This article introduces the paper "Three-Phase 75 kW Brushless Direct Current Motor for Electric Vehicles: Different Power Stage Design, Calculation of Losses, Cooling Techniques, and Comparison".
1. Overview:
- Title: Three-Phase 75 kW Brushless Direct Current Motor for Electric Vehicles: Different Power Stage Design, Calculation of Losses, Cooling Techniques, and Comparison
- Authors: Ali Bahadir, Omer Aydogdu, Elif Bahadir
- Year of Publication: 2024
- Journal/Conference: Applied Sciences
- Keywords: brushless DC motor, electric vehicles (EV), power stage, cooling system, losses
2. Research Background:
The increasing need to reduce CO2 and SO2 emissions due to climate change necessitates improvements in electric vehicle efficiency. While Brushless Direct Current (BLDC) motors are widely used in EVs due to their high power density, efficiency, and reliability, their operational lifespan is limited by high internal heat generation and inefficient heat dissipation. Therefore, research focusing on reducing electric motor losses and enhancing efficiency is crucial. Existing studies often focus solely on battery or motor cooling, neglecting the energy consumption of the cooling system itself.
3. Research Objectives and Questions:
- Research Objective: To enhance the efficiency of electric vehicles by designing, calculating losses for, and comparing three different power stage designs and cooling systems (air cooling, fan-assisted air cooling, and liquid cooling) for a 75 kW BLDC motor.
- Key Research Questions: How can the performance of three different power stage designs and cooling systems be compared? How can the efficiency and losses of each cooling system be quantified?
- Research Hypothesis: The liquid cooling system will be more efficient than air cooling and fan-assisted air cooling systems.
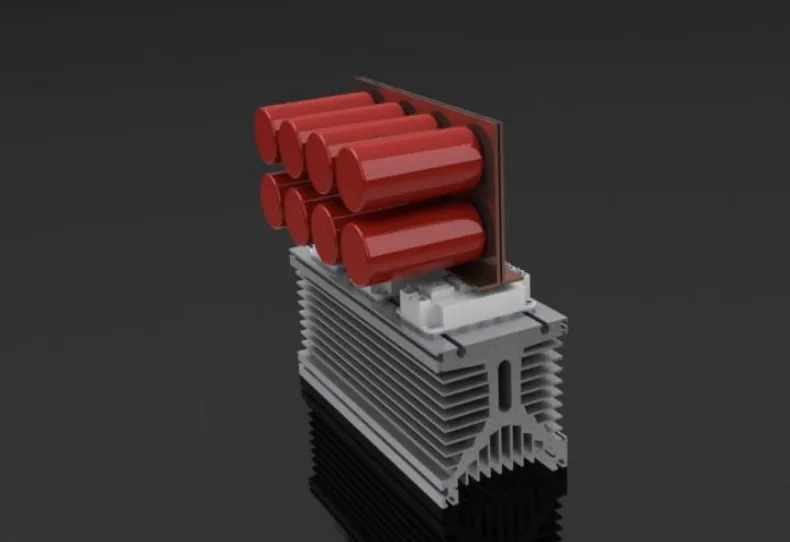
4. Research Methodology:
- Research Design: An electric vehicle model was built using MATLAB/Simulink. Three different power stage designs for a 75 kW BLDC motor were developed. Three different cooling systems were designed and their performance compared.
- Data Collection Methods: Data was collected through simulation and experimentation. IGBT datasheets were used for loss calculations. Cooling system performance was evaluated through temperature measurements.
- Analysis Methods: Loss calculations involved separately calculating switching and conduction losses and then summing them. Cooling system performance comparisons were based on temperature and efficiency.
- Research Subjects and Scope: The study focused on three power stage designs and three cooling systems (air cooling, fan-assisted air cooling, and liquid cooling) for a 75 kW BLDC motor.
5. Main Research Findings:
- Key Findings: The liquid cooling system proved to be the most efficient, followed by fan-assisted air cooling, and then air cooling. The spacing between IGBT modules significantly impacted thermal resistance.
