This article introduces the paper ['Aluminium High Pressure Die Casting Application on Rear Frame Rails'] published by ['European Mechanical Science'].
1. Overview:
- Title: Aluminium High Pressure Die Casting Application on Rear Frame Rails
- Author: Ibrahim Ozbay, Tamer Aydiner, Gürkan Yilmazoglu, Hafize Celik, Levent Aksel, Harun Yeni, Metehan Bayramoglu, Erdem Aydogmus
- Publication Year: 2019
- Publishing Journal/Academic Society: European Mechanical Science
- Keywords: Rear Rail Reinforcement Support Bracket, Al Alloy, High Pressure Die Casting, Body In White (BIW)
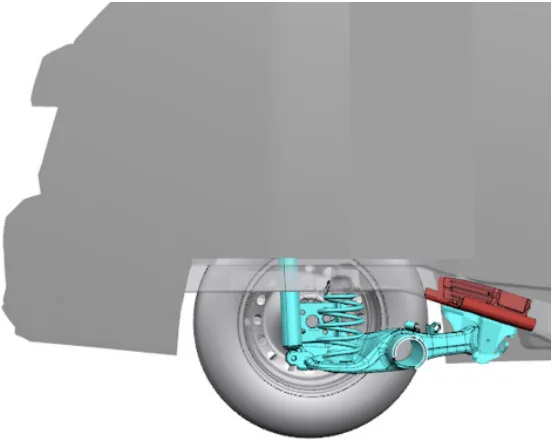
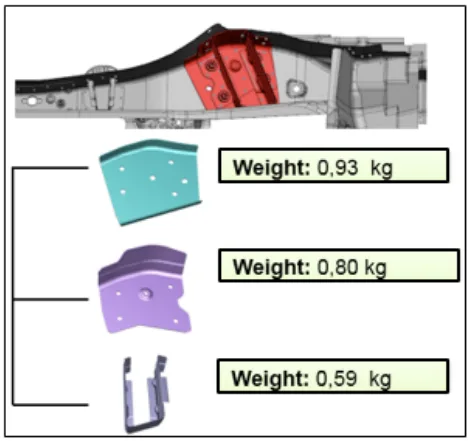
2. Abstracts or Introduction
In the face of intense competition and stringent environmental regulations within the automotive sector, manufacturers are increasingly adopting materials that offer superior mechanical properties and contribute to lightweighting, moving away from conventional materials like steel. Aluminium alloys are exemplary in this regard, being approximately three times lighter than steel. The utilization of aluminium in car body structures is gaining traction due to its inherent durability. When coupled with optimized geometry and appropriate heat treatments, aluminium can meet the mechanical demands of structural components. Casting, as a manufacturing process, facilitates topology optimization and the creation of complex geometries, yielding components with enhanced strength-to-weight ratios compared to stamped sheet metal parts. The rear rail reinforcement support bracket is identified as a prime candidate within Body In White (BIW) structures for the application of topologically optimized aluminium die-casted parts. Traditional reinforcement support brackets, often composed of multiple steel stampings to achieve the required stiffness and durability, result in intricate designs from design, formability, and assembly perspectives. This research investigates the design and production of a novel part using high-pressure die casting to match the performance of existing solutions. Furthermore, various heat treatments were evaluated to identify the optimal cycle for enhancing mechanical properties. The new design and the current solution were subjected to virtual validation, and comparative results are presented.
3. Research Background:
Background of the Research Topic:
The automotive industry's escalating safety standards necessitate new generation vehicle body structures with improved structural integrity and energy absorption capabilities during collisions. Simultaneously, stringent environmental regulations mandate lower carbon emissions. Vehicle weight is a critical factor influencing carbon emissions and fuel consumption. A 100 kg reduction in vehicle weight can lead to a 9g/km decrease in CO₂ emissions. Therefore, reducing vehicle weight is imperative for CO₂ emission reduction while maintaining safety, driving quality, and overall performance. The automotive body structure constitutes approximately 40% of the total vehicle weight, making weight reduction in this area crucial for achieving fuel efficiency, minimizing harmful emissions, and conserving raw materials.
