This article introduces the paper ['Magnesium Advances and Applications in North America Automotive Industry'] published by ['Trans Tech Publications'].
1. Overview:
- Title: Magnesium Advances and Applications in North America Automotive Industry
- Author: Naiyi Li
- Publication Year: 2005
- Publishing Journal/Academic Society: Materials Science Forum
- Keywords: Application automotive industry, Computer modeling
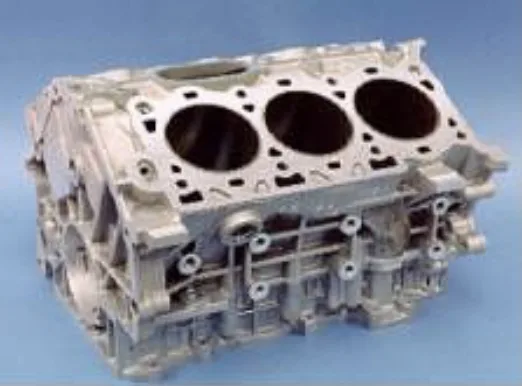
2. Abstracts or Introduction
Abstract:
Magnesium is increasingly recognized as a compelling alternative to traditional materials like steel, aluminum, and polymer composites in the automotive sector. This is primarily driven by the need for vehicle weight reduction to meet stringent vehicle performance requirements, particularly the Corporate Average Fuel Economy (CAFÉ) standards.
The application of magnesium is projected to expand significantly in both structural and powertrain components, especially where material creep resistance is crucial. This paper provides an overview of recent automotive magnesium Research and Development (R&D) programs, including initiatives like Light Metal Cast, Magnesium Powertrain Cast Components, and Structural Cast Magnesium Development.
These programs are supported by the United States Council for Automotive Research (USCAR) and the US Department of Energy. USCAR, an umbrella organization comprising DaimlerChrysler Corporation, Ford Motor Company, and General Motors, was established in 1992 to bolster the US automotive industry's technology base through collaborative, pre-competitive research.
Despite the growth of the magnesium foundry industry over the past decade, the material and manufacturing process costs associated with magnesium die-casting have hindered its widespread adoption in the automotive industry. Consequently, Ford Motor Company initiated the Cost Reduced Magnesium Die Castings Using Heated Runners (CORMAG) program, in partnership with the Advanced Technology Program of the US National Institute of Standards and Technology.
The latter part of this paper briefly outlines the CORMAG program's goals, progress, and impact. Furthermore, the paper showcases specific magnesium applications, such as the 2004 Ford F-150 light truck Front End Support Assembly and the 2005 Ford GT instrument panel structure.
Introduction:
Magnesium has established itself as a structural material in automotive components, demonstrating a proven capacity to reduce automotive weight at an acceptable cost across numerous applications [1,2]. Its increasing attractiveness stems from its ability to simultaneously meet crash-energy absorbing requirements and significantly reduce component weight, positioning it as a viable substitute for steel, aluminum, and polymer composites. The paper highlights three major attributes of magnesium:
a. Lower Density: Magnesium alloys, at a density of 1.8 kg/L, are substantially lighter than competing materials. They are 20 percent lighter than polymer composites, 30 percent lighter than aluminum alloys, and 75 percent lighter than steels and zinc alloys.
b. Outstanding Castability: Magnesium exhibits exceptional castability, enabling the production of components with thin wall thicknesses (1.0 to 1.5 mm) and minimal draft angles (1 to 2 degrees), approximately half of those typical for aluminum. Magnesium's superior fluid flow capability facilitates the creation of large castings that can replace complex assemblies of steel fabrications. Examples include radiator supports for the 2004 Ford F-150 [2], instrument panels for the 2005 Ford GT [3], and steering wheels, where ductility, energy absorption, and impact resistance are critical. For instance, a steel cross-car beam instrument panel (IP) can consist of over 35 parts, whereas a comparable die cast magnesium IP requires only 5.
c. Superior Surface Properties: The surface "skin" of die cast magnesium exhibits enhanced mechanical properties compared to the bulk material [4]. This characteristic allows for thinner, ribbed, and lighter die-castings, reducing material costs while maintaining high strength per unit area, making magnesium competitive with heavier aluminum and plastic components.
Despite these advantages, significant barriers impede the widespread deployment of magnesium in automotive applications. In the North American automotive industry of the twenty-first century, cost control is paramount, often superseding the need for lightweighting. The cost competitiveness of magnesium die-casting remains the primary obstacle, representing a complex and dynamic challenge that the automotive industry is actively striving to address.
