This article introduces the paper ['VIABILITY OF FLAX FIBER-REINFORCED SALT CORES FOR ALUMINUM HIGH-PRESSURE DIE CASTING IN EXPERIMENT AND SIMULATION'] presented at the ['International Journal of Metalcasting']
1. Overview:
- Title: VIABILITY OF FLAX FIBER-REINFORCED SALT CORES FOR ALUMINUM HIGH-PRESSURE DIE CASTING IN EXPERIMENT AND SIMULATION
- Author: Dominik Boos, Klaus Drechsler, Swen Zaremba
- Publication Year: 2024
- Publishing Journal/Academic Society: International Journal of Metalcasting
- Keywords: water-soluble core, expendable core, lost core, hollow parts in HPDC, salt core, fiber reinforcement, flax fiber, aluminum casting, high-pressure die casting, simulation, cavity venting, mechanical characterization, three-point bending, wet compression molding
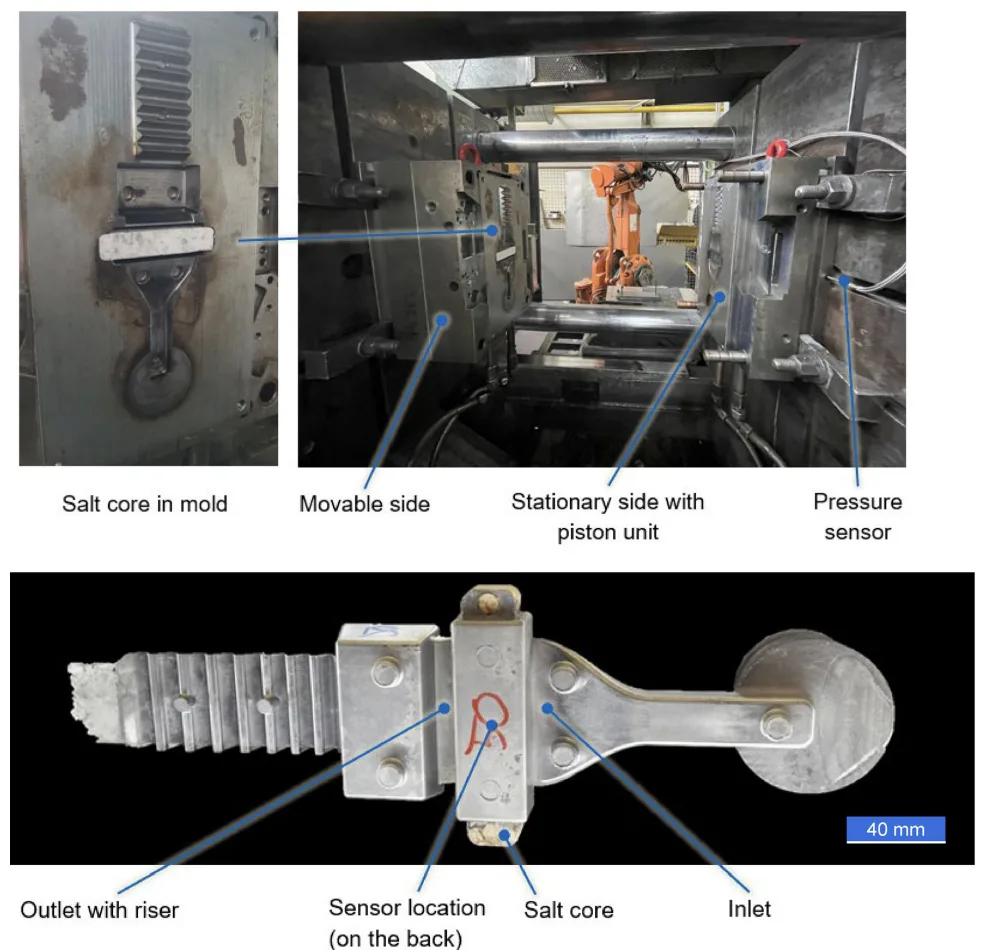
2. Research Background:
Background of the Research Topic:
The pursuit of lightweight design, driven by the global demand for decarbonization and emission reduction, necessitates the production of hollow parts and parts with undercuts. Aluminum high-pressure die casting (HPDC) is an economically effective process for producing complex, near-net shape 3D parts with low wall thickness, offering high lightweight potential. However, manufacturing complex hollow light metal parts via HPDC is challenging due to harsh conditions such as high gate velocities (60 m/s), high packing pressures (1200 bar), mold temperatures (up to 280 °C), and melt temperatures (up to 700 °C). Expendable or lost cores, removed in post-processing, can realize these complex geometries. The challenge lies in identifying a lost core material that balances high process resistance and easy removability.
Status of Existing Research:
Binder-free salts and salt mixtures have been identified as suitable lost core materials, offering improved strength and surface quality compared to binder-stabilized cores. Binder-free salt cores can be produced through sintering, casting of a melt, or wet compression molding of a slurry. However, the brittle nature of binder-free salt, relying on ionic bonds for cohesion, limits their application in HPDC where dynamic loads can cause cracks and flashes. Existing approaches to mitigate these issues include placing cores far from gates, reducing machine parameters, increasing wall thickness, or accepting strength loss at elevated temperatures.
Necessity of the Research:
Conventional salt cores often fail under the highly dynamic loads in HPDC, leading to scrap parts. There is a need for a more robust lost core material to expand the application of HPDC for complex hollow parts, particularly in demanding sectors like mobility.
3. Research Purpose and Research Questions:
Research Purpose:
This paper aims to demonstrate the viability of a new fiber-reinforced salt material for lost cores in HPDC. The research utilizes simulation to estimate transient bending moments on core inserts and validates these findings with casting experiments.
Key Research:
The key research questions addressed are:
- Can flax fiber reinforcement enhance the viability of salt cores in HPDC?
- How do simulation results of melt flow and pressure distribution correlate with experimental outcomes in HPDC using fiber-reinforced salt cores?
- What are the bending strengths and energy absorption capabilities of flax fiber-reinforced salt cores compared to conventional salt cores?
Research Hypotheses:
The central hypothesis is that flax fiber reinforcement improves the toughness of salt cores, enabling them to withstand the dynamic loads of HPDC and remain viable for producing complex hollow aluminum parts. It is also hypothesized that simulation can accurately predict the loads on the salt core during HPDC filling.
4. Research Methodology
Research Design:
The research employs a mixed-method approach combining experimental and simulation-based investigations. Experiments include three-point bending tests to characterize the mechanical properties of fiber-reinforced salt cores and HPDC experiments to assess core viability under real-world casting conditions. Simulations involve 2D and 3D computational fluid dynamics (CFD) analyses using ANSYS Fluent 2023R1 to model the aluminum melt flow and pressure distribution during HPDC filling.
