This article introduces the paper ['Simulation-enabled casting product defect prediction in die casting process'] presented at the ['International Journal of Production Research']
1. Overview:
- Title: Simulation-enabled casting product defect prediction in die casting process
- Author: M.W. Fu & M.S. Yong
- Publication Year: 2009
- Publishing Journal/Academic Society: International Journal of Production Research
- Keywords: CAE simulation; high pressure die casting; product quality assurance; defect prediction
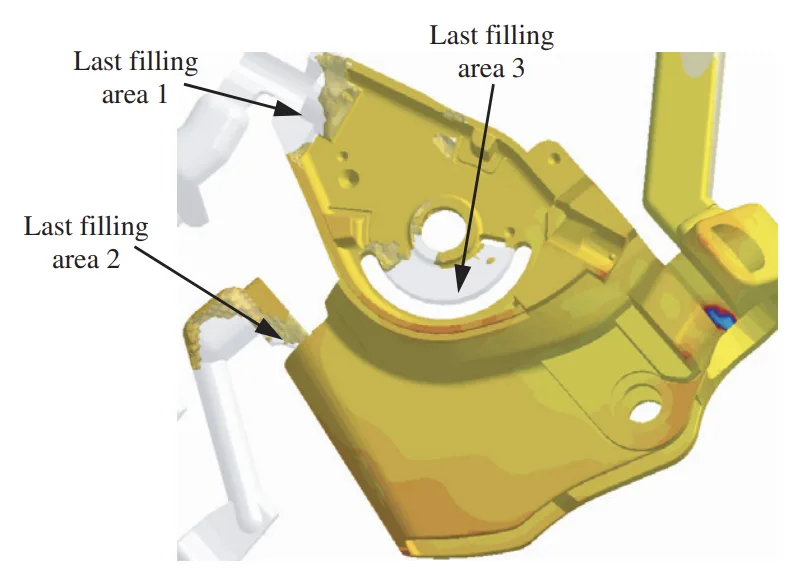
2. Research Background:
Background of the Research Topic:
In contemporary casting industries, a paradigm shift is observed from traditional trial-and-error workshop practices to Computer-Aided Engineering (CAE)-enabled simulation and 'proof-of-concept' methodologies. This transition signifies a move from heuristic know-how and experiential learning towards a more scientific approach grounded in simulation, evaluation, analysis, and calculation. This evolution is driven by the increasing demands for reduced design and manufacturing lead-times, enhanced dimensional accuracy, superior product quality, and agile adaptation to product design changes within the casting sector. High Pressure Die Casting (HPDC) processes, renowned for their near-net shape capabilities, high productivity, and suitability for complex geometries, are particularly relevant in this context. However, the traditional product development paradigm, heavily reliant on know-how and experience, often proves to be time-consuming, error-prone, and necessitates extensive experimental validation in the workshop.
Status of Existing Research:
Conventional Computer-Aided Design (CAD) and Computer-Aided Manufacturing (CAM) technologies serve as essential tools for representing design intent and facilitating physical realization. They contribute significantly to enhancing design quality and shortening lead-times. Nevertheless, CAD/CAM technologies alone are insufficient to address critical aspects of casting process design, tooling structure, product properties configuration, and comprehensive quality control and assurance. Prior research efforts in casting simulation have been largely monolithic, lacking a systematic and comprehensive approach to simulation-enabled product defect prediction. These studies have not fully articulated the capabilities of CAE simulation in defect prediction and avoidance, the specific information derivable from CAE, the types of defects occurring during filling and solidification, and the strategies for defect mitigation based on simulation insights.
Necessity of the Research:
To overcome the limitations of traditional methodologies and fragmented research, there is a pressing need for an efficient product development paradigm underpinned by CAE simulation technology. This is crucial for addressing the bottleneck in casting production industries caused by the increasing demands for process configuration and product quality. CAE simulation technology emerges as a technologically efficient and cost-effective solution for analysis, prediction, and evaluation of casting product quality and defects, thereby reducing reliance on physical trial-and-error and accelerating product development cycles.
