This article introduces the paper "A COMPARATIVE ANALYSIS ON ORGANIC AND INORGANIC CORE BINDERS FOR A GRAVITY DIECASTING AL ALLOY COMPONENT" presented at the International Journal of Metalcasting
1. Overview:
- Title: A COMPARATIVE ANALYSIS ON ORGANIC AND INORGANIC CORE BINDERS FOR A GRAVITY DIECASTING AL ALLOY COMPONENT
- Authors: A. Fortini, M. Merlin, and G. Raminella
- Publication Year: 2022
- Publishing Journal/Academic Society: International Journal of Metalcasting
- Keywords: sand cores, optical measurement, gravity diecasting, moisture absorption tests, storage stability
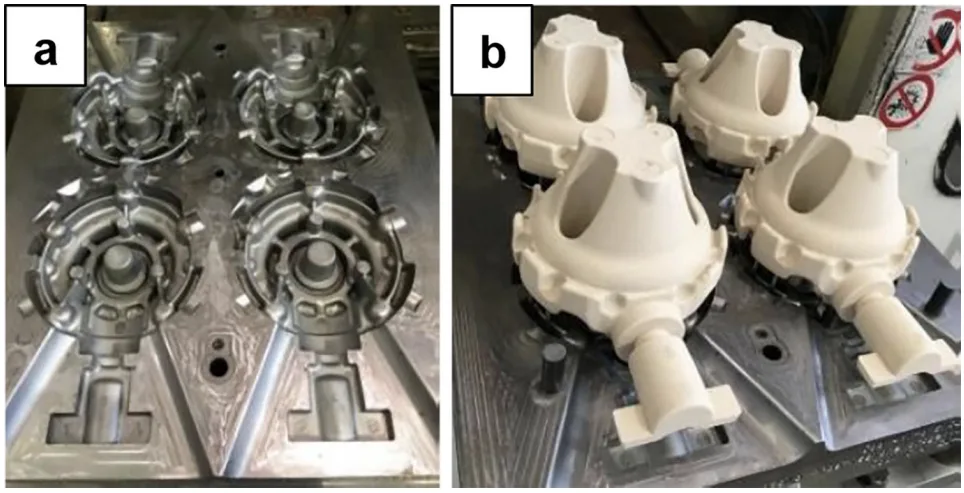
2. Research Background:
The metal casting industry has witnessed an increasing interest in inorganic binders for core making over the past two decades. This shift is primarily driven by the health and environmental advantages associated with inorganic binders compared to traditional organic binders. However, the widespread adoption of inorganic binders in commercial applications necessitates continuous technical advancements to overcome certain inherent limitations, particularly concerning storage stability. Inorganic cores are known to be susceptible to degradation during storage, raising concerns about their suitability as direct replacements for organic cores. Existing research has not sufficiently addressed the practical implementation and performance of these binder systems within foundry environments, especially considering the impact of moisture absorption. This study addresses this gap by investigating the feasibility of using inorganic core binders as substitutes for organic binders in the production of gravity die-cast aluminum alloy components, focusing on the critical aspect of moisture sensitivity during typical foundry storage conditions.
3. Research Purpose and Research Questions:
This research aims to evaluate and compare the performance of organic and inorganic core binders in the context of gravity die casting of aluminum alloy components. The study specifically investigates the effects of moisture absorption on core stability and the resulting impact on the quality of the final castings.
Key research questions addressed in this paper include:
- Can inorganic core binders effectively replace organic core binders in the production of gravity die-cast aluminum alloy components?
- How does moisture absorption during foundry storage affect the dimensional stability and structural integrity of inorganic cores compared to organic cores?
- What are the differences in mechanical properties and microstructure of aluminum alloy castings produced using organic versus inorganic core binders?
- What are the comparative levels of harmful emissions generated during the casting process when using organic and inorganic core binders?
The underlying hypothesis is that while inorganic cores offer environmental benefits, their moisture sensitivity might pose challenges in practical foundry applications. This study seeks to quantify these challenges and assess the overall viability of inorganic cores as a sustainable alternative to organic cores.
4. Research Methodology
This study employed a comparative experimental research design to evaluate organic and inorganic core binders. The research methodology encompassed the following key steps:
- Research Design: A comparative analysis was conducted, contrasting organic cores produced using a phenolic urethane cold-box process with inorganic cores made with a commercial sodium silicate-based Cordis binder system.