Status of Existing Research:
Various design methodologies and innovative materials, including aluminium, magnesium, and composites, are being explored to reduce vehicle body weight. Aluminium is highlighted as a leading material for body weight reduction due to its cost-effectiveness, workability, corrosion resistance, recycling advantages, and widespread acceptance in the automotive industry. Aluminium alloys offer several advantages over steel in automotive applications, including: lower density (2.7g/cm³ compared to 7.87 gr/cm³ for steel), higher impact energy absorption per unit weight, and superior thermal conductivity, beneficial for radiator cores and heat exchangers.
Necessity of the Research:
In current vehicle designs, rear suspension support brackets are typically constructed from three pieces of steel sheets, weighing 2.7 kg in total. These components are joined using numerous spot welds and structural adhesives, leading to increased vehicle weight and manufacturing costs. There is a need to explore alternative materials and manufacturing processes to reduce weight and cost while maintaining or improving performance.
4. Research Purpose and Research Questions:
Research Purpose:
The primary objective of this study is to redesign a rear rail suspension support bracket using aluminium alloy and high-pressure die casting to achieve weight reduction and cost efficiency without compromising structural performance and safety.
Key Research:
The key research focuses on:
- Designing a single-piece rear suspension support bracket using aluminium alloy and high-pressure die casting.
- Optimizing the design through topology optimization to maximize stiffness and minimize weight.
- Determining the optimal heat treatment for the aluminium die-casted bracket to achieve desired mechanical properties.
- Validating the performance of the new aluminium die-casted bracket through virtual analysis, comparing it to the existing steel bracket solution in terms of crashworthiness, durability, and NVH (Noise, Vibration, and Harshness) characteristics.
Research Hypotheses:
The research hypothesizes that:
- An aluminium high-pressure die-casted rear suspension support bracket can achieve comparable or superior structural performance to the existing multi-piece steel bracket.
- The redesigned aluminium bracket will result in a significant weight reduction compared to the steel bracket.
- Optimized heat treatment will enhance the mechanical properties of the aluminium die-casted bracket, making it suitable for structural automotive applications.
5. Research Methodology
Research Design:
The research employs a design and validation approach. Initially, topology optimization was utilized to generate an optimal design for the aluminium bracket based on the load conditions at the suspension connection area. The design space for optimization was defined within the U-section crossmember. Finite Element Method (FEM) was used for topology optimization under unit loads applied in X, Y, and Z directions at the suspension joint point.
Data Collection Method:
The study primarily utilizes virtual validation tools for performance evaluation. Experimental data on material properties of Silafont-36 aluminium alloy and different heat treatments were used to inform the virtual simulations.
Analysis Method:
Virtual analysis methods were employed to assess:
- Casting Analysis: Mold filling and solidification simulations were conducted to identify potential casting defects like porosity and distortion, and to optimize the gating and cooling system design.
- Virtual Verification:
- Rear Crash Performance (TRIAS 33): Simulations were performed according to TRIAS 33 rear crash scenario to evaluate the structural integrity and deformation behavior of the aluminium bracket compared to the steel bracket.
- Fatigue Performance: Fatigue analysis was conducted to assess the fatigue life of the aluminium bracket under repeated shock loads.
- Modal Analysis Performance: Modal analysis was performed to evaluate the NVH characteristics, specifically the natural frequencies and dynamic stiffness, of the vehicle with the aluminium bracket.
- Torsional-Bending Stiffness Performance: The torsional and bending stiffness of the vehicle with the aluminium bracket were evaluated and compared to the steel bracket.
Research Subjects and Scope:
The research focuses on the rear suspension support bracket of a passenger vehicle. The material under investigation is Silafont-36 (AlSi10MnMg) aluminium alloy, processed by high-pressure die casting. The scope includes design, material selection, heat treatment optimization, and virtual validation of the aluminium die-casted bracket.
6. Main Research Results:
Key Research Results:
- Weight Reduction: The aluminium die-casted rear suspension support bracket achieved a weight reduction of approximately 3.0 kg per vehicle compared to the steel bracket assembly.
