This introductory paper is the research content of the paper "Influence of Alumina (Al2O3) and Titanium Diboride (TiB2) nanoparticulates on the microstructure and properties of Al Si9 Cu3 Fe1 alloys for high pressure die casting applications" published by Université Bordeaux I.
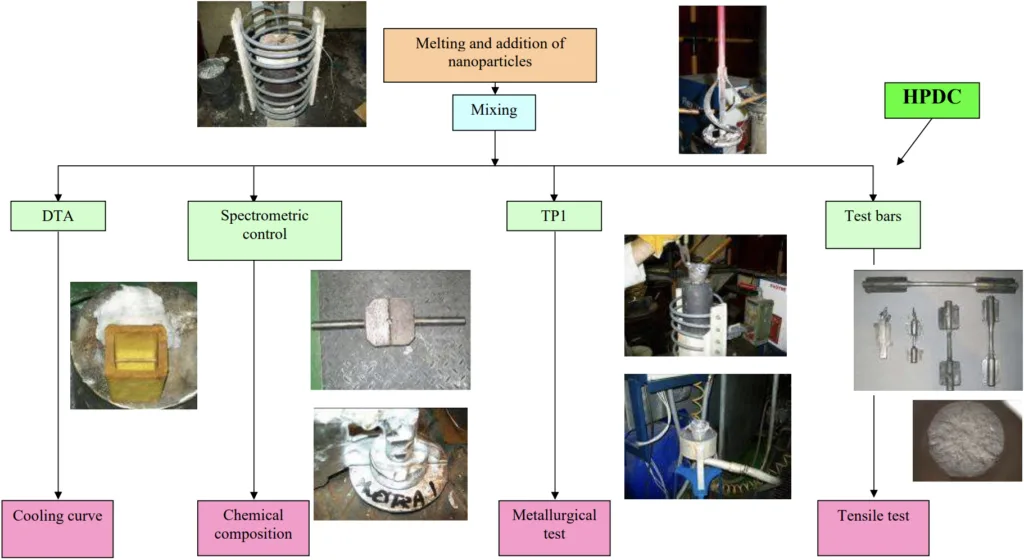
1. Overview:
- Title: Influence of Alumina (Al2O3) and Titanium Diboride (TiB2) nanoparticulates on the microstructure and properties of Al Si9 Cu3 Fe1 alloys for high pressure die casting applications.
- Author: Iban Vicario Gomez
- Publication Year: 2011
- Published Journal/Society: Université Bordeaux I (PhD Thesis)
- Keywords: Al-Si9-Cu3-Fe1, Al2O3, TiB2, nanoparticles, microstructure, mechanical properties, thermal properties, high pressure die casting (HPDC), grain refinement, reinforcement.
2. Abstract
The main objective of the work is to study the influence of TiB2 and Al2O3 nano particles (up to 1 wt. %) on the properties and physical features of aluminium casting alloys processed through an under pressure process known as high pressure die casting. [Page 3]
3. Research Background:
Background of the research topic:
- High pressure die casting (HPDC) is a widely used process for producing light alloy components, especially in the automotive, transport, and energy sectors. [Page 2]
- Aluminium alloys are commonly used in HPDC due to their excellent properties and lightweight construction. [Page 2]
- The Al-Si9-Cu3-Fe1 alloy is the most common alloy used in HPDC. [Page 2]
Status of previous research:
- Previous research has focused on improving aluminium alloy properties through alloying elements and the use of grain refiners (e.g., Al-Ti-B master alloys). [Page 7]
- Metal matrix composites (MMCs) have been investigated to enhance mechanical properties. [Page 8]
- Nanoparticles are being investigated for various applications, including structural applications in light metals. [Page 8]
Need for research:
- There is a need to develop aluminium cast parts with better mechanical properties at higher temperatures and higher service pressures, while reducing weight. [Page 2]
- There is limited industrial employment of nanoparticles as refining and reinforcement agents in Al-Si9-Cu3-Fe1 alloys. [Page 2]
- Specific grain refiners for Al-Si9-Cu3-Fe1 alloys are lacking. [Page 2]
4. Research purpose and research question:
Research purpose:
- To study the influence of TiB2 and Al2O3 nanoparticles (up to 1 wt.%) on the properties of Al-Si9-Cu3-Fe1 alloys processed by HPDC. [Page 3]
Core research:
- Analysis of the influence of TiB2 and Al2O3 nanoparticles on the solidification and microstructure of the Al-Si9-Cu3-Fe1 alloy. [Page 3]
- Analysis of the influence of Al2O3 and TiB2 nanoparticles on the mechanical and thermal properties of the Al-Si9-Cu3-Fe1 alloy. [Page 5]
5. Research methodology
- Research Design: Experimental study.
