This technical brief is based on the academic paper "Productivity Improvement by Value Stream Mapping in Die Casting Industry" by Pradip Gunaki and S.N. Teli, published in the Journal of Emerging Technologies and Innovative Research (JETIR) (2015). It is summarized and analyzed for HPDC professionals by the experts at CASTMAN.
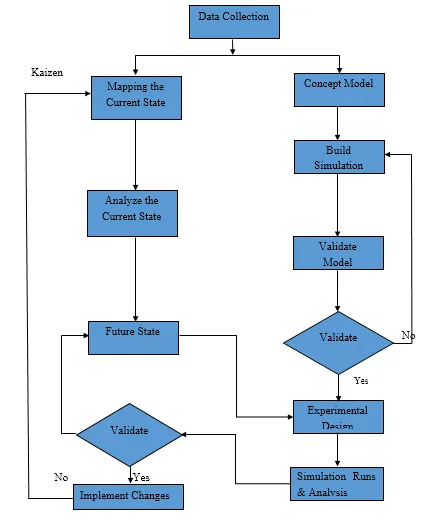
Keywords
- Primary Keyword: Value Stream Mapping in Die Casting
- Secondary Keywords: Lean Manufacturing, Cycle Time Reduction, Die Casting Process, Arena Simulation, Kaizen, Non-Value Added Activities, Productivity Improvement
Executive Summary
- The Challenge: A die casting facility was struggling with increased production cycle times and unidentified waste, making it difficult to meet customer demand and maintain efficiency.
- The Method: Researchers applied Value Stream Mapping (VSM), a core lean manufacturing tool, to visualize the entire production process. This was combined with Arena simulation software to precisely quantify value-added vs. non-value-added activities.
- The Key Breakthrough: The initial analysis revealed that a staggering 39.96% of the total production time was consumed by non-value-added activities, such as waiting, unnecessary transport, and over-production.
- The Bottom Line: By implementing targeted improvements based on Kaizen principles, the facility reduced total cycle time by 6.146% and slashed non-value-added activities by over 15 percentage points, boosting overall productivity and capacity.
The Challenge: Why This Research Matters for HPDC Professionals
In today's competitive market, die casting manufacturers are under constant pressure to be more efficient and flexible. As described in the paper's Problem Definition
, many facilities face the challenge of increasing cycle times that prevent them from producing the desired product volume to satisfy customer needs. This issue is often caused by hidden "non-value-added" activities within the value stream—steps that consume time and resources but add no value to the final product. Identifying and eliminating this waste is critical for improving productivity, meeting deadlines, and ensuring economic success.
The Approach: Unpacking the Methodology
To tackle this common industry problem, the researchers employed a powerful, two-pronged approach detailed in the paper's Research Methodology
and visualized in Figure 1 and Figure 2.
- Value Stream Mapping (VSM): They began by creating a "Current State Map" (Figure 6) of the die casting foundry. This involved meticulously documenting every step of the process—from raw material to dispatch—and collecting real-world data on cycle times, information flow, and material flow. This visualization tool is designed to make waste obvious.
- Simulation Modeling: The data from the VSM was used to build a dynamic model of the production line in Arena simulation software (Figure 7). This allowed the researchers to run virtual experiments, accurately quantify the time spent on value-added versus non-value-added tasks, and validate the impact of proposed changes before implementing them on the shop floor.
This combination of VSM and simulation provides a low-risk, high-impact framework for process improvement.
The Breakthrough: Key Findings & Data
The study produced clear, quantifiable results that highlight the power of this methodology.
- Finding 1: Quantifying the Waste: The initial simulation of the current state (Figure 10) confirmed the scale of the problem. The total production time was 65.08 minutes per part, with 39.96% of that time (nearly 26 minutes) being non-value-added. This included waiting time, material transfer, and other inefficiencies.
- Finding 2: Pinpointing the Bottlenecks: The Current State Map (Figure 6) visually identified the specific process steps and the time consumed by each, allowing the team to focus their improvement efforts where they would have the most significant impact.
- Finding 3: Implementing Lean Solutions: The researchers proposed corrective actions based on the Kaizen philosophy, including the 5S methodology (Sort, Straighten, Sweep, Sanitize, Sustain) to improve workplace organization and efficiency, as detailed in the
Kaizen
section. - Finding 4: Validating the Improvement: A "Future State Map" (Figure 15) was created to reflect the proposed changes. The simulation of this future state showed a reduction in total cycle time to 61.08 minutes per part and a dramatic drop in non-value-added time to just 24.57%. The comparison in Figure 16 clearly illustrates this significant improvement.