- Spot Welding Reduction: The new design eliminated approximately 35% of spot welding joints compared to the existing steel bracket.
- Material Selection and Heat Treatment: Silafont-36 aluminium alloy with T6 heat treatment was selected as the optimal material and heat treatment combination, offering a balance of strength and elongation. T6 heat treatment involves solutionizing at 520°C, quenching, and artificial aging at 180°C.
- Casting Analysis: Casting simulations informed design modifications to mitigate porosity and distortion risks, optimizing the mold design with additional cooling lines and multiple gates.
- Virtual Verification:
- Rear Crash Performance (TRIAS 33): TRIAS 33 simulations indicated satisfactory rear crash performance for the aluminium bracket, showing no negative results compared to the steel bracket (FIG.11 Rear impact virtual analysis result - bottom view).
- Fatigue Performance: Fatigue analysis demonstrated improved fatigue life performance for the aluminium bracket due to design optimizations in critical areas (FIG.12 Fatigue Life Analysis).
- Modal Analysis Performance: Modal analysis showed a slight increase (~0.5 Hz) in the vehicle's torsional mode with the aluminium bracket, indicating improved NVH characteristics in this aspect (Fig.13 NVH analysis for suspension joint point).
- Torsional-Bending Stiffness Performance: The torsional mode of the vehicle increased by 3-5% with the aluminium bracket, suggesting enhanced torsional stiffness.
Analysis of presented data:
The data presented in figures and charts demonstrate the effectiveness of the aluminium die-casted bracket. Figure 6 illustrates the yield strength and elongation of Silafont-36 under various heat treatments, highlighting the T6 condition as a suitable choice. Figure 7 shows the schematic representation of the T6 heat treatment cycle. Figure 8 and 9 depict the casting analysis results, showing porosity and distortion analysis and mold filling and solidification analysis respectively. Figures 11, 12, and 13 present the virtual verification results for rear impact, fatigue life, and NVH performance, demonstrating the aluminium bracket's comparable or improved performance