This introductory paper is the research content of the paper "Fundamental Research Needs for the Magnesium Powertrain Cast Components (MPCC) Project" published by TMS (The Minerals, Metals & Materials Society).
![Figure 1. Calculated isothermal section at 298 K for MgAl-Ca alloy system [3].](https://castman.co.kr/wp-content/uploads/image-1507-png.webp)
1. Overview:
- Title: Fundamental Research Needs for the Magnesium Powertrain Cast Components (MPCC) Project
- Author: Randy Beals¹, Lawrence Kopka¹, John Allison², Joy A. Hines², Bob McCune², Alan Luo³, Bob Powell³ and Peter Ried⁴
- Publication Year: 2004
- Publishing Journal/Academic Society: Magnesium Technology 2004, Edited by Alan A. Luo, TMS (The Minerals, Metals & Materials Society)
- Keywords: Magnesium alloy development, structure-property relationships, phase equilibrium, computational thermodynamics, creep deformation mechanisms, casting, solidification, corrosion, recycling.
2. Abstracts / Introduction
Abstract
The Magnesium Powertrain Cast Components Project is a jointly sponsored effort by the US Department of Energy and the US Council for Automotive Research to determine the feasibility and practicality of producing a magnesium-intensive engine. The Project seeks to determine the technical and economic requirements of a V6 engine. Several newly-developed, high temperature magnesium alloys will meet those requirements. An additional objective of the Project is to identify the fundamental scientific challenges of using magnesium alloys and casting processes in powertrain components. The areas of research are: magnesium alloy development (structure-property relationships), phase equilibrium and computational thermodynamics, creep deformation mechanisms, casting (solidification) behavior, corrosion and recycling. The goal of this objective of the MPCC Project is to promote new and strengthen existing magnesium scientific research in the North America.
Introduction
Magnesium can improve automobile gas mileage. To enable the use of magnesium in automotive powertrains, there is a need for alloys with improved performance at higher operating temperatures (150–180°C). The Magnesium Powertrain Cast Components Project (MPCC) was initiated to determine the readiness of magnesium alloys for use in automotive powertrains [1].
3. Research Background:
Background of the Research Topic:
- The need for improved fuel efficiency and reduced emissions in the automotive industry.
- The potential of magnesium alloys, due to their low density, to contribute to these goals.
- The limitations of existing magnesium alloys at higher operating temperatures (150-180°C) required for powertrain applications.
Status of Existing Research:
- Development of new high-temperature magnesium alloys with improved creep properties.
- Limited understanding of the creep deformation mechanisms in these new alloys.
- Lack of comprehensive thermodynamic data and phase diagrams for the newly developed alloys.
- Need for improved understanding of the solidification behavior of these alloys in casting processes.
- Concerns about the corrosion resistance and recyclability of the new alloys.
Necessity of the Research:
- To enable the widespread use of magnesium alloys in automotive powertrains.
- To realize the full weight-saving potential of these alloys, further improvements in their properties are required.
- To optimize alloy compositions and processing techniques for specific powertrain components.
- To address the challenges related to casting, corrosion, and recycling.
4. Research Purpose and Research Questions:
Research Purpose:
- The long-range objective is to identify and publicize critical scientific areas of research for magnesium powertrain applications to promote the growth of the North American magnesium scientific infrastructure.
- The short-range objective of the program is to identify and implement research in areas that will contribute to the MPCC Project directly.
Key Research:
- Magnesium alloy development (structure-property relations).
- Phase Equilibria and Computational Thermodynamics.
- Creep Deformation Mechanisms
- Casting (Solidification) Behavior
- Corrosion
- Recycling
5. Research Methodology
Research Design:
- Collaborative research workshop involving members of the MPCC core team, the U.S. Department of Energy, national laboratories, and universities.
- Combination of experimental investigations and computational modeling.
Data Collection Method:
- Microstructural characterization using techniques such as optical microscopy, SEM, TEM, XRD, and EPMA.
- Mechanical testing, including creep testing.
- Corrosion testing using methods like ASTM B117 salt spray, ASTM D1384, and ASTM D4340.
- Thermodynamic data collection from literature and experimental measurements.
Analysis Method:
- Computational thermodynamics using the CALPHAD technique.
- Development of quantitative models relating metal processing parameters to microstructure and properties.
- Analysis of creep deformation mechanisms.
- Assessment of casting behavior and solidification processes.
- Evaluation of corrosion mechanisms and recyclability.
Research Subjects and Scope:
- Six die-cast magnesium alloys: Dead Sea Magnesium (MRI 153M, MRI 230D), Noranda (AJ52), Hydro (AS21X), GM (AXJ530), Avisma (AS31).
