This article introduces the paper ['50 Years of Foundry-Produced Metal Matrix Composites and Future Opportunities'] published by ['Springer'].
1. Overview:
- Title: 50 Years of Foundry-Produced Metal Matrix Composites and Future Opportunities
- Author: P. Ajay Kumar, Pradeep Rohatgi & David Weiss
- Publication Year: 2019
- Publishing Journal/Academic Society: International Journal of Metalcasting, Official Journal of the WFO World Foundry Organization(WFO)
- Keywords: metal matrix composites, hybrid MMC, functionally graded materials, stir casting, nano MMC, foundry
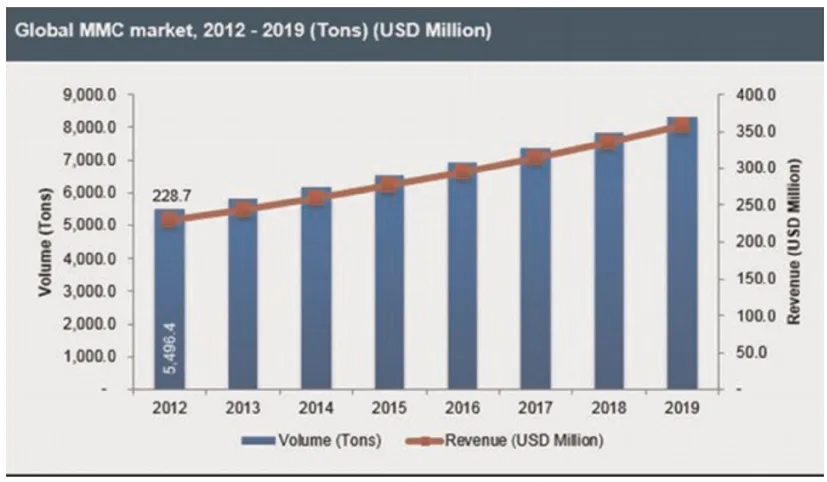
2. Abstracts or Introduction
This paper, commemorating the Golden Anniversary of the 1969 AFS paper "Dispersion of Graphite Particles in Aluminum Castings through Injection of the Melt," provides a comprehensive review of the advancements in cast metal matrix composites (MMCs) over the past 50 years. It elucidates the property motivations, current applications in sectors such as automotive, railways, space, computer hardware, and recreational equipment, and the status of the MMC industry, including production volumes and key manufacturers. The paper delves into specific cast MMCs, encompassing aluminum-graphite, aluminum-silicon carbide, aluminum-alumina, and aluminum-fly ash composites. Furthermore, it explores contemporary and prospective trends in cast MMCs, including the fabrication of foundry-produced nanocomposites, functionally gradient materials, syntactic foams, self-healing, and self-lubricating composites. Recent strides in developing lightweight self-lubricating cylinder liners for compressors, pistons, and rotary engines, utilizing Al-graphite and Al-graphite-SiC composites, are also discussed. The paper concludes by presenting future prospects for foundry-produced MMCs.
3. Research Background:
Background of the Research Topic:
The escalating demand for lightweight, high-performance, and recyclable materials across diverse applications has positioned Metal Matrix Composites (MMCs) as pivotal engineered materials. MMCs offer superior alternative solutions by integrating two or more materials, with a metallic element as a matrix. These materials have successfully substituted conventional materials in critical sectors, including aerospace, automotive, and defense. Metal matrix composites generally comprise continuous or discontinuous fibers, whiskers, or particulates, uniformly dispersed within a metallic alloy matrix. These reinforcements are instrumental in endowing the composite with enhanced properties that are unattainable in monolithic alloys.
Status of Existing Research:
According to the Global MMC Market Report 2019, the MMC production sector has experienced consistent linear growth. MMC production volume has increased from 5 million kilograms to 7 million kilograms post-2012, with revenue escalating from 228.8 USD million to 400 USD million (Figure 1). In 2004, 3.5 million kilograms of MMCs were utilized, and this figure continues to rise at an annual growth rate exceeding 6%. Concurrently, publications on MMCs have shown exponential growth, as depicted in Figure 2. Cast metal matrix composites are extensively produced within the foundry industry. An Al-Si alloy exemplifies an in situ composite, formed through the solidification of a liquid solution of silicon in aluminum, dictated by their phase diagram (Figure 3a). Ductile cast iron (Figure 3b), where graphite nodules are dispersed in a ferrite matrix, represents another common foundry composite. This paper distinguishes itself by focusing on synthetically produced composites, contrasting them with phase diagram-restricted composites.
Necessity of the Research:
Phase diagram-restricted composites, such as Al-Si alloys and ductile cast iron, are inherently limited in the achievable volume percentages of their constituent phases and are confined to narrow compositional ranges dictated by their phase diagrams. The morphology and spatial arrangement of reinforcements in these materials are not as freely modifiable as in synthetically produced composites. Synthetically produced composites, the primary focus of this paper, offer the flexibility to manipulate chemistry, shape, volume percentage, and distribution of second-phase reinforcements, thereby overcoming the limitations inherent in phase diagram-restricted composites.
4. Research Purpose and Research Questions:
Research Purpose:
This paper aims to review the advancements in cast Metal Matrix Composites (MMCs) over the 50 years following the seminal 1969 AFS paper. It seeks to elucidate the motivations behind employing MMCs, examine their current applications, and explore future directions in their development and foundry production. The study also intends to highlight the prospects for future foundry-produced MMCs.
Key Research:
The key research areas addressed in this paper include:
- A comprehensive review of the progress in cast MMCs over the last half-century.
- An analysis of the property motivations driving the use of MMCs and their current applications across various industries.
- An exploration of current and emerging trends in cast MMC technology, including nanocomposites and functionally graded materials.
- An assessment of the future prospects and opportunities for foundry-produced MMCs.
Research Hypotheses:
While not explicitly stated as formal hypotheses, the paper implicitly operates under the premise that:
- Significant advancements have been achieved in cast MMC technology and applications since 1969.
- The superior properties of MMCs, compared to monolithic alloys, are the primary drivers for their increasing adoption across diverse sectors.
- Foundry processes are adaptable and scalable for the cost-effective production of advanced MMCs, including nanocomposites and other sophisticated composite systems.
- Substantial future opportunities exist for expanding the role of foundry-produced MMCs in meeting evolving engineering material demands.
5. Research Methodology
Research Design:
The research employs a review-based design, synthesizing existing literature and industry reports to chart the evolution of cast Metal Matrix Composites (MMCs) over a 50-year period. This approach involves a historical analysis of MMC development, focusing on key milestones, technological advancements, and application trends.
