This article introduces the paper ['Thermal Conductivity of AlSi10MnMg Alloy in Relation to Casting Technology and Heat Treatment Method'] presented at the ['MDPI Materials']
1. Overview:
- Title: Thermal Conductivity of AlSi10MnMg Alloy in Relation to Casting Technology and Heat Treatment Method
- Author: Iva Nováková, Milan Jelínek and Martin Švec
- Publication Year: 2024
- Publishing Journal/Academic Society: Materials, MDPI
- Keywords: aluminium alloy; thermal diffusivity; thermal conductivity; casting; heat treatment
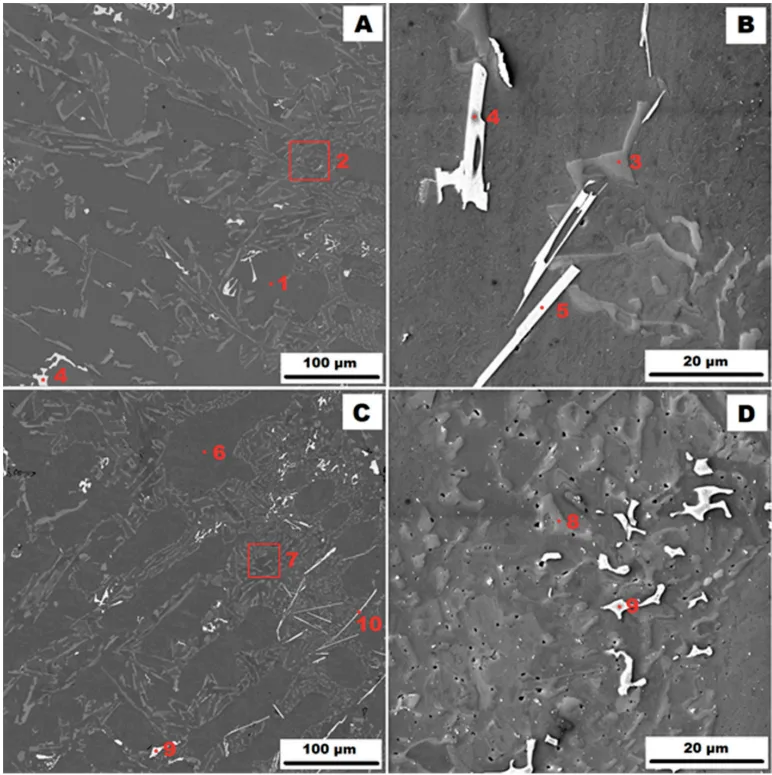
2. Research Background:
Background of the Research Topic:
In contemporary industrial applications, particularly with the burgeoning field of electromobility, there is an escalating demand for cast components that exhibit not only superior mechanical properties but also enhanced thermal conductivity. This research addresses this imperative by focusing on the AlSi10MnMg alloy, a material of interest for components like motor housings and heat sinks, where both mechanical robustness and efficient heat dissipation are critical.
Status of Existing Research:
Prior investigations have established that the thermal conductivity of aluminium alloys is influenced by a multitude of factors, including temperature, chemical composition, and microstructure. Specifically, studies [5,6] have highlighted temperature as a critical parameter, while others [7-9] suggest an inverse relationship between the strength and thermal conductivity of as-cast Al-Si alloys. Casting technology [5,21,22] and heat treatment [25-28] are also recognized to play significant roles in determining the final thermal properties of aluminium castings.
Necessity of the Research:
Current industrial standards necessitate precise thermal conductivity values for cast components, often stipulated by production regulations. This study is motivated by the industrial need for specific thermal diffusivity and thermal conductivity data for the AlSi10MnMg alloy under varying casting conditions and heat treatment regimes. The aim is to provide valuable data that can assist industries in mitigating issues related to insufficient or excessive thermal conductivity in their products.
3. Research Purpose and Research Questions:
Research Purpose:
The primary objective of this research is to evaluate the impact of different casting technologies—high-pressure die casting (HPDC), gravity sand casting (GSC), and gravity die casting (GDC)—and subsequent T5 heat treatments (artificial ageing at HT200, HT300, and HT400) on the thermal diffusivity and thermal conductivity of the AlSi10MnMg alloy.
