This article introduces the paper 'INDUSTRY 4.0 FOUNDRY DATA MANAGEMENT AND SUPERVISED MACHINE LEARNING IN LOW-PRESSURE DIE CASTING QUALITY IMPROVEMENT' published by 'International Journal of Metalcasting'.
1. Overview:
- Title: INDUSTRY 4.0 FOUNDRY DATA MANAGEMENT AND SUPERVISED MACHINE LEARNING IN LOW-PRESSURE DIE CASTING QUALITY IMPROVEMENT
- Author: Tekin Ç. Uyan, Maria Santos Silva, Pedro Vilaça, Kevin Otto, Elvan Armakan
- Publication Year: 2023
- Publishing Journal/Academic Society: International Journal of Metalcasting
- Keywords: low-pressure die casting, machine learning, alloy wheels, industry 4.0, smart foundry, sustainable metals processing
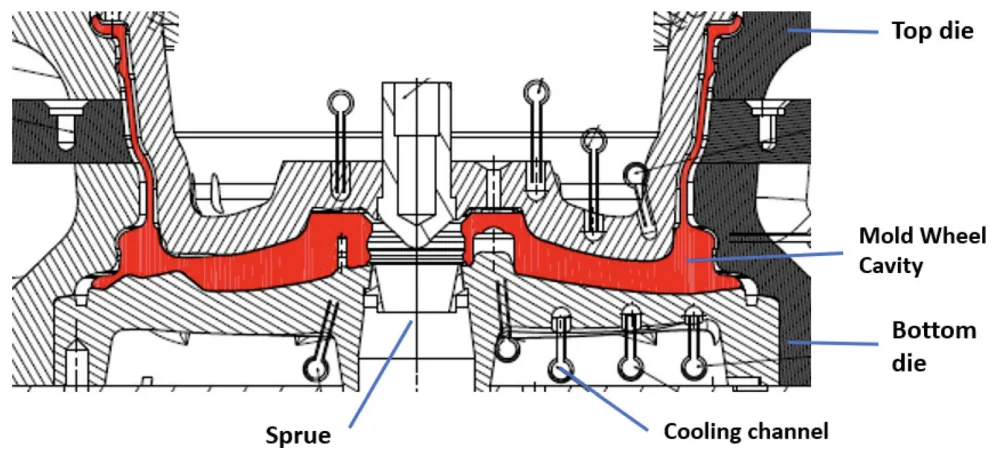
2. Abstracts or Introduction
Low-pressure die casting (LPDC) is essential for producing high-performance aluminum alloy automobile wheel castings, where porosity defects are unacceptable. Maintaining the quality of LPDC parts is heavily dependent on process conditions. Optimizing process variables is crucial to minimize defects like gas and shrinkage porosity. This study utilizes Industry 4.0 cloud-based systems to extract process data and employs supervised machine learning classification models to identify conditions leading to defects in an industrial Aluminum LPDC process. Root cause analysis is challenging due to the low defect rate and numerous potential process variables. An XGBoost classification algorithm-based model was used to map the complex relationship between process conditions and defect formation in wheel rims. Data was collected from a specific LPDC machine and die mold over three shifts for six continuous days. Porosity defect occurrence rates were predicted using 36 features from 13 process variables, derived from a small sample (1077 wheels with 62 defectives). The model achieved 87% accuracy for good parts and 74% accuracy for parts with porosity defects. This research aids in process parameter tuning for new product pre-series production to reduce defectives.
3. Research Background:
Background of the Research Topic:
Low-pressure die casting (LPDC) is widely used for manufacturing metal cast components requiring high performance and precision, particularly aluminum alloy wheel rims in the automotive sector. Porosity discontinuities are a common defect in LPDC aluminum products, compromising component integrity and performance. Therefore, preventing porosity defects is a key focus in quality control, driving the need to optimize process variables for improved part quality. Porosity can arise from various factors, including metal composition, hydrogen content, casting pressures, temperatures, and die thermal management for directional cooling rates. Diagnosing the root cause of casting defects and adjusting process parameters accordingly is often challenging. Monitoring and analyzing process settings and deviations that contribute to porosity is essential. Industry 4.0 quality control systems can link recorded data from process measurement points to individual parts and their inspection results. Machine learning classifier algorithms can then identify process setting combinations that lead to defects, aiding in process control tuning.
