This article introduces the paper "Causes of Casting Defects with Remedies" presented at the "International Journal of Engineering Research & Technology (IJERT)"
1. Overview:
- Title: Causes of Casting Defects with Remedies
- Author: Rahul T Patil, Veena S Metri, Shubhangi S Tambore
- Publication Year: November-2015
- Publishing Journal/Academic Society: International Journal of Engineering Research & Technology (IJERT), Vol. 4 Issue 11
- Keywords: Die Casting; Defects in Casting; Causes and Remedies for Casting Defects
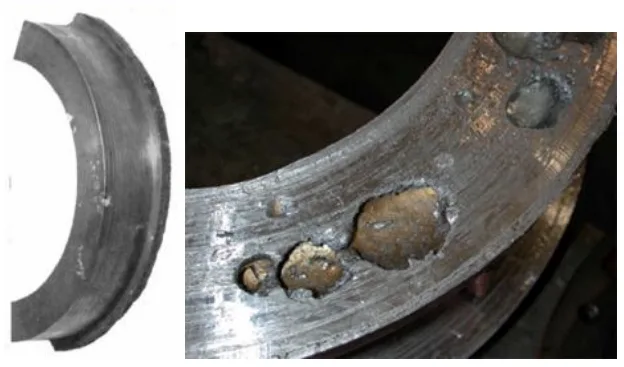
2. Research Background:
- Social/Academic Context of the Research Topic: Die casting is highlighted as an efficient and economical manufacturing process capable of producing geometrically complex components. However, the occurrence of casting defects is a recognized challenge within this process. Identifying and addressing these defects is crucial for maintaining quality and efficiency in die casting applications.
- Limitations of Existing Research: The paper does not explicitly state limitations of existing research, but implies a need for a consolidated resource that classifies and explains casting defects, their causes, and remedies specifically within aluminum-alloy die casting.
- Necessity of the Research: The research is necessary to provide a structured understanding of casting defects in aluminum die casting. By classifying defects based on their root causes and detailing remedies, the paper aims to assist casting suppliers and customers in identifying, analyzing, and rectifying defects, ultimately improving casting quality and reducing rejections.
3. Research Purpose and Research Questions:
- Research Purpose: The main objective of this paper is to identify different defects encountered in aluminum-alloy die casting and to provide remedies for these defects along with their root causes.
- Key Research Questions: The paper implicitly addresses the following research questions:
- What are the common defects observed in aluminum-alloy die casting?
- What are the root causes of these defects?
- What are the effective remedies to mitigate or eliminate these defects?
- Research Hypotheses: The paper does not explicitly state research hypotheses but operates under the implicit hypothesis that classifying defects by their sources and providing corresponding remedies will be beneficial for the die casting industry.
4. Research Methodology
- Research Design: This paper is a review and classification study. It compiles and categorizes existing knowledge on casting defects, causes, and remedies, specifically focusing on aluminum die casting.
- Data Collection Method: The research is based on a review of existing literature and industry knowledge related to die casting defects. The paper references handbooks, conference proceedings, and journal articles as sources of information.
- Analysis Method: The paper employs a qualitative analysis approach, classifying casting defects based on their sources (Metallurgical, Heat-related, and Mechanically induced). For each defect type, the paper describes the causes and proposes remedies based on established die casting principles and best practices.
- Research Subjects and Scope: The scope of the paper is limited to casting defects in aluminum die casting. The defects discussed are categorized based on their sources of occurrence, and both surface and bulk defects are considered within each category.
5. Main Research Results:
- Key Research Results: The paper classifies casting defects in aluminum die casting into three main categories based on their source: Metallurgical defects, Defects due to heat, and Mechanically induced defects. Within each category, specific defect types are identified, along with their causes and remedies.
- Statistical/Qualitative Analysis Results: The paper is primarily qualitative and does not present statistical analysis. The results are presented as a structured classification and description of defects, causes, and remedies.
- Data Interpretation: The paper interprets casting defects based on established metallurgical and manufacturing principles. Causes are explained in terms of process parameters, material properties, and design factors. Remedies are suggested based on correcting these identified causes.
