This introduction paper is based on the paper "3W SFP Interface Development" published by Metropolia University of Applied Sciences.
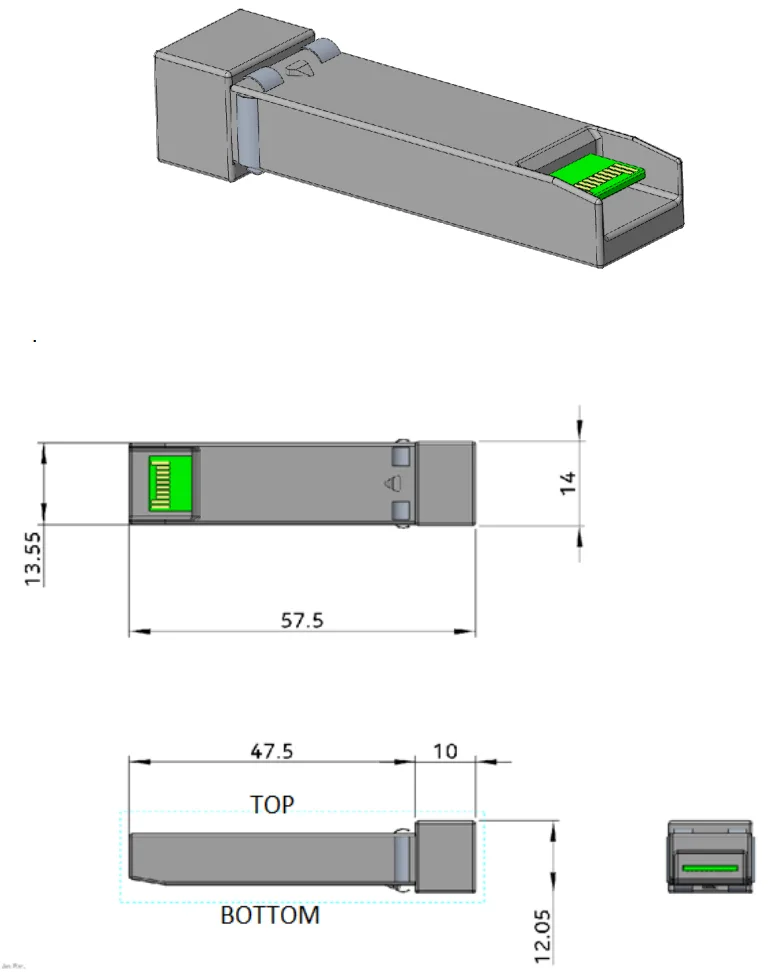
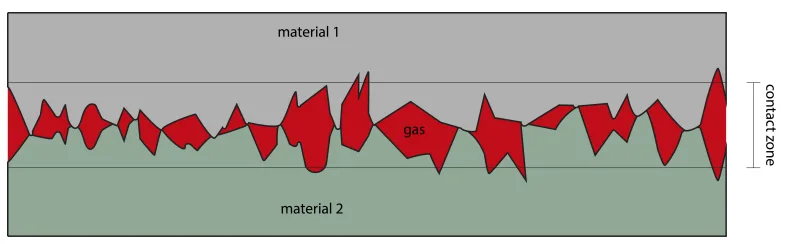
1. Overview:
- Title: 3W SFP Interface Development
- Author: Joonas Turunen
- Year of publication: 2022
- Journal/academic society of publication: Metropolia University of Applied Sciences
- Keywords: thermal design, cooling, product design, mechanical design
2. Abstract:
The rapid increase in data transfer demands efficient cooling for Small Form-Factor Pluggable (SFP) transceivers, which generate significant heat due to higher energy consumption. This thesis, conducted from February 1 to June 30, 2022, focused on developing and testing thermal interface materials (TIMs) and contact pressure for a 3W SFP module to enhance cooling efficiency. Two thermal interface concepts, GH4 and AB1, were selected for further development based on their thermal performance and usability.
3. Introduction:
The increasing data transfer rates in modern technologies have led to higher energy consumption in SFP transceivers, necessitating advanced cooling systems to manage the resultant heat. The 3W SFP module, with a 50% increase in heat output compared to its 2W predecessor, requires efficient thermal management to prevent overheating. This study addresses the design and testing of thermal interfaces to ensure effective heat dissipation from the SFP to the heatsink.
4. Summary of the study:
Background of the research topic:
The rise in data transfer needs has increased the power consumption of SFP transceivers, resulting in excess heat that must be dissipated to maintain performance (Section 1, Introduction). Efficient cooling is critical as the SFP's heat output has risen from 2W to 3W, a significant proportional increase (Section 1, Introduction). The thermal chain, including the SFP, TIM, and heatsink, is pivotal in managing heat transfer (Section 2.2, Thermal chain).