- Quantitative/Qualitative Analysis Results: Total losses for the three power systems were calculated to be approximately 2.3 kW, resulting in a system efficiency of about 97%. The liquid cooling system maintained an outlet temperature of 20.5 °C, removing 4.5 °C from the system. Without cooling, IGBT temperatures reached 96 °C, but with 20mm spacing, this reduced to 90 °C.
- Data Interpretation: Efficient heat removal through the liquid cooling system lowered system temperatures and improved efficiency. IGBT module spacing significantly impacts heat transfer, necessitating optimization. The sandwich busbar design effectively reduced parasitic inductance and system size.
- Figure List and Description: Figures in the paper visually represent the electric vehicle model, power stage designs, cooling system designs, loss calculations, and experimental results.
- Here's a Figure List in English based on the provided text. Since the OCR was not perfect and some figure descriptions were incomplete, I've made educated guesses where necessary. You should verify this list against the original paper for complete accuracy.
- Figure List
- Figure 1: Force components acting on the vehicle.
- Figure 2: Vehicle general model.
- Figure 3: Internal structure block of the general vehicle model.
- Figure 4: BLDC motor Simulink model.
- Figure 5: Load model.
- Figure 6: IGBT modules selected for BLDC motor driver.
- Figure 7: Thermal resistance of the system with cooler.
- Figure 8: Placement of IGBT modules in the heatsink.
- Figure 9: Sample IGBT (20 mm) thermal distribution.
- Figure 10: Sample IGBT (0 mm) thermal analysis.
- Figure 11: Liquid cooler module top and profile view.
- Figure 12: Liquid cooling module top view.
- Figure 13: Liquid cooling module with IGBTs in place.
- Figure 14: (a) Axial-flow fan; (b) Radial-flow fan; (c) Cross-flow fan.
- Figure 15: Sandwich busbar design.
- Figure 16: DC-Bus IGBT heatsink and capacitance.