- Figure Name List:
- Fig 3.1 Gas porosity
- Fig 3.2 Shrinkage Porosity
- Fig 3.3 Sinks
- Fig 3.4 Blister
- Fig 3.5 Soldering
- Fig 3.6 Segregation
- Fig 3.7 Inclusion
- Fig 3.8 Dross
- Fig 4.1 Crack
- Fig 5.1 Hot tears
- Fig 5.2 Hot tears in part
- Fig 6.1 cold shut in part
- Fig 7.1 Misrun in part
- Fig 8.1 Thermal defect
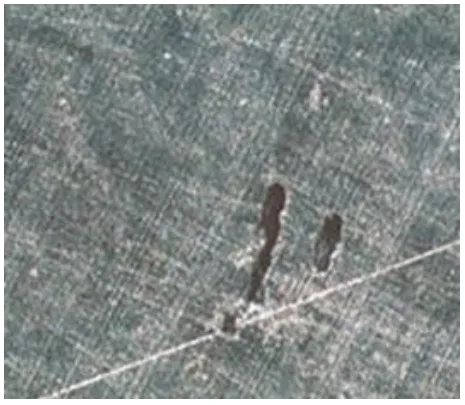
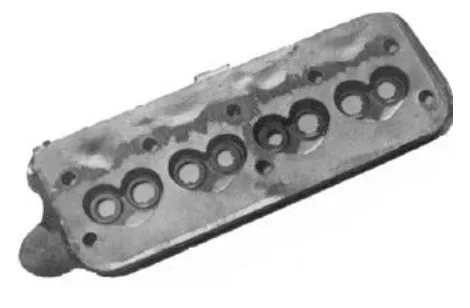
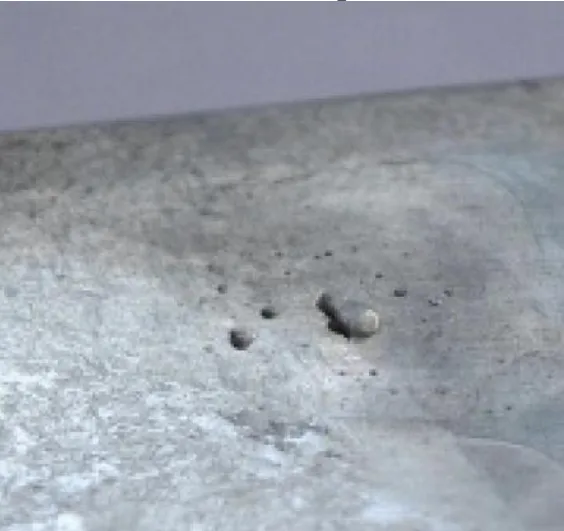
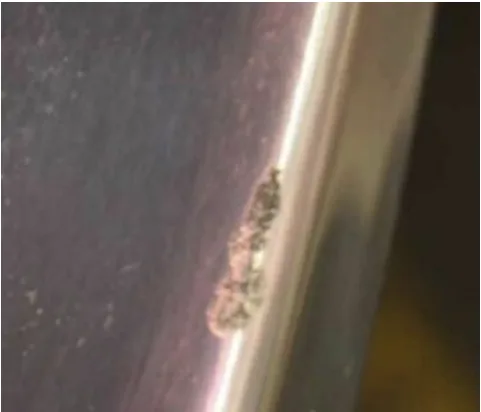
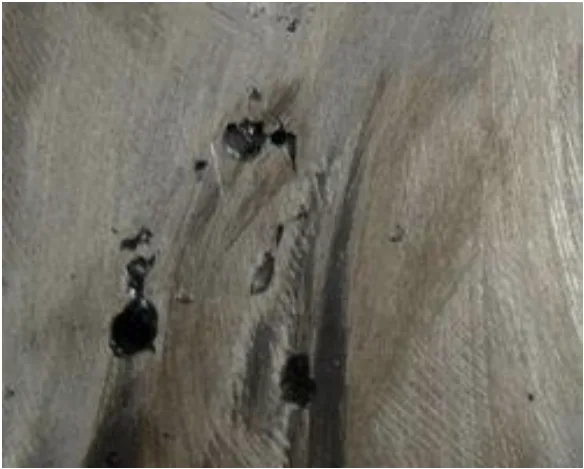
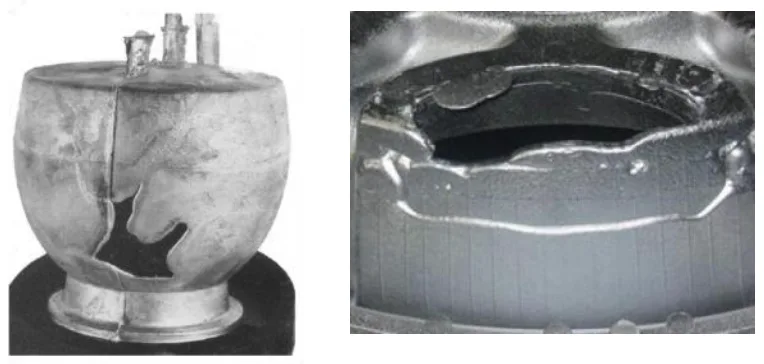
6. Conclusion and Discussion:
- Summary of Main Results: The paper successfully classifies and describes various casting defects in aluminum die casting, categorizing them by source and providing detailed causes and remedies for each. The classification includes Metallurgical defects (Porosity, Sinks, Inclusion, Dross, Soldering), Heat-related defects (Hot tears, Cold shut, Thermal fatigue), and Mechanically induced defects (Surface marks, bending, undercuts).