Status of previous research:
Previous studies, such as those by Navnri N. Verma &co [4] and Junfeng Peng & Jun Hong [6], modeled thermal contact resistance but were less applicable to systems involving silicone-based TIMs (Section 2.1, Basic theory). Empirical tests were found to provide case-specific data for thermal contact efficiency (Section 2.1, Basic theory). Existing SFP concepts like EF3 and AB1 provided a baseline for thermal performance comparisons (Section 4, Previous SFP -module concepts).
Purpose of the study:
The purpose was to develop a thermal interface for a 3W SFP module to ensure efficient cooling, focusing on optimizing TIMs and contact pressure while maintaining usability and manufacturability (Section 1, Introduction). The study aimed to evaluate thermal performance through prototype testing and select suitable concepts for further development (Section 2, Abstract). Ensuring the SFP remains below critical temperature thresholds in varying environmental conditions was a key goal (Section 3.4, Thermal performance).
Core study:
The study involved designing and testing prototypes of the 3W SFP module, focusing on thermal interface materials (TIMs) such as silicone-based pads and phase-change materials (PCMs), and evaluating the impact of contact pressure on thermal efficiency (Section 2.3, TIM material; Section 7, Thermal tests). Four concepts (AB1, EF3, CD2, GH4) were tested, with performance assessed through thermal resistance and insertion/extraction forces (Section 5, Tested SFP - modules). A custom jig was designed to measure the effect of contact pressure on temperature differences (Section 7.2, Contact pressure test).
5. Research Methodology
Research Design:
The research was structured around empirical thermal testing of SFP module prototypes, comparing different TIMs and thermal connection concepts (Section 7, Thermal tests). A special jig was designed to apply varying contact pressures (35N, 87N, 350N) to evaluate their impact on thermal performance (Section 7.2, Contact pressure test). The study reused components from previous SFP designs to ensure manufacturability and functionality (Section 3.1, Manufacturability).
Data Collection and Analysis Methods:
Temperature differences across the SFP and heatsink were measured using external thermocouples to calculate thermal efficiency (Section 7.1, Testing setup and environment). Data was collected from a test setup with a PCB, housing, and a modified SFP with heat resistors to control power levels (Section 7.1, Testing setup and environment). Thermal resistance was analyzed to compare the performance of different TIMs and concepts (Section 8, Test results).
Research Topics and Scope:
The research focused on thermal design, specifically the efficiency of TIMs and contact pressure in the 3W SFP module’s thermal chain (Section 2, Thermal connection). The scope included testing four thermal connection concepts (AB1, EF3, CD2, GH4) and various TIMs, such as Nolato and Allied pads, under controlled conditions (Section 5, Tested SFP - modules). The study also addressed manufacturability and usability constraints, such as insertion forces not exceeding 18N (Section 3.2, Usability).
6. Key Results:
Key Results:
- The AB1 and GH4 concepts demonstrated superior thermal performance and usability, making them suitable for further development (Section 9, Conclusions).
- Nolato TIM pads showed slightly better thermal performance than Allied #3, but Allied pads were more robust (Section 8.1, TIM).
- The CD2 concept, despite excellent thermal performance, was impractical due to high insertion forces (50N) (Section 8.2, Thermal connection concept).
- Higher contact pressure improved cooling efficiency, particularly for metal-to-metal contacts, but had a lesser effect on PCM TIMs (Section 8.4, Contact pressure).
- The thermal chain’s efficiency was limited by surface imperfections, with silicone-based TIMs compensating for these issues (Section 2.3, TIM material).
- Simulations indicated that selected designs could perform adequately with fan cooling but struggled with passively cooled variants (Section 9, Conclusions).