Data Collection Method:
Data collection was primarily conducted through an extensive review of scholarly literature, encompassing research papers, industry-specific reports, and patents related to cast MMCs. Market data, notably from the Global MMC Market Report 2019, was also utilized to assess industry trends and growth. Publications from AFS Transactions and other relevant sources were consulted to gather comprehensive information on MMC processing, properties, and applications.
Analysis Method:
The analysis is predominantly qualitative, focusing on identifying and interpreting trends in MMC research, development, and industrial applications. Descriptive analysis is used to categorize MMC types, processing methodologies, and property enhancements. The synthesis of findings from the literature review facilitates the identification of key advancements, current challenges, and future directions within the field of cast MMCs.
Research Subjects and Scope:
The research subject is broadly defined as Cast Metal Matrix Composites (MMCs), with a specific focus on those produced via foundry techniques. The scope of the review spans a 50-year period, from 1969 to 2019, tracing the technological and application landscape of these materials. The study encompasses various industries utilizing MMCs, including but not limited to automotive, railways, aerospace, computer hardware, and recreational equipment, providing a holistic view of the field's development and impact.
6. Main Research Results:
Key Research Results:
The review highlights a consistent linear growth in the Metal Matrix Composites (MMC) market, paralleled by an exponential surge in related publications, underscoring the field's expanding research and industrial interest. MMCs are categorized based on reinforcement morphology, primarily into fiber-reinforced and particle-reinforced composites, each offering distinct property profiles. Stir casting is identified as a prevalent and economically viable method for MMC manufacturing. Significant progress in aluminum-graphite composites has been noted, particularly for self-lubricating applications. The development and application of MMC components