- Data Collection Method:
- Moisture Absorption Tests: Sand samples and complete cores were subjected to various humidity conditions. Weight loss on ignition and weight gain in controlled humidity environments (climatic chamber at 40 °C and 100% relative humidity, and foundry warehouse conditions) were measured to assess moisture sensitivity.
- 3D Optical Measurements: Dimensional changes in inorganic cores due to moisture absorption were precisely measured using a GOM Atos ScanBox 4105 optical 3D measuring machine, comparing measurements against the CAD model.
- Casting Trials: Gravity die casting trials were performed using A356 aluminum alloy and both organic and inorganic cores to produce drivetrain motorcycle components.
- Mechanical Testing: Tensile properties (yield strength Rp0.2, tensile strength Rm, and elongation A%) of the castings were evaluated using a Galdabini Quasar 50 testing machine.
- Microstructural Analysis: Secondary dendrite arm spacing (SDAS) and porosity content were analyzed using a ZEISS Axioscope 7 optical microscope and Zen Core 2.7 image analysis software.
- Emission Analysis: Gaseous organic compound emissions during casting were collected and analyzed using gas chromatography technique following UNI CEN/TS 13649 standards. Visual inspection of mold cavity conditions after casting cycles was also conducted.
- Analysis Method: Quantitative data analysis was performed on weight measurements, dimensional deviations, tensile properties, SDAS, porosity, and emission concentrations. Qualitative assessments were made based on visual inspections of sand, core appearance, and mold conditions.
- Research Subjects and Scope: The study focused on comparing a specific organic binder system (phenolic urethane cold-box) and an inorganic binder system (sodium silicate-based Cordis) for producing sand cores used in gravity die casting of A356 aluminum alloy components for automotive applications. The scope included evaluating core performance under different storage humidity conditions relevant to foundry operations.
5. Main Research Results:
The experimental results provided a comprehensive comparison of organic and inorganic core binder performance. Key findings are summarized below:
- Moisture Absorption:
- Weight Loss (WL): Table 2 shows the weight loss on ignition for both core types. Organic cores exhibited WL values of 1.068-1.187%, while inorganic cores showed WL values of 0.184-0.332%. It's noted that for organic cores, the WL values include approximately 1.06% due to binder evaporation.
- Moisture Absorption (MA) in Climatic Chamber: Figure 3 illustrates that inorganic cores exhibited a greater tendency for moisture absorption in the climatic chamber (40 °C and 100% relative humidity) compared to organic cores, reflected in higher MA percentages.
- Moisture Absorption in Foundry Warehouse: Figure 5b demonstrates that the moisture absorption increment for inorganic cores during storage in the foundry warehouse (18 °C and 32% relative humidity) was negligible over 14 days, with MA increasing from 0.191% to 0.245%.
- Dimensional Stability:
- 3D optical measurements revealed that inorganic cores experienced dimensional changes under high humidity conditions in the climatic chamber (Figure 7a, b), with over-width deviations exceeding 0.3 mm.
- However, after 14 days of storage in the foundry warehouse (18 °C and 32% relative humidity), dimensional deviations of inorganic cores were minimal (Figure 7c, d), indicating dimensional stability under typical foundry storage conditions.
- Even under more extreme simulated storage conditions under a covered portico (temperature ranging from -8 °C to 2 °C and 80 % relative humidity), dimensional changes remained limited and structurally sound for up to 48 hours (Figure 8).
- Mechanical Properties of Castings:
- Tensile testing (Figure 9) showed comparable yield strength (Rp0.2) and tensile strength (Rm) values for castings produced with both organic and inorganic cores.
- Elongation (A%) values for castings made with inorganic cores were on average slightly higher and less scattered compared to those made with organic cores.
- Microstructure of Castings:
- Microstructural analysis (Figure 10b) indicated that castings produced with inorganic cores exhibited slightly lower secondary dendrite arm spacing (SDAS) values (22-27 µm) compared to organic cores (30-33 µm), suggesting a finer microstructure.
- Porosity levels (Table 3) were similar and low (below 0.08%) for castings produced with both core types.