Figure Name List:
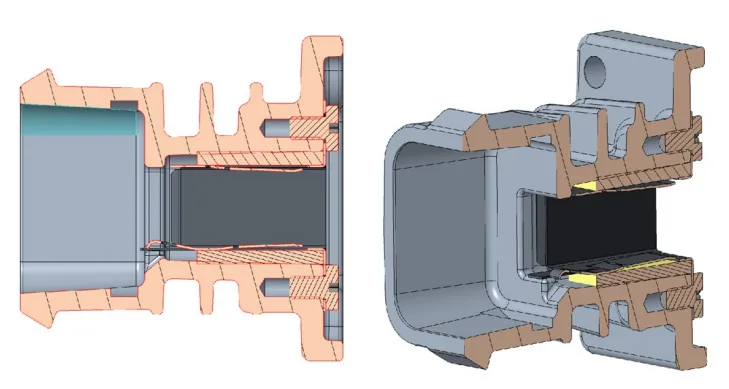
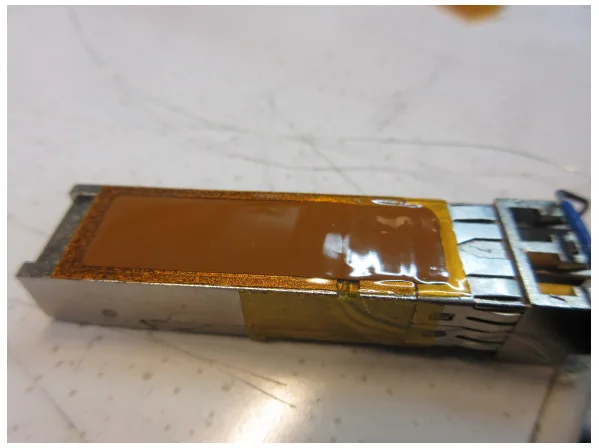
- Figure 1 SFP main dimensions
- Figure 2 contact zone
- Figure 3 Thermal chain
- Figure 4 EF3 - concept
- Figure 5 The cage protects TIM pads and functions as spring to provide contact pressure
- Figure 6 AB1 - concept
- Figure 8 spring clip
- Figure 9 isolation plate with O-rings and sheet metal EMI -seal
- Figure 10 left AB1, right AB1 #2
- Figure 11 SFP heatsink with EF3 -type thermal connections
- Figure 12 CD2 solution E
- Figure 13 CD2 solution E, finger springs and cage
- Figure 14 GH4 - concept
- Figure 16 PCB and housing for testing
- Figure 17 thermo couple on SFP
- Figure 18 cross section of pressure testing jig design
- Figure 19 pressure marks on TIM after testing with elevated pressure
- Figure 20 double spring
- Figure 21 TIM also under the spring
7. Conclusion:
The study successfully identified the AB1 and GH4 concepts as viable solutions for the 3W SFP module’s thermal management, balancing thermal performance and usability (Section 9, Conclusions). Further development is needed to optimize spring clip thickness, TIM adhesion durability, and manufacturability, particularly for the GH4’s foam material and AB1’s assembly tooling (Section 9, Conclusions). The research highlighted the importance of contact pressure and TIM selection in overcoming surface imperfections and achieving efficient cooling (Section 8.4, Contact pressure).
8. References:
- [1] SNIA. SFF-84332 Rev 5 Specification for SFF+ Module and Cage
- [2] Thermal contact conductance Web2. Wikipedia
- [3] Chakaravi1 V Madhuudcan. Thermal Contact Conductance 2014 Springer International Publishing Switzerland
- [4] Navi N. Verra Sanand\ Mazunder 2015. Extraction of thermal contact conductance of metal-metal contacts from scale-resolved direct numerical simulation. International Journal of Heat and Mass Transfer
- [5] Kivjoja. Kivuvon. Salonen. Tribologia. Kiika. kuluminen ja voltelu. Otaileto
- [6] Junfeng Peng & Jun Hong
- [7] Unspecified reference for PCM properties
9. Copyright:
- This material is a paper by Joonas Turunen. Based on "3W SFP Interface Development".
- Source of the paper: Not available (thesis document, no DOI provided)
This material is summarized based on the above paper, and unauthorized use for commercial purposes is prohibited.
Copyright © 2025 CASTMAN. All rights reserved.
Paper Summarize:
The "3W SFP Interface Development" thesis by Joonas Turunen addresses the critical need for efficient cooling in 3W Small Form-Factor Pluggable (SFP) transceivers due to increased data transfer and heat output. Conducted between February and June 2022, the study tested thermal interface materials (TIMs) and contact pressure, selecting the AB1 and GH4 concepts for their superior thermal performance and usability. The research underscores the importance of optimizing TIMs and contact pressure to manage surface imperfections and ensure effective heat dissipation.
Key questions and answers about the research:
Q1. What is the primary challenge addressed in the 3W SFP Interface Development?
A1. The primary challenge is managing the increased heat output from 3W SFP transceivers, necessitating efficient cooling systems to prevent overheating (Section 1, Introduction).
Q2. Which thermal interface materials (TIMs) were tested, and how did they compare?
A2. Nolato and Allied TIM pads were tested, with Nolato showing slightly better thermal performance but Allied offering greater robustness (Section 8.1, TIM).
Q3. How did contact pressure affect the thermal performance of the SFP module?
A3. Higher contact pressure improved cooling efficiency, particularly for metal-to-metal contacts, but had a lesser impact on PCM TIMs (Section 8.4, Contact pressure).
Q4. Why was the CD2 concept rejected despite its thermal performance?
A4. The CD2 concept was rejected due to excessively high insertion forces (50N), which compromised usability (Section 8.2, Thermal connection concept).
Q5. Which thermal connection concepts were selected for further development?
A5. The AB1 and GH4 concepts were selected for their balance of thermal performance and usability (Section 9, Conclusions).
Q6. What further developments are needed for the selected concepts?
A6. The AB1 concept requires studies on thicker spring clips and TIM assembly tooling, while GH4 needs investigation into foam material durability and machining costs (Section 9, Conclusions).