This article introduces the paper "Clinching of inductively heated aluminum die casting" presented at the "Production Engineering"
1. Overview:
- Title: Clinching of inductively heated aluminum die casting
- Author: Sinan Yarcu, Bernd-Arno Behrens, Sven Huebner, Torsten Schuchardt, Klaus Dilger, Thomas Paul Meichsner
- Publication Year: 2022
- Publishing Journal/Academic Society: Production Engineering
- Keywords: Joint, Clinching, Die casting, Heated clinching, Tempered clinching
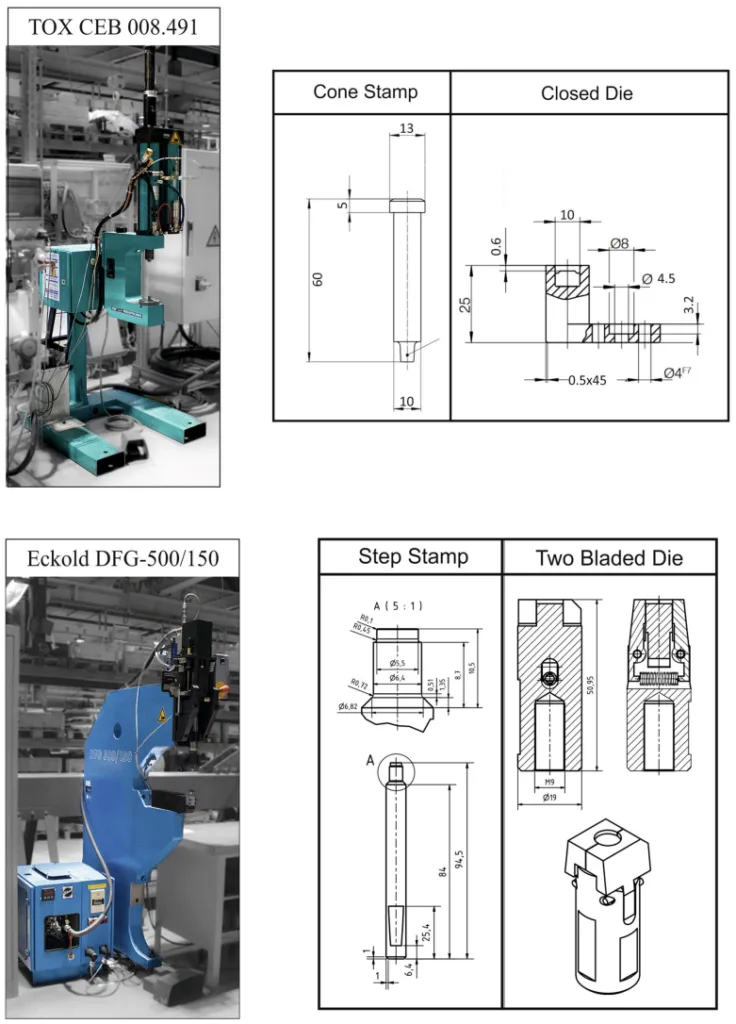
2. Research Background:
- Social/Academic Context of the Research Topic:
In the automotive industry, the use of multi-material bodies (MMB) is increasing to optimize vehicle weight and performance. Joining dissimilar materials like aluminum and steel presents challenges for conventional methods like spot welding due to differing thermal properties. Clinching is considered a suitable alternative. However, aluminum die casting alloys, known for their brittleness, are difficult to clinch without cracking. Previous research indicated that preheating magnesium die casting can prevent cracking, but this approach was not explored for aluminum die casting. - Limitations of Existing Research:
Existing research on clinching aluminum die casting alloys reveals issues with cracking due to the material's inherent brittleness. While optimized tool geometry and alternative methods like self-pierce riveting and friction stir riveting have been explored, they often result in reduced interlocking or are still susceptible to fracture. Preheating methods to mitigate cracking in magnesium die casting were known, but the application of preheating, specifically inductive heating, to aluminum die casting clinching was not sufficiently researched. - Necessity of the Research:
To expand the application of clinching for joining aluminum die casting alloys in MMB structures, it is necessary to overcome the cracking issue associated with their brittleness. Inductive heating has shown promise as a rapid and efficient heating method. Therefore, research is needed to investigate and optimize inductive heating strategies to enable process-safe clinching of aluminum die casting alloys, ensuring crack-free joints and improved joint strength.