Data Collection Method:
- Three-point bending tests: Force and displacement data were collected using a 10-kN load cell and a video extensometer. Specimen geometry was a rectangular bar, and tests were conducted according to DIN EN 843 standards.
- HPDC experiments: Pressure profiles near the core surface were logged using a Kistler 6175A2 pressure sensor connected to a HBM QuantumX MX410B measurement amplifier. Visual inspection of cast parts and salt cores was conducted after experiments.
- CFD Simulations: Data on pressure distribution, melt velocity, and volume fraction were generated from ANSYS Fluent simulations.
Analysis Method:
- Mechanical Characterization: Bending strength, bending modulus, and absorbed energy were calculated from three-point bending test data.
- CFD Simulation Analysis: Simulation results were analyzed to determine pressure loads and bending moments acting on the salt core. A one-dimensional analytical outlet model was developed and compared with CFD results for validation. Mesh convergence studies were performed to ensure numerical accuracy.
- Correlation of Simulation and Experiment: Simulation-predicted loads were compared with the performance of salt cores in HPDC experiments to assess core viability and validate the simulation approach.
Research Subjects and Scope:
The research focuses on flax fiber-reinforced salt cores produced by wet compression molding. Two flax fiber-reinforced salt core specimens (F0310 and F3010) and conventional sintered salt cores (NaCIEM) were tested. HPDC experiments were conducted using an Italpress IP 300 SC cold chamber die casting machine and EN-AC AlSi9Cu3(Fe) aluminum alloy. Simulations were performed using 2D and 3D models of a rectangular pipe casting geometry with a core insert.
5. Main Research Results:
Key Research Results:
- Mechanical Properties: Flax fiber-reinforced salt cores exhibited significantly higher energy absorption (8 to 31 times) in three-point bending tests compared to conventional salt cores, indicating improved toughness. Bending strength varied between 11 and 37 MPa for fiber-reinforced cores depending on fiber parameters.
- CFD Simulation Validation: 2D filling simulations demonstrated mesh convergence. The one-dimensional analytical outlet model showed excellent agreement with CFD results for vent pressure loss. 3D simulations predicted stress peaks up to 33 MPa on the salt core at an ingate speed of 64 m/s.
- HPDC Core Viability: Conventional salt cores (bending strength ~15 MPa) failed in HPDC experiments under high parameter settings, consistent with simulation predictions. Fiber-reinforced salt cores, with their higher bending strengths and toughness, remained viable in HPDC experiments, demonstrating their robustness.
Data Interpretation:
- The enhanced toughness of flax fiber-reinforced salt cores, evidenced by higher energy absorption, is crucial for their viability in HPDC. This toughness allows them to withstand the high dynamic loads and resist brittle fracture observed in conventional salt cores.
- CFD simulations, particularly 3D, provide a valuable tool for predicting stress loads on salt cores during HPDC filling, enabling optimization of core material and process parameters. The validated outlet vent model improves the accuracy of these simulations.
- The experimental validation confirms that fiber reinforcement is an effective strategy to improve the performance of salt cores in HPDC, opening possibilities for manufacturing more complex hollow parts.
Figure Name List:
- Figure 1. Wet compression molding process and basic tool components for a short fiber-reinforced salt core.14
- Figure 2. Fracture patterns of unreinforced salt (left) and flax fiber-reinforced salt (right). Due to the partly translucent salt matrix, the fibers close to the surface are visible in the non-damaged areas creating a marbled appearance.
- Figure 3. Bending test results representing brittle (left) or pseudo-ductile (right) material behavior for NaCIEM (benchmark) or F1520* specimens, respectively.14
- Figure 4. Summary of three-point bending test results for flax fiber-reinforced and conventional salt core specimens.14 Bars represent the 25% and 75% percentiles; the circles represent the mean values, and the antennas reach out to the extrema of the test series. Plots generated with boxplot_custom.m.45
- Figure 5. Typical HPDC mold setup (top) and surrogate model (bottom) for vent modeling according to Bar-Meir et al.64 or Nouri-Borujerdi and Goldak.65
- Figure 6. The HPDC mold setup (top) and demonstrator part (bottom)66.
- Figure 7. Shot curves measured by the HPDC sensor for "high" and "low" parameter settings. The averaged curves show the mean of the curves. Scatter area is represented by the hull curves. Please note the log scale on the abscissa.
- Figure 8. Geometric features of a sharp bend according to Idel'chik68
- Figure 9. Mesh and boundaries for the 2D CFD vent model.
- Figure 10. Mesh domains for the HPDC simulation.
- Figure 11. Mesh with polyhedral surface mesh and polyhedral and hexahedral volume elements for the 3D HPDC simulation. The dash-dotted line on the left represents the symmetry plane.
- Figure 12. Mach number and static pressure distribution for a stagnation pressure of 1e5 Pa at the inlet.
- Figure 13. Mach number and static pressure distribution for a stagnation pressure of 1e7 Pa at the inlet.
- Figure 14. Loss coefficient (fD,CFD) and inlet Mach number (Min,CFD) obtained from the CFD solution for the 2D vent model with sensitivity checks for higher stagnation temperature ("-hot") or finer mesh (“-fine”).
- Figure 15. Loss coefficient over the mean Re number in the vent for the modified 1D analytical model (fD,V), 1D analytical model according to the original literature (fD,f) and 2D CFD simulation (fD,CFD). The discontinuity in the curves for the analytical models is caused by the discrete transition from laminar to turbulent flow at Re=2300.
- Figure 16. Jet breakup at a fill fraction of 22% for the 2D mesh variants. The dimensionless characteristic numbers for the jet based on the hydraulic diameter of the gate are: Re = 215e3, We = 519, Oh = 8e-4. Red cells represent the melt volume fraction, whereas blue cells represent air.
- Figure 17. Solution on M2D1 at fill time 2.886 ms/fill fraction 22%.
- Figure 18. Solution on M2D1 at fill time 3.830 ms/fill fraction 30%.
- Figure 19. Solution on M2D1 at fill time 5.281 ms/fill fraction 40%.
- Figure 20. Solution on M2D1 at fill time 8.010 ms/fill fraction 60%.
- Figure 21. Solution on M2D1 at fill time 12.033 ms/fill fraction 86%.
- Figure 22. Simulated cavity pressure at the sensor location for parameter setting "high".
- Figure 23. Resulting total forces on the core in x- and y-direction on M2D1 for parameter setting "high".
- Figure 24. Simulated outlet Mach number for parameter setting "high".