- Emissions and Mold Condition:
- Emission analysis (Table 4) demonstrated significantly lower mass concentrations of harmful organic compounds emitted during casting with inorganic cores compared to organic cores.
- Visual inspection (Figure 11) showed that mold cavities used with inorganic cores remained cleaner after 200 cycles, with minimal residue compared to the dark resin coating observed in molds used with organic cores.
Figure Name List:
- Figure 1. Organic cores production by the cold-box process: (a) half core box, (b) organic cores.
- Figure 2. Images of the sand appearance during the moisture absorption test. Organic cores: (a) initial condition, (b) after loss of ignition for 2 hours, (c) after loss of ignition for 3 hours and (d) after loss of ignition for 4 hours. Inorganic cores: (e) initial condition, (f) after loss of ignition for 1 hour, (g) after loss of ignition for 2 hours and (h) after loss of ignition for 3 hours.
- Figure 3. Bar chart of MA (%) for organic and inorganic cores by storage time in the climate chamber.
- Figure 4. Images of cores after moisture absorption tests in the climate chamber: (a) organic after conditioning for 60 min; (b) inorganic core after conditioning for 60 min; (c) and (d) breakage of the inorganic core in (b).
- Figure 5. Moisture absorption tests for inorganic cores in the warehouse of the foundry: (a) image of the cores storage conditions, (b) bar chart of MA (%) by storage time.
- Figure 6. 3D digital color plots of an inorganic core in the initial condition: (a) front and (b) rear isometric views.
- Figure 7. 3D digital color plots of an inorganic core after moisture absorption: (a) front and (b) rear isometric views after 60 minutes of storage at 40 °C and 100% relative humidity in the climatic chamber, (c) front and (d) rear isometric views after 14 days of storage in the foundry warehouse at 18 °C and 32% relative humidity.