3. Research Purpose and Research Questions:
Research Purpose:
The primary purpose of this research is to present CAE technology as a pivotal tool for casting process simulation and product defect prediction in die casting. The study aims to articulate the modelling of the casting process, detail critical simulation issues, and demonstrate how CAE simulation reveals information pertaining to filling, solidification, and after-ejection behaviour. Through industrial case studies, the paper intends to illustrate the efficacy of CAE simulation in identifying and predicting process-related defects and to validate its overall efficiency in enhancing product quality assurance.
Key Research:
This research focuses on several key aspects:
- Modelling the casting process using numerical methods and establishing the association between the real process, modelling, simulation, and output variables.
- Articulating the information flow within the simulation process and the solution generation cycle.
- Proposing a process-based simulation paradigm for the prediction of casting defects.
- Categorizing the information revealed by simulation and the defect categories predictable from this information.
- Analyzing, through case studies, the simulation process, procedure, and the mechanisms of defect occurrence in the casting process based on identified simulation parameters.
Research Hypotheses:
The central hypothesis is that CAE simulation technology provides a robust and effective methodology for predicting casting product defects in the die casting process. It is posited that by accurately modelling the casting process and analyzing simulation outputs, process-related defects can be identified, understood, and ultimately avoided, leading to improved product quality and reduced manufacturing costs. The research further hypothesizes that a systematic, process-based simulation paradigm can be developed and validated to facilitate defect prediction and process optimization in die casting.
4. Research Methodology
Research Design:
The research employs a process-based simulation framework for casting defect prediction. This framework is structured around the integration of product design specifications with CAE simulation to analyze and optimize the casting process. The design involves modelling the entire casting system, encompassing casting geometry, process route, and parameter determination, within a CAE environment. The methodology is validated through industrial case studies, focusing on High Pressure Die Casting (HPDC) processes.
Data Collection Method:
Data for this research are primarily derived from CAE simulations conducted using Magmasoft, a commercial casting simulation software. The input data for simulations include CAD STL models of casting geometries, material properties for both cast alloys (AlSi9Cu3) and die materials (X38CrMoV5), and process parameters relevant to HPDC. Industrial case studies provide the practical context and validation for the simulation results. Simulation outputs, such as melt flow patterns, temperature distributions, solidification sequences, and stress-strain analyses, constitute the primary data collected for defect prediction.
Analysis Method:
The analysis method is centered on the interpretation of CAE simulation results to predict and understand casting defects. Numerical methods, including Finite Element Method (FEM) and Finite Difference Method (FDM), are utilized within the CAE software to quantitatively represent the physical behavior of the casting system. The analysis involves:
- Examining melt-front advancement (MFA) to identify potential air entrapment and filling imbalances.
- Analyzing temperature distributions during solidification to predict shrinkage porosity and hot spots.
- Evaluating stress and strain distributions post-ejection to assess distortion and residual stress.
- Comparing simulation-predicted defects with observed defects in industrial case studies to validate the simulation methodology.
Research Subjects and Scope:
The research subjects are industrial High Pressure Die Casting (HPDC) processes, specifically focusing on four-cavity die casting configurations. Two industrial cases are presented in detail. The scope of the research is limited to process-related defects in HPDC, including defects arising from filling, solidification, and thermal stress. The materials under investigation are AlSi9Cu3 as the cast material and X38CrMoV5 as the die material, representative of common materials in die casting applications. The simulation analysis encompasses mould filling, solidification and cooling, and stress and strain distribution of casting after ejection.