span diverse sectors, notably automotive and aerospace, showcasing their versatility. Advancements in sophisticated MMC systems, such as nanocomposites and syntactic foams, represent cutting-edge developments. The study also delineates critical research imperatives essential for the future progression of cast MMCs, focusing on overcoming existing limitations and capitalizing on emerging opportunities.
Analysis of presented data:
- Figure 1: "Global MMC Market review 2019.3" illustrates a linear progression in both MMC volume and revenue, indicating steady market expansion.
- Figure 2: "Number of papers on cast MMCs published from 1988 to 2018.3" demonstrates an exponential increase in publications, reflecting heightened research activity.
- Figure 4: "Classification of metal matrix composites depending on size, arrangement, and shape of the reinforcement" provides a schematic categorization of MMCs based on reinforcement characteristics.
- Figure 5: "Cost and type of reinforcements used in MMCs.2" outlines the cost-effectiveness of different reinforcement types in relation to MMC production.
- Figure 9: "Examples of aluminum-graphite MMC components" showcases practical applications of these composites, particularly in automotive engineering.
- Table 1: "Selected Matrix-Dispersoid Combinations Used to Make Cast Metal Matrix Composites" lists various material combinations and their proportions in MMC synthesis.
- Table 2: "Selected Landmarks in the Development of Cast Metal Matrix Composites During 1965–2018" chronologically presents significant milestones in MMC research and development.
- Table 3: "List of MMC Uses in Different Sectors" enumerates diverse applications of MMCs across various industries.
- Table 4: "List of MMC Manufacturers and Use of MMCs in Automotive Application" details key industry players and their specific applications of MMCs in the automotive sector.
- Table 5: "Comparative Analysis of Cylinder Sleeve Materials" provides a comparative assessment of different materials used for cylinder sleeves, including MMCs.
Figure Name List:
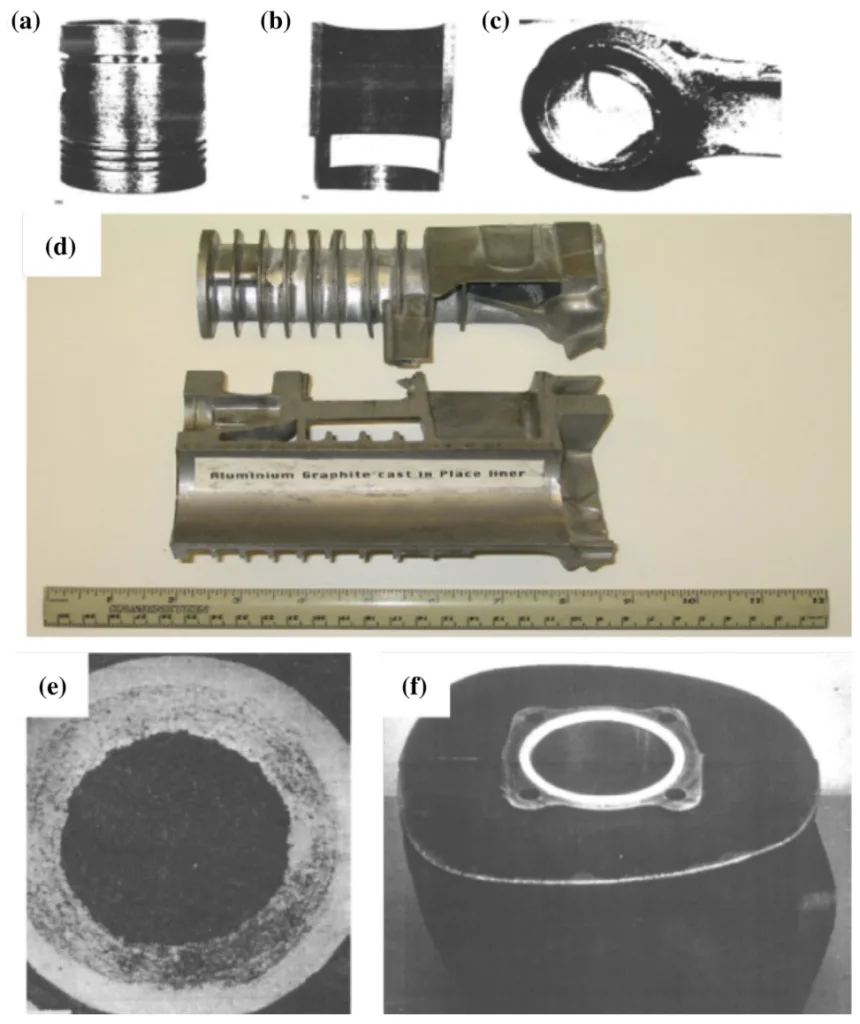
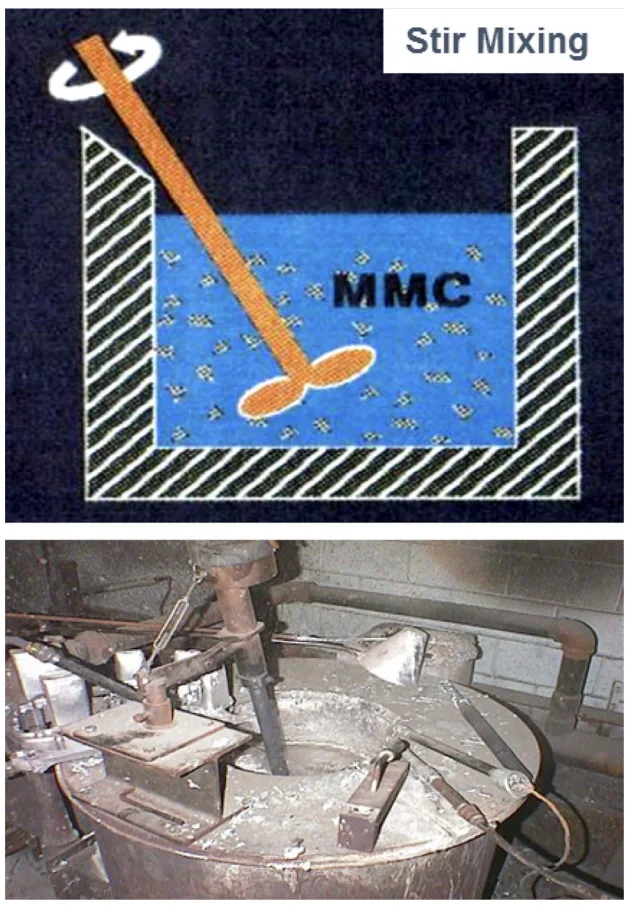