3. Research Purpose and Research Questions:
- Research Purpose:
The primary aim of this research is to enhance the clinching process for aluminum die casting alloys by employing local heat treatment to achieve process-safe joining. The focus is to use inductive heating to temporarily reduce the brittleness of the aluminum die casting alloy, thereby preventing cracking during clinching and improving joint performance. - Key Research Questions:
- How does local inductive heat treatment affect the formation of crack-free clinch points in aluminum die casting alloys?
- What is the optimal heating strategy (heating time, temperature) using inductive heating for clinching aluminum die casting alloys with different tool systems?
- How do different clinching tool systems (flexible die vs. rigid die) and inductor designs influence the clinching process and joint characteristics when combined with inductive heating?
- What is the impact of inductive heating on the geometric dimensions (interlock, bottom thickness, neck thickness) of clinch joints in aluminum die casting alloys?
- How does inductive heating affect the tensile strength of clinched joints in aluminum die casting alloys?
- Research Hypotheses:
- Local inductive heating will reduce cracking during the clinching of aluminum die casting alloys.
- Inductive heating will improve the interlock and consequently the head tensile strength of clinched joints.
- Different inductor and tool designs will have varying effects on heating time, crack behavior, and joint geometry.
- Optimized inductive heating parameters can enable crack-free clinching of aluminum die casting alloys within a short process time (below 6 seconds).
4. Research Methodology
- Research Design:
This research employs an experimental design to investigate the effects of inductive heating on the clinching of aluminum die casting alloys. The study compares two clinching tool systems (flexible die and rigid die) and two inductor designs with varying diameters. The independent variables are heating strategy (inductive heating parameters), tool system, and inductor design. The dependent variables are heating time, crack behavior, surface quality of clinch points, joint geometry (interlock, bottom thickness, neck thickness), and head tensile strength. - Data Collection Method:
- Time-temperature curves: Measured using type K thermocouples inserted into the die casting material to determine heating times for different power levels and inductor configurations.
- Surface analysis: Microscopic examination of clinch points to assess crack formation and surface quality at different heating temperatures.
- Dimensional measurements: Analysis of clinch point geometry (interlock, bottom thickness, neck thickness) using profile projectors or similar measurement tools.
- Mechanical testing: Head tension tests according to DVS 3480 standard to evaluate the joint strength of clinched samples with and without inductive heating.
- Analysis Method:
- Qualitative analysis: Visual inspection of clinch points for crack detection and surface characteristics.
- Quantitative analysis: Statistical analysis of time-temperature data, dimensional measurements, and head tensile strength test results. Mean values and standard deviations were calculated.
- Comparative analysis: Comparison of results obtained with different tool systems, inductor designs, and heating parameters to determine optimal conditions for crack-free clinching and improved joint performance.
- Research Subjects and Scope:
The research focuses on joining aluminum die casting alloy EN AC-AlSi9Mn (3 mm thickness) in the as-casted condition (F) to aluminum sheet EN AW-5182 (1.5 mm thickness). Two clinching presses (Eckold DFG-500/150 and TOX CEB 008) and associated tooling systems (BTM flexible die and TOX rigid die) were used. Miniaturized ring inductors were designed and manufactured for each press. The scope is limited to laboratory experiments and material characterization to assess the feasibility and benefits of inductively heated clinching for this specific material combination.
5. Main Research Results:
- Key Research Results:
- Crack-free clinching of aluminum die casting alloy EN AC-AlSi9Mn was achieved using local inductive heating with both flexible (BTM) and rigid (TOX) die systems.
- Inductive heating significantly reduced the time required to achieve crack-free clinching points, with successful joints produced in under 6 seconds.
- The rigid die system (TOX) required lower heating temperatures (220 °C) compared to the flexible die system (BTM) (260 °C) to achieve crack-free clinching.
- Inductive heating led to an increased interlock in the clinch joints for both tool systems.
- Head tensile strength was improved by inductive heating, showing a 26% increase for the BTM tool system and a 25% increase for the TOX tool system compared to clinching at room temperature.
- Neck thickness remained largely unchanged with inductive heating, suggesting shear tensile strength is not significantly affected.
- Statistical/Qualitative Analysis Results:
- Time-temperature curves demonstrated faster heating rates with higher generator power and for the inductor used with the Eckold press (larger diameter).
- Surface analysis micrographs confirmed the absence of cracks in clinch points produced with inductive heating above specific temperature thresholds for both die systems.