Status of Existing Research:
LPDC production has historically faced high defective rates, necessitating X-ray inspection for porosity defects in almost every part. While X-ray inspection remains essential, machine learning can help predict porosity defectives and quantify their causes. Foundries often manage numerous models and introduce new product models annually, making rapid process tuning in pre-series production critical. Existing foundry process controls are generally inspection-based, relying on visual inspection of X-Ray images for porosity voids and monitoring process parameters for compliance within specified limits. This approach suffers from repeatability and reproducibility issues in visual inspection and manual control. It may also fail to detect porosity defects arising from combinations of inputs within tolerance limits. A "Digital Twin," constructed from machine learning, is proposed as a virtual process model to predict part quality. This model relies on part marking and tracking throughout foundry operations and extensive quality data acquisition, which are not yet widely common in Industry 4.0.
Necessity of the Research:
Challenges in utilizing factory data for machine learning models include the vast number of potential causal factors, difficulty in instrumenting and collecting all process data, and identifying relevant features in time series data (e.g., shifts, variability, jumps). Associating process data with specific parts requires part tracking throughout the foundry, a key Industry 4.0 challenge for Smart Foundries operating in harsh conditions. Preprocessing time series data into meaningful features for machine learning is also crucial, focusing on engineering statistics understandable by process engineers (e.g., phase-based statistics like mean and variance). Finally, selecting appropriate classification methods to link features to defect rates remains a research opportunity to better understand defect sources and root causes. Current state of defective control is difficult due to visual inspection and manual control which has substantial repeatability and reproducibility measurement errors.
4. Research Purpose and Research Questions:
Research Purpose:
The objective of this research is to develop a methodology for collecting LPDC foundry process data and applying machine learning models to correlate process parameters and tolerances with the occurrence of critical defects. This method aims to utilize machine process data collection, part tracking, and quality inspection data to predict porosity defectives in LPDC processing of aluminum alloy high-performance automotive wheels within an industrial foundry setting, using a small dataset to establish process settings.
Key Research:
- Development of an Industry 4.0 data collection system for LPDC foundries to digitally timestamp and track parts and associated data.
- Application of supervised machine learning classification models, specifically XGBoost, to identify process conditions predicting porosity defects.
- Feature engineering of time series process data into relevant statistical features for machine learning analysis.
- Evaluation of model performance in predicting porosity defects using a small and imbalanced industrial dataset.
- Interpretation of feature importance using Shapley values to identify key process parameters influencing porosity defects.
Research Hypotheses:
- Industry 4.0 data collection systems, combined with machine learning, can effectively predict porosity defects in LPDC processes using routinely collected production data.
- XGBoost algorithm is suitable for handling imbalanced datasets and can achieve acceptable accuracy in predicting porosity defects in LPDC with a limited dataset.
- Statistical features extracted from time series process data can effectively represent process variations and correlate with porosity defect occurrence.
- Identifying key process parameters through feature importance analysis can provide actionable insights for process optimization and defect reduction in LPDC.
5. Research Methodology
Research Design:
This research employed a data-driven approach, utilizing historical production data from an industrial LPDC foundry. The study focused on a specific LPDC machine and die mold producing aluminum alloy wheel castings. Data collection spanned three shifts over six continuous days. The research design involved:
- Data Collection System Implementation: Utilizing an Industry 4.0 cloud-based system to extract and integrate process data from various sources (LPDC machine sensors, material batch data, X-ray inspection data).
- Part Tracking: Implementing a system to track individual parts throughout the foundry process, linking process data to quality inspection results.
- Feature Engineering: Preprocessing time series process data to extract statistical features (means, standard deviations, durations) relevant to porosity defect formation.
- Machine Learning Model Development: Training and evaluating an XGBoost classification model to predict porosity defects based on the extracted features.
- Model Validation: Assessing model performance using a stratified split of the dataset into training and testing sets, and employing 10-fold cross-validation.
- Feature Importance Analysis: Utilizing Shapley values to interpret the XGBoost model and identify key process parameters influencing porosity defects.
Data Collection Method:
Data was collected from Cevher Wheels Casting Plant in Izmir, Turkey. The data collection process included:
- LPDC Machine Data: Time series data from sensors monitoring molding pressure, temperature, air and water channel cooling, recorded at one- to two-second intervals.
- Material Batch Data: Aluminum alloy metal batch properties, including density index (DI) and silicon content (Si), obtained from laboratory chemical analysis of samples taken at the furnace.
- X-ray Inspection Data: Pass/fail results for porosity defects, determined by X-ray scanning of 100% of the wheel rims, according to DIN EN ISO 19232-1 and DIN EN ISO 19232-5 standards.
- Part Tracking Data: Time stamps and part identifiers at each stage of the process (LPDC machine, X-ray inspection) to link datasets.
Analysis Method:
The analysis methods employed were:
- Statistical Feature Extraction: Time series data was segmented into phases (e.g., fill, solidification), and statistical features (mean, standard deviation) were calculated for each phase for variables like pressure and temperature.