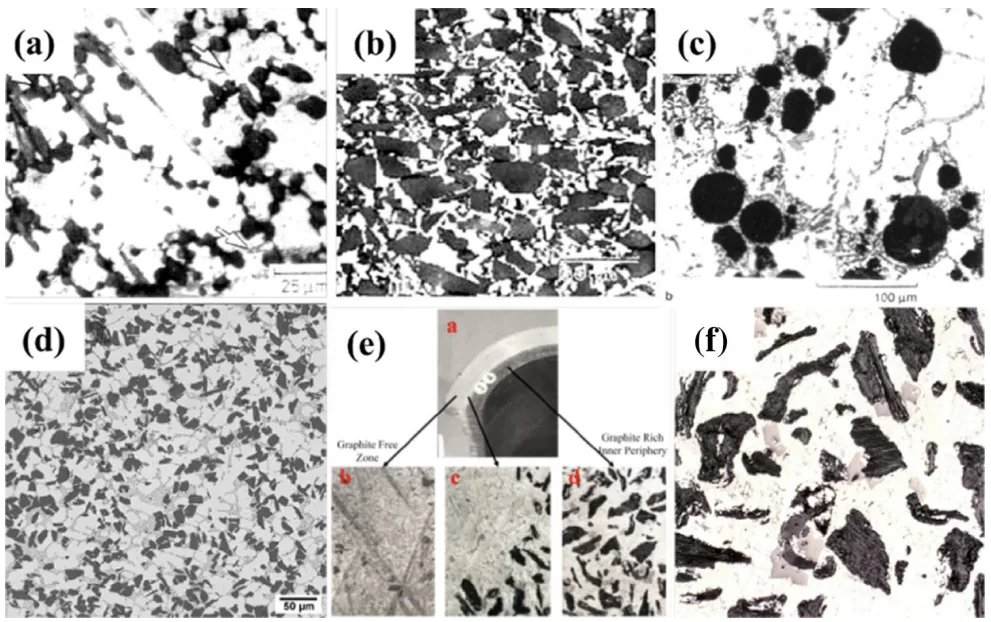
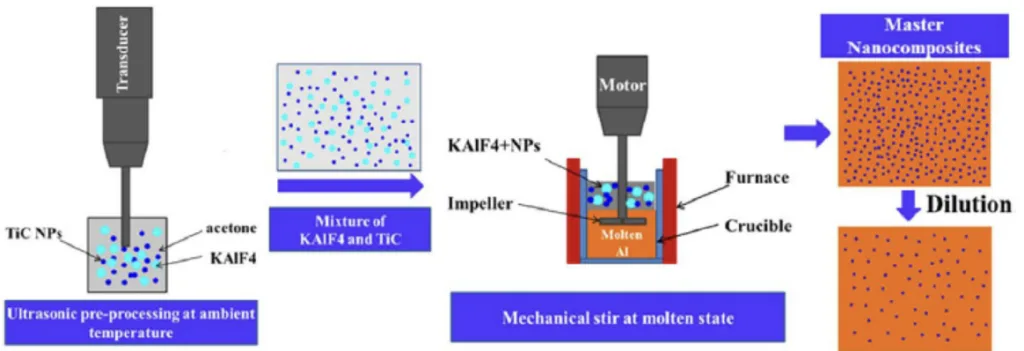
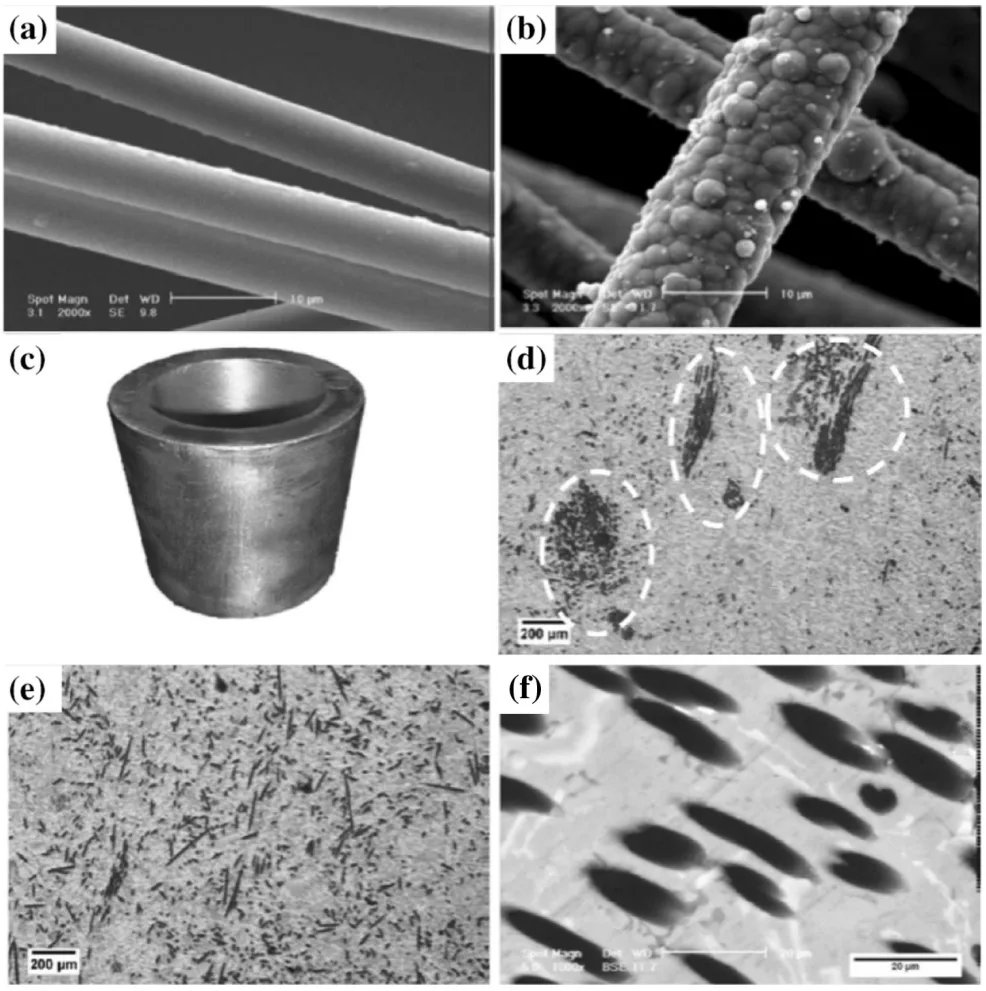
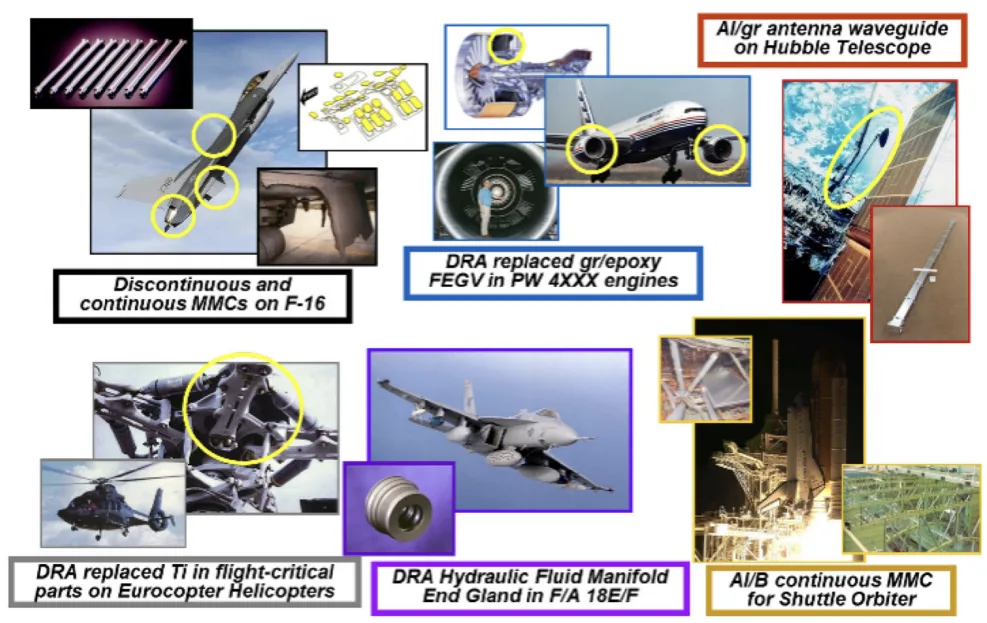
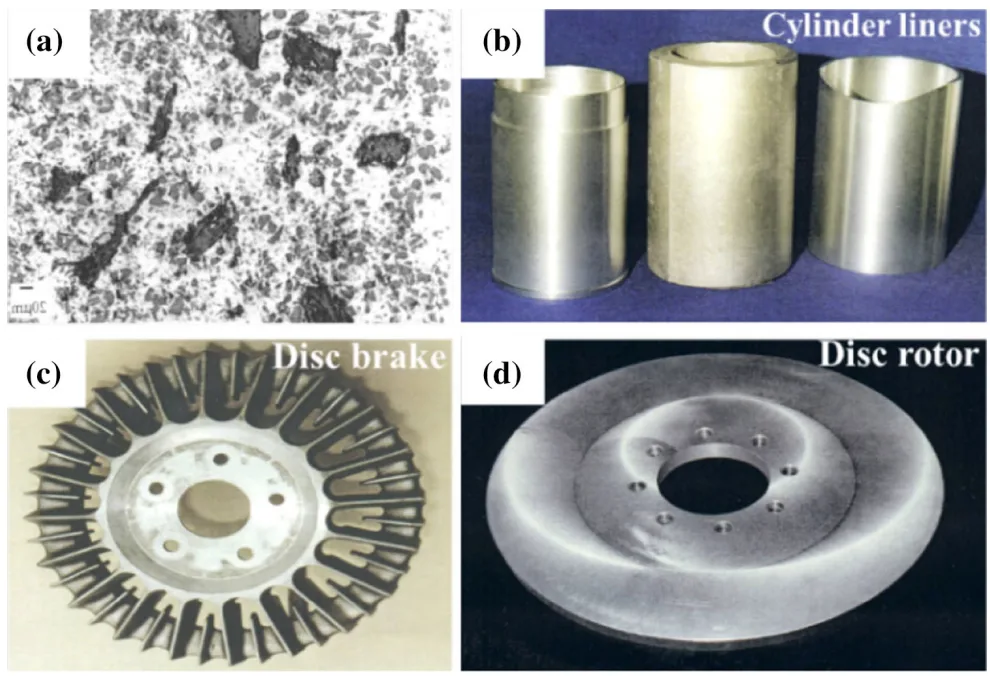
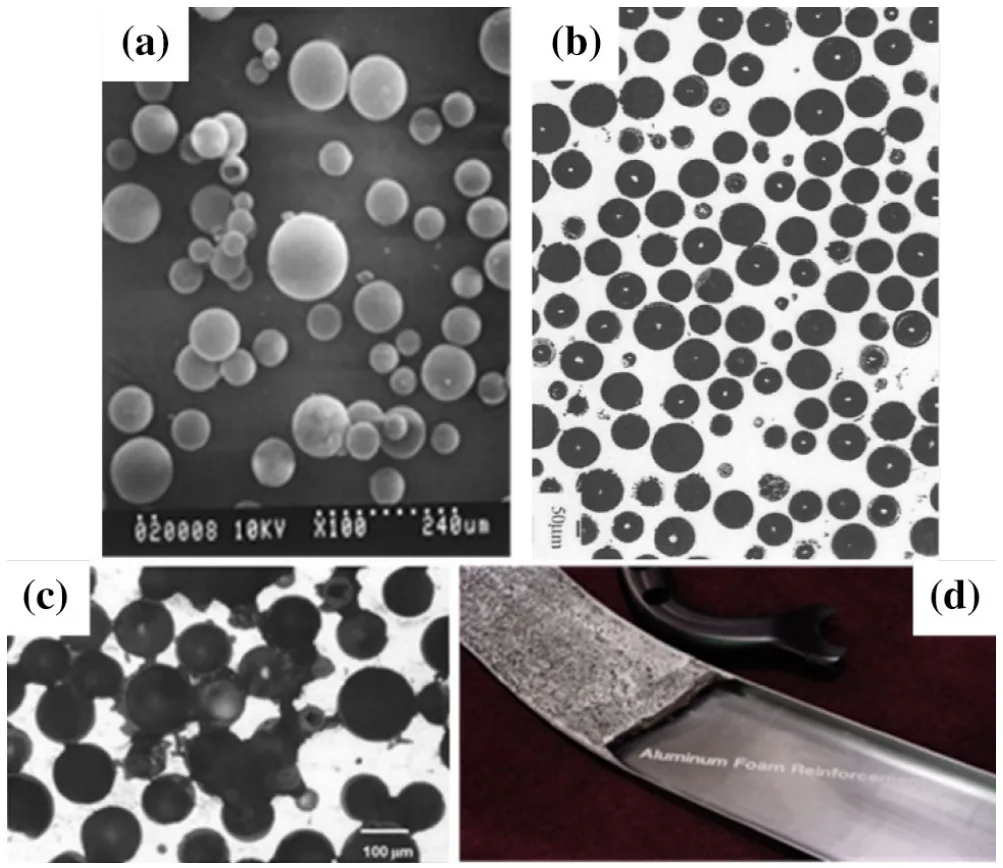
- Figure 1. Global MMC Market review 2019.3
- Figure 2. Number of papers on cast MMCs published from 1988 to 2018.3
- Figure 3. Phase diagram restricted metal composites (a) Al-Si alloy, and (b) ductile cast iron.2
- Figure 4. Classification of metal matrix composites depending on size, arrangement, and shape of the reinforcement.
- Figure 5. Cost and type of reinforcements used in MMCs.2
- Figure 6. Injection of nickel-coated graphite in molten aluminum alloys in an initial experiment on casting aluminum-graphite particle composites by Rohatgi. (Merica Laboratory, International Nickel Company, 1965).6
- Figure 7. Injection of nickel-coated graphite in molten aluminum alloys in an initial experiment on casting aluminum-graphite particle composites by Badia. (Merica Laboratory, International Nickel Company, 1965).6
- Figure 8. Dispersion of graphite particles in an AI-9.2Si-4.7Ni-base.6
- Figure 9. (a) Aluminum-graphite piston, (b) aluminum-graphite liners used in Alpha Romeo and Ferrari automobiles in Formula One races, (c) aluminum-graphite connecting rod, (d) aluminum-graphite liner die cast in place, in a small engine, (e) centrifugally cast aluminum-graphite liner, (f) liner from a small engine block.2
- Figure 10. Schematic views of the stir casting process.
- Figure 11. (a) microstructure of Al-Si/Saffil fiber, (b) A356/SiC composites, (c)Al-Si/20 vol% spherical Al2O3p, (d)silicon carbide particle-reinforced aluminum composite, and (e-f) Al-Si/20 vol%-graphite particle composite.2
- Figure 12. SEM micrographs of as-cast composites: (a, b) Al6061-9 wt%. TiB2.59
- Figure 13. (a) Schematic diagram of the rheoformed die of the 7075 AMCs reinforced with nano-sized particles, (b) Schematic diagram of the deformation of the semisolid slurries during the rheoforming process, (c) A cylindrical part drawing and three dimension model of the rheoformed part of the 7075 AMCs reinforced with nano-sized particles, (d) real product of the rheoformed die of the 7075 AMCs reinforced with nano-sized particles (e) Macrographs of inside surface of the rheoformed cylindrical parts of the 7075 AMCs reinforced with nano-sized SiC particles. 61