- Dimensional measurements showed a notable increase in interlock (f) with inductive heating for both tool systems (up to +47% for TOX and +30% for BTM). Bottom thickness (tb) was significantly reduced with inductive heating, particularly for the flexible die. Neck thickness (tn) remained relatively stable.
- Head tension tests indicated statistically significant increases in joint strength for inductively heated samples compared to room temperature clinched samples.
- Data Interpretation:
- Local inductive heating effectively reduces the brittleness of aluminum die casting alloy, enabling crack-free clinching in short process times.
- The rigid die system's concentrated heat in the die body facilitates faster and more efficient heating compared to the flexible die system, which experiences heat loss through the blades.
- The increased interlock achieved through inductive heating is the primary factor contributing to the enhanced head tensile strength.
- The consistent neck thickness suggests that the improvement in joint strength is mainly due to form closure enhancement (interlock) rather than increased material strength in the neck region.
- Figure Name List:
- Fig. 1 Aluminum-intensive mixed construction using the Audi e-tron GT Coupé as an example [3]
- Fig. 2 Clinching press of the company Eckold (down) and the company TOX (up); the used clinching tool system of the company BTM (down) and the company TOX (up)
- Fig. 3 Production drawing of the miniaturized ring inductor for the Eckold clinching press (left) and for the TOX clinching press (right)
- Fig. 4 Setup of the inductive heating concept suitable for series production for the Eckold clinching press (up) and TOX clinching press (down)
- Fig. 5 Casting part with the sample positions (left) and measured mechanical properties
- Fig. 6 General view of the fracture surface of the prematurely cracked tensile specimen of the alloy EN AC-AlSi9Mn, the area with the cold shut is clearly visible (left) and rendered 3D model of the pore analysis of a tensile specimen next to the venting
- Fig. 7 Principle scheme of the shielding of the magnetic field lines
- Fig. 8 Dimensions of clinch elements of a rigid die (up) and a flexible die (down) [13]
- Fig. 9 Time-temperature curve for inductive heating with different manipulated variable (power value) for the inductor on the TOX clinching press (left) and the inductor on the Eckold clinching press (right)
- Fig. 10 Overview table of surface analysis of a moving BTM die (blue box) with a rigid die (green box) using a miniaturized inductor (colour figure online)