5. Main Research Results:
Key Research Results:
The research demonstrates that CAE simulation effectively reveals critical information about the die casting process, enabling the prediction of product defects. Key results include:
- Filling Process Simulation: CAE simulation accurately depicts melt-front positions, turbulence, and filling smoothness. It identifies potential air entrapment areas and assesses venting requirements. Simulation also reveals thermal behavior, temperature distribution, filling sequences, and melt velocity distribution, which are crucial for predicting die erosion and surface finish quality. Undesirable filling behaviors like split melt streams and misruns are also identifiable.
- Solidification Process Simulation: Simulation elucidates the solidification sequence, temperature distribution in the casting and die, and identifies the last solidification areas and potential hotspots. It aids in evaluating cooling system design, runner system design, and predicting shrinkage and porosity distribution. CAE simulation also assists in determining feeder size and location for porosity-free castings.
- Stress Analysis in Casting: CAE simulation predicts temperature distribution and distortion post-ejection, residual stress distribution, and potential product defects related to stress. It supports the optimization of casting system design and die stress analysis for improved die life and casting accuracy.
Data Interpretation:
The simulation results are interpreted to correlate specific simulation outputs with potential casting defects. For instance, imbalanced MFA patterns are linked to defects arising from uneven filling and air entrapment. Hotspots identified in solidification simulations are indicative of potential shrinkage porosity and orange skin defects. High stress concentrations predicted in stress analysis suggest areas prone to distortion or fatigue failure. The case studies validate these interpretations by showing a strong correlation between simulation-predicted defects and actual defects observed in industrial castings. For example, in Case I, MFA analysis predicted air entrapment in boss features, which