- Figure 25. High interface velocities and cell residuals in vicinity of a merging phase interface for the solution on M2D1 at fill fraction 60% (close-up view of Figure 20, upper right corner). The figure shows an overlay of the phase fraction field where the interface between melt and air is indicated by a dashed line. Vectors that are colored according to their magnitude represent the velocity field. The imbalance of the energy equation is shown by the temperature residual for each cell. The maximum air speed is 330 m/s (Mach 0.54).
- Figure 26. Absolute values of the maximum bending stress in the core during the 2D filling simulation for parameter setting "high".
- Figure 27. Solution on M3D at fill time 1.992 ms/fill fraction 14%.
- Figure 28. Solution on M3D at fill time 3.101 ms/fill fraction 22%.
- Figure 29. Solution on M3D at fill time 4.203 ms/fill fraction 30%.
- Figure 30. Solution on M3D at fill time 5.801 ms/fill fraction 40%.
- Figure 31. Solution on M3D at fill time 12.702 ms/fill fraction 86%.
- Figure 32. Absolute values of the maximum bending stress in the core and sensor pressure during the 3D filling simulation for parameter settings "low" and "high".
- Figure 33. Cross sections of salt cores after aluminum HPDC for “low” and “high” parameter settings.
- Figure 34. Micrographs of overmolded F0310 (left) and F3010 (right) specimens for the parameter setting "high".
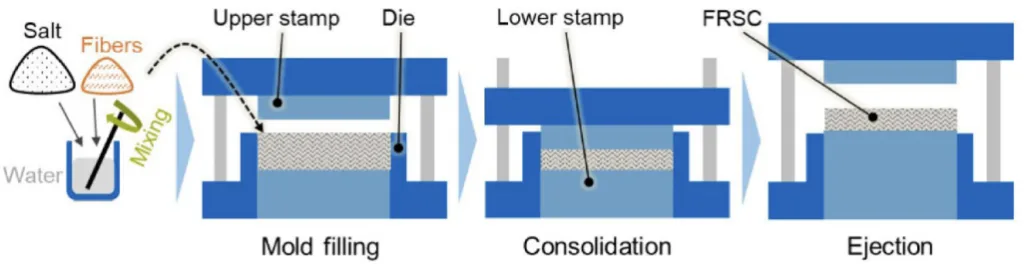
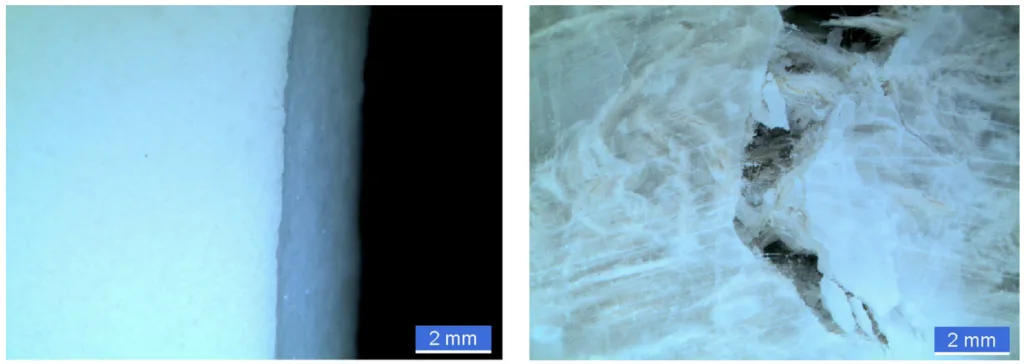
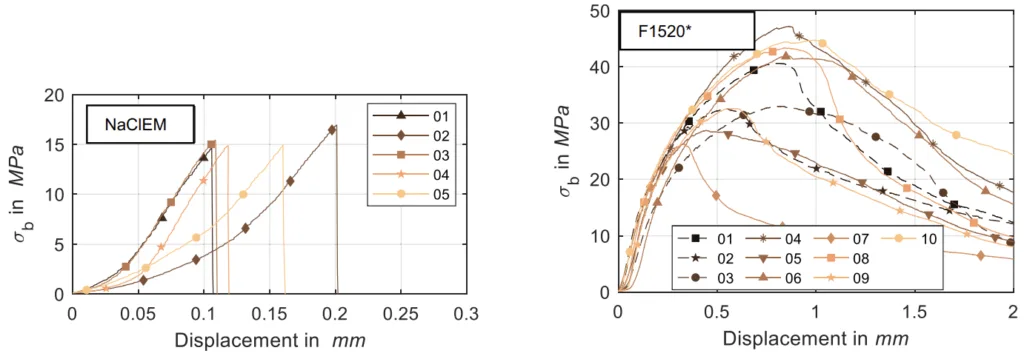
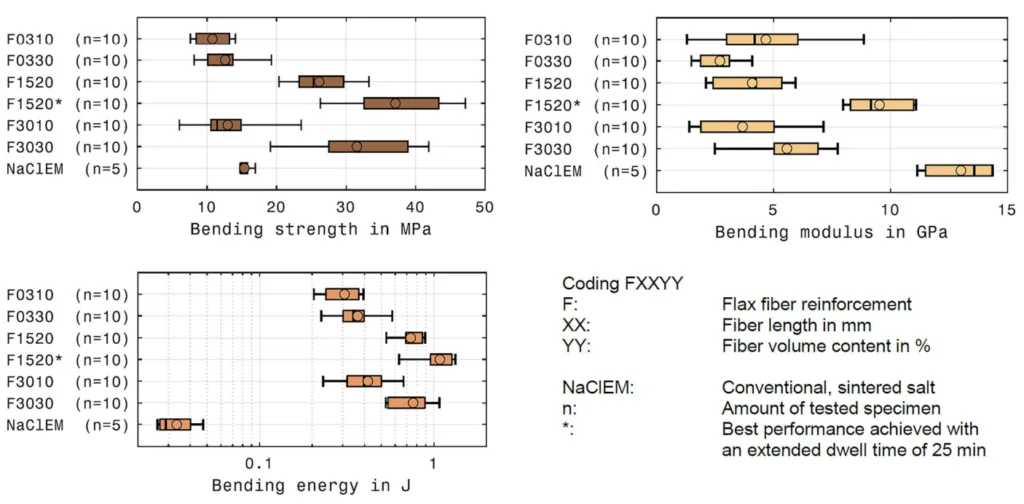
specimens.14 Bars represent the 25% and 75% percentiles; the circles represent the mean values, and the antennas reach out to the extrema of the test series. Plots generated with boxplot_custom.m.45
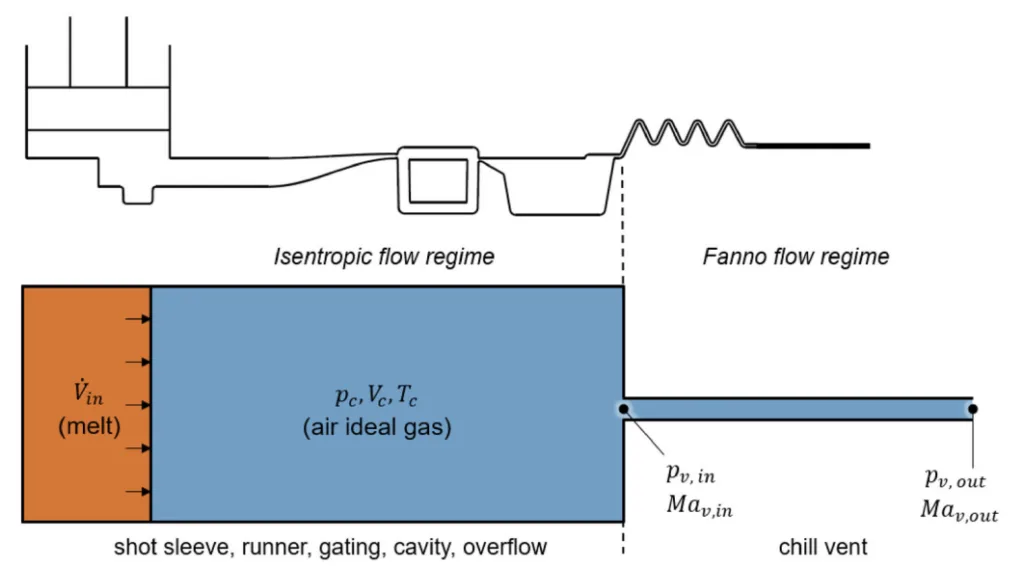
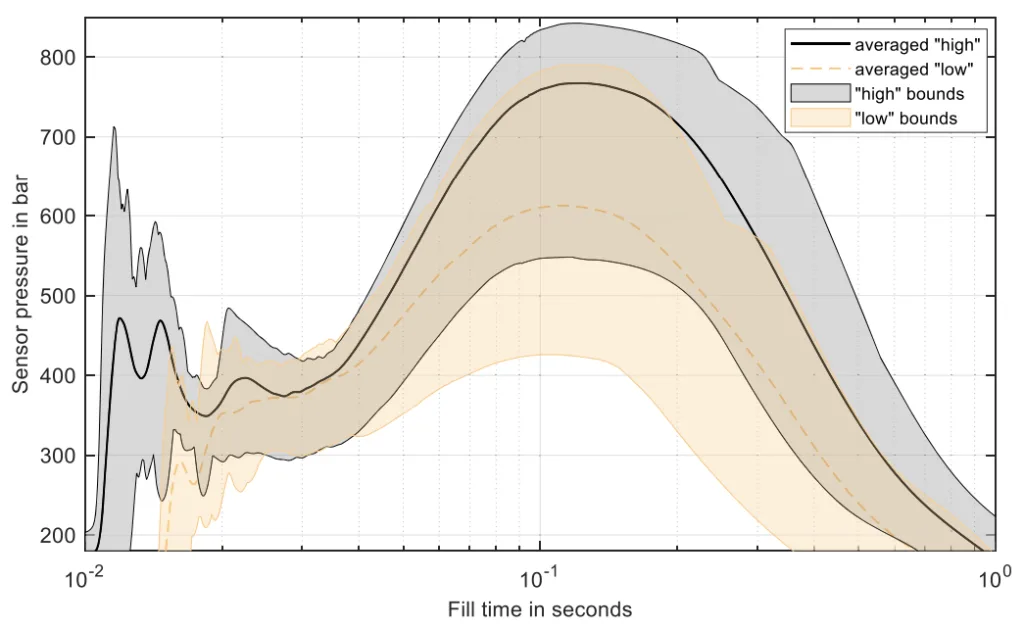
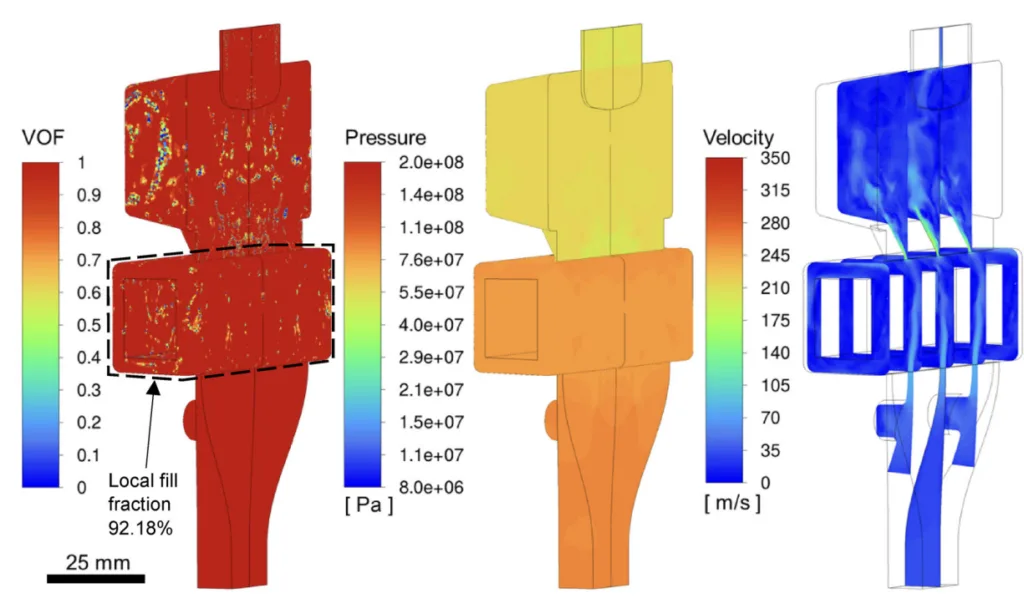
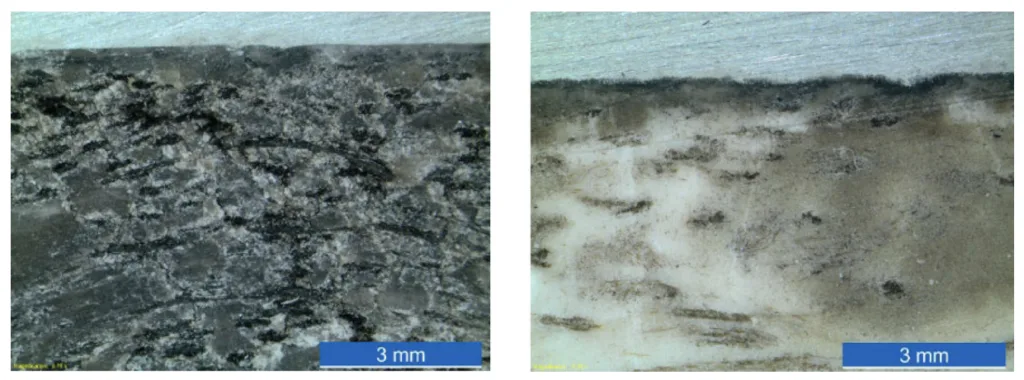
6. Conclusion:
Summary of Main Results:
This research successfully demonstrated the viability of flax fiber-reinforced salt cores for aluminum HPDC. Key findings include:
- Flax fiber reinforcement significantly enhances the toughness of salt cores, as evidenced by increased energy absorption in bending tests.