Practical Implications for Your HPDC Operations
This research offers a practical blueprint for any die casting facility looking to enhance productivity.
- For Process Engineers: The findings in the
Corrective Action for Improvement
section demonstrate that VSM is a highly effective tool for identifying specific, often overlooked, non-value-added activities. The paper suggests that by applying lean principles like Kaizen, engineers can systematically eliminate waste and streamline the production flow. - For Operations Managers: The use of simulation software, as detailed in the
Integration of Value Stream Mapping with Simulation
section, provides a powerful business case for lean initiatives. It allows you to quantify the potential gains and de-risk changes by validating them virtually before committing resources on the shop floor, ensuring a higher probability of success. - For Continuous Improvement Teams: This study reinforces the value of the Kaizen philosophy. The implementation of 5S, as mentioned in the paper, not only improves efficiency but also creates a cleaner, safer, and more organized work environment, which has a positive cascading effect on morale and quality.
Paper Details
Productivity Improvement by Value Stream Mapping in Die Casting Industry
1. Overview:
- Title: Productivity Improvement by Value Stream Mapping in Die Casting Industry
- Author: Pradip Gunaki, S.N. Teli
- Year of publication: 2015
- Journal/academic society of publication: Journal of Emerging Technologies and Innovative Research (JETIR)
- Keywords: Value Stream, Current Stream Mapping, Future State Mapping, Takt time, Cycle Time, Lean Manufacturing, Simulation.
2. Abstract:
Value Stream Mapping has the reputation of uncovering waste in manufacturing, production and business processes by identifying and removing or streamlining non-value-adding steps. A flow diagram showing the process is drawn to reflect the current state of the operation. The non-value actions are identified in each step and between each step by their waste of time and resources. The process is analyzed with the help of simulation software for opportunity to drastically reduce and simplify it to the fewest actions necessary. By reducing wastefulness the proportion of value adding time in the whole process rises and the process throughput speed is increased. This makes the redesigned process more effective (the right things are being done) and more efficient (needing fewer resources). This paper explains about the corrective methods for eliminating the non-value added activities in the die casting industry with the help of Arena simulation software. The reengineered process is flow charted in its future state with process steps and information flows redesigned, simplified and made less expensive and increase in productivity.
3. Introduction:
The paper highlights the increasing intensity of global market competition, which forces manufacturers to develop more flexible and high-quality production systems while reducing costs. It introduces Value Stream Mapping (VSM) as a communication, business planning, and change management tool. The primary focus of VSM is cost reduction by eliminating non-value-added activities throughout a product's value stream, a philosophy known as lean manufacturing.
4. Summary of the study:
Background of the research topic:
The research is set in a die casting company ("Company XYZ") that is driven to meet customer demands but faces challenges in its product realization process.
Status of previous research:
The literature review cites several studies on VSM in manufacturing, including its application in product development, its ability to identify opportunities for improvement, and its role in visualizing and streamlining work processes to decrease waste.
Purpose of the study:
The study aims to improve productivity in a die casting facility by identifying and eliminating waste. The core problem identified is an increased cycle time due to non-value-added activities, which prevents the company from meeting customer demand. The goal is to use VSM and lean principles to create a more efficient and flexible production system.
Core study:
The core of the study involves applying the VSM methodology to the foundry shop floor of the die casting company. This includes gathering data, creating a current state map to identify problems, and then developing a future state map with proposed improvements. The study integrates VSM with Arena simulation software to model the process, quantify waste, and validate the effectiveness of the proposed changes.
5. Research Methodology
Research Design:
The research follows the VSM methodology outlined in Figure 1. It starts with identifying the critical shop floor (foundry), collecting information and material flow data, identifying wastes, drawing a current state map, identifying problems and improvement strategies, and finally drawing a future state map. This process is integrated with simulation modeling as shown in Figure 2.
Data Collection and Analysis Methods:
Data was collected through site visits, structured interviews with key personnel (managers, supervisors, operators), and observation of the production process across day and night shifts. The collected data on process cycle times (Table 2) was then used to build the VSM maps and the Arena simulation model for analysis.
Research Topics and Scope:
The study is a case study focused on the foundry of an aluminum die casting company. The scope is limited to analyzing and improving the production process for a specific product ("Pivot Housing") by reducing cycle time and eliminating non-value-added activities.