- Figure 14. Schematic of the casting experimental setup used by Li57
- Figure 15. (a) High magnification SEM image from Mg-TiC nanocomposites and (b) microhardness measurements with varying amount of TiC in the matrix.57
- Figure 16. Schematic of the solidification nanoprocessing method. The nanoparticles were first ultrasonic preprocessed with molten salt at room temperature and then incorporated into molten Al assisted by molten salt and mechanical stir.57
- Figure 17. Schematic of the experimental methods.58
- Figure 18. SEM images of the WC nanoparticle dispersion in zinc.58
- Figure 19. Experimental setup of (a) salt-assisted nanoparticle incorporation and (b) melt pressing using a hydraulic press.52
- Figure 20. SEM micrograph of carbon short fibers used, (a) uncoated, (b) Ni-P coated, (c) picture an as-cast sample, (d) distribution of uncoated CSFs in composite C3 samples, (e) distribution of coated CSFs in composite CE3 samples, and (f) SEM micrograph of an agglomerated fiber region in sample CE3.54
- Figure 21. Formation of the composite during non-isothermal infiltration of a fiber preform by liquid metal.
- Figure 22. Schematic of Advanced Pressure Infiltration Casting (APICTM) Process. 68
- Figure 23. Physical and mechanical properties of composites as compared with the two most commonly used alloys, i.e., steel and aluminum.
- Figure 24. Comparison of specific properties of aluminum and magnesium matrix composites indicating the increase in stiffness and strength with respect to the matrix.
- Figure 25. MMC uses in automotive applications as cylinder liners, brake rotors, intake and exhaust valves, and driveshaft, etc.
- Figure 26. A359/20 vol%-SiCp composite brake rotor for an electric vehicle
- Figure 27. Al-SiC composites as heat-spreader plates of an electronics cooling device for the world's first hybrid vehicle, the PRIUS.
- Figure 28. MMC crankshaft pulley made by infiltration of SIALON preform with aluminum.