- CFD simulations, validated by experimental data, accurately predict stress loads on salt cores during HPDC filling.
- Conventional salt cores fail under HPDC conditions, while fiber-reinforced salt cores remain viable due to their improved mechanical properties.
- A modified one-dimensional venting model accurately represents the complex vent geometry and improves simulation accuracy.
Academic Significance of the Research:
This research contributes to the academic field by:
- Providing a comprehensive investigation into the application of fiber-reinforced salt cores in HPDC, combining experimental and simulation methodologies.
- Validating CFD simulation as a tool for predicting core viability in HPDC, with a focus on accurate vent modeling.
- Expanding the understanding of material behavior under HPDC conditions, particularly the role of toughness in lost core materials.
Practical Implications:
The practical implications of this research are significant for the die casting industry:
- Flax fiber-reinforced salt cores offer a robust alternative to conventional salt cores, enabling the production of more complex and lightweight aluminum parts with undercuts and hollow sections via HPDC.
- The developed simulation methodology can be used to optimize core design and process parameters, reducing scrap rates and improving casting quality.
- The new lost core material provides foundries with a technology advantage, potentially opening new markets, especially in the mobility sector where lightweighting is critical.
Limitations of the Research
The research acknowledges the following limitations:
- Material characterization of flax fiber-reinforced salt cores is primarily at room temperature. Behavior at elevated temperatures relevant to HPDC preheating requires further investigation.
- Material behavior at high strain rates, relevant to the dynamic loading in HPDC, is not fully characterized and should be explored for more refined simulation models.
- The study focuses on specific flax fiber reinforcement parameters (length and volume content). Further optimization of fiber parameters and core composition may be possible.
- The simulation model simplifies certain aspects of the HPDC process, such as neglecting the packing phase and assuming idealized machine behavior.
7. Future Follow-up Research:
- Directions for Follow-up Research
Future research directions include: - Testing the failure behavior of flax fiber-reinforced salt cores at elevated temperatures to simulate preheated core inserts.
- Investigating the strain-rate dependency of the material behavior to improve simulation accuracy.
- Optimizing flax fiber parameters and core composition for enhanced performance.
- Coupling fluid and structural damage models in simulations to identify critical core areas for tailored fiber reinforcement.
- Conducting dissolution and recycling experiments to assess the feasibility of separating and reusing flax fibers and salt in core production.
- Areas Requiring Further Exploration
Areas requiring further exploration include: - Surface quality of castings produced with fiber-reinforced salt cores and methods for improvement.
- Tooling design and manufacturing considerations for wet compression molding of complex fiber-reinforced salt cores.
- Economic analysis of using flax fiber-reinforced salt cores in industrial HPDC production.
- Investigating the use of modular elements and joining techniques for complex core geometries to reduce tooling costs for prototyping and low-series production.
8. References:
- 1. B. Fuchs, Salzkerntechnologie für Hohlgussbauteile im Druckguss, Dissertation, FAU Erlangen-Nürnberg, 1st edn. (Cuvillier Verlag, Göttingen, 2014)
- 2. L.H. Kallien, Salzkerne im Druckguss, Giesserei-Special(01), (2016), pp. 32–43
- 3. J. Campbell, Complete casting handbook: metal casting processes, techniques and design, 2nd edn. (Butterworth-Heinemann, Amsterdam, 2015)
- 4. P. Fickel, Hohl- und Verbundguss von Druckgussbauteilen-Numerische Auslegungsmethoden und experimentelle Verifikation, Dissertation, Universität Stuttgart (2017). https://doi.org/10.18419/opus-9068
- 5. C. Herrmann, H. Pries, G. Hartmann (eds.), Energie- und ressourceneffiziente Produktion von Aluminium-druckguss, 1st ed., Springer Vieweg, Berlin, Heidelberg (2013). https://doi.org/10.1007/978-3-642-39853-7
- 6. M. Scheydecker, K.-L. Weisskopf, Innovationspotenzial Salzkerne. Herausforderungen für die Serienanwendung im Aluminium-Guss, VDI-Berichte 2217, pp. 19–39 (2014)
- 7. K. Vollrath, Herstellung hochwertiger Salzkerne durch Warmkammer-Druckgießen. Giesserei 104(01), 32-37 (2017)
- 8. T. Nitschke-Pagel, Thermisches Fügen, in Handbuch Leichtbau: Methoden, Werkstoffe, Fertigung. ed. by F. Henning, E. Moeller (Hanser, München Wien, 2011), pp.855-885
- 9. L.H. Kallien, V. Görgrün, Einfluss der Elektromobilität auf die Gussproduktion in der deutschen Gießerei-Industrie: Teil 1. Giesserei 105(4), 70–80 (2018)
- L.H. Kallien, V. Görgrün, Einfluss der Elektromobilität auf die Gussproduktion in der deutschen Gießerei-Industrie: Teil 2. Giesserei 105(7), 60–66 (2018)
- H. Mählmann, M. Baader, GDA Jahresbericht 2020, Gesamtverband der Aluminiumindustrie e. V. (2020)
- F. Bonollo, N. Gramegna, G. Timelli, High-pressure die-casting: contradictions and challenges. Miner. Metals Mater. Soc. 67(5), 901–908 (2015). https://doi.org/10.1007/s11837-015-1333-8
- M.T. Murray, M. Murray, High pressure die casting of aluminium and its alloys, in Fundamentals of aluminium metallurgy: production, processing and applications, 1st edn., ed. By R. Lumley (Woodhead Publishing Limited, Cambridge, 2011), pp. 217–261. https://doi.org/10.1533/9780857090256.1.217
