This technical brief is based on the academic paper "Preparation and properties of a binary composite water-soluble salt core for zinc alloy by die casting" by TU Suo, FAN Zi-tian, LIU Fu-chu, and GONG Xiao-long, published in the Chinese Journal of Engineering (2017). It is summarized and analyzed for HPDC professionals by the experts at CASTMAN.
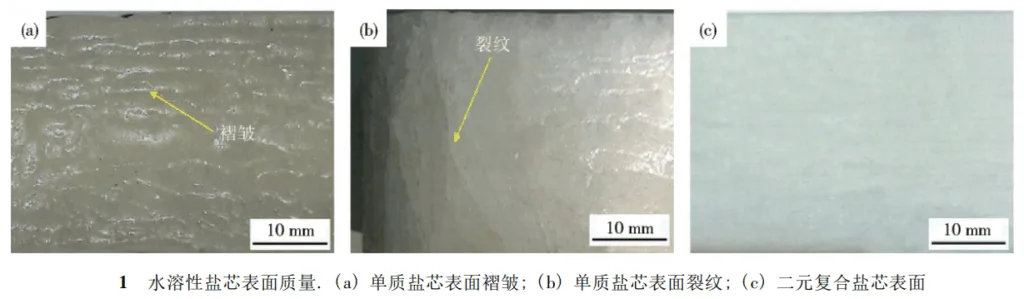
Keywords
- Primary Keyword: water-soluble salt core for zinc alloy
- Secondary Keywords: HPDC zinc alloy, binary composite salt core, potassium chloride potassium nitrate core, core strength in die casting, complex internal cavity casting, salt core properties
Executive Summary
- The Challenge: Manufacturing zinc alloy die-cast parts with complex internal cavities is a major hurdle. Traditional cores are either difficult to remove (ceramic/sand) or too weak and prone to cracking (single-component salt cores), which is a significant issue given the high density of zinc alloys.
- The Method: Researchers developed a novel binary composite water-soluble salt core (WSSC) using a mixture of 20% potassium chloride (KCl) and 80% potassium nitrate (KNO₃) formed by a gravity pouring process.
- The Key Breakthrough: This composite core demonstrates vastly superior performance, achieving a bending strength of 21.2 MPa—many times stronger than single-salt cores. It also features a smooth, crack-free surface and excellent water solubility for easy removal.
- The Bottom Line: This research presents a viable, high-strength salt core that enables the production of intricate and complex zinc alloy components, opening new doors for advanced product design in HPDC.
The Challenge: Why This Research Matters for HPDC Professionals
For decades, engineers have struggled to produce zinc alloy die castings with elaborate internal geometries. While zinc alloys offer excellent castability and mechanical properties, creating features like long, slender channels or complex undercuts is problematic.. Conventional sand or ceramic cores, while strong, are notoriously difficult to clean out from the finished casting, especially in thin-walled sections..
An alternative, the water-soluble salt core, offers the promise of easy, residue-free removal. However, existing single-component salt cores lack the mechanical strength required for zinc alloy HPDC.. Zinc's higher density compared to aluminum or magnesium means the molten metal exerts greater force during injection. This often leads to core failure, cracking, and dimensional inaccuracy in the final part. This study directly addresses this critical industry need for a salt core that is both strong enough to withstand the rigors of zinc HPDC and easily removable.
The Approach: Unpacking the Methodology
To solve the strength problem, the researchers created a binary composite salt core from a mixture of high-melting point potassium chloride (KCl) and low-melting point potassium nitrate (KNO₃). [ABSTRACT]. The specific composition studied was 20% KCl and 80% KNO₃ (molar ratio).
The methodology was as follows:
- The KCl and KNO₃ salts were mixed and melted in an electric furnace.
- The molten salt mixture was then poured into a pre-heated steel mold using a gravity casting process to form the core test samples. [1.3.1].
- These composite cores were then subjected to a battery of tests and compared directly against cores made from pure KCl and pure KNO₃.
- Advanced analytical techniques, including Scanning Electron Microscopy (SEM) and X-ray Diffraction (XRD), were used to examine the microstructure and phase composition to understand the source of the improved properties. [1.3.3, ABSTRACT].
The Breakthrough: Key Findings & Data
The results clearly demonstrate the superior performance of the 20% KCl-80% KNO₃ binary composite core compared to its single-component counterparts.