This paper is structured in two parts. The first part introduces two ongoing magnesium programs involving Ford Motor Company. The second part focuses on a magnesium research program initiated and implemented by Ford Motor Company, aimed at pioneering industry-first manufacturing technology in the near future.
3. Research Background:
Background of the Research Topic:
The automotive industry is under constant pressure to reduce vehicle weight to meet Corporate Average Fuel Economy (CAFÉ) standards and enhance fuel efficiency. Magnesium alloys offer a significant weight reduction potential compared to steel, aluminum, and polymer composites, making them attractive for automotive applications. However, the high cost of magnesium die-casting has been a major impediment to its widespread adoption.
Status of Existing Research:
Prior research and development efforts, including the Partnership for New Generation of Vehicles (PNGV) in 1993 [5], have highlighted the importance of mass reduction in vehicles. To promote magnesium applications, collaborative programs such as the Structural Cast Magnesium Development (SCMD) and the Magnesium Powertrain Cast Components (MPCC), under the organizational leadership of USCAR and USAMP with support from the US Department of Energy [6,7], were established. These programs involve team members from major automotive companies and aim to evaluate the technical and economic feasibility of magnesium in chassis, interior, and body components. Furthermore, European automakers like BMW and VW have also initiated research and manufacturing programs focusing on magnesium powertrain components [9].
Necessity of the Research:
Despite the inherent advantages of magnesium, its higher manufacturing cost compared to alternative materials limits its broader application in the automotive industry. To overcome this barrier, there is a critical need for research focused on cost reduction in magnesium die-casting processes. Specifically, addressing the challenges associated with die-casting larger, thin-walled structural components is essential for increasing magnesium's competitiveness and enabling its wider implementation in automotive manufacturing.
4. Research Purpose and Research Questions:
Research Purpose:
The primary purpose of the research outlined in this paper is to investigate and develop cost-effective magnesium die-casting technologies for automotive applications. This overarching goal is addressed through the examination of two key programs: the USCAR programs (SCMD and MPCC) and the Ford-initiated CORMAG program. The research aims to demonstrate the feasibility of magnesium in both structural and powertrain components and to overcome the cost barriers associated with its manufacturing.
Key Research:
The key research areas explored in this paper are:
- USCAR Programs (SCMD & MPCC): To determine the technical feasibility and cost-benefit ratio of using magnesium alloys in lightweight chassis, interior, and body components, with a focus on engine cradles and magnesium-intensive engines. The MPCC program specifically aims to develop a magnesium-intensive powertrain with demonstrable cost-effective performance benefits and manufacturability.
- CORMAG Program: To develop and implement innovative hot runner technology in high-pressure magnesium die-casting to reduce manufacturing costs, improve casting yield, and enhance component quality. This program focuses on overcoming the limitations of traditional cold runner systems, particularly for large, thin-walled castings.
Research Hypotheses:
While not explicitly stated as hypotheses, the research operates under the implied assumptions that:
- Magnesium die-casting costs can be significantly reduced through innovative process technologies like hot runner systems (CORMAG).
- Optimized design-for-manufacturing rules and advanced CAE modeling can improve casting yield and reduce scrap in magnesium die-casting.
- Magnesium components, particularly in powertrain and structural applications, can offer cost-effective performance benefits that justify their implementation in automotive vehicles.
5. Research Methodology
Research Design:
The research employs a program-based approach, focusing on collaborative R&D initiatives. It involves both application-driven programs (USCAR's SCMD and MPCC) and technology-focused programs (Ford's CORMAG). The USCAR programs are designed to assess the feasibility of magnesium in specific automotive component categories, while the CORMAG program is designed to develop and validate a specific manufacturing technology.
Data Collection Method:
The paper primarily presents an overview of program objectives, approaches, and expected outcomes. It references specific examples of magnesium applications (Ford F-150 front end support, Ford GT instrument panel) and program activities (CORMAG casting trials). Data collection methods within the referenced programs likely involve material testing, component performance evaluation, cost analysis, and process optimization studies. The CORMAG program specifically utilizes casting trials and computer modeling to validate the hot runner technology.
Analysis Method:
The analysis methods described are primarily focused on:
- Program Overviews: Describing the goals, participants, and technical approaches of the USCAR and CORMAG programs.
- Technology Description: Explaining the principles and innovations of the CORMAG hot runner system.
- Case Studies: Presenting examples of magnesium applications and casting trials to illustrate the potential of magnesium and the CORMAG technology.
- Computer Modeling: Utilizing CAE software (EKK) for simulation of metal flow, heat transfer, and solidification in magnesium die-casting, particularly in the context of hot runner system design and optimization.