- Materials:
- Base alloy: Al-Si9-Cu3-Fe1. [Page 3]
- Reinforcement nanoparticles: TiB2 (commercial and SHS-produced, ~200 nm and mesh 325) and Al2O3 (15-40 nm). [Page 2]
- Data Collection:
- Differential Thermal Analysis (DTA) for solidification curves. [Page 3]
- Optical Microscopy (OM), Scanning Electron Microscopy (SEM), Transmission Electron Microscopy (TEM), and Atomic Force Microscopy (AFM) for microstructural analysis. [Page 5]
- Image analysis and elemental analysis (EDS, WDS) to study the influence of nanoparticles. [Page 5]
- Tensile tests at room temperature and 200°C. [Page 5]
- Thermal conductivity measurements. [Page 5]
- Grain Refining test of Aluminium Association (TP1). [Page 9]
- Analysis Method: Comparison of solidification curves, microstructural features, mechanical properties, and thermal properties between reinforced and unreinforced alloys. Comparison with existing models for calculating mechanical and thermal properties. [Page 5]
- Sample Preparation:
Samples of two different reinforcement nanoparticles (Al2O3 and TiB2) has been made in a high pressure die casting machine. [Page 2]
6. Key research results:
Key research results and presented data analysis:
- TiB2 and Al2O3 nanoparticles influence the solidification behavior of the Al-Si9-Cu3-Fe1 alloy, acting as grain refiners and modifying the microstructure. [Page 122]
- The addition of nanoparticles generally increases the nucleation temperature and decreases the undercooling. [Page 71]
- TiB2 particles have a more pronounced effect on grain refinement than Al2O3 particles. [Page 82]
- Nanoparticles reduce porosity size and quantity. [Page 123]
- The microstructure of the reinforced alloys shows finer dendrite arm spacing (SDAS) and a more refined eutectic structure. [Page 93]
- The mechanical properties (UTS, elongation) are generally improved with the addition of nanoparticles, especially TiB2. [Page 129]
- Electrical conductivity decreases with the addition of nanoparticles. [Page 117]
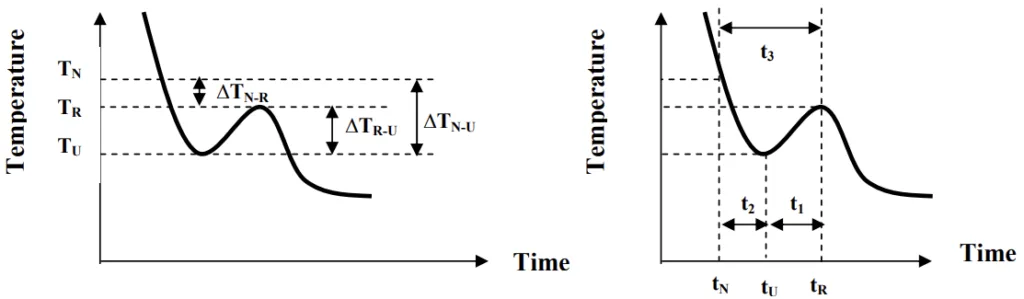
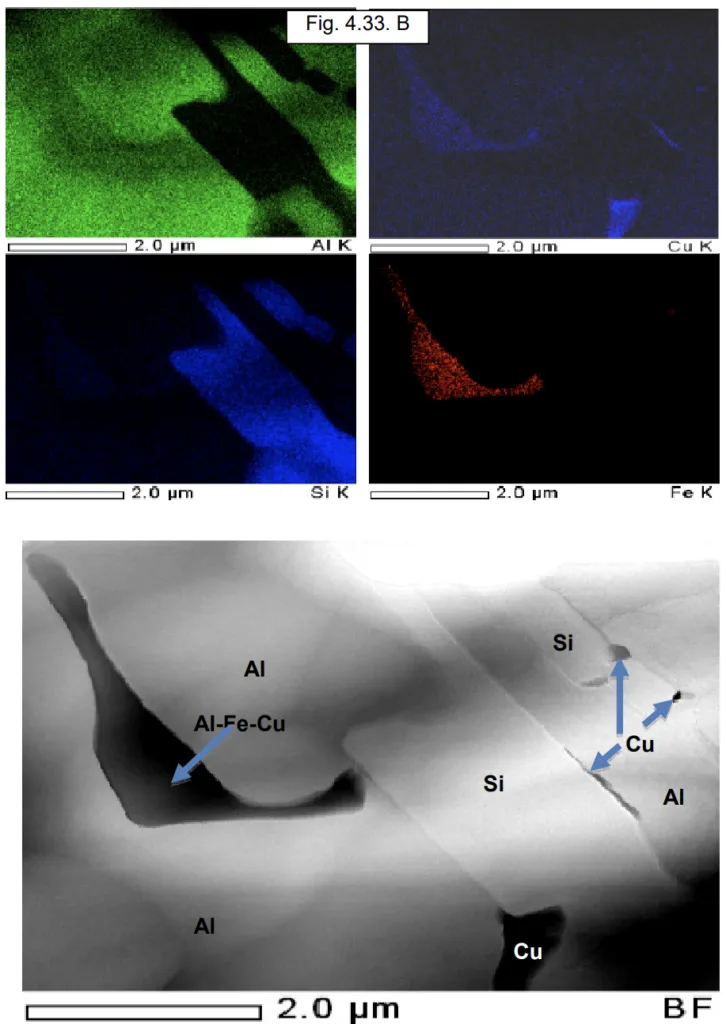
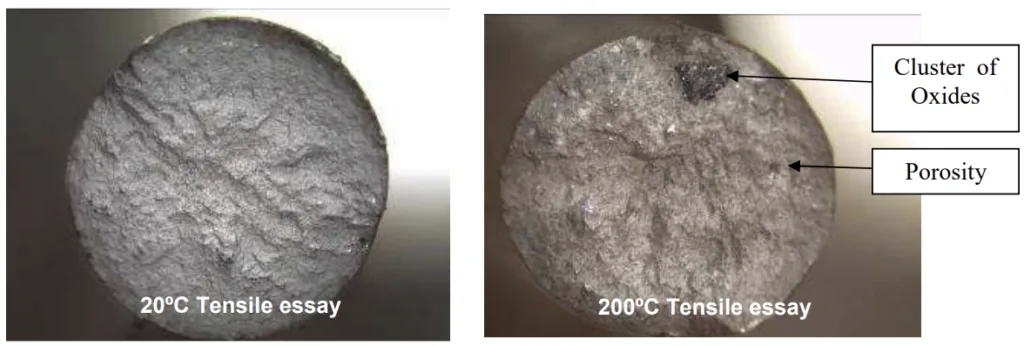
![Table 5.3: Comparison of properties obtained with NADCA formula and experimental essays [Mak 98]](https://castman.co.kr/wp-content/uploads/image-1605-1024x235.webp)
List of figure names:
- Fig.2.1: Illustration of cold chamber high pressure die casting. [Page 10]
- Fig.2.2: Blistering process with entrapped gas porosity. [Page 12]
- Fig.2.3. (a) and Fig.2.3. (b): Solidification diagrams of Temperature / Time [Ask 03]. [Page 16]
- Fig.2.4: Determination of critical radius [Ask 03]. [Page 17]
- Fig.2.5: Undercooling variation between homogeneous and heterogeneous nucleation. [Page 18]
- Fig.2.6.: Necessary undercooling in function of particle diameter [Que 04-02]. [Page 21]
- Fig.2.7: AMC processing routes [Mor 01]. [Page 22]
- Fig.2.8: Reinforcement shape classification of AMC [Mor 01]. [Page 24]
- Fig.2.9.: Materials employed in MMCs by number of companies [Mor 01]. [Page 25]
- Fig.2.10.: Stress – strain diagram. [Page 32]
- Fig.2.11.: Scheme of the crystal structure of TiB2. [Page 36]
- Fig.2.12.: Scheme of the crystal structure of Al2O3 [Wik 11]. [Page 39]
- Fig.2.13.: Relation between grain size and hardness [Sch 01]. [Page 44]
- Figures 3.3: SEM images of TiB2 obtained by SHS with reactor. [Page 55]
- Figures 3.4: Particle size distribution of TiB2 obtained by SHS with reactor. [Page 55]
- Figures 3.5: SEM images of SHS milled materials. [Page 56]
- Figures 3.6.: SEM images of commercial milled materials. [Page 56]