- Figure 29. REL AI-MMC for (a) brake drum, (b) motorcycle brake rotor, and (c) automotive rotor.
- Figure 30. Al-SiC-graphite piston cylinder made by Eck Industries.
- Figure 31. MMC uses in space industries.
- Figure 32. Discontinuously reinforced aluminum MMCS for electronic packaging applications: (a-top) SiCp/Al electronic package for a remote power controller (photo courtesy of Lockheed Martin Corporation), and (b-bottom) cast Grp/Al components (photo courtesy of MMCC, Inc.).
- Figure 33. Train rotor made from Duralcan.
- Figure 34. Montage of lead-free copper-graphite composite castings.
- Figure 35. A356–10 vol%SiC-4 vol%Gr composite components.
- Figure 36. (a) Microstructure of A356-10 vol% fly ash composite. (b) Intake manifold made of Al-10% fly ash.
- Figure 37. Foam material created by introducing gas in Al-SiC melt.
- Figure 38. (a) Fly ash cenospheres, (b) fly ash cenospheres (hollow) in a-Al matrix (c) Al foam (d) aluminum-fly ash cenosphere syntactic foam (micrograph inset) within a steel frame. Courtesy of Bob Purgert.
7. Conclusion:
Summary of Key Findings:
The extensive review of cast Metal Matrix Composites (MMCs) over five decades reveals substantial progress, marked by linear market growth and an exponential increase in research publications. MMCs have proven to be versatile materials, offering tailored properties for a wide array of applications, particularly in the automotive and aerospace sectors. Foundry processes, including stir casting, squeeze casting, and infiltration techniques, are pivotal in the cost-effective manufacturing of MMCs. The field is continuously evolving, with significant advancements in sophisticated MMC systems such as nanocomposites, syntactic foams, and self-lubricating composites. Future research and development are crucial to address key imperatives, including cost reduction, enhancing machinability, establishing comprehensive material databases, and developing efficient recycling methods to fully realize the potential of cast MMCs.
Academic Significance of the Study:
This study provides a valuable academic contribution through its comprehensive historical review of cast MMC development, offering a structured overview of the field's evolution over 50 years. It synthesizes key research trends, processing methodologies, and application domains, serving as a consolidated resource for researchers and industry professionals. By identifying future research directions and challenges, the paper stimulates further academic inquiry and technological innovation in materials science and engineering.
Practical Implications:
The practical implications of this review are significant for industries seeking advanced material solutions. It underscores the potential of cast MMCs to meet demanding performance criteria in sectors like automotive and aerospace, offering pathways for enhanced component design and manufacturing. The insights into cost-effective foundry processes for MMC production are particularly relevant for industrial scalability. The paper encourages the broader adoption of MMCs in commercial applications by highlighting their benefits and addressing existing limitations, thereby fostering innovation and market growth.
Limitations of the Study and Areas for Future Research:
As a review paper, this study is inherently limited by its reliance on existing literature and does not introduce new experimental data. Future research should prioritize addressing the identified imperatives for the field's advancement. Key areas for future investigation include: reducing MMC production costs, improving machinability to facilitate wider industrial adoption, creating robust material databases to support component design, and developing effective recycling technologies for sustainable MMC utilization. Furthermore, research should focus on the next generation of MMCs, such as graphene-reinforced composites and self-healing materials, alongside large-scale performance testing and standardization efforts to ensure reliability and consistency in MMC component applications.
8. References:
- 1. P.K. Rohatgi, B.C. Pai, S.C. Panda, Preparation of cast aluminum-silica particulate composites. J. Mater. Sci. (UK) 14, 2277-2283 (1979)
- 2. P. Rohatgi, Cast metal matrix composites: past, present, and future, in Transactions of the American Foundry Society and the One Hundred Fifth Annual Castings Congress, 2001, pp. 1-25
- 3. Metal Matrix Composites (MMC) Market for Ground Transportation, Electronics/Thermal Management, Aerospace, and Other End-users-Global Industry Analysis, Size, Share, Growth, Trends and Forecast, 2013-2019
- 4. M.K. Surappa, P.K. Rohatgi, Preparation and properties of cast Al-alloy-ceramic particulate composites. J. Mater. Sci. (UK) 16(4), 983–993 (1981)
- 5. R. Mehrabian, A. Sato, M.C. Flemings, Cast composites of aluminum alloys. Light Met. 1975, 2 (1975)
- 6. F.A. Badia, P.K. Rohatgi, Dispersion of graphite particles in aluminum castings through injection of the melt. Trans. AFS 76, 402-406 (1969)
- 7. T.P.D. Rajan, R.M. Pillai, B.C. Pai, K.G. Satyanarayana, P.K. Rohatgi, Fabrication and characterization of Al-7Si-0.35 Mg/fly ash metal matrix composites processed by different stir casting routes. Compos. Sci. Technol. 67, 3369–3377 (2007)
- 8. M.R. Madhava, S. Raman, P.K. Rohatgi, M.K. Surappa, Influence of certain microstructural parameters on the ultrasonic velocities and elastic constants of aluminum alumina particulate composites. Scr. Metall (USA) 15, 1191-1195 (1981)
- 9. D. Nath, P.K. Rohatgi, Cast aluminum alloy composites containing copper coated ground mica particles. J. Mater. Sci. (UK) 16(6), 1599–1606 (1981)