Research Subjects and Scope:
The research subjects are primarily focused on magnesium die-casting technology and its application in the North American automotive industry. The scope includes:
- Magnesium Alloys: Specifically mentioning AM60B alloy used in CORMAG casting trials.
- Automotive Components: Focusing on structural components (front end support, engine cradle, chassis structures) and powertrain components (engine block, bedplate, oil pan, front cover, instrument panel).
- Die-Casting Processes: Comparing traditional hot chamber die-casting with CORMAG hot runner die-casting, and mentioning High Pressure Die Casting (HPDC) and Low Pressure Permanent Mold (LPPM) methods.
- Computer Modeling Software: Utilizing EKK software for process simulation.
6. Main Research Results:
Key Research Results:
The paper presents the following key research results and program outcomes:
- USCAR Programs (SCMD & MPCC): These programs are ongoing and aimed at demonstrating the technical and economic viability of magnesium in automotive structures and powertrains. They have identified specific components (engine cradle, magnesium-intensive engine) for development and evaluation. The MPCC program selected the Ford 2.0L V6 DURATEC engine as a basis for redesign with magnesium components (Figure 1). The SCMD program focuses on developing front structural cradles (Figure 2).
- CORMAG Program: This program has successfully retrofitted a 300-ton IdraPrince hot chamber machine with CORMAG hot runner technology. Initial casting trials using a "mule tool" (thin-walled computer case) have been successful. Figure 6 shows a comparison of computer cases cast with traditional hot chamber and CORMAG hot runner processes, demonstrating reduced sprue material in the CORMAG process. Computer modeling using EKK software is being used to optimize hot runner system design and process parameters (Figure 7). The program is developing rapid acting valve technology for hot runner systems and software-based modeling tools for runner/ingate system design.
Analysis of presented data:
The presented data primarily consists of program descriptions, objectives, and visual representations of components and casting processes. Figures 1 and 2 illustrate target components for the USCAR programs. Figures 3, 4, and 5 depict the hot chamber die-casting process and tooling used in the CORMAG program. Figure 6 visually compares castings produced with traditional and CORMAG processes, highlighting the reduction in sprue material. Figure 7 shows simulation results from EKK software, demonstrating its application in analyzing temperature and cooling rate in the casting process. The analysis suggests that the CORMAG program is making progress in developing and validating hot runner technology for magnesium die-casting, with potential for cost reduction and improved material utilization.
Figure Name List:
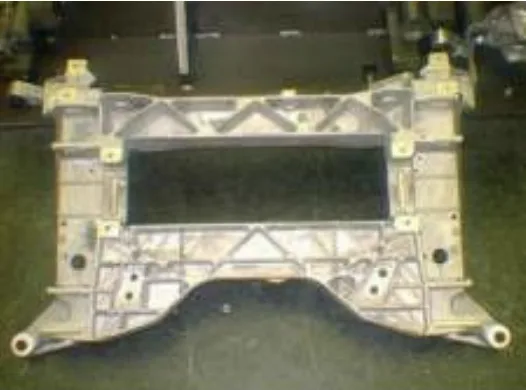
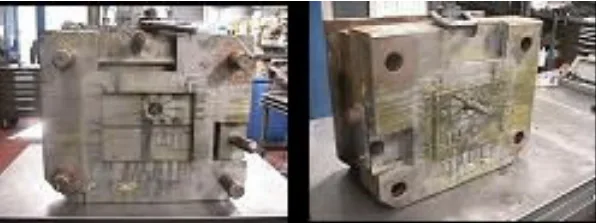
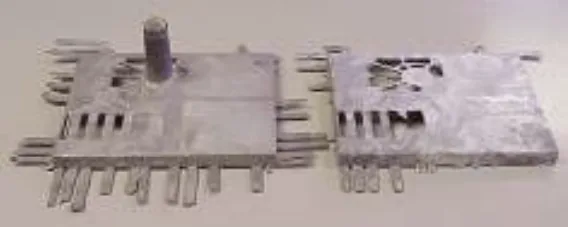
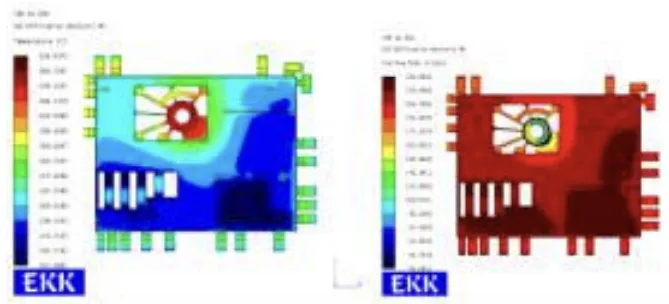
- Figure 1. DURATEC V6 engine block and bedplate (MPCC)
- Figure 2. Magnesium front engine cradle casting (SCMD)
- Figure 3. The hot chamber process schematic
- Figure 4. A set of cover and ejector dies for conventional hot chamber casting
- Figure 5. A set of cover and ejector dies for the CORMAG process
- Figure 6. Computer cases of AM60B made by hot chamber process (left) and the CORMAG hot runner process, respectively.