relative to the steel counterpart. Chart 1 details the chemical composition of Silafont-36, and Chart 2 summarizes the experimental study parameters and results for different heat treatments.
Figure Name List:
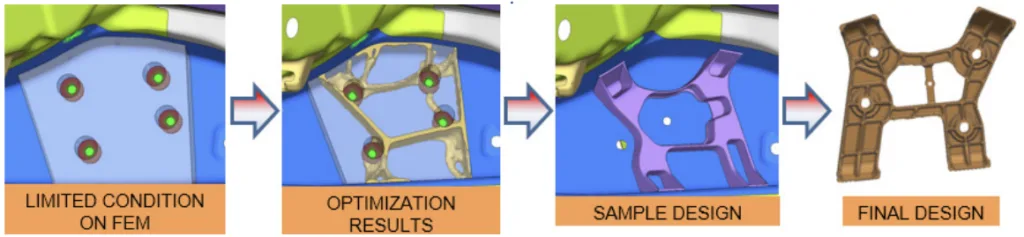
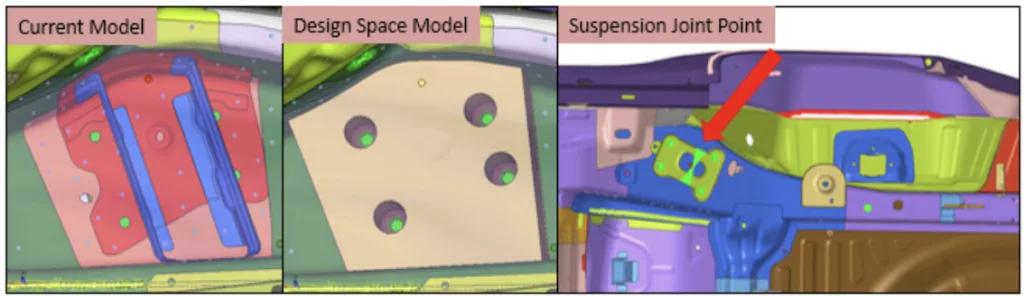
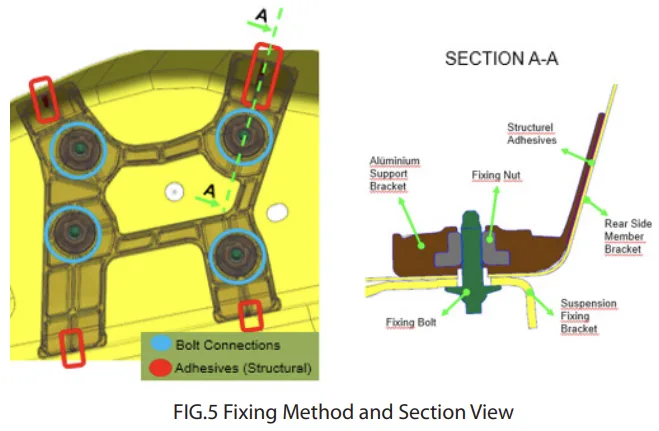
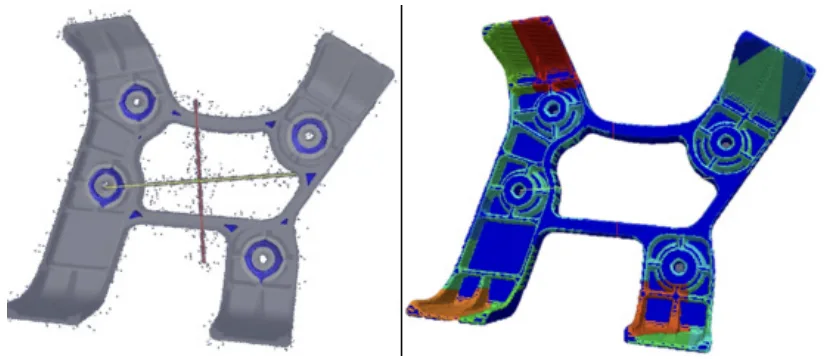
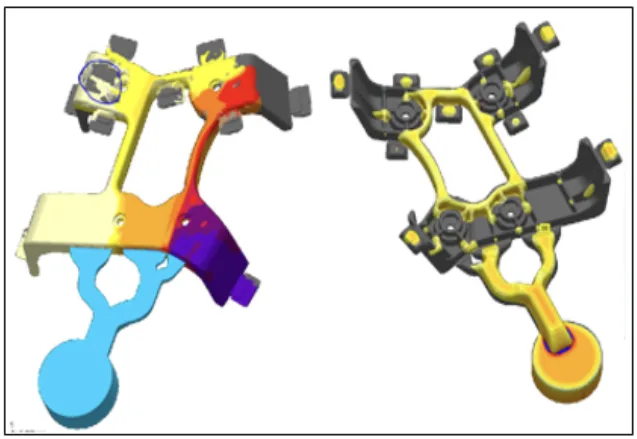
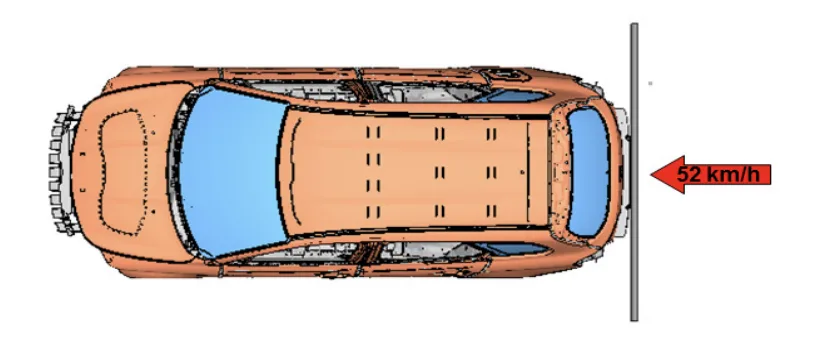
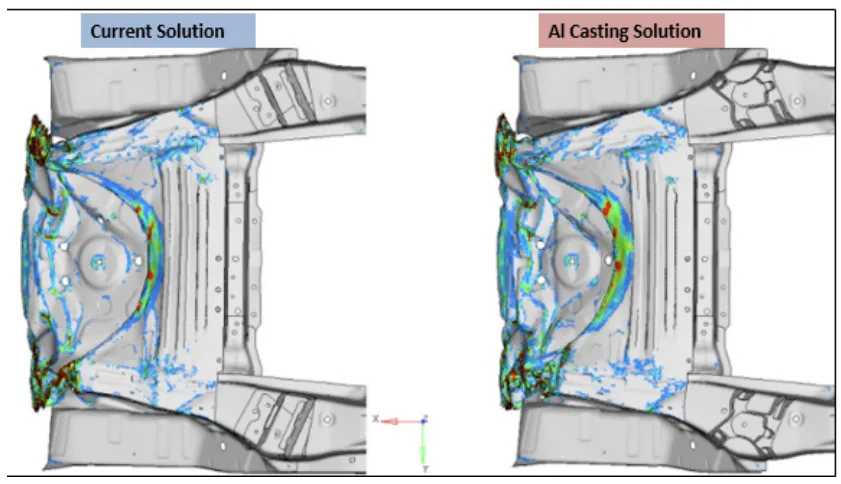
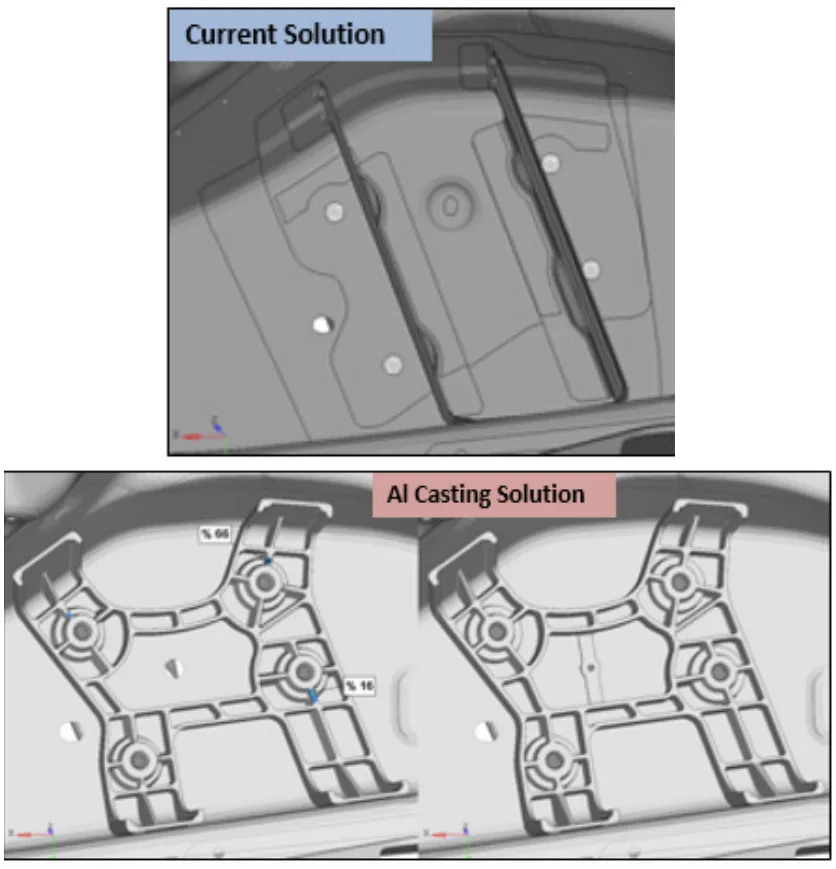
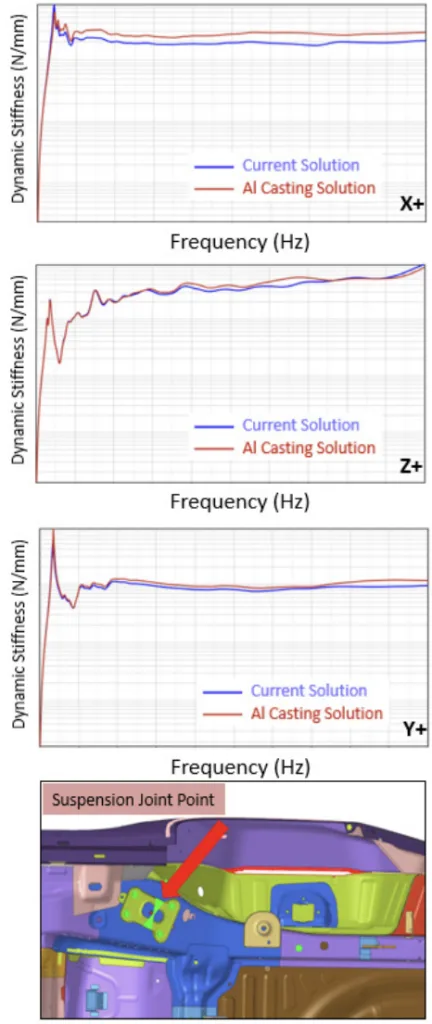
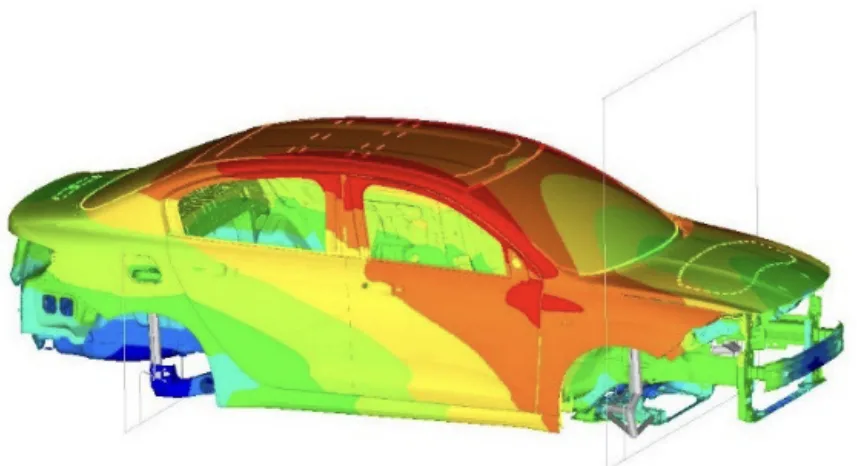
- FIG.1 Connection of Rear Suspension to Body experimental procedure
- FIG.2 Rear Suspension Support Brackets Display and Assembling Details
- FIG.3 The Topology Optimization and Final Design
- FIG.4 Current model, design space model in U-section body arm and Suspension Joint Point.
- FIG.5 Fixing Method and Section View
- FIG.6 Silafont-36 Yield strength and elongation in various heat treatment states [6]
- FIG.7 T6 heat treatment schematic representation (temperatures and durations may vary depending on the type of material, design and requirements)
- FIG.8 Porosity and Distortion Analysis and of Design
- FIG.9 Mold Filling and Solidification Analysis and of Design
- FIG.10 Rear Impact Condition of the Vehicle for TRIAS 33 Validation
- FIG.11 Rear impact virtual analysis result - bottom view
- FIG.12 Fatigue Life Analysis
- FIG.13 NVH analysis for suspension joint point
- FIG. 14 Torsional- Bending Stiffness Analysis in BIW model
7. Conclusion:
Summary of Key Findings:
This study successfully demonstrated the feasibility of using aluminium high-pressure die casting for manufacturing rear suspension support brackets in automotive BIW structures. The redesigned aluminium bracket, made from Silafont-36 alloy and subjected to T6 heat treatment, achieved a significant weight reduction of 3.0 kg per vehicle and a 35% reduction in spot welding compared to the conventional steel assembly. Virtual validation confirmed that the aluminium bracket meets or exceeds the performance of the steel bracket in terms of crashworthiness, fatigue life, and NVH characteristics.