- Fig. 11 Close-up surface analysis of a moving BTM die (blue box) with a rigid die (green box) using a miniaturized inductor (colour figure online)
- Fig. 12 Head tensile strength of the clinching joints at room temperature and at 220 °C for a rigid die (TOX) and a flexible die (BTM)
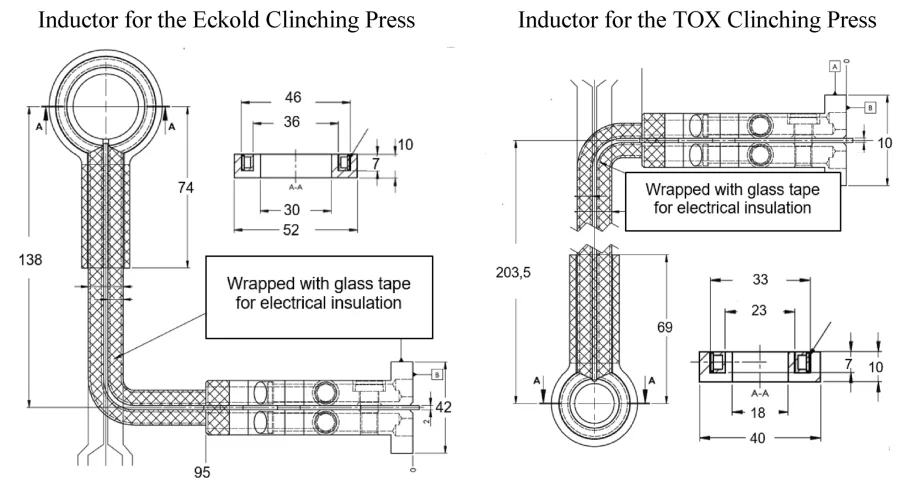
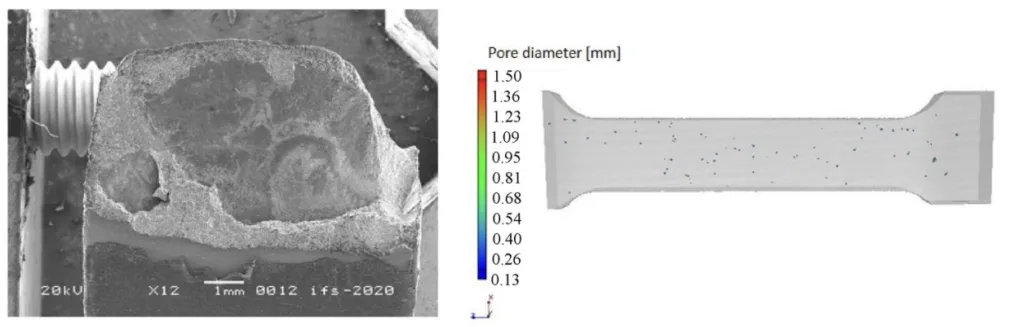
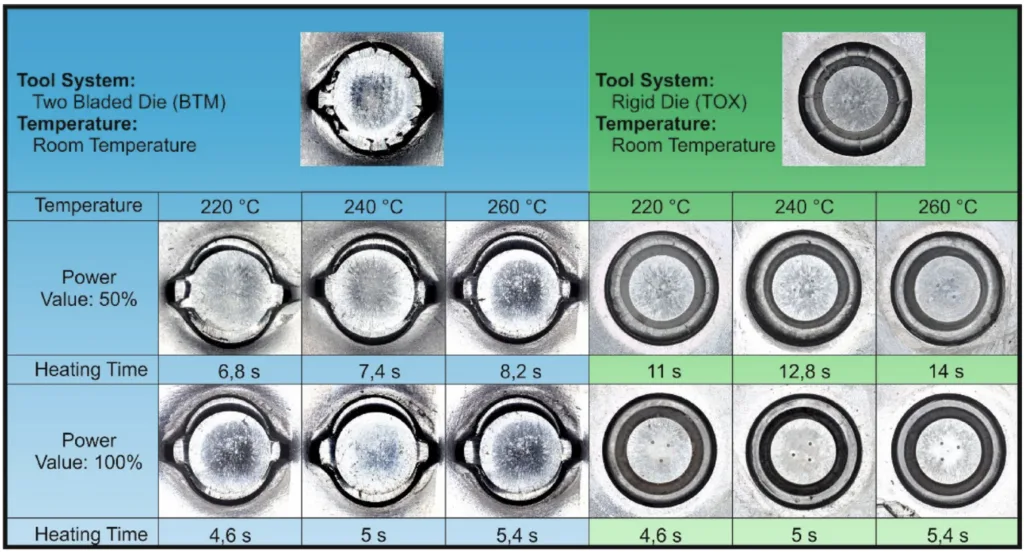
6. Conclusion and Discussion:
- Summary of Main Results:
This study successfully demonstrated that local inductive heating enables crack-free clinching of aluminum die casting alloy EN AC-AlSi9Mn in short cycle times (less than 6 seconds). Both rigid and flexible die systems, when combined with inductive heating, produced improved clinch joints with enhanced interlock and head tensile strength. The rigid die system proved more efficient in terms of heating temperature requirements. - Academic Significance of the Research:
This research contributes to the fundamental understanding of joining brittle materials like aluminum die casting alloys. It provides valuable insights into the application of inductive heating for enhancing the clinching process. The study highlights the influence of tool system design and heating strategy on joint quality and process efficiency. The findings can be used as a basis for further optimization of heated clinching processes for lightweight automotive structures. - Practical Implications:
The developed inductively heated clinching method offers a practical solution for joining aluminum die casting components in automotive manufacturing and other industries. The process enables the use of lightweight materials in complex designs by overcoming the limitations of conventional joining techniques. The short cycle times achieved with inductive heating are suitable for high-volume production. The improved joint strength enhances the reliability and durability of multi-material structures. - Limitations of the Research:
The study is limited to a specific aluminum die casting alloy and sheet material combination. Further research is needed to evaluate the applicability of this method to other aluminum alloys and material pairings. The long-term durability and corrosion behavior of inductively heated clinch joints were not investigated in this study. The optimization of inductor design and heating parameters could be further explored for different component geometries and production scenarios.
7. Future Follow-up Research:
- Directions for Follow-up Research:
- Investigate the application of inductively heated clinching to a wider range of aluminum die casting alloys and dissimilar material combinations (e.g., aluminum to steel).