- M.K. Surappa, S.V. Prasad, P.K. Rohatgi, Wear and abrasion characteristics of cast Al-alumina particle composites. Wear (UK) 77, 295–302 (1981)
- P.K. Rohatgi, S. Ray, P.K. Kelkar, Preparation of aluminum-alumina composite. Indian Patent 124305, 1972
- Rohatgi et al., Aluminum-silicon carbide; aluminum-Al2O3; aluminum-mica composite (IISc, Bangalore, 1974)
- A. Banerjee, P.K. Rohatgi, Cast aluminum alloy containing dispersions of titania and zirconia particles. J. Mater. Sci. (UK) 17(2), 335–342 (1982)
- M.D. Skibo, D.M. Schuster. Process for the production of metal matrix composites by casting and composite therefrom. U.S. Patent 4,759,995. Issued July 26, 1988
- M. Suwa, K. Komuro, Method of producing graphite-containing copper alloys. U.S. Patent 4,207,096. Issued June 10, 1980
- D. Rohatgi, Aluminum–Microballoon Syntactic Foam (AMPRI, Bhopal, 1984)
- Aluminum-TiC by X-D In-situ Process at Martin Marietta 1985
- A. Mortensen, M.N. Gungor, J.A. Cornie, M.C. Flemings, Alloy microstructures in cast metal matrix composites. JOM 38(3), 30–35 (1986)
- B.K. Prasad, T.K. Dan, P.K. Rohatgi, Pressure-induced improvement in interfacial bonding between graphite and the aluminum matrix in graphitic-aluminum particle composites. J. Mater. Sci. Lett. 6(9), 1076-1078 (1987)
- M.K. Aghajanian, J.T. Burke, D.R. White, A.S. Nagelberg, A new infiltration process for the fabrication of metal matrix composites. SAMPE Q. 20, 43-46 (1989)
- Honda, Al-Saffil/Alumina/Graphite Fiber Composite by Pressure Infiltration (Honda, Hamamatsu, 1992)
- T. Suganuma, Al/SiCp Brake Drum (Toyota, Toyota city, 1997)
- Al/SiCp Brake drum using stir casting for Volkswagen 1999
- T. Suganuma, Al-Al2O3/SiO3/Mullitep Composites for Toyota (Toyota, Toyota city, 2000)
- D.P. Robertson, M. Gajdardziska-Josifovska, J.K. Kim, R.Q. Guo, P.K. Rohatgi, Electron microscopy characterization of aluminum alloy-fly ash composites. Microsc. Microanal. 8(S02), 1278–1279 (2002)
- P.K. Rohatgi, P. Shukla, R.B. Thakkar, D. Weiss, Tensile and fatigue properties of permanent mold cast A359-SICp aluminum alloys. Afford. Met. Matrix Compos. High Perform. Appl. 2, 113-126 (2010)
- M. Kestursatya, J.K. Kim, P.K. Rohatgi, Wear performance of copper-graphite composite and a leaded copper alloy. Mater. Sci. Eng. A 339(1–2), 150-158 (2003)
- A. Daoud, M.T. Abou-Elkhair, P. Rohatgi, Wear and friction behavior of near eutectic Al-Si + ZrO2 or WC particle composites. Compos. Sci. Technol. 64(7-8), 1029–1040 (2004)
- Y. Yang, J. Lan, X. Li, Study on bulk aluminum matrix nano-composite fabricated by ultrasonic dispersion of nano-sized SiC particles in molten aluminum alloy. Mater. Sci. Eng. A 380(1–2), 378-383 (2004)
- S. Naher, D. Brabazon, L. Looney, Development and assessment of a new quick quench stir caster design for the production of metal matrix composites. J. Mater. Process. Technol. 166(3), 430–439 (2005)
- P.K. Rohatgi, J.K. Kim, N. Gupta, S. Alaraj, A. Daoud, Compressive characteristics of A356/fly ash cenosphere composites synthesized by pressure infiltration technique. Compos. Part A Appl. Sci. Manuf. 37(3), 430-437 (2006)
- H.G. Seong, H.F. Lopez, M. Gajdardziska-Josifovska, P.K. Rohatgi, Nucleation effects in thermally managed graphite fiber-reinforced Al-Cu and Al-Si composites. Metall. Mater. Trans. A 38(11), 2796–2804 (2007)
- A. Daoud, M.T. Abou El-Khair, M. Abdel-Aziz, P. Rohatgi, Fabrication, microstructure and compressive behavior of ZC63 Mg-microballoon foam composites. Compos. Sci. Technol. 67(9), 1842–1853 (2007)
- H. Uozumi, K. Kobayashi, K. Nakanishi, T. Matsunaga, K. Shinozaki, H. Sakamoto, T. Tsukada, C. Masuda, M. Yoshida, Fabrication process of carbon nanotube/light metal matrix composites by squeeze casting. Mater. Sci. Eng., A 495(1–2), 282–287 (2008)
- P.K. Rohatgi, B.F. Schultz, A. Daoud, W.W. Zhang, Tribological performance of A206 aluminum alloy containing silica sand particles. Tribol. Int. 43(1–2), 455-466 (2010)
- B.F. Schultz, J.B. Ferguson, P.K. Rohatgi, Microstructure and hardness of Al2O3 nanoparticle reinforced Al-Mg composites fabricated by reactive wetting and stir mixing. Mater. Sci. Eng., A 530, 87-97 (2011)
- C. Borgonovo, M.M. Makhlouf, Synthesis of die-castable nano-particle reinforced aluminum matrix composite materials by in situ gas-liquid reactions. Metall. Sci. Technol. 30(1) (2012)
- L. Ivanchev, S.T. Camagu, G. Govender, Semi-solid high pressure die casting of metal matrix composites produced by liquid state processing, in Solid State Phenomena, vol. 192, ed. by R. Lawrance, R.K. Maynard (Trans Tech Publications, Zurich, 2013), pp. 61-65
- G.A.R. Rivero, B.F. Schultz, J.B. Ferguson, N. Gupta, P.K. Rohatgi, Compressive properties of Al-A206/SiC and Mg-AZ91/SiC syntactic foams. J. Mater. Res. 28(17), 2426-2435 (2013)
- J.A. Santa Maria, B.F. Schultz, J.B. Ferguson, P.K. Rohatgi, Al-Al2O3 syntactic foams-part I: effect of matrix strength and hollow sphere size on the quasi-static properties of Al-A206/Al2O3 syntactic foams. Mater. Sci. Eng. A 582, 415–422 (2013)
- J.B. Ferguson, J.A. Santa Maria, B.F. Schultz, P.K. Rohatgi, Al-Al2O3 syntactic foams-part II: predicting mechanical properties of metal matrix syntactic foams reinforced with ceramic spheres. Mater. Sci. Eng. A 582, 423–432 (2013)
- M.F. Ibrahim, A.M. Samuel, M.S. Soliman, H.R. Ammar, F.H. Samuel, A new technology for the production of Al-B4C metal matrix composites. Trans. AFS Trans. 121, 99–110 (2013)
- L.-Y. Chen, D. Weiss, J. Morrow, X. Jia-Quan, X.-С. Li, A novel manufacturing route for the production of high-performance metal matrix nanocomposites. Manuf. Lett. 1(2-4), 62-65 (2013)