- XGBoost Classification: The XGBoost algorithm was used for binary classification (good/defective parts). Hyperparameter tuning was performed using Bayesian Optimization from the Hyperopt library.
- Performance Metrics: Model performance was evaluated using accuracy, precision, recall, and F1 score. Area Under the Curve (AUC) was used as the objective function for hyperparameter optimization.
- Shapley Value Analysis: Shapley values were calculated to determine the contribution of each input feature to the model's predictions, providing insights into feature importance.
Research Subjects and Scope:
The research subjects were aluminum alloy wheel castings produced by a specific LPDC machine and die mold at Cevher Wheels Casting Plant. The dataset comprised 1077 wheel rims, of which 62 were identified as defective due to porosity. The scope was limited to porosity defects and did not include other types of casting defects. The analysis focused on 36 features derived from 13 process variables related to LPDC machine operation and material properties.
6. Main Research Results:
Key Research Results:
- The XGBoost classification model achieved 87% accuracy in predicting good parts and 74% accuracy in predicting parts with porosity defects on the test dataset.
- Feature importance analysis using Shapley values identified air channel flow rates, particularly the standard deviation of air flow in channels near the center hub, and melt silicon content as the most significant predictors of porosity defects.
- The model demonstrated the ability to predict porosity defects using a small and imbalanced industrial dataset, highlighting the potential of machine learning for quality improvement in LPDC.