- Finding 1: Dramatically Increased Bending Strength: The composite core achieved a bending strength of 21.2 MPa. This is over 5 times stronger than the pure KCl core (4.01 MPa) and over 6 times stronger than the pure KNO₃ core (3.45 MPa). [Table 1]. This high strength is critical for surviving the high-pressure injection of zinc alloy.
- Finding 2: Superior Surface Quality: Macroscopic observation revealed that pure salt cores suffered from significant surface folds and cracks. In contrast, the binary composite core was smooth and largely free of defects, which translates to a better internal surface finish on the final cast product. [Fig. 1].
- Finding 3: Optimized Physical and Dissolution Properties: The composite core showed lower apparent porosity (0.458%) than pure cores, indicating a denser, more robust structure. [Table 1]. It also maintained a high water-soluble rate of 208.63 kg·min⁻¹·m⁻³ in 80°C water, ensuring fast and efficient removal after casting. [Table 1].
- Finding 4: A Unique Strengthening Mechanism: SEM analysis revealed the reason for the composite's high strength. Its microstructure consists of fine, interlocked grains. When a crack attempts to form, it is forced to deflect and travel along a much longer, more complex path around these grains, dissipating energy and resisting fracture. This is a significant improvement over the brittle, direct fracture path seen in pure salt cores. [Fig. 4, Fig. 6].
Practical Implications for Your HPDC Products
The findings of this paper have direct, actionable implications for manufacturers seeking to push the boundaries of zinc alloy component design.
- For Part Designers: The exceptional bending strength of 21.2 MPa means you can now confidently design parts with more intricate and slender internal passageways, previously impossible to cast reliably. This allows for greater design freedom, component consolidation, and the creation of parts with higher functionality.
- For Process Engineers: The research suggests that using this binary composite core can lead to higher casting yields. Its resistance to cracking and fracture during injection minimizes core-related scrap. Furthermore, the high dissolution rate (208.63 kg·min⁻¹·m⁻³ at 80°C) points to faster, more efficient core removal, potentially reducing cycle times and operational costs. [Table 1].
- For Quality Control: The smooth surface of the composite core, as shown in Figure 1, directly translates to a superior internal surface finish in the final zinc casting. This can reduce or eliminate the need for costly and time-consuming secondary finishing operations.
Paper Details
Preparation and properties of a binary composite water-soluble salt core for zinc alloy by die casting
1. Overview:
- Title: Preparation and properties of a binary composite water-soluble salt core for zinc alloy by die casting
- Author: TU Suo, FAN Zi-tian, LIU Fu-chu, GONG Xiao-long
- Year of publication: 2017
- Journal/academic society of publication: Chinese Journal of Engineering, Vol. 39, No. 11
- Keywords: water-soluble salt core; potassium nitrate; potassium chloride; composite salt core; gravity pouring process; die casting
2. Abstract:
For realizing complicated shapes of the inner cavity of zinc alloy castings by pressure die casting, the problem of poor leachability has to be solved and the high-strength requirement of the water-soluble salt core should be met. High-melting potassium chloride salt and low-melting potassium nitrate salt were used as the core materials. High-strength binary composite water-soluble salt core (WSSC) was formed by the process of melting and gravity pouring. The performance characteristics of the potassium chloride core, potassium nitrate core, and binary composite WSSC (20% KCI-80% KNO₃) were investigated. Scanning electron microscopy (SEM) and X-ray diffraction (XRD) studies were performed to examine the micro-morphology and phase composition of WSSC. The results indicate the following: the binary composite WSSC has excellent comprehensive performance, its bending strength can exceed 21.2 MPa, the 24 h hydroscopicity rate is 0.568%, the water-soluble rate can exceed 208.63 kg·min⁻¹·m⁻³ in water at 80°C and its surface has no cracks and folds unlike the pure salt core. Crack growth in the binary composite salt core occurs by deflection, which is the main reason for the improvement in bending strength. [ABSTRACT].
3. Introduction:
Zinc alloys are widely used for high-quality components due to their low melting point, high strength, and corrosion resistance.. Many of these components require complex internal cavities, which are typically formed using cores. However, for zinc alloy die casting, conventional cores present significant challenges. Resin sand and ceramic cores are difficult to clean out post-casting. Water-soluble salt cores are a promising alternative and have been used successfully in aluminum and magnesium die casting.. However, zinc alloys have a higher density, which demands a core with much higher strength. Previous studies have shown that single-component salt cores are often too weak and prone to cracking.. Therefore, developing a high-strength, easily removable salt core specifically for zinc alloy die casting is of great practical importance.