Academic Significance of the Study:
This research contributes to the growing body of knowledge on lightweighting in automotive engineering, specifically by demonstrating the application of aluminium high-pressure die casting for structural components. It highlights the effectiveness of topology optimization and virtual validation in designing and verifying high-performance die-casted parts. The study also provides valuable insights into the material selection and heat treatment optimization for aluminium alloys in structural automotive applications.
Practical Implications:
The findings of this study have significant practical implications for the automotive industry. The successful implementation of aluminium high-pressure die-casted rear suspension support brackets can lead to:
- Reduced vehicle weight, contributing to improved fuel efficiency and lower CO₂ emissions.
- Simplified assembly processes and reduced manufacturing costs due to the single-piece design and decreased spot welding.
- Enhanced vehicle performance and NVH characteristics.
- Increased utilization of recyclable aluminium alloys in automotive structures, promoting sustainability.
Limitations of the Study and Areas for Future Research:
This study primarily relies on virtual validation. Future research should include physical prototyping and experimental testing to further validate the performance of the aluminium die-casted bracket in real-world conditions. Further investigation into different aluminium alloys, casting process parameters, and joining techniques could also be explored to optimize the design and manufacturing process further. The long-term durability and corrosion resistance of the aluminium bracket in service conditions warrant further investigation.
8. References:
- [1] Hirsch, J. (2011). Aluminium in Innovative Light-Weight Car Design. Materials Transactions, 52(5): 818-824, DOI:10.2320/matertrans.L-MZ201132.
- [2] Altınok, E., Kayserili, H., Mert A., Altınel, S.A. (2017). Lightweight Door Ring Solution in Car Body Development. International Journal of Advances on Automotive and Technology, 1(3): 131-136, DOI: 10.15659/ijaat.17.07.529.
- [3] Başer, T. A. (2013). Alüminyum alaşımları ve otomotiv endüstrisinde kullanımı. Mühendis ve Makina, 53(635): 51-58.
- [4] Mallick, P.K. (2010). Materials, Design and Manufacturing for Lightweight Vehicles, Cambrighe, UK: Woodhead Publishing Limited.
- [5] Wu, P., Ma, Q., Luo, Y., Tao, C. (2016). Topology Optimization Design of Automotive Engine Bracket. Energy and Power Engineering, 8(4): 230-235, DOI: 10.4236/epe.2016.84021.
- [6] KG, Rheinfelden Alloys GmbH & Co., "Primary Aluminium Alloys for Pressure Die Casting," A company of the Aluminium Rheinfelden Group, Friedrichstraße 80.
- [7] Chaudhury, S.K., Apelian, D. (2006). Fluidized Bed Heat Treatment of Cast Al-Si-Cu-Mg Alloys. Metallurgical and Materials Transactions A, 37A: 2295-2311.
- [8] M. Hartlieb, (2013). Aluminium Alloys For Structural Die Casting. Die Casting Engineer, 41.
- [9] Kurisu, F., Miyauchi, K. (2004). Application of ADAMS Mechanism Analysis Software To Powertrains. Mazda Technical Review, 22: 44-49.
- [10] Aksel, L., Efendioğlu, Ş., Yeni H., Bilge, Ç. (2016). Weight Reduction Study on BIW by Using Boron Alloyed Hot Stamping Solution of Front Frame Rail Instead Conventional HSS or AHSS Applications. in International Conference on Advanced Technology & Sciences.
- [11] Joost, W. J., Krajewski, P.E. (2017). Towards magnesium alloys for high-volume automotive applications. Scripta Materialia, 128: 107-112, DOI: 10.1016/j.scriptamat.2016.07.035.
9. Copyright:
- This material is "Ibrahim Ozbay, Tamer Aydiner, Gürkan Yilmazoglu, Hafize Celik, Levent Aksel, Harun Yeni, Metehan Bayramoglu, Erdem Aydogmus"'s paper: Based on "Aluminium High Pressure Die Casting Application on Rear Frame Rails".
- Paper Source: https://doi.org/10.26701/ems.422299
This material was summarized based on the above paper, and unauthorized use for commercial purposes is prohibited.
Copyright © 2025 CASTMAN. All rights reserved.