6. Key Results:
Key Results:
The initial analysis of the Current State Map (Figure 6) and simulation (Figure 10) revealed a total production time of 65.08 minutes per part. The simulation quantified that 39.96% of this time was non-value-added. After applying corrective actions based on Kaizen, the Future State Map (Figure 15) showed a reduced total cycle time of 61.08 minutes per part. The simulation analysis confirmed a reduction in total cycle time by 6.146% and a reduction in non-value-added activities from 39.96% to 24.57%.
Figure Name List:
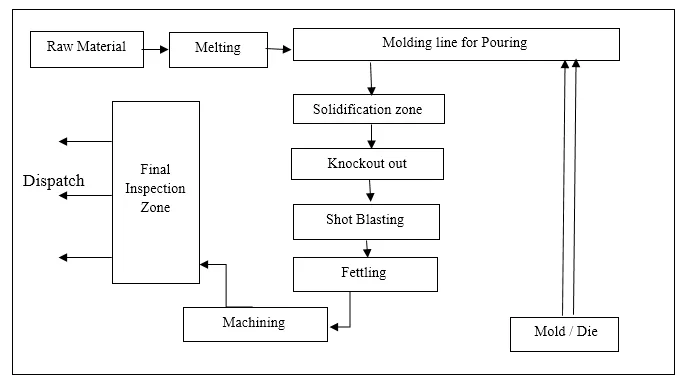
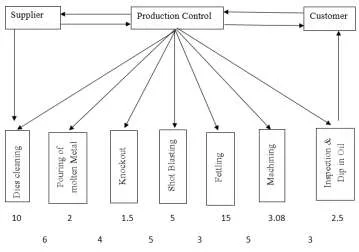
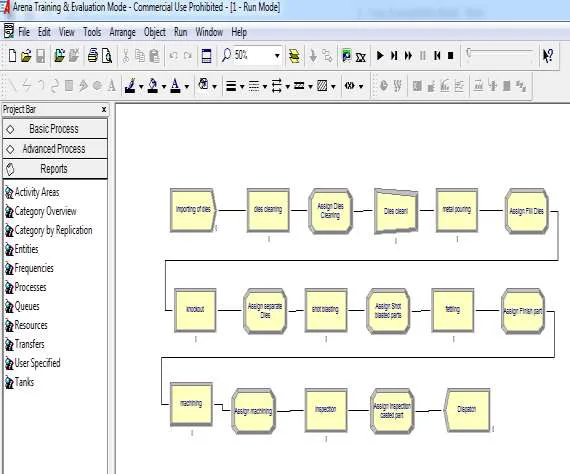
- Figure 1. Value Stream Mapping Methodology
- Figure 2. Integration of Value Stream Mapping with Simulation
- Figure 3. Site Visits
- Figure 4. Structured Interviews
- Figure 5. Current Foundry Production Lay out
- Figure 6. Current State Map
- Figure 7. Arena Simulation Model for Current State Map
- Figure 8. Key Performance Indicator
- Figure 9. Category Overview of Queue
- Figure 10. Category Review of Time Entity
- Figure 11. Kaizen Umbrella
- Figure 12. Arena Simulation Model
- Figure 13. Category Review of non-value added activities
- Figure 14. Category Overview of Product Entity
- Figure 15. Future State Map
- Figure 16. Comparison between Current & Future State Map
7. Conclusion:
The study concludes that Value Stream Mapping is an effective tool for eliminating waste in a die casting industry. The results show a 15% reduction in waste from non-value-added activities, leading to a total cycle time reduction of 6.146%. The paper emphasizes that the integration of VSM with simulation software is crucial for properly analyzing the system and identifying opportunities to improve productivity.
8. References:
- 1) R.M. Belokar, Sandeep Singh Kharb, Vikas Kumar “An Application of Value Stream Mapping In Automobile Industry: A Case Study”, International Journal of Innovative Technology and Exploring Engineering (IJITEE) ISSN: 2278-3075, Vol.- 1(2), pp.231-236, (2012).
- 2) Muhammad Abdus Samad et.Al, “Value Stream Mapping To Reduce Manufacturing Lead Time In A Semi-Automated Factory”, Asian Transactions On Engineering, Vol.2 Issue 06, pp. 22-28, (2013).
- 3) Danijela Gracanina & BorutBuchmeister, BojanLalic “Using Cost-Time Profile for Value Stream Optimization”, Procedia Engineering 69 (2014), p. 1225 – 1231.
- 4) Rahani AR, Muhammad al-Ashraf “Production Flow Analysis through Value Stream Mapping: A Lean Manufacturing Process Case Study”, Procedia Engineering, Vol.41, pp.1727 – 1734, (2012).