Key Research:
This study is centered on elucidating the effects of:
- Casting method on the thermal conductivity of AlSi10MnMg alloy.
- T5 heat treatment temperature on the thermal conductivity of AlSi10MnMg alloy.
Research Hypotheses:
The research operates under the following hypotheses:
- The thermal diffusivity and thermal conductivity of the AlSi10MnMg alloy are dependent on the casting technology employed.
- Slower cooling rates during casting result in higher thermal conductivity values.
- Heat treatment without prior solution treatment (T5) positively influences the thermal conductivity of the AlSi10MnMg alloy.
4. Research Methodology
Research Design:
This study employs an experimental research design to quantitatively assess the thermal properties of AlSi10MnMg alloy samples produced via different casting methods and subjected to varying heat treatments. The thermal diffusivity was measured across a temperature range, and the microstructure was characterized to correlate with the thermal conductivity data.
Data Collection Method:
- Thermal Diffusivity Measurement: A DLF 2 (Discovery laser flash, TA Instruments, New Castle, UK) was utilized to measure the thermal diffusivity of machined specimens (12.68 mm diameter, 4 mm thickness) as a function of temperature (50–300 °C).
- Chemical Composition Analysis: A Q4 TASMAN optical spectrometer (Bruker Elemental GmbH, Berlin, Germany) was used to determine the chemical composition of the AlSi10MnMg alloy.
- Microstructural Characterization: A Tescan Mira 3 electron microscope (Tescan Orsay Holding a.s., Brno, Czech Republic), equipped with an Oxford UltimMax65 energy dispersive detector and an Oxford SYMMETRY detector (Oxford Instruments plc, Oxfordshire, UK), was employed for microstructure analysis, including EDX for phase identification and EBSD for grain size and orientation analysis.
Analysis Method:
- Thermal Conductivity Calculation: Thermal conductivity (λ) was calculated from the measured thermal diffusivity (a), specific heat capacity (Cp), and density (ρ) using the relationship: λ = a ⋅ Cp ⋅ ρ. The specific heat capacity was measured during the thermal diffusivity measurement, and density variation with temperature was calculated based on thermal expansion measurements using a DIL 805L dilatometer (TA Instruments, New Castle, UK).
- Microstructural Analysis: EDX analysis was used to identify the chemical composition of different phases present in the microstructure. EBSD analysis provided data on grain size and crystallographic orientation.
Research Subjects and Scope:
The research focused on the AlSi10MnMg alloy. Samples were prepared using three casting methods: gravity sand casting (GSC), gravity die casting (GDC), and high-pressure die casting (HPDC). Heat treatments included artificial ageing at 200 °C (HT200), 300 °C (HT300), and 400 °C (HT400) for 1 hour, without prior solution treatment (T5 temper). The thermal property measurements were conducted in the temperature range of 50–300 °C.
5. Main Research Results:
Key Research Results:
- Casting Technology Influence: The study revealed that casting technology significantly affects thermal diffusivity and thermal conductivity. Samples produced by GSC exhibited the highest thermal conductivity, followed by GDC and then HPDC. For instance, at 50 °C, the thermal diffusivity of GSC samples was approximately 12% higher than that of HPDC samples.
- Temperature Dependence: Regardless of the casting method, the thermal conductivity of the AlSi10MnMg alloy showed a tendency to increase with temperature in the range of 50–300 °C. A noticeable increase in thermal conductivity was observed in the temperature range of 150–200 °C for all casting methods.
- Heat Treatment Effect: T5 heat treatment (HT200, HT300, HT400) demonstrated a positive effect on thermal conductivity across all casting methods. The thermal conductivity increased with increasing heat treatment temperature. For example, artificial ageing at 400 °C (HT400) increased the thermal diffusivity at 50 °C by approximately 25% compared to the as-cast HPDC samples.