- Figure 8. 3D digital color plots of an inorganic core after moisture absorption: (a) front and (b) rear isometric views after 24 hours of storage under the covered portico of the foundry, (c) front and (d) rear isometric views after 48 hours of storage under the covered portico of the foundry.
- Figure 9. Effect of core binder system on the tensile properties: (a) location of tensile specimens, (b) tensile properties for casting trials made with organic cores, (c) tensile properties for casting trials made with inorganic cores.
- Figure 10. Effect of core binder system on SDAS values: (a) location of specimens, (b) bar chart of SDAS by locations for organic and inorganic cores.
- Figure 11. Images of the upper mold halves after 200 cycles with: (a) organic cores, (b) inorganic cores.
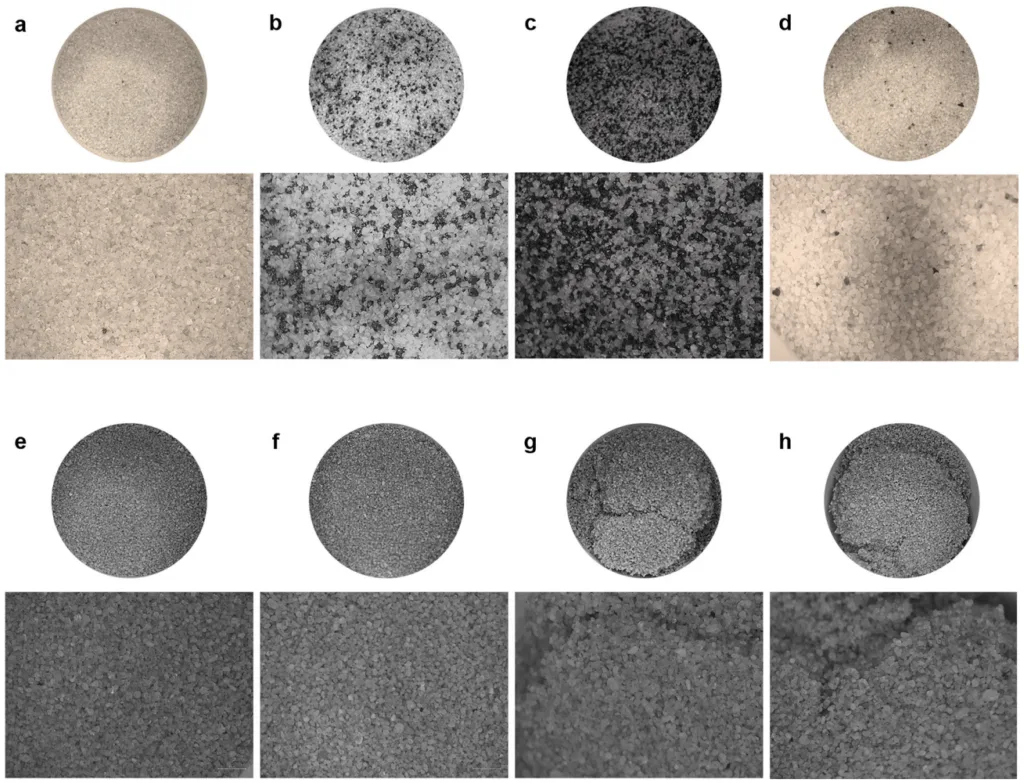
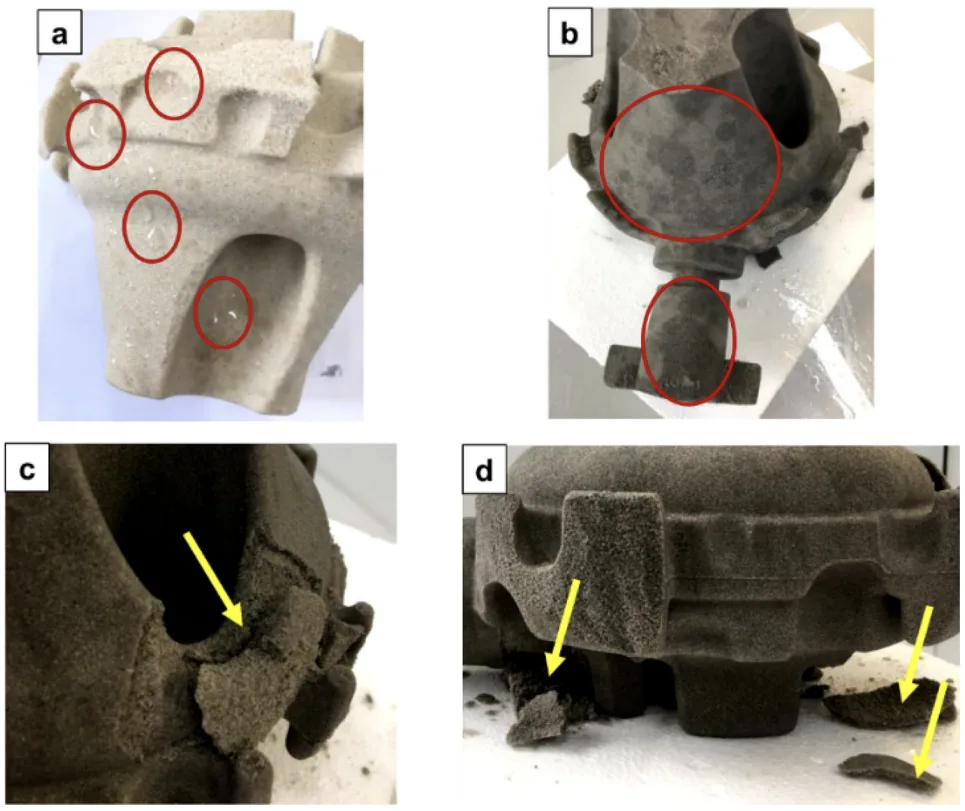
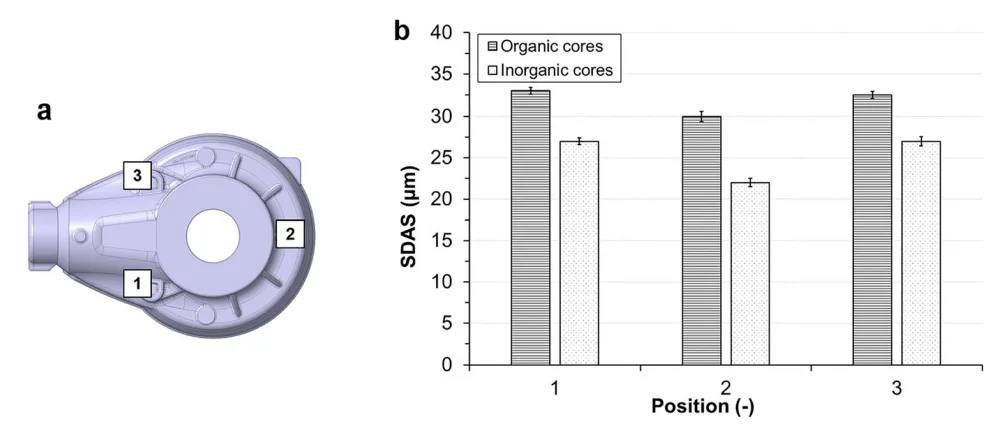
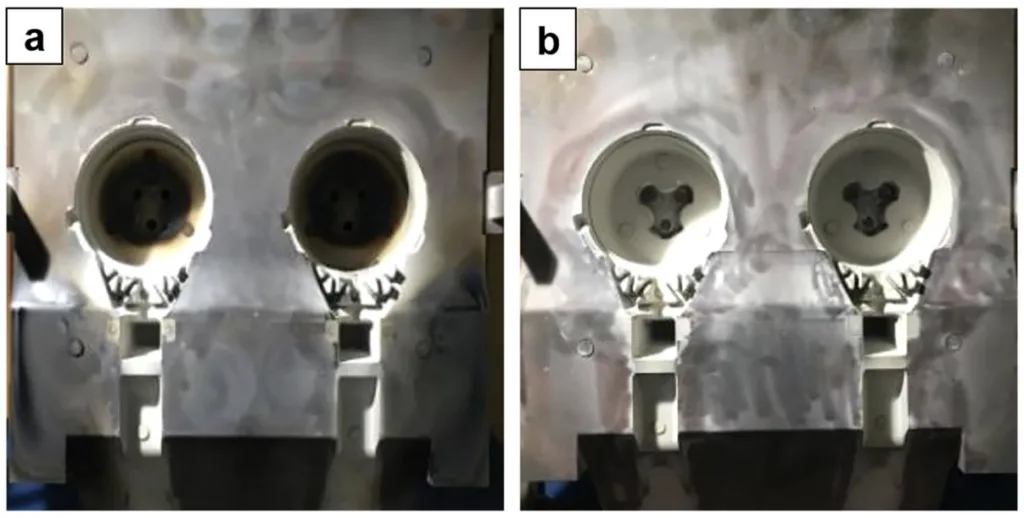
6. Conclusion and Discussion:
Summary of Main Results: This study concludes that inorganic core binders, specifically sodium silicate-based systems, present a viable alternative to traditional organic binders for gravity die casting of aluminum alloys. While inorganic cores exhibit a higher susceptibility to moisture absorption under extreme humidity conditions, they demonstrate sufficient stability and dimensional integrity under typical foundry warehouse storage conditions (up to 14 days). Castings produced with inorganic cores achieve comparable or even slightly improved mechanical properties and a finer microstructure compared to those made with organic cores. Crucially, inorganic cores offer significant environmental advantages by drastically reducing harmful gaseous emissions during casting and maintaining cleaner mold conditions over extended casting cycles.
Academic Significance of the Research: This research contributes valuable empirical data to the growing body of knowledge on inorganic binders in metal casting. It directly addresses concerns regarding moisture sensitivity and provides evidence of successful foundry application in gravity die casting. The study highlights the importance of considering realistic foundry storage conditions when evaluating the performance of inorganic core systems.
Practical Implications: The findings strongly suggest that foundries can confidently adopt inorganic core binders for gravity die casting to enhance sustainability and improve workplace environment without compromising casting quality. The reduced emissions and cleaner molds associated with inorganic cores translate to environmental and health benefits, as well as potential cost savings through reduced maintenance and cleaning. The study indicates that concerns about moisture-related storage instability of inorganic cores are manageable under typical foundry practices, particularly with storage durations up to 14 days in warehouse conditions.
Limitations of the Research: The study acknowledges limitations related to the confidentiality of the exact compositions of the organic and inorganic binder systems used. Furthermore, the long-term storage stability of inorganic cores beyond 14 days in foundry warehouse conditions was not extensively investigated.
7. Future Follow-up Research:
Directions for Follow-up Research: Future research should focus on further optimizing the composition of inorganic binders to enhance their inherent humidity resistance, potentially through the incorporation of specific additives.