- Figure 17: IGBT module design on a fluid cooling system.
- Figure 18: Original 75 kW fan-assisted natural-air cooled three-phase inverter circuit.
- Figure 19: Original 75 kW liquid-cooled three-phase inverter circuit.
- Figure 20: Original three-phase 75 kW liquid cooled inverter circuit with six IGBT modules.
- Figure 21: Three-dimensional design visuals of the cooling module from the front, top and side.
- Figure 22: SKiM459GD12E4 IGBT module, adapter circuit, and IGBT driver assembly.
- Figure 23: (a) Original three-phase 75 kW liquid cooled inverter circuit with six IGBT modules; (b) Different angle view of Figure 23(a).
- Figure 24: The BLDC motor's rapid control prototyping block diagram with dSpace Micro-Auto Box.
- Figure 25: System engine-generator test platform with DS1401 dSpace Micro-Auto Box.
- Figure 26: BLDC motor phase currents and interphase voltages.
- Remember that this list is based on the extracted text and might not be entirely complete or perfectly accurate. Always refer to the original paper for definitive information.
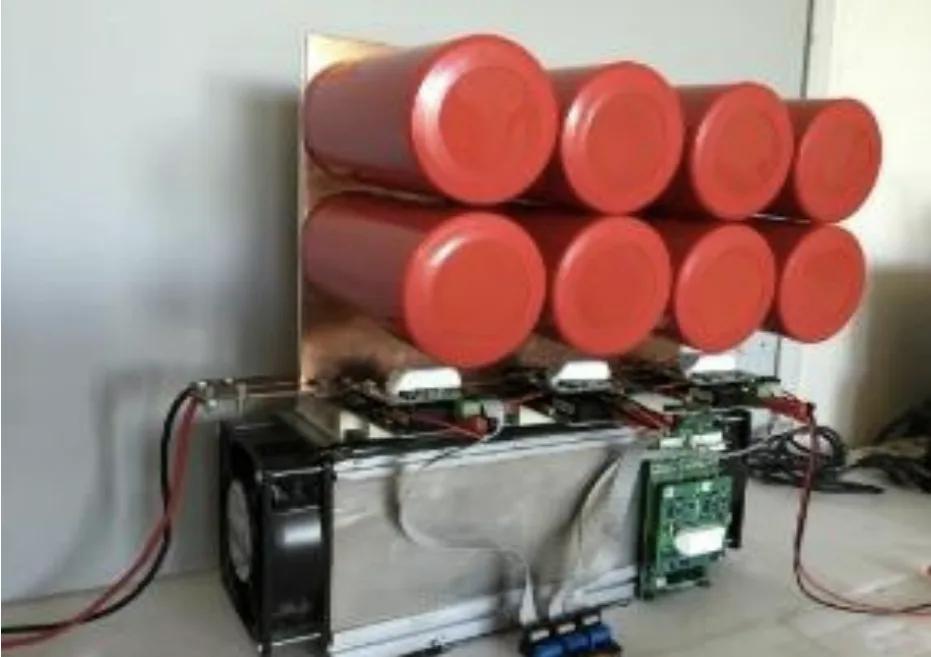
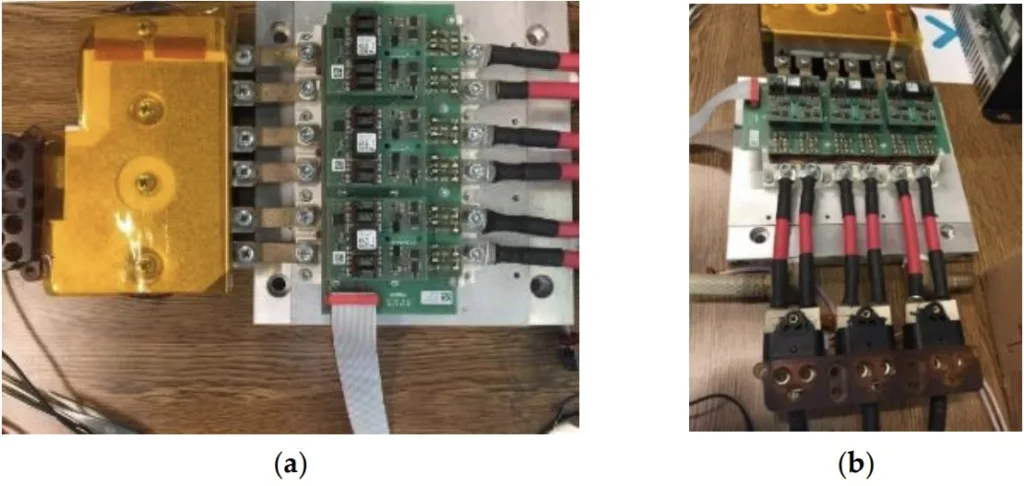
6. Conclusions and Discussion:
Comparative analysis of three different power stage designs and cooling systems revealed that the liquid cooling system offered superior efficiency. This research provides valuable insights into the design of power and cooling systems for enhanced electric vehicle efficiency. The sandwich busbar design is effective in minimizing size and losses. Optimization of IGBT module spacing is crucial for reducing thermal resistance.
Limitations: The study was conducted via simulation and in a laboratory setting; performance under real-world driving conditions may differ.
7. Future Research:
Future research should focus on validating performance under real-world driving conditions, analyzing the impact of varying driving cycles on cooling system performance, and developing more efficient cooling systems and control algorithms.