- D. Boos, S. Zaremba, K. Drechsler, Towards a robust, water-soluble, lost core material:part two-fiber-reinforced salt by wet compression molding. J. Plast. Technol. 19(5), 190–226 (2023). https://doi.org/10.3139/0999.01052023
- P. Jelínek, E. Adámková, F. Mikšovský, J. Beňo, Advances in technology of soluble cores for die castings. Arch. Foundry Eng. 15(2), 29–34 (2015). https://doi.org/10.1515/afe-2015-0032
- W. Jiang, J. Dong, L. Lou, M. Liu, Z. Hu, Preparation and properties of a novel water soluble core material. J. Mater. Sci. Technol. 26(3), 270–275 (2010)
- A. Dworog, Abschlussbericht des Verbundprojektes 3D-Freiformkanäle im Druckguss/Medienführende Kanäle, BMBF Forschung für die Produktion von morgen, Förderkennzeichen 02PU2243, Nordwalde (2011)
- Z. Xiao, L.T. Harper, A.R. Kennedy, N.A. Warrior, A water-soluble core material for manufacturing hollow composite sections. Compos. Struct. 182, 380-390 (2017). https://doi.org/10.1016/j.compstruct.2017.09.058
- T. Hartig, G. Schiller, C. Bütterich, Salt Core Technology. Lost cores aluminium casting applications, Wilhermsdorf (2018)
- A. Kugel, A. Bührig-Polaczek, Möglichkeiten zur Erzeugung von Hohlräumen in Druckgussteilen. Gießereiforschung 56(1), 14–22 (2004)
- J. Yaokawa, D. Miura, K. Anzai, Y. Yamada, H. Yoshii, Strength of salt core composed of alkali carbonate and alkali chloride mixtures made by casting technique. Mater. Trans. 48(5), 1034–1041 (2007). https://doi.org/10.2320/matertrans.48.1034
- F. Czerwinski, M. Mir, W. Kasprzak, Application of cores and binders in metalcasting. Int. J. Cast Met. Res. 28(3), 129–139 (2015). https://doi.org/10.1179/1743133614Y.0000000140
- H.D. Grözinger, WO 2005/080022 A2 (2005)
- P.A.M. Vitor, P.H.F. Santos, A.K. Alves, C.P. Bergmann, Study of densification by pressing and sintering of NaCl and KCl salts, in 7th International Congress on Ceramics & 62° Congresso Brasileiro de Cerâmica, (2018), pp. 734–740
- X. Gong, X. Liu, Z. Chen, Z. Yang, W. Jiang, Z. Fan, 3D printing of high-strength water-soluble salt cores via material extrusion. Int. J. Adv. Manuf. Technol. 118, 2993-3003 (2022). https://doi.org/10.1007/s00170-021-08131-x
- K. Oikawa, K. Meguro, J. Yaokawa, K. Anzai, Y. Yamada, A. Fujiwara, H. Yoshii, Mechanical properties of mixed salt core made by die casting machine. J. Jpn. Foundry Eng. Soc. 81(5), 232–237 (2009). https://doi.org/10.11279/jfes.81.232
- D. Pierri, C. Beck, Lost Core Technologie-offen für alle. Chancen und Grundlagen des Verfahrens, Giesserei 103(10), 46–52 (2016)
- L.H. Kallien, T. Weidler, M. Becker, Production of magnesium die castings with hollow structures using gas injection technology in the hot chamber die casting process. Int. Foundry Res. 66(4), 20–27 (2014)
- L.H. Kallien, C. Böhnlein, A. Dworog, B. Müller, Ergebnisse aus dem Forschungsprojekt 3-D-Freiform-medienführende Kanäle im Druckguss. Giesserei 100(12), 36-43 (2013)
- R. Huang, B. Zhang, Study on the composition and properties of salt cores for zinc alloy die casting. Int. J. Metalcast. 11, 440–447 (2017). https://doi.org/10.1007/s40962-016-0086-7
- K. Oikawa, K. Sakakibara, Y. Yamada, K. Anzai, High-temperature mechanical properties of NaCl–Na2CO3 salt-mixture removable cores for aluminum die-casting. Mater. Trans. 60(1), 19–24 (2019). https://doi.org/10.2320/matertrans.MG201804
- S. Tu, F. Liu, G. Li, W. Jiang, X. Liu, Z. Fan, Fabrication and characterization of high-strength water-soluble composite salt core for zinc alloy die castings. Int. J. Adv. Manuf. Technol. 95, 505-512 (2018). https://doi.org/10.1007/s00170-017-1208-y
- S. Findeisen, R. van der Auwera, M. Heuser, F.-J. Wöstmann, Gießtechnische Herstellung von E-Motorengehäusen mit interner Kühlung. Giesserei 106(06), 72-78 (2019)
- X. Gong, W. Jiang, F. Liu, Z. Yang, F. Guan, Z. Fan, Effects of glass fiber size and content on microstructures and properties of KNO3-based water-soluble salt core for high pressure die casting. Int. J. Metalcast. 15, 520-529 (2021). https://doi.org/10.1007/s40962-020-00480-9
- C. Cantas, B. Baksan, Effects of composition on the physical properties of water-soluble salt cores. Int. J. Metalcast. 15, 839–851 (2021). https://doi.org/10.1007/s40962-020-00511-5
- F. Liu, S. Tu, X. Gong, G. Li, W. Jiang, X. Liu, Z. Fan, Comparative study on performance and microstructure of composite water-soluble salt core material for manufacturing hollow zinc alloy castings. Mater. Chem. Phys. 252, 123257 (2020). https://doi.org/10.1016/j.matchemphys.2020.123257
- X. Wang, W. Liu, X. Liu, L. Song, First-principles calculation and mechanical properties of NaCl–Na2SO4 composite water-soluble salt core. Int. J. Metalcast. 17, 263–271 (2023). https://doi.org/10.1007/s40962-022-00769-x
- M. Becker, Hohle Aluminiumstrukturbauteile durch Salzkerne im Druckguss, Dissertation, TU Clausthal, Clausthal-Zellerfeld (2021). https://doi.org/10.21268/20211123-0
- B. Fuchs, H. Eibisch, C. Körner, Core viability simulation for salt core technology in high-pressure die casting. Int. J. Metalcast. 7, 39–45 (2013). https://doi.org/10.1007/BF03355557
- A. Schilling, D. Schmidt, J. Glück, N. Schwenke, H. Sharabi, M. Fehlbier, About the impact on gravity cast salt cores in high pressure die casting and rheocasting. Simul. Modelling Pr. Theory 119, 102585 (2022). https://doi.org/10.1016/j.simpat.2022.102585