- Figures 3.7.: SEM images of Nano commercial TiB2 milled with aluminium. [Page 57]
- Fig. 3.8: Al-Si phase diagram [Zol 07]. [Page 58]
- Fig. 3.9: Fe phases determination. [Page 58]
- Fig. 3.10.: Test procedure. [Page 64]
- Figure 3.11.- HPDC Test bars. [Page 65]
- Figure 3.12.- Commercial sand cup for DTA determination. [Page 67]
- Figure 4.1.- T=f(t) curve aspects and key parameters in nucleating zone. [Page 71]
- Figure 4.2.- Nucleation (Area 1) and Modification (Area 2) curves and arrests. [Page 72]
- Figure 4.3.- T=f(t) and dT/dt curves with main identified reactions. [Page 73]
- Figure 4.4.- T=f(t) and dT/dt curves with main identified reactions. [Page 74]
- Figure 4.5.- Nucleation temperature (Tn) and time (tn) determination. [Page 74]
- Figure 4.6.- Point of start of liquidus (N) determination with 5th derivative. [Page 75]
- Figure 4.7.- Eutectic reaction characteristic parameters. [Page 75]
- Figures 4.8. A and B- Determination of liquidus temperature and precipitations with Thermo-calc. [Page 77]
- Figure 4.9.- Determination of Al2Cu and Al5Mg8Cu2Si6 start point and area. [Page 78]
- Figure 4.10.- DTA solidification of Al Si9 Cu3 + 0.15% nano TiB2 sample. [Page 79]
- Figure 4.11.- DTA solidification of Al Si9 sample. [Page 80]
- Figure 4.12.- DTA solidification of 0.2% SHS-TiB2. [Page 81]
- Figure 4.13.- DTA solidification of 0.2% commercialTiB2 briquette. [Page 81]
- Figure 4.14.- DTA solidification of 0.1% of gamma Al2O3 briquette. [Page 84]
- Figure 4.15.- DTA solidification of 0.17% of alpha Al2O3 briquette. [Page 85]
- Figure 4.16.- Temperature evolution graphic. [Page 90]
- Figure 4.17.- Recalescence comparison between samples. [Page 91]
- Figure 4.18.- Modification comparison between samples. [Page 92]
- Figure 4.19.- Al Si9 Cu3 alloy TP1 essay OM macrograph analysis. [Page 95]
- Fig. 4.20.: Al Si 9 Cu3 OM micrographs. [Page 96]
- Figure 4.21.- Al Si9 Cu3 typical SEM micrographs. [Page 96]
- Figure 4.22.- SHS-TiB2 reinforced alloy TP1 essay OM macrograph analysis. [Page 97]
- Fig. 4.23: OM Study of grain and precipitates in the central and peripheral areas. [Page 98]
- Fig. 4.24.: SEM study of SHS-TiB2 reinforced alloy. [Page 99]
- Figure 4.25.- Phase determination in SHS-TiB2 reinforced alloy by EDS and SEM. [Page 100]
- Figure 4.26.- 0.1 wt.% γ-Al2O3 reinforced alloy TP1 essay OM macrograph analysis. [Page 101]
- Figures 4.27.: OM Study of grain and precipitates in the central and peripheral areas. [Page 102]
- Figure 4.28.- Phase determination in γ-Al2O3 reinforced alloy by EDS and SEM. [Page 102]
- Figures 4.29. A,B,C,D and E.- Al2O3 particles detection by EDS and SEM. [Page 103]
- Figures 4.30. A,B and C.- Al2O3 particles detection by EDS and SEM. [Page 105]
- Figures 4.31.- Determination of peripheral Al dendrite composition by WDS. [Page 106]
- Figures 4.32.- Determination of central Al dendrite composition by WDS. [Page 107]
- Figures 4.33. A and B shows typical microstructure of the matrix taken into the center of the sample where acicular grains are found in two areas. [Page 108]
- Figure 4.33.- A and B : TEM micrograph of typical microstructure of sample in the center of the foundry sample namely acicular grain zone. Each TEM micrograph (bright field image is associated with 4 EDS corresponding maps (Al, Cu, Si and Fe)). [Page 109]
- Figure 4.34.- TEM micrograph of typical microstructure of sample in the edge of the foundry sample. [Page 110]
- Figures 4.35. A) and a B) show typical microstructure of the matrix taken into the peripheral area of sample, where small grain zones are found. Each of the bright field micrograph is associated with EDS maps in order to analyze the distribution of the Al, Cu, Si and Fe elements within the TEM analysis zone. [Page 111]