- Figure 7. Simulated temperature (left) and cooling rate (right) of the computer case at ejection
7. Conclusion:
Summary of Key Findings:
The paper concludes that while the magnesium foundry industry has grown, the high cost of magnesium die-casting remains a barrier to large-scale implementation in the automotive industry. The USCAR programs (SCMD and MPCC) and the CORMAG program are key initiatives aimed at addressing this challenge. The USCAR programs focus on demonstrating the feasibility of magnesium in structural and powertrain components, while the CORMAG program is developing innovative hot runner technology to reduce die-casting costs and improve efficiency. The CORMAG program has shown promising initial results in casting trials and computer modeling, indicating the potential of hot runner technology to advance magnesium die-casting.
Academic Significance of the Study:
This paper provides a valuable overview of ongoing research and development efforts in magnesium die-casting for the automotive industry. It highlights the importance of collaborative programs like USCAR and industry-led initiatives like CORMAG in driving innovation and overcoming technological and economic barriers. The paper contributes to the academic understanding of the challenges and opportunities associated with magnesium application in mass production automotive manufacturing.
Practical Implications:
The research described has significant practical implications for the automotive and die-casting industries. Successful development and implementation of cost-effective magnesium die-casting technologies, such as the CORMAG hot runner system, can enable wider adoption of lightweight magnesium components in vehicles. This can lead to improved fuel efficiency, reduced emissions, and enhanced vehicle performance, contributing to meeting CAFÉ standards and sustainability goals.
Limitations of the Study and Areas for Future Research:
This paper is an overview and does not present detailed experimental data or in-depth analysis of the research programs. The CORMAG program is still in development, and further research is needed to fully validate the hot runner technology and assess its performance in producing complex automotive components. Future research should focus on:
- Detailed performance evaluation of magnesium components produced with CORMAG technology.
- Cost-benefit analysis of CORMAG technology compared to traditional die-casting methods.
- Optimization of hot runner system design and process parameters for various magnesium alloys and component geometries.
- Addressing other barriers to magnesium adoption, such as corrosion resistance and joining technologies.
8. References:
- [1] D. Albright, "Global Automotive Applications Review," the 13th Automotive Magnesium Seminar, International Magnesium Association, 2002.
- [2] J. Balzer et al., 'Structural Magnesium Front End Support Assembly', SAE paper 2003-01-0186.
- [3] T. Hubbert, X. Chen, N. Li, and S. Pineo, "2005 Ford GT Magnesium I/P Structure," SAE paper 2004-01-1261.
- [4] W. Sequeira and G. Dunlop, "Microstructure, Mechanical Properties and Fractography of High Pressure Diecast Magnesium Alloy AZ91D," p213-221, NADCA Congress 2003.
- [5] R. J. Osborne et al., "Design and Product Optimization for Cast Light Metals USAMP-LMD Project", AFS publication, ISBN 0-87433-246-X, 2001.
- [6] R .J. Osborne et al., "USCAR Project on Magnesium Structural Castings," Proc. 57th Annual World Magnesium Conference, International Magnesium Association, p1-5, 2000.
- [7] B. R. Powell, "The USAMP Magnesium Powertrain Cast Components Project," p141-150, NADCA Congress 2003.
- [8] R. S. Beals et al., "The USAMP Magnesium Powertrain Cast Components Project: Part III," Magnesium Technology, p11-17, TMS 2004.
- [9] J. Bohme et al, "AUDI Hybrid Magnesium Technology – A new approach to the lightweight engine block," Proc. 61st Annual World Magnesium Conference, International Magnesium Association, 2004.
- [10]R. J. Osborne et al., "Large, Complex Magnesium Chassis Structure Development", SAE 2004.
- [11]N. Li et al., "The Cost Reduced Magnesium Die Castings Using Heated Runners (CORMAG) Program and Computer Simulations," p395-403, NADCA Congress 2003.
9. Copyright:
- This material is "Naiyi Li"'s paper: Based on "Magnesium Advances and Applications in North America Automotive Industry".
- Paper Source: doi:10.4028/www.scientific.net/MSF.488-489.931
This material was summarized based on the above paper, and unauthorized use for commercial purposes is prohibited.
Copyright © 2025 CASTMAN. All rights reserved.