- DIN EN 843-1, Hochleistungskeramik - Mechanische Eigenschaften monolithischer Keramik bei Raumtemperatur—Teil 1: Bestimmung der Biegefestigkeit, Beuth Verlag GmbH, Berlin (2008)
- DIN EN 843-2, Hochleistungskeramik - Mechanische Eigenschaften monolithischer Keramik bei Raumtemperatur—Teil 2: Bestimmung des Elastizitätsmoduls, Schubmoduls und der Poissonzahl, Beuth Verlag GmbH, Berlin (2007)
- R. Telle (ed.), Keramik, 7th edn. (Springer, Berlin Heidelberg, 2007)
- H.L. Bos, The potential of flax fibres as reinforcement for composite materials, Dissertation, Technische Universiteit Eindhoven, Eindhoven (2004)
- G. Talbot, Boxplots Custom, MATLAB Central File Exchange (2022)
- E.J. Vinarcik, High integrity die casting processes, 1st edn. (John Wiley & Sons, INC., New York, 2003)
- S. Mirjalili, S.S. Jain, M.S. Dodd, Interface-capturing methods for two-phase flows: an overview and recent developements, Annual Research Briefs, Center for Turbulence Research, Stanford University (2017)
- S. Kohlstädt, M. Vynnycky, J. Jäckel, Towards the modelling of fluid-structure interactive lost core deformation in high-pressure die casting. Appl. Math. Model. 80, 319–333 (2020). https://doi.org/10.1016/j.apm.2019.10.060
- S. Kohlstädt, M. Vynnycky, A. Neubauer, A. Gebauer-Teichmann, Comparative RANS turbulence modelling of lost salt core viability in high pressure die casting. Prog. Comput. Fluid Dyn. 19(5), 316-327 (2019). https://doi.org/10.1504/PCFD.2019.102054
- J.H. Ferziger, M. Perić, R.L. Street, Computational methods for fluid dynamics (Springer, Cham, 2020). https://doi.org/10.1007/978-3-319-99693-6
- B. Nogowizin, Theorie und Praxis des Druckgusses, 1st edn. (Schiele & Schön, Berlin, 2011)
- M.C. Carter, S. Palit, M. Littler, Characterizing flow losses occuring in air vents and ejector pins in high pressure die castings (2010)
- E. Koya, M. Nakagawa, S. Kitagawa, J. Ishimo, Y. Nakano, N. Ochiai, Visualization of microscopic behavior of atomized flow in high-pressure die casting products using a multiphase flow analysis system. Int. J. Metalcast. 17, 2508–2521 (2023). https://doi.org/10.1007/s40962-023-01015-8
- S. Kohlstädt, M. Vynnycky, S. Goeke, On the CFD modelling of slamming of the metal melt in high-pressure die casting involving lostcores. Metals 11(1), 78 (2021). https://doi.org/10.3390/met11010078
- M. Kan, O. Ipek, M. Koru, An investigation into the effect of vacuum conditions on the filling analysis of the pressure casting process. Int. J. Metalcast. 17, 430-446 (2023). https://doi.org/10.1007/s40962-022-00770-4
- E. Koya, M. Nakagawa, S. Kitagawa, J. Ishimoto, Y. Nakano, N. Ochiai, CFD analysis of mechanisms underlying the porosity-reducing effect of atomized flows in high-pressure die cast products, in MATEC Web Conference, vol. 326, pp. 1-10 (2020). https://doi.org/10.1051/matecconf/202032606006
- M. Karkkainen, L. Nastac, Evaluation and implementation of a fundamental model for interfacial heat transfer coefficient in high-pressure die-casting. Metall. Mater. Trans. B 51(2), 664–676 (2020). https://doi.org/10.1007/s11663-020-01784-1
- T. Wang, J. Huang, H. Fu, K. Yu, S. Yao, Influence of process parameters on filling and feeding capacity during high-pressure die-casting process. Appl. Sci. 12, 4757 (2022). https://doi.org/10.3390/app12094757
- A.I.N. Korti, S. Abboudi, Effects of shot sleeve filling on evolution of the free surface and solidification in the high-pressure die casting machine. Int. J. Metalcast. 11, 223–239 (2017). https://doi.org/10.1007/s40962-016-0051-5
- P. Homayonifar, R. Babaei, E. Attar, S. Shahinfar, P. Davami, Numerical modeling of splashing and air entrapment in high-pressure die casting. Int. J. Adv. Manuf. Technol. 39, 219–228 (2008). https://doi.org/10.1007/s00170-007-1214-6
- E. Altuncu, A. Doğan, N. Ekmen, Performance evaluation of different air venting methods on high pressure aluminum die casting process. Acta Phys. Pol. A 135(4), 664–667 (2019). https://doi.org/10.12693/APhysPolA.135.664
- D.T. Phan, S.H. Masood, S.H. Riza, H. Modi, Development of high performance copper alloy chill vent for high pressure die casting. IJMERR 9(7), 943–948 (2020). https://doi.org/10.18178/ijmerr.9.7.943-948
- P. Meethum, C. Suvanjumrat, Evaluate of chill vent performance for high pressure die-casting production and simulation of motorcycle fuel caps, in MATEC Web Conference, vol. 95, pp. 1–4 (2017). https://doi.org/10.1051/matecconf/20179507025
- G. Bar-Meir, E.R.G. Eckert, R.J. Goldstein, Pressure die casting: a model of vacuum pumping. J. Manuf. Sci. Eng. 118(2), 259–265 (1996). https://doi.org/10.1115/1.2831019
- A. Nouri-Borujerdi, J.A. Goldak, Modeling of air venting in pressure die casting process. J. Manuf. Sci. Eng. 126(3), 577–581 (2004). https://doi.org/10.1115/1.1767187
- P. Erhard, D. Boos, D. Günther, In-mold coating in pressing of natural-fiber-reinforced salt cores for high-pressure die-casting applications, in Proceedings of the Munich Symposium on Lightweight Design, 1st edn., ed. by J. Rieser, F. Endress, A. Horoschenkoff, P. Höfer, T. Dickhut, M. Zimmermann (Springer, Berlin, Heidelberg, 2021), pp. 35-43. https://doi.org/10.1007/978-3-662-65216-9_4
- N. N., Ansys Fluent 2023 R1 Documentation (2023)
- I.E. Idel'chik, Handbook of hydraulic resistance: coefficients of local resistance and friction, Israel Programm for Scientific Translations Ltd., Jerusalem (1966)
- Ν.Ν., ΜATLAB R2021b Documentation (2021)
- W. Sutherland, LII. The viscosity of gases and molecular force. Lond. Edinb. Dublin Philos. Mag. J. Sci. 36(223), 507–531 (1893). https://doi.org/10.1080/14786449308620508