- Three sand-cast magnesium alloys: Dead Sea Magnesium (MRI 201S), Australian Magnesium Corp. (SC1), Solikamsk (ML10).
- Focus on powertrain components: V6 engine block, structural oil pan, and front engine cover.
6. Main Research Results:
Key Research Results:
- The equilibrium phases in the Mg-Al-Ca alloys are primary Mg matrix and C15-Al2Ca.
- The calculated volume fractions of eutectic phase(s) in several Mg-Al-Ca and Mg-Al-Ca-Sr alloys are in good agreement with the experimental results.
- Several main alloying elements for creep resistance : AS, AXJ, AE and AJ.
- The new creep-resistant magnesium alloys contain various elements, such as Sr, Ca, and rare earth elements (Nd, Ce, La, Pr, etc.)
- During HPDC process, solidification begins in the shot sleeve even before the melt enters the die cavity.
Analysis of presented data:
- Figure 1: Shows a calculated isothermal section at 298 K for the Mg-Al-Ca alloy system, confirming the presence of lamellae-type ternary (Mg, Al)₂Ca.
- Figure 2: Presents ASTM D1384 Corrosion Results (specific alloy and coolant identifications are not disclosed).
- Figure 3: Presents ASTM D4340 Corrosion Results (specific alloy and coolant identifications are not disclosed).
Figure Name List:
- Figure 1. Calculated isothermal section at 298 K for Mg-Al-Ca alloy system [3].
- Figure 2. ASTM D1384 Corrosion Results
- Figure 3. ASTM D4340 Corrosion Results
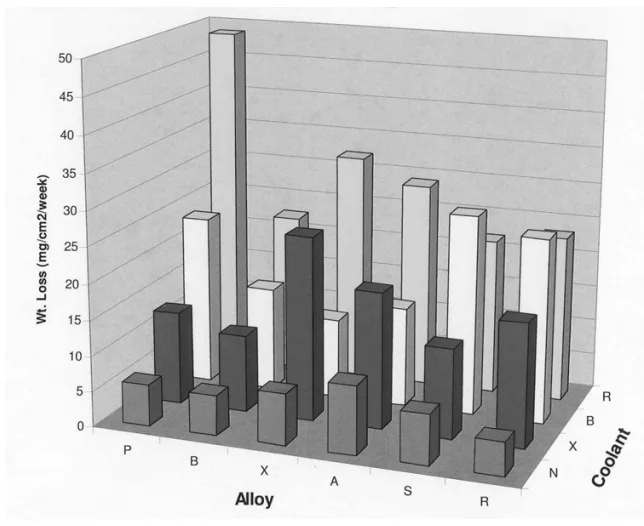
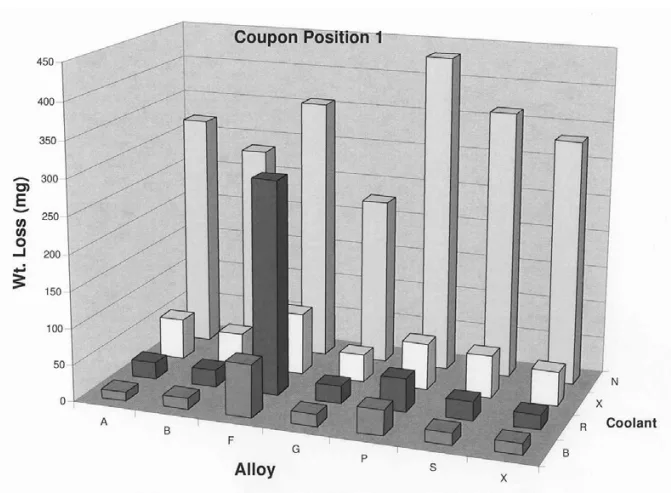
7. Conclusion:
Summary of Key Findings:
- New creep-resistant magnesium alloys show promise for powertrain applications but require further research.
- Key research areas include alloy development (structure-property relationships), phase equilibria, creep mechanisms, casting behavior, corrosion, and recycling.
- Computational thermodynamics is a valuable tool for alloy development.
- Control of grain boundary structure is critical for creep resistance.
- Casting processes need to be optimized for the new alloys.
- Corrosion resistance and recyclability are important considerations.
Academic Significance of the Study:
- Identifies critical research needs for advancing magnesium technology.
- Promotes the development of a strong magnesium scientific infrastructure.
- Provides a framework for future research on high-temperature magnesium alloys.