- A tradeoff between precision and recall was observed, allowing for adjustment of model parameters to prioritize either minimizing false positives or false negatives based on specific foundry needs.
Analysis of presented data:
- Confusion Matrix (Figure 6): Shows the model's classification performance, with TN=440, FN=65, FP=8, and TP=23. This indicates a higher accuracy for good parts (87% recall) compared to defective parts (74% recall).
- Statistical Summary Report (Table 2): Provides precision, recall, and F1 score for both good and defective parts, further quantifying the model's performance.
- Example Binary Decision Tree Estimator (Figure 7): Illustrates a simplified decision tree from the XGBoost model, showing how specific feature values (e.g., Air Channel 2 std, Density Index) influence the probability of failure.
- Feature Importance Order (Figure 8): Ranks the input features based on their Shapley index, highlighting the most influential variables in predicting porosity defects. The top features are related to air flow standard deviation in different cooling channels and melt silicon content.
- Model Tradeoff Curve (Figure 9): Demonstrates the tradeoff between pass and fail accuracy, showing that increasing defective part prediction accuracy reduces good part prediction accuracy, and vice versa.
Figure Name List:
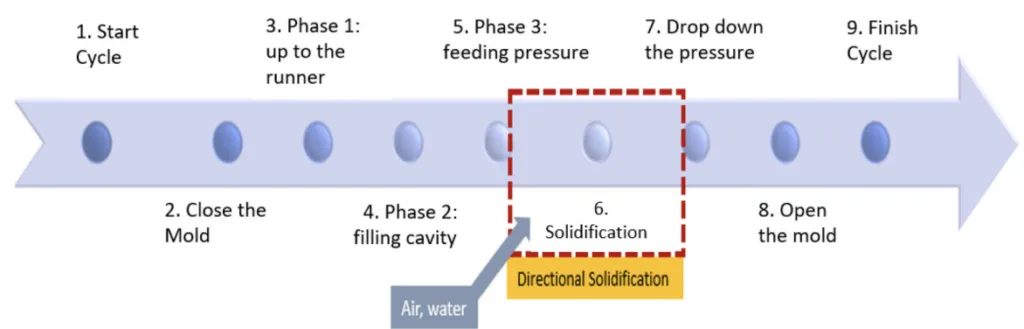


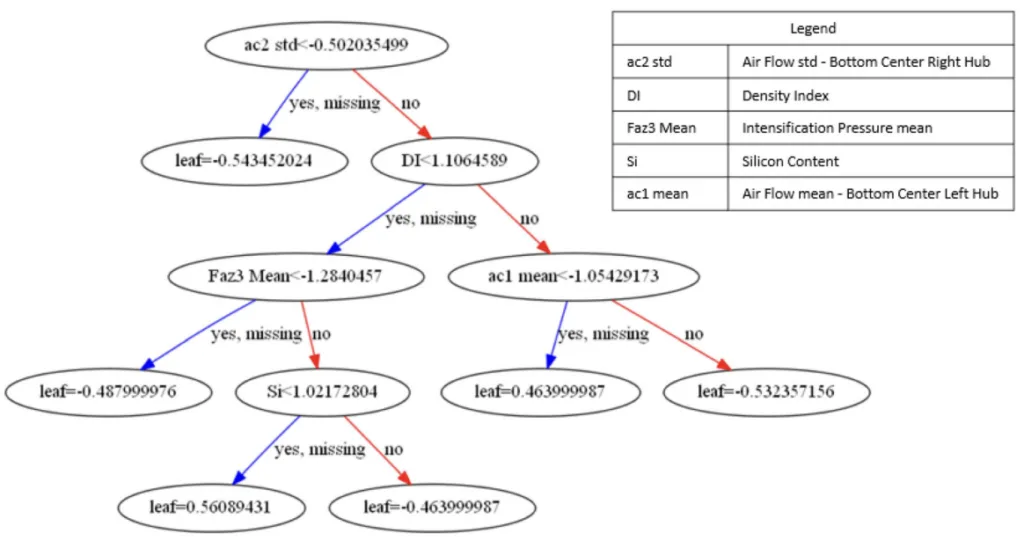
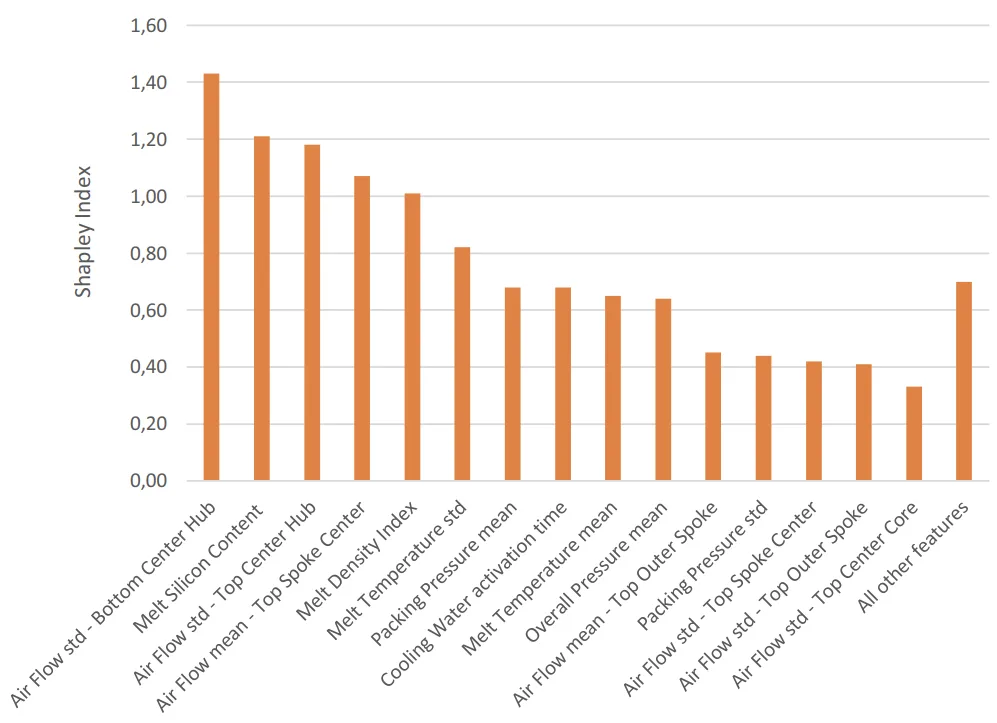
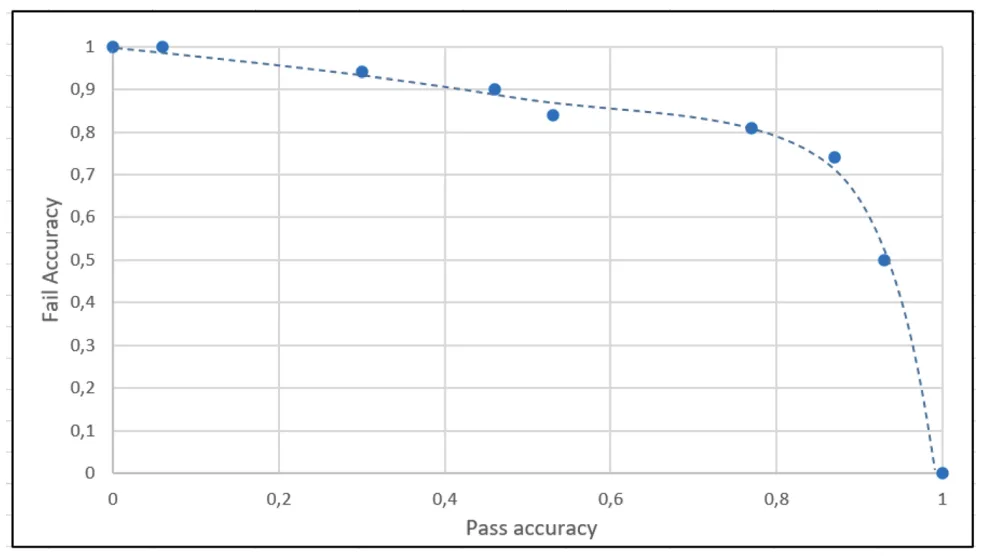
- Figure 1. Intersection of a die mold of LPDC machine.