- Figure 4.35. A) and B).- TEM micrograph of typical microstructure of sample in the edge of the foundry sample namely small grain zone. Each TEM micrograph (bright field image is associated with 4 EDS corresponding maps (Al, Cu, Si and Fe)). [Page 112]
- Figure 4.36.- Acicular dendrite zone detail in the center of a reinforced alloy. [Page 114]
- Figure 4.37.- Secondary dendrite arm spacing determination. [Page 114]
- Figures 4.38.- Secondary dendrite arm spacing determination. [Page 115]
- Figure 4.39.: Comparative diagram between SDAS and IACS. [Page 120]
- Figure 5.1: UTS at room temperature for reinforced and base Al Si9 Cu alloys. [Page 130]
- Fig. 5.2: YS at room temperature for reinforced and base Al Si9 Cu alloys. [Page 131]
- Fig. 5.3 Elongation at room temperature for reinforced and base Al Si9 Cu alloys. [Page 131]
- Fig. 5.4: UTS at 200ºC for reinforced and base Al Si9 Cu alloys. [Page 133]
- Fig. 5.5: YS at 200ºC for reinforced and base Al Si9 Cu alloys. [Page 133]
- Fig. 5.6 Elongation at 200ºC for reinforced and base Al Si9 Cu alloys. [Page 134]
- Figure 5.7: Fracture analysis of base alloy. [Page 136]
- Figure 5.8: Fracture analysis of 0.02% SHS TiB2 reinforced alloy. [Page 136]
- Figure 5.9: Fracture analysis of 0.1% Al2O3 gamma alumina reinforced alloy. [Page 137]
7. Conclusion:
Summary of key findings:
- Nano-sized TiB2 and Al2O3 particles act as grain refiners in Al-Si9-Cu3-Fe1 alloys, modifying the solidification behavior and microstructure. [Page 142]
- TiB2 has a more potent grain refining effect than Al2O3. [Page 142]
- Nanoparticles reduce porosity size and quantity, with Al2O3 being more effective than TiB2. [Page 142]
- The addition of nanoparticles generally improves the ultimate tensile strength (UTS) and elongation, especially at room temperature. [Page 143]
- The yield strength (YS) is slightly reduced with nanoparticle addition at room temperature but increases at 200°C. [Page 143]
- The electrical conductivity decreases with nanoparticle addition. [Page 142]
Summary of research results. Academic significance of the research, practical implications of the research
- The addition of nanoparticles in the Al-Si alloys changes the solidification curves, promoting a better nucleation. [Page 122]
- TiB2 particles have a great influence in the solidification and in the obtained microstructure of the aluminium alloys. [Page 3]
- The addition of grain refiners in the Al Si9 Cu3 Fe1 as Al Ti5 B1, Al Ti3 B1 and Al Ti C have been reported [Boo 02] to decrease the internal porosity, with an average lower porosity size and with a better distribution of porosity in the part. [Page 4]
- The microstructure and composition of the reinforced alloys has been thoroughly studied through Optical Microscopy, Scanning Electronic Microscopy (SEM), Transmission Electronic Microscopy (TEM) and Atomic Force microscopy (AFM). [Page 5]
- The thermal and mechanical characterization has been carried out with samples obtained with the DC and HPDC process. [Page 5]
- The experimental results have been compared with the models employed for calculating mechanical and thermal properties of materials reinforced with ceramic particles and to check the expected improvement in the alloy properties. [Page 5]
8. References:
- [Agu 10] Aguilar-Santillan J. Wetting of the (0001) α-Al2O3 sapphire surface by molten aluminium: Effect of surface roughness. The minerals, metals & materials society and ASM international. 2010.