Data Interpretation:
- Microstructure and Casting Method: The variation in thermal conductivity across different casting methods is attributed to differences in microstructure. Slower cooling rates in GSC lead to a coarser eutectic structure and potentially lower solute content in the α(Al) matrix, which enhances thermal conductivity. Conversely, the rapid cooling in HPDC results in a finer microstructure and higher solute content, reducing thermal conductivity.
- Heat Treatment Mechanism: The increase in thermal conductivity after T5 heat treatment is likely due to the precipitation of alloying elements from the supersaturated solid solution, particularly in the temperature range of 150–200 °C. This precipitation reduces the scattering of electrons, thereby improving thermal conductivity. The refinement of the eutectic structure and more uniform distribution of secondary phases after heat treatment also contribute to enhanced thermal properties.
Figure Name List:
- Figure 1. Structure of the AlSi10MnMg alloy cast into a sand mould (GSC): (A)—as-cast condition (HV 10 kV, BSE); (B)-as-cast condition (HV 10 kV, SE); (C)-condition after HT400 (HV 10 kV, BSE); and (D)-condition after HT400 (HV 10 kV, SE).
- Figure 2. Structure of gravity die-cast (GDC) AlSi10MnMg alloy: (A)-as-cast condition (HV 10 kV, BSE); (B)-as-cast condition (HV 10 kV, SE); (C)-condition after HT400 (HV 10 kV, BSE); and (D)-condition after HT400 (HV 10 kV, SE).
- Figure 3. Structure of high-pressure die-casting (HPDC) AlSi10MnMg alloy: (A)-as-cast condition (HV 10 kV, BSE); (B)-as-cast condition (HV 10 kV, SE); (C)-condition after HT400 (HV 10 kV, BSE); and (D)-condition after HT400 (HV 10 kV, SE).
- Figure 4. Four EBSD grain maps of investigated alloys (measured area 750 × 750 µm, step size 2 µm, and HV 10 kV): (A) gravity sand-cast sample (GSC)—as-cast condition; (B) gravity sand-cast sample (GSC)-condition after HT400; (C) gravity die-cast sample (GDC)—as-cast condition; (D) gravity die-cast sample (GDC)—condition after HT400; (E) vacuum high-pressure die casting (HPDC)—as-cast condition; and (F) vacuum high-pressure die-casting (HPDC)—condition after HT400.
- Figure 5. Temperature dependence of average thermal diffusivity of GSC, GDC, and HPDC samples.
- Figure 6. Temperature dependence of the average thermal diffusivity of GSC samples heat-treated at 200 °C (HT200), 300 °C (HT300), and 400 °C (HT400).
- Figure 7. Temperature dependence of the average thermal diffusivity of GDC samples in as-cast condition and heat-treated at 200 °C (HT200), 300 °C (HT300), and 400 °C (HT400).
- Figure 8. Temperature dependence of the average thermal diffusivity of HPDC samples as-cast and heat-treated at 200 °C (HT200), 300 °C (HT300), and 400 °C (HT400).
- Figure 9. Temperature dependence of thermal conductivity of GSC, GDC, and HPDC samples.
- Figure 10. Thermal conductivity of HPDC samples in as-cast condition and heat-treated at 130 °C, 200 °C, 300 °C, and 400 °C.