- Figure 2. Low-pressure die casting process cycle.
- Figure 3. Time series pressure measurement on LPDC machine.
- Figure 4. X-ray scan of die cast wheel rim with a porosity defect on a spoke.
- Figure 5. An example of an intensification pressure cycle with high variability.
- Figure 6. Confusion matrix of the XGBoost model for part quality.
- Figure 7. Example binary decision tree estimator.
- Figure 8. Feature importance order.
- Figure 9. Model tradeoff between pass and fail accuracy.
7. Conclusion:
Summary of Key Findings:
This study successfully demonstrated the application of Industry 4.0 data management and supervised machine learning for quality improvement in LPDC. The XGBoost model effectively predicted porosity defects with reasonable accuracy using a small, imbalanced industrial dataset. Key predictors of porosity defects were identified as variations in air cooling channel flow rates and melt silicon content. The research provides a methodology for foundries to leverage production data for process optimization and defect reduction.
Academic Significance of the Study:
This research contributes to the growing body of literature on applying machine learning in manufacturing, specifically in metal casting. It demonstrates the feasibility of using readily available industrial data and advanced machine learning techniques like XGBoost and Shapley values to address complex quality control challenges in LPDC. The study also highlights the importance of feature engineering and data preprocessing for effective machine learning model development in industrial settings.
Practical Implications:
The findings have significant practical implications for LPDC foundries. The developed methodology can be implemented to:
- Predict porosity defects in pre-series production: Assisting in rapid process parameter tuning for new products.
- Identify critical process parameters: Enabling targeted process optimization efforts to reduce defects.
- Improve quality control: Complementing traditional inspection methods with predictive capabilities.
- Reduce scrap rates and production costs: By proactively addressing defect causes.
- Enable data-driven decision-making: Providing a quantitative basis for process adjustments and quality management.
Limitations of the Study and Areas for Future Research:
- Small Dataset: The model was trained and validated on a relatively small dataset from a single LPDC machine and die mold. Larger and more diverse datasets are needed to improve model generalization and robustness.
- Limited Defect Types: The study focused solely on porosity defects. Future research could expand the scope to include other types of casting defects and develop multiclass classification models.
- Feature Set: While 36 features were used, exploring additional process parameters and more sophisticated feature engineering techniques could further enhance model performance.
- Automated Data Collection and Tracking: The current data collection was semi-automated. Future work should focus on implementing fully automated part tracking and data acquisition systems for seamless integration and real-time quality monitoring.
- Real-time Prediction and Control: Future research could explore integrating the developed model into a real-time process control system for proactive defect prevention.
8. References:
- [1] T. Uyan, K. Jalava, J. Orkas, K. Otto, Sand casting implementation of two-dimensional digital code direct-part-marking using additively manufactured tags. Int. J. Metalcast. (2021). https://doi.org/10.1007/s40962-021-00680-x
- [2] J. Landry, J. Maltais, J.M. Deschênes, M. Petro, X. Godmaire, A. Fraser, Inline integration of shot-blast resistant laser marking in a die cast cell. NADCA Trans 2018, T18–T123 (2018)
- [3] A. Fraser, J. Maltais, A. Monroe, M. Hartlieb, X. Godmaire, Important considerations for laser marking an identifier on die casting parts
- [4] D. Blondheim Jr., S. Bhowmik, Time-series analysis and anomaly detection of high-pressure die casting shot profiles. NADCA Die Cast. Eng., 14–18 (2019)