8. References:
- Tutelea, L.; Boldea, I. Optimal Design of Residential Brushless D.C. Permanent Magnet Motors with FEM Validation. In
Proceedings of the Aegean Conference on Electric Machines, Power Electronics and Electromotion (ACEMP ‘07), Bodrum, Turkey,
10–12 September 2007; pp. 435–439. - Zarko, D.; Ban, D.; Lipo, T.A. Analytical Solution for Cogging Torque in Surface Permanent-Magnet Motors Using Conformal
Mapping. IEEE Trans. Magn. 2007, 44, 52–64. [CrossRef] - Ustun, O.; Yilmaz, M.; Gokce, C.; Karakaya, U.; Tuncay, R.N. Energy Management Method for Solar Race Car Design and
Application. In Proceedings of the IEEE International Electric Machines and Drives Conference, Miami, FL, USA, 3–6 May 2009;
pp. 804–811. - Markovic, M.; Hodder, A.; Perriard, Y. An Analytical Determination of The Torque–Speed and Efficiency–Speed Characteristics
of a BLDC Motor. In Proceedings of the Energy Conversion Congress and Exposition (ECCE 2009), San Jose, CA, USA, 20–24
September 2009; pp. 168–172. - Zhao, L.; Ham, C.; Zheng, L.; Wu, T.; Sundaram, K.; Kapat, J.; Chow, L. A Highly Efficient 200,000 Rpm Permanent Magnet Motor
System. IEEE Trans. Magn. 2007, 43, 2528–2530. [CrossRef] - Tuncay, R.N.; Üstün, O.; Yılmaz, M.; Gokce, C.; Karakaya, U. Design and Implementation of An Electric Drive System for In-Wheel
Motor Electric Vehicle Applications. In Proceedings of the 7th IEEE Vehicle Power and Propulsion Conference (VPPC’11), Chicago,
IL, USA, 6–9 September 2011; pp. 1–6. - Bahadir, A.; Aydogdu, O. Modeling of a brushless dc motor driven electric vehicle and its pid-fuzzy control with dSPACE. Sigma
J. Eng. Nat. Sci. 2023, 41, 156–177. [CrossRef] - Wu, W.; Wang, S.; Wu, W.; Chen, K.; Hong, S.; Lai, Y. A critical review of battery thermal performance and liquid based battery
thermal management. Energy Convers. Manag. 2019, 182, 262–281. [CrossRef] - Arasu, M.; Ahmed, Q.; Rizzoni, G. Optimizing battery cooling system for a range extended electric truck. SAE Tech. Pap. 2019,
2019, 158. - Kong, D.; Peng, R.; Ping, P.; Du, J.; Chen, G.; Wen, J. A novel battery thermal management system coupling with PCM and
optimized controllable liquid cooling for different ambient temperatures. Energy Convers. Manag. 2020, 204, 112280. [CrossRef] - Davin, T.; Pellé, J.; Harmand, S.; Yu, R. Experimental study of oil cooling systems for electric motors. Appl. Therm. Eng. 2015,
75, 1–13. [CrossRef] - Fang, G.; Yuan, W.; Yan, Z.; Sun, Y.; Tang, Y. Thermal management integrated with three-dimensional heat pipes for air-cooled
permanent magnet synchronous motor. Appl. Therm. Eng. 2019, 152, 594–604. [CrossRef] - Huang, J.; Naini, S.S.; Miller, R.; Rizzo, D.; Sebeck, K.; Shurin, S.; Wagner, J. A Hybrid Electric Vehicle Motor Cooling System—
Design, Model, and Control. IEEE Trans. Veh. Technol. 2019, 68, 4467–4478. [CrossRef] - Lombardi, S.; Villani, M.; Chiappini, D.; Tribioli, L. Cooling System Energy Consumption Reduction through a Novel All-Electric
Powertrain Traction Module and Control Optimization. Energies 2021, 14, 33. [CrossRef] - Bhosale, P.; Hermwille, M. Connection of Gate Drivers to IGBT and Controller. Semikron Application Note AN-7002. 5 September
- Available online: www.Semikron.com/Application/DriverConnection (accessed on 18 January 2024).
- Daucher, C.; Wintrich, A.; Pluschke, N. SEMIKRON Application Manual—Power Modules; 4 April 2006 Rev1; SEMIKRON:
Nuremberg, Germany, 2006. - Wintrich, A.; Nicolai, U.; Tursky, W.; Reimann, T. SEMIKRON Application Manual—Power Semiconductors, 2nd ed.; ISLE Verlag,
SEMIKRON International: Nuremberg, Germany, 2015; pp. 299–302, ISBN 978-3-938843-83-3. - Pluschke, N. Application Manual Power Modules; SEMIKRON: Nuremberg, Germany, 2006.
Copyright:
This summary is based on the paper "Three-Phase 75 kW Brushless Direct Current Motor for Electric Vehicles: Different Power Stage Design, Calculation of Losses, Cooling Techniques, and Comparison" by Ali Bahadir, Omer Aydogdu, and Elif Bahadir.
DOI URL: https://doi.org/10.3390/app14041365
This material is a summary and its unauthorized commercial use is prohibited.
Copyright © 2025 CASTMAN. All rights reserved.