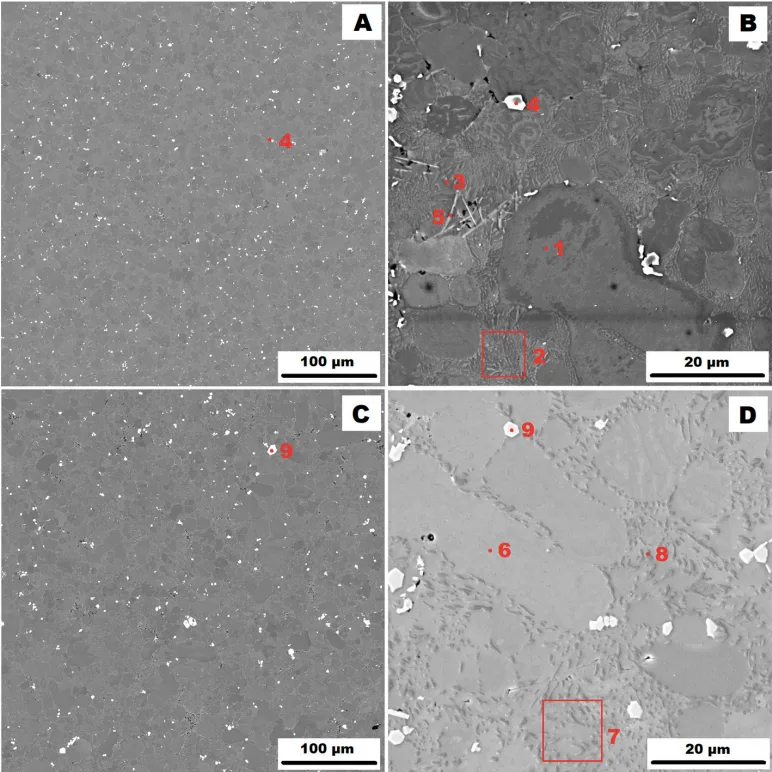
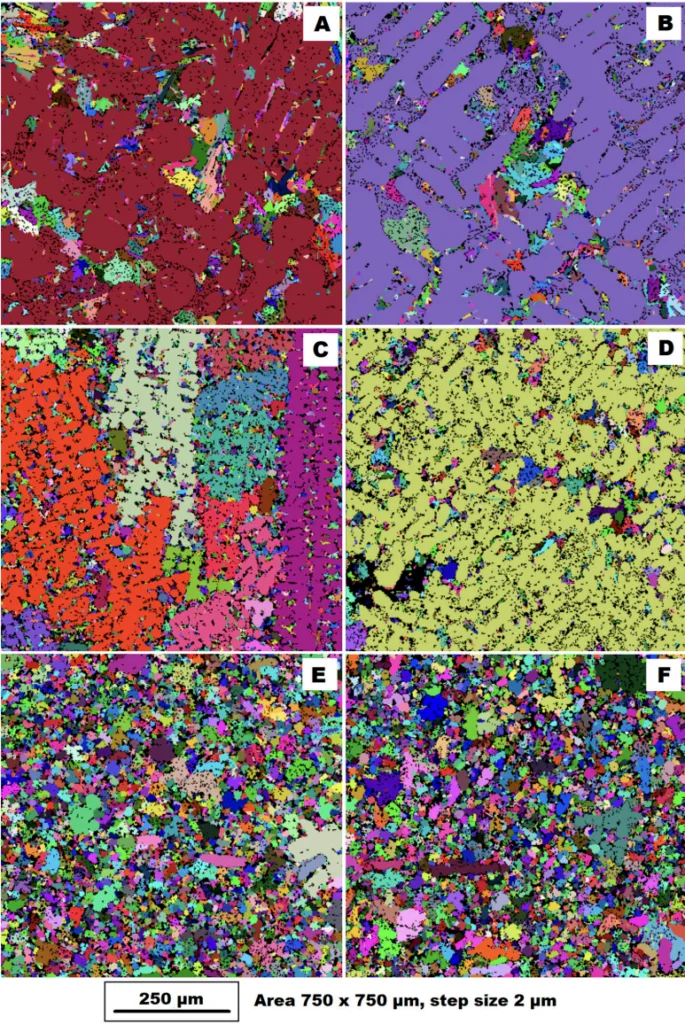
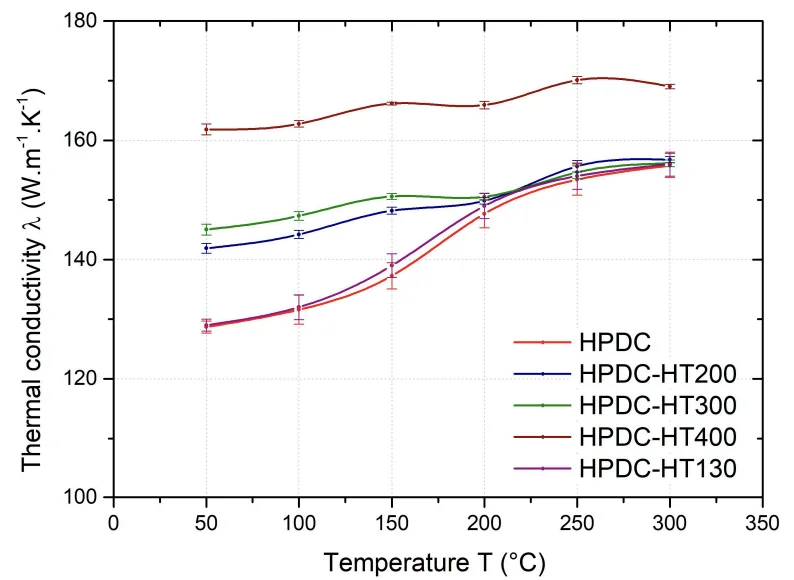
6. Conclusion:
Summary of Main Results:
This study conclusively demonstrates that both casting technology and subsequent T5 heat treatment significantly influence the thermal conductivity of AlSi10MnMg alloy. Slower cooling rate casting methods, such as GSC, yield higher thermal conductivity compared to faster methods like GDC and HPDC. Furthermore, T5 heat treatments (HT200, HT300, HT400) effectively enhance the thermal conductivity of the alloy, irrespective of the casting method. The thermal conductivity of all investigated samples increases with rising temperature in the range of 50–300 °C.
Academic Significance of the Research:
This research contributes valuable insights into the thermal behavior of AlSi10MnMg alloy under different processing conditions. It provides a comprehensive dataset on thermal diffusivity and thermal conductivity, enhancing the fundamental understanding of how casting and heat treatment parameters modulate the thermal properties of this industrially relevant alloy.
Practical Implications:
The findings of this study have direct practical implications for industries utilizing AlSi10MnMg alloy, particularly in automotive and electronics sectors where thermal management is crucial. The data suggests that for applications prioritizing thermal conductivity, GSC may be preferred. Moreover, the application of T5 heat treatment, especially within the industrially relevant range of 160–230 °C for mechanical property enhancement, also beneficially improves thermal conductivity. For components produced by GDC and HPDC where thermal conductivity is paramount and high mechanical strength is not a primary requirement, heat treatments at higher temperatures (300–400 °C) can be employed to further augment thermal conductivity, provided that blistering is not a concern.