- [5] D. Blondheim, Improving manufacturing applications of machine learning by understanding defect classification and the critical error threshold. Int. J. Metalcast. (2021). https://doi.org/10.1007/s40962-021-00637-0
- [6] T. Prucha, From the editor big data. Int. J. Met. 9(3), 5 (2015)
- [7] T. Prucha, From the editor—AI needs CSI: common sense input. Int. J. Met. 12(3), 425–426 (2018)
- [8] T. Chen, C. Guestrin. Xgboost: a scalable tree boosting system. In: Proceedings of the 22nd international conference on knowledge discovery and data mining, pp. 785–794 (2016)
- [9] W. Dong, Y. Huang, B. Lehane, G. Ma, XGBoost algorithm-based prediction of concrete electrical resistivity for structural health monitoring. Autom. Construct. 114, 103155 (2020)
- [10] M.S. Alajmi, A.M. Almeshal, Predicting the tool wear of a drilling process using novel machine learning XGBoost-SDA. Materials (Basel) 13(21), 1–16 (2020). https://doi.org/10.3390/ma13214952
- [11] K. Gao, H. Chen, X. Zhang, X.K. Ren, J. Chen, X. Chen, A novel material removal prediction method based on acoustic sensing and ensemble XGBoost learning algorithm for robotic belt grinding of Inconel 718. Int. J. Adv. Manuf. Technol. 105(1-4), 217-232 (2019). https://doi.org/10.1007/s00170-019-04170-7
- [12] S. Chakraborty, S. Bhattacharya, Application of XGBoost algorithm as a predictive tool in a CNC turning process. Reports Mech. Eng. 2(2), 190–201 (2021). https://doi.org/10.31181/rme2001021901b
- [13] K. Chen, H. Chen, L. Liu, S. Chen, Prediction of weld bead geometry of MAG welding based on XGBoost algorithm. Int. J. Adv. Manuf. Technol. 101(9–12), 2283–2295 (2019). https://doi.org/10.1007/s00170-018-3083-6
- [14] Z. Zhang, Y. Huang, R. Qin, W. Ren, G. Wen, XGBoost-based on-line prediction of seam tensile strength for Al-Li alloy in laser welding: experiment study and modelling. J. Manuf. Process. 64, 30-44 (2021). https://doi.org/10.1016/j.jmapro.2020.12.004
- [15] J. Deng, Y. Xu, Z. Zuo, Z. Hou, S. Chen, Bead geometry prediction for multi-layer and multi-bead wire and arc additive manufacturing based on XGBoost. Trans. Intell. Weld. Manuf. (2019). https://doi.org/10.1007/978-981-13-8668-8_7
- [16] D.K. Choi, Data-driven materials modeling with XGBoost algorithm and statistical inference analysis for prediction of fatigue strength of steels. Int. J. Precis. Eng. Manuf. 20(1), 129–138 (2019). https://doi.org/10.1007/s12541-019-00048-6
- [17] K. Song, F. Yan, T. Ding, L. Gao, S. Lu, A steel property optimization model based on the XGBoost algorithm and improved PSO. Comput. Mater. Sci. (2020). https://doi.org/10.1016/j.commatsci.2019.109472
- [18] S. Yan, D. Chen, S. Wang, S. Liu, Quality prediction method for aluminum alloy ingot based on XGBoost. In: Proceedings of the 32nd Chinese Control Decis. Conf. CCDC 2020, pp. 2542-2547, 2020. https://doi.org/10.1109/CCDC49329.2020.9164112
- [19] S. Pan, Z. Zheng, Z. Guo, H. Luo, An optimized XGBoost method for predicting reservoir porosity using petrophysical logs. J. Pet. Sci. Eng. 208, 109520 (2022). https://doi.org/10.1016/j.petrol.2021.109520
- [20] T. Tao et al., Wind turbine blade icing diagnosis using hybrid features and Stacked-XGBoost algorithm. Renew. Energy 180, 1004–1013 (2021). https://doi.org/10.1016/j.renene.2021.09.008
- [21] V.D. Tsoukalas, S.A. Mavrommatis, N.G. Orfanou-dakis, A.K. Baldoukas. A study of porosity formation in pressure die casting using the Taguchi approach. In: Proc. Inst. Mech. Eng. Part B J. Eng. Manuf., vol. 218, no. 1, pp. 77-86, 2004. https://doi.org/10.1243/095440504772830228
- [22] Q.C. Hsu, A.T. Do, Minimum porosity formation in pressure die casting by taguchi method. Math. Probl. Eng. (2013). https://doi.org/10.1155/2013/920865
- [23] W. Ye, W. Shiping, N. Lianjie, X. Xiang, Z. Jianbing, X. Wenfeng, Optimization of low-pressure die casting process parameters for reduction of shrinkage porosity in ZL205A alloy casting using Taguchi method. Proc. Inst. Mech. Eng. 228(11), 1508–1514 (2014). https://doi.org/10.1177/0954405414521065