- M. Estruga, L. Chen, H. Choi, X. Li, S. Jin, Ultrasonic-assisted synthesis of surface-clean TiB2 nanoparticles and their improved dispersion and capture in Al-matrix nanocomposites. ACS Appl. Mater. Interfaces 5(17), 8813–8819 (2013)
- J.A. Santa Maria, B.F. Schultz, J.B. Ferguson, N. Gupta, P.K. Rohatgi, Effect of hollow sphere size and size distribution on the quasi-static and high strain rate compressive properties of Al-A380-Al2O3 syntactic foams. J. Mater. Sci. 49(3), 1267–1278 (2014)
- P.K. Rohatgi, Al-shape memory alloy self-healing metal matrix composite. Mater. Sci. Eng. A 619, 73-76 (2014)
- M.R. Dehnavi, B. Niroumand, F. Ashrafizadeh, P.K. Rohatgi, Effects of continuous and discontinuous ultrasonic treatments on mechanical properties and microstructural characteristics of cast Al413-SiCnp nanocomposite. Mater. Sci. Eng. A 617, 73–83 (2014)
- J.B. Ferguson, I. Aguirre, H. Lopez, B.F. Schultz, K. Cho, P.K. Rohatgi, Tensile properties of reactive stir-mixed and squeeze cast Al/CuOnp-based metal matrix nanocomposites. Mater. Sci. Eng. A 611, 326-332 (2014)
- L. Xiaochun, Y. Yang, D. Weiss. Theoretical and experimental study on ultrasonic dispersion of nanoparticles for strengthening cast aluminum alloy A356. Metall. Sci. Technol. 26(2), 12-20 (2013)
- E. Omrani, A.D. Moghadam, M. Algazzar, P.L. Menezes, P.K. Rohatgi, Effect of graphite particles on improving tribological properties Al-16Si-5Ni-5Graphite self-lubricating composite under fully flooded and starved lubrication conditions for transportation applications. Int. J. Adv. Manuf. Technol. 87(1-4), 929-939 (2016)
- S.K. Pradhan, S. Chatterjee, A.B. Mallick, D. Das, A simple stir casting technique for the preparation of in situ Fe-aluminides reinforced Al-matrix composites. Perspect. Sci. 8, 529-532 (2016)
- W. Liu, C. Cao, X. Jiaquan, X. Wang, X. Li, Molten salt assisted solidification nanoprocessing of Al-TiC nanocomposites. Mater. Lett. 185, 392–395 (2016)
- A.D. Moghadam, E. Omrani, H. Lopez, L. Zhou, Y. Sohn, P.K. Rohatgi, Strengthening in hybrid alumina-titanium diboride aluminum matrix composites
- M. Baghi, B. Niroumand, R. Emadi, Fabrication and characterization of squeeze cast A413-CSF composites. J. Alloy. Compd. 710, 29–36 (2017)
- L. Pan, Y. Yang, M.U. Ahsan, D.D. Luong, N. Gupta, A. Kumar, P.K. Rohatgi, Zn-matrix syntactic foams: effect of heat treatment on microstructure and compressive properties. Mater. Sci. Eng. A 731, 413-422 (2018)
- Z. Guan, I. Hwang, X. Li, Highly concentrated WC reinforced Ag matrix nanocomposite manufactured by molten salt assisted stir casting. Procedia Manuf. 26, 146-151 (2018)
- A. Javadi, S. Pan, X. Li, Scalable manufacturing of ultra-strong magnesium nanocomposites. Manuf. Lett. 16, 23-26 (2018)
- I. Hwang, Z. Guan, X. Li, Scalable manufacturing of zinc-tungsten carbide nanocomposites. Procedia Manufacturing 26, 140–145 (2018)
- Y. Pazhouhanfar, B. Eghbali, Microstructural characterization and mechanical properties of TiB2 reinforced Al6061 matrix composites produced using stir casting process. Mater. Sci. Eng. A 710, 172-180 (2018)
- J. Jiang, Y. Wang, Microstructure and mechanical properties of the rheoformed cylindrical part of 7075 aluminum matrix composite reinforced with nano-sized SiC particles. Mater. Des. 79, 32–41 (2015)
- P.K. Rohatgi, J.K. Kim, N. Gupta, S. Alaraj, A. Daoud, Compressive characteristics of A356/fly ash cenosphere composites synthesized by pressure infiltration technique. Compos. Part A Appl. Sci. Manuf. 37, 430-437 (2006)
- A. Mortensen, V.J. Michaud, M.C. Flemings, Pressure-infiltration processing of reinforced aluminum. JOM 45(1), 36-43 (1993)
- E.M. Klier, A. Mortensen, J.A. Cornie, M.C. Flemings, Fabrication of cast particle-reinforced metals via pressure infiltration. J. Mater. Sci. 26(9), 2519-2526 (1991)
- A. Mortensen, L.J. Masur, J.A. Cornie, M.C. Flemings, Infiltration of fibrous preforms by a pure metal: part I. Theory. Metall. Trans. A 20(11), 2535–2547 (1989)
- C. McCullough, H.E. Deve, T.E. Channel, Mechanical response of continuous fiber-reinforced Al2O3- Al composites produced by pressure infiltration casting. Mater. Sci. Eng., A 189(1–2), 147–154 (1994)
- J. Yang, D.D.L. Chung, Casting particulate and fibrous metal-matrix composites by vacuum infiltration of liquid metal under inert gas pressure. J. Mater. Sci. 24(10), 3605–3612 (1989)
- M.K. Aghajanian, M.A. Rocazella, J. Tetal Burke, S.D. Keck, The fabrication of metal matrix composites by a pressureless infiltration technique. J. Mater. Sci. 26(2), 447-454 (1991)
- J. Cornie, Advanced pressure infiltration casting technology produces a near-absolute net-shape metal matrix composite components cost competitively. Mater. Technol. 10(3-4), 43-48 (1995)
- D.B. Miracle, Metal matrix composites-from science to technological significance. Compos. Sci. Technol. 65(15-16), 2526–2540 (2005)
- W.H. Hunt, D.B. Miracle. Automotive applications of metal-matrix composites. 2001
- A. Evans, C. San Marchi, A. Mortensen, Metal Matrix Composites in Industry: An Introduction and a Survey (Springer, Berlin, 2013)
- S.P. Rawal, Metal-matrix composites for space applications. JOM 53(4), 14–17 (2001)
- C. Zweben, Thermal Management and Electronic Packaging Applications (Materials Park, ASM International, 2001), pp. 1078–1084
- A. Macke, B.F. Schultz, P. Rohatgi, Metal matrix composites. Adv. Mater. Process. 170(3), 19-23 (2012)
9. Copyright:
- This material is "Ajay Kumar P., Pradeep Rohatgi & David Weiss"'s paper: Based on "50 Years of Foundry-Produced Metal Matrix Composites and Future Opportunities".
- Paper Source: DOI 10.1007/s40962-019-00375-4
This material was summarized based on the above paper, and unauthorized use for commercial purposes is prohibited.
Copyright © 2025 CASTMAN. All rights reserved.