- 5) Mahmoud Al-Odeh et.al, “Value Stream Mapping: Recreating an Industrial Environment in an Educational Setting”,
- Proceedings of The (2014) IAJC/ISAM Joint International Conference ISBN, p.978-1-60643-379-9.
- 6) Palak P. Sheth1 et.Al, “Value Stream Mapping: A Case Study of Automotive Industry”, Ijret (2014), p.2321-7308.
- 7) Rehab M. Ali et.al “Dynamic Lean Assessment for Takt Time Implementation”, Procedia CRIP 17 (2014), p.577-581.
- 8) G. M. Gohane, A. S. Bonde & C.S. Sable,” Improvement of Productivity Using Value Stream Mapping”, IJSRD -International Jour nal for Scientifi c Research & Development| Vol. 2(8), ISSN (online): 2321-0613, pp.1-5, (2015).
- 9) G. Sahitya Reddy, Harsha Lingareddy & K.Jagadeeshwar, “Value Stream Mapping In A Manufacturing Industry”, International Journal of Advanced Engineering Technology E-ISSN 0976-3945, Vol.4(2), pp.20-23,(2013).
- 10) Binu Bose V & K N Anilkumar, “Reducing rejection rate of castings using Simulation Model”, Proceedings of International Conference on Energy and Environment, International Journal of Innovative Research in Science, Engineering and Technology, Vol. 2(1), pp.589-597,(2013).
- 11) Petter Solding & Per Gullandar, “Concepts for Simulation Based Value Stream Mapping”, Proceedings of the 2009 Winter Simulation Conference, pp.2231-2237, (2009).
- 12) Wei Xia & Jiwen Sun, “Simulation guided value stream mapping and lean improvement:A case study of a tubular machining facility”, Journal of Industrial Engineering and Management, JIEM,pp.456-476, (2013).
- 13) Abu Md. Saifuddoha, Md. Ahasan Habib2, Sohana Yasmin Sumi, Md. Jennurine, Md. Saiful Islam, “Minimization Of Waste By Applying Value Stream Mapping In The Supply Chain Of Cement Industry”, IOSR Journal of Business and Management (IOSR-JBM), ISSN: 2319-7668, Volume 9, Issue 3,pp.79-84,(2013).
- 14) S. Santhosh kumar, M. Pradeep kumar, “Cycle Time Reduction of truck body assembly in an automobile industry by lean principles”, Procedia Materials science, Vol.5, pp.1853-1862, (2014).
- 15) Schönemann, M. et.al “Integrating product characteristics into extended value stream modeling”, Procedia CIRP (2014) p.368 – 373.
Expert Q&A: Your Top Questions Answered
Q1: What was the single biggest source of inefficiency identified in this study?
A1: The study concluded that non-value-added activities were the biggest source of inefficiency, accounting for 39.96% of the total production time. As stated in the Corrective Action for Improvement
section, this includes activities like waiting, unnecessary transportation, and over-production.
Q2: What specific tool did the researchers use to visualize and quantify this waste?
A2: The researchers used a combination of two tools, as detailed in the Research Methodology
. They first used Value Stream Mapping (VSM) to create a visual map of the entire process (Figure 6) and then used Arena simulation software (Figure 7) to build a dynamic model that precisely quantified the time spent on value-added versus non-value-added activities.
Q3: What was the primary solution proposed to fix the problem?
A3: The primary solution, described in the Kaizen
section, was the implementation of lean manufacturing principles. Specifically, the paper highlights the Kaizen philosophy and the 5S methodology (Sort, Straighten, Sweep, Sanitize, Sustain) to improve the work environment and streamline processes.
Q4: How much tangible improvement did the proposed changes deliver?
A4: According to the simulation analysis
results on page 15, the implemented changes resulted in a 6.146% reduction in total cycle time and a significant reduction in non-value-added activities from 39.96% down to 24.57%.
Q5: Is this finding applicable to any die casting operation?
A5: While this research was a specific case study of an aluminum die casting foundry ("Company XYZ"), the Conclusion
states that "Value stream mapping tool can be used effectively in any kind of sectors as it is a world class manufacturing tool." The principles of identifying and eliminating waste are universally applicable to manufacturing processes.
Q6: What is the direct, practical takeaway from this paper for a die casting facility?
A6: The core takeaway, based on the paper "Productivity Improvement by Value Stream Mapping in Die Casting Industry," is that integrating VSM with simulation software provides a powerful, data-driven method to identify, quantify, and eliminate waste, leading to direct improvements in productivity and cycle time.