4. Summary of the study:
Background of the research topic:
The need to create complex internal geometries in zinc alloy die-cast parts is limited by the performance of existing core materials.
Status of previous research:
Previous work has shown that single-component water-soluble salt cores are generally too weak and susceptible to cracking to be used effectively in zinc alloy die casting, which requires higher core strength than aluminum or magnesium casting..
Purpose of the study:
To develop and characterize a high-strength, binary composite water-soluble salt core suitable for use in zinc alloy die casting to overcome the limitations of existing core technologies.
Core study:
The study focused on the preparation and performance analysis of a 20% KCl-80% KNO₃ binary composite salt core. It compared its mechanical properties (bending strength), physical properties (porosity, hygroscopicity, dissolution rate), and surface quality against pure KCl and pure KNO₃ cores. The microstructure was analyzed to understand the strengthening mechanism.
5. Research Methodology
Research Design:
The research was designed as a comparative study. A binary composite salt core (20% KCl-80% KNO₃) was fabricated and its performance was benchmarked against two control samples: a pure KCl core and a pure KNO₃ core.
Data Collection and Analysis Methods:
- Core Fabrication: A gravity pouring method was used where molten salt was poured into a 22.36 mm × 22.36 mm × 173.36 mm steel mold. [1.2, 1.3.1].
- Mechanical Testing: Bending strength was measured using a SWG lever-type universal strength testing machine. [1.2].
- Physical Testing: Apparent porosity was determined using Archimedes' principle. Hygroscopicity was measured by weight gain in a 98%-100% relative humidity environment. The water-soluble rate was calculated by timing the dissolution of a standard-sized sample. [1.3.2].
- Microstructural Analysis: A Quanta 200 scanning electron microscope (SEM) was used to observe the fracture surfaces and microstructure. An Empyrean X-ray diffractometer (XRD) was used to identify the phase composition of the composite core. [1.2, 1.3.3].
Research Topics and Scope:
The research was limited to a specific composition (20% KCl-80% KNO₃) of a water-soluble salt core intended for zinc alloy die casting. It did not investigate suitability for other alloys like aluminum or magnesium, and in fact, noted it would be unsuitable for them. [Introduction].
6. Key Results:
Key Results:
The binary composite salt core showed significantly improved properties over single-component cores. Its bending strength reached 21.2 MPa, its surface was smooth and free of cracks, and it possessed a dense microstructure. [Table 1, Fig. 1]. The primary reason for the increased strength was identified as a crack deflection mechanism, where the composite microstructure forces cracks to follow a longer, more tortuous path, thus increasing fracture toughness. [Fig. 6, Fig. 7].
Figure Name List:
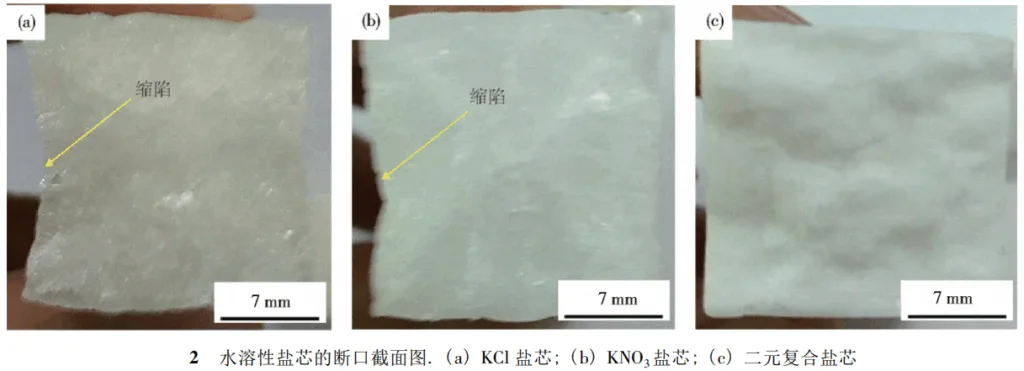
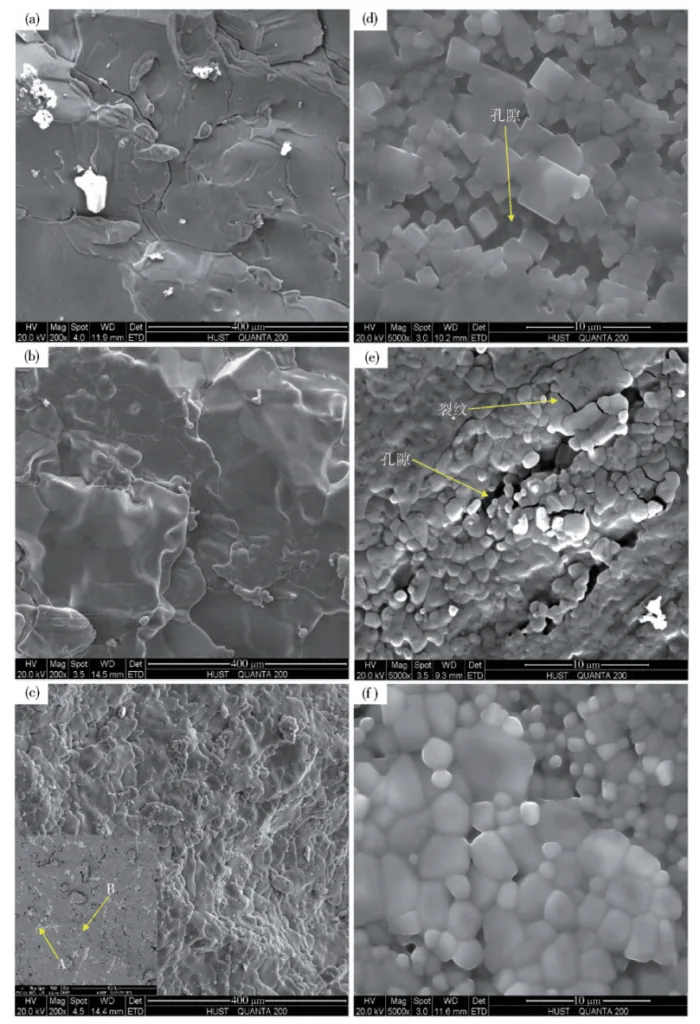
- Fig. 1 Surfaces quality of WSSC: (a) folds of pure WSSC; (b) cracks of pure WSSC; (c) surface of binary composite WSSC
- Fig. 2 Fracture macrographs of WSSC: (a) KCI WSSC; (b) KNO₃ WSSC; (c) binary composite WSSC
- Fig. 3 Phase diagram of KNO₃-KCl binary system
- Fig. 4 Morphology of three kinds of WSSCs: (a) fracture of KCI WSSC; (b) fracture of KNO₃ WSSC; (c) fracture of binary composite WSSC; (d) solidified structure of KCI WSSC; (e) solidified structure of KNO₃ WSSC; (f) solidified structure of binary composite WSSC
- Fig. 5 X-ray diffraction pattern of binary composite WSSC
- Fig. 6 Schematic drawings of strengthening mechanisms of WSSC
- Fig. 7 Crack curves occurred at WSSC: (a) KCI WSSC; (b) KNO₃ WSSC; (c) binary composite WSSC
7. Conclusion:
The study successfully demonstrated that a 20% KCl-80% KNO₃ binary composite water-soluble salt core has excellent properties for zinc alloy die casting. It exhibits superior surface quality and a high bending strength of 21.2 MPa. [Conclusion (1)]. The improved strength is attributed to a crack-deflection mechanism within its dense, composite microstructure. [Conclusion (2)]. The authors conclude that this development is promising for the industry but note that challenges such as shrinkage and hygroscopicity still need to be addressed for widespread practical application. [Conclusion (3)].