was confirmed by the casting analysis. In Case II, simulation predicted irrational flow and temperature distribution leading to orange skin and fracture defects, which were also observed in the real part.
Figure Name List:
- Figure 1. Modelling of the casting process from physical and mathematical perspectives: action-behaviour-property relationship.
- Figure 2. Association among the process, modelling, simulation and output variables.
- Figure 3. The process-based simulation paradigm for prediction of casting defects.
- Figure 4. The layout of the casting filling system in Case I.
- Figure 5. The MFA positions in the filling process. (a) Filling at 85% of the whole process; (b) filling at 90% of the whole process.
- Figure 6. The layout of the casting filling system in Case II.
- Figure 7. The melt-front advancement position in filling process.
- Figure 8. Unreasonable filling pattern and the defect caused. (a) Simulation predicted irrational flow; (b) the real defect revealed by experiment.
- Figure 9. Defect caused by the unreasonable temperature distribution in the solidification process. (a) Simulation result; (b) real part.
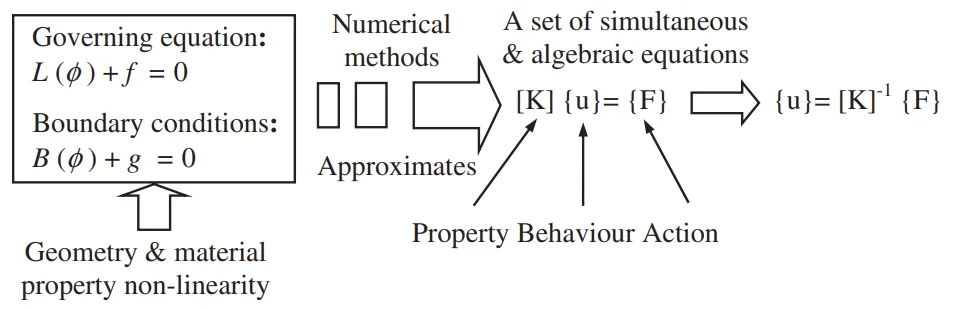
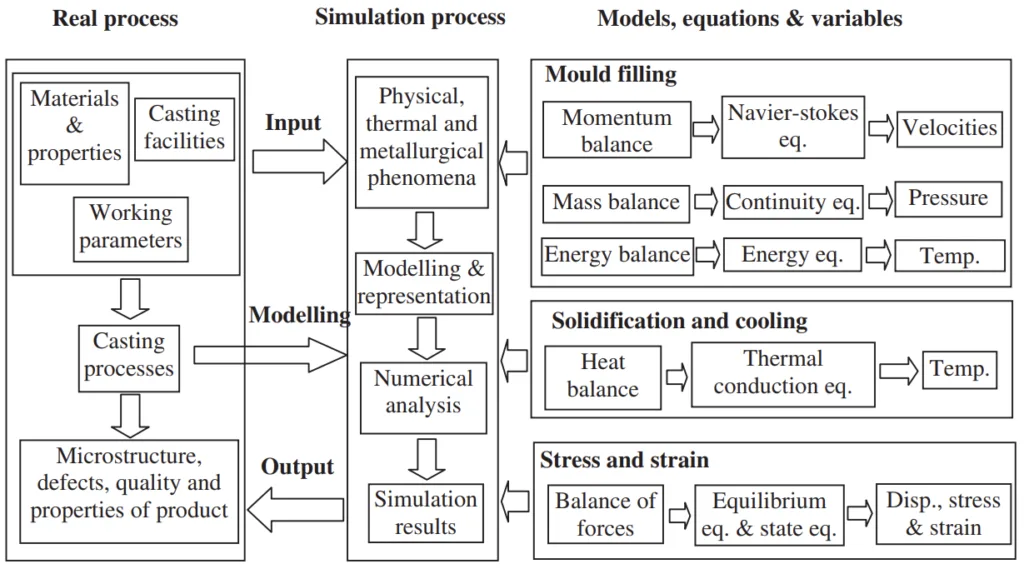
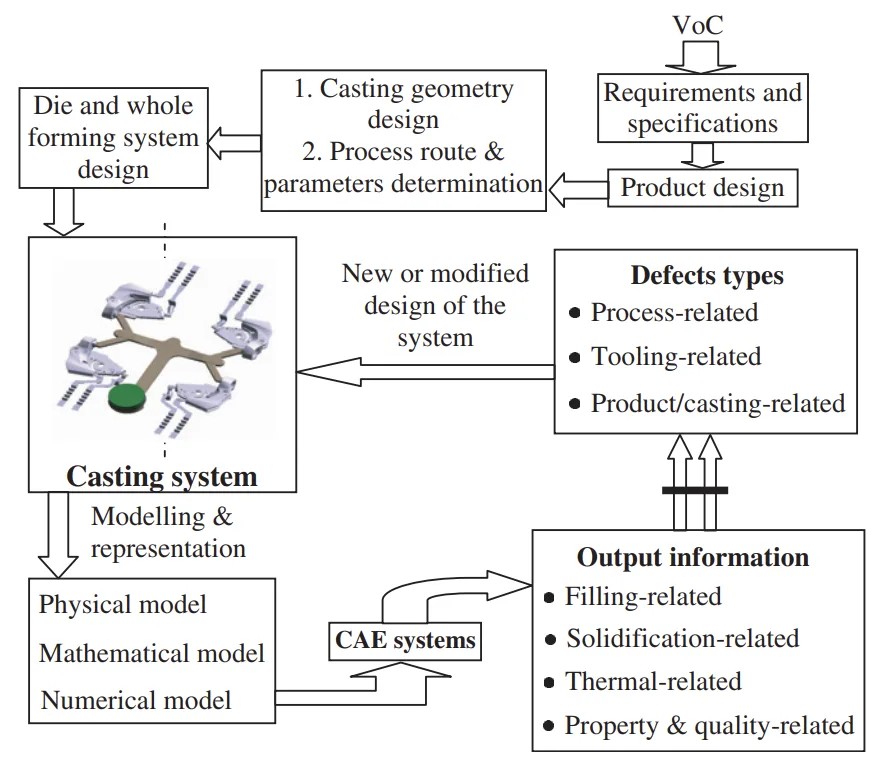
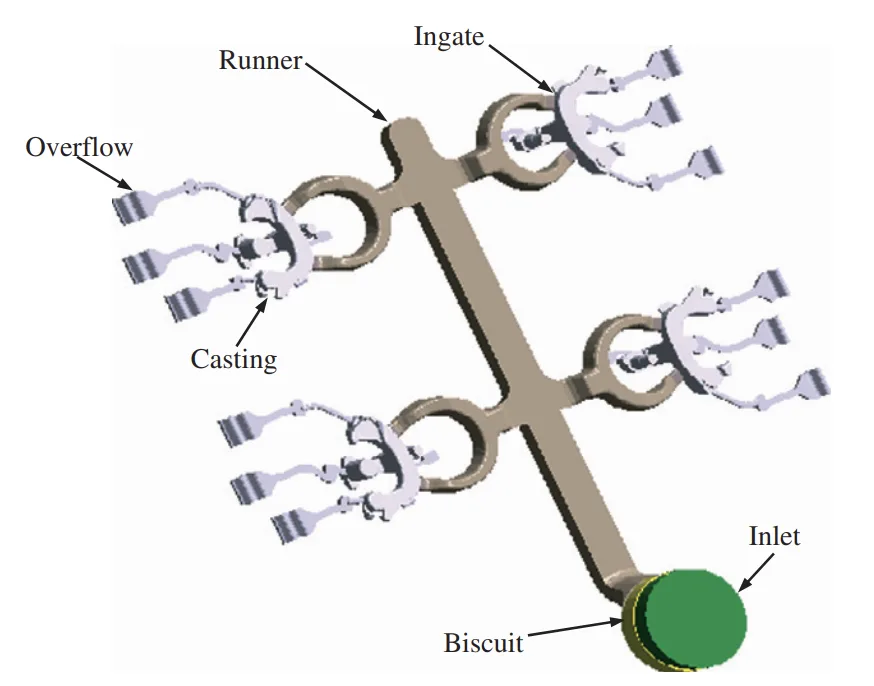
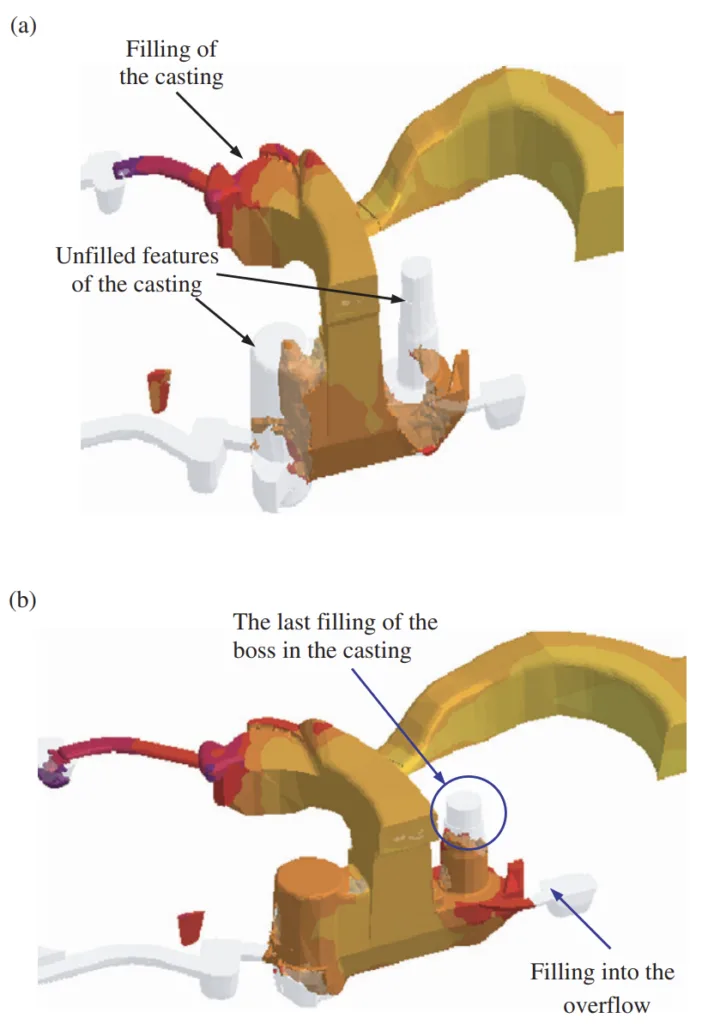
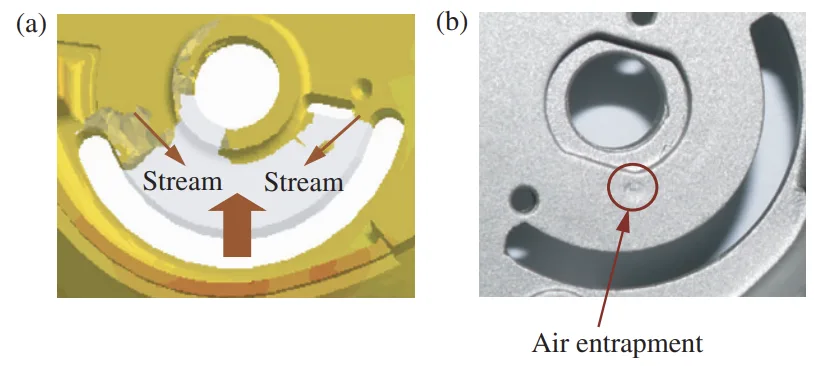
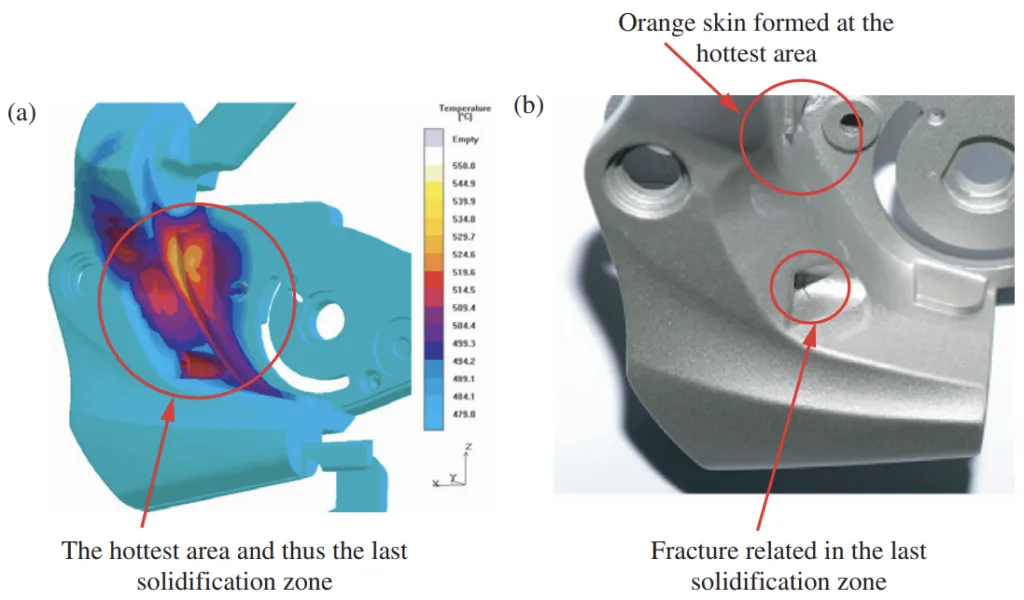
6. Conclusion:
Summary of Main Results:
This research conclusively demonstrates the effectiveness of simulation-enabled casting product defect prediction in the die casting process. By employing CAE simulation, the complexities of casting processes, including filling, solidification, and post-ejection behavior, can be virtually realized and analyzed. The study articulates a comprehensive framework, procedure, and process for simulation-enabled defect prediction, validated through industrial case studies. The findings confirm that CAE simulation is a powerful tool for identifying and predicting process-related defects, thereby reducing the reliance on traditional trial-and-error methods in casting product development.