- [Aik 97] Aikin Jr. R.M.”The mechanical properties of in situ composites”. JOM. 49 (8) (1997), pp. 35-39.
- [All 74] United States Patent US 3.961.995. 1974. Alliot M., Beguin J.C., Moutach M., Percheron J.C. Mother Alloy of Aluminium, Titanium and Boron and process for fabrication.
- [Alu 11] http://aluminium.matter.org.uk/content/html/eng/ default.asp?catid=71&pageid=2075282087
- [Arp 03] Arpón R., Molina J.M., Saravanan R.A., García Cordobilla C., Louis E., Narciso j. “Thermal expansion behaviour of aluminium/SiC composites with bimodal particle distributions”. Acta Materalia 51 (2003) pp. 3145-3156.
- [Ask 03] The Science and Engineering of Materials, 4th ed. 2003. Brooks and Cole. Askeland D. R. –Phulé P. P.
- [Bac 74] United State Patents US 3785807. 1974. Backerud S.L. Method for producing a master alloy for use in aluminium casting processes.
- [Bac 90] Solidification Characteristics of Aluminium Alloys, Vol. 2. Foundry Alloys. AFS and Skanaluminium of Norway. 1990. AFS. Backerud L., Chai G., Tamminen J.
- [Bac 00] United States Patents US 6.073.677. 2.000. Bäckerud L; Johnsson M; Sigworth J. Method for optimization of the grain refinement of aluminium alloys.
- [Ban 88] United States Patent US 4.748.001. 1988. Banerji A., Reif W. Producing titanium carbide particles in metal matrix and method of using resulting product to grain refine.
- [Boo 02] Boot D., Cooper P., StJohn D.H., Dahle A.K. A Comparison of Grain Refiner Master Alloys for the Foundry. TMS 2002.
- [Bro 99] Foseco Non-Ferrous Foundry man’s Handbook.1999. Elsevier Ltd. Brown J. R.
- [Buh 11] http://www.buhlergroup.com
- [Bru 87] United States patent US 4.710.348. 1987. Brupbacher J.M., Christodoulou L., Nagle D.C. Process for forming metal-ceramic composites.
- [Cac 96] Cáceres C.H., Wang Q. G. "Dendrite cell size and ductility of Al-Si-Mg casting alloys: Spear and Gardner revisited". International Journal of Cast Metals Research. 1996. Vol.9, Nº 3. pp. 157-162.
- [Cti 01] Aleaciones de aluminio para el moldeo. Version 1. CTIF. 2002. CTIF.
- [Cly 93] Clyne T.W., Withers P.J. “An introduction to metal matrix composites”. Cambridge University Press. 1993. ISBN 0-521-41808-9.
- [Con 00] Conrad H, Narayan J. On the grain size softening in nanocrystalline materials. Scripta Mater 2000;42(11). pp. 1025–1030.
- [Dav 07] Davis B.; Hyn J. Innovative forming and fabrication technologies: New opportunities. Final report. Argonne National Laboratory. ANL-07/31. 2007.
- [Dho 11] Dhokey N. B., Rane K. K. Wear Behavior and Its Correlation withMechanical Propertiesof TiB2 Reinforced Aluminium-Based Composites. Advances in Tribology. Vol. 2011, pp. 1-8.
- [Din 10] Aluminium and aluminium alloys – Castings – Chemical composition and mechanical properties. English translation of DIN EN 1706:2010-06.
- [Dju 04] Djurdjevic M.B., Francis R., Sokolowski J.H. Emaldi D., Sahoo M. Comparison of different analytical methods for the calculation of latent heat of solidification of 3XX aluminium alloys. Material Science and engineering. 2004. A 386. pp. 277-283.