- Academic Significance of the Research: The paper provides a valuable handbook-level summary of casting defects, consolidating information from various sources into a structured and easily accessible format. This classification approach can serve as a useful reference for researchers and practitioners in the field of die casting.
- Practical Implications: The detailed description of causes and remedies for each defect type offers practical guidance for quality control departments in casting industries. By utilizing this information, die casters can improve their defect analysis processes, optimize process parameters, and implement effective remedies to enhance productivity and casting yield. The paper emphasizes that minimizing casting rejections relies on understanding and addressing the root causes of defects.
- Limitations of the Research: The paper is a review and classification study and does not involve empirical testing or validation of the proposed remedies. The effectiveness of the remedies is based on general die casting principles and industry best practices, and may need to be further validated through specific case studies or experimental research.
7. Future Follow-up Research:
- Directions for Follow-up Research: Future research could focus on:
- Empirical validation of the proposed remedies through designed experiments and case studies in industrial settings.
- Quantitative analysis of the effectiveness of different remedies on defect reduction.
- Development of advanced diagnostic tools and techniques for real-time defect detection and analysis in die casting processes.
- Investigating the application of simulation software to predict and prevent casting defects, as briefly mentioned in the context of shrinkage porosity remedies.
- Areas Requiring Further Exploration: Further exploration is needed in the area of optimizing process parameters and alloy compositions to minimize defect occurrence, and in developing more robust and automated quality control systems for die casting.
8. References:
- [1] D.L cocks. “A proposed simple qualitative classification for die-casting"; 'Proc Die-casting Conference, Montreaux(1996)
- [2] ASM Handbook: Volume 15: Casting edition 9",2008,pp629-620.
- [3] J. Campbell, R.A hardening. "Casting technology", in TAIAT 2.0ncd-rom, EAA, Brussels, 2000
- [4] John Gilbert Kaunfman, Elwin L. Rooy," Aluminum alloy casting: Properties, Processes, and application", ASM international,pp47-54
- [5] R.Monroe," porosity in casting", AFS Transcation,2005,pp1-29.
- [6] Defect formation in cast iron LennartElmquist School of Engineering Jönköping University, SwedenTammerfors, Finland, November 8, 2012.
- [7] Analysis of Casting Defects and Identification of emedial Measures - A Diagnostic Study Dr D.N. Shivappal, Mr Rohit2, Mr. Abhijit Bhattacharya3 International Journal of Engineering Inventions ISSN: 2278-7461, www.ijeijournal.com Volume 1, Issue 6 (October2012) PP: 01-05
- [8] Casting Defect Analysis using Design of Experiments (DoE) and Computer Aided Casting Simulation Technique Uday A. Dabade* and Rahul C. Bhedasgaonkar,(2013) [5]. Reduction of defects in grey cast iron castings by six sigma approach Raguramsingh.M#1, SyathAbuthakeer.S*2 #ME Lean Manufacturing, PSG.
- [9] W.G WAlkington, “Gas Porosity: A guid t corrective the problem, North America die casting association, "1997.
9. Copyright:
*This material is "Rahul T Patil, Veena S Metri, Shubhangi S Tambore"'s paper: Based on "Causes of Casting Defects with Remedies".
*Paper Source: www.ijert.org
This material was summarized based on the above paper, and unauthorized use for commercial purposes is prohibited.
Copyright © 2025 CASTMAN. All rights reserved.