Academic Significance of the Research:
The academic significance of this research lies in its systematic approach to integrating CAE simulation into the die casting product development paradigm. It provides a structured methodology for defect prediction that moves beyond monolithic approaches and offers a holistic view of the casting process. The research contributes to the theoretical understanding of how CAE simulation can be effectively utilized to reveal critical process parameters and their relationship to defect formation in die casting. By categorizing simulation outputs and correlating them with specific defect types, the study enhances the scientific basis for casting process optimization and quality assurance.
Practical Implications:
The practical implications of this research are substantial for the die casting industry. The application of CAE simulation technology, as presented in this study, offers a pathway to:
- Reduce Trial-and-Error: By virtually simulating the casting process, manufacturers can minimize costly and time-consuming physical experiments in the workshop.
- Cut Product Development Costs: Early detection and mitigation of potential defects through simulation can significantly reduce downstream rework, scrap rates, and overall production costs.
- Shorten Time-to-Market: Streamlined product development cycles, facilitated by CAE-driven design optimization, enable faster delivery of casting products to the market.
- Improve Casting Quality: Enhanced understanding of defect mechanisms and process parameters through simulation leads to improved product quality, dimensional accuracy, and functional performance.
- Optimize Casting Design and Process: CAE simulation provides actionable insights for optimizing casting geometry, tooling design, process parameters, and cooling strategies, resulting in more efficient and robust casting processes.
Limitations of the Research
While the research effectively demonstrates the capabilities of CAE simulation, it is important to note potential limitations. The case studies are primarily focused on four-cavity HPDC processes and specific materials (AlSi9Cu3 and X38CrMoV5). The generalizability of the findings to other casting processes (e.g., gravity die casting, low pressure die casting) and a broader range of materials may require further investigation. Additionally, the accuracy of simulation results is contingent on the fidelity of input data, including material properties and process parameters. Despite these limitations, the research provides a strong foundation for the broader application of CAE simulation in die casting defect prediction.
7. Future Follow-up Research:
- Directions for Follow-up Research
Future research should focus on expanding the application of the presented CAE simulation framework to a wider spectrum of casting processes beyond HPDC, including gravity die casting and low-pressure die casting. Investigating the effectiveness of this methodology across diverse casting materials, including ferrous and non-ferrous alloys, is also crucial. Further research could explore the integration of real-time process monitoring and control systems with CAE simulation to enable adaptive process optimization during production. - Areas Requiring Further Exploration
Areas requiring further exploration include the development of more sophisticated and predictive defect models within CAE software, particularly for complex defect types such as hot tearing and fatigue-related failures. Enhancing the computational efficiency of simulations to enable faster turnaround times and integration into rapid product development cycles is also essential. Investigating the use of advanced simulation techniques, such as multi-physics simulations and machine learning algorithms, to improve defect prediction accuracy and process optimization capabilities represents a promising avenue for future research.
8. References:
- Barriere, T., Liu, B., and Gelin, J.C., 2003. Determination of the optimal process parameters in metal injection molding from experiments and numerical modeling. Journal of Materials Processing Technology, 143–144 (December), 636-644.
- Bird, R.B., Stewart, W.E., and Lightfoot, E.N., 1960. Transport Phenomena. New York: J. Wiley & Sons.
- Cleary, P., et al., 2002. Flow modeling in casting processes. Applied Mathematical Modeling, 26, 171-190.
- Dai, X., et al., 2003. Effects of runner system design on the mechanical strength of Al-7Si-Mg alloy castings. Materials Science and Engineering: A, 354 (1), 315–325.