Areas Requiring Further Exploration: Further exploration is recommended to investigate the long-term storage behavior of inorganic cores under a wider range of foundry conditions and to evaluate their performance with different aluminum alloys and casting processes beyond gravity die casting. Investigating the economic benefits of reduced mold maintenance and cleaning associated with inorganic cores would also be a valuable area for future study.
8. References:
[1] F. Czerwinski, M. Mir, W. Kasprzak, Application of cores and binders in metalcasting. Int. J. Cast Met. Res. 28, 129-139 (2015). https://doi.org/10.1179/1743133614Y.0000000140
[2] A. Kmita, C. Fischer, K. Hodor, M. Holtzer, A. Roczniak, Thermal decomposition of foundry resins: a determination of organic products by thermogravimetry-gas chromatography-mass spectrometry (TG–GC-MS). Arab. J. Chem. 11, 380–387 (2018). https://doi.org/10.1016/j.arabjc.2016.11.003
[3] S.M. Glowacki, C.R. Crandell, G.R. Cannon, F.S. Clobes, J.K. Voigt, R.C. Furness, J.C. McComb, B.A. Knight, Emissions studies at a test foundry using an advanced oxidation-clear water system. AFS Trans. 111, 579-598 (2003)
[4] Y. Wang, F.S. Cannon, M. Salama, J. Goudzwaard, J.C. Furness, Characterization of hydrocarbon emissions from green sand foundry core binders by analytical pyrolysis. Environ. Sci. Technol. 41, 7922–7927 (2007). https://doi.org/10.1021/es0716570
[5] S.M. Dobosz, K. Major-Gabryś, A. Grabarczyk, New materials in the production of moulding and core sands. Arch. Foundry Eng. 15, 25–28 (2015). https://doi.org/10.1515/afe-2015-0073
[6] R. Ramakrishnan, B. Griebel, W. Volk, D. Günther, J. Günther, 3D printing of inorganic sand moulds for casting applications. Adv. Mater. Res. 1018, 441-449 (2014)
[7] H. Polzin, Inorganic Binders: For Mould and Core Production in the Foundry (Schiele & Schön, Berlin, 2014).
[8] P. Lechner, G. Fuchs, C. Hartmann, F. Steinlehner, F. Ettemeyer, W. Volk, Acoustical and optical determination of mechanical properties of inorganically-bound foundry core materials. Materials (Basel) 13, 2531 (2020). https://doi.org/10.3390/ma13112531
[9] B.J. Stauder, H. Kerber, P. Schumacher, Foundry sand core property assessment by 3-point bending test evaluation. J. Mater. Process. Technol. 237, 188-196 (2016). https://doi.org/10.1016/j.jmatprotec.2016.06.010
[10] B. Grabowska, S. Żymankowska-Kumon, S. Cukrowicz, K. Kaczmarska, A. Bobrowski, B. Tyliszczak, Thermoanalytical tests (TG-DTG-DSC, Py-GC/MS) of foundry binders on the example of polymer composition of poly(acrylic acid)-sodium carboxymethylcellulose. J. Therm. Anal. Calorim. 138, 4427-4436 (2019). https://doi.org/10.1007/s10973-019-08883-5
[11] B.J. Stauder, D. Gruber, P. Schumacher, Specific fracture energy and de-agglomeration rate of silicate-bonded foundry sand cores. Prod. Eng. 12, 807-816 (2018). https://doi.org/10.1007/s11740-018-0854-8
[12] H. Bargaoui, F. Azzouz, D. Thibault, G. Cailletaud, Thermomechanical behavior of resin bonded foundry sand cores during casting. J. Mater. Process. Technol. 246, 30-41 (2017). https://doi.org/10.1016/j.jmatprotec.2017.03.002
[13] C. Menet, P. Reynaud, G. Fantozzi, D. Thibault, A. Laforêt, Thermomechanical properties and fracture of resin-bonded-sand cores – experimental study and application in aluminium foundry. EPJ Web Conf. 140, 08006 (2017). https://doi.org/10.1051/epjconf/201714008006