Limitations of the Research
The scope of this research is limited to the AlSi10MnMg alloy and specific T5 heat treatment conditions (HT200, HT300, HT400). The generalizability of these findings to other aluminium alloys or different heat treatment regimes requires further investigation.
7. Future Follow-up Research:
- Directions for Follow-up Research: Future research should explore the effects of T6 and T7 heat treatments (solution treatment followed by ageing) on the thermal conductivity of AlSi10MnMg alloy, especially in the context of vacuum die casting. Investigating the influence of other alloying elements and their interactions on thermal conductivity would also be beneficial.
- Areas Requiring Further Exploration: Further studies could focus on optimizing heat treatment parameters to maximize thermal conductivity while simultaneously achieving desired mechanical properties. A more detailed investigation into the quantitative relationship between specific microstructural features (e.g., grain size, secondary phase characteristics) and thermal conductivity would provide deeper insights and enable more precise material design.
8. References:
- [1] Biswas, P.; Patra, S.; Roy, H.; Tiwary, C.S.; Paliwal, M.; Mondal, M.K. Effect of Mn Addition on the Mechanical Properties of Al-12.6Si Alloy: Role of Al15(MnFe)3Si2 Intermetallic and Microstructure Modification. Met. Mater. Int. 2021, 27, 1713–1727. [CrossRef]
- [2] Mrówka-Nowotnik, G.; Sieniawski, J.; Wierzbiński, M. Intermetallic phase particles in 6082 aluminium alloy. Arch. Mater. Sci. Eng. 2007, 28, 69–76.