Practical Implications:
- Enables the use of magnesium alloys in powertrain components, leading to vehicle weight reduction and improved fuel efficiency.
- Guides the development of optimized alloys and processing techniques.
- Addresses the challenges of corrosion and recycling, facilitating the sustainable use of magnesium.
Limitations of the Study and Areas for Future Research:
- Limited understanding of creep deformation mechanisms in the new alloys.
- Need for more comprehensive thermodynamic data and phase diagrams.
- Further research on solidification behavior and casting optimization.
- Investigation of corrosion mechanisms and development of reliable accelerated corrosion tests.
- Exploration of the economic and technical issues of recycling the new alloys.
8. References:
- [Reference lists]
- B. Powell, L. Ouimet, J. Allison, J. Hines, R. Beals, L. Kopka, and P. Ried, "The USAMP Magnesium Powertrain Cast Components Project," in Magnesium Technology 2004, ed. by A. Luo, TMS, Warrendale, PA, USA 2004.
- L. Kaufman and H. Bernstein, "Computer Calculation of Phase Diagrams with Special Reference to Refractory Metals", Academic Press, New York, 1970.
- K. Ozturk, Y. Zhang, A.A. Luo and Z.-K. Liu, “Creep-Resistant Mg-Al-Ca Alloys: Computational Thermodynamics and Experimental Investigation", JOM, Vol. 55, November 2003, 40-44.
- K. Ozturk, Z.-K. Liu, A.A. Luo, "Phase Identification and Microanalysis in the Mg-Al-Ca Alloy
- System", in Magnesium Technology 2003, ed., H.I. Kaplan, TMS, Materials Park, OH, 2003.
- Y. Zhang, K. Ozturk, Z.-K. Liu and A.A. Luo, "Computational Thermodynamics and Experimental Investigation of the Mg-Al-Ca-Sr Alloys", in Magnesium Technology 2002, ed., H.I. Kaplan, TMS, Materials Park, ОН, 2002, 69-73.
- B.R. Powell, A. Luo, V. Rezhets, J.J. Bommarito and B.L. Tiwari: "Development of Creep-Resistant Magnesium Alloys for Powertrain Applications: Part 1 of 2", SAE Technical Paper 2001-01-0422, Detroit, MI, 2001.
- B.R. Powell, V. Rezhets, and R.A. Waldo, "The Relationship Between Microstructure and Creep Behavior in AE42 Magnesium Die Casting Alloy," in Magnesium Technology 2001, ed. by J.N. Hryn, TMS, Warrendale, PA, USA, 2001, pp 175-181.
- Chengou Tian of Hydro Magnesium, USCAR MPCC (AMD 304) Quarterly Review Meeting Notes, 2003.
- M. Pekguleryuz, P.Lebelle, D. Argo, E. Baril, "Magnesium Die Casting Alloy AJ62X with Superior Creep Resistance, Ductility and Diecastability", in Magnesium Technology 2003, ed. H.I. Kaplan, TMS, Materials Park, OH, 2003, 201-206.
- L. Backerud, E. Krol, J. Tamminen, Solidification Characteristics of Aluminum Alloys, v.2 Foundry Alloys, AFS/Skanaliuminum, 1990.
- D.H. StJohn, A.K. Dahle, T. Abbott, M.D. Nave, Ma Qian, "Solidification of Cast Magnesium Alloys", in Magnesium Technology 2003, ed. H.I. Kaplan, TMS, Materials Park, OH, 2003, 95-100.
- P.R. Roberge, "What is Accelerated in Accelerated Testing: A Framework for Definition." Cyclic Corrosion Testing, ASTM STP 1238, Gardner S. Haynes, Ed.; American Society for Testing of Materials, Philadelphia, 1995.
- O. Lunder, K. Nisancioglu, R. Steen Hansen, „Corrosion of Die Cast Magnesium-Aluminum Alloys“, SAE paper 930755, SAE Int. Cong.&Expo. Detroit, MI 1995.
9. Copyright:
- This material is Randy Beals¹, Lawrence Kopka¹, John Allison², Joy A. Hines², Bob McCune², Alan Luo³, Bob Powell³ and Peter Ried⁴.'s paper: Based on "Fundamental Research Needs for the Magnesium Powertrain Cast Components (MPCC) Project".
- Paper Source: Not provided in the OCR.(Need to manually add the DOI from the first page if available,e.g. https://www.researchgate.net/publication/242243178)
This material was created to introduce the above paper, and unauthorized use for commercial purposes is prohibited.
Copyright © 2025 CASTMAN. All rights reserved.