- Fuh, J.Y.H., et al., 2004. Computer-aided Injection Mould Design and Manufacture. New York: Marcel Dekker.
- Guo, Z., et al., 2005. Modelling of materials properties and behavior critical to casting simulation. Materials Science and Engineering: A, 413-414, 465-469.
- Hsu, Y.L. and Yu, C.C., 2006. Computer simulation of casting process of aluminum wheels a case study. Proceedings of the I MECH E Part B Journal of Engineering Manufacture, 220 (2), 203-211.
- Hu, B.H., et al., 2000. Design and optimization of runner and gating systems for the die casting of thin-walled magnesium telecommunication parts through numerical simulation. Journal of Materials Processing Technology, 105 (1), 128-133.
- Krimpenis, A., et al., 2006. Simulation-based selection of optimum pressure die-casting process parameters using neural nets and genetic algorithms. International Journal of Advanced Manufanuring Technology, 27 (5–6), 509–517.
- Lewis, R.W. and Ravindran, K., 2000. Finite element simulation of metal casting. International Journal for Numerical Methods in Engineering, 47 (1–3), 29–59.
- Louvo, A., 1997. Casting simulation as a tool in concurrent engineering. In: International ADI and simulation conference, 28–30 May, Espoo, Finland.
- McMillin, T., Hartmann, G., and Egner-Walter, A., 2002. CAE opens new frontier in casting design. Engineered Casting Solutions, Spring 2002, 29–31.
- Midea, A., et al., 2000. Using computer modeling to optimize casting processes. Modern Casting, 90, May 2000, 4-10.
- Mirbagheri, S.M.H., et al., 2002. Simulation of melt flow in coated mould cavity in the casting process. Journal of Materials Processing Technology, 142 (2), 493–507.
- Mochnacki, B., Lara, S., and Pawlak, E., 2005. Multiscale model of segregation process. Journal of Materials Processing Technology, 162–163, May 2005, 766–769.
- Monroe, C. and Beckermann, C., 2005. Development of a hot tear indicator for steel castings. Materials Science and Engineering: A, 413-414, 30-36.
- Naher, S., Brabazon, D., and Looney, L., 2003. Simulation of the stir casting process. Journal of Materials Processing Technology, 143-144, 567–571.
- Neumann, L., et al., 2005. Prediction of texture induced anisotropy by through-process modelling. Materials Science Forum, 495–497, 1657–1662.
- Peng, Y.H., et al., 2005. Numerical study on the low pressure die casting of AZ91D wheel hub. Materials Science Forum, 488-489, 393-396.
- Sequeira, W., et al., 2001. Optimization of die casting part design, process parameters and process control using newly die casting simulation tool. In: proceedings of die casting in the 21th century, Cincinnati, Ohio.
- Sturm, J.C., et al., 2001. Optimized development for castings and casting processes. In: 19th CAD-FEM users' meeting 2001, international congress on FEM technology, 17–19 October, Postdam, Germany.
- Ulysse, P., 1999. Optimal extrusion die design to achieve flow balance. International Journal of Machine Tools and Manufacture, 39 (7), 1047–1064.
- Venkatesan, A., Gopinath, V.M., and Rajadurai, A., 2005. Simulation of casting solidification and its grain structure prediction using FEM. Journal of Materials Processing Technology, 168 (1), 10-15.
- Zhang, X.P., Xiong, S.M., and Xu, Q.Y., 2006. Numerical methods to improve the computational efficiency of solidification simulation for the investment casting process. Journal of Materials Processing Technology, 173 (1), 70–74.
9. Copyright:
- This material is "M.W. Fu & M.S. Yong"'s paper: Based on "Simulation-enabled casting product defect prediction in die casting process".
- Paper Source: http://dx.doi.org/10.1080/00207540801935616
This material was summarized based on the above paper, and unauthorized use for commercial purposes is prohibited.
Copyright © 2025 CASTMAN. All rights reserved.