- Optimize inductor designs and heating parameters for different component geometries and thicknesses to improve energy efficiency and process robustness.
- Conduct durability testing (fatigue, corrosion) to evaluate the long-term performance of inductively heated clinch joints in various environmental conditions.
- Explore advanced control strategies for temperature regulation during inductive heating to further enhance process stability and joint quality.
- Investigate the integration of this technology into industrial production lines and assess its scalability and cost-effectiveness.
- Areas Requiring Further Exploration:
- The influence of different surface treatments and coatings on the inductively heated clinching process and joint performance.
- The effect of varying air gaps between the inductor and workpiece on heating efficiency and joint characteristics.
- The potential for integrating process monitoring and quality control systems into the inductively heated clinching process.
- Numerical simulation and modeling of the coupled electromagnetic, thermal, and mechanical phenomena during inductively heated clinching to optimize process parameters and tool design.
8. References:
- [1] Hirsch J (2011) Aluminium in innovative light-weight car design. Mater Trans 52(5):818-824
- [2] Taub AL, Krajewski PE, Luo AA et al (2007) The evolution of technology for materials processing over the last 50 years: the automotive example. JOM 59(2):48-57
- [3] Audi MediaCenter (2021) https://www.audi-mediacenter.com/de/hightech-trifft-handarbeitdie-produktion-des-audi-e-tron-gt-in-den-boellinger-hoefen-13242/leidenschaft-fuer-qualitaet-und-progressivitaet-der-neue-audi-e-tron-gt-13243
- [4] Behrens B-A, Bouguecha A, Vucetic M, Hübner S, Yilkiran D, Jin Y, Peshekhodov I (2015) FEA-based optimisation of a clinching process with an open multiple-part die aimed at damage minimisation in CR240BH-AlSi10MnMg joints. Mater Sci Eng Chem 21:1-7
- [5] Zhao X, Meng D, Zhang J, Han Q (2020) The effect of heat treatment on die casting aluminum to apply self-pierce riveting. Int J Adv Manuf Technol 109:2409-2419
- [6] Zhao X (2019) Research on applying the self-pierce riveting (SPR) for die casting aluminum alloys. A Dissertation submitted to the Faculty of Purdue University
- [7] Böllhoff (2021) Joining of aluminium cast with new ring groove die, Homepage. https://www.boellhoff.com/de-en/news/news/2017/rivset-ring-groove-die.php
- [8] Jäckel M, Coppieters S, Hofmann M, Vandermeiren N, Landgrebe D, Debruyne D, Wallmersberger T, Faes K (2017) Mechanical joining of materials with limited ductility: analysis of process-induced defects. In: Proceedings of the 20th international ESA-FORM conference on material forming, AIP conference proceedings, vol 1896, pp 110009-1-110009-6
- [9] Hovanski Y, Upadyay P, Kleinbaum S, Carlson B, Boettcher E, Ruokolainen R (2017) Enabling dissimilar material joining using friction stir scribe. JOM 69(6):1060-1064
- [10] Ang HQ (2021) An overview of self-piercing riveting process with focus on joint failures, corrosion issues and optimisation techniques. Chin J Mech Eng 34:2. https://doi.org/10.1186/$10033-020-00526-3
- [11] Wang JW, Liu ZX, Shang Y et al (2011) Self-piercing riveting of wrought magnesium AZ31 sheets. J Manuf Sci Eng 133(3):031009
- [12] Yarcu S, Huebner S, Yilkiran D, Brunotte K, Behrens B-A, Schuchardt T, Mueller S, Dilger K (2021) Clinching of heated aluminium die cast. In: Journal: proceedings of the 11th congress of the German Academic Association for Production Technology
- [13] Merkblatt DVS/EFB 3420: Clinchen-Überblick / Clinching basics (2018) DVS-Deutscher Verband für Schweißen und Verwandte Verfahren e.V., EFB-Europäische Forschungsgesellschaft für Blechverarbeitung e. V
- [14] Varis J (2006) Ensuring the integrity in clinching process. J Mater Process Technol 174:277-285
9. Copyright:
*This material is Sinan Yarcu's paper: Based on "Clinching of inductively heated aluminum die casting".
*Paper Source: https://doi.org/10.1007/s11740-022-01116-z
This material was summarized based on the above paper, and unauthorized use for commercial purposes is prohibited.
Copyright © 2025 CASTMAN. All rights reserved.