- [24] D.M. Maijer, W.S. Owen, R.A. Vetter, An investigation of predictive control for aluminum wheel casting via a virtual process model. J. Mater. Process. Technol. 209(4), 1965–1979 (2009). https://doi.org/10.1016/J.JMATPROTEC.2008.04.057
- [25] V.D. Tsoukalas, Optimization of porosity formation in AlSi9Cu3 pressure die castings using genetic algorithm analysis. Mater. Des. 29(10), 2027–2033 (2008). https://doi.org/10.1016/j.matdes.2008.04.016
- [26] Guo, S.M., et al., Inline inspection improvement using machine learning on broadband plasma inspector in an advanced foundry fab. In: Proceedings of the SEMI Advanced Semiconductor Manufacturing Conference (ASMC). IEEE (2019)
- [27] Park, S., et al., Prediction of the CNC tool wear using the machine learning technique.. In: Proceedings of the 2019 International Conference on Computational Science and Computational Intelligence (CSCI)
- [28] D. Wilk-Kolodziejczyk, K. Regulski, G. Gumienny, Comparative analysis of the properties of the nodular cast iron with carbides and the austempered ductile iron with use of the machine learning and the support vector machine. Int. J. Adv. Manuf. Technol. 87(1-4), 1077–1093 (2016)
- [29] R. Rodríguez-Pérez, J. Bajorath, Interpretation of machine learning models using shapley values: application to compound potency and multi-target activity predictions. J. Comput. Aided. Mol. Des. 34(10), 1013-1026 (2020). https://doi.org/10.1007/$10822-020-00314-0
- [30] L. Zaremba, C.S. Zaremba, M. Suchenek, Modification of shapley value and its implementation in decision making. Found. Manag. 9(1), 257-272 (2017). https://doi.org/10.1515/fman-2017-0020]
- [31] D.C. Landinez-Lamadrid, D.G. Ramirez-Ríos, D. Neira Rodado, K. Parra Negrete, J.P. Combita Niño, Shapley Value: its algorithms and application to supply chains. INGE CUC 13(1), 61–69 (2017). https://doi.org/10.17981/ingecuc.13.1.2017.06
- [32] J. Ohana et al., Shapley values for LightGBM model applied to regime detection. 2021. [Online]. Available: https://hal.archives-ouvertes.fr/hal-03320300
- [33] J.K. Kittur, G.C. ManjunathPatel, M.B. Parappagoudar, Modeling of pressure die casting process: an artificial intelligence approach. Int. J. Metalcast. 10(1), 70–87 (2016). https://doi.org/10.1007/s40962-015-0001-7
- [34] J.K. Rai, A.M. Lajimi, P. Xirouchakis, An intelligent system for predicting HPDC process variables in interactive environment. J. Mater. Process. Technol. 203(1-3), 72–79 (2008). https://doi.org/10.1016/J.JMATPROTEC.2007.10.011
- [35] A. Kopper, R. Karkare, R.C. Paffenroth, D. Apelian, Model selection and evaluation for machine learning: deep learning in materials processing. Integr. Mater. Manuf. Innov. 9(3), 287-300 (2020)
- [36] A.E. Kopper, D. Apelian, Predicting quality of castings via supervised learning method. Int. J. Metalcast. (2021). https://doi.org/10.1007/s40962-021-00606-7
- [37] N. Sun, A. Kopper, R. Karkare, R.C. Paffenroth, D. Apelian, Machine learning pathway for harnessing knowledge and data in material processing. Int. J. Metalcast. 15(2), 398–410 (2021). https://doi.org/10.1007/s40962-020-00506-2
- [38] C. Reilly, J. Duan, L. Yao, D.M. Maijer, S.L. Cockcroft, Process modeling of low-pressure die casting of aluminum alloy automotive wheels. JOM 65(9), 1111-1121 (2013)
- [39] L. Zhang, R. Wang, An intelligent system for low-pressure die-cast process parameters optimization. Int. J. Adv. Manuf. Technol. 65(1-4), 517–524 (2013)
- [40] B. Zhang, S.L. Cockcroft, D.M. Maijer, J.D. Zhu, A.Β. Phillion, Casting defects in low-pressure die-cast aluminum alloy wheels. JOM 57(11), 36–43 (2005). https://doi.org/10.1007/s11837-005-0025-1
- [41] ASTM E155-15, Standard reference radiographs for inspection of aluminum and magnesium castings. ASTM International, West Conshohocken, 2015, www.astm.org
- [42] ISO 19232-1:2013, Non-destructive testing-image quality of radiographs-Part 1: determination of the image quality value using wire-type image quality indicators
- [43] ISO 19232-5:2018, Non-destructive testing-image quality of radiographs-Part 5: determination of the image unsharpness and basic spatial resolution value using duplex wire-type image quality indicators