Conclusion & Next Steps
This research provides a valuable roadmap for enhancing productivity in HPDC operations. By moving beyond guesswork and using systematic tools like VSM and simulation, the findings offer a clear, data-driven path toward improving quality, reducing waste, and optimizing production flow.
At CASTMAN, we are dedicated to applying the latest industry research to solve our customers' most challenging die casting problems. If the issues of high cycle times and hidden inefficiencies discussed in this paper resonate with your operational goals, contact our engineering team to discuss how we can help you implement these advanced lean principles in your components and supply chain.
References
- 1) R.M. Belokar, Sandeep Singh Kharb, Vikas Kumar “An Application of Value Stream Mapping In Automobile Industry: A Case Study", International Journal of Innovative Technology and Exploring Engineering (IJITEE) ISSN: 2278-3075, Vol.- 1(2), pp.231-236, (2012).
- 2) Muhammad Abdus Samad et.Al, “Value Stream Mapping To Reduce Manufacturing Lead Time In A Semi-Automated Factory", Asian Transactions On Engineering, Vol.2 Issue 06, pp. 22-28, (2013).
- 3) Danijela Gracanina & BorutBuchmeister, BojanLalic “Using Cost-Time Profile for Value Stream Optimization”, Procedia Engineering 69 (2014), p. 1225 – 1231.
- 4) Rahani AR, Muhammad al-Ashraf “Production Flow Analysis through Value Stream Mapping: A Lean Manufacturing Process Case Study”, Procedia Engineering, Vol.41, pp.1727 – 1734, (2012).
- 5) Mahmoud Al-Odeh et.al, “Value Stream Mapping: Recreating an Industrial Environment in an Educational Setting", Proceedings of The (2014) IAJC/ISAM Joint International Conference ISBN, p.978-1-60643-379-9.
- 6) Palak P. Sheth1 et.Al, “Value Stream Mapping: A Case Study of Automotive Industry”, Ijret (2014), p.2321-7308.
- 7) Rehab M. Ali et.al “Dynamic Lean Assessment for Takt Time Implementation”, Procedia CRIP 17 (2014), p.577-581.
- 8) G. M. Gohane, A. S. Bonde & C.S. Sable," Improvement of Productivity Using Value Stream Mapping", IJSRD - International Jour nal for Scientifi c Research & Development| Vol. 2(8), ISSN (online): 2321-0613, pp.1-5, (2015).
- 9) G. Sahitya Reddy, Harsha Lingareddy & K.Jagadeeshwar, "Value Stream Mapping In A Manufacturing Industry", International Journal of Advanced Engineering Technology E-ISSN 0976-3945, Vol.4(2), pp.20-23,(2013).
- 10) Binu Bose V & K N Anilkumar, “Reducing rejection rate of castings using Simulation Model”, Proceedings of International Conference on Energy and Environment, International Journal of Innovative Research in Science, Engineering and Technology, Vol. 2(1), pp.589-597,(2013).
- 11) Petter Solding & Per Gullandar, “Concepts for Simulation Based Value Stream Mapping", Proceedings of the 2009 Winter Simulation Conference, pp.2231-2237, (2009).
- 12) Wei Xia & Jiwen Sun, “Simulation guided value stream mapping and lean improvement: A case study of a tubular machining facility", Journal of Industrial Engineering and Management, JIEM,pp.456-476, (2013).
- 13) Abu Md. Saifuddoha, Md. Ahasan Habib2, Sohana Yasmin Sumi, Md. Jennurine, Md. Saiful Islam, “Minimization Of Waste By Applying Value Stream Mapping In The Supply Chain Of Cement Industry”, IOSR Journal of Business and Management (IOSR-JBM), ISSN: 2319-7668, Volume 9, Issue 3,pp.79-84,(2013).
- 14) S. Santhosh kumar, M. Pradeep kumar, “Cycle Time Reduction of truck body assembly in an automobile industry by lean principles", Procedia Materials science, Vol.5, pp.1853-1862, (2014).
- 15) Schönemann, M. et.al “Integrating product characteristics into extended value stream modeling”, Procedia CIRP (2014) p.368 – 373.
Copyright
- This material is an analysis of the paper "Productivity Improvement by Value Stream Mapping in Die Casting Industry" by Pradip Gunaki and S.N. Teli.
- Source of the paper: https://www.researchgate.net/publication/317427739ProductivityImprovementbyValueStreamMappinginDieCastingIndustry
- This material is for informational purposes only. Unauthorized commercial use is prohibited.
- Copyright © 2025 CASTMAN. All rights reserved.