- F.R. Menter, Two-equation eddy-viscosity turbulence models for engineering applications. AIAA J. 32(8), 1598–1605 (1994). https://doi.org/10.2514/3.12149
- C. Rumsey, The menter shear stress transport turbulence model, turbulence modeling resource, NASA Langley Research Center (2023). https://turbmodels.larc.nasa.gov/sst.html. Accessed 11 Apr 2024
- P.H. Oosthuizen, W.E. Carscallen, Compressible Fluid Flow, 1st edn. (The McGraw-Hill Companies Inc, New York, 1997)
- N.T. Basse, Mind the gap: boundary conditions for turbulence modelling, Danfoss CFD Community Tech Talk, Gothenburg (2022). https://doi.org/10.13140/RG.2.2.23072.87043/1
- B. Sasanapuri, M. Kumar, S. Wirogo, Simulation of flow through supersonic cruise nozzle: a validation study, thermal & fluids analysis workshop, NASA Langley Research Center (2011). https://tfaws.nasa.gov/TFAWS11/. Accessed 23 Oct 2024
- E. Michaelides, C.T. Crowe, J.D. Schwarzkopf (eds.), Multiphase flow handbook, 2nd edn. (CRC Press, Taylor & Francis Group, LLC, Boca Raton, 2017)
- N.I. Kolev, Multiphase flow dynamics 1: fundamentals, 5th edn. (Springer, Cham Heidelberg, New York Dordrecht London, 2015). https://doi.org/10.1007/978-3-319-15296-7
- J.U. Brackbill, D.B. Kothe, C. Zemach, A continuum method for modeling surface tension. J. Comput. Phys. 100, 335–354 (1992)
- D.C. Wilcox, Turbulence modeling for CFD, 3rd ed., DCW Industries, La Canada Calif. (2006)
- C.W. Hirt, B.D. Nichols, Volume of fluid (VOF) method for the dynamics of free boundaries. J. Comput. Phys. 39, 201–225 (1981)
- R. Mayon, Z. Sabeur, T. Mingyi, K. Djidjeli, Free surface flow and wave impact at complex solid structures, in 12th International Conference on Hydrodynamics, article 154, pp. 1–11 (2016)
- P.J. Martínez-Ferrer, D.M. Causon, L. Qian, C.G. Mingham, Z.H. Ma, A multi-region coupling scheme for compressible and incompressible flow solvers for two-phase flow in a numerical wave tank. Comput. Fluids 125, 116–129 (2016). https://doi.org/10.1016/j.compfluid.2015.11.005
- R. Wemmenhove, R. Luppes, A.E.P. Veldman, T. Bunnik, Application of a VOF method to model compressible two-phase flow in sloshing tanks, in Proceedings of the ASME 27th International Conference on Offshore Mechanics and Arctic Engineering, OMAE2008-57254, pp. 1–10 (2008)
- M. Jadidi, M. Tembely, S. Moghtadernejad, A. Dolatabadi, Coupled level set and volume of fluid method in openfoam with application to compressible two-Phase flow, in 22nd Annual Conference of the CFD Society of Canada, pp. 1–5 (2014)
- E. Johnsen, F. Ham, Preventing numerical errors generated by interface-capturing schemes in compressible multi-material flows. J. Comput. Phys. 231, 5705–5717 (2012). https://doi.org/10.1016/j.jcp.2012.04.048
- S.A. Beig, E. Johnsen, Maintaining interface equilibrium conditions in compressible multiphase flows using interface capturing. J. Comput. Phys. 302, 548-566 (2015). https://doi.org/10.1016/j.jcp.2015.09.018
- D.L. Youngs, Time-dependent multi-material flow with large fluid distortion: atomic weapons research establishment, Aldermaston, in Numerical Methods in Fluid Dynamics, ed. by K.W. Morton, Baines, M.J. (eds.) (Academic Press, 1982), pp. 273–285
- Q.M. Bui, D. Osei-Kuffuor, N. Castelletto, J.A. White, A scalable multigrid reduction framework for multiphase poromechanics of heterogeneous media. SIAM J. Sci. Comput. 42(2), B379–B396 (2020). https://doi.org/10.1137/19M1256117
- V. Inguva, A. Schulz, E.Y. Kenig, On methods to reduce spurious currents within VOF solver frameworks. Part 1: a review of the static bubble/droplet. Chem. Prod. Process. Model. 17(2), 121–135 (2022). https://doi.org/10.1515/cppm-2020-0052
- DIN EN 1676, Aluminium and aluminium alloys-alloyed ingots for remelting-specifications (Beuth Verlag GmbH, Berlin, 2020)
- H. Cao, C. Wang, J. Che, Z. Luo, L. Wang, L. Xiao, J. Wang, T. Hu, Effect of flow state of pure aluminum and A380 alloy on porosity of high pressure die castings. Materials (2019). https://doi.org/10.3390/ma12244219
- J. Eggers, E. Villermaux, Physics of liquid jets. Rep. Prog. Phys. 71, 1–79 (2008). https://doi.org/10.1088/0034-4885/71/3/036601
- E. Koya, M. Nakagawa, S. Kitagawa, J. Ishimoto, Y. Nakano, N. Ochiai, Atomization in high-pressure die casting-step 2 simulation of atomized flow of molten aluminum by LES-VOF method, in SAE Technical Paper, 2018-01-1393 (2018). https://doi.org/10.4271/2018-01-1393
- H.K. Barton, The pressure diecasting of metals. Metal. Rev. 9(36), 305–414 (1964). https://doi.org/10.1179/mtlr.1964.9.1.305
- M. Wörner, Numerical modeling of multiphase flows in microfluidics and micro process engineering: a review of methods and applications. Microfluid. Nanofluid. 12(6), 841–886 (2012). https://doi.org/10.1007/s10404-012-0940-8
- B. Sjögreen, H.C. Yee, Grid convergence of high order methods for multiscale complex unsteady viscous compressible flows. J. Comput. Phys. 185(1), 1-26 (2003). https://doi.org/10.1016/S0021-9991(02)00044-X
- S. Kohlstädt, On determining lost core viability in high-pressure die casting using computational continuum mechanics, Dissertation, KTH Royal Institute of Technology, Stockholm (2019)
9. Copyright:
- This material is "Dominik Boos and Klaus Drechsler and Swen Zaremba"'s paper: Based on "VIABILITY OF FLAX FIBER-REINFORCED SALT CORES FOR ALUMINUM HIGH-PRESSURE DIE CASTING IN EXPERIMENT AND SIMULATION".
- Paper Source: https://doi.org/10.1007/s40962-024-01461-y
This material was summarized based on the above paper, and unauthorized use for commercial purposes is prohibited.
Copyright © 2025 CASTMAN. All rights reserved.