[14] P. Lechner, J. Stahl, F. Ettemeyer, B. Himmel, B. Tananau-Blumenschein, W. Volk, Fracture statistics for inorganically-bound core materials. Materials (Basel) 11, 2306 (2018). https://doi.org/10.3390/ma11112306
[15] J.T. Fox, F.S. Cannon, N.R. Brown, H. Huang, J.C. Furness, Comparison of a new, green foundry binder with conventional foundry binders. Int. J. Adhes. Adhes. 34, 38–45 (2012). https://doi.org/10.1016/j.ijadhadh.2011.11.011
[16] A. Bobrowski, S. Żymankowska-Kumon, K. Kaczmarska, D. Drożyński, B. Grabowska, Studies on the gases emission of moulding and core sands with an inorganic binder containing a relaxation additive. Arch. Foundry Eng. (2020). https://doi.org/10.24425/afe.2020.131296
[17] K. Major-Gabryś, Environmentally friendly foundry molding and core sands. J. Mater. Eng. Perform. 28, 3905–3911 (2019). https://doi.org/10.1007/s11665-019-03947-x
[18] M. Holtzer, R. Dańko, A. Kmita, D. Drożyński, M. Kubecki, M. Skrzyński, A. Roczniak, Environmental impact of the reclaimed sand addition to molding sand with furan and phenol-formaldehyde resin—a comparison. Materials (Basel) 13, 4395 (2020). https://doi.org/10.3390/ma13194395
[19] Y.S. Zhang, L. Xia, J. Huang, Study on a new inorganic binder for fabricating casting mold and core. Adv. Mater. Res. 287–290, 1603–1606 (2011)
[20] W. Liu, T. Wang, Y. Li, Y. Ren, W. Huo, Preparation of a new animal glue binder for foundry use. China Foundry. 13, 238–242 (2016). https://doi.org/10.1007/s41230-016-6029-3
[21] K. Major-Gabrys, A. Grabarczyk, M. Dobosz, Modification of foundry binders by biodegradable material. Arch. Foundry Eng. 18, 31-34 (2018). https://doi.org/10.24425/122498
[22] I. Vasková, L. Varga, I. Prass, V. Dargai, M. Conev, M. Hrubovčáková, M. Bartošová, B. Bul'ko, P. Demeter, Examination of behavior from selected foundry sands with alkali silicate-based inorganic binders. Metals (Basel) 10, 235 (2020). https://doi.org/10.3390/met10020235
[23] L. Song, W. Liu, F. Xin, Y. Li, Effect of silica fume on humidity resistance of sodium silicate binder for core-making process. Int. J. Met. 14, 977–986 (2020). https://doi.org/10.1007/s40962-019-00405-1
[24] L. Zaretskiy, Modified silicate binders new developments and applications. Int. J. Met. 10, 88–99 (2016). https://doi.org/10.1007/s40962-015-0005-3
[25] J. Weise, J. Hilbers, F. Handels, D. Lehmhus, M. Busse, M. Heuser, New core technology for light metal casting. Adv. Eng. Mater. 21, 1800608 (2019). https://doi.org/10.1002/adem.201800608
[26] L. Zaretskiy, Hydrous solid silicates in new foundry binders. Int. J. Met. 12, 275–291 (2018). https://doi.org/10.1007/s40962-017-0155-6
[27] T. Sivarupan, M. El Mansori, N. Coniglio, M. Dargusch, Effect of process parameters on flexure strength and gas permeability of 3D printed sand molds. J. Manuf. Process. 54, 420–437 (2020). https://doi.org/10.1016/j.jmapro.2020.02.043
[28] L. Song, W. Liu, Y. Li, F. Xin, Humidity-resistant inorganic binder for sand core making in foundry practice. China Foundry 16, 267–271 (2019). https://doi.org/10.1007/s41230-019-8169-8
[29] F. Liu, Z. Fan, X. Liu, H. Wang, J. He, Research on humidity resistance of sodium silicate sand hardened by twice microwave heating process. Mater. Manuf. Process. 29, 184–187 (2014). https://doi.org/10.1080/10426914.2013.872260
[30] F. Liu, Z. Fan, X. Liu, Y. Huang, P. Jiang, Effect of surface coating strengthening on humidity resistance of sodium silicate bonded sand cured by microwave heating. Mater. Manuf. Process. 31, 1639–1642 (2016). https://doi.org/10.1080/10426914.2015.1117631