8. References:
- Zhang X. Casting zinc alloys research and application. Energy Energy Conservation, 2012(4): 93
- Li K L, Wu C J, Peng H P, et al. Effect of Mg on the solidification structure and growth of the intermetallic layer of a Zn-41% Al alloy coating. Chin J Eng, 2016, 38(8): 1123
- Luo J X. The research and application of high pressure resistant dissolvable core. Foundry, 2002, 51(2): 92
- Huang R H, Zhang B P. Progress and analysis of salt core made under high pressure for die casting. Foundry, 2016, 65(8): 757
- Yaokawa J, Anzai K, Yamada Y, et al. Castability and strength of potassium chloride-ceramic composite salt cores. J Japan Foundry Eng Soc, 2004, 76(10): 823
- Yaokawa J, Miura D, Anzai K, et al. Strength of salt core composed of alkali carbonate and alkali chloride mixtures made by casting technique. Mater Trans, 2007, 48(5): 1034
- Yaokawa J, Anzai K, Yamada Y. Expandable Core for Use in Casting: US Patent, US 11/377,125. 2006-3-16
- Hirokawa K. Disintegrative Core for High Pressure Casting, Method for Manufacturing the Same, and Method for Extracting the Same: US Patent, 6755238. 2004-6-29
- Xu P C. Research on High Strength & Water-soluble Halides Salt-core [Dissertation]. Wuhan: Huazhong University of Science and Technology, 2007
- Chen W P, Zheng H W. Progress in research on water-soluble salt-core used for high-pressure casting. Foundry Technol, 2010, 31(2): 241
- COSTIND. HB 5352.4—2004 Test method for properties of investment casting shell-Part 4: determination of permeability to gas. Beijing: Beijing Aeronautical Materials Research Institute, 2004
- Zheng H W. Research on the Water-soluble Salt-core Used by High-pressure Casting [Dissertation]. Guangzhou: South China University of Technology, 2010
- Foundry Branch of China Mechanical Engineering Society. Foundry Handbook: Casting Process. 2nd Ed. Beijing: Mechanical Industry Press, 2003
- CRCT. FTsalt-FACT Salt Phase Diagrams [DB/OL]. Centre for Research in Computational Thermochemistry (2010–04–10) [2017–01–15]. http://www.crct. polymtl.ca/fact/documentation/FTsalt/FTsalt_Figs.htm
- Huang R H, Zhang B P. Study on the composition and properties of salt cores for zinc alloy die casting. Int J Metalcasting, 2017, 11(3): 440
Expert Q&A: Your Top Questions Answered
Q1: What was the single most critical factor identified in this study for improving core strength?
A1: The study concluded that the formation of a binary composite microstructure was the most critical factor. This structure, with its fine, interlocked grains, forces cracks to deflect and take a longer path, which is the primary reason for the significant increase in bending strength. This is detailed in the "Conclusion" and visualized in the schematic in Figure 6.
Q2: How does this research compare to traditional methods for addressing the problem?
A2: The paper's Introduction
notes that traditional methods like sand or ceramic cores are difficult to clean, while simple water-soluble cores are too weak and crack-prone for zinc HPDC. This research introduces a binary composite approach that provides both the high strength needed to withstand casting pressures and the easy water-based removal that simplifies production.
Q3: Is this finding applicable to all types of alloys, or a specific one?
A3: The research, as described in the Introduction
, was specifically conducted for zinc alloy die casting. The paper explicitly states the composite core is not suitable for aluminum alloys (due to surface melting) or magnesium alloys (due to violent chemical reactions).
Q4: What specific measurement or simulation technique did the researchers use to arrive at this conclusion?
A4: The researchers utilized a "SWG lever-type universal strength testing machine" to measure bending strength, "Scanning Electron Microscopy (SEM)" to analyze the microstructure and fracture surfaces, and "X-ray Diffraction (XRD)" to determine the phase composition of the core. This is explained in the "1.2 Test Equipment" and "1.3 Test Methods" sections.
Q5: According to the paper, what is the main limitation or area for future research?
A5: The authors state in the Conclusion
(point 3) that key limitations for practical application are issues related to "shrinkage, hygroscopicity, and toughening," and suggest these are the critical problems that need to be solved in future research.
Q6: What is the direct, practical takeaway from this paper for a die casting facility?
A6: The core takeaway is that by using a 20% KCl-80% KNO₃ binary composite salt core, it is possible to achieve the high strength required to produce zinc alloy castings with complex internal geometries, while still benefiting from simple and fast water-based core removal, a conclusion strongly supported by the overall results of the paper, "Preparation and properties of a binary composite water-soluble salt core for zinc alloy by die casting".
Conclusion & Next Steps
This research provides a valuable roadmap for enhancing the production of complex zinc alloy components in HPDC. The findings offer a clear, data-driven path toward improving part integrity, enabling greater design freedom, and potentially optimizing production efficiency.
At CASTMAN, we are dedicated to applying the latest industry research to solve our customers' most challenging die casting problems. If the issues discussed in this paper resonate with your operational goals, contact our engineering team to discuss how we can help you implement these advanced principles in your components.
Copyright
- This material is a paper by "TU Suo, FAN Zi-tian, LIU Fu-chu, GONG Xiao-long". Based on "Preparation and properties of a binary composite water-soluble salt core for zinc alloy by die casting".
- Source of the paper: DOI: 10.13374/j.issn2095-9389.2017.11.012
This material is for informational purposes only. Unauthorized commercial use is prohibited.
Copyright © 2025 CASTMAN. All rights reserved.