- [Dju 11] Djurdjevic M.B. “Thermal Description of Al-Si Alloys Using Their Known Chemical Compositions”. European Conference on Aluminium Alloys (ECAA 2011). 2011.
- [Eas 10-1] Easton M., Davidson C., John D.S. Effect of alloy composition on the dendrite arm spacing of multi-component aluminium alloys. The minerals, Metals & materials Society and ASM international 2010.
- [Eas 10-2] Easton M., Davidson C., John D.S. Effect of alloy composition on the dendrite arm spacing of multi-component aluminium alloys. Metallurgical and materials transactions A. 2010. Nº 1528-Volume 41A.
- [Egi 07] Egizabal P. Influence of Titanium Diboride (TiB2) particles on the microstructure and properties of reinforced Al-Si7Mg0.3 and Al-Cu5MgTi alloys for plaster casting applications. Université Bordeaux 1. 2007.
- [El- 10] El-Mahallawi I. S.; Shash Y.; Eigenfeld K.; Mahmoud, T. S.; Ragaie R. M., Shash A. Y., El Saeed M. A. Influence of nano-dispersions on strength–ductility properties of semisolid cast A356 Al alloy. Materials Science and Technology. 2010. Vol. 26, Nº 10 , pp. 1226-1231.
- [El- 11] El-Mahallawi I.S., Shash Y., Ragaie R.M., Abdelaziz M.N., Mayer J., Schwedt A. Influence of nano-dispersions on microstructure features of cast Al-Si Hypereutectic Alloys. European conference on Aluminium Alloys. 2011. Poster A-134.
- [Fu 07] Fu Q., Wagner T. Interaction of nano-structured metal over layers with oxide surfaces. Surface Science reports 2007. Nº 62. pp. 431-498.
- [Gre 00] Greer A.L, Bunn A.M, Tronche A, Evans P.V, Bristow D.J. Modelling of inoculation of metallic melts: application to grain refinement of aluminium by Al–Ti– B. Acta Materalia, 2000, Vol. 48, Issue 11, pp. 2823-2835.
- [Gro 09] Grosselle F., Timelli G., Bonollo F., Molina R. Correlation between microstructure and mechanical properties of Al-Si diecast engine blocks. Metallurgical Science and Technology. Vol 27.2. 2009.
- [Gru 95] Gruzleski et.al. AFS Inc. Des Plaines, Illinois. 1995.
- [Gu 02] Gu Y., Qian Y., Chen L., Zhou F. A mild solvothermal route to nanocrystalline titanium diboride. Journal of Alloys and Compounds. Volume 352, Issues 1-2. 2003. pp. 325-327.
- [Guz 86] United State patent. US 4.612.073. 1986. Guzowski M.M., Sentner D.A., Sigworth. Aluminium grain refiner containing duplex crystals.
- [Hal 51] Hall E.D. Proc. Phys. Soc. Serie B 64. 1951. pp. 747-765.
- [Han 02] Han Y., Liu X., Bian X. “In situ TiB2 particulate reinforced near eutectic Al-Si alloy composites”. Composites A 33. 2002. pp. 439-444.
- [Han 05] Han J. “Processing, microstructure evolution and properties of nano-scale aluminium alloys”. PhD. University of Cincinnati. 2005. pp. 38-44.
- [Hid 99] Hind A.R., Bhargava S.K., Grocott S. C. The surface chemistry of Bayer process solids: a review. Colloids and Surfaces A: Physicochemical and Engineering Aspects. Volume 146, Issues 1-3. 1999. pp. 359-374.
- [Hum 91] Humphreys F.J., Basu A., Djazeb M.R. “The microstructure and strength of particulate metal-matrix composites”. Metal matrix composites. Processing, microstructure and properties. 12th Riso International Symposium on materials science. 1991. pp. 51-66.
- [Hüs 06] Hüseying S., Kurnaz C. Properties of alumina particulate reinforced aluminium alloy produced by pressure die casting. Materials and design. 2006. Nº 27. pp. 676- 683.
- [Iba 99] Ibarra D. G. Control of grain refinement of Al-Si alloys by thermal analysis. Mc Gill University. 1999.
- [Iva 04] Ivar H. High Pressure Die Casting of Aluminium and Magnesium Alloys - Grain Structure and Segregation Characteristics. Norwegian University of Science and Technology (NTNU). 2004.
- [Jac 77] Alumina: sintering and optical properties. 1977. Technische Hogeschool Eindhoven. Jacob J. G.
- [Jia 08] Jiang Q., Lu H.M. Size dependent interphase energy and its applications. Surface Science Reports. 2008. Nº63. pp. 427– 464.
- [Kau 07] Kaufmann H., Uggowitzer P.J. Metallurgy and processing of high integrity light metal pressure castings. Fachverlarg Schiele & Schön Gmbh Berlin. 2007. pp.56.
- [Kas 01] Kashyap K. T., Chandrashekar T. Effects and mechanisms of grain refinement in aluminium alloys. Bull. Mater. Sci., Vol. 24, No. 4, 2001, pp. 345–353.