[31] Z. Chun-Xi, Recent advances in waterglass sand technologies. China Foundry 4, 13–17 (2007)
[32] J.F. Allen, F.S. Cannon, C. Nieto-Delgado, R.C. Voigt, J.T. Fox, J. Lamonski, J.D. Kirby, Full-scale air emissions monitoring and casting quality demonstration of a hybrid hydrolyzed collagen-alkali silicate core binder. Int. J. Met. 10, 172–189 (2016). https://doi.org/10.1007/s40962-016-0021-y
[33] J.T. Fox, J.F. Allen, F.S. Cannon, C.C. Cash, R.C. Voigt, J.A. DeVenne, J.C. Furness, J.S. Lamonski, P. Farver, Full-scale demonstration of a hybrid hydrolyzed collagen-alkali silicate core binder. Int. J. Met. 9, 51-61 (2015). https://doi.org/10.1007/BF03355623
[34] X.J. Li, Z.T. Fan, H.F. Wang, Strength and humidity resistance of sodium silicate sand by ester-microwave composite curing. Zhuzao/Foundry 61, 147–151 (2012)
[35] M. Stachowicz, K. Granat, Long-term effects of relative humidity on properties of microwave hardened moulding sand with sodium silicate. Arch. Foundry Eng. (2017). https://doi.org/10.1515/afe-2017-0104
[36] C. Lustig, M. Baldy, E. Müller, M.L. Reinold, S.M. Anderten, M. Schweinefuß, R. Vargovic, Method for producing a moulding material mixture and a moulded body thereof in the casting industry and kit for use in this method. US 2020/0130049 A1, (2020)
[37] T. Pabel, C. Kneißl, P. Schumacher, J. Brotzki, J. Müller, Improved properties of aluminium cast parts through the use of inorganic cores. Foundry Trade J. Int. 186, 257-261 (2012)
[38] N. Ünlü, A. Odabaş, Development and evaluation of a new eco-friendly sodium silicate-based binder system. Int. J. Met. 12, 765–771 (2018). https://doi.org/10.1007/s40962-018-0210-y
[39] K. Lochte, The inorganic binder system properties and experience. Cast. Plant Technol. Int. 21(32), 6 (2005)
[40] J. Peng, X. Tang, J. He, D. Xu, Effect of heat treatment on microstructure and tensile properties of A356 alloys. Trans. Nonferrous Met. Soc. China 21, 1950–1956 (2011). https://doi.org/10.1016/S1003-6326(11)60955-2
[41] J. Pezda, A. Jarco, Effect of T6 heat treatment parameters on technological quality of the AlSi7Mg alloy. Arch. Foundry Eng. 16, 95–100 (2016). https://doi.org/10.1515/afe-2016-0091
[42] J. Pezda, Influence of heat treatment parameters on the mechanical properties of hypoeutectic al-si-mg alloy. Metalurgija. 53, 221–224 (2014)
[43] F. Xin, W. Liu, L. Song, Y. Li, Modification of inorganic binder used for sand core-making in foundry practice. China Foundry 17, 341–346 (2020). https://doi.org/10.1007/s41230-020-0018-2
[44] P. Jelínek, H. Polzin, R. Škuta, Utilization of physical dehydradion for hardening of cores bonded with colloidal solutions of alkaline silicates. Acta Metall. Slovaca. 10, 10–23 (2004)
[45] R. Krishnaraj, Control of pollution emitted by foundries. Environ. Chem. Lett. 13, 149–156 (2015). https://doi.org/10.1007/s10311-015-0500-z
[46] D.K. Ghosh, Comparison of molding sand technology between alphaset (ApNB) and furan (FNB). Arch. Foundry Eng. (2019). https://doi.org/10.24425/afe.2019.129623
9. Copyright:
This material is A. Fortini, M. Merlin, G. Raminella's paper: Based on A COMPARATIVE ANALYSIS ON ORGANIC AND INORGANIC CORE BINDERS FOR A GRAVITY DIECASTING AL ALLOY COMPONENT.
Paper Source: https://doi.org/10.1007/s40962-021-00628-1
This material was summarized based on the above paper, and unauthorized use for commercial purposes is prohibited.
Copyright © 2025 CASTMAN. All rights reserved.