mater. Technol. 35, e00543 (2023). https://doi.org/10.1016/j.susmat.2022.e00543
- [60] P. Ferro, F. Bonollo, Materials selection in a critical raw materials perspective. Mater. Des. 177, 107848 (2019). https://doi.org/10.1016/j.matdes.2019.107848
- [61] M. Di Sabatino, On fluidity of aluminium alloys. Metall. Ital. 100 (2008)
- [62] J. Campbell, Complete casting Handbook: Metal Casting Processes, Metallurgy, Techniques and Design (Butterworth-Heinemann, 2015)
- [63] H.S. Bang, H.I. Kwon, S.B. Chung, D.U. Kim, M.S. Kim, Experimental investigation and numerical simulation of the fluidity of A356 aluminum alloy. Metals (Basel). 12, 1–13 (2022). https://doi.org/10.3390/met12111986
- [64] A. Heidarzadeh, M. Emamy, A. Rahimzadeh, R. Soufi, D. Sohrabi BabaHeidary, S. Nasibi, The effect of copper addition on the fluidity and viscosity of an Al-Mg-Si Alloy. J. Mater. Eng. Perform. 23, 469–476 (2014). https://doi.org/10.1007/s11665-013-0794-6
- [65] A.T. Dinsdale, P.N. Quested, The viscosity of aluminum and its alloys - a review of data and models. J. Mater. Sci. 39, 7221–7228 (2004). https://doi.org/10.1023/B:JMSC.0000048735.50256.96
- [66] E.A. Moelwyn-Hughes, Physical Chemistry (Cambridge University Press, 2015)
- [67] A.K. Dahle, D.H. StJohn, Rheological behaviour of the mushy zone and its effect on the formation of casting defects during solidification. Acta Mater. 47, 31–41 (1998). https://doi.org/10.1016/S1359-6454(98)00342-5
- [68] S. Bozorgi, K. Haberl, C. Kneissl, T. Pabel, P. Schumacher, Effect of alloying elements (magnesium and copper) on hot cracking susceptibility of AlSiMgCu-alloys. TMS Annu. Meet. (2011). https://doi.org/10.1002/9781118062050.ch14
- [69] J.F. Wallace, A guide to correcting soldering. Die Cast. Eng. 50, 44–47 (2006)
- [70] B. Dewhirst, S. Li, P. Hogan, D. Apelian, Castability measures for diecasting alloys: fluidity, hot tearing, and die soldering. Metall. Ital. 101 (2009)
- [71] M. Kohlhepp, P.J. Uggowitzer, M. Hummel, H.W. Höppel, Formation of die soldering and the influence of alloying elements on the intermetallic interface. Materials (Basel) (2021). https://doi.org/10.3390/ma14071580
- [72] S. Belmares-Perales, M. Castro-Román, M. Herrera-Trejo, L.E. Ramirez-Vidaurri, Effect of cooling rate and Fe/Mn weight ratio on volume fractions of a-AlFeSi and ẞ-AlFeSi Phases in Al-7.3Si-3.5Cu Alloy. Met. Mater. Int. 14, 307–314 (2008). https://doi.org/10.3365/met.mat.2008.06.307
- [73] S. Seifeddine, S. Johansson, I.L. Svensson, the influence of cooling rate and manganese content on the ẞ-Al5FeSi phase formation and mechanical properties of Al-Si-based alloys. Mater. Sci. Eng. A 490, 385–390 (2008). https://doi.org/10.1016/j.msea.2008.01.056
- [74] Q. Han, S. Viswanathan, Analysis of the mechanism of die soldering in aluminum die casting. Metall. Mater. Trans. A Phys. Metall. Mater. Sci. 34, 139–146 (2003). https://doi.org/10.1007/s11661-003-0215-9
- [75] J.C. Lin, Q.T. Fang, C.E. Garesche, H. Haddenhorst, Al-Si-Mg-Mn casting alloy and method 11 (2004)
- [76] R.D. Peterson, A historical perspective on dross processing. Mater. Sci. Forum 693, 13–23 (2011). https://doi.org/10.4028/www.scientific.net/MSF.693.13
- [77] E. Tillová, M. Chalupová, L. Kuchariková, I. Švecová, J. Belan, Sludge phases as cause of higher wear of cutting tools during machining of secondary AlSi12Cu₁ castings. Manuf. Technol. 19, 874–879 (2019). https://doi.org/10.21062/ujep/387.2019/a/1213-2489/mt/19/5/874
- [78] S. Ferraro, G. Timelli, Influence of sludge particles on the tensile properties of die-cast secondary aluminum alloys. Metall. Mater. Trans. B Process Metall. Mater. Process. Sci. 46, 1022–1034 (2015). https://doi.org/10.1007/s11663-014-0260-3
- [79] A. Fabrizi, G. Timelli, The influence of cooling rate and Fe/Cr content on the evolution of Fe-rich compounds in a secondary Al–Si–Cu diecasting alloy. IOP Conf. Ser. Mater. Sci. Eng. (2016). https://doi.org/10.1088/1757-899X/117/1/012017
- [80] S.G. Shabestari, The effect of iron and manganese on the formation of intermetallic compounds in aluminum-silicon alloys. Mater. Sci. Eng. A 383, 289–298 (2004). https://doi.org/10.1016/j.msea.2004.06.022
9. Copyright:
- This material is a paper by "Osama Asghar, Mattia Franceschi, Paolo Ferro and Franco Bonollo": Based on "A NOVEL ALUMINIUM ALLOYS DESIGN STRATEGY FOR LOW USAGE OF CRITICAL RAW MATERIALS AND HIGH CASTING PROCESSIBILITY FOR AUTOMOTIVE APPLICATIONS".
- Source of paper: https://doi.org/10.1007/s40962-024-01502-6
This material was created to introduce the above paper, and unauthorized use for commercial purposes is prohibited. Copyright © 2025 CASTMAN. All rights reserved.