- [Kum 09] Kumar S., Subramaniya V., Murty B.S. Functionally graded Al alloys matrix in-situ composites The minerals, metals & materials society and ASM international. 2009.
- [Lem 81] Principles of Mechanical Metallurgy. Edward Arnold..1981. Elsevier. LeMay. pp. 155-211.
- [Loe 01] Loeffler J. Nano-material roadmap 2015. Overview of promising nano materials for industrial applications. Steinbeis-Europa-Zentrum. 2005.
- [Li 03] Li P., Kandalova E.G., Nikitin V.I., Luts A.R., Makarenko A.G., Zhang Y. Effect of fluxes on structure formation of SHS Al–Ti–B grain refiner. Materials Letters. 2003. Vol. 57. pp. 3694–3698.
- [Ma 01] Ma Z.Y., Li J.H., Luo M., Ning X.G., Lu Y.X., Bi J., Zhang Y.Z. In-situ formed Al2O3 and TiB2 particulates mixture-reinforced aluminium composite. Scripta Metallurgical et Materialia, 1994, Vol. 31, Issue 5, pp. 635-639
- [Mac 96] Mackay R. I. Quantification of Iron in Al-Si Foundry alloys via thermal analysis. Mc Gill University. 1996.
- [Mah 08] Mahboob H., Sajjadi S. A., Zebarjad S. M. Synthesis of Al-Al2O3 Nano Composite by mechanical alloying and evaluation of the effect of ball milling time on the microstructure and mechanical properties. The International Conference on MEMS and Nanotechnology, ICMN'08.2008.
- [Mak 98] Makhlouf M., Apealian D., Wang L. Microstructures and properties of aluminium die casting alloys. North American Die Casting Assoc. 1998. NADCA
- [Mar 08] Martin M.I., Rabanal M.E., Gomez L.S., Torralba J.M., Milosevic O. Microstructural and morphological analysis of nanostructured alumina particles synthesized at low temperature via aerosol route. Journal of the European Ceramic Society 2008. Nº 28, pp. 2487-2494.
- [Mat 07] Matsunaga T., Matsuda K.; Hatayama T., Shinozaki K., Yoshida M. Fabrication of continuous carbon fiber reinforced aluminium-magnesium alloy composite wires using ultrasonic infiltration method. Composites. 2007. Part A 38 . pp 1902-1911.
- [Max 01] Maxwell I, Hellawell A. An analysis of the peritectic reaction with particular reference to Al-Ti alloys Acta Metallurgical, 1975, Vol. 23, Issue 8, pp. 901-909.
- [Mil 90] Miller W.S., Humphreys F.J. “Strengthening mechanisms in metal matrix composites”. Fundamental relationships between microstructure & mechanical properties of metal matrix composites. Law P.K., Gunger M.N. The Minerals, metals and materials society, 1990.
- [Mis 04] Miserez A., Muller R., Rossoll A. et al. 2004. “Particle reinforced metals of high ceramic content” Mat sci eng A-Struct 387-89: pp. 822-831.
- [Mit 95] Mitra R., Mahajan Y.R. Interfases in discontinuosly reinforced metal matrix composites: An overview. Mater. Sci. 1995, Vol. 18, Nº 4, pp. 405-434.
- [Miy 73] United States Patent US 3.857.705. 1973. Miyasaka Y; Masuda Y. Small grain promoting Aluminium-Titanium-Boron mother Alloy.
- [Mor 01] Mortensen A. Metal Matrix Composites in industry: An overview. Ecole Politechnique Fédérale de Lausanne. 2001.
- [Mon 79] Aluminium Alloys, structures and properties. London, Butherworths. 1979. Mondolfo L.F.
- [Mun 97] Munro R. G. "Evaluated Material Properties for a Sintered alpha-Al2O3,". Journal of the American Ceramic Society. 1997. Vol. 80, pp. 1919-1928.
- [MMC 01-2] http://www.ceramics.nist.gov/srd/summary/scdaos.htm
- [Mun 00] Munro R. G. "Material Properties of Titanium Diboride", Journal of Research of the National Institute of Standards and Technology. 2000.Vol. 105, pp. 709-720 .
- [MMC 01-1] http://www.ceramics.nist.gov/srd/summary/scdtib2.htm
- [Nan 11] http://www.nanophase.com/products/details.aspx?ProductId=1
- [Nik 00] Nikitin V.I., Wanqi J.I.E., Kandalova E.G., Makarenko A.G., Yong L. Preparation of al-ti-b grain refiner by shs technology. Scripta mater. 2000. Vol. 42. pp. 561–566.
- [Nik 11] Niklas A., Abaunza U., Fernandez Calvo A.I., Lacaze J., Suarez R. Thermal análisis as a microstructure prediction tool for A356 aluminium parts solidified under various cooling conditions. The 69th WFC paper. 2011.
- [Que 04-01] Quested T.E; Greer A.L; The effect of the size distribution of inoculant particles on as-cast grain size in aluminium alloys. Acta materalia. 2004, Vol. 52, Issue 13, pp. 3859-3868
- [Que 04-02] Quested T. E., Solidification of Inoculated Aluminium Alloys. University of Cambridge. 2004.