- [3] Gan, J.; Du, J.; Wen, C.; Zhang, G.; Shi, M.; Yuan, Z. The Effect of Fe Content on the Solidification Pathway, Microstructure and Thermal Conductivity of Hypoeutectic Al-Si Alloys. Int. J. Met. 2022, 16, 178–190. [CrossRef]
- [4] Radetić, T.; Popović, M.; Novaković, M.; Rajić, V.; Romhanji, E. Identification of Fe-bearing phases in the as-cast microstructure of AA6026 alloy and their evolution during homogenization treatment. J. Min. Metall. Sect. B Metall. 2023, 59, 327-338. [CrossRef]
- [5] Zhang, A.; Li, Y. Thermal conductivity of aluminium alloys—A review. Materials 2023, 16, 2972. [CrossRef]
- [6] Madelung, O.; Klemens, P.G. Thermal Conductivity of Pure Metals and Alloys; Springer: Berlin/Heidelberg, Germany, 1991.
- [7] Davis, J.R. Aluminum and Aluminum Alloys; ASM International: Materials Park, OH, USA, 2001.
- [8] Vandersluis, E.; Lombardi, A.; Ravindran, C.; Bois-Brochu, A.; Chiesa, F.; MacKay, R. Factors Influencing Thermal Conductivity and Mechanical Properties in 319 Al Alloy Cylinder Heads. Mater. Sci. Eng. A 2015, 648, 401–411. [CrossRef]
- [9] Chen, J.K.; Hung, H.Y.; Wang, C.F.; Tang, N.K. Thermal and Electrical Conductivity in Al-Si/Cu/Fe/Mg Binary and Ternary Al Alloys. J. Mater. Sci. 2015, 50, 5630-5639. [CrossRef]
- [10] Kim, C.W.; Kim, Y.C.; Kim, J.H.; Cho, J.I.; Oh, M.S. Effect of Alloying Elements on the Thermal Conductivity and Casting Characteristics of Aluminum Alloys in High-Pressure Die Casting. Korean J. Met. Mater. 2018, 56, 805-812. [CrossRef]
- [11] Gan, J.Q.; Huang, Y.J.; Cheng, W.E.N.; Jun, D.U. Effect of Sr modification on microstructure and thermal conductivity of hypoeutectic Al-Si alloys. Trans. Nonferrous Met. Soc. China 2020, 30, 2879–2890. [CrossRef]
- [12] Choi, S.W.; Cho, H.S.; Kumai, S. Effect of the Precipitation of Secondary Phases on the Thermal Diffusivity and Thermal Conductivity of Al-4.5Cu Alloy. J. Alloys Compd. 2016, 688, 897-902. [CrossRef]
- [13] Zhou, Y.; Zhang, X.; Zhong, G.; Zhang, J.; Yang, Y.; Kang, D.; Li, H.; Jie, W.; Schumacher, P.; Li, J. Elucidating Thermal Conductivity Mechanism of Al-9Si Based Alloys with Trace Transition Elements (Mn, Cr, V). J. Alloys Compd. 2022, 907, 164446. [CrossRef]
- [14] Choi, S.W.; Kim, Y.M.; Kim, Y.C. Influence of Precipitation on Thermal Diffusivity of Al-6Si-0.4Mg-0.9Cu-(Ti) Alloys. J. Alloys Compd. 2019, 775, 132-137. [CrossRef]
- [15] Luo, G.; Zhou, X.; Li, C.B.; Du, J.; Huang, Z.H. A Quantitative Study on the Interaction Between Silicon Content and Heat Treatment on Thermal Conductivity of Al-Si Binary Alloys. Int. J. Met. 2022, 16, 1585–1594. [CrossRef]
- [16] Zhang, X.; Zhou, Y.L.; Zhong, G.; Zhang, J.C.; Chen, Y.N.; Jie, W.Q.; Schumacher, P.; Li, J.H. Effects of Si and Sr Elements on Solidification Microstructure and Thermal Conductivity of Al-Si-Based Alloys. J. Mater. Sci. 2022, 57, 6428–6444. [CrossRef]
- [17] Weng, W.P.; Nagaumi, H.; Sheng, X.D.; Fan, W.Z.; Chen, X.C.; Wang, X.N. Influence of Silicon Phase Particles on the Thermal Conductivity of Al-Si Alloys. In Light Metals 2019; Springer International Publishing: New York, NY, USA, 2019; pp. 193–198.