- [44] D. Dispinar, J. Campbell, Porosity, hydrogen and bifilm content in Al alloy castings. Mater. Sci. Eng. A 528(10-11), 3860–3865 (2011). https://doi.org/10.1016/j.msea.2011.01.084
- [45] S. Akhtar, L. Arnberg, M. Di Sabatino et al., A comparative study of porosity and pore morphology in a directionally solidified A356 alloy. Int. Metalcast. 3, 39-52 (2009). https://doi.org/10.1007/BF03355440
- [46] P. Fan, S.L. Cockcroft, D.M. Maijer, L. Yao, C. Reilly, A.B. Phillion, Porosity prediction in A356 wheel casting. Metall. Mater. Trans. B. Sci. 50, 2421-2425 (2019)
- [47] M. Uludağ, R. Çetin, L. Gemi et al., Change in porosity of A356 by holding time and its effect on mechanical properties. J. Mater. Eng. Perform. 27, 5141-5151 (2018). https://doi.org/10.1007/s11665-018-3534-0
- [48] S.G. Lee, A.M. Gokhale, G.R. Patel, M. Evans, Effect of process parameters on porosity distributions in high-pressure die-cast AM50 Mg-alloy. Mater. Sci. Eng. A 427(1-2), 99–111 (2006). https://doi.org/10.1016/j.msea.2006.04.082
- [49] K.N. Obiekea, S.Y. Aku, D.S. Yawas, Effects of pressure on the mechanical properties and microstructure of die cast aluminum A380 alloy. J. Miner. Mater. Charact. Eng. 02(03), 248-258 (2014). https://doi.org/10.4236/jmmce.2014.23029
- [50] H.S. Jang, H.J. Kang, J.Y. Park, Y.S. Choi, S. Shin, Effects of casting conditions for reduced pressure test on melt quality of Al-Si alloy. Metals 10(11), 1422 (2020). https://doi.org/10.3390/MET10111422
- [51] M. Di Sabatino, L. Arnberg, Castability of aluminium alloys. Trans. Indian Inst. Met. 62(4), 321–325 (2009)
- [52] B. Dybowski, L. Poloczek, A. Kiełbus, The porosity description in hypoeutectic Al-Si alloys. In Proceedings of the Key Engineering Materials (vol. 682, pp. 83-90). Trans Tech Publications Ltd (2016)
- [53] G.T. Gridli, P.A. Friedman, J.M. Boileau, Manufacturing processes for light alloys.. In Proceedings of the materials, design and manufacturing for light-weight vehicles, pp. 267-320. Woodhead Publishing (2021)
- [54] D. Sui, Z. Cui, R. Wang, S. Hao, Q. Han, Effect of cooling process on porosity in the aluminum alloy automotive wheel during low-pressure die casting. Int. J. Met. 10(1), 32–42 (2016). https://doi.org/10.1007/s40962-015-0008-0
- [55] D. Blondheim, A. Monroe, Macro porosity formation: a study in high pressure die casting. Int. J. Metalcast. 16(1), 330-341 (2022). https://doi.org/10.1007/s40962-021-00602-x
- [56] T. Prucha, From the editor—signals within signals. Int. J. Met. 9(2), 4 (2015)
- [57] D. Krstajic, L.J. Buturovic, D.E. Leahy, S. Thomas, Cross-validation pitfalls when selecting and assessing regression and classification models. J. Cheminform. 6(1), 10 (2014). https://doi.org/10.1186/1758-2946-6-10
- [58] J. Bergstra, D. Yamins, D.D. Cox, Making a science of model search: hyperparameter optimization in hundreds of dimensions for vision architectures. To appear in Proc. of the 30th International Conference on Machine Learning (ICML 2013)
- [59] G. Lemaître, F. Nogueira, C.K. Aridas, Imbalanced-learn: a python toolbox to tackle the curse of imbalanced datasets in machine learning. J. Mach. Learn. Res. 18(1), 559–563 (2017)
- [60] D.L. Wilson, Asymptotic properties of nearest neighbor rules using edited data. IEEE Trans. Syst. Man Commun. 2(3), 408–421 (1972)
- [61] L.S. Shapley, Notes on the N-person Game—I: characteristic-point solutions of the four-person game. Rand Corporation (1951)
- [62] D. Blondheim Jr., Utilizing machine learning autoencoders to detect anomalies in time-series data. NADCA Die Casting Engineer (2021)
9. Copyright:
- This material is "The Author(s)"'s paper: Based on "INDUSTRY 4.0 FOUNDRY DATA MANAGEMENT AND SUPERVISED MACHINE LEARNING IN LOW-PRESSURE DIE CASTING QUALITY IMPROVEMENT".
- Paper Source: https://doi.org/10.1007/s40962-022-00783-z
This material was summarized based on the above paper, and unauthorized use for commercial purposes is prohibited.
Copyright © 2025 CASTMAN. All rights reserved.