- [Ram 08] Ramachandran T.R., Sharma P.K. , Balasubramanian K. Grain Refinement of Light Alloys. 68th WFC - World Foundry Congress7th - 2008, pp. 189-193.
- Okay, let's continue building the WordPress post with the remaining sections from the provided document.
- 8. References (Continued):
- [Sat 06] Sato T. Nanostructure Control for High-Strength and High-Ductility Aluminium Alloys. Nanomaterials 2006. pp. 315-346.
- [Sch 98] Schumacher P, Greer A. New studies of nucleation mechanism in aluminium alloys. Implication for grain refinement practice. Mater Sci Technol. 1998;14:394.
- [Sch 01] Schiøtz J. Simulations of nanocrystalline metals at the atomic scale. what can we do? what can we trust?. Science of Metastable and Nanocrystalline Alloys" A.R. Dinesen et al., 2001. A.R. Dinesen et al. pp. 127-139.
- [Sch 04] Schiøtz J. Strain-induced coarsening in nanocrystalline metals under cyclic deformation. Materials Science and Engineering. 2004. A 375–377, pp. 975–979.
- [Sch 07] Schaffer P.L., Miller D. N., Dahles A. K. Crystallography of engulfed and pushed TiB2 particles in aluminium. Scripta Materalia. 2007. Nº57, pp.1129-1132
- [Sei 09] Seifeddine S. The influence of Fe and Mn content and cooling rate on the microstructure and mechanical properties of A380-die casting alloys. Svensson. Metallurgical Science and Technology. Vol.27-1. Ed. 2009.
- [She 05] Shen P., Fujii H., Matsumoto T., Nogi K. Critical Factors Affecting the Wettability of α-Alumina by Molten Aluminum. Journal of the American ceramic society. Journal of the American Ceramic Society. 2004. Vol. 87, Issue 11, pp. 2121-2159.
- [Sig 86] United States Patent US 4.812.290. 1986. Sigworth G. Third element additions to Aluminium-Titanium Master Alloys.
- [Sig 91] United States Patents, US 5.055.256. 1991. Sigworth G; Guzowski M. Grain refiner for aluminium containing silicon.
- [Spa 10] Sparkman D. Thermal Analysis Metrics by derivatives. Meltlab. 2010. www.meltlab.com/hottopics/feb2010htopic.pdf
- [Tam 05] Tam K.F. Mechanical and thermal characteristics of HIPed A1-TiB2 MMCs. City university of Hong Kong. 2005.
- [Tay 04] Taylor J.A. The effect of iron in Al-Si9 casting alloys. 35th Australian Foundry Institute National Conference. 2004.
- [Tee 01] Tee K.L., Lu L., Lai M.O. “In situ stir cast Al-TiB2 composite: processing and mechanical properties”. Material Science and Technology. 2001. Vol. 17. pp 201-206.
- [Tjo 03] Tjong S.C., Tam K.F., Wu S.Q. Thermal cycling characteristics of in-situ Al-based composites prepared by reactive hot pressing. Composites science and technology 2003, 63, pp. 89-97.
- [Tjo 05] Tjong S.C., Wang G.S., Mai Y.W. Low-cycle fatigue behaviour of Al-based composites containing in situ TiB2, Al2O3 and Al3Ti reinforcements . Materials Science and Engineering: A. 2003. Volume 358, Issues 1-2, pp. 99-106
- [Tjo 06] Tjong S.C., Tam K.F. Mechanical and thermal expansion behaviour of hipped aluminium-TiB2 composites Materials. Chemistry and physics. 2006. 97, pp. 91-97.
- [Wik 11] http://en.wikipedia.org/wiki/Alumina
- [Wik 11-02] http://en.wikipedia.org/wiki/Solid_solution_strengthening
- [Wik 11-03] http://en.wikipedia.org/wiki/Work_hardening
- [Zha 08] Guo Z., Saunders N., Miodownik P., Schillé J.P. Prediction of room temperature mechanical properties in aluminium castings. International Congress of Aluminium Alloys ICAA11. 2008.
- [Zho 07] Zhong X.L., Wong W.L.E., Gupta M. Enhancing strength and ductility of magnesium by integrating it with aluminium nanoparticles. Acta materalia. 2007. Vol. 55 pp. 6338-6344.
- [Zol 07] Casting aluminium alloys. Elsevier. 2007. Zolotorevsky V.S.; Belov N.A.; Glazoff M.V. pp. 359-362.
9. Copyright:
- This material is a paper by "Iban Vicario Gomez": Based on "Influence of Alumina (Al2O3) and Titanium Diboride (TiB2) nanoparticulates on the microstructure and properties of Al Si9 Cu3 Fe1 alloys for high pressure die casting applications.".
- Source of paper: tel-00670402, https://tel.archives-ouvertes.fr/tel-00670402
This material was created to introduce the above paper, and unauthorized use for commercial purposes is prohibited. Copyright © 2025 CASTMAN. All rights reserved.