- [18] Zhang, A.L.; Li, Y.X. Effect of Alloying Elements on Thermal Conductivity of Aluminum. J. Mater. Res. 2023, 38, 2049–2058. [CrossRef]
- [19] Wen, C.; Gan, J.Q.; Li, C.B.; Huang, Y.J.; Du, J. Comparative Study on Relationship Between Modification of Si Phase and Thermal Conductivity of Al-7Si Alloy Modified by Sr/RE/B/Sb Elements. Int. J. Met. 2021, 15, 194–205. [CrossRef]
- [20] Wang, K.; Li, W.F.; Xu, W.Z.; Hou, S.Y.; Hu, S.D. Simultaneous Improvement of Thermal Conductivity and Strength for Commercial A356 Alloy Using Strontium Modification Process. Met. Mater. Int. 2021, 27, 4742-4756. [CrossRef]
- [21] Butler, C.; Babu, S.; Lundy, R.; Meehan, R.R.; Punch, J.E.F.F.; Jeffers, N. Effects of Processing Parameters and Heat Treatment on Thermal Conductivity of Additively Manufactured AlSi10Mg by Selective Laser Melting. Mater. Charact. 2021, 173, 110945. [CrossRef]
- [22] Kim, M.S. Effects of Processing Parameters of Selective Laser Melting Process on Thermal Conductivity of AlSi10Mg Alloy. Materials 2021, 14, 2410. [CrossRef]
- [23] Chen, J.K.; Hung, H.Y.; Wang, C.F.; Tang, N.K. Effects of Casting and Heat Treatment Processes on the Thermal Conductivity of an Al-Si-Cu-Fe-Zn Alloy. Int. J. Heat Mass Transf. 2017, 105, 189-195. [CrossRef]
- [24] Ramirez, A.M.; Beltrán, F.E.; Yáñez-Limón, J.M.; Vorobiev, Y.V.; Gonzalez-Hernandez, J.; Hallen, J.M. Effects of porosity on the thermal properties of a 380-aluminum alloy. J. Mater. Res. 1999, 14, 3901–3906. [CrossRef]
- [25] Zhang, C.; Du, Y.; Liu, S.H.; Liu, S.J.; Jie, W.Q.; Sundman, B. Microstructure and Thermal Conductivity of the As-Cast and Annealed Al-Cu-Mg-Si Alloys in the Temperature Range from 25_C to 400 _C. Int. J. Thermophys. 2015, 36, 2869-2880. [CrossRef]
- [26] Li, K.; Zhang, J.; Chen, X.L.; Yin, Y.H.; He, Y.; Zhou, Z.Q.; Guan, R.G. Microstructure Evolution of Eutectic Si in Al-7Si Binary Alloy by Heat Treatment and Its Effect on Enhancing Thermal Conductivity. J. Mater. Res. Technol. 2020, 9, 8780-8786. [CrossRef]
- [27] Kim, Y.M.; Choi, S.W.; Kim, Y.C.; Kang, C.S. Increasing the Thermal Diffusivity of Al-Si-Mg Alloys by Heat Treatment. J. Therm. Anal. Calorim. 2022, 147, 2139-2146. [CrossRef]
- [28] Rauta, V.; Cingi, C.; Orkas, J. Effect of Annealing and Metallurgical Treatments on Thermal Conductivity of Aluminium Alloys. Int. J. Met. 2016, 10, 157–171. [CrossRef]
- [29] Lumley, R.N.; Deeva, N.; Larsen, R.; Gembarovic, J.; Freeman, J. The role of alloy composition and T7 heat treatment in enhancing thermal conductivity of aluminium high pressure diecastings. Metall. Mater. Trans. A 2013, 44, 1074–1086. [CrossRef]
9. Copyright:
- This material is "Iva Nováková, Milan Jelínek and Martin Švec"'s paper: Based on "Thermal Conductivity of AlSi10MnMg Alloy in Relation to Casting Technology and Heat Treatment Method".
- Paper Source: https://doi.org/10.3390/ma17215329
This material was summarized based on the above paper, and unauthorized use for commercial purposes is prohibited.
Copyright © 2025 CASTMAN. All rights reserved.